- 2021-10-20 发布 |
- 37.5 KB |
- 32页
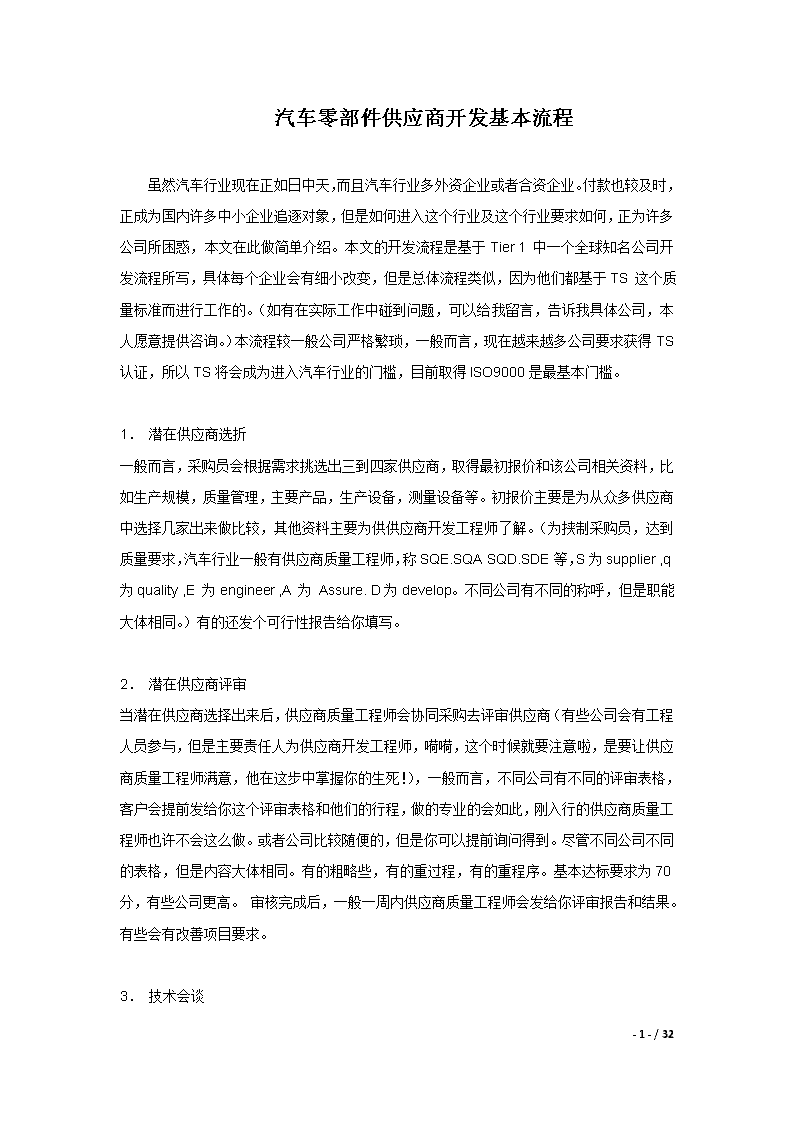
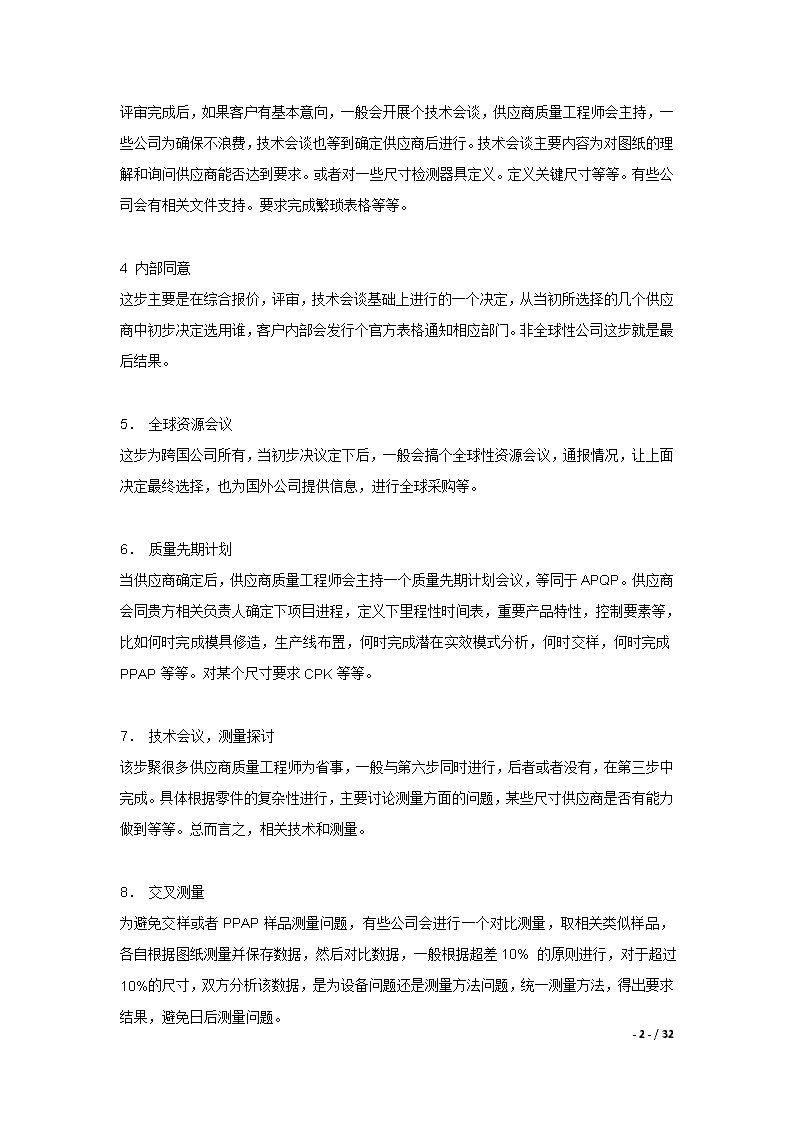
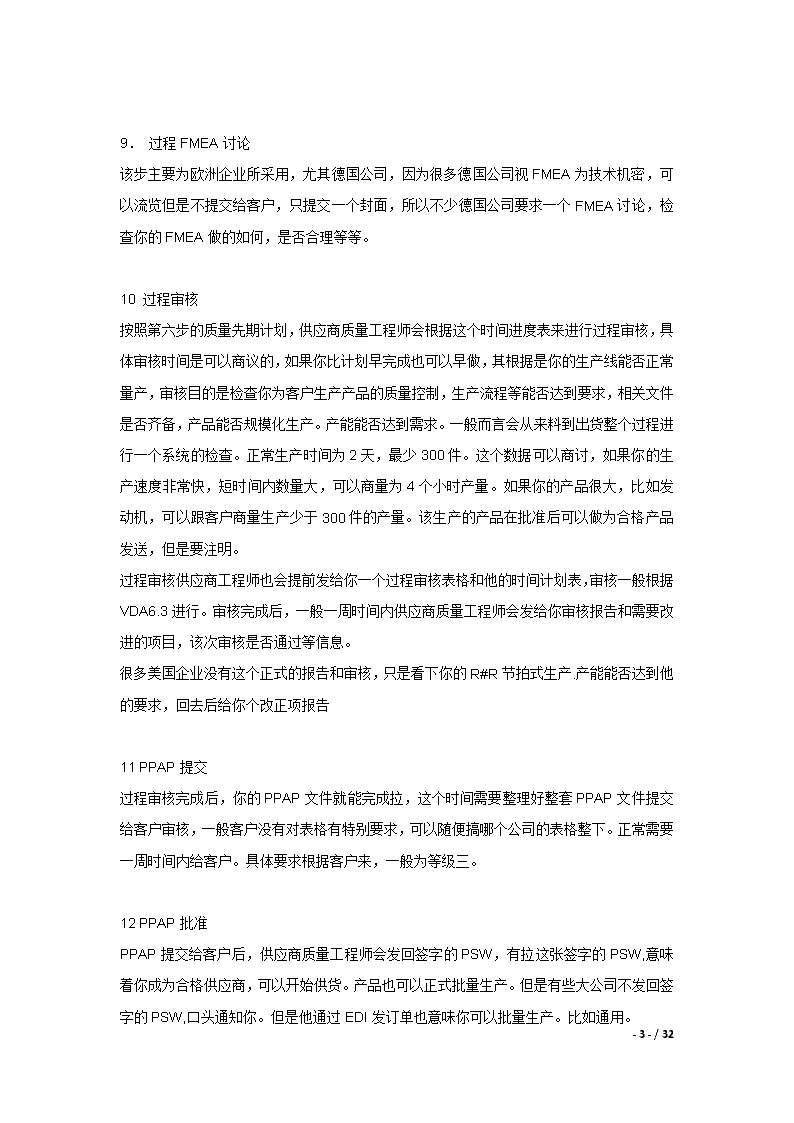
申明敬告: 本站不保证该用户上传的文档完整性,不预览、不比对内容而直接下载产生的反悔问题本站不予受理。
文档介绍
汽车零部件供应商开发基本流程(_完整版)
汽车零部件供应商开发基本流程 虽然汽车行业现在正如日中天,而且汽车行业多外资企业或者合资企业。付款也较及时,正成为国内许多中小企业追逐对象,但是如何进入这个行业及这个行业要求如何,正为许多公司所困惑,本文在此做简单介绍。本文的开发流程是基于Tier 1 中一个全球知名公司开发流程所写,具体每个企业会有细小改变,但是总体流程类似,因为他们都基于TS 这个质量标准而进行工作的。(如有在实际工作中碰到问题,可以给我留言,告诉我具体公司,本人愿意提供咨询。)本流程较一般公司严格繁琐,一般而言,现在越来越多公司要求获得TS认证,所以TS将会成为进入汽车行业的门槛,目前取得ISO9000是最基本门槛。 1. 潜在供应商选折 一般而言,采购员会根据需求挑选出三到四家供应商,取得最初报价和该公司相关资料,比如生产规模,质量管理,主要产品,生产设备,测量设备等。初报价主要是为从众多供应商中选择几家出来做比较,其他资料主要为供供应商开发工程师了解。(为挟制采购员,达到质量要求,汽车行业一般有供应商质量工程师,称SQE.SQA SQD.SDE等,S为supplier ,q为quality ,E 为engineer ,A 为 Assure. D为develop。不同公司有不同的称呼,但是职能大体相同。)有的还发个可行性报告给你填写。 2. 潜在供应商评审 当潜在供应商选择出来后,供应商质量工程师会协同采购去评审供应商(有些公司会有工程人员参与,但是主要责任人为供应商开发工程师,嗬嗬,这个时候就要注意啦,是要让供应商质量工程师满意,他在这步中掌握你的生死!),一般而言,不同公司有不同的评审表格,客户会提前发给你这个评审表格和他们的行程,做的专业的会如此,刚入行的供应商质量工程师也许不会这么做。或者公司比较随便的,但是你可以提前询问得到。尽管不同公司不同的表格,但是内容大体相同。有的粗略些,有的重过程,有的重程序。基本达标要求为70分,有些公司更高。 审核完成后,一般一周内供应商质量工程师会发给你评审报告和结果。有些会有改善项目要求。 3. 技术会谈 - 32 - / 32 评审完成后,如果客户有基本意向,一般会开展个技术会谈,供应商质量工程师会主持,一些公司为确保不浪费,技术会谈也等到确定供应商后进行。技术会谈主要内容为对图纸的理解和询问供应商能否达到要求。或者对一些尺寸检测器具定义。定义关键尺寸等等。有些公司会有相关文件支持。要求完成繁琐表格等等。 4 内部同意 这步主要是在综合报价,评审,技术会谈基础上进行的一个决定,从当初所选择的几个供应商中初步决定选用谁,客户内部会发行个官方表格通知相应部门。非全球性公司这步就是最后结果。 5. 全球资源会议 这步为跨国公司所有,当初步决议定下后,一般会搞个全球性资源会议,通报情况,让上面决定最终选择,也为国外公司提供信息,进行全球采购等。 6. 质量先期计划 当供应商确定后,供应商质量工程师会主持一个质量先期计划会议,等同于APQP。供应商会同贵方相关负责人确定下项目进程,定义下里程性时间表,重要产品特性,控制要素等,比如何时完成模具修造,生产线布置,何时完成潜在实效模式分析,何时交样,何时完成PPAP等等。对某个尺寸要求CPK等等。 7. 技术会议,测量探讨 该步聚很多供应商质量工程师为省事,一般与第六步同时进行,后者或者没有,在第三步中完成。具体根据零件的复杂性进行,主要讨论测量方面的问题,某些尺寸供应商是否有能力做到等等。总而言之,相关技术和测量。 8. 交叉测量 为避免交样或者PPAP样品测量问题,有些公司会进行一个对比测量,取相关类似样品,各自根据图纸测量并保存数据,然后对比数据,一般根据超差10% 的原则进行,对于超过10%的尺寸,双方分析该数据,是为设备问题还是测量方法问题,统一测量方法,得出要求结果,避免日后测量问题。 - 32 - / 32 9. 过程FMEA讨论 该步主要为欧洲企业所采用,尤其德国公司,因为很多德国公司视FMEA为技术机密,可以流览但是不提交给客户,只提交一个封面,所以不少德国公司要求一个FMEA讨论,检查你的FMEA做的如何,是否合理等等。 10 过程审核 按照第六步的质量先期计划,供应商质量工程师会根据这个时间进度表来进行过程审核,具体审核时间是可以商议的,如果你比计划早完成也可以早做,其根据是你的生产线能否正常量产,审核目的是检查你为客户生产产品的质量控制,生产流程等能否达到要求,相关文件是否齐备,产品能否规模化生产。产能能否达到需求。