- 2021-10-21 发布 |
- 37.5 KB |
- 1页
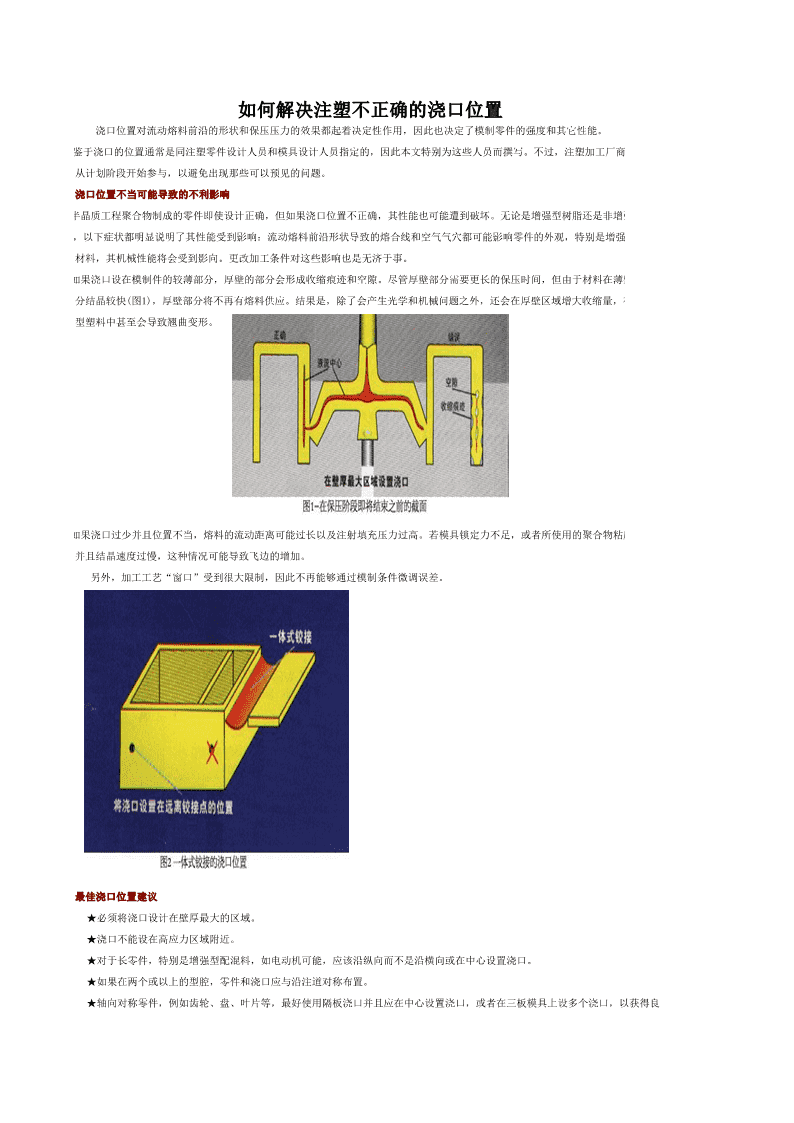
申明敬告: 本站不保证该用户上传的文档完整性,不预览、不比对内容而直接下载产生的反悔问题本站不予受理。
文档介绍
如何解决注塑不正确的浇口位置
如何解决注塑不正确的浇口位置 浇口位置对流动熔料前沿的形状和保压压力的效果都起着决定性作用,因此也决定了模制零件的强度和其它性能。 鉴于浇口的位置通常是同注塑零件设计人员和模具设计人员指定的,因此本文特别为这些人员而撰写。不过,注塑加工厂商也应 从计划阶段开始参与,以避免出现那些可以预见的问题。 浇口位置不当可能导致的不利影响 半晶质工程聚合物制成的零件即使设计正确,但如果浇口位置不正确,其性能也可能遭到破坏。无论是增强型树脂还是非增强型 树脂,以下症状都明显说明了其性能受到影响:流动熔料前沿形状导致的熔合线和空气气穴都可能影响零件的外观,特别是增强纤维 材料,其机械性能将会受到影向。更改加工条件对这些影响也是无济于事。 如果浇口设在模制件的较薄部分,厚壁的部分会形成收缩痕迹和空隙。尽管厚壁部分需要更长的保压时间,但由于材料在薄壁部 分结晶较快(图1),厚壁部分将不再有熔料供应。结果是,除了会产生光学和机械问题之外,还会在厚壁区域增大收缩量,在非增强 型塑料中甚至会导致翘曲变形。 如果浇口过少并且位置不当,熔料的流动距离可能过长以及注射填充压力过高。若模具锁定力不足,或者所使用的聚合物粘度低 并且结晶速度过慢,这种情况可能导致飞边的增加。 另外,加工工艺“窗口”受到很大限制,因此不再能够通过模制条件微调误差。 最佳浇口位置建议 ★必须将浇口设计在壁厚最大的区域。 ★浇口不能设在高应力区域附近。 ★对于长零件,特别是增强型配混料,如电动机可能,应该沿纵向而不是沿横向或在中心设置浇口。 ★如果在两个或以上的型腔,零件和浇口应与沿注道对称布置。 ★轴向对称零件,例如齿轮、盘、叶片等,最好使用隔板浇口并且应在中心设置浇口,或者在三板模具上设多个浇口,以获得良 好的实际流动特性。 ★有一体式铰接的零件在布置浇口时,应使熔合线远离铰接点。在任何情况下。都应避免将熔料停止流动部分设计在铰接点附近。 ★杯形零件(例如小壳体、电容器杯等)的浇口应设计在底座附近,以避免产生空气气穴。 ★对于管形零件,应使熔料首先填充一端的圆周,然后再填充管本身的全长部分。这样,可使熔料流动前沿避免产生不对称形状。 ★在塑孔栓、熔出型芯和其它金属镶嵌件周围镶嵌模塑时,熔化的树脂应能够在镶嵌件周围流动,以尽可能减少镶嵌件位置的不准确。 ★对于不可见缺陷(例如浇口痕迹)的外露表面,可以将浇口设在内部,用遂道式浇口供料至弹出销上。 ★在复杂的零件及具有不同形状的多型腔模具上,浇口位置应尽可能使熔料流动前沿在填充过程中避免产生短暂停止。 这些建议显然并不能函盖所有应用情况,在实际情况中总是要妥协以求得平衡,这取决于具体模制工艺的复杂程度。不过,应在 计划阶段就尽可能深入地考虑我们的上述建议。模拟模具填充试验对该情况极为有帮助,应尽可能采用。 