- 2022-04-22 发布 |
- 37.5 KB |
- 238页
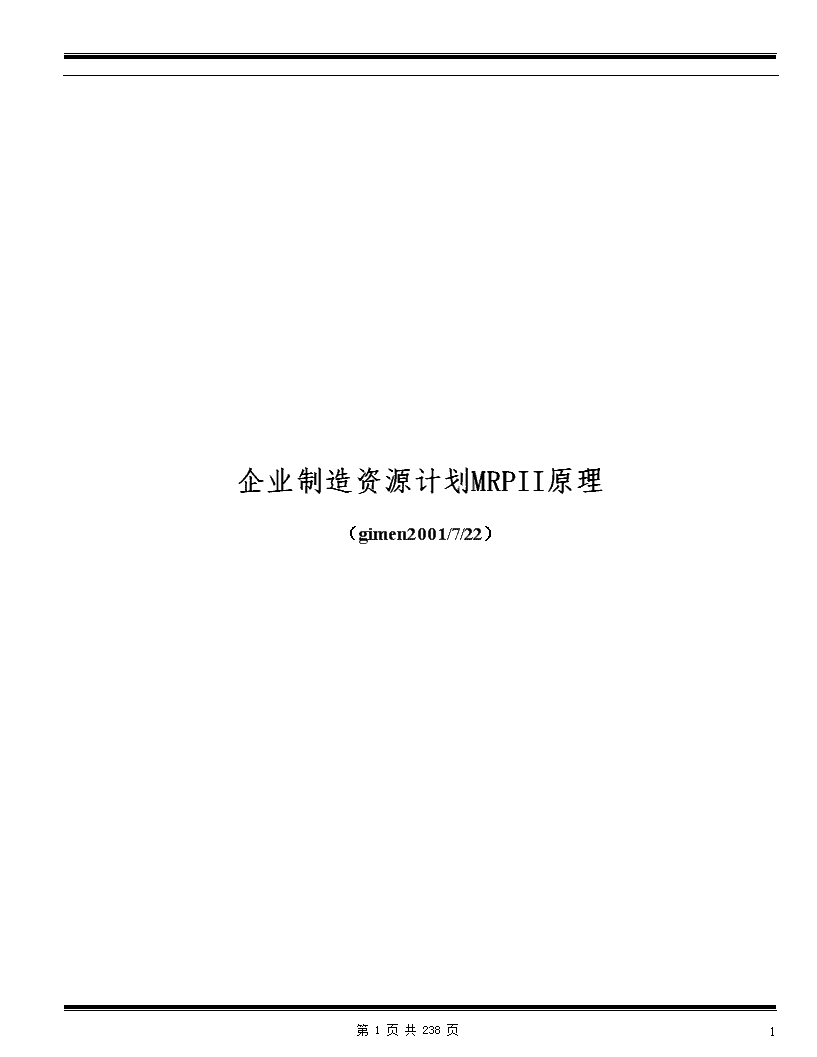
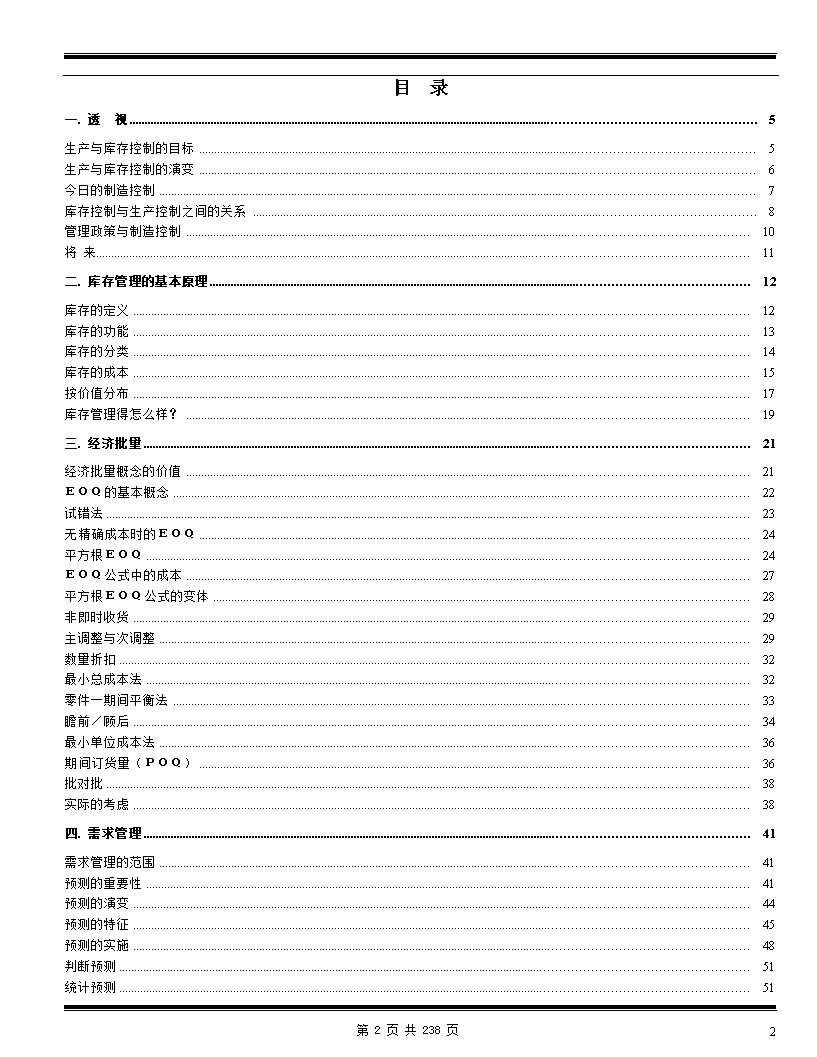
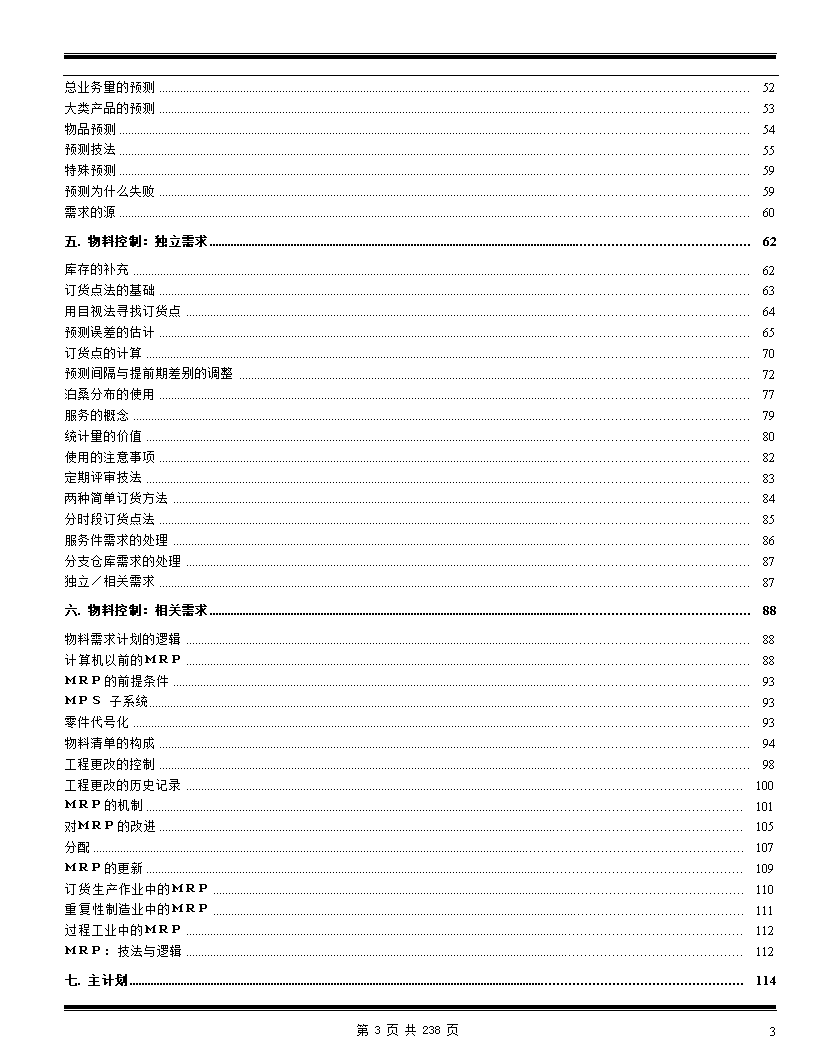
申明敬告: 本站不保证该用户上传的文档完整性,不预览、不比对内容而直接下载产生的反悔问题本站不予受理。
文档介绍
制造资源计划--企业制造资源计划mrpii原理
企业制造资源计划MRPII原理(gimen2001/7/22)238第238页共238页n目录一.透 视生产与库存控制的目标生产与库存控制的演变今日的制造控制库存控制与生产控制之间的关系管理政策与制造控制将来二.库存管理的基本原理库存的定义库存的功能库存的分类库存的成本按价值分布库存管理得怎么样?三.经济批量经济批量概念的价值EOQ的基本概念试错法无精确成本时的EOQ平方根EOQEOQ公式中的成本平方根EOQ公式的变体非即时收货主调整与次调整数量折扣最小总成本法零件─期间平衡法瞻前/顾后最小单位成本法期间订货量(POQ)批对批实际的考虑四.需求管理需求管理的范围预测的重要性预测的演变预测的特征预测的实施判断预测统计预测238第238页共238页n总业务量的预测大类产品的预测物品预测预测技法特殊预测预测为什么失败需求的源五.物料控制:独立需求库存的补充订货点法的基础用目视法寻找订货点预测误差的估计订货点的计算预测间隔与提前期差别的调整泊桑分布的使用服务的概念统计量的价值使用的注意事项定期评审技法两种简单订货方法分时段订货点法服务件需求的处理分支仓库需求的处理独立/相关需求六.物料控制:相关需求物料需求计划的逻辑计算机以前的MRPMRP的前提条件MPS子系统零件代号化物料清单的构成工程更改的控制工程更改的历史记录MRP的机制对MRP的改进分配MRP的更新订货生产作业中的MRP重复性制造业中的MRP过程工业中的MRPMRP:技法与逻辑七.主计划238第238页共238页n计划的阶梯结构主生产计划(TheMasterProductionSchedule缩写为MPS)MPS是什么MPS不是什么MPS的输入不同企业中的MPS为了灵活性而超量计划MPSMPS的视界MPS的格式关于MPS的误解MPS的问题MPS的用途管理层对MPS的作用八.总量库存管理总量控制的必要性投入产出总量控制总量批量库存总量安全存货库存总量在制品库存总量期望库存总量运输库存总量屏障库存管理好总的库存投资九.能力需求计划提前期:种类与要素能力计划的一种合理方法生产计划的制定季节性生产计划生产计划工作中的实际因素功能部门的粗能力计划细能力需求计划外购物料的能力计划订货生产工厂中的能力计划工作能力计划图解技法优先级与能力计划的结合十.投入控制投入控制在有效制造控制中的作用选择恰当的投入从属工作中心的日程计划控制车间投入的行动安排日程计划的技法工作中心加负荷的方法238第238页共238页n对供应商的投入控制装配作业的日程计划安排线性规划与排队论实际的考虑十一.产出控制控制的要素控制能力的必要投入/产出控制能力控制中的实际考虑产出控制中的相关要素优先级控制的目的催稽(Expediting)调度(Dispatching)流动控制(FlowControl)重新安排日程计划与优先级规则看板提前期控制任务车间仿真(JobShopSimultion)有效的车间现场控制产出控制技法的选择十二.反馈与校正行动反馈──控制的基础订货生产厂中的反馈与校正行动备货生产厂中的反馈与校正行动采购中的反馈几种反馈技法绩效的度量作业控制(OperatingControls)系统健康状况诊断校正行动的生成计划与控制职能的管理压缩库存缩短提前期制造控制的未来238第238页共238页n企业制造资源计划MRPII原理一.透 视生产与库存控制的目标大多数旨在获取利润的制造企业有三个主要目标:1、最大的客户服务2、最小的库存投资3、高效率(低成本)的工厂作业达成这些目标的过程中主要的问题是这些目标基本上是互相冲突的。若把库存水平提得很高而且不惜通过改变生产水平与生产日程去满足客户需求的变化,就可以提供最大的客户服务。但这种做法要以牺牲第二,第三个目标来达成第一个目标。若生产水平难得更改,不发生加班加点,机器一旦调整好之后就长期地运转,只生产这一特定产品,则工厂作业可保持高效率;然而,其结果却是在达成最高工厂效率这一目标的同时带来巨大的库存量与不良的客户服务。倘若使客户等待而且强迫工厂对客户需求的变化与生产的中断迅速作出响应,则库存可以保持低水平。在现实世界中,由于上述的三个目标对于持久的成功几乎同等地重要,很少有哪家公司能当得起只顾全其中一个目标而排斥另外两个目标。生产与库存控制基本上就是同为在工厂作业中协调这些目标所需的日常决策提供所需信息这件事打交道。对于拥有自己的小小制造公司的一名经理,这些目标基本冲突这一事实是明摆着的。他对工厂中的机器设备投入了他的资金,他控制着自己的制造日程,他又是他自己的销售代表。当一家客户要求立即交货时,他的对策是清楚的─-或者化钱去搞调整机器与加班加点,或者让客户等待。他也可以采取为未来的生意持有库存──成品、零件或原材料──的对策,以便有可能给他的客户以更好的服务。在这样一个只有一名经理的公司中就存在着这些目标之间的冲突,它们不是容易解决的,但至少该经理能看到这个冲突并权衡自己的诸种对策。在今日的一家大的制造公司里,为客户服务的责任落在组织中的一个部门,即销售部,它很少考虑提高工厂效率或降低库存水平的责任。另一方面,制造部门的人员通常对库存感有不多的责任,对客户服务也许感有稍多一点责任。事实上,许多车间经理与监工人员恐怕从来也不是从客户的观点来看待他们的活动的。往往,这些人员的绩效并非以他们对公司总体目标的贡献来衡量,而是以他们达成他们被委派的有限目的的能力来衡量的。例如,很少有第一线的监工人员是以他们控制提前时间与保持存货中有物品的能力来衡量的。但他们的事业很大程度上取决于他们完成生产任务有多好,同工会打交道有多好以及能否满足预算的开销目标。由于同样的原因,很少有销售人员是按他们对利润的贡献来判断的;他们完全是根据销售更多产品的能力来评价的。在今日的商业界有一种被说得过了头的陈词滥调,这就是:让一家公司内部的经理们互相竞争是健康的。如果这些经理是为着同一些目标而竞争,那么这种说法之中确有真理,因为这样竞争能产生极好的结果,但若他们开始为着不同目标而竞争,则其结果将是浪费、冲突与挫折。在一家现代化的公司里,经理们的责任已经明确划分,他们的绩效度量鼓励他们去搞次238第238页共238页n优化,在这种公司里要去协调这些互相冲突的目标成了一个挑战性的问题;试图解决这一问题便是生产与库存计划与控制的主要功能。生产与库存控制要通过一个信息系统来起作用,它编制计划,对照计划度量实际绩效,然后将信息传递给必须采取校正行动的直线管理人员,其功能就是去协调这些目标以满足公司总的利润目标。没有其它小组去干这件事。生产与库存控制的演变生产控制与库存控制是分开来发展的。在最初,生产控制只是直线主管人员要完成的许多功能之一。他订购材料,通过雇佣与解雇人员确定工人人数与生产水平,通过他的部门催稽工作并通过库存来控制客户服务,而库存多少又是他努力的结果。由于工作量的增加,用一名文书作他的助手,以关照计时,保管各种记录及电话应答等职能。这使得文书在回答工作状态与有关交货允诺的查询时经常同销售部门发生接触;除了跟踪工作进展之外,文书还开始作物料订货与生产上所需的其它准备工作的计划。这种文书实际上就是生产控制职能的开始。后来,随着记录保管活动被转移到了主办公室,这个文书发展成为一名催货员。在1890年代,一家著名的新英格兰公司中有一个部门就叫"催办部"──很容易想象这些人的责任与活动。对生产控制有过一些使之成为更加有组织并更加科学的方法的企图;在1880年代某兵工厂(WatertowArsenal)曾设置相当广泛的生产控制系统,但第二次世界大战以前它并未得到普遍的应用。在第二次世界大战中,催货员的处境是名誉扫地,因为在同事心目中他是同危机、混乱、压力与麻烦相伴的。造船公司老板HennyKaiser把他公司里的催货员取名为催稽员。他通过《读者文摘》上的文章,推广了催稽员作为一名志向行动的能干而有进取心并对满足生产日程作出极其重要贡献的人的概念。1950年代时,在书本里往往用催稽这个词来定义生产控制。当时的一位实际工作人员把他自己的活动描述为收到一位客户的订单之后他先订购装配所需要的零件,然后,当客户来查问为何未能如期交货时,则追踪订单,找出这些零件在哪里,并贴上“急件”标签。即使今天,催稽员仍是大多数生产控制系统的必要组成部分之一。库存控制是沿着更为科学的(至少在理论上)路线发展的。经济批量的基本概念发表于1915年(1),确定订货点的统计方法在1934年由R.H.Wilson提出。(8)然而,这些相当复杂的库存管理系统技法很少获得应用。也许这是因为由于1930年代与1940年代不是鼓励科学管理的年代。在1930年代的衰退时,对大多数公司而言最重要的目标是生存。就像在大洋上空一架失事的飞机上的人们为了减轻飞机的载荷而往机外投掷食品与珍贵物品那样,在大衰退的年代里长期利润与成长变成次要的了。1940年代后期,当被抑制的需求为所能生产出来的每件东西提供有一个现成的市场时,库存控制的目标──平准工作负荷或在客户服务的基础上竞争──在大多数企业经营中也不是重要问题。自从1900年代早期到第二次世界大战,在Taylor,Emerson,Gannt,Gilbreth以及其他人所创导下的科学管理运动使得人们公认生产计划与控制应该是一种参谋活动;其结果是在大多数公司里建立了明确的生产与库存控制职能──但它通常是非常原始的。生产控制,除了有一些简单的机器加载技法以外,在大多数公司里仍基本上是靠催稽;库存控制虽然开发出了一些科学的理论,但并无多大实际的应用。从第二次世界大战迎来了运筹学,即应用科学技法去解决战争问题的学问。在战争中有限资源的分配是关系到战争胜负的大事。运筹学的技法在二次大战中显得相当管用。当这些做过运筹工作的科学家回来处理和平世界的问题时,他们的注意力集中到了生产与库存控制问题上,因为该问题的要素可用数字表达,用得上概率统计理论,而且这方面有许多决策是238第238页共238页n平衡多种解决方案的结果。在预测、库存控制与数学规划方面得出了一些值得注意的结果。虽然运筹学并未解决了多少它着手解决的事务问题,但它确实引发了采用一种更加合理的方法去控制生产与库存的新的兴趣。在工业中应用科学技法的最大问题恐怕是事实上公司并未为科学技法的应用作好准备。他们甚至还未开始去解决制造控制中的许多基本问题。许多公司甚至连比较精确的构成产品的零件清单或说明作业顺序的工艺单也没有;他们依靠的是工厂里已制造过该产品多年的人们的记忆。要应用科学技法,基本信息必须准确而且立等可用。此外,要应用由运筹学高度地开发出来的诸如统计预测技法与确定订货点的统计技法,所需的计算工作量也大大超过了手工系统的能力。到了1950年代后期,工业中已广泛使用了电子计算机,但如同大多数新技术一样,在这些强有力的工具的应用中,失败与成功一样的多。被计算机处理的信息应该完整而准确,因为倘若丢失了信息,就会产生明显可笑的错误,却没有人工干预可以来弥补。由于计算机在计算方面提供了几乎无限的能力,人们集中注意于信息处理中所需的纪律,因为许多公司在过去并未注意过这个问题。应用计算机的努力往往是企图在公司中装置一套机械化的系统而没有对手工系统给予足够的重视,以致使系统不能顺利地工作。1957年,27名生产与库存控制工作者集会于Cleveland并创建了美国生产与库存控制协会(APICS)。其目标是开发本行业的知识主体,传播关于语言、原理与技法的信息,以及对会员与本领域的其它人员进行教育。APICS通过它的杂志,训练手段,特别报告,支部会议与研讨会,地区性会议以及每年一度的国际会议,在生产与库存控制的发展中已成为一支强有力的力量。在它的第一个25年中,该协会已成长到拥有约200个支部──遍及全世界每一工业国家──会员人数已超过了50,000人。同时,该领域的语言有了一本辞典加以定义,文献被编入一系列文献目录,建立了教育与研究基金会以扩充知识主体,设置了一个学术联络委员会以促进实际工作者与学术界之间的沟通,而协会的财务力量增强到了能够在Virginia州FallsChurch购置了协会的总部大楼。然而,也许最有影响的发展还是证书计划。像公证会计师、工程师、医生与其它专业人员一样,现在人们可以通过考试来证明他们对本领域的理解了。自1973年起到本协会的25岁生日为止,已进行过70,000次以上考试,7300多人获得了证书,其中1100多人达到了受人尊敬的会员水平。随着实际工作者作用的增大,他们在各自公司组织中的地位和薪金也随之高升。生产与库存控制人员从催货员与文书,经过计划员、主管人与经理一直不断地升迁到主管同该领域有关的一切职能(在许多情况下包括数据处理职能)的公司副主席级别。