一般而言会从来料到出货整个过程进行一个系统的检查。正常生产时间为2天,最少300件。这个数据可以商讨,如果你的生产速度非常快,短时间内数量大,可以商量为4个小时产量。如果你的产品很大,比如发动机,可以跟客户商量生产少于300件的产量。该生产的产品在批准后可以做为合格产品发送,但是要注明。 过程审核供应商工程师也会提前发给你一个过程审核表格和他的时间计划表,审核一般根据VDA6.3进行。审核完成后,一般一周时间内供应商质量工程师会发给你审核报告和需要改进的项目,该次审核是否通过等信息。 很多美国企业没有这个正式的报告和审核,只是看下你的R#R节拍式生产.产能能否达到他的要求,回去后给你个改正项报告 11 PPAP提交 过程审核完成后,你的PPAP文件就能完成拉,这个时间需要整理好整套PPAP文件提交给客户审核,一般客户没有对表格有特别要求,可以随便搞哪个公司的表格整下。正常需要一周时间内给客户。具体要求根据客户来,一般为等级三。 12 PPAP批准 PPAP提交给客户后,供应商质量工程师会发回签字的PSW,有拉这张签字的PSW,意味着你成为合格供应商,可以开始供货。产品也可以正式批量生产。但是有些大公司不发回签字的PSW,口头通知你。但是他通过EDI发订单也意味你可以批量生产。比如通用。 - 32 - / 32 13 爬坡活动 RAM UP PLAN 有些公司在PPAP批准后,会有一个爬坡活动,也就是质量控制方面逐步放宽,三个月或者更长时间后才为批量生产,质量控制也可以放宽。正常状态下,PPAP 批准后仍然为试生产,三个月没有问题后直接转为批量生产,控制计划需要从试生产状态转为生产状态。很少公司有如此细节要求。 14 年度审核 正式量产后,如果没有新的项目,很多公司会有个年度审核,供应商质量工程师主导进行。一般采用过程审核的表格。如果有新项目,不少公司会取消年度审核。 15 8D 检查 在正式量产过程中,如果大的质量问题,供应商工程师在要求8D后会有个8D验证。对该问题进行检查,是否达到要求。 有些公司也只要求8D而非有正式的8D验证。 APQP=Advanced Product Quality Planning 中文意思是:产品质量先期策划(或者产品质量先期策划和控制计划)是QS9000/TS16949质量管理体系的一部分。 定义及其他知识点: 产品质量策划是一种结构化的方法,用来确定和制定确保某产品使顾客满意所需的步骤。 产品质量策划的目标是促进与所涉及每一个人的联系,以确保所要求的步骤按时完成。 有效的产品质量策划依赖于高层管理者对努力达到使顾客满意这一宗旨的承诺。 理解要点 · 结构化、系统化的方法; · 确保使产品满足顾客的需要和期望; · 团队的努力,(横向职能小组是重要方法); · 从产品的概念设计、设计开发、过程开发、试生产到生产,以及全过程中的信息反馈、纠正措施和持续改进活动; · 不断采取防错措施降低产品风险(见“8.APQP与防错”); - 32 - / 32 · 持续改进; · 制定必要的程序、标准和控制方法; · 控制计划是重要的输出; · 制定、实施时间表。 APQP的益处 —引导资源,使顾客满意; —促进对所有更改的早期识别; —避免晚期更改; —以最低的成本、及时提供优质产品。 APQP的基础 1 组织小组 ·横向职能小组是APQP实施的组织; ·小组需授权(确定职责); ·小组成员可包括:技术、制造、材料控制、采购、质量、销售、现场服务、供方、顾客的代表。 2 确定范围 具体内容包括: ·确定小组负责人; ·确定各成员职责; ·确定内、外部顾客; ·确定顾客要求; ·理解顾客要求和期望; ·评定所提出的设计、性能要求和制造过程的可行性; ·确定成本、进度和限制条件; ·确定需要的来自顾客的帮助; ·确定文件化过程和形式。 3 小组间的联系 · 顾客、内部、组织及小组内的子组之间; · 联系方式可以是举行定期会议,联系的程度根据需要。 4 培训 - 32 - / 32 ·APQP成功取决于有效的培训计划; ·培训的内容:了解顾客的需要、全部满足顾客需要和期望的开发技能,例如:顾客的要求和期望、Working as a team 、开发技术、APQP、FMEA、PPAP等。 5 顾客和组织参与 · 主要顾客可以和一个组织开始质量策划过程; ·组织有义务建立横向职能小组管理APQP; ·组织必须同样要求其供方。 6 同步工程 ·同步工程:横向职能小组同步进行产品开发和过程开发,以保证可制造性、装配性并缩短开发同期,降低开发成本; 理解要点 · 同步技术是横向职能小组为一共同目标努力的过程; · 取代以往逐级转递的方法; · 目的是尽早使高质量产品实现生产; · 小组保证其他领域/小组的计划和活动支持共同的目标; · 同步工程的支持性技术举例; —网络技术和数据交换等相关技术; —DFX技术; —QFD; —此外,同步工程还大量用到田口方法、FMEA和SPC等技术。 7 控制计划 控制计划—控制零件和过程的系统的书面描述。