- 2022-09-27 发布 |
- 37.5 KB |
- 63页
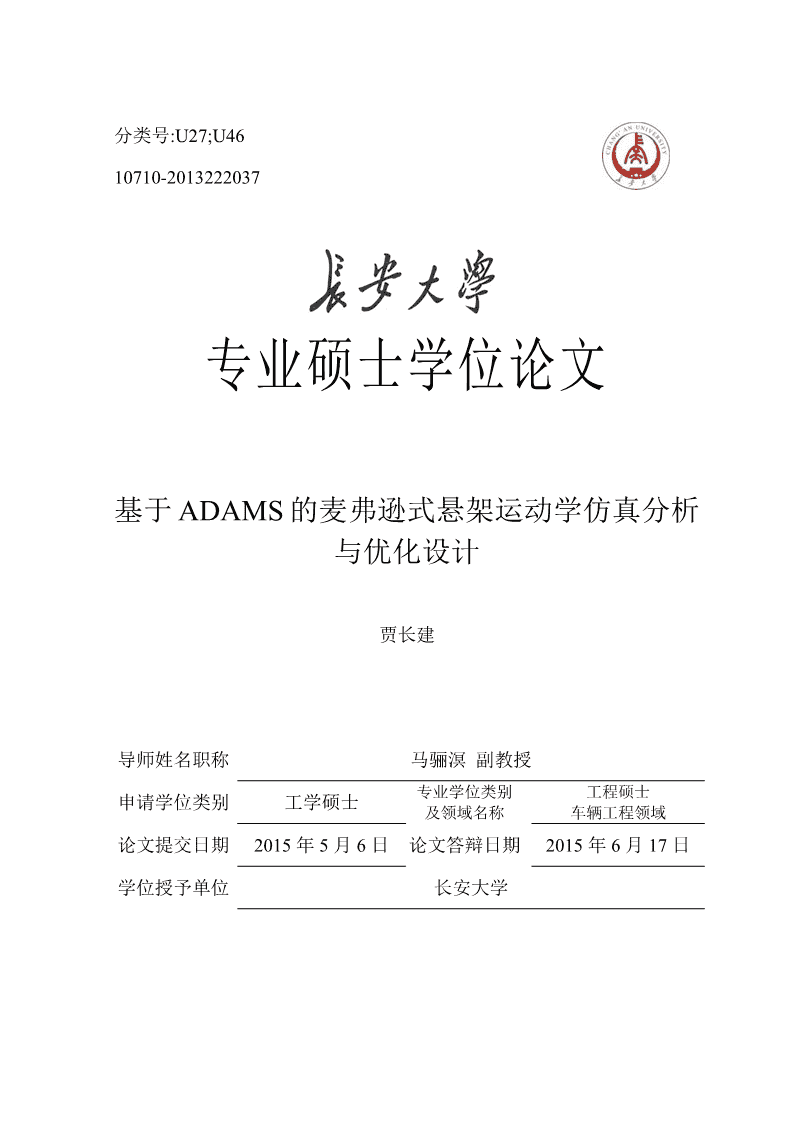
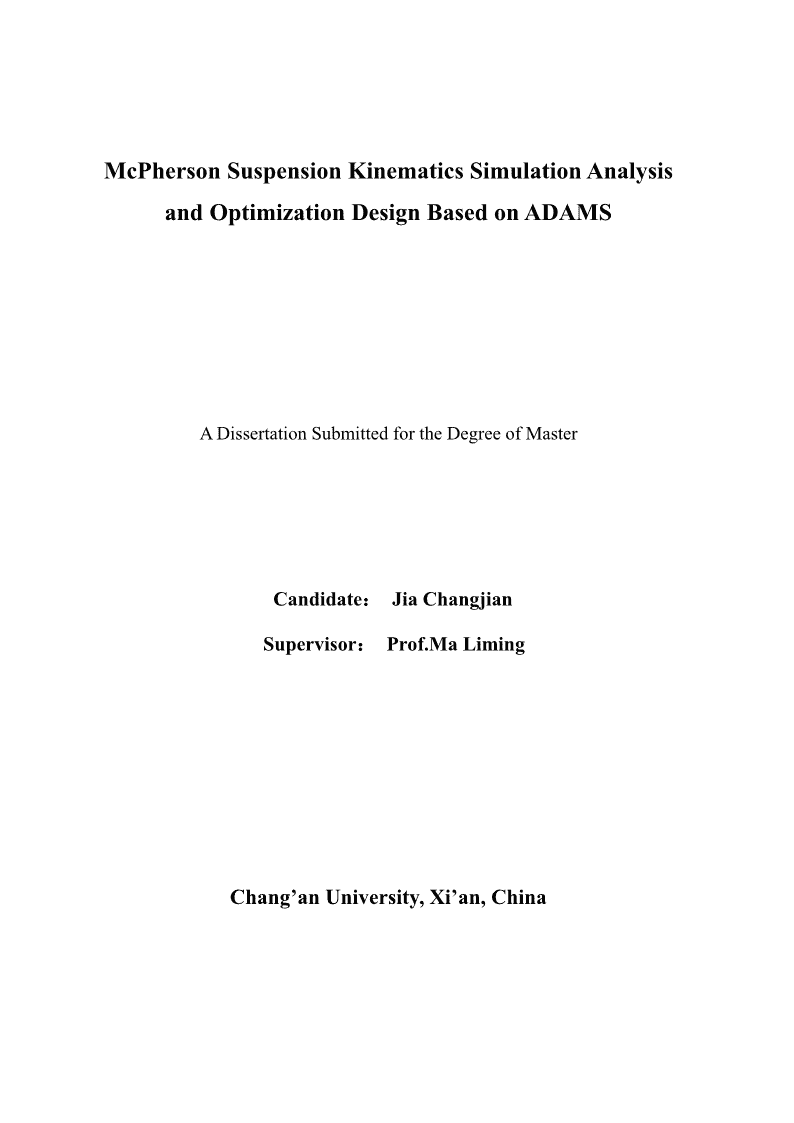
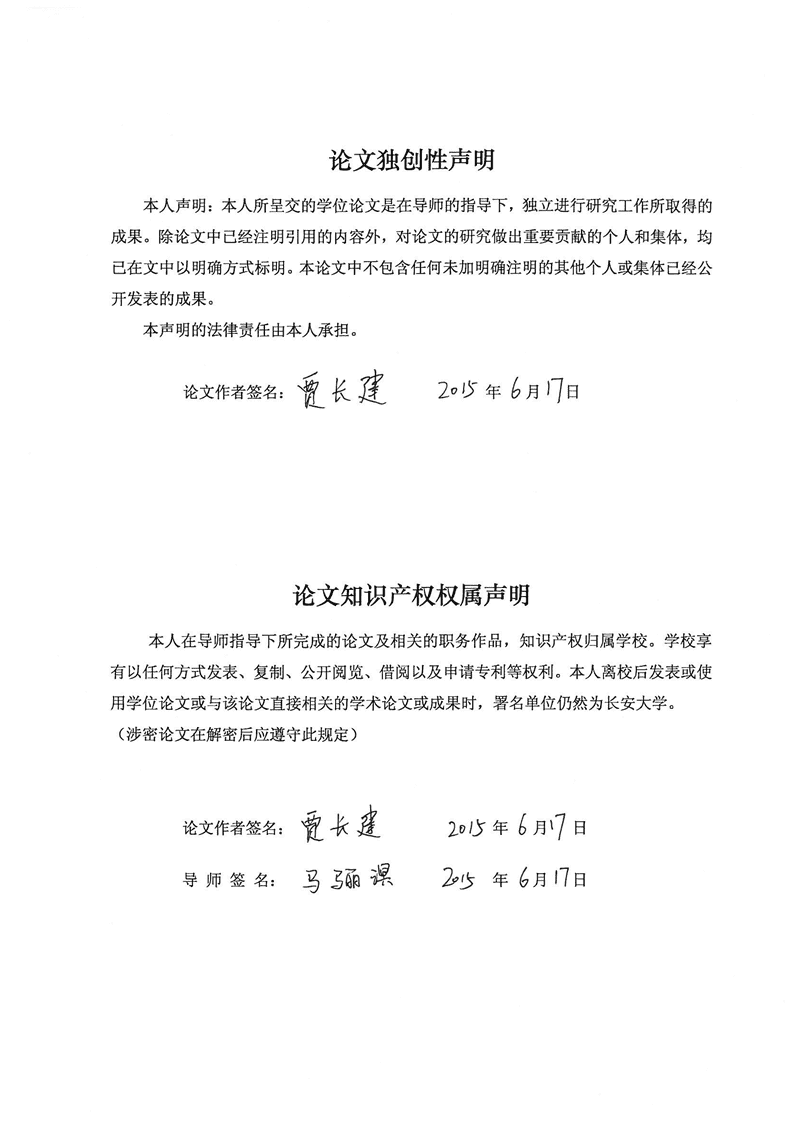
申明敬告: 本站不保证该用户上传的文档完整性,不预览、不比对内容而直接下载产生的反悔问题本站不予受理。
文档介绍
基于adams的麦弗逊式悬架运动学仿真分析与优化设计硕士论文
分类号:U27;U4610710-2013222037专业硕士学位论文基于ADAMS的麦弗逊式悬架运动学仿真分析与优化设计贾长建导师姓名职称马骊溟副教授专业学位类别工程硕士申请学位类别工学硕士及领域名称车辆工程领域论文提交日期2015年5月6日论文答辩日期2015年6月17日学位授予单位长安大学\nMcPhersonSuspensionKinematicsSimulationAnalysisandOptimizationDesignBasedonADAMSADissertationSubmittedfortheDegreeofMasterCandidate:JiaChangjianSupervisor:Prof.MaLimingChang’anUniversity,Xi’an,China\n\n\n摘要随着科学技术的飞速发展,人们对汽车性能的要求变高,汽车的操纵稳定性已经成为各大汽车制造厂商为提升产品竞争力所越来越重视的一项性能指标。传统的分析方法已经跟不上汽车飞速发展的脚步,虚拟样机技术的应用变得愈发重要。悬架的运动学仿真分析在汽车悬架系统的设计和开发中占有重要的地位,通过仿真软件ADAMS可以对汽车性能进行高效的研究。本文采用悬架系统运动学研究方法对麦弗逊悬架系统进行研究。文中对麦弗逊式独立悬架的结构进行了分析,以此为基础在ADMAS/Car中建立麦弗逊前独立悬架的简化仿真模型,在软件中分别进行双轮同向和双轮反向激振情况下的悬架运动学仿真,根据仿真分析结果得到不符合设计要求的车轮定位参数。然后,以车轮定位参数为目标函数,运用ADAMS/Insight的DOE试验设计功能找出对各个车轮定位参数影响较大的悬架结构设计硬点,并比较优化前后的仿真分析结果,对优化目标进行验证。全文以在ADAMS中所建立的模型为基础,实现了在计算机上对汽车悬架性能的仿真分析。本文优化后的车轮定位参数运动学特性得到了较大的改善,提高了汽车的操纵稳定性,对于汽车制造厂商在产品研发过程中缩短设计周期、降低开发成本和提高产品质量都有非常重要的意义。关键词:麦弗逊悬架,ADAMS,仿真分析,优化设计i\nAbstractWiththerapiddevelopmentofscienceandtechnologypeople'srequesttoautomobileperformancebecomeshigher,theVehiclehandlingandstabilityperformanceofvehiclehasbecomeaveryimportantperformancemetricswhenthecarisinthedevelopmentstage.Thetraditionalmethodofanalysishasnotkeptupwiththerapidpaceofdevelopmentofautomobile,theapplicationofvirtualprototypetechnologybecomesmoreandmoreimportant.Thekinematicsimulationanalysesofsuspensionplaysaveryimportantroleinsuspension’sdesignandexploitation.DeveloperscandoresearchonvehicleperformanceefficientthroughthesimulationsoftwareofADAMS.ThispapertakethekinematicsofsuspensiontostudyMcPhersonsuspension.thepaperanalysisthestructuraloftheMcPhersonsuspension,establishasimplifiedmodelofMcPhersonsuspensioninthemoduleofADMAS/Car,anddothekinematicssimulationofsuspensionintheexcitationofparallelwheeltravelandoppositewheeltravel.Accordingtotheresultsofsimulation,wegetthewheelalignmentparameterwhichisnotuptotherequirementofdesign.Then,Takingthewheelalignmentparametersastheobjectivefunction,weusetheDOEfunctionofADAMS/InsighttomodifythecoordinateofhardpointthatisassociatedwithVariouswheelalignmentparameters.Bycomparingtheresultsbeforeandafter,itverifiesthefeasibilityofthismethod.BasedonthemodelofADAMS,thepaperachievedthegoalthatsimulationanalysisoftheperformanceofsuspensionThisarticleimprovingthekinematiccharacteristicsofthewheelalignmentparametersandimprovingthecar’shandlingandstability.Thismethodhasveryimportantsignificance,itcanshortendesigncycle、lowercostandimproveproductqualityinthedevelopmentstages.Keywords:McPhersonsuspension,Simulationanalysis,Optimization,ADAMSii\n目录第一章绪论.............................................................................................................................11.1研究背景....................................................................................................................11.2麦弗逊悬架的简介....................................................................................................21.2.1麦弗逊悬架的组成.........................................................................................21.2.2麦弗逊悬架的特点.........................................................................................31.2.3麦弗逊悬架的导向机构的设计要求.............................................................31.3国内外研究现状........................................................................................................41.3.1国外研究现状.................................................................................................41.3.2国内研究现状.................................................................................................41.4研究内容与意义........................................................................................................51.4.1研究内容.........................................................................................................51.4.2研究意义.........................................................................................................6第二章多体系统动力学及ADAMS仿真原理.........................................................................72.1多体系统动力学研究的发展及其理论....................................................................72.2多体系统动力学建模与求解过程............................................................................72.3多刚体系统动力学计算步骤....................................................................................