妇女们起着越来越大的作用并且现今已在组织的各级任职。本领域的名称先是更改为物料控制,后来又更名为制造控制ManufacturingControl)。今日的制造控制改进作业的计划与控制今天被认为是一家公司恢复或保持力量中不可缺少的需要。从1970年代中期开始,采用现代的计算机化的一体化系统的项目来达到这一目的是普通的。在许多公司里都采用叫做物料管理的组织结构。虽然有许多不同的做法,典型的形式是,物料经理负责交通、采购、库存与生产的计划与控制、收发货、分库、存货房以及厂际卡车运输。物料管理概念是杂志文章的主题,并引起了采购代理人、库存与生产控制经理与物料搬运经理之间的许多热烈的讨论与竞争。关于哪一种活动提供了物料管理职位的最好准备,他们意见纷纭──往往忽视了这样一个事实,为这样一个新近建立的职位选用人员应该在很大程度上看他个人的专业知识与管理才能而不是看他过去的经验。 作为一种组织形式,物料管理确会带来一些实在的好处,不幸的是,它也不是万应灵丹238第238页共238页n。这种组织形式并不会自动促进计划与控制系统、过程或技法的使用。没有它也可以使用所有上述这些。从这种组织形式可以导致的主要好处是由于所有与工厂内部的物流有关的人员都向一个人报告,此人能够指导这些人齐心工作去获得最好的合作与有效性。如果要使主管们与他手下负责物料搬运、交通、采购与生产控制的人员一道有效地工作的唯一办法是让他们向一个头头报告,那么物料管理概念确会带来真实的潜在好处。缺点是缺乏远见;物料毕竟只是制造控制中的一个重要因素,资金、工人与机器至少也是同样重要的。 一家公司应否采用物料管理概念?如果公司有一个组织问题或者如果一次重新组织将带来更多内行人才来帮助解决某些问题,那是应该采用的。倘若实际问题在于系统设计不当、信息质量不好且不及时或执行不力,则改变组织将不能解决这些问题,这时采用重新组织反而会分散注意力或延误了解决实际问题的行动。 制造控制的真正挑战在于恰当地去应用已知的工具与技法。自相矛盾的是实际工作者知道他们的公司“与众不同”,可是他们又在不断地寻找一种别人成功地使用过的技法,希望这种技法能解决他们的问题。倘若对基本原理无知或忽视了,那么盲目地移植技法是无用的。只要继续仅仅看重技法而把原理当作技法的附属品,那么再好的技法也将被误用,而结果将是令人失望的。原理1对于一切制造行业,有效的计划与控制所需的系统框架是共同的。 只是着重的要素有所不同,技法的应用方法也不一样。在我们的工具箱中有满满一整套的工具;有普遍适用的基本原理;应用这些原理并恰当地使用工具,我们就能像模像样地做好制造业的管理。可以从每一行业中举出成功的公司的实例来证明我们是站得住脚的。时常有人这样提问:在西方工业世界(美国、加拿大、欧洲)罕有公司能比得上日本人的绩效,其奥秘在哪里?真相既简单又优美──日本人按基本原理正确地去做,他们把整个作业看作一个单一的过程并通过集体协作去改善它。 原理2一家制造工厂是一个单独的实体,需要有一个一体化的系统与集体的协作去管理它。 生产前:研究与开发应用设计样品生产(原型生产)方法,机床安装与标准设备采购工厂布局 作业计划与控制:主生产计划能力优先级执行:供应商交货车间中心的出产机器设备的维修解决问题238第238页共238页n库存控制与生产控制之间的关系 工业界一种常遇的误解是认为生产控制与库存控制是分开的功能:库存控制写订单;生产控制把它们在工厂里造出来。然而,基本的真理是一家制造厂里的库存是用来支持生产的,而库存本身又是生产的结果。只有在库存是采购进来而不作进一步加工就再出售的场合,库存控制方能具有独立于生产控制之外的意义。 确定经济批量: 平方根法 零件一周期平衡法 最小总成本法 Welch系列 最小单位成本法 批对批 主/次调整 期间订货量法 LIMIT 预测: 台尔菲法 一阶指数平滑法 判断法 二阶指数平滑法 移动平均法 基指数法(季节性) 加权平均法 S-曲线 Focus 物料计划: 一般的: ABC分类法,总量交易曲线 订货点: 经典的 保留存货(正态分布) 分时段的 保留存货(泊桑分布) 两箱的 周期性评审 目视评审 物料需求计划: 展开表 结构化物料清单 传统的 工程更改控制 重新生成法 分配法 净改变法 溯源法 能力计划: 生产计划 细能力需求计划 粗能力需求计划 图解法 投入控制: 定单选择 块日程计划法 CPM 向前安排日程法 无限负荷法 CPS 倒推安排日程法 有限负荷法 PERT 出产控制: 投入/出产控制 赶制 临界比 调度 反馈 流动控制 许多文献提到订货量、订货点与MRP等主题时把一家制造厂里的库存控制假设为一种独立的功能。然而,倘若不考虑它们如何影响工厂的生产量与组件的日程计划,就不能成功地使用MRP、订货点与经济订货量等方法去控制成品的库存。同理,也不能离开了生成订238第238页共238页n单从而构成生产日程的库存控制系统去开发生产日程计划技法。摆在工厂里各个作业面前的欠交订单是非常实际的库存,而且通过它们对提前时间的影响会对订货技法具有非常实际的影响。如果日程计划系统要恰当地去控制生产,它就必须控制这些库存。 由于采购通常同库存控制与生产控制二者都是分开的,自然把三者都当作独立活动来运行。然而,当库存控制在功能上同生产控制分开时,典型的做法是库存管理人员在个别物品达到其订货点或订单发放日期时就给车间发放订单,然后生产管理人员就试图加快这些订单通过各道制造作业,对车间人员施加压力去加点工作,作额外的调整,转移劳动力或采取其它非常的──因而是昂贵的──行动去对付工作的峰谷起伏。实际上,这种做法往往造成波动不定的欠交制造订单与各制造设施面前大量的在制物料,因为车间作业人员总是力求保持生产以均衡速率来进行。使用欠交订单来平整工作负荷当然意味着高库存、长提前期与不良的服务。在许多公司里,库存控制对这一问题的反应就是简单地断言他们提出了订单的正确交货日期而制造部门必须按时完成这些订单。运筹学的主要论点是人们趋向于朝着次要的目标去工作,或者说去搞“次优化”,前述情况是这一论断再好不过的说明了。也许这种责任分割与随之发生的两种职能双双低效,其最重要的后果就是生产控制与制造部门几乎总是沦为工厂诸种毛病的代人受罪者。生产控制人员把第一线人员看成是目光短浅的与不愿合作的。车间人员感到生产控制人员是不负责任而且总是要求什么而本身对高效地运行工厂不但极少或是毫无贡献,甚至是一种干扰与引起混乱的原因。销售人员则把车间看作“套在我们脖子上的一块磨石”。有效的制造控制要求所有职能部门协力工作以达成所有三个目标。如果该控制系统能够分解为独立的要素以致各自可以处理自己的责任领域而无需顾及其它要素的话,那当然皆大欢喜。不幸的是,一个制造控制系统的诸要素是相互密切地联系着的,实际上你不能把它们互相孤立起来而不损害它们的有效性。管理政策与制造控制为了达成客户服务、库存周转与高效的工厂作业这三个目标,所采取的行动应该根据明确的管理政策来进行,但往往发生两种失误。一种是管理者未能掌握作出正确决策所需的突出的事实,另一种是管理者未能确定恰当地控制其作业所需的重要政策。第一种情况的适例是许多管理者根据行业平均数来确定对库存周转率的政策。采取行业平均周转率为本公司的目标有两个基本假设:第一、本行业其它公司对他们的作业管理得颇为得当;第二、这些行业是可比的。这两条假设都是颇成问题的。此外,他们忽略了:大多数管理者把周转目标订得很低。另一方面,倘若政策没有明确定义,管理者通过默认就会把决策权下放给了文书人员。例如,物料计划人员会按照他们发出补充库存订单的方式来制订公司政策。这些文书人员并不具备为公司的总体要求来确定最佳库存水平所需的信息。他们总是对眼前的压力作出反应──当工厂达成生产目的有最大困难时就增加库存,当工厂能够以较高产量生产产品时就减少库存。缺乏关于库存水平的明智政策也会导致在生意下降时去采取过分地看重库存的惊谎失措的行动。通常的反应是去发布一个规定,必须削减多少库存量,而不考虑生意上的需要,也未充分理解这种削减可能对客户服务、成本与雇佣水平产生的影响。不但客户服务会受到损失,不适时地过分地压缩库存会使原来由于需求下降而引起的产量变化大大地放大。当生意又转好并发动应急计划来重建已耗尽的库存时,又会发生相反的顺序(伴之以同样的放大效应)。不良的库存管理与生产计划工作恶化了经济危机周期的后果。现代社会,还有专业管理人员,应该期望与要求有更好的绩效。在一家运营良好的现代公司里,有关库存、客户服务与工厂雇佣与解雇的管理政策应根238第238页共238页n据制造计划与控制职能提供的信息合理地来制订。有效的管理者明辨每一问题处境中的真正备选方案,深知许多看起来不可摧毁的公司由于其管理者不能认识与面对不愉快的备选方案并适时作出必要的决定去防止现实的灾难而垮掉了。主生产计划提供一种把政策转换成计划的机制。把政策翻译成数目字的过程(叫做制订主生产计划)要求所有职能之间的集体协作。这一过程所开发出的一套数目字是用来驱动正式系统的。一旦政策已经建立,制造计划与控制经理就开发计划以配合这些政策并跟踪查看该计划被恰当地执行。经理无需直接指挥领班或车间与工具房中的工人,也无需直接指挥维修人员或工程技术人员,他的主要角色是对其它经理人员发出信息,必须完成什麽以达到共同目标。在某种程度上,经理必须作为催化剂,催促别人采取正当的行动以达成公司的总体目标。要做好这件事,经理不需拥有去告诉一名主管人员何时必须加点或应去从事更加紧迫的工作的权威──这种权威应该放给直线人员,车间经理,主管人与部门主管。也许可用5W1H这六个基本问题来说明其间的区别。计划与控制根据管理政策与三项基本目标确定应该制造什么物品(What)、多大数量以及应该何时完成(When)。决定该产品应如何(How)并在何处(Where)制造,以及谁(Who)应去制造它则是制造人员与其支持部门的事。当实际绩效不符计划时(这是常有的事),对为什么(Why)的答案将取决于其原因是计划不好还是执行得不好。将来制造控制已经从一组简单的日常零星工作演变到如今接近于管理上注意力的焦点这样一种地位。先进的高层主管人员认识到需有一个健全的职能去计划与控制工厂的作业。计算机的到来已使配有强有力技法的、完全一体化的系统成为实际可行,然而许多公司发现难以充分利用这些可能性。主要原因是他们未能以任何一种实际控制系统都要求的有纪律的方式来掌握信息。同时,他们发现产品越来越复杂,加上在成本与服务上的竞争压力,已经使得用人工的与支离破碎的系统去管理他们的作业成为不可能的了。必须废弃老办法。1960年代期间,制造计划与控制挣扎着要打破“发出订单然后催办”的作业方式。设计出了计算机程序来保管库存记录与重新计算所需的经济订货量与安全存货。实际工作者勇敢地工作以获得正确的批量与安全存货量以便为需求与提前期中不可避免的变化作缓冲。他们对数学家、统计学家的帮助与计算机的魔力是满怀感激之情的。然而,在1970年代里,已经弄清楚真正需要的是有效的订单交货日期。这就要求有一种重新计划的能力,一个联系着物料清单中父件与组件的一体化日程计划以及通过控制订单优先级的提前期管理。这时人们把希望寄托在强有力的计算机上的MRP身上。1980年代初期,大局完全澄清了。去管理任何制造作业都要求有一个健全的、一体化的、执行得好的计划。更频繁地去修改计划并不会改进计划。原理3.更短的提前期是使计划更加有效的最重要因素。执行计划要求解决妨碍生产的各种问题,而不是用库存去弥补问题或用缓冲时间去补偿问题。解决这些问题要靠整个制造过程中涉及的所有人员之间的集体协作。没有万应灵丹,没有祷告词,没有咒语,没有魔法──只有依靠在基本问题上的苦干。制造控制是一种一体化的概念,不是许多技法的松散的汇集。它的注意力集中在为所有管理人员提供及时、客观的决策备选方案。这些管理人员转过来正在认识着一个竞争性商业世界中的一条基本真理:在任何一个想利用它的市场营销机会、控制其财务投资与运转其制造设施去获取利润的公司里,其心脏是一个有效的计划与控制系统──但还必须有肌肉去执行该项计划。制造是可以控制的,而且其回报是巨大的。成功的公司要使计划与执行平衡发展。238第238页共238页n二.库存管理的基本原理库存的定义若向同制造有关的任何一群人提问什么是库存,你将得到两种答案。1.主要同成本与财务有关的人将回答库存是金钱,一种取物料形式的资产或现金。2.同作业有关的人将说库存是成品、原材料、在制品或产品中使用的物料。这种财务观点是一种真正的自相矛盾。毫无疑问库存具有价值,特别是当买进或卖出公司时,它们的价值总是表示在资产负债平衡表上资产的一方。然而哪位经理能够具体地讲得出库存如何赚得回一笔利润(任何资产都应赚回利润)或者,至少同样重要的,它赚回了多少利润?实际上毫无例外地,从财务观点看库存的人都深信库存越少越好──从错误的理由得出的一个正确结论,并且是对待真实资产的一种奇怪方法。他们谈论库存好象它们纯粹是债务似的。把库存看作生产用物料的人也有类似的近视病。一般说来他们相信库存多些更好。它可为抵挡“蛮横的命运女神的投石器与箭”──变幻莫测的客户,蹩脚的供应商,不正常的机器还有墨菲定律──提供缓冲软垫。