每个控制计划包括三个阶段; ·样件——对发生在样件制造过程中的尺寸测量、材料与性能试验的描述; ·试生产——对发生在样件之后,全面生产之前的制造过程中的尺寸测量、材料和性能试验的描述; ·生产——对发生在批量生产过程中的产品/过程特性、过程控制、试验和测量系统的综合描述。 8 问题的解决 ·APQP的过程是解决问题的过程; ·解决问题可用职责—时间矩阵表形成文件; - 32 - / 32 ·遇到困难情况下,推荐使用论证的问题—解决方法; ·可使用附录B中的分析技术。 9 产品质量先期策划的时间计划 ·APQP小组在完成组织活后的第一件工作—制定时间计划; ·考虑时间计划的因素—产品类型、复杂性和顾客的期望; ·小组成员应取得一致意见; ·时间计划图表应列出—任务、职责分配及其它有关事项(参照附录B关键路径法): ·供策划小组跟踪进度和设定会议日期的统一格式; ·每项任务应有起始日期、预计完成时间,并记录实际情况; ·把焦点集中于确认要求特殊注意的项目,通过有效的状况报告活动支持对进度的监控。 10 与时间计划图表有关的计划 ·项目的成功依赖于——以及时和价有所值方式; ·APQP时间表和PDCA循环要求APQP小组竭尽全力于预防缺陷。APQP的过程是采取防错措施,不断降低产品风险的过程; ·缺陷预防——由产品设计和制造技术的同步工程推进; ·策划小组应准备修改产品策划计划以满足顾客期望; ·策划小组的责任——确保进度满足或提前于顾客的进度计划。 APQP进度图 ·五个过程; ·五个里程碑; ·前一个过程的输出是后一个过程的输入; ·各个过程在时间上重叠,体现同步工程; ·“反馈、评定和纠正措施”过程贯穿始终; ·一个策划循环的结束,另一个策划循环的开始; 时间进度表的一种常见形式——甘特图 甘特图举例 任务 时间进度 1月 2月 3月 4月5月 6月 7月 8月9月 10月 11月12月 计划与定义 产品设计与开发 - 32 - / 32 过程设计与开发 产品与过程确认 反馈、评定和纠正措施 ·关键路径法:在甘特图上以粗线表示需要最长时间完成的任务;同时以细线表示需并进行的任务子项,以提供以下重要的信息: ——各项任务之间的关系 ——明确责任 ——对问题及早预测 ——资源分配 产品质量策划循环 ·是著名的戴明PDCA质量循环概念在产品质量策划中的应用; ·持续改进是APQP循环的要点; ·APQP是QS—9000系统中不可或缺的重要子系统; ·APQP子系统中还包含其它许多系统,如FMEA,控制计划。 APQP的五个过程 1 计划和定义 本过程的任务: ·如何确定顾客的需要和期望,以计划和定义质量大纲; ·做一切工作必须把顾客牢记心上; ·确认顾客的需要和期望已经十分清楚。 2 产品的设计与开发 本过程的任务和要点: ·讨论将设计特征发展到最终形式的质量策划过程诸要素; ·小组应考虑所有的设计要素,即使设计是顾客所有或双方共有; ·步骤中包括样件制造以验证产品或服务满足“服务的呼声”的任务; ·一个可行的设计应能满足生产量和工期要求,也要考虑质量、可靠性、投资成本、重量、单件成本和时间目标; ·尽管可行性研究和控制计划主要基于工程图纸和规范要求,但是本章所述的分析工具也能猎取有价值的信息以进一步确定和优先考虑可能需要特殊的产品和过程控制的特性; ·保证对技术要求和有关技术资料的全面、严格的评审; - 32 - / 32 ·进行初始可行性分析,以评审制造过程可能发生的潜在问题。 3 过程设计和开发 本过程的任务和要点: —保证开发一个有效的制造系统,保证满足顾客的需要、要求和期望; —讨论为获得优质产品而建立的制造系统的主要特点及与其有关的控制计划。 4 产品和过程的确认 本过程的任务和要点: —讨论通过试生产运行评价对制造过程进行验证的主要要点。 —应验证是否遵循控制计划和过程流程图,产品是否满足顾客的要求。 并应注意正式生产前有关问题的研究和解决。 5 反馈、评定和纠正措施 本过程的任务与要点: —质量策划不因过程确认就绪而停止,在制造阶段,所有变差的特殊原因和普通原因都会表现出来,我们可以对输出进行评价,也是对质量策划工作有效性进行评价的时候。 —在此阶段,生产控制计划是用来评价产品和服务的基础。 —应对计量型和计数型数据进行评估。采取SPC手册中所描述的适当的措施。 ppap=Production part approval process生产件批准程序 ppap生产件提交保证书:主要有生产件尺寸检验报告,外观检验报告,功能检验报告,材料检验报告; 外加一些零件控制方法和供应商控制方法;主要是制造形企业要求供应商在提交产品时做ppap文件及首件,只有当ppap文件全部合格后才能提交;当工程变更后还须提交报告。 ppap是对生产件的控制程序,也是对质量的一种管理方法。 FMEA=Failure Mode and Effects Analysis失效模式与影响分析或潜在失效模式与后果分析 - 32 - / 32 在设计和制造产品时,通常有三道控制缺陷的防线:避免或消除故障起因、预先确定或检测故障、减少故障的影响和后果。