- 2022-09-27 发布 |
- 37.5 KB |
- 18页
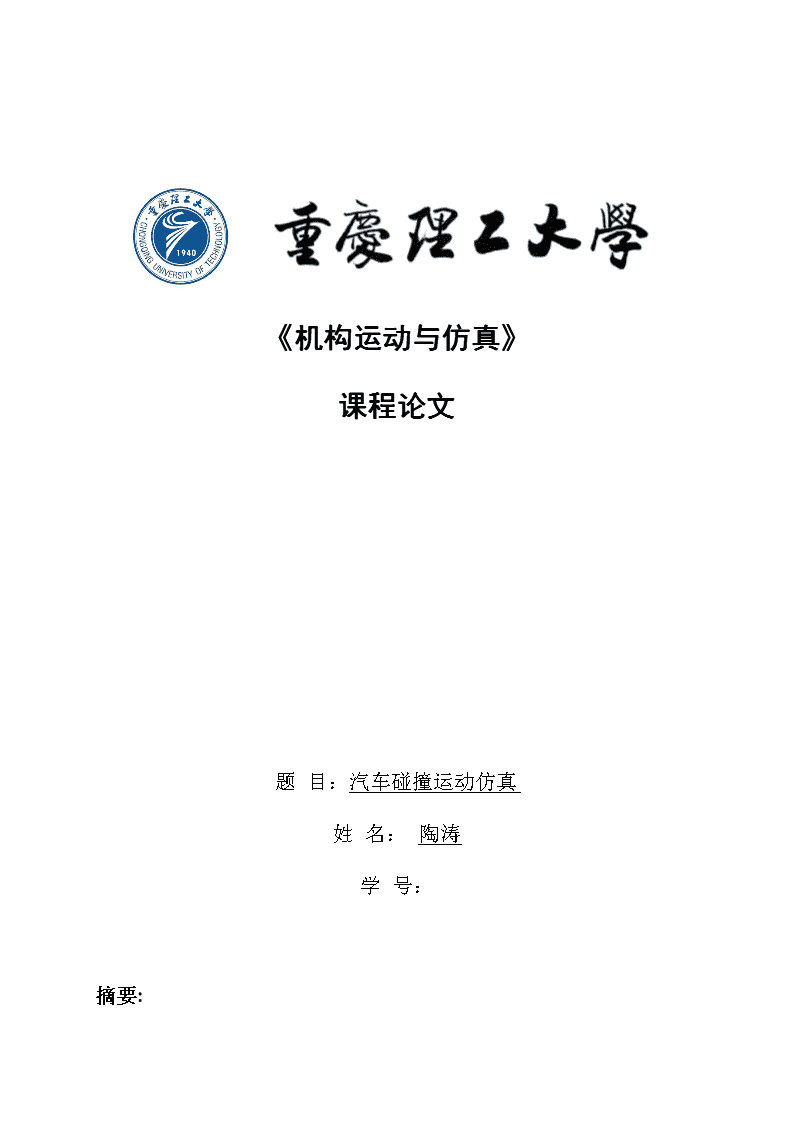
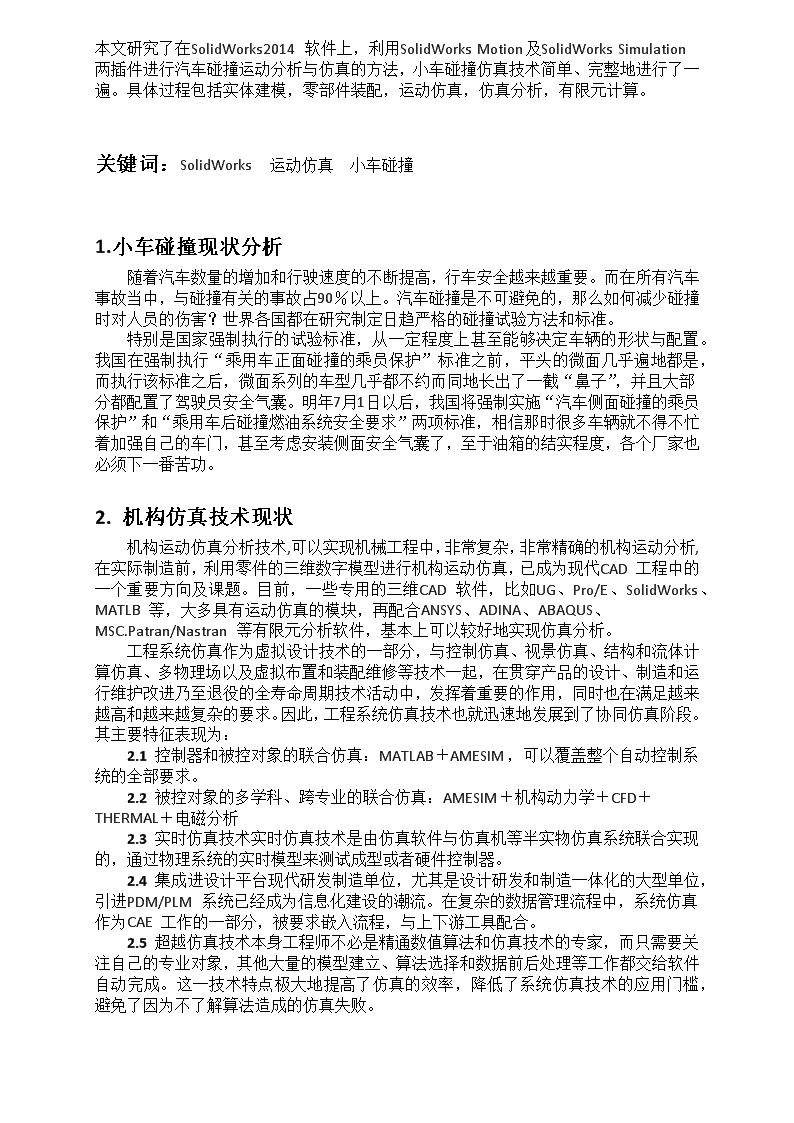
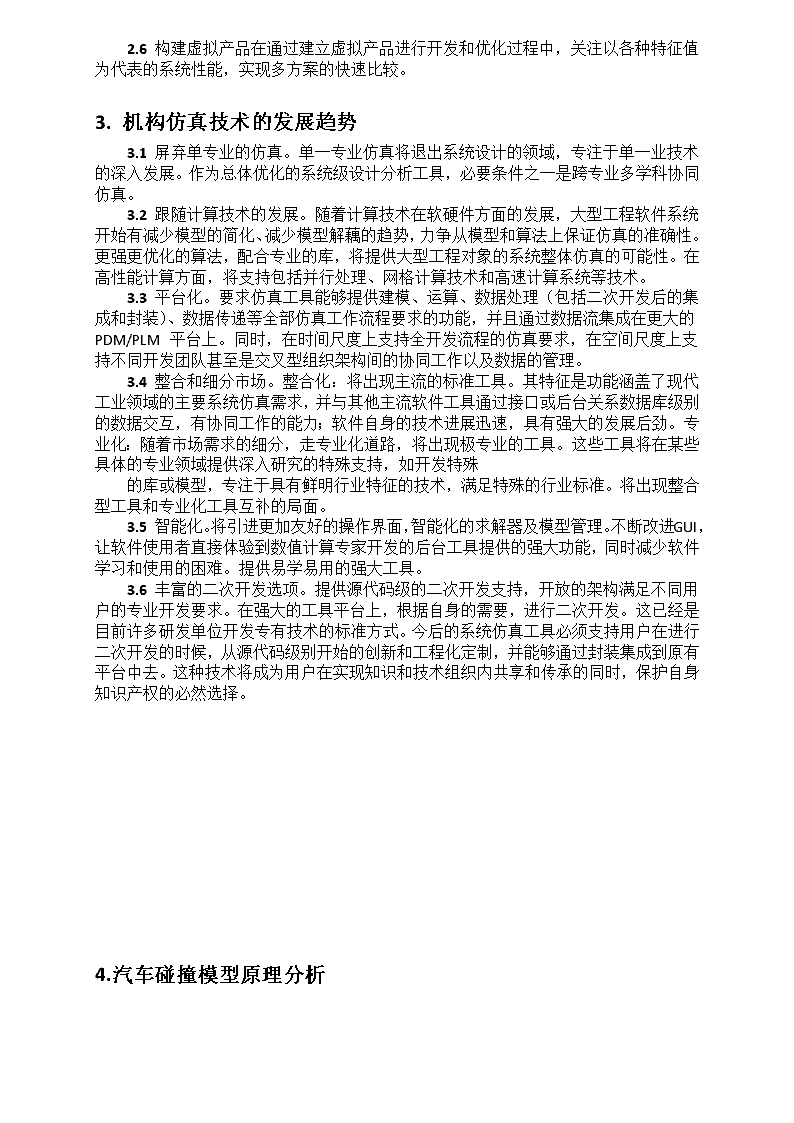
申明敬告: 本站不保证该用户上传的文档完整性,不预览、不比对内容而直接下载产生的反悔问题本站不予受理。
文档介绍
机构运动与仿真课程论文-汽车碰撞运动仿真
《机构运动与仿真》课程论文题目:汽车碰撞运动仿真姓名:陶涛学号:摘要:\n本文研究了在SolidWorks2014软件上,利用SolidWorksMotion及SolidWorksSimulation两插件进行汽车碰撞运动分析与仿真的方法,小车碰撞仿真技术简单、完整地进行了一遍。具体过程包括实体建模,零部件装配,运动仿真,仿真分析,有限元计算。关键词:SolidWorks运动仿真小车碰撞1.小车碰撞现状分析随着汽车数量的增加和行驶速度的不断提高,行车安全越来越重要。而在所有汽车事故当中,与碰撞有关的事故占90%以上。汽车碰撞是不可避免的,那么如何减少碰撞时对人员的伤害?世界各国都在研究制定日趋严格的碰撞试验方法和标准。特别是国家强制执行的试验标准,从一定程度上甚至能够决定车辆的形状与配置。我国在强制执行“乘用车正面碰撞的乘员保护”标准之前,平头的微面几乎遍地都是,而执行该标准之后,微面系列的车型几乎都不约而同地长出了一截“鼻子”,并且大部分都配置了驾驶员安全气囊。明年7月1日以后,我国将强制实施“汽车侧面碰撞的乘员保护”和“乘用车后碰撞燃油系统安全要求”两项标准,相信那时很多车辆就不得不忙着加强自己的车门,甚至考虑安装侧面安全气囊了,至于油箱的结实程度,各个厂家也必须下一番苦功。2.机构仿真技术现状机构运动仿真分析技术,可以实现机械工程中,非常复杂,非常精确的机构运动分析,在实际制造前,利用零件的三维数字模型进行机构运动仿真,已成为现代CAD工程中的一个重要方向及课题。目前,一些专用的三维CAD软件,比如UG、Pro/E、SolidWorks、MATLB等,大多具有运动仿真的模块,再配合ANSYS、ADINA、ABAQUS、MSC.Patran/Nastran等有限元分析软件,基本上可以较好地实现仿真分析。