库存多一点为好,以防万一。他们也并未考虑投资的回报。这两种人都把他们的思考局限于产品库存──同被生产出来并卖出去的货物有关的物料。 真正的专业人员懂得还有其它两类库存:生产前的物料与维修用物料。它们二者都需要显著的投资(虽然有些会计人员把大量的项目作为开支冲销),二者对制造都是不可缺少的,而且对二者都可使用正式的计划与控制系统中的信息与库存控制的优良技法做出更加有效的管理。这两类库存的采购与补偿问题超出了本书的范围。第四条原理确认这种管理是必要的。原理4.制造控制要求对所有的三类库存有效地加以管理。在商业界时常听说三种陈词滥调: 1.你不能从空的货车卖货。 2.库存是企业的墓地。 3.你们为何不多制造点──我们好一直使用它们。 这些评语说明在达到合理的库存决策过程中涉及的问题。库存虽代表一家公司总资产的相当大的一部分,但难得有其它业务问题受到人们如此的偏袒。销售部门把库存看作良好的客户服务所不可少的,而倘若当应该发货时有什么物品缺货的话就感到是制造部门失责了。财务人员相信库存是一种必要的祸害,因为它束缚了资金,本来可以更好地使用于别处的。车间人员不易理解持有库存的代价而时常由于库存控制措施给车间带来明显不便就以感到沮丧的态度来对待这些措施。显然,问题是由于他们各自都是从狭隘的观点而不是从公司总体的观点来看待库存的。然则从公司总体观点来看什么是库存呢?库存在一家企业中的作用犹如一辆汽车的悬挂系统,销售量的起伏可由库存来吸收,犹如汽车的弹簧可吸收道路的颠簸。没有库存,如果要不使对客户的服务受到损害就必须使生产直接响应销售。库存还解脱具有不同生产速率的各个制造作业。批量库存使得较少生产调整与更高的机器利用率成为可能。在制品可以防范由于不稳定的物流引起的人员与设备的停工。 在前面讲过制造中三个冲突的目标是良好的客户服务、最小限度的库存投资与高效的工厂作业,而制造控制工作就是为公司的最大利益去协调这三个目标。库存对于作出良好的客户服务,通过保持生产以相当速率运行并运作合理规模的制造批量从而使工厂更有效率地运238第238页共238页n行都是必要的。库存并非一种必要的祸害而是一种非常有用的减震器。然而,虽然持有一些库存是必要也是有用的,库存过多却是有害的。在大多数公司里,资源都是有限的:用在库存上面的金钱对于改进工厂、给股东支付红利、开发新产品以及一家朝气蓬勃的公司对资金的其它用途也是需要的。过量的库存没有用处而只是束缚了资金。 因此,从公司总体的观点,考虑每一种资金需求的利益与代价来平衡库存投资与其它资金需求是重要的。这种平衡所要求的决策可分为四大类:1.库存投资与客户服务之间希望有什么样的平衡?在具有有效的制造控制去执行管理政策并有意料之外的需求或供应中断发生的地方,库存持有量与其所造成的服务之间存在着一种确定的关系。库存量越低,欠交与缺货就越多;库存量越高,服务就越好。2.库存投资与改变生产水平所伴随的成本之间希望有什么样的平衡?如果生产必须响应销售率的变化而波动,则过大的设备能力、加班加点、停工、雇佣、培训与解雇工人等有关费用将升高。库存可以阻滞这些波动。3.库存投资与发放补充库存的订单之间希望有什么样的平衡?频繁地运行工作或以小批量多次发放采购订单可以降低库存持有量。这样做的结果是高的生产调整与采购费用、过多的其它作业开支与失去了数量折扣。4.库存投资与运输成本之间希望有什么样的平衡?例如,为每小时移动工件去提供劳务与物料搬运设备比之每日移动工件要求较大的开销。运输方式越快,成本越高。库存的功能按功能区分,库存有五种基本类型:1.波动(需求与供应)库存2.预期库存3.批量库存4.运输库存5.屏障库存波动库存:这是由于销售与生产的数量与时机不能被准确地预测而持有的库存。对一给定物品其平均订货量可能是每周100单位,但有时销售量可高达300或400单位。通常从工厂订货后三周可收到订货,但有时可能要用六周。这些需求与供应中的波动可用后备存货或安全存货来弥补;后备存货或安全存货也就是波动库存的常用名。当通过诸工作中心的工作流不能完全平衡时,在工作中心也存在波动库存。在生产计划中可以提供名为稳定存货的波动库存以满足需求中的随机变化而不需改变生产水平。预期库存:这是为迎接一个高峰销售季节、一次市场营销推销计划或一次工厂关闭期而预先建立起来的库存。基本上,预期库存就是为未来的需要也是为了限制生产速率的变化而储备工时与机时。批量库存:要按照物品的销售速率去制造或采购物品往往是不可能或不实际的。因此,要以大于眼前所需的数量去获得物品;由此造成的库存就是批量库存。生产调整时间是确定此类库存时的一个主要因素。运输库存:这是由于物料必须从一处移动到另一处而存在的库存。处在卡车上被运往一个仓库去的库存在途中可能要经历10天之久。当在途时,库存不能为工厂或客户服务──它存在的原因只是由于运输需要时间。屏障(或投机性)库存:使用大量基本矿产品(诸如煤、汽油、银或水泥)或农牧产品238第238页共238页n(诸如羊毛、谷类或动物产品)的公司可以通过在价低时大量购进这些价格易于波动的物品而实现可观的节约,这种库存就叫屏障库存。还有,对预计以后将要涨价的物品在现行价格较低时便买进额外数量就将降低该物品的物料成本。这类交易中的重要因素包括价格趋势、废弃风险与处理商品的前景等,已超过了本书的范围。显然,由此而实现的节约是对该项追加投资真正的报酬。作为例子,考虑一种典型的成品,它可按每年12批。每批1000件来制造。每个月,库存将收货1000件。如果均匀地使用掉,则现有数将平均为500件──其平均批量库存就将是500件。为弥补需求的波动,可能再额外持有250件作为后备或安全存货。因此该物品的平均总库存量(等于平均批量库存加上安全存货)将为750件。为迎接即将来临的一个假期,那时工厂将关闭,可能要给库存再加上250件,这就是预期库存。如果此产品要通过远方的分支仓库来分配,则在主厂与仓库之间还将存在在途的运输库存。下面是各类按功能区分的库存其投资与报酬之间的关系。注意这些库存的功能是有重叠的。季节性的预期库存将像安全存货那样提供更好的客户服务,例如,它们同样能减少对总需求率中小量变化作出反应的必要性。为利用库存所能起的双重作用,彻底考虑这些库存共享的相互关系是必要的。类型功能好处批量为各制造作业解偶(即采购上的折扣;减少生产自动机床与装配;供应调整、物料搬运、文书工商与使用者)作与检查费用等等。需求-波动为意料之外的需求保险增加销售;减少外运、替(安全存货)代更高价产品、客户服务、文书的、电话、电报、包装等费用。供给-波动为供应中断保险(即罢减少停工与加点、替代物工,供应商提前期变动)料与货物运入;增加销售预期平整生产量(即去满足季减少加点、转包合同、雇佣、节性销售,市场营销的促解雇、解雇保险、培训、报销)废与返工费用等等。减少所需设备的富裕能力运输填满分配渠道(即在途,增加销售,减少运输、搬分支仓库与托付物料)运与包装费用屏障为涨价提拱屏障(即铜、降低物料成本银)库存的分类除了按功能分类之外,库存也可按其在加工过程中的地位来分类1、原料:用来制造成品中组件的钢铁、面粉、木料、布料或其它物料。2、组件:准备投入产品总装的零件或子装配件。3、在制品:工厂中正被加工或等待于作业之间的物料与组件。4、成品:备货生产工厂里库存中所持有的已完工物品或订货生产工厂里准备按某一订单发货给客户的完工货物。238第238页共238页n在会计报告中,库存总值是用这种分类法分别加以表示的。每家公司都有这类数据;其唯一用处是去显示库存是增加了还是减少了。为什么如此,一家工厂应该持有多少库存,该库存赚回着什么报酬,这些都是合理的问题。不幸的是,最多只能说这样分类方便了会计的工作而已。原理5、控制要求有真正算数的数字,而不只是容易计数的数字。成本会计做法的细节超出了本书的范围。使用以后各章所述的技法对库存按其功能作一分析,通常能在不减收的条件下带来非常可观的库存压缩或在不增额外库存的条件下带来非常可观的增收。库存的成本决定持有多大库存时必须确定每一具体决定对成本的影响。在库存决策中涉及的成本有以下几类:1、订货成本:订货成本有两种:一种是由于发出采购订单去向供应商购买物料而发生的成本;另一种是由于向工厂发出订单而发生的成本。采购物料时,必须书写物料申请单与采购订单,必须处理发票付款给供应商,收进的货物必须检查并送交存贮室或加工地。向工厂订制一批物料时,要发生文书工作的成本、机器调整费、新调整后首次生产带来的开工报废品以及其它取决于订货或生产的批数的一次性费用。所有这些费用之和就是该批的订货成本。2、库存持有成本:包括公司由于所持有的库存量而发生的一切成本。通常包括下列因素:a、报废.由于销售模式与客户要求更改使库存物资不再可销而发生的费用。在时尚货物、高技术与国防工业中,这个问题是尖锐的。b、损坏.库存物资可能受潮、干透、由于搬运而弄脏或以其它许多方式损坏,因而不再可售或不再可用。c、税.许多州、市要课库存税。有些是根据年度中某一特定时间的库存投资额,有的根据全年的平均库存投资额来课税。d、保险.库存像其它资产一样要投保,通常这是公司保险政策的一部分。e、存储.存储库存需要有存储室、主管人员、操作人员、物料搬运设备、必要的记录、等等。倘若没有库存,就不会发生这些设施的费用。f、资金.投资于库存的金钱就不能用于公司的其它活动了。事实上,可能要从银行去借这笔钱。借钱的代价或失去的投资机会即使用这笔资金于公司的其它用途的机会,必须算作库存投资的资金成本。3、缺货成本:倘若客户订货时没有该物料可供发货,就可能失去销售或可能发生叫作缺货成本的额外的破费。处理欠交订单的工作量(发货、开发票还有库存控制的文书工作与加点)可能是可观的。欠交订单的费用不但来自额外的文书工作,还来自各部门中处理欠交订单文书、检货与包装、回答查询的人员化费的时间。此成本还可能包括诸如由于发货量小而产生高货运额外费用等因素。4、能力关联成本:与能力有关的成本包括加点、转包合同、雇佣、培训、解雇与停工时间费用。当需要增加或减少能力或能力暂时地过多或过少时就会发生这种费用。要确定与使用各项成本来作库存决策会遇到许多困难问题。即使认识了要加以考虑的具体因素,对大多数公司而言其会计记录也不能立即以可使用与有意义的形式来提供所需的成本数据。有两条基本法则可适用于这些成本:1、它们应当是实际的付现成本,而不是标准会计成本。238第238页共238页n2、它们应该是真正受到正在被作出的具体决定影响的那些费用。在使用成本数据于一个库存决策问题之前,必须具体地回答“该项节约将来自何方?”与“将节约多少?”这两个问题,以便确信该计算真正代表实际生活处境。下面一一考察这四种成本。订货成本:订货成本的基本问题是如何分离出那些随发出订单的多少而变化的成本要素。下面举一个采购物料的简单例子。一家很小的公司里用一位年薪¥16,000的采购员,他一年发出2000份采购订单,主要给本地商人。该采购员不用文书工作,他每次化¥025拨公用电话就把订单发出了。货款从办公桌抽屉里一个现金匣内支付。每份采购单的成本可计算如下:采购员工资=¥16,000电话费=500────────总计=¥16,500每份订单的成本=¥16,500/2000=¥8.25显然,该公司每年少发些订单将可以省些钱。如果采购批量稍增一些,每年只发1500份采购订单,则节约金额似乎为:(2000-1500)×¥8.25=500×¥8.25,或每年¥4125。然而,由于采购员的工资不会因之而减少,他的时间也不能有效地用来做其它工作,实际上少发订单只能省下些电话费,所以公司实际上只能节省¥125每年。如此看来,一份采购订单的成本不是¥8.25,而只是¥0.25。在作库存决策时,只有在能够取消所有采购时(或者采购单降到很低水平以致某一其它人员可以兼顾此项工作而不需公司增加开支,从而取消了采购员职位时),才可以把¥8.25作为一份采购订单的订货成本。研究制造批量与订货成本时对生产调整费用也需作类似的分析。通过运行较大批量来减少生产调整次数也将不能为公司节省一分钱,如果其结果只是使调整人员的工作轻松些而已。同理,除非减少订单能够减少文书工作的费用,否则就不应把这种间接费用包括进去。库存持有成本:库存持有成本是一个有用的概念(尽管它是一个人工的概念),它是用来计算批量的数学公式中所需要的。如前所述,这项费用是假设由许多个别要素构成的。在任何库存中报废都是一种现实,但这一要素随时间而大大地变动,而且对不同物品也不相同(即对时尚物品这一费用最高)。这就意味着在存货清单中每一物品要使用不同的持有成本。这显然是不实际的,通常选用一个平均数字,或适用于所有产品或适用于每一种主要产品类型。同样的道理也适用于损坏费用。税款通常较易处理,特别当税率是根据库存的平均价值来制订时。至少迄今为止,税款只占总的库存持有成本中很小的一部分。在决定批量大小时,存储费用与有关的搬运费用可作为一个单独的要素来处理,如附录Ⅲ的EOQ公式推导中所示。然而,为了简化与方便起见,这些费用通常假设为库存持有成的一部分。库存持有成本中的存储费部份,像其它要素一样,被假设为随着库存量的大小而正变。