- 2022-09-27 发布 |
- 37.5 KB |
- 62页
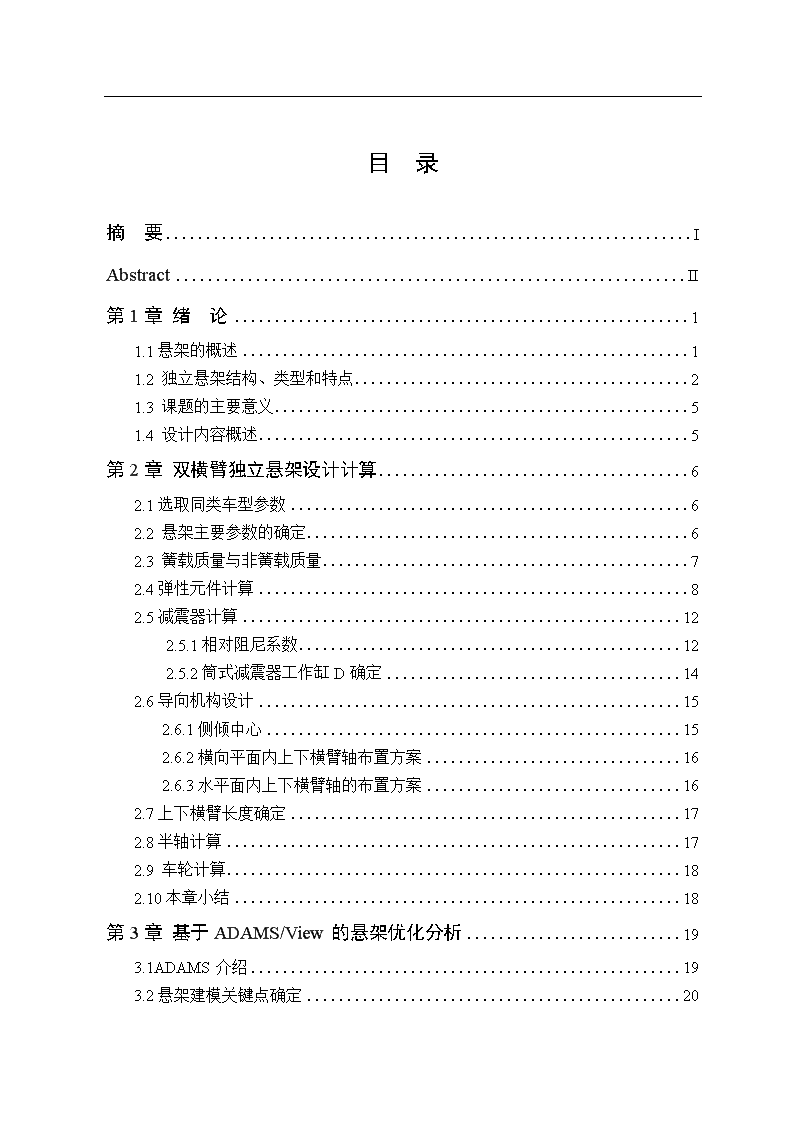
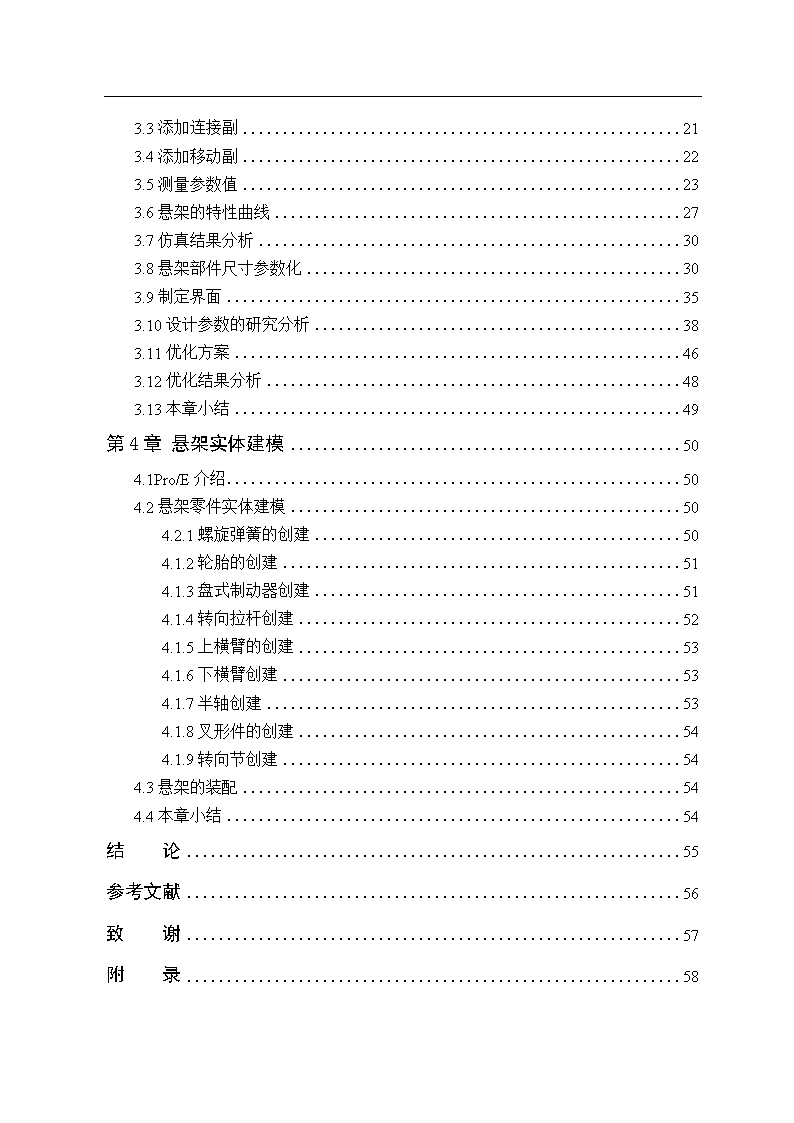
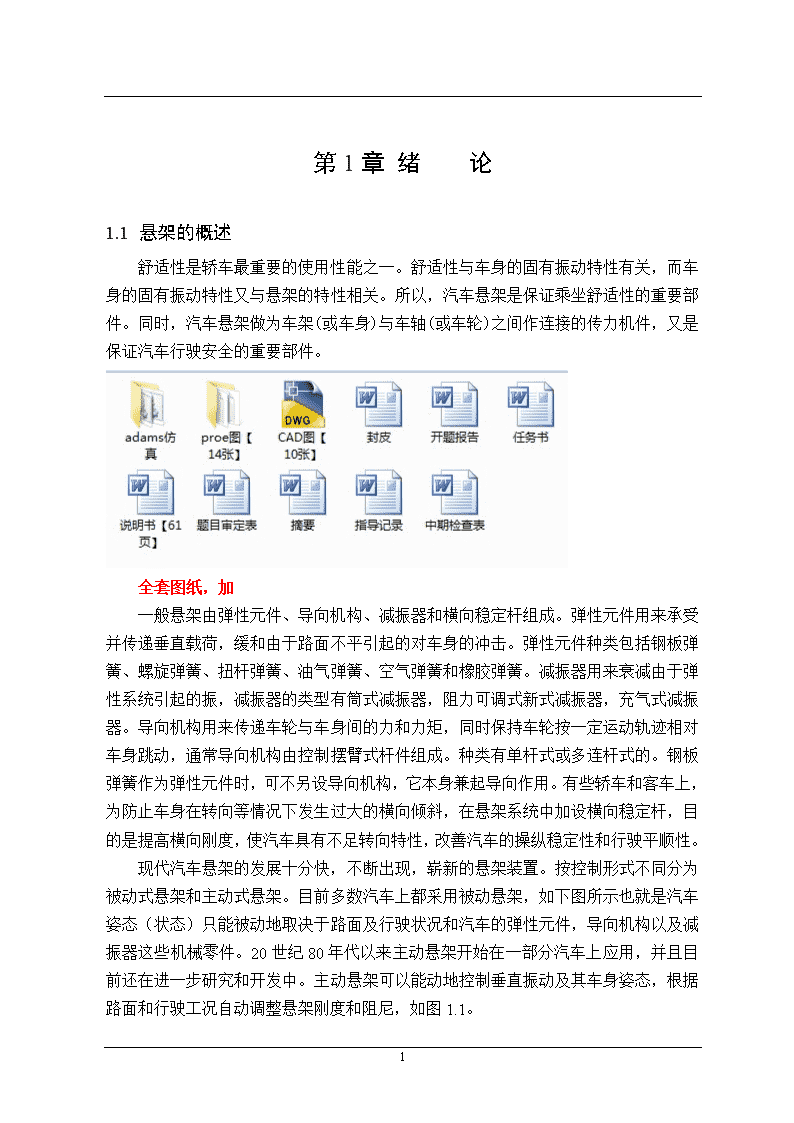
申明敬告: 本站不保证该用户上传的文档完整性,不预览、不比对内容而直接下载产生的反悔问题本站不予受理。
文档介绍
车辆工程毕业设计(论文)-双横臂前悬架参数匹配与运动仿真【全套图纸三维】
目录摘要IAbstractII第1章绪论11.1悬架的概述11.2独立悬架结构、类型和特点21.3课题的主要意义51.4设计内容概述5第2章双横臂独立悬架设计计算62.1选取同类车型参数62.2悬架主要参数的确定62.3簧载质量与非簧载质量72.4弹性元件计算82.5减震器计算122.5.1相对阻尼系数122.5.2筒式减震器工作缸D确定142.6导向机构设计152.6.1侧倾中心152.6.2横向平面内上下横臂轴布置方案162.6.3水平面内上下横臂轴的布置方案162.7上下横臂长度确定172.8半轴计算172.9车轮计算182.10本章小结18第3章基于ADAMS/View的悬架优化分析193.1ADAMS介绍193.2悬架建模关键点确定20\n3.3添加连接副213.4添加移动副223.5测量参数值233.6悬架的特性曲线273.7仿真结果分析303.8悬架部件尺寸参数化303.9制定界面353.10设计参数的研究分析383.11优化方案463.12优化结果分析483.13本章小结49第4章悬架实体建模504.1Pro/E介绍504.2悬架零件实体建模504.2.1螺旋弹簧的创建504.1.2轮胎的创建514.1.3盘式制动器创建514.1.4转向拉杆创建524.1.5上横臂的创建534.1.6下横臂创建534.1.7半轴创建534.1.8叉形件的创建544.1.9转向节创建544.3悬架的装配544.4本章小结54结论55参考文献56致 谢57附录58\n第1章绪论1.1悬架的概述舒适性是轿车最重要的使用性能之一。舒适性与车身的固有振动特性有关,而车身的固有振动特性又与悬架的特性相关。所以,汽车悬架是保证乘坐舒适性的重要部件。同时,汽车悬架做为车架(或车身)与车轴(或车轮)之间作连接的传力机件,又是保证汽车行驶安全的重要部件。全套图纸,加一般悬架由弹性元件、导向机构、减振器和横向稳定杆组成。弹性元件用来承受并传递垂直载荷,缓和由于路面不平引起的对车身的冲击。弹性元件种类包括钢板弹簧、螺旋弹簧、扭杆弹簧、油气弹簧、空气弹簧和橡胶弹簧。减振器用来衰减由于弹性系统引起的振,减振器的类型有筒式减振器,阻力可调式新式减振器,充气式减振器。导向机构用来传递车轮与车身间的力和力矩,同时保持车轮按一定运动轨迹相对车身跳动,通常导向机构由控制摆臂式杆件组成。种类有单杆式或多连杆式的。钢板弹簧作为弹性元件时,可不另设导向机构,它本身兼起导向作用。有些轿车和客车上,为防止车身在转向等情况下发生过大的横向倾斜,在悬架系统中加设横向稳定杆,目的是提高横向刚度,使汽车具有不足转向特性,改善汽车的操纵稳定性和行驶平顺性。现代汽车悬架的发展十分快,不断出现,崭新的悬架装置。按控制形式不同分为被动式悬架和主动式悬架。目前多数汽车上都采用被动悬架,如下图所示也就是汽车姿态(状态)只能被动地取决于路面及行驶状况和汽车的弹性元件,导向机构以及减振器这些机械零件。20世纪80年代以来主动悬架开始在一部分汽车上应用,并且目前还在进一步研究和开发中。主动悬架可以能动地控制垂直振动及其车身姿态,根据路面和行驶工况自动调整悬架刚度和阻尼,如图1.1。60\n1弹性元件2减震器纵向推力杆横向推力杆3横向稳定器图1.1悬架图根据汽车导向机构不同悬架种类又可分为独立悬架,非独立悬架。如下图1.2所示:(a)非独立悬架(b)独立悬架图1.2非独立悬架与独立悬架示意图非独立悬架如上图(a)所示。其特点是两侧车轮安装于一整体式车桥上,当一侧车轮受冲击力时会直接影响到另一侧车轮上,当车轮上下跳动时定位参数变化小。若采用钢板弹簧作弹性元件,它可兼起导向作用,使结构大为简化,降低成本。目前广泛应用于货车和大客车上,有些轿车后悬架也有采用的。非独立悬架由于非簧载质量比较大,高速行驶时悬架受到冲击载荷比较大,平顺性较差。60\n独立悬架是两侧车轮分别独立地与车架(或车身)弹性地连接,当一侧车轮受冲击,其运动不直接影响到另一侧车轮,独立悬架所采用的车桥是断开式的。这样使得发动机可放低安装,有利于降低汽车重心,并使结构紧凑。独立悬架允许前轮有大的跳动空间,有利于转向,便于选择软的弹簧元件使平顺性得到改善。同时独立悬架非簧载质量小,可提高汽车车轮的附着性。如上图(b)所示。1.2独立悬架结构、类型和特点1、单横臂式这种悬架在车轮跳动时.车轮倾角有显著的变化,侧滑量大、轮胎磨损严重,转向轮采用这种悬架对转向操纵有一定影响因此很少用于的前悬架。对后悬架来说.汽车在小向心加速度行驶时车轮外倾角变化将增加汽车不足转向因素.而在大向心加速度时车身产生“举升”现象。单横臂式悬架结构简单、质量小、成本低,在早期轿车后悬架上采用得比较多,目前已很少使用。2、单纵臂式单纵臂式悬架在车轮跳动时,车轮外倾角和前束不变,但后倾角变化较大,因此多用于不转向的后轮。转弯行驶时,由于车轮随车身一起向外倾斜,后悬架采用这种悬架容易出现过多转向趋势。单纵臂式悬架结构简单、质量小,可以得到较大的室内空间,所以在前轮驱动汽车的后悬架上应用的比较多,目前被单斜臀式、麦弗逊式独立悬架所代替。3、单斜臂式介于单横臂式和单纵臂式之间的一种悬架结构。摆臂的转动轴线与汽车纵轴线所成角度在0º-90º之间。单斜臂式悬架自60年代初问世以来,在后轮驱动汽车的后悬架上得到了广泛应用。目前由于对汽车干顺性和操纵稳定性提出了更高要求,有些汽车采用了结构更复杂的双横臂式或多杆式独立悬架。今后伴随着后轮驱动汽的减少,单斜臂式悬架应用会逐渐减少。4、纵臂扭转梁式这种悬架主要优点是,车轮运动特性比较好,左、右车轮在等幅正向或反向跳动时,车轮外倾角、前束及轮距无变化,汽车具有良好的操纵稳定性。但这种悬梁在侧向力作用时。呈过多转向趋势。另外,扭转梁因强度关系,允许承受的载荷受到限制。扭转梁式悬架结构简单、成本低、在一些前置前驱动汽车的后悬架上应用得比较多。5、多杆式多杆式悬架主要优点是,利用多杆控制车轮的空间运动轨迹,以便更好地控制车轮定位参数变化规律,得到更为满意的汽车顺从转向特性,最大限度满足汽车操纵性和平顺性要求。缺点是零件数量多、结构复杂、要求精度高。多杆式悬架是目前最为先进的悬架结构。6、麦弗逊式60\n它可看成是上摆臂等效无限长的双横臂式独立悬架。它的突出优点是简化了结构,减小了质量,节省了空间,有利于前部地板构造和发动机布置。它的缺点是:由于自由度少,悬架运动特性的可设计性不如双横臂悬架;振动通过上支点传递给汽车头部,需采取相应的措施隔离振动、噪声;减震器的活塞杆与导向套之间存在摩擦力,使得悬架的动刚度增加,弹性特性变差,小位移时这一影响更加显著;对轮胎的不平衡性较敏感;减震器紧贴车轮布置,其空间很小,有些情况下不便于采用宽胎或加装防滑链。7、双横臂式双横臂式独立悬架按其上、下横臂的长短又分为等长双横臂式和不等长双横臂式两种。