技術專欄: 塑膠機類 射膠螺桿簡介與影響塑化品質之主要因素 射膠螺桿之功能: 加料、輸送、壓縮、熔化、排氣、均化 螺桿之重要幾何尺寸: 螺桿直徑、進料段、壓縮段、計量段、進料牙深、 計量牙深: 螺桿直徑(D) 與所要求之射出容積相關 射出容積 = 1/4π‧D2‧(射出行程)‧0.85 一般而言,D2與最高射出壓力成反比 D愈大,押出率愈大;Q ≒ 1.29D2HmNr‧60/1000 (kg/ Hr) 入料段: ‧ 負責塑料的輸送、推擠與預熱 ‧ 應保証入料段結束時開始熔融,預熱到熔點。 ‧固態比熱↑、熔點↑、潛熱↑,加熱到熔點需熱多,入料段應長固態熱傳導係數↓,傳熱慢 、塑料中心溫升慢,入料段應長預 熱↑, 入料段可短。 ‧結晶性料最長(如:POM、PA);非晶性料次之(如:PS、PU);熱敏性最短(如:PVC)。 壓縮段: ‧負責塑料的混鍊、壓縮與加壓排氣,通過這一段的原料應該已經幾乎全部熔解,但是不一定會均勻混合。 ‧在此區域,塑料逐漸熔融,螺槽體積必須相應下降,否則料壓不實、傳熱慢、排氣不良。 ‧對非晶性塑料,壓縮段應長一些,否則若螺槽體積下降快,料體積未減少,會產生堵塞。 ‧結晶型塑料實際上非全部結晶(如 PE:40~90%結晶度,LDPE: 65%結晶度),因此目前壓縮段有加長的趨勢。 ‧一般佔25%螺桿工作長度。 ‧尼龍(結晶性料)2~3圈,約佔15%螺桿的工作長度。 ‧高黏度、耐火性、低傳導性、高添加物,佔40%~50%螺桿的工作長度。 ‧PVC可利用佔100%螺桿的工作長度,以避免激 烈的剪切熱。 計量段: ‧理論上到計量段之開始點,料應全部熔融,但至 少要計量段 = 4D,以確保溫度均勻、混鍊均勻。 ‧計量段長,則混鍊效果佳;計量段太長則易使熔 體停留過久,而產生熱分解;太短則易使溫度不均勻。 ‧一般佔20~25%螺桿工作長度。 ‧PVC熱敏性,不宜停留過長,以免熱分解(可不要計量段)。 進料牙深、計量牙深: ‧進料牙深愈深,在進料區之輸送量愈大,但需考慮螺桿強度。 ‧計量牙深愈淺,塑化之發熱、混合性能指數愈高,但需防範塑料燒焦,(計量牙深太淺,則剪切熱↑,自生熱↑,溫升太高,尤 其不利於熱敏性塑料。) ‧計量牙深 = KD = (0.03~0.07)D- D ↑,K 選小; D↓,細長比 ↑,熱穩定性差之塑料,K 選大 影響塑化品質之主要因素: 細長比、壓縮比、背壓、螺桿轉速、電熱溫度設定。 細長比: ‧細長比=螺桿工作長度/螺桿直徑。 ‧細長比大,則吃料易均勻,但容易過火。 ‧熱穩定性較佳之塑料可用較長之螺桿,以提高混鍊性而不慮燒焦;熱穩定性較差之塑料,可用較短之螺桿或螺桿尾端無螺紋。 ‧以塑料特性考量,一般細長比如下: 塑 料 特 性 細長比 熱固性 14~16 硬質PVC、高黏度 PU等熱敏性 17~18 一般塑料 18~22 PC、POM等高溫穩 定性塑料 22~24 ‧以混色能力考量,一般細長比如下 細長比 混色能力 12~16 以染好顏色之膠粒成型為 宜,避免色差發生。 16~18 以色母在料管內混鍊、染色 、成型品質均勻,色差不良 較小。 20~24 用色料在料管內混鍊染色、 分散性均勻,對成品物性有 較佳的保護作用。 壓縮比: ‧壓縮比=進料牙深/計量牙深 ‧考慮料的壓縮性、裝填程度、回流、製品要密實、傳熱與排氣。 ‧適當的壓縮比,可增加塑料之密度,使分子與分子之 ‧間結合更加緊密,有助於減少空氣的吸入,降低因壓力而產生之溫升,而影響輸出量的差異,而不適當之壓縮比將會破壞塑膠的物性。 ‧壓縮比值越高,對塑料在料管內塑化過程中產生的溫升越高,對膠化中的塑料產生較佳的混鍊均勻度,相對的出料量大為減少。 ‧高壓縮比適於不易熔塑料,特別具低熔化黏度、熱安定性塑料。 ‧低壓縮比適於易熔塑料,特別具高熔化黏度性,熱敏性塑料。 背壓: ‧增加背壓可增加螺桿對熔融樹脂所做的功、消除未熔的塑膠顆粒、增加料管內原料密度及其均勻程度、減少射出收壓和翹曲等問題。 ‧背壓被運用來提高料管溫度,其效果最為顯著。 ‧背壓過大,對熱敏性較高的塑料易分解;對低黏度的塑料可能會產生"流鼻"現象。 ‧背壓太小,射出的成品可能會有氣泡。 螺桿轉速: ‧螺桿的轉動速度直接影響塑料在螺旋槽內的切變。 ‧小型螺桿槽深較淺,吸收熱源快速,足夠促使塑料在壓縮段時軟化,螺桿與料管璧間的磨擦熱能較低,適宜高速旋轉,增加塑化能力。 ‧大型螺桿則不易快速旋轉,以免塑化不均及造成過度摩擦熱。 ‧對熱敏性較高的塑料,射膠螺絲轉速過大的話,塑料便會很容易被分解。 ‧通常各尺寸之螺桿有一定之轉速範圍,一般轉速 100~150 rpm太低,則無法熔化塑膠;太高,則將塑料燒焦。 ‧目前最大表面速度1m/sec為限,對剪切敏感材料,低於0.5m/sec。 電熱溫度設定: ‧使滯留於料管及螺桿內之冷硬樹脂熔融以利螺桿之轉動,提供樹脂獲得熔融所需的一部份熱量。 ‧設定比熔膠溫度低5~10℃(部份由摩擦熱能提供) ‧噴嘴溫度的調整也可用來控制流涕、凝固(塞頭)、牽絲等問題。 ‧結晶性塑料一般溫度控制: 塑料種類 料管溫度℃ 噴出料管溫度℃ 射出壓力Kg/cm2 HDPE 210℃後降溫呈180 ℃操作 200~220 500~1,500 PP 200~270 210~280 400~1,000 PA6 225~280 240~280 700~1,000 PA6/6 260~280 270~310 600~1,500 DELRIN 180~200 190~220 800~1,100 鳩拉康 220~270 230~280 400~1,000 ‧非結晶塑料: 塑料種類 料管溫度℃ 噴出料管溫度℃ 射出壓力Kg/cm2 PS 180~240 190~260 400~1,300 ABS 200~230 200~240 800~1,500 PMMA 180~220 200~230 700~1,500 PC 260~310 280~320 800~1,500 變性PPO 240~280 250~300 850~1,400 硬質PVC 165~185 175~195 1,000~1,500 註一:以上均是以不添加玻璃纖維的非強化塑膠為標準。 註二:管內之熔膠溫度通常高於管外控制的溫度,從噴嘴出料溫示之。 一般塑料性質與成型作業之關係: PE料: 屬流動性良好、熱安定性佳的塑料,但分子配性強容易變形,高密度PE料有明顯的結晶化溫度,最好增大射出 速度。對厚肉製 品而言,增快射出速度尤為重要:可改良製品的表面光澤、防止翹曲、減少成型收縮率等。因此,螺桿設計及止逆配備尤需精密,若 有損耗及傷痕, 加料時會產生漸慢現象。(因塑料逆流而產生射入模具的量減少,熔料倒迴於計量部,使進料段的新料 滯留,造成 新陳代謝失效,因而形成成型品品質不堅實,縮水度強,不良率高的現象。) PP料: 屬流動性良好塑料,近似PE料。