实际上,除非减少库存省下来的存储空间能改作它用,否则是没有节约的,反之,除非增加的存储空间必须用或建造更多的仓储能力,否则,增加库存并不增加存储费用。重要并引起争议最多的库存持有成本要素之一是资金成本,它包括束缚于库存中的资金的价值。前面讲过有两种可供选择的方案:1、倘若增加库存时要从银行或其它资金源去借款。倘若降低库存可以减少贷款,则假238第238页共238页n设这种贷款的利息作为库存资金的恰当成本看来是合理的。2、许多实际工作者相信恰当的成本是管理者对本企业中总资金所期望的投资报酬,不管该资金源是存货销售款,应计盈余还是借来的钱。第二方案比第一方案中库存的成本要高得多。使用第二方案还产生一个采用什么样的报酬率的问题──是用现在实际赚进的报酬率还是用管理者计划在未来要赚的净资产报酬率呢?恰当的选择也可能要因时而异。某一时候管理者可能希望降低库存以便从内部挖掘资金的潜力或提高公司净资产的报酬以便使公司的股票对投资者或在兼并交易中更具吸引力。把这样的目标表达为一种成本简直不值得。上述全部讨论纯粹是学院式的。库存持有成本的实际用途只是作为管理上的一个政策变量,与其说它是一个固定的,不可思议的数目字,不如说这是一个应加以驾驭以达成公司总体目标的一个变量。这一概念的进一步讨论及其在库存管理中的使用方法。缺货成本:要试图去确定缺货成本也会引起同上的困难问题。客户对欠交订单的不满可能是代价十分昂贵的,但要给它定一个具体值是困难的──如果不说是不可能的话。一份欠交订单可能引起客户小的或无所谓的不便,而再次的欠交就可能成为将来客户到别处去购买的原因。缺货成本,如同库存持有成本一样,是数学公式所要求的人工概念,这数学公式是为了辅助作出库存决策而推导出来的。我们不应该,因为有了这样一个数目字就如此地“被数学上的方便所迷惑”⑴以致看不清这类决策的实际含义或其总合的影响。能力关联成本:诸如加点与停工时间之类的成本,往往可使用会计数据计算出来;然而,雇用、培训与解雇费用,像订货成本那样,不是线性的。虽然举例说解雇补偿税明显地随雇佣水平而变,其它伴随雇佣、培训与解雇的费用是隐蔽在诸如人事部门的主管或作业总费用之中的,只有当一项活动的变化达到使人事部门中的文书劳务有所增减时才会使这些费用变化。按价值分布对于任何给定的组类,组类中的少数项目将占总值的大部份。在美国约20%的人占有80%的财富;约20%不同样式的车辆占了年度汽车销售量的80%;家庭预算中20%项目占了现金开支80%。这是商务中非常有用的一个概念,它可应用于库存控制、生产控制、质量控制以及其它许多管理问题。这是生产控制的基本原理中最有用、最有效却最少被利用的。应用于库存时,这一概念叫做ABC分类法。任何库存可区分为三个不同部份:1、A类物品:高值──其价值占库存总值70─80%的相对少数物品。通常为物品的15─20%。2、B类物品:中值──其总值占库存总值的15─20%。物品数居中,通常占物品的30─40%。3、C类物品:低值──其库存总值几乎可以忽略不计,只占5─10%。是物品的大多数,通常占60─70%。分为A、B、C三大类当然是任意的;许多公司作进一步的分类,例如加一个D类或把A类再分为AAA、AA与A三等。每类物品,当然在该类之中又作ABC分布。有些物品值得工厂经理个人的关怀,只因为它们代表巨额的金钱。这一概念在许多其它制造控制活动中有着广泛的应用:238第238页共238页n1、少数客户给一家公司大多数的订单。2、少数部门完成制造作业的大部分工作。3、少数作业产生废品的大多数。4、少数供应商造成大多数采购物品中的延误。5、少数物品包揽了大多数对客户的欠交订单。以一个只有10种物品的简化例子来说明如何去做ABC分析。第一步列出这些物品及其年度使用量,然后用单价乘以年度使用量,最后从年度使用金额最高的开始将这些物品排序,物品每年使用件数单位成本(¥)年度使用金额(¥)序数──────────────────────────────────F-1140,0000.07¥2,8005F-20195,0000.1121,4501F-314,0000.104009L-45100,0000.055,0003L-512,0000.1428010L-16240,0000.0716,8002L-1716,0000.081,2806N-880,0000.064,8004N-9110,0000.077007N-1005,0000.094508──────────────────────────────────第二步,按序数排列这些物品并计算出累计年使用金额与累计百分数,如果任意地决定A类物品将是这些物品中最前面的20%,则A类将包括第一与第二两种物品。第三到第五这三类物品将属B类物品,它们占总物品数的30%。其余50%的物品将属C类物品。物品年度使用金额(¥)累计年使用金额(¥)累计百分数类别──────────────────────────────────F-20¥21,450¥21,45039.8%AL-1616,80038,25071.0%AL-455,00043,25080.2%BN-84,80048,05089.3%BF-112,80050,85094.4%BL-171,28052,13096.7%CN-9170052,83097.9%CN-10045053,28098.9%CF-3140053,68099.6%CL-5128053,960100.0%C──────────────────────────────────这一ABC分析可归纳下表所示。如果把最大精力集中于A类物品,可使其库存压缩25%。这就是总库存的相当可观的一笔压缩,即使C类物品由于控制不严而增加了50%也不要紧。分类物品的%每组的年使用金额金额的%──────────────────────────────────A=F-20,L-1620%¥38,25071.0%B=L-45,N-8,F-1130%12,60023.4%238第238页共238页nC=所有其它50%3,1105.6%──────────────────────────────────总计100%¥53,960100%关于ABC方法有两条基本法则要牢记:1、控制的程度:a.对A类物品,尽可能地严加控制,包括最最完备、准确的记录,最高层监督的经常评审,从供应商按总括订单频繁交货,对车间紧密跟踪去压缩提前期,等等。b.对B类物品,作正常控制,包括良好的记录与常规的关注。c.C类物品,尽可能使用最简便的控制,诸如定期目视检查库存实物、简化的记录或只有最简的标志法表明补充存货已经订货了,采用大库存量与订货量以避免缺货还有安排车间日程计划时给以低优先级就可以了。2、库存记录:a.A类物品要求最准确、完整与明细的记录,要频繁地甚至实时地更新记录。对事务文件、报废损失、收货与发货的严密控制是不可能缺少的。b.B类物品只需正常的记录处理,成批更新,等等。c.C类物品,不用记录(或只用最简单的),成批更新,简化的以大量计数等等。3、优先级a.在一切活动中给A类物品以高优先级以压缩其提前期与库存。b.B类物品只要求正常的处理,仅在关键时给以高优先级。c.给C类物品以最低的优先级。4、订货过程a.对A类物品提供仔细、准确的订货量、订货点与MRP数据。对计算机数据需用人工核对,再加上频繁地评审以压缩库存。b.对B类物品,每季度或当发生主要变化时评审一次EOQ与订货点,MRP的输出按例行公事处理。c.对C类物品不要求作EOQ或订货点计算。订货往往不用MRP作计划。手头存货还相当多时就订上一年的供应量。使用目视评审,堆放,等等。库存管理得怎么样?工业的库存在经济危机周期中的作用已成为经济学家、政治家与企业界领导人极为关注的话题。他们对于如何最好地解决这一问题拿不出什么一致的意见,但都认为问题在于如何能控制住库存以便最大限度地减少或消除它对经济危机周期的放大效应。当销售率在消费者水平上变化时,生产速率也必须改变。这些变化之间的时间间隔取决于1、新趋势被识别为一种趋势而非随机性波动有多快。2、库存应该增加还是减少。3、希望库存改变多少。当销售率增大时,控制良好的库存水平也必须增大以维持客户服务在同一水平上。于是要求加大生产量以满足1、销售率的增大2、所希望的库存增长额这第二个因素当然是暂时的,它只存在到必要的库存增长额得到供应为止。然而由于它,238第238页共238页n销售量中等的增长就会引起生产上很大的增长,特别当管理者迅速行动去维持客户服务时。相反的效应则是当销售量虽然中等地下降时,却引起了生产剧烈地下降。对这种波动必须建立控制以缓解解雇的冲击与衰退──繁荣周期的其它弊病。有许多例子,例如:...在汽车制造业中,零售业销售量中5%的变化,可以放大为汽车装配厂中10%的变化,装配厂下面一级组件制造商那里20%的变化,在第三级那里也许40%的变化。如果我们比较汽车零售销售趋势与汽车用钢板的采购量,我们发现汽车用钢板采购量的大幅度升降更多地是由于库存修正引起的,而不是对汽车的真正需求量的变化引起的。这不仅是一个汽车的问题,因为大多数美国工业是按同样的原理起作用的。⑷由于汽车行业在控制技法方面比许多其它行业更为先进,所以这一效应特别显著。另一篇文章认为零售销售量中的变化对工厂出产的影响将被放大到6─10倍。⑺为60天订货法则,它说明当我们采用“凭常识的”库存控制技法时,怎么会发生这种类型的被放大的库存涨落。六十天订货法则是一种很简单的技法,可陈述如下:“每次重新订货时,订足够数量的物料使得现有库存与已订货量的总数等于过去60天的销售量”。这一法则体现了销售方面对库存应如何管理的概念,它在分支仓库被广泛应用。┎────┰────┰────┰────┰────┐┃月份┃销售量┃目标库存┃现有库存┃工厂订货│┠────╂────╂────╂────╂────┤┃一月┃60┃120┃60┃60│┠────╂────╂────╂────╂────┤┃二月┃60┃120┃60┃60│┠────╂────╂────╂────╂────┤┃三月┃80┃140┃40┃100│┠────╂────╂────╂────╂────┤┃四月┃90┃170┃50┃120│┠────╂────╂────╂────╂────┤┃五月┃100┃190┃70┃120│┠────╂────╂────╂────╂────┤┃六月┃90┃190┃100┃90│┠────╂────╂────╂────╂────┤┃七月┃80┃170┃110┃60│┠────╂────╂────╂────╂────┤┃八月┃60┃140┃110┃30│┖────┸────┸────┸────┸────┘在上例中,销售从三月至五月增加相当多而从六月至八月下降了许多。目标库存,或“达标水平”总是等于前两个月的销售量。例如二月份的目标库存是120,等于一、二月份销售量之和。现有库存量是上月的余额加上月的工厂订货再减去本月的销售量。本月份的新工厂订货量等于从目标库存减去现有库存。注意这种“常识性”技法所造成的相当大的放大作用。销售量从最低点增大到最高点100,而工厂订货增到120。当销售量八月份降低到60时工厂订货实际下降到30。这种内行所用的订货技法是引起严重的库存升降问题的相当重要原因。库存的大幅升降又放大了经济危机周期。当生意上去时如果要提供同等水平的服务毫无疑问库存应有所增加,但只要对健全的库238第238页共238页n存控制原理略有所知,就懂得库存的增加不应正比于销售的增长。实际上,如果恰当地来管理库存,对于短期的销售增长,减少点库存并不会损害客户服务。而且,制品的库存不能由库存控制技法单独来控制,因为改变生产量代价高而且不容易,所以要用库存来帮助稳定生产,特别在重复性生产与过程工业中。有效地使用库存来帮助维持低成本并提供有竞争力的客户服务而又无需过多的库存投资,要求懂得制造控制的基本原理。这些原理与实施它们的技法将是后续各章的主题。238第238页共238页n三.经济批量经济批量概念的价值在制造控制的分析中,通常把自然地落入同一组类的物品放在一起研究是方便与实际的。这些组类可以是同一些制造设备所加工的零件组成,或由同一采购员办理的采购物品组成,或由从同一供应商订货的物品组成。在确定采购物品的批量时特别适用。当考虑相关零件的系列时,成本、资金需求、空间需求、作业条件及确定批量时必须考虑的其它因素最有意义。在批量计算的首例中,有5个物品。这些物品可想象为在同一设备上制造的产品。图所示为现状,批量根据经验确定,每季度运行一次,这是非专业人员时常采用的具有代表性的直觉法则。物品年使用金额目前年订货次数目前订货量───────────────────────────────────1¥10,0004¥2,50026,40041,60032,5004625440041005144436───────────────────────────────────总计20¥4,861平均批量库存=¥2,430经验批量对每种物品一年做4次生产调整或订货,总计每年有20份订单;平均批量库存等于批量库存总计的二分之一,即¥2430。