82.4车辆动态仿真分析软件ADAMS..........................................................................112.5本章小结..................................................................................................................12第三章麦弗逊式前悬架虚拟样机建模...............................................................................133.1麦弗逊式前悬架结构分析......................................................................................133.1.1麦弗逊悬架的简化和假设...........................................................................133.1.2麦弗逊悬架模型的运动学分析...................................................................133.2麦弗逊式前悬架虚拟样机模型建立......................................................................153.2.1建模数据准备...............................................................................................153.2.2麦弗逊式悬架子系统及悬架总成创建过程...............................................163.3本章小结..................................................................................................................18第四章麦弗逊式前悬架仿真及影响因素分析...................................................................194.1麦弗逊悬架运动学仿真过程..................................................................................194.2双轮同向跳动时车轮前束角分析..........................................................................214.2.1车轮前束角对整车性能的影响...................................................................214.2.2车轮前束角仿真分析...................................................................................244.3双轮同向跳动时车轮外倾角分析..........................................................................24iii\n4.3.1车轮外倾角的定义及其对整车性能的影响...............................................244.3.2车轮外倾角仿真分析...................................................................................264.4双轮同向跳动时主销后倾角分析..........................................................................264.4.1主销后倾角的定义及其对整车性能的影响...............................................264.4.2主销后倾角的仿真结果分析.......................................................................284.5双轮同向跳动时主销内倾角分析..........................................................................284.5.1主销内倾角的定义及其对整车性能的影响...............................................284.5.2主销内倾角的仿真结果分析.......................................................................304.6双轮同向跳动时主销偏移距分析..........................................................................314.6.1主销偏移距的定义及其对整车性能的影响...............................................314.6.2主销偏移距的仿真结果分析.......................................................................314.7双轮异向跳动仿真分析..........................................................................................324.7.1车轮前束角...................................................................................................324.7.2车轮外倾角...................................................................................................324.7.3主销后倾角...................................................................................................334.7.4主销内倾角...................................................................................................334.7.5主销偏移距...................................................................................................334.8本章小结..................................................................................................................34第五章麦弗逊式前悬架优化分析.......................................................................................355.1优化设计的方法......................................................................................................355.2ADAMS的试验设计..............................................................................................355.2.1试验设计原理...............................................................................................355.2.2ADAMS试验设计的过程和方法...............................................................365.3麦弗逊悬架的试验设计..........................................................................................365.4对悬架进行优化分析..............................................................................................415.5优化前后仿真结果的比较......................................................................................485.6本章小结..................................................................................................................50结论与展望...............................................................................................................................51结论...................................................................................................................................51展望...................................................................................................................................51参考文献...................................................................................................................................52致谢.......................................................................................................................................55iv\n第一章绪论第一章绪论1.1研究背景汽车工业诞生于德国,至今已经有一百多年的历史了,在发展的初期,汽车作为一种奢侈品,保有量特别少。