等长双横臂式悬架在其车轮作上、下跳动时,可保持主销倾角不变,但轮距却有较大的变化,会使轮胎磨损严重,故已很少采用,多为不等长双横臂式悬架所取代。后一种形式的悬架在其车轮上、下跳动时,只要适当地选择上、下横臂的长度,并合理布置,即可使轮距及车轮定位参数的变化量限定在允许的范围内。这种不大的轮距改变,不引起车轮沿路面的侧滑,而为轮胎的弹性变形所补偿。因此,不等长双横臂独立悬架能保证汽车有良好的行驶稳定性,已为中高级轿车的前悬架所广泛采用。双横臂悬架的突出优点在于设计的灵活性,可以通过合理的选择空间导向杆系的铰接点的位置及导向臂的长度,使得悬架具有合适的运动特性,并且形成恰当的侧倾中心和纵倾中心。为了隔离振动和噪声并补偿空间导向机构由于上、下横臂摆动轴线相交带来的运动干涉,在个铰接点处一般采用橡胶支承。显然,各点处受力越小,则橡胶支承的变形越小,车轮的导向和定位也就越精确。分析表明,为了减小铰接点处的作用力,应尽量增大上、下横臂间的垂直距离。当然,上下横臂各铰接点位置的确定还要综合考虑布置是否方便以及悬架的运动特性是否合适,如图1.3。1,6-下摆臂及上摆臂;2,5-球头销;3-半轴等速万向节;4-立柱;7,8-缓冲块图1.3无主销前转向驱动桥的双横臂悬架60\n1.3课题的主要意义悬架是车辆重要的组成部分。其主要任务是传递车轮与车架之间的力和力矩,并缓和冲击、衰减振动。对改善车辆的行驶平顺性、减轻车辆自重以及减少对公路的破坏具有重要息义。传统的汽车设计是由最初的设计→试验→设计。在制造出样品产品后,进行测试,测试合格,制造出产品。如果不合格,重新设计,直到合格为止。在从设计到制造要经过多次的重试,需要很长的时间,浪费了大量的人力和物力,并且延长了新产品的上市时间。本课题研究的主要意义就在于运用ADAMS软件对车辆双横臂独立式悬架进行虚拟设计,在试制前的阶段进行设计和试验仿真,并且提出优化设计的意见,获得分析车轮垂直跳动、转动与车轮前束角的变化等关系。获得相关数据,在产品制造出之前,就可以发现并更正设计缺陷,完善设计方案,缩短开发周期,提高设计质量和效率,为生产实际提供理论支持。运用虚拟样机技术,结合虚拟设计和虚拟试验,可以大大简化悬架系统设计开发过程,大量减少产品开发费用和成本,提高产品系统性能,获得最优设计产品。1.4设计内容概述分析双横臂独立式悬架的结构和悬架设计要求,在悬架设计中,根据整车的布置要求以及经验数据,确定悬架的整体空间数据和性能参数,在ADAMS软件平台上建立双横臂独立悬架的简化物理模型,进行动力学仿真分析,通过分析车轮垂直跳动、转动与车轮前束角的变化等关系获得相关数据,优化相关参数建立虚拟双横臂独立选件模型。运用PRO/E建立三维实体模型,如图1.4所示。收集材料,完成开题报告初步计算悬架零部件尺寸校核强度和使用寿命否运用ADAMS创建简化物理模型并运动分析是根据有优化后的尺寸绘制Pro/E实体模型创建Pro/E二维工程图及实体装配图一套修改60\n检查、审核编辑说明书,完成毕业设计是图1.4毕业设计流程图第2章双横臂独立悬架计算2.1选取同类车型参数本次设计选用车型为2011款比亚迪F6舒适型2.0L手动挡,设计前悬架参考的主要参数如下表2.1。表2.1参考车型主要参数车身长/宽/高(mm)4850/1822/1465整车整备质量(kg)1435总质量(kg)1435+570=1785前轮距(mm)1551后轮距(mm)1551前轮胎规格205/65R15前轮辋规格6.5J15最小离地间隙(mm)1502.2悬架主要参数的确定1.悬架静挠度悬架静挠度是指汽车满载静止时悬架上的载荷与此时悬架刚度之比,即(2.1)对于大多数汽车而言,其悬挂质量分配系数60\n,因而可以近似地认为,即前后桥上方车身部分的集中质量的垂向振动是相互独立的。并用偏频表示各自的自由振动频率。一般采用钢制弹簧的轿车,约为(次/min),约为(次/min)非常接近人体步行时的自然频率。为了避免汽车的角振动,一般汽车前后悬架偏频之比约为:。取,因此在允许范围当时,汽车前后桥上方车身部分的垂向振动频率为:(2.2)(2.3)式中——重力加速度,;——前后悬架刚度,;——前后悬架悬挂质量,。由上式得到:(2.4)(2.5)式中的单位。2、悬架的动挠度悬架的动挠度是指从满载静平衡位置开始悬架压缩到结构允许的最大变形(通常指缓冲块压缩到其自由高度的或)时,车轮中心相对车架(或车身)的垂直位移。要求悬架应有足够大的动挠度,以防止在坏路面上行驶时经常碰撞缓冲块。乘用车,取。60\n取对于一般轿车而言,悬架总的工作行程即静挠度与动挠度之和应当不小于。2.3簧载质量与非簧载质量非簧载质量:根据是否由徐昂家弹簧支撑,汽车的总质量可以分为悬挂质量和非悬挂质量两部分,非悬挂质量即为非簧载质量。对于轿车驱动桥:采用独立悬架的非悬挂质量为。表1.2悬挂质量与非悬挂质量悬架类型双横臂,螺旋弹簧,中央制动器13%87%6.714.9%DEDion桥,螺旋弹簧,中央制动器15%85%5.717.6%双横臂,螺旋弹簧18%82%4.622%纵臂,螺旋弹簧18%82%4.622%DEDion桥,螺旋弹簧20%80%4.025%整体刚性桥,导向杆系,螺旋弹簧22%78%3.528.2%整体刚性桥,钢板弹簧26%74%2.835.1%因此簧载质量。现代汽车质量分配系数接近于1。60\n。非簧载质量。单个车轮的非簧载质量为(满足要求)2.4弹性元件计算1、螺旋弹簧的初步选择材料:油淬火回火硅锰弹簧钢丝;牌号:60si2MnA;推荐温度范围:。2、弹簧的设计弹簧刚度3、设计载荷时弹簧受力4、初选弹簧高度初步选择;悬架在压缩行程极限位置时的弹簧高度为180mm5、初步选择弹簧中径初选中径:端部结构形式:两端两端碾细。6、参考相关标准确定台架实验时伸张及压缩极限位置相对于设计载荷位置的弹簧变形量7、确定弹簧寿命圆柱螺旋弹簧按所受载荷情况可分为三类:60\n第一类————受循环载荷作用次数在1次以上的弹簧;第二类————受循环载荷作用次数在1~1次范围内及受冲击载荷的弹簧;第三类————受静载荷及受循环载荷次数1以下的弹簧。汽车圆柱弹簧应选取第二类。8、初选钢丝直径d=14mm根据直径材料选取许用拉应力[]=1569Mpa。9、求解弹簧工作圈数i弹簧刚度;轴向载荷P作用下变形;式中Dm——弹簧中径,d——弹簧钢丝直径,i——弹簧工作圈数;G——弹簧材料剪切弹性模量取。圈(2.6)压缩弹簧i取值为9圈弹簧完全并紧时的高度,总全数。两端碾细总圈数:圈(2.7)完全并紧时的高度:(2.8)式中1.01——螺旋角的补偿系数;t——端部碾细时的端末厚度t=d/3。10、弹簧完全并紧时的高度60\n11、由、、及求出弹簧在完全压紧时载荷,台架试验伸张、压缩极限位置对应载荷、以及工作压缩极限位置的载荷分别为:(2.9)=2261.4(2.10)(2.11)(2.12)弹簧指数旋绕比C范围(满足要求)。曲率系数是考虑簧圈曲率对强度影响的系数:12、剪切应力计算、、、60\n(2.13);;;13、校核台架试验条件下弹簧寿命给定试验条件下循环次数可估算:(2.14)式中;因此:(满足要求)。14、确定弹簧自由高度(2.15)取。15、最小工作高度60\n(2.16)式中——与弹簧指数有关的系数有关的系数:(2.17)14、稳定性校核又细又高的弹簧在大载荷作用下会失稳,失稳的临界载荷不仅与高度和直径之比:(两端固定)。