这是假设每批都是收进一整批货然后在一段时间内均匀地使用,直到库存降为零,因此平均批量库存为批量的一半。显然,倘若把物品5的若干次生产调整转用于物品1,就可显著地压缩库存。即使一次生产出全年度的物品5,对库存投资也无多大影响,而对于物品1每多作一次生产调整却可减少相当多的库存。图所示为重新分配这20次生产调整后的情形。其结果是每年总的订货次数没有变,但平均批量库存由¥2430降到了¥1828。物品年使用金额建议的年订货次数建议的订货量───────────────────────────────────1¥10,00010¥1,00026,40051,28032,50038334400140051441144──────────────────────────────────238第238页共238页n总计20¥3,657平均批量库存=¥1,828生产调整的经济使用原理6.把生产调整次数分配给高值物品以降低其库存,可轻而易举地补偿低值物品库存的增长。用目视法作这类分析只有在物品数很小时才实用。有时对一些由关键工作中心制造的关键物品使用这种普通方法就可作出显著改进。虽然所得的订货量尚非经济订货量(因为未考虑库存持有成本、生产调整或订货成本),但它们比原来的订货量要合理些。使用它们将降低同持有成本相关的一切费用而并不影响同订货有关的成本。在许多公司里──特别是从制造厂家购进货物然后销售给零售商的批发仓库──多年来通常使用这样的制度:每隔2或3个月审查一次全部产品并将它们全部同时重新订货,而且其订货量以供应时间计算是相等的(譬如每种物品2个月的供应量)。当联合采购所有物品可享受折扣时,这种办法是有点道理的,但这类重新订货的体制时常只是由于它看起来似乎有道理就被采用了。例如第二章中所举的60天订货法则与图凭目视法作出的改进都是非专业方法的适例。它们都不是经济解;有更好的重新分配生产调整或重新订货的办法可以显著地改进公司资源的使用。所示的办法是否每年作20次生产调整的最优分配法?实际上它不是的。有一种简单的数学方法可以得出订货的更好分配法。在研究这种计算法之前,首先要懂得EOQ(EconomicOrderQuantity)即经济订货量的概念。在许多情况下EOQ概念是没有价值的。在下列情况下计算EOQ是没有理由的,当1、客户规定了数量(即,对于订货生产物品)2、生产运行批量受设备能力限制(例如精细化工产品)。3、产品的货架寿命是短促的。4、工具寿命或需要磨刀、修饰等等、限制了运行时间。5、原料的批量限死了订货量。EOQ的基本概念在库存管理中必须作出的基本决定之一就是对照发出重新补充库存的订单的成本平衡库存投资的成本。要回答的问题是,应该订多少货。正确的订货数量要使同发出订单的次数有关的成本与同所发订单的订货量有关的成本达到最好的平衡。当这两种成本恰当地平衡时,总成本最小。这时所得的订货量就叫做经济批量或经济订货量(EOQ)。EOQ概念适用于下列情况:1、该物品成批地,或通过采购或通过制造而得到补充,它不是连续地生产出来的。2、销售或使用的速率是均匀的,而且同该物品的正常生产速率相比是低的,使得显著数量的库存因而产生。EOQ概念并不适用于为库存而生产的一切物品。例如,在一家精炼厂或一条装配线上,生产是连续的而且不存在这样的批量。在一家订货生产工厂里大多数工作是按客户订货的批量生产的。工具寿命有限、货架寿命短、原料的经济使用和其它约束压倒了EOQ技法的应用。尽管如此,这一概念在工业界仍有广泛的应用,因为大多数生产不是连续式的而是从一个库存取出一批一批的物料进行加工,然后送交另一库存。在一个制造组织中去区分经济的制造批量与移动批量是重要的。移动批量通常由容器尺238第238页共238页n寸或货盘容量确定,它可以是经济批量的一小部份。管好制造批量与采购批量这二者是必不可少的,因为它们往往代表库存的最大的单独起作用的部份。确定批量的技法是这类管理工作的良好工具,但专业的实际工作者知道它们的应用实际上只是在一种恶劣情况下求其尽可能地好而已。当生产调整成本或订货成本高时,EOQ引进订货成本与库存持有成本的平衡使总成本最小。但若能压低生产调整或订货的成本,则可以实现更好的结果,加上某些巨大的额外利益。原理7.正确的EOQ是好的,但更短的生产调整比它要好得多。独立地工作时,物料控制人员可选用批量确定技法并应用它们为公司取得某些好处。同主管人员、工具设计者、制造与设计工程师与工人集体合作时,这些人员通过缩短生产调整时间可以产生比这些利益大许多倍的利益。日本人已不容置疑地证明了这一点。试错法在选用批量时有哪些备选方案呢?假设工厂制造订单授权本厂的工人去制造一种标准的存货物品。可以发一份补货订单去生产全年的需求量。这意味着工厂在该年度将只需为制造物品作一次生产调整。也意味着平均批量库存很大,如果使用率是均匀的,它将等于半年的需求量。倘若一年中订货50次──接近于每周一次──就可大大削减这一年平均批量库存。但将给该厂加上一个很重的负担,因为这项工作要作50次生产调整才能完成全年的需求量。这两种极端的方案所示。在确定经济批量时必年需求量=¥1,000产值─────────────────────每年补货次数批量平均批量库存1¥1,000¥500502010─────────────────────须面临的基本的两难问题是:不频繁地订货可使订货或生产调整成本下降但带来的库存投资将很高;频繁地订货可使库存降低但带来的订货成本将很高。确定经济批量要求找出能使总成本即二者之和最小的那个订货量。例如,设发一份补货订单的成本是¥10(如果只考虑付现成本,这可以是实际的;本例的成本数据并非旨在表现实际成本而是为了说明如何计算,说明其中的关系)。再设库存持有成本等于每年库存投资金额平均值的20%。可用试错法来确定经济批量,如图所示。如果此物品的年度使用量值¥1000,订货成本=¥10年使用金额=¥1,000库存持有成本=20%───────────────────────────────────订货量平均库存持有成本年订货次数订货成本总成本───────────────────────────────────¥5025¥520¥200¥205100501010100110238第238页共238页n200100205507025012525440655002505022070───────────────────────────────────试错计算法每次订货量为¥50,则平均批量库存将为¥25;年持有成本将为¥25的20%即¥5;年订货次数为20,每次¥10,年订货成本为¥200;总成本将为¥205,等于¥200订货成本与¥5持有成本之和。订货量加大时,平均库存随之增大,其结果是库存持有成本增大。订货量较大时,年订货次数减少,使订货成本下降。注意最右一列其标题是“总成本”。可以看出总成本最低是在订货量为¥250元之时。这就是能使订货成本与持有成本“相平衡”的订货量;它是该物品的EOQ。随着订货量增大,持有成本上升而订货成本下降。上面的曲线是总成本曲线,随着订货量的增大它在订货量为¥250时降到最低点;再增大订货量时总成本反而上升,然而要注意这增量是相对地小的。订货量大于EOQ时,其惩罚要远小于订货量小于EOQ的时候。然而要记住,这里只考虑了订货成本与持有成本。在库存控制中这是一个有用的概念,它比凭直觉的“猜测”能够导至可观的节约。订货量为¥250时的总成本比订货量¥50时总成本的一半还要小。无精确成本时的EOQ在前述例子中,假定订货成本与持有成本的精确数值是已知的。每一个EOQ公式都是这样假设的。实际应用时,这些成本是难以准确地确定的(理由见本章后面)实际工作者不应由于缺乏精确成本数据而泄气以致不去通过使用EOQ寻找可能的节约。无论如何,由于下述两个原因,使用经济批量概念是可以给生产控制带来实际好处的。1、根据一贯而有序的方法所确定的订货量比凭经验或猜测确定的订货量,其结果要好得多。几乎总是可以比直觉批量作出改进。2、总成本曲线(见图3-5)在EOQ的两边都有一相当宽的扁平区。这说明即便使用被认为远非完善的成本数据也可以找出相当经济的订货量。也说明可以修改从公式计算出来的订货量而不致于牺牲显著的节约(例如不妨将公式算出的EOQ=1910取整数成为更切合实际的2000)。平方根EOQ在工业界,采用试错法去求库存中成千种物品的经济批量是不切实际的。有若干公式可用来计算任一物品的EOQ。最早的形式是─────EOQ=√2AS/I其中A=年度使用量,用金额(元)表示S=生产调整或订货成本(元)I=库存持有成本,用每元平均库存的小数表示238第238页共238页n把数据代入此式,可算出──────────────EOQ=√2×1000×10/0.20───────=√100,000=¥316注意此公式给出了比试错法计算得更精确的答案。它是否更经济?(3-1)式是通过解出库存持有成本方程与订货成本方程去找出最低总成本从而推导出来的,详见附录Ⅱ。换句话说,此公式找出了总成本曲线的最低点,它比选出的值稍有不同。EOQ公式(3-1)包括两个成本因素:生产调整或订货成本S与库存持有成本I。对一个物品系列,通常库存持有成本假设对所有物品都相同,而生产调整或订货成本对该组物品往往实际上是相同的。如果上述成立,公式(3-1)可写成:──────EOQ=√2S/I×√A=K×√A其中────K=√2S/I公式指出一个非常有用的关系:最经济的批量是年使用量金额的平方根的函数。现在可以用公式计算出5种物品的经济批量,所示。─计算所得物品年使用金额√A目前年订货目前订货量年订货次数订货量A次数N───────────────────────────────────1¥10,000¥1004¥2,5007.6¥1,31026,4008041,6006.21,05032,5005046253.865544002041001.52625144124360.9157───────────────────────────────────26220¥4,86120.0¥3,434平均批量库存¥2,430¥1,717给定总订货次数条件下的最低库存计算中要用到的20次订货的K值可从公式(3-3)导出的另一关系式求得,即──∑√A262K=──────=────=13.1(3-4)∑N20─在此公式中,所有物品的年使用量平方根之和(∑√A)除以目前这些物品每年订货的总次数(∑N)就得到K值。已知K值,则使用公式(3-2)立即可以算出每一物品的EOQ,最右一列所示。当238第238页共238页n每年共发出20份订单时,¥1,717这个平均批量库存就是这组物品的最低总批量库存。计算此值无需知道订货成本与库存持有成本的具体值。对于实际工作者而言,每年7.6次订货这个概念是令人恼火的,因为0.6次生产调整是无实际意义的。然而,订货量为¥1310───它很可能将四舍五入为¥1300───对于物品1是有效的。在实际工厂里,它将成为某些年份订7次,其它年份订8次。虽然分数的生产调整不实际,但在作批量计算中是方便的,因为如此便可始终使用1年为期间以便比较各项成本。这种方法也可用来计算给定平均批量库存条件下的最少总订货次数,计算方法是使用公式:∑Q4861K=──────=─────=18.55──262∑√A其中,∑Q是目前各物品订货量之和。─物品年使用金额√A目前年订货目前订货量计算所得A次数Q年订货次数订货量───────────────────────────────────1¥10,0001004¥2,5005.4¥1,85526,4008041,6004.41,48432,5005046252.792844002041001.13715144124360.7223───────────────────────────────────26220¥4,86114.3¥4,861平均批量库存¥2,430¥2,430库存的最少订货次数再次使用公式,可算出每种物品的新的批量而无需知道订货成本与库存持有成本的具体值。对本例中这一系列物品,若给定的平均批量库存为¥2430,可算出最低订货次数为每年14.3次。计算K值的公式首先是由W.EventWelch提出的(9),这是尝试计算总量批量库存的第一次。这一EOQ计算方法有5个显著优点:1、对于生产调整(或订货)成本与库存持有成本都差不多相同的一个物品系列,它提供一种简化得多的EOQ计算方法。首先一次性地计算出所有这些物品适用的K值,然后分别乘以每一物品年使用金额的平方根,就可算出其EOQ。例见下一节。2、如果当前的组织其订单处理能力有限,则此法可用来计算受此约束的物品系列的最小总批量库存,3、如果库存量不能被增大到EOQ所要求的程度,则此法可用来确定受此条件约束时238第238页共238页n的批量使得总的订货次数为最少也就是订货成本最小,4、此法说明把EOQ概念应用到过去靠直觉手段来确定订货量的场合,可以得到若干立竿见影的好处。如前所述,保持订货成本不变时可使库存降低,或保持库存不变时可使订货成本降低。5、此计算方法说明一个非常重要的问题:当物品成组研究时,EOQ的应用要有效得多。人们往往忽视了这一点。