中国汽车工业开始于1956年,就在这一年,我国生产的第一辆汽车下线,从此,中国汽车工业较快的向前发展。在汽车工业日益发达的今天,无论白领还是普通的工人,都渴望拥有一辆属于自己的汽车,这也成为促进国内汽车工业发展的重要原因之一。同时,汽车企业之间也增加了相互的竞争,因此,各个企业都在积极的研究性价比更高的汽车。人们对汽车各项性能的要求也日益提高,人们比较关注的汽车性能主要是汽车的安全性和乘坐舒适性。在国内,汽车逐渐被普及,同时,人们对汽车性能的要求也日益增加,比如汽车的平顺性、操纵稳定性和舒适性能,这也就推动了汽车悬架各项性能的迅速发展[1]。国内汽车工业经过快速的发展,汽车保有量快速增加,据统计,2014年中国汽车销量总数达2349.19万辆,目前已经连续六年蝉联世界第一。不过,值得一提的是,对于中国汽车市场来说,自主品牌占有的份额比较少,所以,国内汽车工业当务之急在于创新。在整车的研发中,针对悬架的研究是一项重要的工作,悬架对于现代汽车的正常行驶发挥着重要的作用,它的位置一般在车身与车轮之间,是车身与车轮弹性连接起来;悬架主要有由弹性元件、减震器、缓冲块、导向装置和横向稳定器等五部分组成[2]。悬挂系统对整个汽车的性能有很大影响,它与汽车的操纵稳定性和乘坐舒适性(平顺性)息息相关,而悬架的种类也直接决定了整车制造成本的高低。目前来说,悬挂系统主要分为独立悬架和非独立悬架,非独立悬架和独立悬架主要的区别是:当一端车轮跳动时,另一端车轮是否跟着跳动。由于人们生活水平的提高,对汽车的乘坐舒适性和操作稳定性要求越来越高,所以在小型汽车上不采用非独立悬架,非独立悬架一般只用在大客车和货车上。现代中小型汽车基本采用的是独立悬架,左右车轮的跳动互不影响。在很多中小型汽车上,大多采用麦弗逊式独立悬架作为前悬架,不是因为它的性能最好,也不是因为它的技术含量高,而是因为其性价比非常高,而且,它的结构简单、维修方便、制造成本低,另外,其舒适性也能满足基本的要求,因此,麦弗逊悬架被广泛的采用,不管是国产车还是高性能的汽车,很多都是采用麦弗逊悬架,比如,宝马M3采用的是麦弗逊悬架系统,在国产车里,奇瑞的很多款车型都是采用的麦弗逊悬架系统。麦1\n长安大学硕士学位论文弗逊悬挂通常由螺旋弹簧加上减震器以及A字型托臂组成,螺旋弹簧起到减震的作用,而减震器除了减震还起到支撑车身的作用;A字形托臂一般有两个作用,一是用来给车轮提供部分横向支持力,二是用来承受来自前后方向的预应力。这两个部件承受了所有的冲击。麦弗逊悬架还有一个突出的优点,就是其占用空间比较小,这样,对于发动机前置的汽车,悬架就给发动机的安装留有更大的空间,这样,在发动机前置的中型车上就能放下大型发动机,同样,在一些小型汽车上,能给安装中型发动机留有更大的空间。1.2麦弗逊悬架的简介1.2.1麦弗逊悬架的组成麦弗逊式悬架在很多中小型轿车上应用很广泛,多用于轿车的前悬架。虽然麦弗逊悬架的技术含量不高,但其还是受到各大汽车厂商的青睐,究其原因,是由于麦弗逊悬架成本低,且占用空间小。在国内,很多轿车上都采用的是麦弗逊悬架。麦弗逊式悬挂主要由三部分组成,包括螺旋弹簧、减震器和三角形下摆臂。麦弗逊悬架的结构特点使其占用空间比较小,其中,螺旋弹簧套在减震器上,由于结构上的特点,使得减震器限制弹簧只能作上下方向的振动,避免了弹簧在其他方向的振动。麦弗逊悬架中的下摆臂在受力方面起到很大的作用,它承受了车轮所受的大部分侧向力,所以在设计当中,尽量使下摆臂具有高强度和轻质量。减振器上端与车架连接位置铰链的中心与三角形下摆臂外端球铰链中心的连线为主销轴线[23]。麦弗逊悬架三维图及其在实车上的图形分别如图1.1和1.2所示:螺旋弹簧减震器A字形下摆臂图1.1麦弗逊悬架2\n第一章绪论减震器A字形下摆臂转向节图1.2麦弗逊悬架在实车上的示意图1.2.2麦弗逊悬架的特点麦弗逊悬架的主销和减震器中心线不共线,这样的布置可以使悬架的受力比较合理。另外,还有一个突出的特点,在悬架随着车轮跳动过程中,各点至主销的距离是变化的[24]。麦弗逊悬架在随着车轮上下跳动过程中,车轮定位参数和主销偏移距是不断变化的,如果悬架设计的合理,那么这些参数随着车轮跳动的变化范围很小。麦弗逊悬架的选择给发动机的布置提供了更大的空间。麦弗逊悬架虽然有很多优点,但是它的一些缺点也是不容忽视的,麦弗逊悬架的抗侧倾能力较差,稳定性差,转弯侧倾有些明显。不过,在中小型汽车上,这些缺点不足以掩盖麦弗逊悬架的优点,所以,麦弗逊悬架还是很受欢迎的。1.2.3麦弗逊悬架的导向机构的设计要求悬架的导向机构有很重要的作用,它承担着很多的作用力(除了垂直力之外),其中一些部件的位置决定了定位参数的选取。所以,本文在进行悬架优化设计的时候,需要满足如下要求[25]:首先,侧倾中心是个比较重要的参数,优化设计的时候侧倾中心要形成的比较恰当;其次,为了保证导向机构的导向精度,减少机构中某些元件的弹性变形,应该要求各个铰点处的受力尽可能的小。再次,由于车轮定位参数对整车的性能影响较大,所以应该使这些参数的变化符合理想的变化趋势。另外,保证轮距的变化应该在一定范围之内。最后,导向机构应该具有足够的寿命和较强的抗疲劳能力。3\n长安大学硕士学位论文1.3国内外研究现状1.3.1国外研究现状国外对于悬架系统的研究开始比较早,目前为止,国外对于悬架系统的研究已经达到比较成熟的阶段[6],可以说,麦弗逊悬架的研究已经趋于成熟,国外技术人员开始研究新类型的悬架,虽然关于麦弗逊悬架的技术比较成熟,但是很多国外汽车中普遍采用麦弗逊悬架,主要是因为其性价比很高。德国有本著作《汽车底盘技术》[7]详细的介绍了多种悬架的结构和运动特征,其中就提到了麦弗逊悬架,文中介绍了麦弗逊悬架的结构特点和主要的定位参数,并且详细的介绍了各个定位参数对于汽车使用性能的影响。国外对于麦弗逊悬架的研究开始比较早,在1950年,福特在英国的子公司生产的两款车,是世界上首次使用麦弗逊悬架的商品车。从那以后,各大汽车企业都认识到麦弗逊悬架的优点,都在各地的中小型车上甚至高档车上配置麦弗逊悬架,麦弗逊悬架由于构造简单,性能优越的缘故,被行家誉为经典的设计。在19世纪50年代,Janeway准则和K系数法相继被提出[8],这两项理论都做了大量的试验,其中试验的基础都是振动试验台,采用正弦激振的方式输入,但是所研究的成果不是很满意,究其原因主要是没有分析汽车随机振动所产生的影响,只是给试验台输入有规律的振动,汽车在行驶过程中,所受到的都是随机振动,想要精确的分析由此带来的影响是比较困难的。19世纪80年代,《人体承受全身振动评价—第一部分:一般要求》被颁布[9],从而给各大企业对于悬架的研究提供了一个要求和标准。目前来说,在国外,对于麦弗逊悬架的研究也日趋成熟,很多研究机构开始研究可控悬架等一些高性能悬架,不过,麦弗逊悬架也凭借其低廉的制造成本等优点,依旧受到国外企业的青睐。1.3.2国内研究现状对于国内来说,针对悬架的研究起步较晚,从80年代才开始的,虽然比国外起步较晚,但是在参考国外文献和研究成果的基础上,发展迅速,很快就有了明显的进展。在1976年,郭孔辉院士发表了一篇“汽车振动与载货的统计分析及悬挂系统参数选择”文章,此文章详细的介绍了怎样选择悬架参数,以实现对汽车的行驶平顺性进行研究并讨论[10]。从90年代初开始,研发人员尝试用多种方法将柔性体的力学效应纳入到多体运动力学的方程中进行详细的分析与求解[11]。4\n第一章绪论此外,国内设计人员大都是采用虚拟样机技术对汽车的悬架进行仿真分析和优化,这项技术越来越成熟,虽然虚拟样机技术和实车道路试验相比有一定的误差,但是它可以缩短研发周期,为其它的研究提供一个参考的依据。近几年,国内很多高校的硕士、博士研究生相继发表了有关悬架方面的研究论文,通过不同的角度分析了悬架的特点和对整车性能的影响。2010年吉林大学的李宁[12],发表的文章主要是通过调整悬架K&C特性来改善汽车动力学性能,通过建立悬架模型,并且对其进行仿真,分析悬架参数对整车性能的影响。2014年李翔晟等人在《汽车麦弗逊悬架性能仿真和优化研究》一文中,采用免疫算法对麦弗逊悬架的结构参数进行优化,并进行实车验证[13],验证了优化方法的可行性,提高了整车的操纵稳定性。1.4研究内容与意义1.4.1研究内容本文研究对象是某款车型的麦弗逊式悬架,由于该汽车操作稳定性不好,通过分析,得出需要对悬架模型中的部分硬点坐标进行优化,从而优化车轮定位参数,改善汽车操作稳定性,具体内容如下:(1)文章首先介绍了课题的研究意义、研究背景和国内外研究现状,并且对多体系统动力学和ADAMS软件进行了简单的介绍;(2)在ADAMS/CAR中对所研究的麦弗逊悬架进行建模,根据悬架的参数,相对准确的建立仿真模型;(3)在建立好模型之后,对模型进行左右车轮同向跳动和左右车轮异向跳动仿真试验,设置车轮上下跳动行程都为50mm,仿真步数为50。仿真完成后,在后处理模块分析本文所研究的五个参数随着车轮上下跳动的变化曲线,找出哪些参数的曲线变化范围不满足理想要求;(4)针对仿真分析得出的不足之处,对悬架模型中影响较大的硬点坐标进行优化,通过试验设计找出对目标函数影响较大的试验因子,并以此作为设计变量,在优化模块中进行优化设计,最终优化了部分硬点坐标,使车轮定位参数随车轮跳动的变化满足理想要求。