- 2021-04-10 发布 |
- 37.5 KB |
- 31页
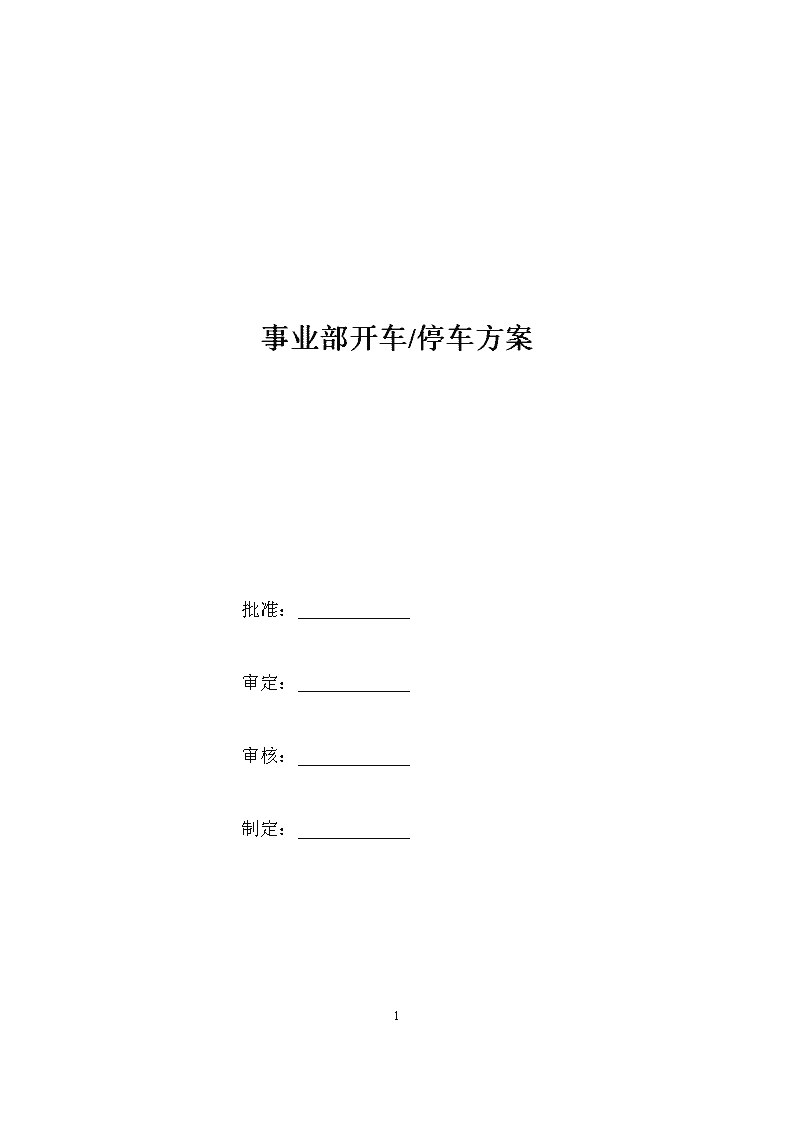
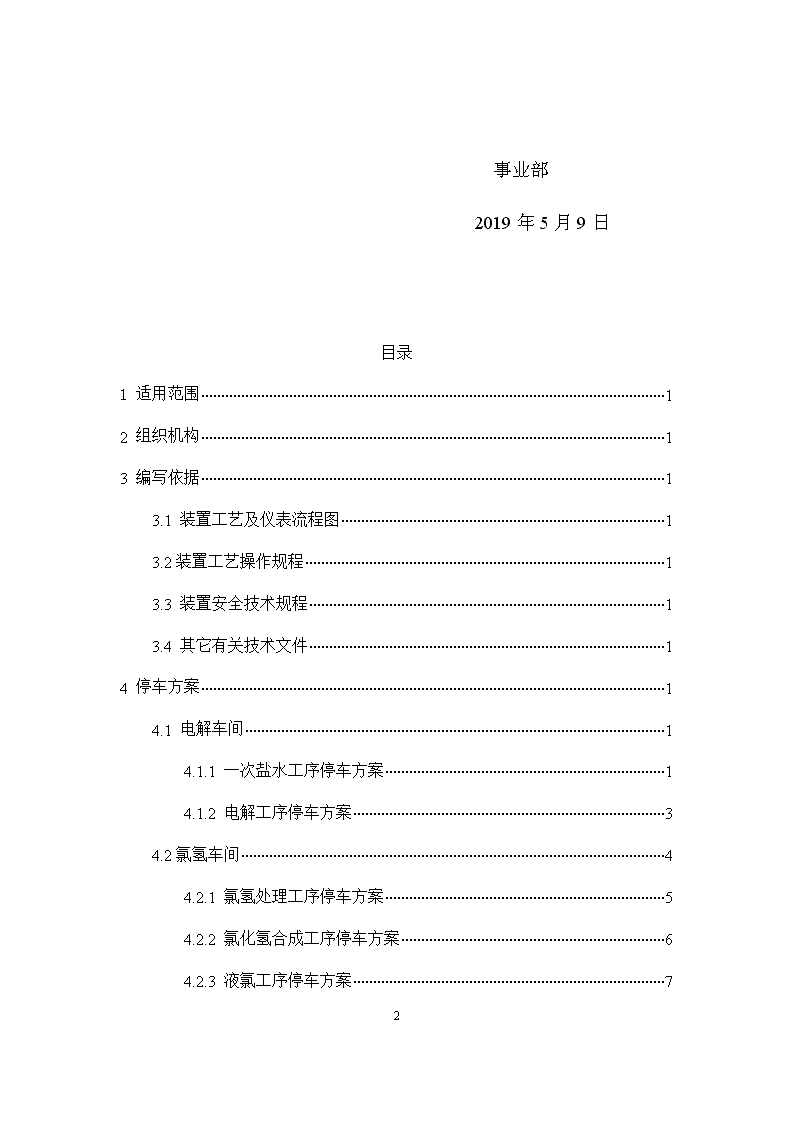
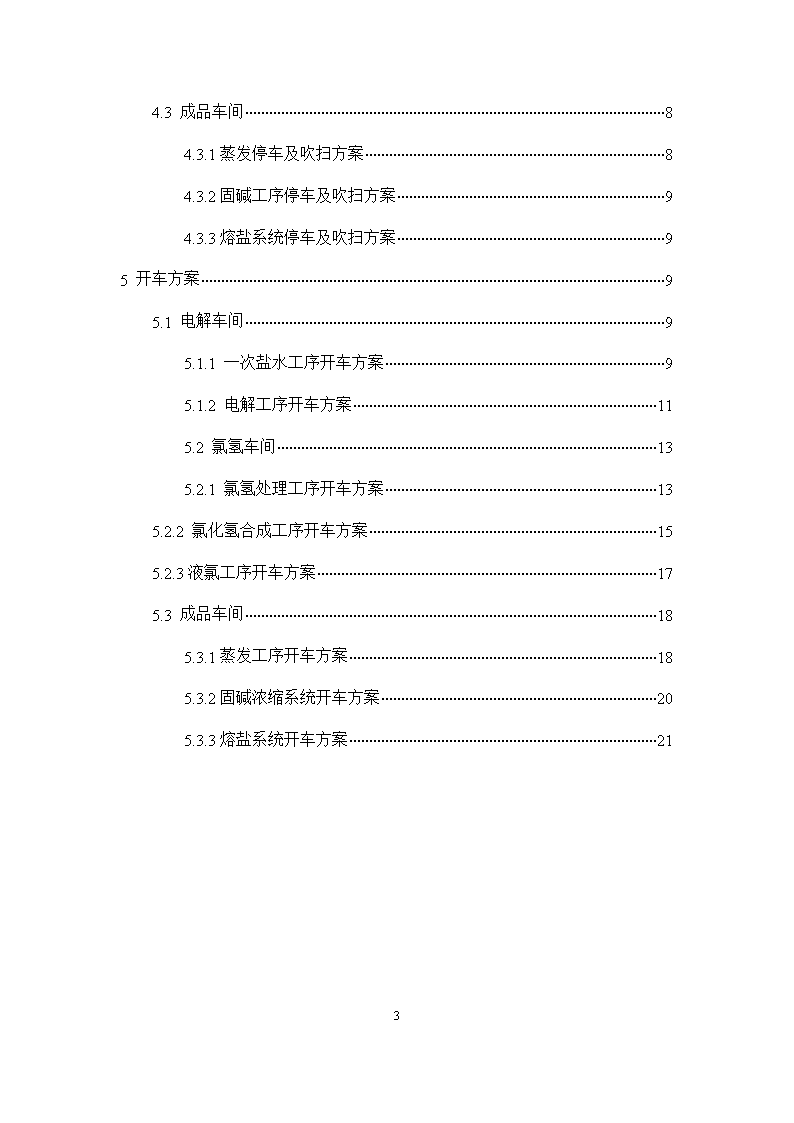
申明敬告: 本站不保证该用户上传的文档完整性,不预览、不比对内容而直接下载产生的反悔问题本站不予受理。
文档介绍
烧碱事业部电解开停车方案
事业部开车/停车方案 批准: 审定: 审核: 制定: 4 事业部 2019年5月9日 目录 1 适用范围 1 2 组织机构 1 3 编写依据 1 3.1 装置工艺及仪表流程图 1 3.2装置工艺操作规程 1 3.3 装置安全技术规程 1 3.4 其它有关技术文件 1 4 停车方案 1 4.1 电解车间 1 4.1.1 一次盐水工序停车方案 1 4.1.2 电解工序停车方案 3 4.2氯氢车间 4 4.2.1 氯氢处理工序停车方案 5 4.2.2 氯化氢合成工序停车方案 6 4.2.3 液氯工序停车方案 7 4 4.3 成品车间 8 4.3.1蒸发停车及吹扫方案 8 4.3.2固碱工序停车及吹扫方案 9 4.3.3熔盐系统停车及吹扫方案 9 5 开车方案 9 5.1 电解车间 9 5.1.1 一次盐水工序开车方案 9 5.1.2 电解工序开车方案 11 5.2 氯氢车间 13 5.2.1 氯氢处理工序开车方案 13 5.2.2 氯化氢合成工序开车方案 15 5.2.3液氯工序开车方案 17 5.3 成品车间 18 5.3.1蒸发工序开车方案 18 5.3.2固碱浓缩系统开车方案 20 5.3.3熔盐系统开车方案 21 4 4 1 适用范围 事业部检修时的系统停车,开车。 2 组织机构 组长: 副组长: 成员:各车间主任、副主任及技术员,工艺、设备、安全专工及技术员,其他事业部行政管理人员。 3 编写依据 3.1 装置工艺及仪表流程图 3.2装置工艺操作规程 3.3 装置安全技术规程 3.4 其它有关技术文件 4 停车方案 4.1 电解车间 4.1.1 一次盐水工序停车方案 4.1.1.1停车步骤 27 要求是在电解槽循环完成,切出系统后,不需要盐水且准备将阳极系统打空时,一次盐水工序停车。 (1)接领导、调度停车通知后,主控(xx)根据系统实际情况将碳酸钠、三氯化铁配制槽、高位槽内的精制剂刚好用完。 (2)主控(xx)通知现场关闭空气缓冲罐Z-401进出口阀,停止加入工艺空气。 (3)主控(xx)停止给E-401蒸汽,停止化盐水泵P-401A/B,同时通知(苏金凤)停止上盐;停止精制剂的加入,并通知电解主控,注意系统的指标变化。 (4)主控根据V-401的液位情况,注意进水量,必要时,通知调度停止外工序水进入V-401。 (5)待粗盐水池液位低时,主控联系现场停加压泵P-404A/B/C,及精制剂的加入。 (6)预处理器上没有盐水流出时,待碳酸钠高位槽内的液位流净后,(xx)关闭碳酸钠溶液进反应槽的阀门FV-5106,停反应槽R-401搅拌器。 (7)主控(xx)观察V-406缓冲槽液位为20%时,通知现场操作人员关戈尔膜过滤器进液阀,同时关闭戈尔膜过滤器上清液出口阀,过滤器内盐水不必放掉(注意,不论生产时还是停车期,戈尔膜必须保持湿润,否则膜干后容易发脆,直接影响下次开车并缩短使用寿命)。 (8)主控(xx)停止给V-408加入盐酸。 (9)主控(xx)等待电解通知不需要盐水时,通知现场停P-409。 4.1.1.2 应急处理 (1)盐酸/管道泄漏:在一次盐水停车过程中,管道里的酸或碱可能会泄漏,现场操作人员在停泵或是在关闭酸碱阀门时,要穿戴好防护用品,将防护面罩、手套穿戴齐全。处理方法:如果不慎,受到酸碱的灼伤,要保持冷静,用流动的水清洗,冲洗要及时、彻底,头面部灼伤要注意眼、耳、口、鼻的清洗,应采用特定的急救药品进行清洗。 27 (2)V-401液位高:处理办法:通知调度,外工序的回收水停止给V-401进液。 4.1.1.3 下次开车准备 (1)在检修期间,由于管道或设备的检修,已将部分重要设备内的液体排净,这些设备内的液体是系统开车的主要物料,一次盐水工序中在开车前必须将V-401的液位保证在65%-75%,化盐槽内的原盐高度必须保证在5米左右。 (2)氢氧化钠高位槽、盐酸高位槽都有液位,供使用。 4.1.1.4 设备维护 (1)戈尔膜过滤器滤芯:现场操作人员将戈尔膜过滤器进液阀、清液出口阀关闭后,要求是过滤器内盐水不能全部放掉,要求将盐水排至栏板10公分即可。 原因是不论生产时还是停车期,戈尔膜必须保持湿润,否则膜干后容易发脆,直接缩短戈尔膜的使用寿命。 (2)将预处理器底部的盐泥必须排净,以防止盐泥堵塞设备。 (3)必须将盐泥池内的盐泥全部处理,为方便下一次顺利开车。 (4)及时放净各盐水泵碳酸钠泵等易结晶泵及管线内剩余液体,防止停车期间结晶堵塞管道。 4.1.2 电解工序停车方案 4.1.2.1 停车步骤 (1) 接到领导、调度停车的通知后,主控(方彤)联系整流控制人员到DCS,准备降电流。 (2) 主控(曹娜)通知现场人员对电解槽进行螺母、油压的调节,9MPa。将电位差联锁切除,同时如果电解槽是加酸情况,则停止给电解槽加酸。 (3)主控开始降电流后,通知现场操作人员巡检电解槽。 27 (4)主控在降电流的过程中,主副操要协作配合好,将总管的压差保证正压范围(2-6kPa),二盐系统及阴阳极系统的液位及指标要在正常控制范围内。 (5)电流降至零后,主控(方彤)检查各项联锁是否启动、氮气是否进入阴极系统。同时通知巡检,等待检查中央断路器的启动情况。 (6)主控(方彤)对树脂塔进行水洗放置,停氯酸盐分解槽。 (7)电解槽循环完成后,巡检开始对电解槽陆续的进行断气相、断液相、排液等操作。 (8)主控(方彤)等待电解槽具体步骤操作完成后,将阴阳极循环系统的各储罐液位全部打空,具体是:1)阳极系统:通知一次盐水工序停P-409泵,关闭TCV-153蒸汽阀,D-150液位0%时通知现场停P-154泵,D-175液位0%时通知现场停P-174泵,D-170液位0%时通知现场关85阀,D-260液位0%时通知现场停P-264泵,T-310液位0%时通知现场停P-314泵,主控停止给脱氯系统加酸、碱。2)阴极系统:电解槽断液后,停止给E-273换热,关闭TCV273/LCV273停止给D-273进液,D-273液位0%时通知现场关88阀,D-270液位0%时停P-274泵。 (9)巡检(丁治旺)对电解槽进行洗槽、保养工作。 4.1.2.2 应急处理 (1)在电解停车过程中,管道里的酸或碱经常会泄漏,现场操作人员在操作时,要穿戴好防护用品,将防护面罩、手套穿戴齐全。如果不慎,受到酸碱的灼伤,要保持冷静,用流动的水清洗,冲洗要及时、彻底,头面部灼伤要注意眼、耳、口、鼻的清洗,应采用特定的急救药品进行清洗。 (2)氯气泄漏,停车后,有时氯气会泄漏,这需要主控人员注意系统负压的调节,通知现场人员在操作中,要戴好防毒面具。如果不慎吸入氯气,要根据吸入量进行相应的解救。 (3)在停车过程中,如遇到电解槽突然跳停情况,主控人员迅速调节保证总管压差为正压范围,且按照正常停车的程序检查电解槽的联锁启动情况。 27 (4)压差异常:在降电流时,有时压力波动较大,如果压差下降较快,主控将氯气阀门开大;如果压差上涨较快,将氯气阀门关小。 4.1.2.3 下次开车准备 (1)在检修期间,由于管道或设备的检修,已将部分重要设备内的液体排净,这些设备内的液体是系统开车的主要物料,电解在开车前必须将D-330的液位保证在85%以上。D-340的液位保证在70%-80%。D-350液位保证在70%以上。 4.1.2.4 设备维护 (1)树脂塔:在电解槽停止循环后,树脂塔T-160A/B/C三塔用纯水进行水洗置换完成后,塔内装水放置。目的是为了防止树脂在盐水、酸碱溶液中受到损坏,丧失交换能力。(停车后,一、二塔分别进行反洗和水洗1即可) (2)电解槽离子膜:在电解槽停车后,进行排液、洗槽,洗槽完成后,要对电解槽离子膜进行膜保养操作,为了是防止停车期间离子膜变干。所以巡检要定时巡检电解槽进液软管的液位及氮气密封桶内的补水情况。 4.2氯氢车间 4.2.1 氯氢处理工序停车方案 4.2.1.1 停车步骤 (1)氯气处理 1)接到调度通知电解降电流,并根据电流情况稳定好总管压力,适当时候打开氯气分配台上至事故氯处理工序氯气管上的阀门。 2)直到全部电槽停止送电后,氯气压缩机(C-501A-D)按正常停车程序停车,关闭进氯气压缩机的氯气阀门,全开氯气压缩机进口管线上至事故氯处理的阀门并用氮气置换氯气压缩机里的氯气,时间大约半小时。 3)关闭进各个换热器的冷却水、冷冻水和硫酸等阀门。 27 4)停氯水循环泵(P-501A/B)、稀硫酸循环泵(P-502A/B)、浓硫酸循环泵(P-503A/B)。 5)排净设备和管道中的残液,并进行清洗和吹扫。 (2)氢气处理 1)接到调度电解降电流通知,通过大回流阀稳定总管压力,根据合成炉降量情况,缓慢打开放空管道阀门,稳定调节压力,最后将氢气放空。 2)同时缓慢打开氢气压缩机(C-551)自身循环阀,关闭氢压机出口阀及进口阀(置换之前必须打开氢压机的进出口阀门)。 3)直到全部电槽停止送电后,打开HV-5462阀门充氮气置换,并调节大回流阀HV-5401和PV-5401B,等待置换。 4)置换合格后缓慢关闭氢气压缩机(C-551)进、出口阀,氢气压缩机停止运转。 5)关闭纯水、冷冻上水和循环上水供水阀门。 (3)事故氯处理 事故氯处理碱液循环泵及引风机一直运转,等待所有车间氯气系统置换合格后,对事故氯处理的碱液化验,方可停车。 4.2.1.2应急处理 (1)停车时碱液管道、硫酸管道、次氯酸钠管道及循环泵有可能出现垫片处泄漏腐蚀性液体,现场巡检穿戴好劳动保护用品,拿配套工具紧螺栓或大卡子,循环泵漏液紧急进行倒泵。 (2)事故氯停车时大量氯气走事故氯,有可能出现碱液浓度低,氯气泄漏,现场巡检戴好防毒面具立刻进行紧急倒槽。 4.2.1.3下次开车准备 (1)氯气洗涤塔、填料干燥塔、组合干燥塔、氢气洗涤塔液位保持到60%,循环水回水池液位保持50%。 27 (2)氯气正负水封、氢气水封槽、氢气放空槽、酸雾捕集器、水雾捕集器加水至溢流。 (3)碱液循环槽液位保持到65%左右,碱液高位槽液位保持到80%,碱液配制槽配制15%碱液备用,浓硫酸高位槽液位保持到80%。 