虽然应用Welch法时不需知道订货成本与库存持有成本的具体值,但必须作出基本假设,即他们对系列中每一物品都是相同的。此外,当考虑实际成本时,计算结果未必就是最经济的,如果能获得代表性的成本数据,可能作出更进一步的改进。在实际应用中,其它制约条件可能使得EOQ的全部好处实际上不能立即得到。这些制约条件有:缺乏可用于库存投资的资金,可用来存贮库存的空间有限,有技术的生产调整人员太少,可用于生产调整的机器能力有限。在诸如此类条件下如何能获得EOQ概念的充分发挥,有一种叫做(批量库存管理内插技法)LIMIT的技法可用。它使我们能够研究在这类约束条件下可以平衡订货成本与库存持有成本的各种备选方案。EOQ公式中的成本毫无疑问,应用EOQ概念时最难办的问题是公式中假设实际的付现库存费用与持有的库存量之间存在着正比关系,并且实际的总订货费用与发生订单数之间也存在着正比关系。而实际上,减少采购订单的数目不见得就会使订货成本成正比地下降。真相是成本与订货量之间的关系并非正比而是阶跃式的。这些阶梯由总量效应控制───诸如要发出的订单的总数以及所需的总的存贮空间───而不是由个别物品的批量来控制的。因此有必要研究整个库存。在II中所给出的库存决策中用来确定成本的两条法则特别适用于经济批量式中使用的成本:1、成本应该是真正取决于所选订货量的那些付现成本。2、成本应该是真正要受订货量大小影响的那些成本。不幸的是,大多数公司会计记录中的成本难得可以直接用于经济批量的计算。EOQ公式中的单价就是这类问题的适例。在许多公司里,一物品的单价往往就是指其“标准成本”,它包括劳务、物料与一切制造作业的间接管理费,其中包括一些用于生产调整的折让。在EOQ公式中确定使用什么单价有两个明显的选择:1、使用标准成本2、只使用标准成本中的劳务与物料部份加上某些随批量而变化的间接费用。如果使用全额标准成本,将违反前述的关于成本的两条法则(因为标准成本的间接部份并不取决于,因而很少受批量改变的影响)。例如,批量库存有所增加时,对大多数间接因素而言,诸如工厂文书性开支、监工开支、设备折旧、检查等等,并不真正要求付现成本有多大增加。倘若用标准成本来推测增加库存将支出的金额,必将失之过大,因为按比例增加的开支将是劳务与物料而非间接费。而且标准成本中通常包括生产调整费用,它在公式中已单独列为一个成本要素,不应再包括在所使用的单价之内。另一方面,会计记录将按标准成本中规定的间接费率来收取库存的间接费。在公式中使用只包括劳务、物料与间接成本可变部份的单价将使计算出的EOQ总库存金额与会计数字不相符合。例如,根据EOQ公式中使用的成本予测出库存将增加¥100,000,这一结果可能引起有关管理人员真正的惊奇,因为会计记录当然将按包括间接费用在内的全额标238第238页共238页n准成本来计算库存金额,该帐面数字可能指出库存将增加¥150,000而不是前面所予测的¥100,000。使用成本时另一常遇问题发生在小批量物品上。当运行具有高生产调整成本的小批量物品的一次大量供应时,它是按标准成本登入库存金额记录中的。如果在同一次机器调整上使生产量加倍,则遭受报废风险的库存值将无疑要增大,但通常其增量并没有会计记录所指示的那么多。在同一次生产调整上再运行一次额外的供应实际上将只会使物料、劳务与一部份间接费按比例增加。有时,在某些半自动设备上,即使劳务成本也不会按比例增加。然而在库存记录上却按全额标准成本记帐──最后也是按此冲帐。如何处理这一两难问题?只有采用讲两种成本语言的办法。一种是真正的付现成本,它真正地影响着决策───用于计算。同时公司的管理者必须意识到库存中一个给定的变化将会对使用另一种语言的会计记录产生什么影响,因为绩效通常是根据这些记录来评价的。在许多公司里,作业人员与会计人员正试图设计出互相满意的成本核算技法。在此期间,作出作业决策的人员必须去做下列:1、了解公司的成本核算制并同公司财务人员密切合作,使得成本被明智地用于作出决策并向管理者提出备选方案。2、在大规模地使用EOQ之前,必先做试点的应用,并根据样本的结果予测EOQ应用对总库存的影响。平方根EOQ公式的变体捷径:上一节讲过对于成组物品当组内每一物品的生产调整或订货成本与库存持有成本均相同时,可用公式(3-2)中的K来简化EOQ的计算。使用公────式(3-3),K=√2S/I立即可算出K值。然后用公式(3-2),EO─Q=K×√A就可算出每一物品的EOQ。例如:────────────────────────────────物品1物品2物品3────────────────────────────────年使用量A¥10,000¥20,000¥30,000订货成本S555库存持有成本I0.20.20.2────────────────────────────────据此可算出K与EOQ───────────K=√2S/I=√2×5/0.2=7.07──EOQ=K×√A=7.07×√A─────对物品1,EOQ=7.07×√10000=¥707─────对物品2,EOQ=7.07×√20000=¥1000─────238第238页共238页n对物品3,EOQ=7.07×√30000=¥1225这种快速算法可大大加快EOQ的计算。当EOQ用件数表示时,可用下式────|2USEOQ=|────(3-6)√IC其中U=年使用量(件)S=订货或生产调整成本(元)I=库存持有成本(小数)C=单价(元/件)非即时收货有时整个批量并非即时收入存货。制造速率可能使得整个批量要化若干天甚至若干星期才能完成并交到存货。当生产正在进行时,有部份产品送到存货但在此期间也有往外的提货发生。其结果平均批量库存将不等于批量的一半。这种情形叫非即时收货,可用基本EOQ公式的如下修正形式:────────|2ASEOQ=|────────(3-7)√I(1-s/p)其中A=年使用量金额(元)S=生产调整或订货成本(元)I=库存持有成本(小数)s=使用率,其单位同生产率p=生产率,其单位同使用率注意用此公式计算出的EOQ将大于从假设收货是即时的(3-1)式计算出的EOQ。就是说,非即时收货时,制造批量要加大些,但平均批量库存并不加大,因为当批的余量还在生产时,同时有物料要被提走。即时收货时,库存一下子升高到顶点,然后逐渐使用掉,如图中虚线构成的直角三角形所示。非即时收货时,直到全部收完一批订货也达不到原来的最高点,锯齿形曲线中的三角形不再是直角三角形。主调整与次调整当以一确定的顺序运行成组的物品为最经济时,主次生产调整是在EOQ的工业应用中常遇的一种情形。例如在自动机床上生产物品时,依次地运行若干相似物品往往是经济的,因为在作好基础的生产调整之后,按照一定顺序每更换一种产品只需作一些次要的调整即可。在轧制薄板时也往往有这种情形。在造纸、化工涂料、化妆品与其它类似的过程工业中,清洗设备是耗时又费钱的,往往先做浅色的,然后依次做越来越深一些的颜色,在最深色处理完毕后再把整条加工线关车、清洗、重新转换。238第238页共238页nEOQ的基本方法仍适用这些情况,但需对数据作些特殊处理。图3-9所示为一次主生产调整可用于五种物品的一例。此例中,设库存持有成本为库存金物品年使用量金额A生产调整成本S─────────────────────────────1¥2,000¥2.0024,0003.0038003.00410,0002.0059002.00─────────────────¥12.00次调整总额¥50.00主调整总额系列总计¥17,700¥62.00图3-9主调整与次调整额的20%,而每种物品的调整成本如图中所列。除了每一物品的调整成本S之外,还有一笔主调整成本¥50,因此总调整成本为¥62,可用稍加修改的标准EOQ公式(3-8)来处理此问题─────────EOQ=√2×∑A×∑S/I(3-8)其中∑A=所有物品年使用量的总和∑S=所有物品调整费的总和其它因素同公式(3-1)。本例中───────────────EOQ=√2×17,700×62/0.2=¥3300即每作一次生产调整后,应依次加工总值为¥3300的这五种物品。可用(3-1)式算出每一物品的相应批量,但这并无实用价值。主要目的应是使每种物品的库存所负担的使用期相等,使得再次做主调整时,所有物品都需投入新的一批。倘若各物品的库存相互之间平衡得很差以致其中的一种用完得比其余的要快许多,就会使人感到很不方便。计算所得的各物品的EOQ是随其使用量的平方根而变的,常用的物品将比慢移物品用完得快。恰当的解法是使每一物品的可供应天数相等,这叫做等耗尽时间法。它是假定按每一物品的平均使用量可以供应相等的天数。更加精细的计算要把可能的误差都估计进去以加大使所有物品同时用完的机会。物品现有库存日使用率(每年以250天计)───────────────────────────1¥336¥8.00232016.0031003.20238第238页共238页n460040.005973.60───────────────────────────总计¥1,453¥70.80图3-10系列物品的现有库存图3-10所示为每种物品的现有库存与平均日使用量,它等于年使用量除以全年的工作日数。计算步骤是首先计算一轮新的运行使库存骤增后的总库存量。由于该系列物品的批量是¥3300,所以此时的总库存量将为¥3300+¥1453=¥4753。倘若所有物品的库存完全平衡,将可供应¥4753/¥70.80=67天。就是说每一物品的批量应该使它的现有库存在一轮运行之后增加到67天的供应量。如图3-11所示,每一物品67天的供应量减去现有库存,就得到批生产量。物品67天的供应量现有库存批生产量─────────────────────────────1¥536¥336¥20021,072320752321410011442,6906002,090524197144──────────────────────────────总计¥4,753¥1,453¥3,300图3-11系列物品的批量──即时收货此例中,用的是基本EOQ公式(3-8)。当这样的成组物品被运行时,该生产运行可能需要相当长的一段时间。果真如此,则应用非即时收货公式(3-7)将更为恰当,如图3-12所示。计算结果是当这组物品被运行时,此成组物品的物品AS日使用率s日生产率p────────────────────────────────1¥2,000¥2.00¥8.00¥6024,0003.0016.008038003.003.2075410,0002.0040.007059002.003.6069主调整50.00────────────────────────────────总计¥17,700¥62.00¥70.80¥354图3-12系列物品的批量──非即时收货238第238页共238页n─────────EOQ=√2×A×s/I(1-S/p)───────────────=√2×17,700×62/0.2(1-70.8/354)=¥3700批量应等于¥3700,它比即时收货时的批量¥3300要大些。其中每一物品的批量应使所有物品的库存具有相等的可供应天数。注意,哪个物品先做,并无什么要求。如果没有类似颜色由浅到深这样的重要考虑,则应该先做最有可能被用完以致引起缺货的物品。数量折扣采购物料时,供应商往往给购买较大批量的买主以一定的优惠,即可以提供折扣。在下述例中:年使用量=¥10,000订货成本=¥5.00库存持有成本=20%使用公式(3-1),可知EOQ=¥707。如果供应商对¥2000以上的批量可提供1%的折扣,则可用列表比较的方法来确定全年的供应总成本,如图3─13所示。左边的数字表明对于计算所得的EOQ,年供应总成本是¥141.10EOQ(无折扣)大批量(有折扣)────────────────────────────────────¥707批量(¥2,000-1%=)¥1,980¥353平均批量库存990¥70.60库存持有成本(20%)¥19814.1每年订货次数5¥70.50订货成本(每次¥5)+25────折扣的节约(1%×10,000=)-100───¥141.10全年供应总成本¥123────────────────────────────────────图3-13有采购折扣时的EOQ有折扣时,批量为¥2,000(1-1%)=¥1,980,平均批量库存为¥990,库存持有成本为¥198,加上全年订货5次的订货成本为¥25,以上小计达¥223。但1%的折扣使单价下降,全年可节支¥100,故实际上全年供应总成本是¥123。说明接收折扣,加大采购批量是有利的。这一点正是标准EOQ公式中未加考虑的。折扣问题的特征如下:1、为了获取折扣,必须以较大批量采购;其结果是库存与库存持有成本将会上升。238第238页共238页n2、以较大批量订货可减少订货次数使总的订货成本下降,这通常在总数上不是一个大的因素(注意较大的批量也减少缺货从而减少了安全存货的需要)。3、折扣降低了年度总使用量的单价,这通常是相当大的一笔节约。