5\n长安大学硕士学位论文1.4.2研究意义悬架系统对整车的很多性能都有影响,从外表上来看,悬架看似简单,但是它的内部包含着很多种力的合成,决定着汽车的很多性能,如:操纵稳定性、乘坐舒适性和安全性等,所以,对悬架的研究属于整车研究的关键之一。改善汽车操动稳定性最重要和最直接的方式是对悬架系统的参数进行优化。目前,悬架的种类越来越多,在很多高档车和赛车上,对于悬架的选择上面,大都采用主动悬架,一部分车型也采用半主动悬架[3,4,5]。但是家用车上采用主动悬架的比较少,因为生产主动悬架所产生的费用比较高,所以,诸如麦弗逊悬架之类的被动悬架在一定时间内仍将是应用最广泛的悬架,通过对悬架结构和参数进行优化,可以继续提升悬架的性能。本课题研究的是被动悬架系统。虽然麦弗逊悬架技术含量不高,但其突出的优点是不可忽视的,其生产费用比较低,且由于麦弗逊悬架结构紧凑,所占用的空间比较小。所以,在悬架的研究成本不增加的情况下,最大程度的提高悬架的使用性能具有重要的意义,本课题是在对悬架结构改动不大的前提下,使其性能更优,具有一定的现实意义。利用ADAMS软件的Car模块和Insight模块对麦弗逊悬架系统进行仿真分析,并对几个参数进行优化设计,此研究方法对于开发悬架系统的时间、费用和成本都有显著的降低。6\n第二章多体系统动力学及ADAMS仿真原理第二章多体系统动力学及ADAMS仿真原理2.1多体系统动力学研究的发展及其理论多体系统动力学是一门重要的学科,对研究其他学科的内容也有一定的指导作用,它被广泛的应用的各大研究中,它的核心问题是建模和求解问题[14],多体系统不单单是由一个物体组成的,它是一个复杂的机械系统,系统内的多个物体通过运动副连接。多体系统是一个新的学科分支,它是基于经典力学所产生的,目前已经趋于成熟。通常情况下,一个复杂的系统是由多个刚体组成的,每个刚体通过运动副连接起来,如果要对其进行分析(一般都是进行动力学和运动学分析),可以在专门的软件中建立数学模型,并且要有一般的数学求解方法,这些方法具有高效和稳定的特点[15]。进行多体系统动力学分析时所用的方法主要有下面几种:牛顿一欧拉方程法、拉格朗日方程法、凯恩(Kane)方法、R—W方法、旋量方法[16,17,18]等。在1775年,欧拉提出了刚体的概念,建立了牛顿-欧拉方程。这对于以后多体系统动力学的进一步的研究和发展具有重要的意义,它提供了一个理论依据。随后,拉格朗日发表了名叫《分析力学》的文章,提出了广义坐标的概念,进一步充实了多体系统动力学的理论基础[19]。这两种方法是经常用到的,它一般被用在刚体数量比较少的系统里面,刚体数量少,计算量就比较少,如果刚体数量比较多,计算量就相应的增大,想得到最终的解也就比较复杂。为了解决这种问题,人们又不断的研究和探索,找到了解决的方法,具体的方法如下:首先是凯恩方法,这种方法的优点是能分析刚体数量比较多的系统,与之前两种方法相比,当系统比较复杂时,优先选用这种方法。另外一种方法就是R—W方法,这种方法也是被经常用到的,它是在1966年被提出的,由于这种方法在分析多刚体系统方面有突出的优点,所以这种方法自从被提出之后,经常被人们所用到。另外,旋量方法也是一种常见的方法,它使计算过程变的简单明了。2.2多体系统动力学建模与求解过程建立一个机械系统需要经过如下图所示的流程。7\n长安大学硕士学位论文建模求解物理建模数学建模数值求解几何模型物理模型数学模型分析结果初始条件计算方程自动组集分析迭代求解器图2.1系统建模与求解过程2.3多刚体系统动力学计算步骤第一步,要确定机械系统的自由度。表2.1ADAMS中运动副自由度约束数运动副转动(自由度约束数)平移(自由度约束数)总自由度约束数铰接副235移动副325圆柱副325球状副303平面副213固定副336万向副134恒速副134点—面303点—线0228\n第二章多体系统动力学及ADAMS仿真原理计算DOF(机械系统的自由度)公式如下:mxDOF6npiqiRk(2.1)i1j1公式中各个字母代表的意思如下:n:活动件总数;p:第i个运动副的约束条件数;iq:第j个原动机的约束条件数;jR:其他约束条件。k第二步,建立动力学方程并求解广义坐标的选取非常重要,因为它直接决定了动力学方程的求解速度。在ADAMS中,广义坐标的位置和方向不能任意确定,而是由其他因素所确定,刚体质心的笛卡尔坐标确定前者,欧拉角确定后者[21],即:TTTTTqixyz,,,,,i,qqq1,2,qn(2.2)ADAMS程序利用拉格朗日乘子法建立的动力学方程为:TTTdTT.Q(2.3)qdtqq完整约束方程:qt,0(2.4).非完整约束方程:qqt,,0(2.5)其中:T:系统动能;q:广义坐标列阵;:完整约束的拉氏乘子列阵;:非完整约束的拉氏乘子列阵;Q:广义力列阵。为了方便求解,把上面所建立的动力学方程改写成一般形式,如下面公式所示:9\n长安大学硕士学位论文.F(q,,,,t)uu0..Guq(,)uq0(2.6).j1(q,t)0.其中::约束反力及作用力列阵;F:系统动力学微分方程及用户定义的微分方程;q:广义坐标列阵;u:广义速度列阵;:描述约束的代数方程列阵。对所建的方程进行求解,这里用吉尔预估-校正算法,运用该算法之前,要先知道一些矢量值,这是运用该算法的前提,然后,预估下一时刻的值,这里运用泰勒级数进行预估[22],预估会出现一个结果,需要对此结果进行分析,若结果满足方程(2.3),则就不需要进行校正;若估算出的数值不满足此方程(2.3),那么就必须对结果进行不断地校正。直到满足方程(2.3)为止。第三步,对系统进行静力学、运动学和初始条件分析。(1)静力学分析进行静力学分析的时候,需要注意的一点是,要假定速度是0,同样,进行准静力学分析是,也是需要注意一点,即假定加速度为0,通过上述分析,可以建立静力学方程:FT()qqqF(2.7)0jjqj(2)运动学分析运动学分析是研究系统的速度、加速度、约束反力和系统位置,因此只需求解系统约束方程:(q,t)0(2.8)n通过约束方程的Newton-Raphson迭代可求得某一时刻的位置:10\n第二章多体系统动力学及ADAMS仿真原理q(q,t)(2.9)jjjnq公式中的qqq,j表示第j次迭代。j1j对约束方程求一阶、二阶时间导数可以得出t时刻速度、加速度:n.()q(2.10)qt..2nn2....()q2qqklqq(2.11)qtk1l1qqklxqqtt时刻约束反力的确定,可由带乘子拉格朗日方程得到:nTTTdTTQ(2.12).qdtqq(3)初始条件分析对于初始条件分析,是通过求解目标函数最小值得到的,这些目标函数包括相应的位置、速度和加速度。在分析过程中,第一步要进行的是对初始位置的分析,第二步是对初始速度进行分析,第三步对初始加速度和初始拉氏乘子进行分析。2.4车辆动态仿真分析软件ADAMSADAMS软件是由美国MDI公司开发出来的机械系统动力学软件,它是在多刚体系统动力学基础上进行开发的,该软件不仅是世界上最热门的研究方向(虚拟样机技术)的代表,而且还是世界上市场占有率最高的机械系统动力学软件。下面主要介绍ADAMS的三个模块在本文中的应用,即ADAMS/Car、ADAMS/PostProcessor和ADAMS/Insight。本文利用ADAMS/Car建立了用于仿真的麦弗逊悬架模型,Car模块有两个界面,一个是标准界面,另外一个是专家用户界面,本文所研究的麦弗逊悬架,在标准界面中有专门的麦弗逊悬架模板,本文的做法是从中直接调用现有的麦弗逊悬架模板,然后对麦弗逊悬架的一些参数进行修改,最后得出用于仿真的麦弗逊悬架模型。除了建立模板之外,在Car模块中还进行了模型的仿真。ADAMS/PostProcessor模块俗称后处理模块,是用于分析仿真完成的分析,在Car模块中仿真之后,就可以直接进入到后处理模块,设定坐标轴的横坐标为Wheeltravel,11\n长安大学硕士学位论文可以查看所分析的目标函数随着车轮上下跳动的变化曲线。在后处理模块可以直观明了的看出哪些目标函数的变化范围不满足理想的要求。并且可以这这里对比优化前后曲线的变化情况。ADAMS/Insight功能比较强大,本研究课题在Insight中进行了试验设计和优化分析,试验设计的结果可以上传到专门的网页上,在此网页中,可以查看到各个设计变量对目标函数的影响程度,据此可以确定哪些因子是主要因子,从而可以更好的选择优化设计中的设计变量,以节约试验时间,提高工作效率。2.5本章小结本章主要介绍了论文所涉及到的基本理论,详细的介绍了多体系统动力学的有关知识,并对其中涉及到的公式做了简单的描述。另外,介绍了ADAMS软件的几个模块在本文中的应用,为下一步建立麦弗逊悬架模型提前做好准备。12\n第三章麦弗逊前悬架虚拟样机建模第三章麦弗逊式前悬架虚拟样机建模3.1麦弗逊式前悬架结构分析3.1.1麦弗逊悬架的简化和假设本文对悬架运动学模型进行简化,这样有利于进行运动学仿真分析,简化和假设如下[26]:(1)悬架中的杆件随着车轮的跳动不发生变形,假定杆件均为刚体;(2)不考虑车轮的变形,把车轮简化为刚体;(3)零部件之间的内部间隙不计,并且连接都简化为铰链;(4)所有零部件都认为是刚体,各运动副均为刚性连接,忽略各个运动副之间的摩擦力;(5)车身相对地面不动,仅研究悬架的特性。3.1.2麦弗逊悬架模型的运动学分析776A9I458BC73ME211.A字形控制臂2.转向节3.车轮轴4.车轮5.支柱性减震器6.螺旋弹簧7.汽车车架8.转向横拉杆9.转向器齿条图3.1麦弗逊悬架示意图前轮定位参数在此模型中可以通过计算得到:车轮外倾角:=arctan((ZZ)/(YY))(3.1)BMBM前轮前束角:=arctan((XX)/(YY))(3.2)BMBM主销内倾角:=arctan((YY)/(ZZ))(3.3)AEAE13\n长安大学硕士学位论文主销后倾角:=arctan((XX)/(ZZ))(3.4)AEAE上图中,E点是转向节和下摆臂连接的球铰中心点;B点是轮轴的内侧端点;M是轮轴的外侧端点;A点是车架和减震器相连的铰接点。下面结合麦弗逊式悬架的结构来研究其运动学特性。由于麦弗逊悬架是独立悬架,左右两边悬架结构形式一样,所以下面分析悬架的1/2模型,悬架刚体部件之间的运动副如表3.1所示,统计出的约束副类型和数量如表3.2所示。