取C0=1(不同支撑方式下C0取值见刘维信汽车设计图13-66)(2.18)=1.2748由于H0已经设计出得H0=320mmf为螺旋弹簧在其轴向载荷P作用下变形(2.19)(2.20)因此:(弹簧稳定)。2.5减震器计算60\n悬架用得最多的减震器是内部充有液体的液力式减震器。汽车车身和车轮振动时,减震器的液体在流经阻尼孔时的摩擦和液体的粘性摩擦形成了振动阻力,将振动能量转变为热能,并散发到周围的空气中去,达到迅速衰减振动的目的。如果能量的耗散仅仅是在压缩行程或者是在伸张行程进行,这把这种减震器称为单向作用式减震器;反之称为双向作用式减震器。本设计选用双向作用式减震器。根据结构形式不同,减震器分为摇臂式和筒式两种筒式减震器又分为单筒式、双筒式和充气筒式三种。由于双筒充气液力减振器具有工作稳定、干摩擦阻力小、噪声低、总长度短等优点,因此在乘用车上得到了越来越多的应用。所以选择的减振器形式为双筒充气式液力减振器。2.5.1相对阻尼系数用相对阻尼系数的大小来评定振动衰减的快慢程度。值大,振动能迅速衰减,同时又能将较大的路面冲击力传到车身;值小则反之。式中——阻力,——减振器阻尼系数。式中c——悬架刚度,——簧载质量。减振器的阻尼力作用在不同刚度c和簧载质量式会产生不同的阻尼效果,值大,振动能衰减的快,同时也会将较大的路面冲击传到车身。值小则相反,振动衰减的比较慢,但是传到车身的冲击也较小。因此通常取减振器的压缩行程的值取小些,伸张行程时的取的大些。并保持=(0.25~0.50)的关系,设计时取与的平均值,的范围时~0.35。初取=0.30。1、减振器阻尼系数的确定60\n减震器阻尼系数。因悬架系统固有振动频率,所以理论上。实际上,应根据减震器的布置特点确定减震器的阻尼系数,如图2.1。图2.1减振器安装位置(2.21)式中:n——双横臂悬架的下臂长;a——减震器在下横臂上的连接点到下横臂在车身上铰链点之间距离;——减震器轴线与铅垂线之间的夹角,取,。2、最大卸荷力的确定为减小传到车身上的冲击力,当减振器活塞振动速度达到一定值时,减振器打开卸荷阀,此时活塞的速度为卸荷速度。为求出减震器的最大卸荷力,先求出当减震器打开卸荷阀时活塞的速度即卸荷速度。(2.22)式中:一般都在;A车身振幅,取40mm;因此可求得在伸张时的最大卸荷力:(2.23)60\n2.5.2筒式减震器工作缸D的确定根据伸张行程的最大卸荷力F0计算工作缸直径D为(2.24)式中[P]为工作缸最大允许压力,;取λ为连杆直径与缸筒直径之比,双筒式减震器取,取0.45=32.43减震器的工作缸直径D有20mm、30mm、40mm、(45mm)、50mm、65mm等几种。选取时按标准选用,相见QC/T491——1999《汽车筒式减震器尺寸系列及技术条件》。取D值40mm。贮油筒直径Dc=(1.30-1.50)D,壁厚取为2mm,材料为可选20钢。Dc取值50mm。2.6.导向机构设计2.6.1侧倾中心双横臂独立悬架的侧倾中心由下图所示得出。将上下横臂内外转动点的连线延长,一边得到极点P同时活的P点的高度。将P点与车轮接地点N连接,即可在汽车轴线上或的侧倾中心W。60\n图2.2双横臂独立悬架侧倾中心W的确定双横臂独立悬架的侧倾中心高度为:(2.25)式中:(2.26)=2371.15(2.27)=200mm因此=63.07mm前悬架侧倾中心高度在范围内,所以满足要求。2.6.2横向平面内上、下横臂轴布置方案60\n将上、下横臂内外转动点的连线延长,以便得到极点P,并同时获得P点的高度。将P点与车轮接地点P连接,即可在汽车轴线上获得侧倾中心。图2.3上下横臂在横向平面内的布置方案2.6.3水平面内上下横臂轴的布置方案上下横臂轴线在水平面内的布置方案为三种a)和皆为正b)为正值,为零c)为正值,为负值图2.4上下横臂水平面布置方案图大多数前置发动机汽车悬架下横臂轴的斜置角为正值,而上横臂轴的斜置角有正值、零值和负值三种布置方案。上、下横臂轴斜置角不同的组合方案,对车轮跳动时前轮定位参数的变化规律有很大的影响。如车轮上跳,下横臂轴斜置角为正,上横臂轴斜置角为负值或零值时,主销后倾角随车轮的上跳而增大。如组合方案为上、下横臂都为正值时,则主销后倾角随车轮的上跳有较小增加甚至减小。本设计选择方案(b),选择下横臂轴的斜置角为正值,上横臂轴的斜置角为零值。取值:,。2.7上下横臂长度确定双横臂式悬架上、下横臂的长度对车轮上、下跳动时的定位参数影响很大。现代乘用车所用的双横臂式前悬架,一般设计成上横臂短,下横臂长。下图为60\n下横臂长度保持不变,改变上横臂长度,使分别为0.4,0.6,0.8,1.0,1.2时计算得到悬架运动特性曲线。图2.5上、下横臂长度之比改变时悬架运动特性图美国克莱斯勒和通用公司分别认为,上、下横臂长度之比取和为最佳,根据我国乘用车设计的经验,在初选尺寸时取上、下横臂长度之比为0.65为宜。本设计初选尺寸下摆臂长度=400mm,因,上摆臂长度。2.8半轴计算半轴根据其车轮端的支撑方式不同,可分为半浮式,3/4浮式和全浮式三种形式。此次设计为全浮式半轴。全浮式半轴的计算载荷可按车轮附着力矩计算,即:(2.28)其中——负荷转移系数,取值1.2;——驱动桥的最大静载荷;——滚动半径,可近似为车轮半径;——附着系数,取值0.8;全浮式半轴轴杆部直径可按下面公式选择60\n(2.29)=21.80mmk为直径系数,取,取0.21,d取22mm。2.9车轮的计算轮胎规格205/65R15;轮胎宽度;扁平率0.65;轮胎高度205;轮辋直径15英寸;因此车轮直径D为。2.10本章小结本章计算了悬架弹性元件、减震器、侧倾中心、上下横臂、半轴、轮胎等基本尺寸及校核,这些是悬架设计必不可少的尺寸要求,对本次设计后期的仿真分析奠定了基础。其中悬架上下横臂斜置角、长度等的初选是根据试验曲线选出,是经验数值。为初选值提供理论支持。60\n第3章基于ADAMS/View的悬架优化分析3.1ADAMS介绍ADAMS(AutomaticDynamicAnalysisofMechanicalSystems),原由美国MDI公司(MechanicalDynamicsInc.)开发,目前已被美国MSC公司收购成为MSC/ADAMS,是最著名的虚拟样机分析软件。它使用交互式图形环境和零件库、约束库、力库,创建完全参数化的机械系统动力学模型,利用拉格朗日第一类方程建立系统最大量坐标动力学微分-代数方程,求解器算法稳定,对刚性问题十分有效,可以对虚拟机械系统进行静力学、运动学和动力学分析,后处理程序可输出位移、速度、加速度和反作用力曲线以及动画仿真。ADAMS软件由核心模块、功能扩展模块、专业模块、工具箱和接口模块5类模块组成。ADAMS一方面是虚拟样机分析的应用软件,用户可以运用该软件非常方便地对虚拟机械系统进行静力学、运动学和动力学分析。另一方面,又是虚拟样机分析开发工具,其开放性的程序结构和多种接口,可以成为特殊行业用户进行特殊类型虚拟样机分析的二次开发工具平台。60\nADAMS软件一方面是机械系统动态仿真软件的应用软件,用户可以运用该软件非常方便地对虚拟样机进行静力学、运动学和动力学进行分析。另一方面,又是机械系统动态仿真分析开发工具,其开放性的程序结构和多种接口,可以成为特殊行业用户进行特殊类型机械系统动态仿真分析的二次开发工具平台。