FMEA正是帮助我们从第一道防线就将缺陷消灭在摇篮之中的有效工具。 FMEA是一种可靠性设计的重要方法。它实际上是FMA(故障模式分析)和FEA(故障影响分析)的组合。它对各种可能的风险进行评价、分析,以便在现有技术的基础上消除这些风险或将这些风险减小到可接受的水平。及时性是成功实施FMEA的最重要因素之一,它是一个“事前的行为”,而不是“事后的行为”。为达到最佳效益,FMEA必须在故障模式被纳入产品之前进行。 FMEA实际是一组系列化的活动,其过程包括:找出产品/过程中潜在的故障模式;根据相应的评价体系对找出的潜在故障模式进行风险量化评估;列出故障起因/机理,寻找预防或改进措施。 由于产品故障可能与设计、制造过程、使用、承包商/供应商以及服务有关,因此FMEA又细分为: DFMEA:设计FMEA PFMEA:过程FMEA EFMEA:设备FMEA SFMEA:体系FMEA 8D 的原名叫做 8 Disciplines,意思是8 个人人皆知解决问题的固定步骤。原始是由Ford 公司,全球化品质管制及改善的特殊必备方法,之後已成为QS9000/ ISO TS16949、福特公司的特殊要求。凡是做 FORD 的零件,必需采用 8D 作为品质改善的工具,目前有些企业并非 FORD 的供应商或汽车业的合作夥伴,也很喜欢用这个方便而有效的方法解决品质问题,成为一个固定而有共识的标准化问题解决步骤。 Discipline 1. 成立改善小组(Form the Team):由议题之相关人员组成,通常是跨功能性的,说明团队成员间的彼此分工方式或担任的责任与角色。 Discipline 2. 描述问题(Describe the Problem):将问题尽可能量化而清楚地表达,并能解决中长期的问题而不是只有眼前的问题。 Discipline 3. 实施及确认暂时性的对策(Contain the Problem):对於解决 D2 之立即而短期行动,避免问题扩大或持续恶化,包含清库存、缩短PM时间、加派人力等。 Discipline 4. 原因分析及验证真因(Identify the Root Cause):发生 D2 问题的真正原因、说明分析方法、使用工具(品质工具)的应用。 Discipline 5. 选定及确认长期改善行动效果(Formulate and Verify Corrective - 32 - / 32 Actions):拟订改善计画、列出可能解决方案、选定与执行长期对策、验证改善措施,清除 D4 发生的真正原因,通常以一个步骤一个步骤的方式说明长期改善对策, 可以应用专案计画甘特图(Gantt Chart),并说明品质手法的应用。 Discipline 6. 改善问题并确认最终效果(Correct the Problem and Confirm the Effects):执行 D5 後的结果与成效验证。 Discipline 7. 预防再发生及标准化(Prevent the Problem):确保 D4 问题不会再次发生的後续行动方案,如人员教育训练、改善案例分享(Fan out) 、作业标准化、产出BKM、执行FCN 、分享知识和经验等。 Discipline 8. 恭禧小组及规划未来方向(Congratulate the Team):若上述步骤完成後问题已改善,肯定改善小组的努力,并规划未来改善方向。 Abbr. Full name Chinese name Remark PPAP Production Part Approval Process 生产件批准程序 FMEA Failure Modes and Effects Analysis 失效模式与影响分析 FMA Failure Modes Analysis 故障模式分析 FEA Failure Effects Analysis 故障影响分析 - 32 - / 32 DFMEA Design Failure Modes and Effects Analysis 设计FMEA PFMEA Process Failure Modes and Effects Analysis 过程FMEA EFMEA Equipment Failure Modes and Effects Analysis 设备FMEA SFMEA System Failure Modes and Effects Analysis 体系FMEA SQE Supplier Quality Engineer 供应商质量工程师 SQD Supplier Quality Develop 供应商质量工程师 SQA Supplier Quality Assure 供应商质量工程师 SDE Supplier Develop Engineer 供应商质量工程师 - 32 - / 32 APQP Advanced Product Quality Planning 产品质量先期策划 CPK Process Capability index 工艺能力指数 工序在一定时间里,处于控制状态(稳定状态)下的实际加工能力。 