- 2021-05-10 发布 |
- 37.5 KB |
- 17页
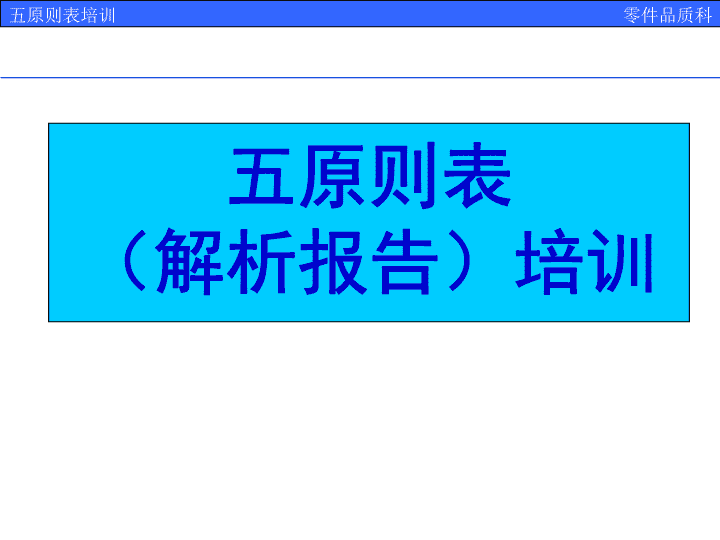
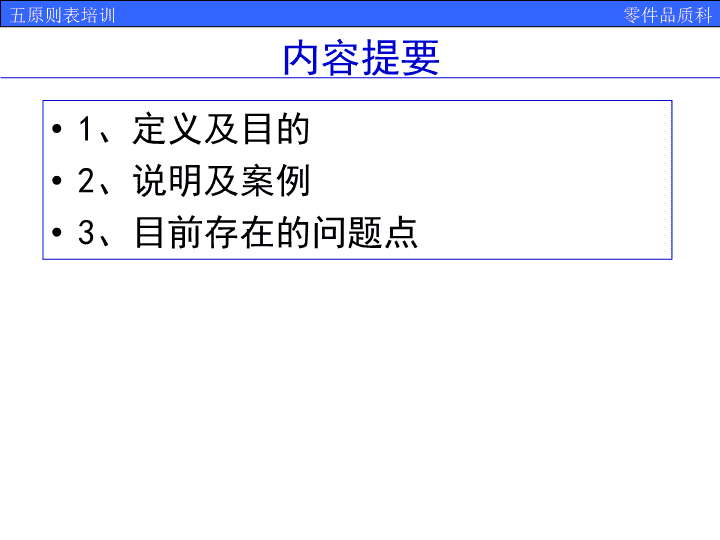
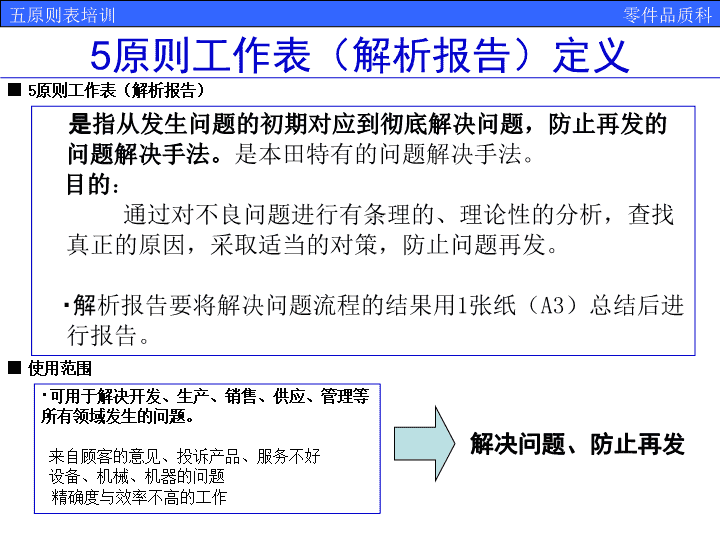
申明敬告: 本站不保证该用户上传的文档完整性,不预览、不比对内容而直接下载产生的反悔问题本站不予受理。
文档介绍
5原则解析报告培训资料
五原则表(解析报告)培训 内容提要 1 、定义及目的 2 、说明及案例 3 、目前存在的问题点 5 原则工作表(解析报告)定义 是 指从发生问题的 初期对应 到 彻底解决问题 , 防止再发 的问题解决手法。 是本田特有的问题解决手法。 目的 : 通过对不良问题进行有条理的、理论性的分析,查找真正的原因,采取适当的对策,防止问题再发。 ・ 解 析报告要将解决问题流程的结果用 1 张纸( A3 )总结后进行报告。 ■ 5 原则工作表(解 析报告) ・ 可用于解决开发、生产、销售、供应、管理等所有领域发生的问题。 来自顾客的意见、投诉产品、服务不好 设备、机械、机器的问题 精确度与效率不高的工作 ■ 使用范围 解决问题、防止再发 重要度的决定及处置判断 重要度、麻烦度、重要保安部品判断 重要度 麻烦度 重要保安部品 A 不良时判断为危害人身安全的重大危害 操纵、行走、制动 火灾、感电、公害、安全不能保护 A 已进行整车的检测、修理 HS 不良时,重要机能丧失,可能引发重大事故 B 除 A 外,产品机能和商品性受到损害 B 已进行零件的检测、修理 HA 不良时,重要机能丧失,可能引发重大事故,但可预知并进行安全处置 C 不属于 A 或 B C 已对供应商进行了警告 HB 不良时,重要机能丧失,不引发重大事故 不良对策要求的发行 对策要求不良 (PIR) (problem improvement request) 信息联络不良 解析报告( 5 原则表)适用范围 “ 重要度 A” 的问题 “重要度 B 或 C” 的问题,但发生频率较高 基本上以 PIR 发行的项目为全部对象 展开解析报告的 5 个步骤 原因 分析 ( WHY 、 WHY 分析) 步骤 2 3 5 4 1 内 容 ( 填写查明 原因 的过程 ) 3 、合适的 対策(対策内容・ 效果顺序 ・PPA ) 2 、查 明原因( 发生 的原因 ・ 重现测试 ) 1-A发生状况(现象・ 所述 内容・发生件数・ 处理 内容) 4 、対策 效果 ( 效果 实绩) 5 、向 源 头反馈 ( 向体制 机构 反映内容) 1- B 把握事实 ( 零件确认结果・要因分析・生产件的品质状况) 1 3 4 5 2 1-A、发生状况(现象・ 所述 内容・发生件数・ 处理 内容 ) 1. 问题 类型 ( 产品 / 服务的投诉 等) 2. 发生 场所 (市 场、 公司内部 ) 3. 问题 发生 时的现象以及所述 内容 4. 发生 年月日 5. 发生 件数 6. 问题 和紧急处理 内容 1- B 、把握事实 ( 零件确认结果・要因分析・生产件的品质状况) 1. 问题 数量 2. 重现 测试 等的結果 3. 问题 发生 的原 因分析 ・用FMEA分析特性原因图 ・原因 和事实 的验证 、QC手法(7 种工具 ) 4. 现在 的対応 状况( 緊急処置後的) 5. 