在产品的开发过程中,工程师通过应用ADAMS软件会收到明显效果传统悬架系统设计、试验、试制过程中必须边试验边改进,从设计到试制、试验、定型,产品开发成本较高周期长。运用机械系统动力学分析软件ADAMS进行仿真分析以及优化设计,可以大大简化悬架系统设计开发过程。大幅度缩短产品开发周期,大量减少产品开发费用和成本,明显提高产品质量,提高产品的系统及性能获得最优化和创新的设计产品。本文应用多体动力学软件ADAMS/View建立了某轻型汽车的前双横臂式独立悬架模型,进而进行运动学分析,得到了上横臂长度主销长度、上横臂在汽车横向平面的倾角、下横臂长度和下横臂在汽车横向平面的倾角的值最终优值,从而为设计和改进提供快速、可靠的技术依据,达到大幅度降低设备研制成本,大大降低了轮胎的磨损情况的目的。3.2悬架建模关键点的确定根据横臂横向、纵向水平的布置方案及坐标系位置可大致确定各部件空间硬点位置,各硬点位置如下:表3.1创建硬点坐标值LOC_XLOC_YLOC_ZLCA_outer000LCA_inner393.92069.46UCA_outer45.90326.59-11.40UCA_inner303.37290.41-11.40Knuckle_outer-140.53138.55-4.84Knuckle_inner19.47138.55-4.84Tie_rod_outer19.47138.55-144.84Tie_rod_inner319.47138.55-144.8460\n1、创建主销点击ADAMS/View零件库中的圆柱体(Cylinder),选择Newpart定义圆柱体的半径为20mm。选择硬点LCA_outer和UCA_outer创建主销。2、创建上横臂点击ADAMS/View零件库中的圆柱体(Cylinder),选择Newpart定义圆柱体的半径为20mm。选择硬点UCA_outer和UCA_inner创建上横臂。用同样方式可创建下横臂、转向拉杆和转向节。3、创建车轮点击ADAMS/View零件库中的圆柱体(Cylinder),选择Newpart定义圆柱体的半径为323.75mm长度为205mm。分别将创建体重命名为:上横臂(UCA)下横臂(LCA)主销(kingpin)拉臂(pull_arm)拉杆(tie_rod)车轮(wheel)。4、创建试验台点击ADAMS/View中零件库的点(Point),选择“AddtoGround”和“Don’tAttach”,在(-340.53,-225.2,-204.84)处建一个点,并以该点为对角点建立一个长400mm宽400mm高40mm的长方体,并以长方体的质心为中心创建一个直径为30mm高300mm的圆柱体,它与长方体组成测试平台。将圆柱体和长方体合为一体。3.3添加连接副根据各部件间连接关系创建连接副,各部件连接方式如下:1、创建球副上横臂与主销之间添加球接触选择2-Bod-1loc和NormalToGrid选择上横臂(UCA)和主销(Kingpin)为参考物体,选择设计点“UCA_outer”为球副的位置点,创建上横臂和主销之间的连接副。60\n下横臂与主销之间添加球接触选择2-Bod-1loc和NormalToGrid选择下横臂(UCA)和主销(Kingpin)为参考物体,选择设计点“UCA_outer”为球副的位置点,创建下横臂和主销之间的连接副。转向拉杆(tie-rod)与拉杆(pull_arm)添加球接触,选择2-Bod-1loc和NormalToGrid选择转向拉杆和拉臂为参考物体,选择设计点“tie-rod”为球副的位置点,创建转向拉杆和拉臂之间的连接副。设置球副的选项为“1Location”和“NormalToGrid”选择设计点“Tie_rod_inner”,创建拉杆和大地之间的球副。2、创建旋转副点击ADAMS/View中约束库的设置旋转副的选项为1-loction和NormalToGrid,选择上横臂点(UCA_inner)为位置点。添加旋转副,同理,创建下横臂旋转副。3、创建固定副点击ADAMS/View中约束库的,设置固定副的选项为2-Bod-1loc和NormalToGrid,选择车轮(wheel)和转向节(knuckle)为参考物体,添加固定副,同理,创建主销和转向节、转向节和拉臂固定副。4、创建点、面约束在试验台和车轮间要创建点面约束,右键点击ADAMS/View中约束库弹出对话框(a)点击,将弹出对话框(b)选择点、面约束,选择约束参考物车轮(wheel)和试验台(顺序不可颠倒)选择按钮,将约束旋转90。60\n(a)约束库图(b)点面约束图图3.1操作截图3.4添加移动副点击ADAMS/View中约束库的在测试平台和大地之间创建一个移动副,移动副位置为测试平台的中心位置,设置移动副的选项为1-loctionPickFeature,方向垂直向上(向下)Adams创建物理模型如下图:图3.2简化模型点击ADAMS/View中驱动库中的直线驱动,选择测试试验台和大地移动副,创建直线驱动后,直接在Edit和Modify,修改直线驱动,在添加驱动对话框”F(time)=()”中输入驱动函数表达式“100*sin(360d*time)”如下图所示:60\n图3.3操作截图点击ADAMS/View中,设置终止时间为1,工步为200,点击仿真按钮,进行仿真。在ADAMS/View中点击File菜单中选择SaveDatebaseAs命令将前悬架模型保存在工作目录下。3.5测量参数值对主销,车轮、等参数值进行测量。1、测量主销内倾角在ADAMS/View菜单栏中,选择Build>Measure>Function>New,创建新的测量函数。在函数编辑器对话窗中的测量名称(MeasureName)栏输入:Kingpin_Inclination,一般属性(GeneralAttributes)的单位(Units)栏中选择“angle”。输入反正切函数“ATAN()选择“Displacement”中的“DisplacementalongX”,测量两点在X轴方向的距离,点击件,弹出对话框,在“ToMarker”栏中输入主销上标志点marker_29,在“FromMarker”栏中输入主销下标记点marker_6,点击ok,系统自动生成测量两点在X轴方向距离的表达式。60\n图3.4操作截图同理测量两点在Y轴方向的距离。点击“OK”键。完成测量主销内倾角的表达式输入。图3.5操作截图图3.6操作截图同时,点击仿真键,系统生成主销内倾角变化的测量曲线,曲线如下:60\n图3.7主销内倾角变化曲线图由图可以看看出主销内倾角并不是在固定不变,而是在范围内变化。2、测量主销后倾角在ADAMS/View菜单栏中,选择Build>Measure>Function>New,创建新的测量函数。在函数编辑器对话窗中的测量名称(MeasureName)栏输入:Caster_Anger,一般属性(GeneralAttributes)的单位(Units)栏中选择“angle”,输入反正切函数“ATAN()选择“Displacement”中的“DisplacementalongZ”,测量两点在Z轴方向的距离,点击件,弹出对话框,在“ToMarker”栏中输入主销上标志点marker_29,在“FromMarker”栏中输入主销下标记点marker_6,点击ok,系统自动生成测量两点在Z轴方向距离的表达式。