工程系统仿真作为虚拟设计技术的一部分,与控制仿真、视景仿真、结构和流体计算仿真、多物理场以及虚拟布置和装配维修等技术一起,在贯穿产品的设计、制造和运行维护改进乃至退役的全寿命周期技术活动中,发挥着重要的作用,同时也在满足越来越高和越来越复杂的要求。因此,工程系统仿真技术也就迅速地发展到了协同仿真阶段。其主要特征表现为:2.1控制器和被控对象的联合仿真:MATLAB+AMESIM,可以覆盖整个自动控制系统的全部要求。2.2被控对象的多学科、跨专业的联合仿真:AMESIM+机构动力学+CFD+THERMAL+电磁分析2.3实时仿真技术实时仿真技术是由仿真软件与仿真机等半实物仿真系统联合实现的,通过物理系统的实时模型来测试成型或者硬件控制器。2.4集成进设计平台现代研发制造单位,尤其是设计研发和制造一体化的大型单位,引进PDM/PLM系统已经成为信息化建设的潮流。在复杂的数据管理流程中,系统仿真作为CAE工作的一部分,被要求嵌入流程,与上下游工具配合。2.5超越仿真技术本身工程师不必是精通数值算法和仿真技术的专家,而只需要关注自己的专业对象,其他大量的模型建立、算法选择和数据前后处理等工作都交给软件自动完成。这一技术特点极大地提高了仿真的效率,降低了系统仿真技术的应用门槛,避免了因为不了解算法造成的仿真失败。\n2.6构建虚拟产品在通过建立虚拟产品进行开发和优化过程中,关注以各种特征值为代表的系统性能,实现多方案的快速比较。3.机构仿真技术的发展趋势3.1屏弃单专业的仿真。单一专业仿真将退出系统设计的领域,专注于单一业技术的深入发展。作为总体优化的系统级设计分析工具,必要条件之一是跨专业多学科协同仿真。3.2跟随计算技术的发展。随着计算技术在软硬件方面的发展,大型工程软件系统开始有减少模型的简化、减少模型解藕的趋势,力争从模型和算法上保证仿真的准确性。更强更优化的算法,配合专业的库,将提供大型工程对象的系统整体仿真的可能性。在高性能计算方面,将支持包括并行处理、网格计算技术和高速计算系统等技术。3.3平台化。要求仿真工具能够提供建模、运算、数据处理(包括二次开发后的集成和封装)、数据传递等全部仿真工作流程要求的功能,并且通过数据流集成在更大的PDM/PLM平台上。同时,在时间尺度上支持全开发流程的仿真要求,在空间尺度上支持不同开发团队甚至是交叉型组织架构间的协同工作以及数据的管理。