发生対象 范围 (发生率和台数) 及其根据 1 、老七种工具 调查表 分层法 排列图 因果图 直方图 控制图 散布图 2 、新七种工具 亲和图 树图 关联图 矩阵图 箭条图 PDPC 法(过程决策程序图法) 矩阵数据分析法 QC 小组活动的具体程序 2 、正确、恰当的应用统计方法 原因分析常用统计工具:因果图 系统图 关联图 三种图示方法的运用 原因分析常用统计工具:因果图 系统图 关联图 方法名称 适 用 场 合 原因之间的关系 展 开 层 次 因果图 / 鱼骨图 针对单一问题 进行原因分析 一般不超过四层 超过用系统图 系统图 / 树图 针对单一个问题 的原因进行分析 原因之间没 有交叉关系 没有限制 关联图 / 关系图 针对单一或多个问题的原因进行分析 原因之间有 交叉关系 没有限制 原因之间没 有交叉关系 1- B 、把握事实 问题点的概要 (测定结果) 从工序流程分析 要因和事实的分析 发生范围,批次追溯 1. 对于 发生要因、流出要因的原因分析 ・根据特性要因图、FMEA、KT手法调查原因 ・特别是由于制造引起的 问题,应从硬件 上 (设备、治具、工具、检具等)查明原因 2、对于原因引起的问题现象的再现性 (再现试验,现场・ 现物 ・ 现实 ・ 原理 ・ 原则检证) 原因 分析 ( WHY 、 WHY 分析) 问题的特性 步骤 2 3 5 4 1 内 容 ( 填写查明 原因 的过程 ) 真 正 原因 2 、查 明原因( 发生 的原因 ・ 重现测试 ) 明确与工序调查、再现试验、发生原理相联系的因果关系,发生原因及流出原因不是现象原因,而是要追溯到根本的原因。 记录查明原因的过程。 (发生要因、流出要因) 原因 分析 成为 特性要因图 问题 的特性 步骤 2 3 5 4 1 内 容 ( 填写查明 原因 的过程 ) 大枝(大骨) 中枝(中骨) 小枝 (真 正 原因 ) 小枝(小骨) 2 、查 明原因( 发生 的原因 ・ 重现测试 ) 3 、合适的 対策(対策内容・ 预测效果 ・PPA ) 对策内容 ・ 发生和流出原因分别填写 ・ 即使是人为引起的原因, 仍应在硬件上作对策 2. 对策年月日、对策对象零件、 机种、车身号 3. 临时对策与永久对策的效果 预测 ・根据再现试验、品质检查 数据预测效果 ・ 如果是暂定对策,明确过 渡到永久对策的期限 4. 填写对已出货产品的对策及 库存零件是否需要处理。 5. 对策的PPA 4 、对 策 效果 ( 效果 实绩) 1. 工序、市场的对策效果确认结果和确认时间 (・效果是由品质数据、数量等在对策前后的变化而取得的) 5 、向 源 头反馈 ( 向体制 机构 反映内容) 1.向持续维持硬件对策项目的相关部门反馈 (基准、标准等) 2.将问题反馈到其它部门(横向展开) (规程、基准、技术积累等) 三、目前存在的问题点 发生状况 不良的批组号容易遗漏 事实把握 不明确此次不良的涉及范围 不进行不良品的分析,履历等把握 不进行现过程,现品的把握 不知道工程概要(系统图)和要因分析的目的(如果结合鱼骨图进行,目的会更清晰) 要因的把握不足(没有认真论证) 原因究明, WHYWHY 分析 不注意因果和并列关系 发生和流出原因混合 分析不太够,太笼统致使无法知道真正的原因 没有必要的中间过渡显示太多 再现试验设定不合理 适当的对策 采用的对策与分析的原因不相符 对策效果 源流反馈 看不出如何反馈到体制或组织 源流反馈方面不太充分,考虑不足查看更多