同理同理测量两点在Y轴方向的距离。点击“OK”键。完成测量主销后倾角的表达式输入。函数表达式为:ATAN(DZ(MARKER_29,MARKER_6)/DY(MARKER_29,MARKER_6))点击仿真键,系统生成主销后倾角变化的测量曲线,曲线图为:图3.8主销后倾角变化曲线图由图可以看出主销后倾角在之间变化。60\n3、测量车轮外倾角函数表达式为:ATAN(DY(MARKER_12,MARKER_23)/DX(MARKER_12,MARKER_23))点击仿真键,系统生成主销后倾角变化的测量曲线,曲线图为:图3.9车轮外倾角变化曲线从图中可以看出外倾角在范围内变化。4、测量前轮前束角函数表达式为:ATAN(DZ(MARKER_12,MARKER_23)/DX(MARKER_12,MARKER_23))点击仿真键,系统生成主销后倾角变化的测量曲线,曲线图为:图3.10前轮前束角变化曲线从图中可以看出外倾角在范围内变化。5、测量车轮接地点侧向滑移量创建标记点MARKER_42在车轮上,坐标值为(-140.53,-185.2,-4.84)创建标记点MARKER_43与大地连接,坐标值与MARKER_42相同在函数编辑器对话窗中的测量名称(MeasureName)栏输入:60\nSideways_Displacement;单位(Units)栏中选择“length”运用函数编辑器提供的基本函数,编辑函数表达式:DX(MARKER_42,MARKER_43)点击仿真键,系统生成主销后倾角变化的测量曲线,曲线图为:图3.11车轮接地点侧向滑移量变化曲线6、测量车轮跳动量运用函数编辑器提供的基本函数,编辑函数表达式:DY(MARKER_42,MARKER_43)点击仿真键,系统生成主销后倾角变化的测量曲线,曲线图为:图3.12车轮跳动量变化曲线3.6悬架的特性曲线选择,进入定制曲线界面,选择data,弹出对话框选择Kingpin_Inclination,点击ok键。在选择Wheel_Travel,点击AddCurves键,即可生成以主销内倾角为X轴,车轮跳动量为Y轴的特性曲线。60\n图3.13创建函数曲线操作截图图3.14操作截图生成特性曲线如下图:图3.15主销内倾角随车轮跳动的变化曲线根据以上方法生成其他特性曲线:60\n图3.16主销后倾角随车轮跳动的变化曲线图3.17车轮外倾角随车轮跳动变化曲线图3.18车轮侧向滑移量随车轮跳动变化曲线60\n图3.19前轮前束角随车轮跳动量变化曲线3.7仿真结果分析主销内倾角变化曲线,主销内倾角随车轮跳动曲线可以看出,车轮从最低点到最高点过程中主销内倾在范围内变化,在允许范围内。主销后倾角曲线分析,主销后倾角随车轮跳动曲线可以看出,车轮从最低点跳到最高点过程中主销后倾角在范围内变化,基本符合要求不大于。车轮外倾角变化曲线分析,其随车轮跳动曲线可以看出,范围内变化,数值范围稍大,需要优化。车轮侧向滑移量变化曲线分析,其随车轮跳动曲线可以看出,车轮从最低点到最高点运动过程中,车轮侧向滑移变化范围-2.3mm~16mm。前轮前束角变化曲线分析,前轮前束角随车轮跳动曲线可以看出,车轮从最低点到最高点运动过程中,前轮前束角变化范围。3.8悬架部件尺寸参数化1、创建设计变量在ADAMS/View菜单栏中,选择Build~DesignVariable~New,设置变量名,及其变化范围值。操作如下图:60\n图3.20操作截图起初系统弹出对话框,取其最初默认变量名DV_1,此变量名记作主销长度,变量类型选择“Real”,变量单位选择“length”,变量的标准值取330,在“ValueRangeby”栏中选择“AbsoluteMinandMaxValues”,输入变量的最小值为280,输入变量的最大值为380,点击apply,完成了主销长度参数化。取其默认变量名DV_2,此变量名记作上横臂长度,变量类型选择“Real”,变量单位选择“length”,变量的标准值取260,在“ValueRangeby”栏中选择“AbsoluteMinandMaxValues”,输入变量的最小值为210,输入变量的最大值为310,点击apply。取其默认变量名DV_3,此变量名记作下横臂长度,变量类型选择“Real”,变量单位选择“length”,变量的标准值取400,在“ValueRangeby”栏中选择“AbsoluteMinandMaxValues”,输入变量的最小值为350,输入变量的最大值为450,点击apply。取其默认变量名DV_4,此变量名记作主销内倾角,变量类型选择“Real”,变量单位选择“angle”,变量的标准值取,在“ValueRangeby”栏中选择“AbsoluteMinandMaxValues”,输入变量的最小值为,输入变量的最大值为,点击apply。取其默认变量名DV_5,此变量名记作主销后倾角,变量类型选择“Real”,变量单位选择“angle”,变量的标准值取,在“ValueRangeby”栏中选择“AbsoluteMinandMaxValues”,输入变量的最小值为,输入变量的最大值为,点击apply。取其默认变量名DV_6,此变量名记作上横臂横向平面倾斜角,变量类型选择“Real”,变量单位选择“angle”,变量的标准值取,在“ValueRangeby”栏中选择“AbsoluteMinandMaxValues”,输入变量的最小值为,输入变量的最大值为,点击apply。取其默认变量名DV_7,此变量名记作上横臂斜置角,变量类型选择“Real”,变量单位选择“angle”,变量的标准值取,在“ValueRangeby”栏中选择“AbsoluteMinandMaxValues”,输入变量的最小值为,输入变量的最大值为,点击apply。60\n取其默认变量名DV_8,此变量名记作下横臂横向平面倾斜角,变量类型选择“Real”,变量单位选择“angle”,变量的标准值取,在“ValueRangeby”栏中选择“AbsoluteMinandMaxValues”,输入变量的最小值为,输入变量的最大值为,点击apply。取其默认变量名DV_9,此变量名记作下横臂斜置角,变量类型选择“Real”,变量单位选择“angle”,变量的标准值取,在“ValueRangeby”栏中选择“AbsoluteMinandMaxValues”,输入变量的最小值为,输入变量的最大值为,点击apply。2、硬点参数化取硬点UCA_outer,右键,选择Modify,将弹出修改对话框,选择设计点“UCA_outer”的X坐标,右键,选择Parameterize~Expression~Builder,使用函数编辑器输入硬点坐标的函数表达式。在函数编辑器下部的“GettingObjectDate”栏中选择“DesignPoint”,输入硬点“LCA_OUTER”的名称(可以通过鼠标右键拾取),点击GetDateOwnedByObject可以获得硬点的相关数据。弹出选择数据对话框,选择“Loc_X”,按 “OK”,系统选硬点LCA_OUTER的坐标值:“LCA_OUTER.loc_x”。在“GettingObjectDate”栏中选择“DesignVariable”,输入设计变量“DV_1”的名称,按“InsertObjectDate”按钮,系统选取设计变量DV_1的值。