表3.1悬架刚体部件之间的运动副序号存在约束的刚体对约束关系1转向节总成—下三角控制臂球铰2转向节总成—转向横拉杆球铰3下三角控制臂—车架旋转副4转向节总成—车轮旋转副5转向节总成—减震器上体圆柱副6减震器上体—车身万向节副7转向横拉杆—转向齿条万向节副8转向齿条—车身移动副9车架—车身固定副表3.21/2前悬架模型约束副类型和数量约束副类型约束副限制自由度数约束副数量万向节42圆柱副41球铰链32移动副5114\n第三章麦弗逊前悬架虚拟样机建模约束副类型约束副限制自由度数约束副数量旋转铰链52固定铰链611/2前麦弗逊悬架自由度为:DOF674241325152613(3.5)所以,1/2麦弗逊悬架能够在三个方向运动,分别为:车轮的上下方向的跳动、车轮绕主销轴线的转动以及车轮绕着车轴的转动。3.2麦弗逊式前悬架虚拟样机模型建立3.2.1建模数据准备本论文实验悬架的结构参数以及关键硬点坐标如表3.3和3.4所示:表3.3整车相关主要参数结构参数数值大小车轮半径(mm)300轮胎垂直刚度(N/mm)200轮胎质量(kg)18簧载质量(kg)1080质心高度(mm)500轴距(mm)2540表3.4硬点参数列表硬点名称XYZ驱动轴内支点0.0-150220.0下控制臂前支点-200.0-400150.0下控制臂外支点0.0-700150.015\n长安大学硕士学位论文硬点名称XYZ下控制臂后支点200.0-400150.0螺旋弹簧下支座点40.0-600600.0减震器下安装点40.0-600600.0副车架前支点-400.0-400150.0副车架后支点400.0-400150.0转向横拉杆内支点200.0-350300.0转向横拉杆外支点150.0-700300.0减震器上安装点60.0-550.0800.0车轮中心0.0-750300.0根据以上参数,就可以在ADAMS中的Car模块建立悬架模型,上述的硬点坐标对于建模时非常重要的,它决定了各个部件之间的相对空间位置,并且每个部件的三个方向的硬点坐标也决定了悬架的各个定位参数的取值。如果硬点坐标设计的不精确,那么仿真分析出来的结果会很不理想,所以,在接下来的建模过程中,应该特别注意各个硬点坐标的取值。3.2.2麦弗逊式悬架子系统及悬架总成创建过程在ADAMS/Car中创建麦弗逊悬架的顺序大致是:首先,创建控制臂、装向节总成和滑柱、减震器与转向横拉杆、螺旋弹簧、参数变量,然后定义约束并且创建悬架子系统,最后把各个子系统装配起来。由于对模型进行的仿真都要基于装配组合,因此,还要把系统与试验台装配起来。上述简单介绍了在ADAMS/Car中建立麦弗逊悬架的过程,本文为了把更多的时间安排在之后的仿真和优化当中,并没有从头开始建立悬架模型,因为ADAMS/Car的模板库中有麦弗逊悬架子系统和前悬架子系统,在子系统的基础上装配前悬架总成,麦弗逊悬架子系统、齿轮齿条转向系统和前悬架总成模型图分别如图3.2、3.3和3.4所示:16\n第三章麦弗逊前悬架虚拟样机建模转向节转向横拉杆螺旋弹簧三角形下摆臂减震器图3.2悬架子系统结构图图3.3转向子系统结构图17\n长安大学硕士学位论文图3.4麦弗逊式前悬架系统总成3.3本章小结本章介绍了试验需要建立的麦弗逊前悬架具体的建模构件以及各自之间的链接关系。并且详细的介绍了麦弗逊悬架的结构特点。根据厂家提供的悬架硬点坐标等参数建立了麦弗逊悬架模型,同时分析了该模型的自由度,为下一章悬架的仿真分析提供可靠的依据。18\n第四章麦弗逊前悬架仿真及影响因素分析第四章麦弗逊式前悬架仿真及影响因素分析4.1麦弗逊悬架运动学仿真过程运动学仿真分析主要目的是为了试图找出早期悬架设计中结构上存在的问题,分析出问题主要出现在什么地方,为下一步的优化改进分析做准备。麦弗逊悬架仿真的基本过程如图:打开已经建立分析仿真结果好的前悬架模进行仿真试验并绘制试验曲型线图图4.1悬架系统仿真的基本过程由于麦弗逊悬架是左右对称的,所以只对左悬架进行分析,运用ADAMS软件对悬架进行运动学仿真分析时,主要方法有三种,分别如下:左右车轮同向跳动,左右车轮反向跳动,单轮跳动。本文采用左右车轮同向跳动实验和左右车轮异向跳动实验,本文考虑的是左边车轮定位参数随左侧车轮上下跳动量的变化关系曲线。采用ADAMS软件自带的标准悬架实验测试台,给测试台输入一个激励,左右测试台各施加一个驱动约束,使左右车轮同向和异向分别上下跳动正负50mm进行仿真分析。首先,进行双轮同向跳动分析。具体的参数设置如图4.3所示,图4.2是根据第三章中表3.3所进行的设置。19\n长安大学硕士学位论文图4.2车辆及悬架参数的设定图4.3悬挂同向激振仿真设置对话框20\n第四章麦弗逊前悬架仿真及影响因素分析仿真结束后,在该界面按照如下步骤查看车轮跳动的动画,在Review下拉菜单中选择AnimationControls,出现如下界面,在该界面中,把Cycles设置成10,方便更好的查看动画。图4.4动画控制菜单4.2双轮同向跳动时车轮前束角分析4.2.1车轮前束角对整车性能的影响(1)前束角的定义汽车纵向中心平面与车轮中心平面和地面的交线之间所成的夹角叫做车轮前束角[27]。如果车轮的前部向内缩,则成为正的前束角;反之则为负值。左右车轮的前束角之和成为总前束角。21\n长安大学硕士学位论文汽车行驶方向汽车纵向平面车轮中心平面前束角X车轮Y转向节汽车横向平面MD转向节轴颈轴线前束角图4.5车轮前束角在汽车行驶过程中,随着路面的不平或其他原因,车轮是上下跳动的,前束角也是随之变化的,前束角的大小对汽车的很多性能都有影响。如果前束角不在合理的范围内变化,那么车辆的直行稳定性、稳态转向响应特性都会受到影响,前束角是悬架的重要设计参数之一[28,29]。(2)前束角对整车性能的影响1)前束角用来补偿车轮外倾角所引起的不良影响在传统的悬架设计中,前束的主要作用是用来弥补外倾角所带来的不利影响,减少轮胎的磨损[30]。在前轮外倾之后,理论上来说,当汽车行驶时,轮胎外侧与地面的接触面积大,轮胎上点的线速度是不同的,外侧线速度比内侧小,但是,实际上,汽车沿直线行驶时,轮胎上点的线速度是相等的,这样,轮胎就会出现滑动,从而使轮胎磨损加快。对于这种现象,就出现了前束角。前束角使得车轮在运动之前反向偏转,从而可以抵消一部分外倾角所引起的偏转。根据外倾角的选择情况,来调整前束角,是之达到最合适的要求,从而可以避免车轮在行驶过程中出现滑动现象,避免了轮胎的快速磨损,提高了汽车的22\n第四章麦弗逊前悬架仿真及影响因素分析经济性和使用年限。2)前束角能保持车辆直线行驶的稳定性现代汽车设计观点认为,前束的作用除了抵消外倾角带来的影响,其主要的作用是补偿和防止车轮后束,因为车轮后束会使车辆直线行驶出现不稳定[31]。在汽车运动过程总,如果汽车带有后束,当车轮受到来自路面的侧向力时,在某个瞬间,汽车的某一个车轮可能处于前进方向,另外一个车轮在处于后束的情况下,汽车会处于转向状态,另外,由于处于前进方向的车轮受到的行驶阻力小,有后束的车轮受到的行驶阻力会增大,此时,会进一步增大汽车的转向角度,使汽车处于危险的状况。当汽车带有前束角时,行驶中的汽车会受到侧向力或者来自路面的作用,使得汽车的某一个车轮处于瞬时的直线运动,另外一侧车轮前束角会相应的增加,汽车处于转向状态,但是由于车轮前束的增加能够产生附加阻力,这个附加阻力能够促使车轮回正,从而,使得汽车回到直线行驶的状态。汽车的驱动形式决定了车轮前束角的正负,如果汽车是后轮驱动,那么车轮前束一般取正前束,原因是,当后轮驱动的汽车在行驶是,由于纵向力的作用,车轮会产生负前束,所以为了抵消由此产生的负前束,前束角一般取一定的正前束。反之,若是前驱的汽车,一般情况下,前束角调整为稍微的负前束,目的是能使汽车直线运动性能能加,从而减少行驶过程中轮胎的磨损。有些厂家考虑到汽车在前驱的情况下,有时候在一些非驱动的时候(如制动),车轮会产生负前束,这样会导致影响汽车的行驶稳定性,所以,有些前驱的汽车也会取一定的正前束[32]。(3)前束角的理想变化趋势汽车在行驶当中,车轮是上下跳动的,在这个过程中,前束角最好是保持不变或者变化范围很小,否则,会影响轮胎的寿命和汽车的行驶稳定性。如果前束角变化范围过大,轮胎的侧偏会比较明显,同时滚动阻力会随之增加。另外,前束角变化过大,会导致转向横拉杆受力增加,会影响转向杆球头的寿命。在进行车轮前束设计时,一般比较理想的范围是车轮上跳50mm时,前束角变化范围应该在应该在0˚~-0.5˚,车轮下跳50mm时,前束角理想变化范围在0˚~0.5˚。这样,在设计前束角时,应该注意以下两个方面,当车轮上跳时,车轮前束角应该是为零或者成弱负角,而当车轮下落时,前轮前束应该朝正值变化。23\n长安大学硕士学位论文4.2.2车轮前束角仿真分析仿真完成之后,进入到后处理模块,车轮前束角的变化曲线如图4.6所示。横坐标表示车轮上下跳动的距离,纵坐标表示车轮前束角的大小。图4.6双轮同向跳动下前束角的变化曲线上图表示在车轮上下跳动过程中,车轮前束角的变化曲线。设计原则是车轮跳动时前束角变化范围越小越好。图中,前束角初始值为弱负值,跳动过程中的变化范围是-1.15~1.1,变化量是2.25,变化范围较大,很明显的超出了较理想的设计值,在第五章的优化中应将前束角作为一个优化目标。4.3双轮同向跳动时车轮外倾角分析4.3.1车轮外倾角的定义及其对整车性能的影响(1)车轮外倾角的定义车轮外倾角是指通过车轮中心的汽车横向平面与车轮中心平面的交线与地面的垂线之间的夹角[33,34]。外倾角也有正负值之分,当车轮的上端倾离车身时,外倾角为负值,当车轮的上端倾向车身时,外倾角为正值。如图4.7所示。24\n第四章麦弗逊前悬架仿真及影响因素分析车轮中心平面地面垂直线外倾角Z车轮X转向节外倾角转向节轴颈轴线D地面平行线DM地面N图4.7车轮外倾角(2)外倾角对整车性能的影响车轮外倾角对汽车操纵稳定性有很大影响,外倾角的变化影响车辆直线稳定性和轮胎磨损等[35,36]。车轮外倾角对整车的影响主要分为两个方面。首先,对汽车的直线行驶稳定性和转向性能有影响。汽车行驶过程中,当汽车需要制动时,会产生相应的纵向力,此时,纵向力会导致汽车有转向的倾向。此时,由于轮胎受到车轮外倾角的影响,使得其接地点向内缩,偏距减少,改善了汽车制动时的行驶稳定性,也可以使转弯时打方向盘比较容易。目前,很多的乘用车前轮都有一定的外倾角,角度一般为1˚左右。其次,外倾角可以避免轮胎过度磨损。汽车是用来载人或者载货的,当汽车负载之后,由于汽车悬挂系统各零部件的变形,使得车轮上端有向车身方向内缩的趋势,这样车轮就不可能垂直于地面行驶了,会加剧轮胎的磨损。而车轮有了轻微的正外倾角之后,会抵消由于负载所产生的负的车轮外倾角,使得汽车负载情况下,前轮外倾角保持在0˚。外倾角不能取较大的正值,因为较大的正值会使轮胎外侧接地面积较大,加大轮胎的磨损。(3)车轮外倾角理想变化趋势汽车在行驶过程中,无论是直线行驶还是曲线行驶,都会引起车轮外倾角的变化,此时如果外倾角变化过大,就会影响汽车的性能。