PP料從280℃附近會開始劣化,所以加熱溫度宜在270℃以下操作,其分子配向性很強,在低溫成 型時,易因分子配向而翹曲及扭曲,宜注意。 PA料: 俗稱尼龍料,其黏度對加熱溫度敏感性高,亦是吸濕性大的塑料,所以射出溫度及乾燥溫度須高。塑料在未達乾燥程度絕對不可 放入熔膠筒內,因帶水份很強而易於卡住在加料段的桿槽裡,形成入料困難的現象。成形時,在射嘴處最易冷卻,倘在冷卻時增大射 出壓力操作,易致使止逆閥破裂,所以射嘴處之溫度控制必須適當。為防止塑料因加料溢入模具,宜用有控制性的射嘴。 在換用其他 塑料進行射出時,應注意原尼龍加熱溫度是270℃以上,而一般料加熱溫度只在200℃左右即行運作,因此必須加熱融膠筒至尼龍加 熱溫度後再行運作,否則易使螺桿之止逆閥與分膠頭折斷。因尼龍料屬高溫時流動性佳的塑料,本身不易熔解,熔解後又易冷卻凝固 ,必須注意成型方法方能產生良好效果。 POM料: 俗稱塑膠鋼,易起熱分解,宜注意成型時的溫度管理,POM料不可在熔膠筒內滯留過長時間,否則易過火、黃色化。熔化後的氣 體很濃,射嘴及法蘭的各部接觸點最易腐蝕,宜用好的材質。 PBT料: 和PET同屬飽和性聚酯類,具熔融度高、成型性良好、結晶性迅速、固化速度快的特性。熔膠筒溫度宜控制在230℃~270℃,模溫 宜設定在40℃~90℃。欲得光澤良好的表面時,宜昇溫,必要時需進行充分的預備乾燥。所需射出壓力約在500~1300kg/m2 。 PS、AS、ABS一般料: 屬乙烯類,乃一般普通料,這些料較易成型。唯ABS常用於鍍金品,其注意事項如下: (1) 熔膠管溫度宜高,約220℃~250℃; (2) 射出溫度宜慢(用二次加壓法)、射出壓力宜低; (3) 不可用離模劑; (4) 不可有收縮下陷及熔接線之流痕; (5) 成品表面不可有創痕。 PC料: 此料熔融黏度高,射出壓力大,管內溫度過高或滯留時間久時,易起熱分解、變色及降低物性,須注意模溫以85℃~120℃為準。對 厚的成品尤其不易成型,因成品易生殘留應力,會造成日後破裂,因此宜用粉末狀的矽利康作離模劑,勿用液狀離模劑。 PMMA料: 俗稱壓克力料,此料特性是韌性強、料流不良,宜在低溫成型。轉速宜慢,使管內不起溫昇。設計模具時宜加大澆道、應加大射 嘴孔。壓克力成型屬技術性加工成型,操作時須闢淨室以隔離灰塵、漏斗宜清潔、取模宜輕巧、帶白手套等以保持乾淨。 硬質PVC料: 此料最易燒焦、產生酸性氣體,所以管內溫度宜取170℃-l90℃加熱,應避免 200℃以上高溫加熱,模溫取50 ℃-60 ℃。塑料滯 留時間宜短,以最慢轉加料法使管內不昇溫度,以慢射出法使氣體可排出於模體。模具排氣孔宜大,螺桿需加電鍍、不必用止逆裝置、 射嘴孔應加大、每次需射到底,使不含滯料在管內。停止操作時,須把溫度慢慢降低,一直操作至不良成品時促使內部滯料全部射 出。 含玻璃纖維的塑料: 含玻纖塑料的流動性低於非強化樹酯,所以常增加熔膠筒加熱溫度與模溫及射出壓力等以方便成形。同時模具的澆口、橫澆道、 澆口等的尺寸,也須大於一般塑料。成型收縮率甚小於非強化樹酯,呈方向性的流動,所以澆口方向宜設法減少配向所致 的不良影響 。成型品的結合線強度常低於其他部份,在設計製品模具時需加注意,宜於熔接處增設排氣孔,使不致包風。模具各部份 (特別是澆 口部)或螺桿組件,熔膠管等磨耗很快,宜注意材質及表面的硬度處理。查看更多