同样可以获取“DV_4”和“DV_5”的值。(LCA_OUTER.loc_x+DV_1*COS(DV_5)*SIN(DV_4))表达式编辑完成后,按“Evaluate”按钮,函数编辑器计算表达式的值,并在“FuctionValue”中显示。按函数编辑器的“OK”键,将函数表达式输入到设计点“UCA_outer”的X坐标栏中。具体操作如下图:60\n图3.21硬点函数话操作截图图3.22函数编辑截图图3.23变量定义截图图3.24函数坐标输入操作截图同理,在硬点“UCA_outer”的Y坐标栏中输入表达式:(LCA_OUTER.loc_y+DV_1*COS(DV_4)*COS(DV_5));在硬点“UCA_outer”Z坐标栏中输入表达式:(LCA_outer.loc_z+DV_1*COS(DV_4)*SIN(DV_5));在硬点“UCA_inner”的X坐标表达式:(UCA_outer.loc_x+DV_2*COS(DV_6)*COS(DV_7));在硬点“UCA_inner”的Y坐标表达式:(UCA_outer.loc_y-DV_2*COS(DV_7)*60\nSIN(DV_6));在硬点“UCA_inner”的Z坐标表达式:(UCA_outer.loc_z+DV_2*COS(DV_6)*SIN(DV_7));在硬点“LCA_inner”的X坐标表达式:(LCA_outer.loc_x+DV_3*COS(DV_8)*COS(DV_9));在硬点“LCA_inner”的Y坐标表达式:(LCA_outer.loc_y+DV_3*COS(DV_9)*SIN(DV_8));在硬点“LCA_inner”的Z坐标表达式:(LCA_outer.loc_z-DV_3*COS(DV_8)*SIN(DV_9));完成以上函数表达式输入后,按列表编辑器的“OK”,将设计点进行了参数化。3、零部件参数化在ADAMS/View工作窗口下,选取主销kingpin,右键选取modify,修改圆柱体,使其尺寸参数化。在修改对话框中将主销长度lengh改为DV_1,单击确定,完成主销实体参数化,操作如图:图3.25下拉式菜单图3.26修改圆柱体对话框重复操作将上横臂长度实体参数化修改为变量DV_2,将下横臂长度修改为DV_3,将拉臂(pull_arm)长度参数化,输入以下函数公式:(SQRT((knuckle_inner.loc_x-Tie_rod_outer.loc_x)**2+(knuckle_inner.loc_y-Tie_rod_outer.loc_y)**2+(knuckle_inner.loc_z-Tie_rod_outer.loc_z)**2))。右键拉臂、修改、在lengh栏右键Parameterize~Expression~Builder,利用函数编辑器,编入函数:60\n图3.27下拉菜单图图3.28函数编辑器3.9定制界面1、创建修改主销参数对话框在ADAMS/view菜单栏中,选择Tools~DialogBox~Create,在系统弹出对话框中,选择DialogBox~New,弹出对话框如下图:图3.26变量修改图窗定义操作60\n修改其Name为Modify_kingpin_parameter,选择ok,apply,cancle。点击OK,弹出对话框图3.27操作截图图3.28定义边界选择对话框中create菜单中slider命令,在修改主销参数对话框创建活动条slider_1,双击活动条,弹出界面修改对话框,Attributes中选择Layout,输入slider_1在界面中的位置和尺寸,定义尺寸left(160)top(25)width(200)height(30),点击apply,选择Attributes中选择value,输入主销标准值330,最小值280,最大值380,apply,在Attributes中选择Commands,输入该变量kingpinlength的表达式:variablesetvariable=DV_1real=$slider_1将对话框Eecutecommandswhilesliding栏打勾,apply。60\n选择create中的lable,点击参数化面板,将lable重命名为kingpinlength,点击apply。选择Attributes中选择value,定义其尺寸left(20)width(120)top(25)height(30)点击apply。同理创建slider_2,尺寸为left(160)width(200)top(70)height(30)点击apply。选择Attributes中选择value,输入主销内倾角标准值8,最小值6,最大值12,apply在Attributes中选择Commands,输入该变量kingpinlength的表达式:variablesetvariable=DV_4real=$slider_2选择create中的lable,点击参数化面板,将lable重命名为kingpin_inclination,点击apply。选择Attributes中选择value,定义其尺寸left(20)width(120)top(70)height(30)点击apply。创建slider_2,尺寸为left(160)width(200)top(115)height(30)点击apply。选择Attributes中选择value,输入主销内倾角标准值-2,最小值-3,最大值0,apply。在Attributes中选择Commands,输入该变量kingpinlength的表达式:variablesetvariable=DV_5real=$slider_3选择create中的lable,点击参数化面板,将lable重命名为caster_Angle,点击apply。选择Attributes中选择value,定义其尺寸left(20)width(120)top(115)height(30)点击apply。2、修改主销参数对话框60\n图3.29定义主销修改对话框3、同理创建上横臂修改参数对话框如下图:图3.30上横臂参数修改对话框4、创建下横臂修改参数对话框图3.31下横臂修改对话框3.10设计参数的研究分析1、参数化分析方法为了减少轮胎的磨损,选择车轮的侧向滑移量的绝对值作为目标函数,通过上横臂长度,下横臂长度,上下横臂在汽车横向平面内倾角的优化分析,使车轮侧向滑移量绝对值最小。2、参数变量对车轮外倾角优化曲线以上横臂为研究对象,让此变量从最小到最大分8阶段变化,得到车轮外倾角随DV_2,变化图,以横坐标为时间。60\n图3.32上横臂长度变化对车轮外倾角影响分析:通过8条曲线分析得到8组数值,分别表示上横臂在不同长度值时的车轮外倾角从中选择值224.29mm,此时车轮外倾角为0.98361。以下横臂长度为研究对象,让此变量从最小到最大分8阶段变化,得到车轮外倾角随DV_3,变化图,以横坐标为时间。图3.33下横臂长度变化对车轮外倾角影响分析:下横臂长度对车轮外倾角影响曲线,从中可以看出下横臂长度对车轮外倾角影响不大,选择下横臂长度421.49,此时车轮外倾角为1.3543.