TS Technical Specification TS16949 VDA Verband der Automobilindustrie 德国汽车工业联合会 德国汽车工业联合会(VDA)制定的德国汽车工业质量标准的第一部分,即有形产品的质量管理体系审核,简称VDA6.1。该标准以ISO 9001为基础,适当增加了来自汽车工业实践的特殊要求。 PSW Part Submission Warrant 零件提交保证书 为PPAP中所要求提交给客户的一个项目 EDI Electronic Data Interchange 电子数据交换 是一种在公司之间传输订单、发票等作业文件的电子化手段。 DFX Design for Experiment 实验性设计 QFD Quality Function - 32 - / 32 Deployment 质量机能展开 把顾客或市场的要求转化为设计要求、零部件特性、工艺要求、生产要求的多层次演绎分析方法,它体现了以市场为导向,以顾客要求为产品开发唯一依据的指导思想。 SPC Statistical Process Control 统计过程控制 指应用统计分析技术对生产过程进行实时监控,科学的区分出生产过程中产品质量的随机波动与异常波动,从而对生产过程的异常趋势提出预警,以便生产管理人员及时采取措施,消除异常,恢复过程的稳定,从而达到提高和控制质量的目的 田口方法 Taguchi Methods - 32 - / 32 田口方法是一种低成本、高效益的质量工程方法,它强调产品质量的提高不是通过检验,而是通过设计。其基本思想是把产品的稳健性设计到产品和制造过程中,通过控制源头质量来抵御大量的下游生产或顾客使用中的噪声或不可控因素的干扰,这些因素包括环境湿度、材料老化、制造误差、零件间的波动等等。 PDCA Plan Do Check Act 戴明循环(Deming Cycle) 戴明循环是一个质量持续改进模型, 它包括持续改进与不断学习的四个循环反复的步骤, 即计划(Plan)、执行(Do)、检查(Check/Study)、处理(Act)。 跨国汽车公司全球采购战略 在汽车生产全球化的情况下,为了保证整车质量和降低成本,许多汽车厂家开展零部件全球采购。这是经历了几乎所有零部件由整车厂自制的初始阶段、逐步增加外购零部件比例的低级阶段后,才逐步发展到目前全球采购的中级阶段。全球采购的优点是整车厂可充分利用世界范围内的零部件竞争优势,获取市场的最新技术,适应汇率波动以及集团采购的批量效果,得到最佳质量、最佳服务、最合理价格的配套产品。因此,实施全球采购战略,扩大外购率,减少自制率,以达到最佳的经济效益和最好的产品质量成为当今世界汽车工业的发展趋势。 汽车零部件供应体系有着清晰的层次: 第一协作层以总成配套厂为主,厂家总量少,规模大; 第二协作层以汽车零部件配套厂为主,围绕各自的总成厂形成较小区域配套网,厂家可多可少,规模可大可小; 第三协作层以原料厂和工艺厂为主,为零件厂、总成厂以及总装厂提供原料和工艺加工。 跨国汽车巨头把世界各国的汽车零部件企业划分为三个梯队: - 32 - / 32 第一梯队是美国、欧洲、日本等先进的零部件企业; 第二梯队是韩国、台湾等国家和地区的汽车零部件企业; 第三梯队是中国、印度等发展中国家的零部件企业。 跨国汽车公司全球采购方式: (1)模块化采购与系统供应; (2)单一供应商采购方式; (3)同步设计与同步采购方式; (4)提高零部件通用性的通用平台采购模式; (5)电子商务采购方式。 中国汽车公司采购模式与趋势 目前,中国不少汽车生产厂家相继宣布实施全球采购战略。一汽大众是第一个向中国的汽车零部件供应商引入全球采购概念的合资企业。上海通用坚持合作伙伴的全球采购流程,对国内零部件企业进行筛选,根据零部件供应16步开发程序,从质量、服务、技术、价格四个方面进行评估,选定零部件供应商。物流方面,大部分实行外仓管理,门对门送货,及时供货这套流程。在销售和服务方面,品牌专销、单层次拉动式销售等,注重在增值环节向国际水平瞄准,以便提升整体竞争力。 中国汽车零部件企业多渠道营销的选择 1.加入跨国汽车公司的全球采购之路。主要跨国公司都走上了全球采购之路,在控制中国整车市场后,中国整车制造企业也开始推行全球采购。零部件企业只有走上全球采购之路才是康庄大道。 2.加入跨国汽车零部件公司的全球采购体系。入世后,中国汽车零部件供应体系正在分化成三层次:系统或模块集成商为一级;围绕一级供应商的组件供应商为二级;零件供应 - 32 - / 32 商为三级。外资零部件供应商将占据一级和部分二级供应商的位置,而国内的供应商将主要占据三级和部分二级供应商的位置。 3.加入国内汽车集团集中采购与配套体系。这是我国多数零部件企业最为现实的选择。一汽、东风都改变过去那种分散采购的模式,成立集团采购部,进行集中采购,并开始全球采购。国内很多零部件企业已经是国内整车企业的配套厂家,要跟上整车企业前进的步伐,以免被淘汰出局。 4.进入汽车售后维修服务体系。