比如,当汽车曲线行驶时,车身会往25\n长安大学硕士学位论文外倾斜,此时,外侧车轮也会随着往外侧倾斜,这样会影响轮胎的侧偏性能。车轮外倾角的理想变化趋势为:外倾角随着车轮的上跳朝着负值方向变化,外倾角随着车轮的下落朝着正值方向变化[37]。在外倾角变化过程中,其变化范围不应该过大,因为外倾角变化过大,产生的外倾推力就会很大,随之,产生的横向力也就比较大,会影响悬架性能,较大的外倾角变化会使车辆的直线稳定性不好[38]。所以,一般情况下,车轮在±50mm的范围上下跳动时,外倾角变化范围在1˚~2˚。4.3.2车轮外倾角仿真分析图4.8双轮同向跳动下车轮外倾角变化曲线图4.8表示车轮外倾角随着车轮上下跳动的变化曲线。横坐标表示车轮的跳动位移,纵坐标表示车轮外倾角。图中可以看出,当车轮没有上下跳动时,外倾角的初始值采用弱负值,此种设计可以提高汽车转向时的抗侧倾能力。一般情况下,我们认为车轮外倾角的理想变化范围是:车轮在上下跳动±50mm的范围内,车轮外倾角的变化范围在1°~2°。从上图可以看出,随着车轮的上下跳动,外倾角的变化外围是-0.90°~1.35°,变化量为2.25°,变化范围不在理想范围内,在下一章需要对外倾角进行优化,使之达到理想的范围。4.4双轮同向跳动时主销后倾角分析4.4.1主销后倾角的定义及其对整车性能的影响(1)主销后倾角的定义主销后倾是四轮定位中的一个项目,是设计汽车转向桥时使主销与车轴纵向平面内有一个向后的倾角,即主销轴线与地面的垂线之间的夹角,称为主销后倾角。主销后倾角是一个重要的参数,它对悬架的性能有很大影响,如果主销后倾角不满足要求,悬架的使用性能会大大降低,主销后倾角分为正后倾角和负后倾角,若主销轴线向地面垂26\n第四章麦弗逊前悬架仿真及影响因素分析直线后面倾斜,那么称为正后倾角,否则,称为负后倾角。主销地面垂直线AZ后倾角Y汽车行驶方向E图4.9主销后倾角(2)主销后倾角对整车性能的影响汽车主销后倾的作用主要是为了保持汽车直线行驶的稳定性,并使汽车转向后,前轮有自动回正的作用。主销后倾角都是取正值。其作用原理主要有下面几个方面:从上图可以看到,主销轴线与地面的接地点总是在轮胎与地面接地点的前面,主销轴线与地面接地点总是在轮胎所受阻力作用点之前,这样,在车轮运动过程中,相当于主销拖着车轮前进,这样可以保证汽车直线行驶稳定性。当汽车行驶过程中遇到弯道时,车轮转向,此时车轮会受到一定的阻力,由于这个阻力的作用线不通过主销轴线,这样,阻力会形成一个反向力矩,这个力矩迫使车轮自动偏转,直到车轮所受阻力作用线通过主销轴线,此时,车轮已经回正,这就是转向车轮的自动回正功能。汽车在转向时产生的绕主销的回正力矩M主要成分为:skMF(nn)(4.1)skxkR其中:Fx表示轮胎的侧向力;nk表示主销后倾拖距;nR表示轮胎的拖距。(3)主销后倾角的理想变化趋势在进行四轮定位时,主销后倾角既不能过大也不能过小,如果主销后倾角过大,会使转向变得沉重,驾驶员容易疲劳;如果主销后倾角过小,当汽车直线行驶时,容易发生前轮摆振,转向盘摇摆不定,转向后转向盘自动回正能力变弱,驾驶员会失去路感。27\n长安大学硕士学位论文一般来说,对于前置前驱轿车,主销后倾角的初始值设置在3˚左右。4.4.2主销后倾角的仿真结果分析图4.10双轮同向跳动下主销后倾角变化曲线图4.10为主销后倾角随车轮上下跳动的变化曲线。一般要求主销后倾角在2°~6°之间变化,从图中看出,主销后倾角初始值为5.4°,主销后倾角随着车轮上下跳动的变化范围为4.95°~6.39°,变化量为1.44°,不符合理想的范围,所以需要对这个参数进行优化。4.5双轮同向跳动时主销内倾角分析4.5.1主销内倾角的定义及其对整车性能的影响(1)主销内倾角的定义从汽车的前面看去,主销轴线与通过前轮中心的垂线之间形成一个夹角,即主销内倾角。如图4.11所示,主销轴线上侧向内倾斜时为正,反之为负。28\n第四章麦弗逊前悬架仿真及影响因素分析地面垂直线AZ前束角内倾角减震器上体X减震器下体车轮主销转向节MODE下摆臂NP主销偏移距图4.11主销内倾角和偏移距示意图(2)主销内倾角对整车性能的影响车轮定位参数是相辅相成的,各个参数之间都会有一定的影响,前面介绍的主销后倾角会产生回正力矩,根据公式MF(nn)可知,M与F(轮胎的侧向力)成skxkRskx正比。当汽车在弯道上行驶时,F与车速的平方成正比。车速越高,F越大,此时回xx正力矩就会越大。但是,汽车是在不同的工况下行驶,不可能一直保持着高速行驶,当车速很小的时候,F相应的比较小,这样,由(主销后倾角)和n(轮胎的拖距)xR产生回正力矩就会比较小。但是,实际中,汽车在低速行驶工况下也需要回正力矩,这是就需要一个定位参数,使其产生的回正力矩不受汽车速度的影响,于是,就设计了主销内倾角。主销内倾角主要作用是使转向轮自动回正,并使转向轻便。当汽车在弯道上行驶时,如果主销内倾角很大,那么汽车前部抬起的越高,此时车轮自动回正能力越强。因为,29\n长安大学硕士学位论文当汽车在弯道行驶时,车轮会绕着主销轴线转动,理论上来说,轮胎最低点应该转动到路面以下,由于轮胎下边缘不可能进入到地面以下,此时,会使转向车轮和整个汽车前部向上抬起一个高度,这样的话,汽车前部会产生一个重力,这个重力会使转向车轮产生回到原来位置的作用,因此,方向盘回位更容易。这种产生回正力矩的方式称为重力回正。由于主销后倾角的作用,主销轴线与地面接地点到轮胎接地点有一定的距离,而有了主销内倾角以后,使得主销轴线与地面接地点到轮胎接地点距离缩短,这样有利于减少转向时所需的力,使转向轻便,减少驾驶员疲劳程度,同时,主销内倾角减少了转向轮传到方向盘上的力。但主销内倾角也不宜过大,这样会加速轮胎的磨损。主销内倾角产生回正力矩的原理如下面公式所示:sin2MGnsin(4.2)sGfl2Gf:前轴负荷;nl:轮心处主销的侧向偏距;:主销内倾角;:前轮转角。公式中显示,当n和时,回正力矩(主销内倾角所产生的)几乎与主销内倾角成l正比,所以,增加主销内倾角有利于提高汽车重力回正的效果。(3)主销内倾角合理变化趋势在汽车行驶过程中,随着车轮的上下跳动,主销内倾角也会随之变化,但是变化的范围尽可能比较小,当车轮上跳时,主销内倾角应该有变大的趋势,当车轮下落过程中,主销内倾角应该有减小的趋势。一般情况下,为了使主销内倾角对整车的影响在合理的范围内,随着车轮的上下跳动,主销内倾角变化范围在7˚~13˚之间比较合适。4.5.2主销内倾角的仿真结果分析图4.12双轮同向跳动下主销内倾角的变化曲线30\n第四章麦弗逊前悬架仿真及影响因素分析从图4.12可以看出,主销后倾角随着车轮的跳动,其变化范围为11.85°~13.75°,超过了理想的范围,在下一章需要对其进行优化。4.6双轮同向跳动时主销偏移距分析4.6.1主销偏移距的定义及其对整车性能的影响(1)主销偏移距的定义主销轴线所在的直线与地面的交点到车轮中心平面与地面的交线之间的距离称为主销偏移距。当主销轴线的延长线与路面的交点在轮胎接地点的内侧时主销偏移距为正,反之为负,如图4.11所示。(2)主销偏移距对整车性能的影响合理的主销偏移距能使汽车保持直线行驶。主销偏移距与主销内倾角有密切关系。轿车上的智能制动系统和智能驱动系统会使车辆两端车轮所受到的侧向力不同,在这种情况下,主销偏移距绝对值不能过大,否则,会导致方向盘难以控制,这样会影响汽车直线行驶稳定性,使得驾驶员驾驶汽车产生疲劳,对汽车行驶安全性有严重影响。如果r=0时,汽车两端车轮所受到的不平衡纵向力就不会影响到方向盘力矩。但是,当车轮s上下跳动时,r不可能始终为零,反而会随着车轮跳动而发生变化,因此,在进行设计s时,主销偏移距的初始值设置成0附近,并且在车轮跳动时,变化不应该很大。理想的变化范围是-10mm~30mm。4.6.2主销偏移距的仿真结果分析图4.13双轮同向跳动下主销偏移距的变化曲线从图4.13可以看出,车轮上下跳动过程中,主销偏移距的变化趋势接近理想的范围,在后期的优化过程中,不需要把它作为一个目标函数,但是在优化其他几个参数的过程31\n长安大学硕士学位论文中,尽量使主销偏移距的范围缩小,使之达到最优的结果。4.7双轮异向跳动仿真分析双轮异向跳动模拟车身因侧倾而引起悬架的运动。在ADAMS/Car模块中,分别给两侧车轮输入方向相反但大小相同的垂直激励。最后得出车轮定位参数随车轮跳动的变化规律曲线。4.7.1车轮前束角图4.14为车轮异向跳动和车轮同向跳动前束角随着车轮变化的对比图,从图中可以看出,车轮异向跳动时,前束角的变化范围在-1.25~1.15,比车轮同向跳动时前束角的变化范围大。不过两种实验得出的结果都是前束角变化范围不符合要求。图4.14车轮异向跳动与车轮同向跳动前束角变化对比图4.7.2车轮外倾角由图4.15中可以看出,车轮外倾角在车轮异向跳动和车轮同向跳动时的变化规律只有细小的差别。图4.15车轮异向跳动与车轮同向跳动外倾角变化对比图32\n第四章麦弗逊前悬架仿真及影响因素分析4.7.3主销后倾角从图4.16中可以看出,主销后倾角在车轮异向跳动和车轮同向跳动时的变化规律几乎没有区别。图4.16车轮异向跳动与车轮同向跳动主销后倾角变化对比图4.7.4主销内倾角从图4.17中可以看出,主销内倾角在车轮异向跳动和车轮同向跳动时的变化规律几乎完全相同。图4.17车轮异向跳动与车轮同向跳动主销内倾角变化对比图4.7.5主销偏移距从图4.18中可以看出,主销偏移距在车轮异向跳动和车轮同向跳动时的变化规律也几乎完全相同。33\n长安大学硕士学位论文图4.18车轮异向跳动与车轮同向跳动主销偏移距变化对比图根据上面的双轮同向跳动和双轮异向跳动仿真分析结果,我们可以得出车轮定位参数的四个参数都需要优化,下一个章节将以这四个定位参数为目标函数进行优化设计。4.8本章小结本章针对所研究的五个参数进行了详细的介绍,并且对所建立的悬架进行了仿真分析,通过分析得出悬架存在了以下问题:车轮的四个定位参数随着车轮跳动的变化曲线均不满足理想的范围。因此,在下一章的优化部分,需要把车轮外倾角、主销内倾角、主销后倾角和前束角均设置能目标函数,使定位参数均达到理想的范围,保证汽车有良好的行驶稳定性。34\n第五章麦弗逊悬架优化分析第五章麦弗逊式前悬架优化分析5.1优化设计的方法参数化分析可以了解设计变量对模型参数的影响。在ADAMS中,有三种参数化方法。具体介绍如下:(1)设计研究设计研究通常是研究单一的设计变量对系统性能的影响,比如,如果研究横拉杆外支点Z方向坐标的坐标对各个参数的影响,就定义横拉杆外支点Z方向坐标在某个范围内按照一定的规则取值,然后针对每一次取值,都对悬架模型进行一次仿真分析,在后处理模块可以分析各次仿真的结果。