以上横臂横向平面倾角为研究对象,让此变量从最小到最大分8阶段变化,得到车轮外倾角随DV_6,变化图,以横坐标为时间60\n图3.34上横臂横向平面倾角变化对车轮外倾角影响分析:根据曲线分析结果可以看出,上横臂横向倾斜角对前轮外倾角影响相对较大,上横臂横向倾斜角取值5.7143,车轮外倾角0.75462。以下横臂横向平面倾角为研究对象,让此变量从最小到最大分8阶段变化,得到车轮外倾角随DV_8,变化图,以横坐标为时间。图3.35下横臂横向平面变化对车轮外倾角影响3、参数变量对前轮前束角优化曲线以上横臂为研究对象,让此变量从最小到最大分8阶段变化,得到前轮前束角随DV_2,变化图,以横坐标为时间。60\n图3.36上横臂长度变化对前轮前束角影响分析;从以上数据可以看出上横臂长度对车轮前束角的影响不是很大,从中我选择上横臂长度224.29mm,前束角为2.5258。以下横臂为研究对象,让此变量从最小到最大分8阶段变化,得到前轮前束角随DV_3,变化图,以横坐标为时间。图3.37下横臂长度变化对前轮前束角影响分析:从分析数值或曲线的变化可以看出,下横臂对车轮前束角影响不大,选取数值为421.43,前束角为3.1655。60\n以上横臂横向平面倾角为研究对象,让此变量从最小到最大分8阶段变化,得到前轮前束角随DV_6,变化图,以横坐标为时间。图3.38上横臂横向平面倾角变化对前轮前束角影响分析:上横臂横向倾角变化曲线可以看看出,上横臂横向倾角对前轮前束角影响相对较大,选择数值为3.8571,相对前束角为1.8350。以下横臂横向平面倾角为研究对象,让此变量从最小到最大分8阶段变化,得到前轮前束角随DV_8,变化图,以横坐标为时间。图3.39下横臂横向平面倾角变化对前轮前束角影响分析:下横臂横向倾角变化对前束角影响较大,从中选择倾斜角为3.5714,相对前束角为1.3806。60\n以上横臂为研究对象,让此变量从最小到最大分8阶段变化,得到车轮接地点侧向滑移量随DV_2,变化图,以横坐标为时间。图3.40上横臂长度变化对车轮接地点侧向滑移量影响分析:上横臂长度对车轮侧滑量影响曲线看出,其数值变化范围不大,从中选择值224.29,相对侧滑量为15.56。以下横臂为研究对象,让此变量从最小到最大分8阶段变化,得到前轮前束角随DV_3,变化图,以横坐标为时间。图3.41下横臂长度变化对车轮接地点侧向滑移量影响分析:下横臂长度对车轮接地点侧滑量影响曲线看出,其数值变化不大,选择数值421.43,相对侧滑量为16.244。60\n以上横臂横向平面倾角为研究对象,让此变量从最小到最大分8阶段变化,得到前轮前束角随DV_6,变化图,以横坐标为时间。图3.42上横臂横向平面倾角变化对车轮接地点侧向滑移量影响分析:上横臂横向平面倾角8组值对其接地点侧向滑移量影响相对很大,从中可选择数值3.8571相对应滑移量13.307。以下横臂横向水平面倾角为研究对象,让此变量从最小到最大分8阶段变化,得到前轮前束角随DV_8,变化图,以横坐标为时间。图3.43下横臂横向平面倾角变化对车轮接地点侧向滑移量影响分析:下横臂横向倾角和车轮接地点侧滑量曲线图中,不难看出其变化范围较大,从中选择横向倾角为-0.71429,其滑移量为15.382。60\n总体分析:从以上对车轮的前束、车轮外倾角和车轮侧向滑移量曲线分析中,选取了相应的合理数值,其中为求实际绘图和生产方便,取其整数值,取其上横臂长度220mm,下横臂长度420mm,上横臂横向倾斜角取,下横臂横向倾角取。3.11优化方案1优化前参数值表3.2优化前参数值名称变量名初始值上横臂长度DV_2260mm下横臂长度DV_3400mm上横臂横向平面倾角DV_6下横臂横向平面倾角DV_82优化后参数值表3.3优化后参数值名称变量名初始值上横臂长度DV_2220mm下横臂长度DV_3420mm上横臂横向平面倾角DV_6下横臂横向平面倾角DV_83.12优化结果分析参数修改界面,修改所有设计变量的初始值以后,模型自动更新,再次进行运动学仿真,得到各目标参数的变化曲线。优化后主销内倾角在车轮跳动过程中从优化前的变为,主销内倾角的变化范围减小,所以更加符合要求。60\n图3.44主销内倾角随车轮跳动变化曲线图3.45主销后倾角随车轮跳动曲线变化图3.46优化后车轮外倾角随车轮跳动变化曲线优化后前轮外倾角由优化前的优化为取得了优化的目的。60\n图3.47前轮前束随车轮跳动变化曲线优化后前轮前束角由优化前的优化为取得了明显优化效果,使前束角在合理范围内。图3.48车轮接地点横向侧滑量随车轮跳动的变化曲线优化后前轮接地点横向侧滑量由优化前的优-2.3mm~16mm化为-0.3mm~9.2mm取得了明显优化效果,车轮接地点横向侧滑量在合理范围内。虽然有一定的负值,但数值比优化前明显改善,对轮胎磨损影响明显降低。3.12本章小结本章节通过Adams/view仿真分析确定零部件在整体装配过程中的尺寸及角度优化,根据创建物理模型运动曲线结果,主要针对车轮侧滑、车轮前束和车轮外倾角等参数优化,优化前车轮侧滑量相对较大,优化后车轮侧滑量明显减少。汽车实际行驶中减少轮胎的磨损,从而延长轮胎使用寿命。对车轮前束、车轮外倾角优化使其变化范围减小,在允许范围内变化,达到优化的目的。60\n第4章悬架实体建模4.1Pro/E介绍自1988年Pro/ENGINEER问世以来,该软件不断发展和完善,目前已是世界上最为普及的CAD/CAE/CAM软件之一,基本上成为三维CAD的一个标准平台。Pro/ENGINEER广泛应用于电子、机械、磨具、工业设计、汽车、航空航天、家电、玩具等行业、是一个全方位的3D产品开发软件。它集零件设计、产品装配、磨具开发、NC加工、钣金设计、铸造件设计、造型设计、逆向工程、自动测量、机构模拟、压力分析、产品数据管理等功能于一体。此外,Pro/ENGINEER采用三维设计技术,不仅能预见设计产品的外观,更能创立统一的数据库,可进行毅力分析、强度分析、质量属性分析、空间运动学分析、装配干涉分析、模具设计与NC可加工型分析、还可自动生成标准、准确的二维工程图。4.2悬架零件实体建模4.2.1螺旋弹簧创建单击菜单文件→新建命令,再打开新建对话框中选择零件类型,在名称栏中输入名称”spring”选择使用缺省模版选项,单击确定按钮没进入零件设计模式。单击菜单[插入]→[螺旋扫描]→[伸出项]命令,打开属性菜单,点击属性菜单命令[常数的]→[穿过轴]→[右手定则],然后点击完成命令。选择FRONT基准面为草绘平面,单击[正向]接受默认试图方向,单击[草绘视图],菜单中的[缺省命令],系统进入草绘状态。绘制旋转轴与轮廓线,如下图:图3.49创建弹簧草图60\n点击,输入螺距值30,绘制截面,截面为直径为14的圆。单击确定按钮,完成spring创建。图3.50弹簧实体模型4.2.2轮胎创建选择拉伸,绘制截面图,拉伸长度为2033.15,采用拉伸,去除材料绘制轮胎花纹,拉伸深度为4,将创建花纹阵列,选择方向阵列。将拉伸的体环行折弯,首先点击插入~高级~环行折弯,在系统弹出对话框中,选择360→双侧都→曲面折弯收缩→完成,绘制特征截面草图,创建草绘坐标系,确定,选择两个平行的面,完成。选择所绘图形镜像实体模型。生成图形如下:图3.51轮胎实体模型60\n4.2.3盘式制动器创建首先运用拉伸命令,拉伸出直径200厚度20的圆盘,再以圆盘一个面为基面,拉伸出直径150,深度为5的体,同理在另一面拉伸一直径为120拉伸长度为50的台,根据直径为22的半轴,拉伸~去材料,拉伸一直径为22.5的通孔。