3.4整合和细分市场。整合化:将出现主流的标准工具。其特征是功能涵盖了现代工业领域的主要系统仿真需求,并与其他主流软件工具通过接口或后台关系数据库级别的数据交互,有协同工作的能力;软件自身的技术进展迅速,具有强大的发展后劲。专业化:随着市场需求的细分,走专业化道路,将出现极专业的工具。这些工具将在某些具体的专业领域提供深入研究的特殊支持,如开发特殊的库或模型,专注于具有鲜明行业特征的技术,满足特殊的行业标准。将出现整合型工具和专业化工具互补的局面。3.5智能化。将引进更加友好的操作界面,智能化的求解器及模型管理。不断改进GUI,让软件使用者直接体验到数值计算专家开发的后台工具提供的强大功能,同时减少软件学习和使用的困难。提供易学易用的强大工具。3.6丰富的二次开发选项。提供源代码级的二次开发支持,开放的架构满足不同用户的专业开发要求。在强大的工具平台上,根据自身的需要,进行二次开发。这已经是目前许多研发单位开发专有技术的标准方式。今后的系统仿真工具必须支持用户在进行二次开发的时候,从源代码级别开始的创新和工程化定制,并能够通过封装集成到原有平台中去。这种技术将成为用户在实现知识和技术组织内共享和传承的同时,保护自身知识产权的必然选择。4.汽车碰撞模型原理分析\n该模型由1,小车2,车轮3,车轮轴4,路面5,墙组成。利用在后轮上添加的一个马达来实现小车的运动,在小车前放置的墙会阻挡小车前进,这样就会产生碰撞,我们要做的就是分析他的:速度,位移,加速度,运动路线。5.汽车碰撞模型建模,仿真与分析5.1建模5.1.1汽车地盘建模先画出如图的矩形线框,在进行倒圆角,在进行拉伸,在进行操作做出一个薄壁。还要在车身上打四个孔,这样小车地盘就建好了\n进行这个操作在侧面打出四个孔\n5.1.2汽车车轮建模建立两个如图所示的大圆500,小圆50的同心圆,在进行拉伸操作150。就可以得到这样一个空心圆柱体。在进行倒圆角R30如图所示。再进行抽壳,如图所示,这样车轮就建好了。\n5.1.3汽车车轮轴建模先草图建立一个直径40的圆,在进行拉伸2100就成了5.1.4路面建模先草图建立一个长10000,宽2800的矩形,再进行拉伸100就好了。5.1.5墙体建模先草图建立一个长2400,宽1000的矩形,再进行拉伸1000就好了\n5.2装配先插入车轮轴和车轮两个端面重合配合,轴向使用同心轴配合。