随着新车的购买使用,4S店的增多,社会汽车保有量的增加,汽车售后服务市场对汽车零部件的需求不断增加,占全球零部件企业第二位的德国博世公司非常注重售后维修服务市场,专门建立了零部件维修服务连锁系统。 5.进入汽配市场(城)销售渠道。全国有规模的汽配市场有300多家,基本覆盖全国地级城市,是终端汽车零部件特别是中低档车零部件购买者比较、选择、购买的理想场所。 6.建立和进入汽车零部件连锁销售体系。可采用三种方式建立这种体系,一是本企业建立自己独立的连锁销售体系,如万向集团;二是零部件生产、流通企业联合建立连锁销售体系;三是零部件连锁经营联合体。 7.开拓电子商务销售渠道。电子商务是目前汽车销售的一大热点,通用、福特、戴克三大汽车公司联合建立电子商务采购平台,丰田、宝马等公司纷纷加入,号称每年通过此平台采购量要达到2500亿元。 客户首先向供应商发出询价单,进行报价商谈,初选供应商,拟定成本目标和潜在供应评审。初选供应商确定后,再进行技术评审,包括全面评审、模具、制造工艺、材料测试、先期质量控制计划和生产件批准。技术评审合格后,客户才给供应商下长达17~29页的订单。 客户为了从供应商得到准时、合格的零部件,对供应商开发的一般过程有三个阶段63 - 32 - / 32 个步骤: 第一阶段是供应商选择与认证,包括目标产品、初选、评估、前期准备和报价认可等。 第二阶段是供应商投产准备,包括技术文件、更改控制、样品、早期生产控制、产品认证和按节拍生产等。 第三阶段是生产与持续提高,包括质量、物流和持续改进等。如果不严格按上述步骤开发供应商,采购将会有很大的风险,如出现供货不及时,造成生产停顿等。 质量要由客户认可的质量体系来保证,如通用Q S9000体系,德国VDA 6.1体系等,都要由第三方评审认可。今后国际各大汽车公司的质量体将逐步统一到TS16949质量体系上来。 要了解主机厂的配套经验,各主机厂对零部件都有很高的要求,对此要弄得很清楚,并接受主机厂的配套程序。要保证质量过程的有效控制,人与测试设备要双重检测。在开始阶段,国际客户对中国供应商的质量要求更加苛刻。 服务:主要通过电子信息交换和现场服务,包括技术和质量服务;仓储管理,仓库设在主机厂旁边;及时供货,保持通讯畅通,把零部件供应到生产线或其附近;安全库存,根据零部件不同需求保持1~1.5个月的库存量;要有快速反应能力,能满足客户对零部件紧急递送需求。 技术:有同主机厂同步开发的能力,开发费用要同产品价格同时报出,由主机厂承担一部分;能进行数据转换;按主机厂要求,能对产品进行各种不同情况下的检测与试验;生产工艺的有效控制;生产能力的提升;快速工程更改,即为满足客户需求对产品需不断改进,工程更改需要投入,这一块也需同主机厂谈判分摊。 价格:全球采购的价格目标,对国外主机厂来说,一般要比本地采购价格低10~15%才有吸引力;同时,还考虑物流费用约占产品出厂价格的20%左右。因此,有竞争力的价格是供应商的价格要比主机厂在当地采购价格低30%左右。如何降低约30%的价格,这就要求中国汽车零部件企业在技术、材料、人力资本、精益生产、管理等方面降低成本。 - 32 - / 32 东风有限供应商QCD评价标准 文件内容提示: QCD总部文件-1包含:标准作业书、 QCD总部文件-2包含:标准作业书-1、标准作业书-2、标准作业书-3、标准作业书-4 标准作业书-5 标准作业书-6 标 准 书 名称 工场诊断(PIP)标准 分类 技术基准书 技术指导费 2、操作手册、评价基准;3、方案集;4、事例集;5、数据集;6、正文 目的及 适用范围 1、目的 * 收集生产工场的管理系统的实际状况及明确生产线状况的改善课题。 2、适用范围 * 对国内外的生产现场管理的实际状况的掌握及应用。 概要 * 工场诊断是致力于改善收益的工作,以诊断基准为主,完善被诊断方的改善措施。 - 32 - / 32 *这个标准是作为收集国内外制造厂家管理状态的有效工具,便于使用而编制的。 *这个详细的内容包括:①导入部分的修订;②诊断顺序(包含日程)的整理;③诊断基准的修订④调查表整理的系统化。 *内容还有不足之外,以后定期收集和修订。 更 改 标 记 N 设计 设计日期 审核 批准 批准日期 有效期限 更改内容 工场诊断(PIP)标准目录 前言 1、方案 ① 工场诊断 - 32 - / 32 ② 工场诊断的对象 ③ 工场诊断的方法 ④ 工场诊断的概要 ⑤ 工场诊断的注意事项 ⑥ 诊断的印象 附表1 工场诊断项目 附表2 工场诊断明细表 2、活动步骤 ① 事前准备 ② 实际调查 ③ 调查汇总 3、工场诊断日程表 ① 基本时间日程 4、工场诊断基准 ① 诊断基准(M、Q、C、D、S) 5、明细表 ① 工场诊断结果报告 ② 企业概要调查表 ③ 工场诊断结果汇总表 ④ 工场诊断表(结果) ⑤ 工场诊断表(原因) 前言 - 32 - / 32 90年7月份编制工场评价系统(PIP=Point of Ideal Plant),作为提高收益改善的标准而进行工场评价,这个评价适应国内外的工场。 