4.2.2 氯化氢合成工序停车方案 4.2.2.1正常停车操作步骤 (1)接到调度停车通知后随着电解槽降电流逐渐减少各台合成炉氯、氢气进炉量(保证氢压不低于联锁值,合成炉纯度控制在90%-93%),然后根据现场运行情况与调度联系逐台将合成炉切回做酸,调节吸收水控制好盐酸指标,待合成炉全部切回做酸后继续对各台炉降量,随着电解槽降电流单台合成炉氢气流量为600Nm³/h,氯气流量300Nm³/h时开始联系调度灭炉,灭炉时主控触动单台停炉联锁关闭进炉氢气、氯气切断阀,巡检同时关闭进炉总阀及操作室手动调节阀,打开充氮阀充氮置换(其它几台合成炉同上)。 (2)停炉后确认炉火熄灭,充氮30分钟后,断开氢气胶管活接头,打开炉门。关闭石墨冷却器进水阀、蒸汽出口阀,稍开蒸汽排空阀缓慢泻去蒸汽压力,保持排空阀长开,以防副产蒸汽系统冷凝形成较大的真空负压。 (3)如果在冬天寒冷季节,正常停炉而又无需长时间检修的情况下,石墨冷却器及吸收塔冷却水出口阀不得关闭,需少许打开冷却水进、出口阀,防止结冰造成设备损坏;副产蒸汽部分需关闭蒸汽出口阀,放净夹套纯水,以免结冰造成设备损坏。长期停车需排净石墨设备内的所有冷却水。与此同时,停止给水,关闭蒸汽输送阀停止供汽,然后再稍开蒸汽排空阀缓慢泻去蒸汽余压。 (4)按规定关闭相关阀门,停止纯水加压泵(P-707A-B)和稀酸泵(P-703A-B)。 (5)停车后,向事业部及调度报告,并认真检查一遍,作好原始停车记录。 4.2.2.2应急处置 27 (1)停车过程中可能出现氯气压力过高,导致出现过氯情况,通知调度紧急处理进行降氯压,让液氯带量必要时直接打开去事故氯处理阀门。 (2)停车过程中可能出现流量计或自控阀出现故障,不可盲目操作及时联系仪表处理。 4.2.2.3下次开车准备 (1)向稀酸贮槽(V-705)注入纯水并保持50%的液位,启动稀酸泵(P-703A-B),检查稀酸泵送出的纯水是否进入→尾气吸收塔(T-703A-F)→二级降膜吸收器(T-702)→一级降膜吸收器(T-701)→盐酸调整罐(V-707)、高纯酸中间罐(V-708),并检查此吸收系统是否正常。 (2)向二合一合成炉(R-701A-F)、一级降膜吸收器(T-701)、二级降膜吸收器(T-702)夹套送循环水,并确认循环水输送正常。 (3)向纯水罐(V-709)注入纯水并保持60%的液位,启动纯水加压泵(P-707A-B),、打开蒸汽闪发罐(V-715A-F)气相放空阀(蒸汽管手动阀)再打开蒸汽炉夹套副产蒸汽部分纯水阀门将夹套充满水至蒸汽闪发罐(V-715A-F)液位计40%处。再关闭纯水阀门, 打开蒸汽闪发罐(V-715A-F)液相排污阀排水至观察两液位计是否一致。 (4)检查炉门、软管及铁丝全部达到点炉要求。 4.2.3 液氯工序停车方案 4.2.3.1正常停车操作步骤 (1)接到调度降电流通知后,注意控制原料氯气及尾气的压力。 (2)接到调度通知停螺杆压缩机后关闭液化器的氯气进口阀、液化器及液氯气液分离器的不凝气出口阀。关闭液氯气液分离器尾气出口阀,停螺杆压缩机,关闭液氯储槽的液氯进口阀。 (3 27 )如需检修,则打开需要检修设备的抽空阀,开启真空泵,抽空系统中氯气,根据设备抽空处理情况,逐个地开关设备的阀门(若停车后不需检修,可不抽空设备和管道中的余氯)。 4.2.3.2应急处理 (1)硫酸管道及真空泵出现泄漏,巡检人员穿戴劳动保护用品拿相应工具现场进行紧螺栓或打卡子及倒泵操作。 (2)氯气管道泄漏,巡检人员戴好防毒面具,用配比好的氨水进行检查漏点,进行堵漏。 4.2.3.3主要设备维护 (1)包装液下泵必须有液氯浸泡。 4.2.3.4下次开车准备 (1)浓硫酸高位槽液位保持到80%; (2)排污罐配比好的15%碱液液位保持到70%; (3)检查螺杆压缩机油液位、氟利昂液位是否在规定值。 4.3 成品车间 4.3.1蒸发停车及吹扫方案 (1)生产装置停车时,应首先将出现故障的设备停车,同时生产调度关闭原水站阀门全部将冷凝液切至一盐。 (2) 关闭蒸汽调节阀[TV-0121],打开余热锅炉及一效前排空阀卸压,保证余热锅炉补水,如余热锅炉补不进去水,加快炉排将煤推掉,并打开观察门,准备碱系统停车。 (3)解除整个生产装置的系统联锁。 (4)依次停Ⅰ效碱泵[P5601]、Ⅱ效碱泵[P5602]、Ⅲ效碱泵[P5603] 27 、循环碱泵[P5608]、原液碱泵[P5607] 、新冷凝水泵[P5604]、冷凝水泵[P5605] 、真空泵[P5606] 、纯水增压泵[P5609]、纯水循环泵[P5610] (5) 关闭各离心泵的机械密封冷却水进口阀,将各离心泵进出口阀关闭。 (6)打开破空阀[ZV154],关闭真空泵[P5606]工作液水进水阀[QV089或 QV089]。 (7)关闭蒸汽冷凝器[E5604]、产品冷却器[E5609]、纯水冷却器[E5610]的循环冷却水进出口阀。 (8)蒸汽冷凝器[E5604]、各效蒸发器内压力为常压后,关闭破空阀[ZV154]和真空泵进口阀[ZV156或 ZV158]。 4.3.2固碱工序停车及吹扫方案 (1)联系生产调度关闭原水站阀门全部将冷凝液切至一盐。 (2)关闭预浓缩加热器的循环阀。 (3)停止50碱泵,停止向预浓缩加热器进碱。 (4)停止真空泵,打开破空阀[ZV424、ZV624],破除系统真空。 (5)停止预浓缩碱泵,停止向最终浓缩加热器进碱。 (6)关闭糖溶解槽出口阀[QV412、QV414],停止向60碱管道加糖液。 (7)重新调整熔盐循环的温度调节器设定值为410℃,熔盐仍然在整个系统内循环。熔盐阀门的蒸汽伴热仍然运行。 (8)将结片机碱槽内的物料处理完毕,关闭结片机和冷却水。 (9)关闭包装机及除尘风机。 (10)以上完成半小时后,用蒸汽冲洗最终浓缩蒸发罐、闪蒸罐和分配罐内的熔融碱管道1-2小时,冲洗时停止氮气供应。 27 4.3.3熔盐系统停车及吹扫方案 (1)首先停止50碱泵、60碱泵,打开U型弯排尽,调高转股转速。 (2)打开5楼吹扫,确认片碱机吹扫是否出汽。 (3)停熔盐泵,加快炉排将煤推掉,并打开观察门,加大鼓引风熔盐炉降温。 5 开车方案 5.1 电解车间 5.1.1 一次盐水工序开车方案 5.1.1.1 开车前准备工作 (1)检修确认 1)检修完成后,检修负责人(曹海龙、郭笑名)确认每一项检修项目完成,检查检修期间所拆的管道、阀门、设备人孔、仪表,是否安装齐全。 2)确认检修质量合格。 (2)工艺确认 1)巡检人员盘泵检查各转动设备,确保灵活备用。 2)联系调度,确认电、生产水、循环水、纯水、压缩空气、仪表空气、蒸汽正常供应。 3)联系分析室,配合分析数据,便于控制精制剂的加入量。 4)配制人员将精制剂配好备用。 5)确认V-401的液位65%-75%,保持盐层高度5米。 5.1.1.2 开车步骤 27 1)接到开车通知后,(马耀英)打开化盐水贮槽V-401A/B的出口阀,启动P-401泵,给E-401进液,将温度控制在57±2℃。 2)盐水进入粗盐水池后,主控(xx)将V-404的过碱量控制在0.2~0.6g/L之间。 3)待粗盐水槽V-404内液位至50%左右时,灌泵并开启加压泵P-404A/B/C。 4)加压溶气罐Z-402液位达到50%时,(xx)打开压缩空气阀门,调节压力在0.2~0.3MPa。 5)待加压溶气罐液位涨至70%-80%,(xx)打开文丘里混合器 (M-401)FeCL3调节阀。 6)将盐水进入预处理器V-405A/B后,出口开始出盐水时,打开后反应槽R-401A上的碳酸钠阀门,调节加入量,使过量碳酸钠在0.3~0.6g/L之间,反应槽R-401A液位达到50%以上时,开启搅拌。 7)开始向缓冲槽V-406进盐水,打开戈尔膜过滤器入口手动阀。 8)现场启动戈尔膜过滤器N-401A/B/C/D/E/F进液程序,打开进液、反洗、排渣等手动阀,清液上升至管板以上按过滤按钮,过滤器进入过滤状态。 9)当过滤盐水进入V-408折流槽时,打开V-425盐酸高位槽的调解阀,设定加入量;盐水pH值调节至9~11。 10)当V-409液位达到50%以上时,通知电解主控,给二盐送盐水。 5.1.2 电解工序开车方案 5.1.2.1 开车前准备工作 (1)检修确认 1)检修完成后,检修负责人(王洪江)确认每一项检修项目完成,检查检修期间所拆的管道、阀门、设备人孔、仪表,是否安装齐全。 2)确认检查气相管道连接完好。 27 3)确认检修质量合格。 (2)工艺确认 1)对所有泵进行盘泵检查各转动设备,确保灵活备用。 2)联系调度,确认电、循环水、纯水、仪表空气、蒸汽正常供应。 3)确认仪表接线完好、仪表显示准确。电解槽具备送电条件。 4)确认电解应急系统的管线已全部置换合格,氮含氧≤1%。 5)确认树脂塔的程序正常。 6)D-330的液位保证在75%-80%(如果D-330的液位不够8台电解槽,可先开4-6台电解槽),D-340的液位保证在70%-80%,盐酸液位70%以上、亚硫酸钠液位70%以上。 7)确认一次盐水送来的盐水各项指标合格。 8)主控检查确认电解槽联锁已复位。 9)确认阀门调试完好,归零状态。 5.1.2.2 开车步骤 (1)置换方案 1)气体置换步骤(参考置换方案或者操作规程) (2)操作步骤 阳极、阴极系统的循环操作 1)接到调度通知,二盐系统及阴阳极系统开始循环。 2)主控联系现场巡检将现场循环所需自控阀的手阀、泵进出口阀打开,准备循环。 3)通知一次盐水工序启动P-409泵,主控将E-153温度调节至55-65℃,D-150 27 液位50%以上后启动P-154泵。 4)盐水进入树脂塔后,分析取样。 5)D-175液位50%以上后启动P-174泵。(树脂塔分析样合格后,启泵送往高位槽) 6)D-170液位80%时,主控通知现场打开85阀。 7)D-260液位50%时,启动P-264泵。 8)T-310液位50%时,启动P-314泵。主控在此时将pH值调节在正常控制指标内。 9)当阳极各储罐液位稳定后,主控通知现场启动真空泵。 10)阳极循环正常后,准备循环阴极。 11)通知现场开86阀给D-270进液,当D-270液位50%时启动P-274泵。 12)D-273液位80%时,现场开88阀。 13)当D-273、D-270液位稳定后,开LCV-270给D-330进液。此时要将E-273/E-330温度控制在正常范围内。(稳定后,将带互备的泵投入互备状态) 电槽进液、送电 1)电解槽充液循环,两台电解槽同时充液。 2)主控打开FCV-242,盐水对水比是2:1。 