再插入车体先用同心轴配合,在用重合配合完成车轮的安装在插入路面用相切命令,再用距离配合把小车安放在路面上插入墙体用几个重合配合完成墙体的安装\n完成整个装配:5.3仿真打开右下角运动算例,选择motion分析5.3.1添加运动添加转动马达\n5.3.2添加接触添加接触,选取接触组,四个轮胎为一组,地面为一组\n5.3.3添加力添加引力,以地面向下为引力方向创建完成参数设置5.3.4仿真模拟仿真时间设定为5s。在工具栏中点击进行仿真。对于本机构我们比较关注的是小车的速度,加速度,位移,运动路线,反作用力。所以输出运动图解如图所示。\n运动仿真结果,较能满足要求。5.4有限元分析在【工具】/【插件】中选中SolidWorksSimulation。如图5.4.1所示\n点击工具栏新算例。选择跌落测试,在点击工具栏跌落设置。设置冲击速度方向如图蓝色区域,引力方向如图粉色区域\n按图进行跌落设置。在按照设置设计好网格。\n然后点击结果选项点击工具栏,计算结果。设置墙体和车身的材料如下图:\n算例结果名称类型最小最大应力1VON:vonMises应力0.N/m^2节:133331.12756N/m^2节:993装配体1-跌落测试1-应力-应力1\n名称类型最小最大位移1URES:合位移34673.1mm节:134673.1mm节:1装配体1-跌落测试1-位移-位移1名称类型最小最大应变1ESTRN:对等应变3.54082e-015单元:126851.12046e-011单元:3365装配体1-跌落测试1-应变-应变1\n6.总结通过solidworks软件进行的汽车碰撞测试,我们可以直观的知道汽车模型的运动路线,位移,速度,加速度,反作用力和自身收到的应力,应变特性等。有利于我研发汽车的进程加快,和改善汽车的机构,比起用真车来进行现场的模拟碰撞测试省下了一大笔经费。虽然不能完美的模拟出实情,但能较大程度的反映现实情况,而且模拟的变量可以设置更多,更加能反映不同状态下的汽车碰撞结果。7.参考文献【1】张晋西等.SolidWorks及COSMOSMotion机械仿真设计[M].北京:清华大学出版社,2007.【2】彭亮、曾德惠等.中文版solidworks三维机械设计快学易通[M].北京:机械工业出版社,2008.查看更多