同时也可作为海外研修生的导入教育的指导。基于这个方面,而重新编制使用。 一方面针对国内往来的厂家的评价的需求较少,使用这个标准评价的人也较少,以及对这个评价不了解的状况也存在,还有,以前评价诊断表的评价内容和评价的定义不明确的地方也存在,因评价人的不同,评价的内容也不同。 这次针对以前的不足之处的修订和今后对海外供应商的诊断,针对具有一个流的生产活动以及各种改善活动等经验、知识的诊断者,对方案推进方法、基准、诊断表进行重新修订。 但是,内容还有不足之处,通过以后国内外诊断活动的意见和希望,对《工场诊断标准》进行修订。 基准不是一成不变的,最后是通过诊断者,如果不能掌握诊断的技巧和工场的现状,也不能作出合适的诊断。(注) 1、方案 1) 工场诊断 * 通过现场观察和咨询来掌握工场的管理系统的实际状况。 * 诊断内容是从工场及生产线的管理状况、管理职能、管理实际情况(管理水平、实际值、改善的灵活性)中明确改善的课题。 * 通过现场诊断(参照生产诊断标准),明确工场的课题是全面提高工场的管理水平和生产能力。 * 生产诊断:通过工作调查削减低效作业以及改善主体作业的充实度,以提高生产能力。 2) - 32 - / 32 工场诊断对象 * 工场相关的全部作为诊断对象,从材料入库到成品交货的全过程。 * 广泛的调查范围是包括全部相关的部门。 * 诊断不只是加工工序,还有相关生产管理、检查、材供、装备等情况。 3) 工场诊断的方法 * 诊断是掌握原材料入库~成品交货的全过程。 * 诊断是通过现场观察和与管理人员、相关人员交流而进行的。 ① 现场观察:进行管理目视板的内容和生产现场、仓库等管理现状的观察,是为了抓住诊断时的遗漏点(而不是推测); ② 交流:掌握管理人员、监督人员在现场工作的实际情况,在有限的时间内采用问答方式交流。 4) 工场诊断的概要 4-1) 工场诊断的内容 * 工场诊断项目按职能分为结论组7项、要因组30项。参照工场诊断项目。 * 管理状况的掌握分为3项。 ① 管理水平:各职能部门的组成和制度的有无。 ② 实施性:制定的计划和制度是否能严格执行。 ③ 改善灵活性:具有提高制定计划和制度的管理水平的工作。 4-2) 评价等级的人员 * 诊断结果是通过评价等级决定的,不是以打分为目的。而是以现场管理状况的问题点,以及存在问题作为改善的课题为目的。 - 32 - / 32 * 诊断后,诊断者通过标准对照对诊断的结果进行等级确定。 * 评价点是减少评价员的主观意念,采用两人诊断方式对每一个数据进行审核,确定评价等级。 * 多个小组诊断时有必要进行小组间的调整。 * 诊断的评价点分为5个阶段,如下表: 评价水平 日产圈的 平均水平以下 日产圈的 平均水平 日产圈 最高水平 日本国内水平 世界内水平 评价的标准 无组织结构 工场诊断项目实施达50% 诊断项目实施达80% 比诊断项目内容有更好的管理方法 除此之外,没有更好的管理方法 差 一般 好 优 未见过 4-3) 工场诊断的评价表 * 为提高诊断的效率,使用评价表。参照《工场诊断(PIP)一览表》。 4-4) 工场诊断结果的使用者 * 通过一次诊断,掌握工场的优势、劣势,以确定改善的课题(只限于一次诊断)。 * 定期诊断是掌握工场管理状况的变化确认。 * - 32 - / 32 根据诊断的目的的不同,数据也要相应变化。 5) 工场诊断的注意事项 * 这个诊断是其他部门的请求而实施的情况较多,确定调查目的。 * 诊断对象是跨行业的,特别是海外厂商的诊断,最好在诊断前掌握国内同行业厂商的实际情况。 * 诊断前,安排诊断交流人员(工场厂长、相关部长等)。 * 其他的诊断、评价进行时,明确参加人员、时间分配等内容。 * 诊断的工具事先准备准备。 * 在诊断实施时,诊断项目的内容和30项目的概要要事前准备。 * 对于诊断的实施者,尽量记下主要内容。 * 诊断将现场实际状况,为弥补不足与相关人员进行交流,对现场状况的好、差必须准确记录。最好不要收集无效的数据。那也是诊断事项。对现场状况调查时,要找对工序和现状了解的人调查。 6) 工场诊断活动的印象 * 最近的诊断事例 2001年3月南美海外工厂的诊断(PIP和CSES的评价) 2002年月月中国海外工厂的诊断(PIP和生产能力诊断) 2、活动步骤 - 32 - / 32 1) 事前准备 序号 步骤 内 容 活动事项 其它 1 确定调查活动内容 *确定调查活动目标、内容(调查目的、对象、时间、成员等) * 确定调查目的,包含方法 * 进行工场诊断时,可以根据情况追加评价、诊断项目 要求作成资料 2 掌握调查工场的概况 * 收集调查工场的情况(公司规模、主要制品、人员等) * 掌握国内供货商的现状(公司规模、制品、人员等) * 确定海外工场的调查活动的不同之处 物流部门(企业调查表)企业概况调查表 3 从其它公司收集调查企业产品的情况 * 从竞争对手收集调查企业的主要产品的情况(工场参观、公司介绍资料) * 通过比较也掌握了竞争对手产品、管理状况和制造管理水平(有必要参观竞争对手的工场) 4 确定调查范围和调查方法 * 