为了简化折扣问题的计算,计算有折扣时较大批量的库存投资这一步时往往可以忽略折扣的价值,即不妨以例中的¥2000代替¥1980。这样计算实际上不会显著地影响计算的结果。最小总成本法平方根EOQ公式根据成本与每一特定公式中所选定的其它因素为每种物品计算一个批量。然而它并未考虑这些物品在物料清单中的关系。一个装配件A(EOQ=200)可能是由组件B(EOQ=450)、C(EOQ=675)与D(EOQ=940)装配而成的。显然一个物品的EOQ同它在父物品中的使用方法之间应该有一种平衡关系;否则就会制造出并在库存中持有一些永远也用不上的组件(叫做剩余物)。平方根公式假设均匀的使用;实际上在成批制造中所有组件的使用都是不均匀的,它们是“成块地”发生的,等于其父件的批量,有时在同一时间期内同时供若干种父件使用。物品成本=¥4.00持有成本=30%/年=0.6%/周───────────────────────────────────未来净第几周累计多余持有持有成本(¥)订货总成本需求需要批量库存周数本批累计成本(¥)(¥)───────────────────────────────────93493000030.0030.00233532623315.595.5930.0035.59194652019429.3114.9030.0044.902197739*219315.7730.6730.0060.678784489───────────────────────────────────*推荐的批量───────────────────────────────────图3-14最小总成本法计算机化的MRP(见第6章)为每一物品推算未来的分时段的需求使它们可使用于批量决策之中以减少或取消剩余物以及假设均匀需求的必要性。最小总成本法就是这样一种技法。其基本假设同平方根公式是一样的:当持有成本等于订货成本时总成本将为最小。但它不假设均匀地使用,而使用未来的需求量,如图3-14所示。此法的机制包含一系列的反复计算。如果批量设定为93,等于第4周的需要量,故没有多余库存(它将在第4周内使用掉),并需要作一次生产调整。要满足未来的需求将需作另一次生产调整。如果第4第5两周的需求量一道做,批量将为326;因而将有233件要在库238第238页共238页n存中持有一个星期,但其持有成本(¥5.59)比再作一次生产调整要少得多。因此,这是一个较好的决策。逐次增加一周的需求量,批量与累计持有成本也将随之增大。当批量增大到739件时,累计持有成本为¥30.67,它非常接近于生产调整成本(¥30)。再进一步增大批量将使累计持有成本超过生产调整成本,不如再作一次生产调整去满足第8周及以后的需求。最小总成本指一个长时间期──譬如说几周──而不是指任何一个期间的总成本。本例中推荐的批量是739件。零件─期间平衡法这就是最小总成本法的别名与另一套计算方法,方法上基本是一样的。这一变体是为IBM的软件包开发的,它更加便于编程序。零件──期间这一名词指1件物品持有1个期间,通常1个期间就是1周。如果将1件物品持有20周将相当于将20件物品持有1周。图3-15说明其计算机制,所用数据与图3-14中相同。订货成本¥30经济零件──期间=─────────────=──────=1,250单位零件──期间的持有成本¥4×0.006───────────────────────────────────未来净需求第几周需要累计批量多余库存持有周数零件──期间数本批累计──────────────────────────────────93493000023353262331233233194652019423886212197739*21936571,278───────────────────────────────────*推荐的批量───────────────────────────────────图3-15零件──期间平衡法第一步是使用图3-15顶上的公式去算出经济零件──期间。然后逐步加大批量去满足相继而来的更多期间的需要并确定累计零件──期间,如此反复地计算如同在最小总成本法中一样。批量达到739件时,累计零件──期间为1,278,它就接近于前面计算出的经济零件──期间1,250,于是739件就是此法要推荐的订货量。注意最小总成本法与零件──期间平衡法给出的答案是一样的。瞻前/顾后为了精益求精,IBM给零件──期间平衡法增添了两个特色──叫做瞻前与238第238页共238页n───────────────────────────────────未来净需求第几周需要累计批量多余库存持有周数零件──期间数本批累计───────────────────────────────────219773921936571,278第1方案87887000044895354481448第2方案878826*8743484489448000───────────────────────────────────*推荐的批量大小───────────────────────────────────图3-16瞻前特色顾后。在用零件──期间平衡法得出一推荐的批量,譬如说在图3-15的例中得出739件之后,程序进一步调查另一方案:看看下一期间(例中的第8周)的需求应不应被包括进刚刚算得的批量之中。注意第9周的大需求量448。第1方案不包括第8周,它将从第8周的需求87开始计算下一批,随后加上第9周的需求448,使得累计的零件──期间数达到448,如图3-16所示。第2方案则把第8周较小的需求87包括在本批之中,使原来推荐的739加上87变成826。然后,下一批将从第9周的448开始。这两个方案比较之下,程序将选用第2方案,因为它只涉及348个零件──期间,而第1方案要有448个零件──期间。特别注意这样计算所得的批量有了显著的变化;想想它对组件可得性与工作中心的负荷可能产生的影响。顾后特色是又一个改善订货的经济性的企图,如图3-17所示。在第1方案──────────────────────────────────未来净需求第几周需要累计批量多余库存持有周数零件──期间数本批累计──────────────────────────────────第1方案44894480000153106011531153153761167776215230522612903226367898387139908743481,331175149815第2方案44894480000153106011531153153238第238页共238页n761167776215230522612226000087133138718787──────────────────────────────────图3-17顾后特色中,按照零件──期间平衡法的正常顺序,该技法确定出从第9周到第13周的最好的批量将是990件。然后首先向前考查第14、15周,结果未发现有显著好处。于是,它向后查看第9周到第13周的需求。由于第12周的需求远大于第13周,图3-17中的第2方案显示出首先以677件做一批,再从第12周开始做下一批226件将比第1方案要好得多。它涉及的零件──期间比第1方案要少得多。所以推荐的批量将是677而不是990。注意瞻前与顾后二者开发出的订货量,变动非常大。这里是又一例子说明从用户观点看,一个好主意如何会被带到一种可笑的极端。最小单位成本法还有一个例子是最小单位成本法,它为反复计算的每一步计算一个单位成本。图3-18使用最小总成本法中讨论过的例子中同样的数据,第4列的总成本在反┏━━━━━━━━━┳━━━━┳━━━┳━━━━┳━━━━┓┃持有成本┃订货┃总┃累计┃单位┃┣━━━━┳━━━━┫┃┃┃┃┃本批┃累计┃成本(¥)┃成本┃批量┃成本┃┣━━━━╋━━━━╋━━━━╋━━━╋━━━━╋━━━━┫┃0┃0┃30.00┃30.00┃93┃0.323┃┣━━━━╋━━━━╋━━━━╋━━━╋━━━━╋━━━━┫┃5.59┃5.59┃30.00┃35.59┃326┃0.109┃┣━━━━╋━━━━╋━━━━╋━━━╋━━━━╋━━━━┫┃9.31┃14.90┃30.00┃44.90┃520┃0.086┃┣━━━━╋━━━━╋━━━━╋━━━╋━━━━╋━━━━┫┃15.77┃30.67┃30.00┃60.67┃739┃0.082┃┣━━━━╋━━━━╋━━━━╋━━━╋━━━━╋━━━━┫┃8.26┃38.93┃30.00┃68.93┃826┃0.084┃┗━━━━┻━━━━┻━━━━┻━━━┻━━━━┻━━━━┛图3-18最小单位成本法复计算的每一步中都除以累计批量从而得出单位成本。这名字不大好。通常所说单位成本是该物品每单位的物料、劳务与间接费用的总和;但在这里是指每单位物品的持有成本加上订货成本。在图3-18的例中,此技法的结论同最小总成本法与零件──期间平衡法所238第238页共238页n推荐的一样,都是739件。IBM与其它公司所做的若干次大规模仿真表明:最小单位成本法有时会推荐出不同的批量,而且──更为重要的是──不如其它方法经济的结果。1968年,有人在APICS季刊《Production&InventoryManagement》上著文论“动态订货论”,文中比较了最小单位成本法与最小总成本法并作出结论说,最小单位成本法的方法是不稳定的,用一组数据它会开发出较低的生产调整成本与较高的库存成本,而对另一组数据它会开发出较高的生产调整成本与较低的库存成本来,但不能保证使总成本最低。所以没有理由去使用最小单位成本法;为什么要多作些计算而去得到更差的结果呢?期间订货量(POQ)对于分时段的数据这是最简单的一种技法,它把订货量表达为等于在若干个时间期间内(譬如六个星期内)的未来净需求的总量。根据订货成本与库存持有成本相平衡的原理,所用的时间期间应使期间订货量是“经济的”。最简单的方法是用平方根公式去算出EOQ,然后根据平均使用率把它转换成等效的供应时间期间,叫做期间订货量(PeriodOrderQuantity)POQ。例如:EOQPOQ=─────────平均周使用量若年使用量=15,600件该物品的EOQ=2,100件2,100则POQ=────────────=7周(15,600÷50)注意用的是近似计算,一年除50周得出平均周使用量,求POQ时用四舍五入得出最接近的整数的周数。这种计算无必要求其精确。现有库存=0安全存货=0提前期=2周──────────────────────────────────第几周1234567891011──────────────────────────────────毛需求510115320400270190605360180410335──────────────────────────────────未了结订货925──────────────────────────────────净需求20400270190605360180410335──────────────────────────────────应交订货20251960──────────────────────────────────订货开始20251960──────────────────────────────────238第238页共238页n图3-19期间订货量图3-19所示为MRP程序中POQ的计算。图中对此组件的毛需求来自制造其父物品的已计划订单。本周到期的未了结订货为925(可能是一部份已完成订货的余额),它可以负担下2周的全部需求以及第3周的部份需求。根据刚刚算出的POQ为7周,故此技法将求出7周的净需求为(510+115+320-925+400+270+190+605+360+180)=2025。这一期间订货量应在第3周交货,其订单应提前2周在本周发出。下一个期间订单应在第10周交货,数量要小些(1960),但该订单要在第8周发出。此技法有一些优点。它以一定间隔定期地订货,有助于平滑对起始工作中心的输入。它满足推测的需求,不应剩下用不着的批量库存的剩余物。在图3-19的例中,倘若用了2,100这个EOQ,则第9周将产生余额75,这一数量不足以负担第10周的需求,因而仍必须另外订货。当然,需求中的变化将改变这种配合;如在第3周,未了结订货比满足该周需求所需的数量就缺了20件。另一种可能性当然可能是因为订货中有20件报废了。批对批理想批量的一个定义是它刚好等于今天或本周实际需要的数量。这种使订货量符合计划期间(通常为1周)的需求量的技法叫做批对批。这在MRP中很容易安排。这种安排使持有的库存很小,进入与通过各工作中心的工作流比较平滑并且更加可靠。物料搬运成本可能大。除非生产调整时间能被缩短,否则生产调整成本也将是高的。前面讲过的原理7强调短生产调整时间的必要性。实际的考虑还有一些确定EOQ的其它技法,其中包括Wagner──Whitin算法。由于它们很少实际应用,本书不再赘述。在数学家的语言中,这些形形色色的EOQ公式都是非常简单的模型。重要的是懂得EOQ的基本概念,而且能够确信所用的模型对所研究的特殊情况是最有效的。