在直径为150的圆台上拉伸一直径为15的圆柱体,拉伸长度为50。螺纹创建,选择主菜单中插入→螺旋扫描→切口,弹出剪切:螺旋扫描对话框,同时弹出的是属性对话框,选择常数→穿过轴→右手定则~完成,弹出设置草绘对话框设置平面对话框下拉菜单中选择新设置→平面。创建DTM1界面选择圆柱体轴、制动盘实体轴确定DTM1。选择DTM1面作为草绘平面。方向下拉菜单中选择正向,草绘视图中选择缺省。进入草绘模式,绘制扫描轨迹,其中中心线代表旋转轴,点击,定义节距为2,绘制螺纹截面线,单击,方向选正向,完成后,单击螺旋扫描对话框,确定按钮,生成切剪螺纹。阵列圆柱体,运用轴,阵列个数6,角度60度点击确定。绘制模型如下:图3.52制动器实体模型4.2.4转向拉杆创建通过拉伸,拉伸长度为300的圆柱体,扫描球型,图形如下:60\n图3.53转向拉杆4.2.5上横臂创建通过扫描绘制球接触面和上横臂杆,拉伸圆柱体绘制销连接体。图3.54上横臂实体模型4.2.6下横臂创建通过拉伸,扫描创建,图形如下:图3.55下横臂实体模型4.2.7半轴创建通过拉伸、扫描~切口创建,模型如下:60\n图3.56半轴实体模型4.2.8叉形件创建通过拉伸扫描,拉伸去除材料绘制叉形件,图形如下:图3.57叉形件实体模型4.2.9转向节的创建通过拉伸,扫描、旋转.图3.58转向节实体模型60\n4.3整体装配图选择组建,将前面所画部件,分别通过放置/约束圆柱/约束平面,将其组建为整体,图3.59悬架装配实体图形创建分解图,在整体装配图基础上,选择视图/分解/法向平面,选取某一方向平面,沿着轴线移动,将零部件放置在方便视图的位置。图3.60悬架装配爆炸图4.4本章小结通过运用软件Pro/E绘制悬架各部件的实体模型,主要应用软件的拉伸、扫描、旋转、螺旋扫描、环行折弯等功能并通过组装的功能,进行整体装配,创建了实体模型,使本次设计更加直观。60\n结论现代汽车悬架的发展十分快,不断出现崭新的悬架装置。悬架技术的每次跨越,都和相关学科的发展密切相关,如计算机技术、自动控制技术、运动仿真等,为悬架的进一步发展提供了有力的保障。悬架的发展也给相关学科提出更高的理论要求,使人类的认识迈向新的、更高的境界。汽车悬架系统是一个比较复杂的多体系统,所以开发和设计合理的汽车悬架系统是十分重要。传统的汽车悬架系统设计都要通过多次物理样机的实验,花费了大量的时间和金钱。因此,汽车悬架系统的虚拟样机仿真分析具有十分重要的意义,虚拟样机技术是在不制造出物理样机的情况下,通过计算机的仿真分析提供悬架设计的仿真数据,为实际悬架系统的设计提供可靠依据。大大缩短了生产周期,提高生产效率。本设计基于机械系统动力学仿真分析软件ADAMS直接创建完全参数化的机械系统几何模型,运用了pro/e软件将优化好的尺寸,构建实体模型,大体设计如下:首先,搜集资料双横臂独立悬架结构及结构优势进行学习,通过对独立双横臂悬架的结构分析,选出在设计中需要参数化的尺寸。其次,运用ADAMS/View软件建立双横臂独立悬架等效物理模型,加上路面的激励后分析车轮跳动时悬架的各种参数的变化。优化分析参数值,使其达到车轮侧滑量最低,减小太磨损,提高其使用寿命。再次,总结优化分析结果,由于汽车悬架的主销后倾角、主销内倾都在合理范围内,主要针对车轮前束、车轮外倾及车轮侧滑量,进行性分析,根据上下横臂的长度、倾角不同,选出参数在其不同取值下的最优值。优化后车轮外倾角由优化前的-1.3~3.3优化为-0.1~2.6,前轮前束角由优化前的-1.8~3优化为-0.8~1.05,前轮接地点横向侧滑量由优化前的-2.3mm~16mm优化为-0.3mm~9.2mm取得了明显优化效果,车轮接地点横向侧滑量在合理范围内。虽然有一定的负值,但数值比优化前明显改善,对轮胎磨损影响明显降低。最后,利用计算机辅助设计软件Pro/E,建立了双横臂独立悬架各部件的三维实体模型,并将其根据连接关系组装,便于观看,创建分解图型。本次设计主要意义,经过分析优化后,改善了传统物理样机试验的繁琐,节省了时间和费用,为实际生产提供有力依据,缩短生产周期,有显著的实际意义。60\n参考文献[1]陈家瑞主编.汽车构造下册/第2版.机械工业出版社[M].2005[2]余志生主编.汽车理论第五版.机械工业出版社[M].2009.3[3]徐灏主编.机械设计手册.第三卷.机械工业出版社[4]刘维信主编.汽车设计第一版.清华大学出版社[M].2001.7[5]刘虹,王其东.基于ADAMS双横臂独立悬架运动学仿真分析[期刊论文].合肥工业大学学报[J].2007.1[6]李静,初亮,鲁和安.双横臂独立悬架导向机构的运动特性[期刊论文]农业机械学报[J].2002.3[7]毛务本,韩锐.独立悬架转向梯形机构断开点的优化[期刊论文].江苏大学学报[J],2004.3[8]杨可桢,程光蕴,李仲生主编.机械设计基础高等教育出版社[M]2006.5[9]王其东,陈无畏,何文辉,吴越俊.基于多体动力学的双横臂独立悬架线刚度的计算.农业机械学报[J].2004.5[10]周四新主编.Pro/ENGINEERWildfire3.0实例教程.电子工业出版社[M].2007.7[11]张亮亮,裴永生,吴丹丹.基于ADAMS的双横臂独立悬架的仿真分析及优化设计.燕山大学车辆与能源学院[J].2010[12]周松鹤,徐烈烜主编.工程力学.机械工业出版社[M].2007.9[13]李军,邢俊,文谭文洁.ADAMS实例教程[M].2002[14]蒋国平,王国林,周空亢.独立悬架转向梯形断开点位置的优化设计[J].2007.2.7.[15]王丰,黄志刚,朱慧.ADAMS在汽车前悬架仿真应用与优化研究[N]:北京工商大学机械自动化学院,北京工商大学学报,2008.5.7.[16]王国强,张进平,马若丁.虚拟样机技术及其在ADAMS上的实践[M]:西北工业大学出版社,2002.[17]梁新成,黄志刚,朱亭,穆以东.汽车悬架的发展现状和展望[D]:北京工商大学机械自动化学院,2006.2.30.[18PengShuang,SongJian.StateKeyLaboratoryofAutomotiveSafetyandEnergy,TsinghuaUniversity,PostCode[19]UsingADAMS/ViewFunctionBuilderVersion12.0.MDI[J].2002[20]KeiichiMotoyamaPhD.TakashiYamanakaAStudyofSuspensionDesignUsingOptimizationTechniqueandDOE[J].200060\n致 谢转眼间,毕业设计设计已接近尾声工作了,毕业设计过程中每天为学习软件和结构布置而忙碌,此刻,深刻体会到,过程虽然痛苦,但感觉却是收获满满,四年的大学生活即将结束,就要离开我生活四年的大学——黑龙江工程学院,,大学四年我从对汽车简单的喜欢到现在的深入学习,此时此刻,感慨颇多。在我的毕业设计过程中,着实遇到了很多问题,软件方面的问题颇多,这些都在杨兆老师的帮助下,一一解决,在此,向在我整个设计过程中提供无私帮助的杨兆老师表示衷心的感谢,此外我要对在这四年生活中默默教授我们专业知识的汽车系全体老师表示感谢和由衷的敬意!60\n60查看更多