(2)试验设计设计研究是研究一个变量对样机性能的影响,而试验设计讨论的是多个变量同时发生变化时,各个设计变量对于样机性能的影响[39]。Insight模块是ADAMS专门用于试验设计的模块,功能更加健全,本文就是选用这个模块进行试验设计,最终能得到各个设计变量对目标函数的影响程度。(3)优化分析优化分析的主要作用是获得最佳的目标函数值,既当设计变量满足规定的约束条件时,目标函数取最值,包括最大值或最小值。在优化分析过程中,必须要规定约束,如果没有这一步,目标函数可能会有无数个解,也可能无法排除不满足条件的设计方案[40,41,42,43]。一般试验设计和优化分析是结合起来运用的,一个系统的变量有很多个,如果全部作为设计变量,浪费时间和精力。在优化分析过程中,可以先通过试验设计,找出对样机性能影响较大的因素,然后,在进行优化分析时,把这些影响较大的因素作为设计变量,对这些变量进行优化。5.2ADAMS的试验设计5.2.1试验设计原理试验设计的理论基础是概率论与数理统计,它是一种研究如何高效而经济地获取所需要的可靠试验数据与有用信息并对其进行分析处理的方法[44]。本文中试验设计的主要作用是变量筛选,既当一个系统中有多个变量时,通常只有35\n长安大学硕士学位论文一小部分是重要的,筛选试验可以用来辨别这些重要的变量及其这些变量对于系统性能影响的程度。5.2.2ADAMS试验设计的过程和方法在试验设计中,主要分为以下四步:首先,要明确试验目的。试验设计的目的是在众多变量中找出对样机性能影响比较大的参数,并且要确定好目标函数作为评价目标。其次,制定试验方案。给每一个设计因子都限定一个范围,试验因子只能在此范围内变化,然后将所有的组合情况排列成试验设计矩阵。再次,就是进行试验。在ADAMS中进行仿真,系统会自动针对每一种变量取值情况都进行一次仿真,仿真的结果都会被记录下来,然后,软件会自行分析试验结果,并把它们用一定的形式呈现出来,让设计人员比较方便的查看影响系统性能最大的因子[45]。在ADAMS中,有两个模块可以实现上述的试验设计,分别是View模块和Insight模块,它们之间的作用是相互补充的,各有优缺点,本论文所采用的是ADAMS/Insight模块,因为ADAMS/Insight模块能比较精确的对系统性能进行预测,并且对试验设计的规模不作限制,使得建立拟合多项式来分析系统的性能更加方便。5.3麦弗逊悬架的试验设计由于本文对悬架只进行了悬架运动学分析,没有进行弹性运动学分析和动力学分析,所以在进行优化分析时,不考虑质量和受力的影响。在对麦弗逊悬架进行优化分析时,不考虑前轴载荷对优化结果的影响。所以,本文在对硬点坐标进行优化时,不需要考虑前轴载荷的影响。在同类研究文章中,多数的文章直接选取多个硬点进行优化分析,把每个硬点的三个方向都作为试验因子。然后得出优化方案,这种策略不是优选,其缺点是浪费大量的试验时间以及对问题的解决不是很有效,因为有些硬点坐标对优化结果影响比较小。本文参考其他文献,根据实际情况,选取下控制臂前支点X、Y、Z方向、下控制臂外支点X、Y、Z三个方向、下控制臂后支点X、Y、Z方向、减震器上安装点X、Y、Z三个方向、转向横拉杆外支点X、Y、Z方向和转向横拉杆内支点X、Y、Z方向,共计18个因子进行试验设计。得出各个因子对系统性能的影响程度,然后根据分析,再确定优化设计时选择哪些作为设计变量。如下图所示。图中可以看出“Effect”和“Effect%”的取值有正值和负值,正值表示响应与因子成正比;负值表示响应与因子成反比。正值和负值不影响判断因子对响应影响程度的大小,因子的“Effect%”绝对值越大,36\n第五章麦弗逊悬架优化分析表明该因子对于响应的影响程度越大。下图表示18个因子对四个响应的影响程度。从图中可以看出,其中有10个因子对响应的影响程度都比较高,分别是下控制臂前支点Z方向、下控制臂外支点X、Y、Z三个方向、下控制臂后支点Z方向、减震器上安装点X、Y、Z三个方向、转向横拉杆外支点Z方向、转向横拉杆外支点Z方向。所以在优化分析阶段,将这10个因子作为设计变量。图5.118个因子对车轮外倾角的影响图5.218个因子对车轮后倾角的影响图5.318个因子对主销内倾角的影响37\n长安大学硕士学位论文图5.418个因子对前束角的影响从上面几幅图中统计出每个定位参数的影响因素,如下表所示:表5.1影响外倾角的因素FactorEffect%top_mount.y14.85top_mount.z-7.92tierod_inner.z2.34tierod_outer.z-1.99lca_front.z1.6lca_outer.z-1.55tierod_outer.y1.03lca_front.y-0.36tierod_inner.y-0.26top_mount.x0.25lca_outer.y-0.21lca_rear.z0.2tierod_outer.x-0.18lca_outer.x-0.1638\n第五章麦弗逊悬架优化分析表5.2影响后倾角的因素FactorEffect%top_mount.z-2.9lca_outer.x-2.88top_mount.x1.97lca_outer.z0.6lca_front.z-0.59lca_rear.z0.52lca_rear.y0.24lca_front.y-0.23top_mount.y-0.11tierod_inner.z0.07tierod_outer.y0.04表5.3影响主销内倾角的因素FactorEffect%lca_outer.y-9.03top_mount.y7.17top_mount.z-2.58lca_outer.z0.16lca_front.z0.16lca_rear.z0.16lca_rear.y0.0539\n长安大学硕士学位论文表5.4影响前束角的因素FactorEffect%tierod_inner.z24.78tierod_outer.z-21.05lca_rear.z-11.3top_mount.y10.92tierod_outer.y10.9lca_outer.y-9.6lca_outer.z8.45top_mount.z-7.8tierod_inner.y-2.75top_rear.y2.68tierod_out.x-1.88lca_front.z1.37lca_outer.x1.25top_mount.x1.22top_front.y-0.51因此当需要调整悬架某些性能可以利用上面的表格方便的找出。5.4对悬架进行优化分析具体步骤如下:(1)建立设计变量本节通过分析试验设计的结果,根据实际经验并且结合麦弗逊悬架简化模型,在保证优化后使车轮定位参数符合理想范围的前提下,要求对悬架系统的改动量越少越好。40\n第五章麦弗逊悬架优化分析最终,选取下控制臂外支点X、Y、Z三个方向、下控制臂前支点Z方向、下控制臂后支点Z方向,减震器上安装点X、Y、Z三个方向,转向横拉杆内支点Z方向,转向横拉杆外支点Z方向,共计10个设计变量。(2)建立目标函数设计变量建立完成之后,就要开始对目标函数进行创建,本文建立了四个目标函数,建立过程如下图所示。图5.5创建目标函数:车轮外倾角图5.6创建目标函数:主销后倾角图5.7创建目标函数:车轮前束角41\n长安大学硕士学位论文图5.8创建目标函数:主销内倾角(3)建立好目标函数之后,然后从Car模块进入Insight模块,如下图所示。图5.9进入ADAMS/Insight界面(4)创建因素和响应1)创建因素:在ADAMS/Insight界面下按照图5.7步骤将下控制臂前点Z方向坐标的相关参数进行修改。42\n第五章麦弗逊悬架优化分析图5.10设计变量的位置修改界面如下图,本文采用的规定是,硬点坐标以初值为中心在上下10mm范围内取值。图5.11设置硬点变化范围之后,将此方向添加到inclusion目录下,并且运用相同的设置方法添加其他因素,添加完成后的示意图如下图所示。43\n长安大学硕士学位论文图5.12将10个变量添加到inclusion目录2)加响应:继续在这个界面中选择Responses/Candidates,按照上面添加设计变量的方法将四个响应目标添加到Responses的inclusion目录下,并进行设置。图5.13将四个响应目标添加到inclusion目录(5)选择试验策略:试验策略选择下图所示。图5.14试验策略的设置44\n第五章麦弗逊悬架优化分析(6)创建设计空间:按照如下步骤可以创建设计空间。Define—experimentdesign—CreateDesignSpace,创建完成后的设计空间如下图所示,图中的-1即该处的坐标取最小值,+1则取最大值。图5.15设计空间(7)创建工作矩阵:Define—experimentdesign—CreateWorkSpace,按照此步骤生成工作矩阵,如下图所示。45\n长安大学硕士学位论文图5.16工作矩阵(8)运行试验:接着在工具栏点击RunSimulation图标。系统会自动地返回到ADAMS/Car中进行仿真试验。下图为优化过程曲线。图5.17车轮外倾角优化仿真过程曲线46\n第五章麦弗逊悬架优化分析图5.18主销后倾角优化仿真过程曲线图5.19主销内倾角优化仿真过程曲线图5.20前束角优化仿真过程曲线在此次优化仿真过程中,选取的10个设计变量是根据上述试验设计所确定的,这些变量对于目标函数都有比较大的影响。优化后相关硬点坐标值取值如下表所示:47\n长安大学硕士学位论文表5.1设计变量的初始值和优化值硬点初始值优化值下控制臂外支点X坐标0.010.0下控制臂外支点Y坐标-700-702.0下控制臂外支点Z坐标150.0145.0下控制臂前支点Z坐标150.0160.0下控制臂后支点Z坐标150.0160.0转向横拉杆外支点Z坐标300.0310.0转向横拉杆内支点Z坐标300.0299.0减震器上安装点X坐标60.050.0减震器上安装点Y坐标-550.0-560.0减震器上安装点Z坐标800.0810.05.5优化前后仿真结果的比较上一节优化了10个设计变量,本节根据上节的内容,对麦弗逊悬架模型进行修改,通过对优化后的硬点坐标进行修改,对悬架再进行一次仿真,分析优化前后各车轮定位参数的变化曲线,如下图所示:图5.21车轮前束角变化情况(优化前后)48\n第五章麦弗逊悬架优化分析图5.22车轮外倾角变化情况(优化前后)图5.23主销后倾角变化情况(优化前后)图5.24主销内倾角变化情况(优化前后)49\n长安大学硕士学位论文图5.25主销偏移距变化情况(优化前后)表5.2车轮定位参数优化前后的对照表名称变化范围(优化前)变化量(优化前)变化范围(优化后)变化量(优化后)车轮前束角(°)-1.15~1.102.25-0.38~0.360.98车轮外倾角(°)-0.90~1.352.25-0.79~1.151.94主销后倾角(°)4.95~6.391.443.26~4.251.01主销内倾角(°)11.85~13.751.9010.76~12.952.19主销偏移距(mm)17.41~30.7213.3119.01~30.7511.74得出如下结论:(1)通过对部分硬点坐标进行优化,车轮定位参数随车轮上下跳动的变化范围符合理想要求,从上表可以看出,优化后的车轮前束角、车轮外倾角、主销后倾角变化量都比优化前的变化量小;(2)经过优化,主销偏移距变化范围是19.01~30.75,变化量是11.74,在此次优化过程中减小了1.57,主销偏移距的变化符合要求。