3)现场开38号阀给阴极充液,一台电槽流量是20m³/h;主控开ZV-241及FCV-231自动阀、3号阀给阳极充液,一台电槽流量是30m³/h。 4)当阴极侧软管溢流时关38号阀。当阳极侧软管溢流时关FCV231。 5)现场对电解槽阀门操作完毕后,主控随时监控D-270/330的液位。同时将阳极循环流量调节至12.4m³/h;阴极循环流量调节至55.2m³/h。 6)8台电解槽全部并入系统后,主控监控槽温,将温度控制在70℃以上。 27 7)当电解槽温度达到70℃,盐水、碱液流量循环正常。 8)通知调度,电槽已具备送电条件。 9)接到调度送电通知,主控再次确认电解槽联锁复位情况,通知现场复位C-DCDS。(注意:电位差联锁切除、盐水阀门切换联锁切除)。 10)升电流开始,主槽将PCV-216阀门调节在自动状态,压差比值开关投入,压差设定4kPa。随着电流的上升,注意FCV-279的调节。副操随时控制系统液位及各项指标(注意:电解槽有运行信号后,方可投入ZV231/241联锁)。 11)电流升至3kA时,通知化验室,取样分析电解槽氯含氢及氯、氢气纯度。 12)电流升至3kA时,投入FI-221、FI-265、FI-231比值开关。 13)分析样合格后,继续升电流,直至升至所需要求电流值(主控主要调节总管压差值,必须保证正压范围)。 5.2 氯氢车间 5.2.1 氯氢处理工序开车方案 5.2.1.1开车前准备工作 (1)检修确认 1)由车间副主任韩月成及当班班长确认氯氢处理检修项目是否全部按计划完成。 2)氯气处理检修由当班巡检工进行确认、氢气处理检修由当班巡检工进行确认、主控系统由当班主控主操及、主控副操进行确认。 3)检查检修项目的完成质量 (2)工艺确认: 1)确认水、电、气等公用工程是否具备开车条件 27 2)确认各设备的液位(水、硫酸、油、碱液等) 3)盘动所有机泵,检查所有阀门及阀门开关是否正确。 4)建立各循环泵与塔、槽的循环。 5.2.1.2氯气处理开车步骤 (1)氯处理操作步骤 1)接到调度准备开车通知后,提前2小时确认氯气压缩机的进口阀门处于关闭状态,打开氮气阀开始置换氯气压缩机,开始空载所要运行的氯气压缩机。 2)在接到调度通知开车,关闭阀门(PV-5301)打开进氯气处理工序的阀门(HV-5301),调节氯压机进口阀门的开度,保持总管压力稳定。氯气处理的废气经氯压机跑氯阀排入事故氯处理。 3)根据电流的大小调整氯气洗涤塔氯水冷却器(E-501)、氯气冷却器冷冻水(E-502),填料塔循环酸冷却器(E-503)、泡罩塔冷冻水盘管(E-530)、浓硫酸冷却器(E-504)冷冻水,控制干燥系统排出气体的水含量。 4)由于开车初期氯气含量较低,因此用氯压机机组上的跑氯阀将不合格氯气送至事故氯处理工序。 5)根据电解槽电流的大小,按氯压机操作要求对氯压机进行升压,手动调节氯压机本机回流阀保持氯气总管压力正常,待电解电流升至3000A时,主控关小跑氯阀,出口压力高于分配台压力时,主控人员通知等候在现场巡检工打开压缩机出口阀门,完成氯压机带量操作,压缩机并入系统。 6)当氯气达Cl2≥70.0%(vol),H2O≤100ppm后,关闭氯气分配台(V-506)上至事故氯处理工序的氯气管上的阀门,同时打开去氯化氢合成的氯气管线上的阀门(注意保持系统压力的稳定),向氯化氢合成工序供应氯气;当氯气纯度达(Cl2≥96.0%(vol),H2O≤100ppm)后,可向液氯工序供合格氯气。 (2)氢气处理开车步骤 1)置换参考置换方案实施 27 2)当接到离子膜开始充氮的通知后,打开氢气洗涤塔(T-551)的氢气进口阀,从氢气洗涤塔(T-551)进口管道上充氮置换本系统内的空气,同时将氢气分配台(V-552)上放空阀门开至一定开度。 3)全开大回流调节阀(PV-5401B和HV-5401)。 4)在提前接到调度开车时间前2小时按氢气压缩机(C-551)操作要求启动氢气压缩机,全开氢气压缩机的出口阀,再全开进口阀,全关氢压机本机回流阀阀门。 5)确认氢气系统被氮气置换合格后放空阀门开至一定开度,准备电解系统开车. 6)电解开始送电时,保持氢气出冷却器的冷却温度在控制范围内,并根据电流升降情况调节冷冻上水和循环上水的进水阀门开启度达到控制指标,同时根据氢气压缩机(C-551)出口压力,调节PV-5401B和HV-5401的大小回流阀。 7)分析氢气纯度,达到要求后,调节放空阀门,通知合成可以点炉。 (3)事故氯处理开车步骤 1)接调度通知,在所有工序开车前提2小时做好一切准备工作。 2)将碱液配制槽配比成15%碱液并保持液位80%,四个碱液循环槽液位保持65%,碱液高位槽液位80%。 3)建立一级碱液循环泵(P-510A/B)与一级碱液吸收塔(T-510)、二级碱液循环泵(P-520A/B) 与二级碱液吸收塔(T-520)的循环,开启E-510、E-520循环水,调节温度在正常范围内。 4)开启风机(C-520A/B)的出口阀门,启动风机,再打开风机的进口阀门。控制事故氯气二级出口压力控制在-1.5~-2.5kPa。 5)等待电解开车时,不合格氯气送到本工序,注意碱浓度的变化情况。随着电解电流逐步上升,分析氯气的纯度,待产生的氯气合格后经氯氢处理工序送往用户,此时可关闭进气阀门。 