确定调查范围(工场综合水平、特殊产品等) * 确定调查方法和调查要点 * 根据调查目的,确定调查地点、内容、时间、诊断人 * 诊断人为两人 5 诊断日程的确定 * 决定诊断对象和日程 * 确定调查要求和诊断日程 - 32 - / 32 * 确定调查项目 * 确定诊断交流人员(厂长、部长等) * 必须有诊断的数据 例:综合指标 6 决定诊断日程 * 决定诊断日程 * 根据调查内容的不同制定不同的计划 * 根据诊断的工场制定诊断日程计划 * 现场观察和交流时间的确定 * 分配好调查时间 诊断日程 2) 调查实施 序号 步骤 内 容 活动事项 其它 1 * 诊断的实施 * 诊断是由两个人实施,为了防止一个人观察时,有疏漏而配置2个人 * 诊断的目的是为了找出工场管理的问题点和改善课题 * 诊断的资料不给交流者,把相关的结论指标使其知道也可以 -1 * * - 32 - / 32 工场诊断的主要说明 进行诊断活动的目的、日程、成员工的介绍 诊断日程表 -2确定公司、工场概况 * 确定诊断的公司概况 * 收集整理公司、工场的情况 * 以前调查的情况可能不准确,从交流者处收集完善必要的内容 * 企业调查表 -3结论指标的确认 * 确定结论指标 --诊断结束后进行 --收集数据进行诊断 (管理项目、数据在短时间内整理出来) *诊断前收集被诊断厂家的情况也可以 * 结论表 2 工场诊断的实施 -1 确定诊断的对象 * 确认工场的平面布置和工艺流程 * 确定诊断的对象、路线 * 确定诊断的对象、路线的同时,对诊断方法与同行的诊断者取得认可 -2 确定现场的实施状况 * 根据日程安排调查 * 确定诊断的实施内容 * 计划的日程不妥时按实际情况重新安排 * 诊断是对作业者、设备状态及相关部门的观察 * 掌握原材料入库--- * 工场诊断表 * 文件夹 - 32 - / 32 * 诊断对象的现场观察和交流 成品交货、各个工序状况和管理状况 * 不只是生产工序,还包括现场辅助部门的确认 * 首先在主要位置观察 * 不明之处咨询管理者,了解实际状况 -- 诊断的目的之一是管理者必须掌握工场状况 * 为了不遗漏观察点,将观察点的现有状况记录在调查表上 * 做好记录 * 在现场的调查记录,以后整理时也可能存在数据不足的情况 * 在现场不能确认的项目,在下一个项目中从相关部门咨询 * 这个阶段,评价等级没有意义 -3 部门交流 * 在现场不能确认的内容进行咨询 * 咨询不只是对实际状况的确认 -- 诊断的目的之一是掌握相关部门管理者是如何管理的 3) 整理调查结果 - 32 - / 32 序号 步骤 内 容 活动事项 其它 1 * 整理诊断结果 -1 诊断内容的整理 * 对诊断结果的汇总和进行等级评价 * 整理工场工序的诊断内容 * 首先,整理个人资料 * 用诊断表的项目对工场诊断内容进行综合汇总 * 对相关内容进行整理(不能推测) * 工场诊断表 -2 诊断结果进行评介 * 对各个项目的汇总内容进行等级评价 * 汇总内容和诊断的各项目根据基准打分 * 工场诊断表 * 工场诊断基准 -3 诊断结果汇总 * 对诊断的内容和等级进行审核 * 对诊断项目的内容和评价等级,与诊断者进行审核 * 如果有遗漏之处的话,审核就非常重要 * 有补充内容和评价等级在表中记录 -4 诊断结果的汇总表 * 整理诊断结果的汇总表 * 整理原因和结果的评价 * 从原因中反映出的问题点、课题,对管理水平、实际状况、改善活动的内容进行整理 * 工场诊断表(结果、原因) * 诊断结果的汇总表 - 32 - / 32 * 对诊断内容进行汇总整理 2 诊断结果报告 * 整理诊断结果报告 * 企业概况和诊断结果按报告书形式整理 * 工场诊断结果报告书 * 诊断结果汇总表 * 企业概况调查表 3、工场诊断时间 1) 基本时间 * 根据调查的对象、范围,如果时间不合适时,可重新安排。 * 针对诊断评价的场合,也可以对实施项目和时间分配重新考虑决定,对生产能力的诊断和实施时,可参照(生产能力诊断标准)的日程。 内 容 所需时间 时间 1 欢迎词 被诊断方 10分 10:00-10:10 2 说明目的和介绍参加人员 日产 3 公司和工场的概况介绍 ① 公司概况(销售额、利润率、主要产品、主要用户、人员等) ② 工场概况 被诊断方 30分 10:1-10:4 - 32 - / 32 (主要产品和生产量、组织结构、人员结构等) ③ 结论指标 (Q、C、D、S) 4 诊断的实施 ① 工场的平面布置和产品流程的确定 ② 诊断实施(原料入库-成品交货) 日产 170分 (20分) (150分) 10:40-14:30 (包含午饭时间) * 公司、工场概况是根据企业概况调查表来掌握被诊断方的状况(根据公司的介绍资料也可以),确定不足之处。 * 结论指标根据调查表收集数据。 * 确定工场布局和产品的工艺流程(为提高诊断效率)。 * 尽量多收集诊断信息。 * 诊断活动数据的整理不在这里进行。 l 诊断活动的整理是在工场参观时对问题点和课题的评价。 - 32 - / 32查看更多