5.6本章小结本章首先对模型进行了参数化分析;其次,对麦弗逊悬架的几个关键点坐标进行了灵敏度分析,找出对目标函数影响程度比较大的十个因子作为设计变量;最后,用ADAMS/Insight中的Optimize功能进行优化分析,优化后的车轮定位参数随车轮跳动的变化规律得到了一定程度的改善,取得了较好的效果,有利于提高汽车的操纵稳定性。50\n结论与展望结论与展望结论本文在ADAMS中建立了麦弗逊悬架仿真分析模型,通过进行双轮同向跳动实验和双轮异向跳动实验两次仿真分析,从而得出了结论:车轮定位参数随着车轮跳动的变化规律不满足理想要求。通过优化分析,得到优化后的硬点坐标,根据优化后的坐标更改悬架模型的参数,通过再一次的仿真分析,使车轮定位参数的变化规律均满足理想的要求。本文的结论可以概括为以下几点:(1)运用ADAMS软件建立了麦弗逊悬架仿真分析模型,并通过调整参数设置,使建立的模型更接近于实际的悬架模型;(2)通过对麦弗逊悬架进行双轮同向跳动实验和双轮反向跳动实验,发现车轮的四个定位参数随车轮跳动的变化范围均不满足理想的要求,表明该款车型的车轮定位参数设计的不合理;(3)利用ADAMS/Insight模块进行试验设计,找出了对目标函数影响较大的十个因子,然后以这十个因子作为设计变量对目标函数进行优化设计,最终使车轮定位参数随车轮跳动的变化范围满足理想要求,从而改善了汽车的操纵稳定性。展望本文还存在以下不足:(1)本文所用的模型是在软件原有子系统的基础上创建的悬架总成,作者在此基础上对硬点和其他的一些参数进行修改,模型比较简化,理论上应该建立精度高贴近实物的悬架模型;(2)本文对悬架只进行了运动学分析,若要更好的对悬架性能进行优化,应该采用悬架动力学和悬架运动学相结合的方法;(3)由于实验条件的限制,本文只运用计算机软件对悬架模型进行了仿真分析,没能进行具体的实车试验,应该把实车试验所得出的结论与仿真软件得出的结论进行对比,找出模型设计方面的问题,然后再进行优化设计。51\n长安大学硕士学位论文参考文献[1]张排排.轿车半主动悬架的参数优化及控制策略研究[D].武汉理工大学,2010[2]王望予.汽车设计[M],北京:机械工业出版社,2004.08[3]DonaldB.T.Carsuspensionandhandling[M].WarrendalePa.:SAEInternational,2004[4]WhitcombD.W.MillikenW,F.Designimplicationsofageneraltheoryofautomotivestabilityandcontrol[J].Proc.IMechE.Auto.Div,1957[5]SegelL.researchinfundamentalsofautomobilecontrolandstability[J].SAETrans,1957,Vol.65,pp527-540[6]Campbell.Newdirectionsinsuspensiondesign.Makingthefastcarfastermanual[J].CambridgeMassaRobertBentley,Ine.1981[7]戴逢权.多连杆悬架系统性能仿真研究[D],武汉理工大学硕士论文.2011:1-4[8]GenM.S.ChengR,W.Geneticalgorithmsandengineeringoptimization[M].Beijing:TisinghuauniversityPress,2004:30~50.[9]JagerB.D.RobustH2optimalcontrolofanactivesuspensioninProc.IEEEInternationalConferenceonControlApplications[J],1997:761~766.[10]GimGand,NikraveshP.E.Ananalyticalstudyofpneumatictypesforvehicledynamicsimulations[J].Part1:Pureslips,Int.J.ofVehicleDesign,1990,Vol.l1,No.6:589~618.[11]赵又群,郭孔辉.汽车操纵性评价指标的研究[J],汽车工程,2001(1):79~80[12]李宁.乘用车悬架KNC特性试验技术与装备研究[D].吉林大学硕士学位论文,2013.7[13]丁亚康,翟润国,井绪文.汽车麦弗逊悬架性能仿真和优化研究[J].中国公路学报,2014[14]芮筱亭,王国平.多体系统动力学研究发展[D].南京理工大学,2011.7[15]孙维超.汽车悬架系统的主动振动控制[D].哈尔滨工业大学博士学位论文.2013[16]陈立平等.机械系统动力学分析与ADAMS应用教程[M].北京:清华大学出版社[17]孙泽敏.基于ADAMS的某车悬架系统运动学仿真及优化[D].长春工业大学硕士学位论文,2014[18]陈清化.某汽车悬架的优化研究[D].西南交通大学,2013[19]詹文章.汽车独立悬架多体系统动力学仿真及转向轮高速摆振研究[D].吉林:吉林大学,200052\n参考文献[20]李善敏.真空断路器操动机构建模及动力学仿真研究[D].昆明理工大学,2012[21]俞凡.汽车动力学及其控制[M].北京:人民交通出版社,2003[22]郑建荣.ADAMS虚拟样机技术入门与提高[M].北京:机械工业出版社,2002[23]郑超.基于虚拟样机技术的轿车前悬架总成优化设计及整车仿真[D].西安建筑科技大学,2012[24]刘臣亚,刘淑艳等.麦式独立悬架运动学分析与优化[J].华南理工大学学报(自然科学版),2003,31(9):94-98[25]ReimpellJ,StollH.TheAutomotiveChassis:EngineeringPrinciples(SECONDEDITION)[M].USA:SAE,2002[26]刘惟信.汽车设计[M].北京:清华大学出版社,2001[27]玄圣夷.专家系统在麦弗逊悬架设计中的应用研究[D].吉林大学硕士学位论文.2007[28]李志永.车辆主动悬架的模糊滑模控制策略研究[D].吉林大学,2013[29]戴逢权.多连杆悬架系统性能仿真研究[D].武汉理工大学硕士学位论文,2011[30]姬鹏,朱天军.车轮跳动对定位参数影响的仿真分析[J].河北工程大学学报(自然科学版),2007,27(2):59-61[31]王孟.车轮定位参数视觉检测系统的研究与开发[D].沈阳工业大学,2012[32]孙海林.轿车多连杆悬架系统运动学特性的仿真分析[D].吉林大学硕士学位论文.2007[33]雷刚.基于ADAMS的麦弗逊式悬架系统的虚拟仿真分析及其优化设计[D].武汉理工大学硕士学位论文.2010[34]GentaG.L.MorellovLZ.TheAutomotiveChassisVol.2:SystemDesign[M].German:SpringerNetherlands,2008[35]耶尔森·赖姆帕尔.张洪欣译.汽车底盘基础[M].北京:科技普及出版社,1992[36]吴武明.基于刚柔耦合多连杆悬架运动学分析及优化[D].华南理工大学硕士学位论文.2010[37]魏道高.汽车前轮定位参数研究与展望[J].合肥工业大学学报(自然科学版),2004,27(12):4951-8951[38]王文.麦弗逊式前悬架运动学分析及优化研究[D].华南理工大学,2013[39]BlundellM.V..Theinfluenceofrubberbushcomplianceonvehiclesuspensionmovement[J].MaterialsandDesign,1998,(19):29-37.53\n长安大学硕士学位论文[40]李增刚.ADAMS入门详解与实例[M].北京:国防工业出版社,2006.[41]葛正浩.ADAMS2007虚拟样机技术汇[M].北京:化学工业出版社,2010.[42]石博强.ADAMS基础与工程范例教程[M].北京:中国铁道出版社,2007[43]范成建.虚拟样机软件ADAMS应用于提高[M].北京:机械一工业出版社,2006[44]刘全.基于虚拟样机技术某电动汽车悬架性能优化及研究[D].吉林大学,2013[45]王朝阳.基于ADAMS的电动汽车前悬架设计与优化[D].山东大学,2010.54\n致谢致谢在论文完成的过程中,除了我自己的潜心学习和研究之外,也凝聚了很多人的心血。所以在这里,我要对帮助我完成论文的所有人表示感谢。我谨以最真诚的心情向两年来在学习上、生活上给予我帮助的老师、同学、朋友以及亲人表达我真挚的感谢!首先,我要感谢我尊敬的导师——马骊溟老师。本研究及学位论文是马老师的亲切关怀和悉心指导下完成的。她严肃的科学态度,严谨的治学精神,精益求精的工作作风,深深地感染和激励着我。从课题的选择到项目的最终完成,马老师都始终给予我细心的指导和不懈的支持。马老师花费了许多宝贵的时间对我的论文进行审阅,给了我很多指导意见,使我能够顺利的完成毕业论文的各项工作,在此,对马老师两年来给我的教诲和指导表示衷心的感谢!其次,非常感谢师兄杨斌、李伟光、姚斌,师弟常志超、申晓康、杨维健给予我的帮助,同时,感谢我的好室友杨阳、刘浪纯、林玉敏,研究生两年中我的室友在生活上和学习上给了我很多帮助,使我感受到了亲人般的温暖,在即将毕业之际,也祝愿他们学习、工作以及生活愉快!最后,我要深深的感谢我的父母和家人,由于他们无私的鼓励与支持,我才能安心学习,顺利的完成学业!55查看更多