5.2.2 氯化氢合成工序开车方案 27 5.2.2.1开车前的准备工作 (1)检修确认: 1)氯化氢合成由车间主任张斌及班长张志明确认检修项目是否全部按计划完成。 2)由杨鹏对吸收系统进行确认、艾飞对氯化氢合成系统进行确认、陈东对储罐系统进行确认。 3)检查检修项目的完成质量 (2)工艺确认: 1)检查控制仪表齐全完好,各阀门灵活好用,处于所规定的开启或关闭状态。 2)盘车检查各动设备是否灵活,各输送设备联轴器是否对中,点动试车,确认转向正确,润滑部位油量适宜,润滑良好。 3)检查水、电、蒸汽、氮气及仪表空气等公用工程是否达到工艺要求。 4)检查二合一合成炉,氯化氢冷却器,降膜吸收塔、尾气吸收塔、风机,等系统设备具备开车条件,并检查防爆膜是否完好。 5)检查本岗位所有设备、管道、阀门、仪表等是否完好,灵活好用,开停车连锁是否正常好用,连锁状态及连锁自动阀是否具备开车条件。 6)启动风机(BL701A-F),调整风量,检查负压是否正常。 5.2.2.2 氯化氢合成开车步骤 (1)吸收系统的确认 1)检查吸收水流量调节阀(FV-5455A-F)是否关闭,前后手动阀是否打开,旁通手动阀是否开启。 2) 检查尾气吸收塔顶部放空阀(HV-5466A-F)是否关闭,检查风机(BL-701A-F)气体进口调节阀(HV-5455A-F)前后手动阀是否打开旁通是否关闭。 27 3)检查盐酸调整罐(V-707)和高纯盐酸中间槽(V-708)进酸手动阀是否关闭。 4)检查一级降膜吸收器(T-701A-F)、二级降膜吸收器(T-702A-F)夹套循环水进出口阀门是否打开,并确认夹套内是否充满水。 5)检查吸收系统所有的排酸阀和取样阀是否关闭。 6)检查吸收系统所有压力检测点底阀是否打开。 (2)氯化氢合成系统确认 1)检查合成炉(R-701A-F)视镜是否干净且安装是否到位。 2)检查合成炉(R-701A-F)炉门垫子是否安装到位。 3)检查氯化氢合成炉(R-701A-F)冷却段循环水进出口阀是否打开,并确认氯化氢出口管线手动阀是否打开。并确认夹套内是否充满水。 4)检查氯化氢合成系统所有的压力测试点根部阀是否全部打开。 5)检查氯化氢合成系统所有排酸、排污、取样口阀门是否关闭。 6)检查氯化氢缓冲罐(V-701)、原氯缓冲罐(V-702)、氯气缓冲罐(V-703)、氢气缓冲罐(V-711)进出口手动阀门是否开启。 7)检查氯化氢一级冷却器(E-703A-B)冷冻水进出口阀门和氯化氢进出口阀门是否开启、氯化氢二级冷却器(E-704A-B)冷冻水进口手动阀门和出口阀门、氯化氢进出口阀门是否开启、氯化氢除雾器(N-701A-B)进出口阀门是否开启。 (3)储罐系统确认 1)检查盐酸调整罐(V-707)、冷凝酸罐(V-706)、高纯酸中间罐(V-708)、稀盐酸循环罐(V-705)上所有的人孔盲板全部封闭。 2)检查盐酸调整罐(V-707)、冷凝酸罐(V-706)、高纯酸中间罐(V-708)、稀盐酸循环罐(V-705)上所有的排酸和排污阀是否关闭。 3)检查盐酸调整罐(V-707)、冷凝酸罐(V-706)、高纯酸中间罐(V-708)、稀盐酸循环罐(V-705)、纯水罐(V-709)上所有液位计根部阀是否打开。 27 (4)置换方案: 由氢气分配台(V-552)送来的氮气进入氢气缓冲罐(V-711),然后打开出口手动阀进入氢气总管,通过放空阀(PV -5452) 置换氢气总管,置换15~20分钟后,待分析氮含氧小于0.5-1.0%,缓慢关小放空阀(PV -5452),将合成氢气总管压力保持在80-85kPa取样分析;尾氯和原氯进入合成氯气缓冲罐通过事故氯阀门HV-5460至事故氯置换系统并取样分析。 (5)点炉操作: 1)先打炉门,开启风机(BL-701A-F)给系统抽负压,检查系统抽负压情况。如抽负压良好,待抽空15-20分钟后,对合成炉炉内含氢进行分析(含氢≤0.5%)方可点炉。 2)当原料气体分析合格,氢气纯度大于98%,氯气度大于85%,系统设备均具备开车条件后。 3)开氢气、氯气总阀调试氢气量及合成炉负压,合格后点火人员站在上风口,点燃氢气,火焰控制在100-200mm长度左右,将胶管迅速套入灯头氢气管接头,用铁丝固定,室内操作人员根据火焰逐步调节,待炉内火焰为青白色时,关闭炉门,并按照比例逐步加大氯、氢流量。关闭炉门后即可停风机加吸收水调节盐酸。 4)点炉后氢气控制在500Nm³/h,氯气350Nm³/h停止加量合成炉开始升温,等到蒸汽压力为180kPa温度130℃左右将蒸汽并入系统逐步给合成炉加量。 5)主控及时分析氯化氢纯度,作好送气准备。 6) 接到调度送气通知后,打开氯化氢一、二级冷却器(E-703A-B)、 (E-704A-B)和除雾器(N-701)进出口阀门。 7)当氯化氢纯度合格、通知VCM工序及调度室送气,调节氯化氢总管温度。 5.2.3液氯工序开车方案 5.2.3.1 开车前的准备工作 27 (1)检修确认: 1)由车间主任任健及班长屈伟斌对整个液化系统在开车前进行试压试漏,并作气密性试验,每台设备在清理后,也必须试压试漏,方能投入生产。如需做水压试验,在试水压后,任何设备管道必须干燥,以防腐蚀。 2)由陈喜红对液化系统进行确认、张强对储槽进行确认、液氯包装人员对包装泵、真空泵进行确认。 (2)工艺确认: 1)检查本岗位所属管线、阀门、设备、电器及仪表是否完好,所有试压盲板是否已拆除;水、电、蒸汽、氮气、压缩空气及仪表空气等公用工程供应是否正常。 2)检查各动、静密封点是否泄漏,冷冻机组运行是否正常,压力是否在规定范围内,制冷剂液面有无变化。 3)检查液氯储槽、液氯包装泵是否完好并试压合格,压力表是否齐全完好。 4)确认所有泵的电机运转方向正确。 5)泵启动前,点动电机电源开关5秒左右,检查声音和振动有无异常。 6)纳氏泵P-609 加浓硫酸,液位达到气液分离器一半后关闭加酸阀。 5.2.3.2 开车操作步骤 在调度通知开车时间前1小时启动需要运转的螺杆压缩机进行空载 1)接到调度开车指令开启准备生产的液化器(E-601)氯气进口及尾气出口阀,气液分离器的液氯出口阀。 2)巡检人员检查液氯储槽下液阀及平衡阀是否开启。 3)当氯气纯度达90%(vol)以上时,得到调度室指令后,开启准备生产的液氯储槽上液氯进口、平衡出口阀,开启液氯气液分离器(V-602)上的尾气出口阀。 4)认真观察原料氯气、尾气的压力波动,调节压力,及时与调度联系。 27 5)当液氯储槽的液位达到50-80%时,开启液氯包装罐液氯进口阀及液氯储槽液氯出口阀,启动液氯泵,开启出口阀,并调节压力至规定值。将液氯送往包装。 5.3 成品车间 5.3.1蒸发工序开车方案 (1)启动纯水循环泵[P5610],启动真空泵[P5606] (2)打开进气阀,开始抽蒸汽冷凝器[E5604]、Ⅲ效蒸发罐[V5606]和总冷凝水罐[V5608]的真空;同时也能抽到Ⅲ效加热器[E5603]、Ⅱ效蒸发罐[V5605]和Ⅲ效冷凝水罐[V5603]的真空。 (3)当Ⅲ效蒸发罐[V5606]出口二次蒸汽真空度值达到8kPa后,可以向Ⅲ效蒸发罐进碱。 (4)将原液碱泵[P5607]电机频率调到5HZ左右,启动原液碱泵,缓慢打开原液碱泵出口阀[XV014或XV015],向Ⅲ效蒸发罐进液,通过调节泵电机频率使Ⅲ效蒸发罐进碱流量保持在35m3/h。 (5)当Ⅲ效蒸发罐[V5606]液位达到10%时,启动循环碱泵[P5608],向Ⅲ效加热器[E5603]送液,当Ⅲ效蒸发罐[V5606]液位达到20%时,启动Ⅲ效碱泵。 (6)打开Ⅱ效一段预热器碱出口阀[XV047]和Ⅱ效二段预热器碱出口阀[XV049]碱液进入Ⅱ效加热器[E5602]后,流入Ⅱ效蒸发罐[V5605],通过调节Ⅲ效碱泵电机频率使Ⅱ效蒸发罐进碱流量保持在35m3/h。 (7)当Ⅱ效蒸发罐液位达到20%时,启动Ⅱ效碱泵; (8)打开Ⅰ效一段预热器碱出口阀[XV067]和Ⅰ效二段预热器碱出口阀[XV069],碱液进入Ⅱ效加热器[E5602]后,流入向Ⅰ效蒸发器[V5604]加碱。 (9)当Ⅰ效蒸发器液位达到10%时,启动Ⅰ效碱泵,打开产品碱冷却器碱出口阀[XV091]和50%回流阀[XV095],让碱回流到原液碱槽[V5607],碱流量保持在35m3/h。 27 (10)通过调节将Ⅰ效蒸发罐[V5604]、Ⅱ效蒸发罐[V5605] 、Ⅲ效蒸发罐[V5606]的液位稳定后设置成自动控制。 (11)向Ⅰ效加热器送蒸汽,将Ⅰ效、Ⅱ效Ⅲ效加热器的不凝气排放阀打开5%,打开蒸汽总阀[ZV111、ZV112]。 (12)将调节阀[TV-0121]打开2%,开始向Ⅰ效加热器通入蒸汽。缓慢调节阀[TV-0121]的开度,保证蒸汽压力不得超过0.9MPa(表)。 (11)Ⅰ效冷凝水罐[V5601]内冷凝水液位上升到50%后,启动新冷凝水泵,打开出口阀[QV131、QV132],将冷凝水送出界区。 (12)缓慢打开Ⅰ效蒸汽冷凝水罐的液位调节阀[LV-0101],待液位平稳后,将调节阀[LV-0101]设置成自动。冷凝水将依次进入Ⅰ效二段预热器[E5606]、Ⅱ效二段预热器[E5608]、新冷凝水泵,最后从调节阀[LV-0101]经室外管网去锅炉。 (13)当Ⅰ效加热器[E5601]的压力达到0.8MPa后,将调节阀[TV-0121]设置成自动。 (14)将去罐区温度控制45[℃]以下。 (15)Ⅱ效冷凝水罐[V5602]内冷凝水液位上升到50%后,缓慢打开Ⅱ效蒸汽冷凝水罐的液位调节阀[LV-0102],待液位平稳后,将调节阀[LV-0102]设置成自动。这时Ⅱ效冷凝水罐[V5602]内冷凝水进入到Ⅲ效冷凝水罐[V5603]。 (16)Ⅲ效冷凝水罐[V5603]内冷凝水液位上升到50%后进入总冷凝水罐[V5608]。 (17)待总冷凝水罐液位上升到50%后,启动冷凝水泵[P5605],将冷凝水送出界区,并将冷凝水泵设为自动。 (18)打开减温器一[M5601]的进水阀[JV179]、减温器二[M5602]的进水阀[JV180] 、减温器三[M5603]的进水阀[JV181],将各效出口二次蒸汽的温度控制在饱和温度范围。 (19)Ⅰ效蒸发罐出料碱浓度达到50%时取样分析。 27 (20)碱浓度合格后,缓慢的打开通往罐区50%阀[XV093],然后缓慢关闭50%产品碱管道回流阀[XV095],50%产品碱将被送往罐区,然后将调节阀[FV-0103]设置为自动。 5.3.2固碱浓缩系统开车方案 (1)最终浓缩加热器进熔盐前6小时打开最终浓缩加热器、熔盐管道、闪蒸罐、分配器、碱液管道以及熔盐阀填料箱的伴热蒸汽进行系统的预热,前3小时将片碱机运行,包装系统进行检查。 (2)为了保证管道的密封,用水或蒸汽冷凝液填充预浓缩冷凝水罐,直到液位调节器(LT-0205、LT-0305)指示值显示50%,设定控制回路为自动运行,关闭控制阀。 (3)将预浓缩蒸发罐液位[LT-0204、LT-0304]设置为手动运行,液位[LT-0204、LT-0304]的设定值为20%左右。 (4)启动50碱泵,50%碱液进入预浓缩加热器,调节50%液碱的进料流量(FT-0201、FT-0301)为:10010kg/h。在糖溶解槽中将固态的糖和蒸汽冷凝水或纯水按比例进行配置充分溶解成满足工艺要求的5%糖溶液,打开阀门[XV420、XV620],5%糖溶液在重力作用下通过流量计计量后自流到预浓缩碱泵的进口管内。 (5)预浓缩蒸发罐液位高于15%,打开去预浓缩加热器的回流阀,启动预浓缩碱泵,使碱液在预浓缩加热器、预浓缩蒸发罐内本体循环。缓慢打开进最终浓缩加热器碱液调节阀 [FV0202、FV0203、FV0302、FV0303],通过调节保证流量保持在7910kg/h(约6.5m3/h),同时保持预浓缩蒸发罐液位在25%左右,并缓慢关闭去预浓缩加热器的循环阀并控制流量稳定。 (6)启动水环真空泵,启动正常10秒后慢慢的打开真空泵的进气阀[ZV426、ZV428、ZV626、ZV628],开始抽蒸汽冷凝器和预浓缩蒸发罐的真空,预浓缩蒸发罐的真空度达到88kPa时即为合格。 27 (7)设定61%碱液温度[TE-0206、TE-0306]为104℃。缓慢增加50%液碱的进料流量(FT-0201、FT-0301)流量值到要求的产量(14322.9kg/h),并设为自动控制。 (8)碱液从预浓缩蒸发罐底部出来依次进入闪蒸罐、分配管,最终进入片碱机,进片碱机前需观察熔融碱的进口温度是否升高。 (9)结片机转鼓浸入碱槽内10-20mm。结片机冷却用水是一个密闭的回路。通过冷却水换热器控制冷却水温度(TE-0267、TE-0367)为40℃,通过进片碱机冷却水流量计[FT-0205、FT-0206、FT-0207、FT-0208、FT-0305、FT-0306、FT-0307、FT-0308]控制冷却水的流量,使冷却水出结片机温度为49℃。 (10)为保护最终浓缩效的浓缩管的使用寿命,必须严格控制进入最终浓缩加热器的61%液碱流量不得小于满负荷的50%。 5.3.3熔盐系统开车方案 (1)向熔盐炉[F5631]燃烧室内放置足够的柴火,点燃柴火引燃炉排上的燃料。 (2)依次开启新冷凝水泵、鼓风机、刮板出渣机,调节烟道闸阀。 (3)先打开新冷凝水进蒸汽发生器自控阀前后手阀[QV815、QV816、QV915、QV916],然后打开调节阀[LV-0402、LV-0502]向热管式蒸汽发生器补水,并保液位在正常指标范围。 (4)手动启动炉排调速器,在正常燃烧的情况下必须要求炉排稳定运行。 (5)点火成功后进行熔盐炉的空管预热,设置内部盘管(TI0415、TI0418)和外部盘管(TI0414、TI0417)的温度分别为350℃和220℃,在燃料燃烧的过程中使熔盐炉内下盘管≥200℃,顶盘管≥200℃,外下盘管≥200℃,燃烧控制器通过自动定时器来控制熔盐炉的运行,预热熔盐炉的盘管温度到250-300℃,完成空管预热过程。 27 (6)所有的熔盐管线,包括熔盐阀都有中压蒸汽伴管,熔盐循环前,至少提前3天开通伴热蒸汽,使主管道温度达到最高[≥150℃]。打开熔盐回流阀,关闭浓缩和伴热熔盐阀,做好启动熔盐泵准备工作。 (7)检查熔盐泵,确认正常启动熔盐泵,无异常后慢慢打开回流阀,熔盐罐内的熔盐经熔盐泵加压后通过熔盐炉又回到熔盐罐。 (8)梯度升温期间设定温度值自动切换至220℃,运行温度为220℃±3℃。 (9)鼓风机变频器的频率自动设定为≤20Hz,燃烧系统进入到低负荷运行状态,此时燃烧系统最大的运行负荷只有总负荷的15%。 (10)熔盐炉内熔盐温度达到220℃后,温度设定值开始自动提高,温度设定值提高的速率为每2分钟1℃,运行温度为设定温度值的±3℃。关闭熔盐罐内电加热器、加热蒸汽及熔盐所经过的管道伴热蒸汽(熔盐阀密封垫处的蒸汽伴热常开),同时打开蒸汽伴管旁路阀排汽。 (11)熔盐温度在220~240℃时,开始进入最终浓缩加热器大循环。逐步关闭排放阀[JV809、JV909] ,同时打开到最终浓缩加热器的熔盐阀[JV810、JV811、JV910、JV911],熔盐罐内的熔盐经熔盐泵加压后通过熔盐炉、最终浓缩加热器又回到熔盐罐。这时需要关闭最终浓缩加热器的伴热蒸汽及熔盐所经过的管道伴热蒸汽(熔盐阀密封垫处的蒸汽伴热常开),同时打开蒸汽伴管旁路阀排汽。 (12)熔盐炉开始自动程序控制升温,由温控器程序控制以每小时30℃的速度逐渐升温至420℃。所有熔盐阀门密封垫处的蒸汽伴管,即使在熔盐高温操作时也不关闭。熔盐温度达到420℃时,熔盐升温阶段结束,最终浓缩加热器准备投料。 (13)正常操作中调节燃煤熔盐炉的进口熔盐阀门,控制熔盐炉内圈流速2.28m/s,外圈流速1.85m/s。 (14)通过变频控制鼓风机的运行频率,控制空气量在17500m3/h左右。 (15)通过变频控制引风机的运行频率,使炉膛呈负压状态,排烟量为32900m3/h。 27 27查看更多