EOQ公式中包含许多假设,实际工作者要恰当地来应用公式就必须懂得这些假设的意义。譬如说,这些公式假设,库存的持有量是发出这些订单的结果而且该库存将以相当均匀的使用率被提取。他们进一步假设在最经济批量的计算中,公式中所包括的因素就是唯一的起显著作用的因素,并且同订货与持有库存有关的成本均匀连续地随订货批量的大小而变。其它成本与有关因素在第二册讨论。本节的其余部份将讨论在应用EOQ公式时必须运用常识判断的几种实际情况。许多产品具有季节性的销售模式。常常可以看到大多数预期的产品需求在高峰季节到来之前老早就已生产出来,以保持全年的生产可以相当地平稳。在建立库存的这一期间,增加的那部份库存叫做预期库存,它不是批量库存,所以常规的EOQ模型是不适用的。这时公司不是要平衡订货成本与库存,而是试图以最经济的方式把工时储备在库存里。如果该季节性高峰非常短促,──例如圣诞节──库存经理唯一可凭借的实际信息就是销售预测,因为关于实际销售情况的信息返回时他已来不及作出反应了。因此,许多季节性产品全年就生产一批。下一批要生产什么的238第238页共238页n问题是通过比较各产品的劳务成本与物料成本,然后排序,使得劳务成本与物料成本之比最高的产品,能够在销售季节到来之前最早地生产出来,因而它们要在库存中持有的时间也最长。对于季节性需求不太明显的大类产品,预期库存只存在一年中很短一段期间,将可以应用经济批量的概念──但在建立库存的期间,有些批可以合并起来以减少生产调整。另一种常遇的情况是为装配件及其组件确定批量的问题。还是以极端情况为例最容易说明。对于由并不使用于其它装配件的专用组件构成的装配件,计算批量时应考虑组件与装配件的所有生产调整成本,而且大多数组件的制造批量应该同装配件一样。有些生产调整成本特别高的组件可以装配件批量的倍数来制造;简单地计算一下由此产生的库存与所节省的生产调整的对比,就可看出决策的经济与否。在大多数EOQ公式中没有考虑实际上对于不同的物品其占用空间的成本是可能大不相同的。装运用的纸板箱通常单价低,有非常吸引人的折扣并且要用大量的存储空间。另一方面,电子组件单价很高,而且用不着多大的存储空间。对这两种物品采用同一持有成本(假设存储成本包含在持有成本之中)将使后者支付的存储费多于前者。特别是对笨大的物品,估计一下EOQ计算结果需多大总空间是重要的;然后就可对相似的成组物品计算存储成本以得到实用的结果。记录上指示的订货量与工厂里实际使用的订货量往往是很不相同的。例如,在一个时常发生组件供应不足的装配车间里,可以发放出数量为2000到3000件的装配工作令,然而装配线上由于缺乏足够的组件供应,从来也做不到500或600件以上。将新的批量同现行订货量作任何比较以确定改变的效果与节约时,应根据在车间里实际上正在加工着的批量,而不是根据物料控制部门规定的数量。许多物品是通过一系列按顺序的作业加工的。这时的订货成本必须包括所有这些作业的生产调整成本的总和。如果其中有一个上游作业其生产调整占了总调整成本中极大的一部份,则在此高调整成本作业之后建立一种叫做持有点的库存然后再去以较小批量做进一步的加工可能是经济的。决定设置这个持有点应根据:是把该批加工到底从而生成已完工零件的库存;还是把该库存作为半成零件持有,然后再以较便宜的形式返回加工顺序。对这类计算要注意下列各点:1、选择究竟以半成品方式持有一物品的库存还是把它加工成完工零件时,在计算中应该只考虑实际受影响的那部份单位成本。把一个物品作为完工零件而非半成状态持有时,库存投资中实际上只增加了半成点以后各作业的劳务与物料成本(当然还有很少或可以不计的管理费),虽然会计记录难得承认这一点。2、补充已完工物品库存所需提前时间将被压缩而且在这个更加昂贵的阶段往往可以少持有一些库存。特别是当若干种完工物品可由一种半成品制成时,它的利益更大。这发生在,譬如说,当该半成品尚未涂色而可以涂成四种不同颜色之一去做成四种不同完工物品时。然而要注意,由于加工的批量更大,把该库存移动进出该持有点的时间也将增加,所以总的提前时间也可能增大。3、一般地说,不应仅仅根据生产调整中的差异就去建立半成品持有点。半成品库存极难控制而且经过主要工序来加工极大的批量,往往使得为满足变化着的成品需求而作的组合控制十分困难。特别当生意正在增长而成品的需求不能完全靠持有点来满足之时,事情就是这样。从该持有点增长着的提货将产生大量补货订单,它们很可能──因为对这些组件,批量通常是大的──在主要工序处造成瓶颈,很快造成严重的缺货,因为不可能使每样东西都通过一些。4、持有点库存将要求更大的控制努力,更多的记录保管工作与更多文书工作。238第238页共238页n考虑建立持有点时对其优缺点应认识清楚。5、最好的周到解是去压缩生产调整时间。原理8.EOQ计算只是起点;修改它们以获取实际的结果。核查计算所得的EOQ是否合理的最好方法之一是请熟悉所涉及的实际情况的人们去作详细的评审。EOQ计算出来之后,熟悉制造设备的某人应同将应用该批量的工区的负责主管人员或同工作在该机器上的生产调整工一道审查它们,并把计算所得的EOQ四舍五入成为可使用的数字。由于EOQ曲线的扁平性,合理的四舍五入不会使EOQ的经济性受到多大损害。而这种评审将确保不致忽视应用该批量中的实际限制。有经验的实际工作者将核对每一EOQ的应用以确信该模型是有效的。彻底了解EOQ公式及其应用时,该技法可被用来收取巨大效益。但若此技法凭死记硬背盲目应用,其结果可能使公司实际上增加了成本。修改EOQ计算结果有许多理由。报废损失可通过把平均期望损失的百分数打进批量而获得补偿。可以在计算所得的EOQ下面设一条最小数量的底线以反映一供应商的最低采购量或每单位(块、张或筐)原料的最低制造批量。计算笨大物品时,由于存在空间限制可设置一个最大量作为上限。计算所得的EOQ还要调整到包装批(如打、货盘或圆桶等等)、搬运时的容器批或制造时的原料单位(成卷、成捆、成桶等等)的倍数。EOQ的计算可由于能产生确实的利益而是值得花费时间的,但也可以成为实际问题的根源。数学计算发出高度精确的辉光,但不要把它同准确混淆起来。不同的技法会给出不同的答案而试图花费时间去寻找“最好的”答案不过是一种琐事锻炼,不如把这份精力用在其它地方。频繁地重新计算EOQ会在计划系统中引起讨厌的精神紧张,第二册将充分讨论这个问题。这些公式一次解决一个物品;它对能力、总投资与系列产品关系的影响通常远大于个别物品上的节约。这些影响见第8章《总量库存管理》与本书一、二册的附录Ⅱ。238第238页共238页n四.需求管理需求管理的范围在术语汇编中,需求管理这个现代术语适用于为一个制造设施作计划与处理对它的各种需求时所涉及的一切活动。这将包括来自下列各方面的需求:1、国内外的客户2、本公司的其它工厂3、在其它地方的分支仓库4、在客户处的寄销存货它将包括下列活动:1、这种需求的预测2、处理订单登录3、作出交货承诺4、同主计划接口需求将涉及各种物料,包括1、成品2、作为产品的组件3、修理件在最广的意义上,需求管理包括筹划仓库地址,从制造源到仓库的替代发运方法,仓库布局,物料搬运与作业。泛称为分配,这些题目超出了本书的范围。第五章包括分时段订货点法,附录Ⅶ包括用于订购补充物料的其它技法与在这种仓库中有效的库存管理的原则。第六章讨论在物料计划中把仓库的需求同其它类型的需求相混合的问题。订单登录活动主要同数据处理有关,本书不予讨论。本章的主要课题是预测来自客户的需求。预测的重要性制造计划与控制基本上关心的是未来的事。已经过去的事无法控制──必须从现状出发为未来作准备。为此,就有必要去猜测、假设或估计从现在开始将发生什么。其它一切条件都相同的情况下,一家公司要生存,至少要准备好自身能同竞争者一样快地去满足客户的要求。预测这个字就包括对这种未来的客户需求的估计。计划与预测是人们给工厂经营有关数据的推测所起的名字。由于一家公司中的一切计划活动都与满足客户的未来需求有关,组织的许多方面必须同销售预测打交道。图4-1所示为一家典型公司所做的各种预测的汇集与这些预测的用途。例如,住户组成数被市场营销部门用来确定总的潜在市场的成长。工厂经理与工厂的工程部门要知道5年的生产需求,因为购置土地的计划、以产量与技术的变化为基础的新生产过程的开发以及要增添的制造设施的采购都需要有长的提前时间。图4-1所示只是主要的需求;使用预测的途经还有许多。238第238页共238页n┏━━━━━━━━━━━━┳━━━━━━━━━━━━━━━━━┓┃预测┃需要者┃┣━━━━━━━━━━━━╋━━━━━━━━━━━━━━━━━┫┃1、住户组成数┃市场营销:确定总的潜在的市场成长┃┣━━━━━━━━━━━━╋━━━━━━━━━━━━━━━━━┫┃2、未来5年所需的总生产┃制造:工厂扩展规划┃┃量┃┃┣━━━━━━━━━━━━╋━━━━━━━━━━━━━━━━━┫┃3、未来2年所需的设备小┃制造:明年的资本预算┃┃时数(按类别)┃┃┣━━━━━━━━━━━━╋━━━━━━━━━━━━━━━━━┫┃4、明年按产品系列分组的┃销售:报价财务:开支预算┃┃个别产品的销售量┃制造:工人与机器能力┃┃┃物料控制:季节性库存需求与总括订单┃┣━━━━━━━━━━━━╋━━━━━━━━━━━━━━━━━┫┃5、个别产品下季度┃物料控制:工作中心能力,自制与采购┃┃销售量┃的组件┃┣━━━━━━━━━━━━╋━━━━━━━━━━━━━━━━━┫┃6、个别产品下周销售量┃物料控制:装配日程与调度优先级┃┗━━━━━━━━━━━━┻━━━━━━━━━━━━━━━━━┛图4-1各类预测及其用途物料控制部门,时常被称为计划部门,其责任是制订计划以满足制造产品的未来需要。需求预测在这一准备中是不可缺少的要素。物料控制人员需要这一预测来计划要买多少组件,买多少原料,用什么速率去做机加工或装配──最重要的是──什么时候去订货。对预测有互相矛盾的要求。例如,总经理关心发货量的预测,因为发货产生公司从客户收来的钱。他可能同市场营销经理意见相左,后者更加关心续入业务,因为这度量要求给予服务的客户对本公司的需求。实际上发货量代表被公司响应需求的能力修正过的续入业务。销售经理典型地感兴趣的是设定乐观的目标作为对销售人员的挑战,而总会计师宁可有一个较保守的预测以便估计利润。物料控制部门要求预测用制造部门能理解的语言来表达(例如,用通过相似制造设施的产品组)。而对市场营销人员有意义的产品组则是在相似销售渠道中销售的产品,它们不一定同制造中的产品组一样。在大多数公司里需要有多种预测。这些预测有多种分类方法,其中之一是按其所涉及的期间长短来区分:长期预测:用于工厂扩展与添置新机器、新设备,以便提前5年或更早地去计划资本投资。中期预测:用于长提前期物料的购买或作业率的计划,提前1至2年考虑季节性或周期性的产品。短期预测:用于为采购件或自制件确定恰当的订货量与订货时机的安排并计划恰当的制造能力,并考虑提前3至6个月平整工作负荷是否值得。近期预测:用于每周或每日的装配进度与成品库存的分配。长期预测涉及复杂的考虑,超过了本书的范围。它的视界从向前看2到5年甚238第238页共238页n至更多年。它需要具有对经济因素、竞争性与技术性影响与最高管理者制订的资本扩展计划的认识。这类预测的开发包括对市场战略、雇佣政策与政府规章的考虑。较大的企业对这种预测越来越重视,但中等与较小的公司大多忽视这种需要。然而,作出认真的努力去为任何一家公司指明航向都是有实际价值的。最大的好处可能是公司宪章的定义:它到底属于哪一种事业?许多行业,特别是铁路与钢铁业,如果他们曾经更加清楚地认定他们真正的事业是提供运输与基本材料的生产,而非限于运行铁路与钢厂,本来可以避免许多严重问题的。一般说来,较短期的预测要求更大的准确性。例如,能力的中期预测可能指示一个工作中心需要多少小时,当利用这些小时的时刻到来时,它们可能被用在原来作能力预测时根本没有考虑过的一件工作上(如果有许多物品要经该部门生产,总的预测小时数仍可能是相当准确的)。另一方面,本周的预测建立一份最终装配或一特定产品组合的包装日程。由于这些产品将确定可供发货的具体成品库存,重要的是这一预测要尽可能地准确。区分预测的另一种方法是按其所包含的物品类型,譬如个别产品,系列产品或小类产品。一家公司具体需要哪些预测取决于其制造周期的长度同它的客户允许的提前期之间的关系,如图4-2所示。倘若在公司确定需要什么物料、购得这些物┏━━━━┳━━━━┳━━━━━┳━━━━━━━┳━━━━━━━━━━┓┃采购物料┃制造组件┃装配产品┃发运┃行业┃┣━━━━╋━━━━╋━━━━━╋━━━━━━━╋━━━━━━━━━━┫┃←──╂──允许┃提前期──╂─────→┃重型资本货物、轮船、┃┃┃(不需产┃品预测)┃┃火车、导弹等等。┃┣━━━━╋━━━━╋━━━━━╋━━━━━━━╋━━━━━━━━━━┫┃┃←──允┃许提前期─╂─────→┃特殊订货、单件小批生┃┃┃(需作原┃料预测)┃┃产、精细化工。┃┣━━━━╋━━━━╋━━━━━╋━━━━━━━╋━━━━━━━━━━┫┃┃┃←──允许┃提前期───→┃机床、电子、定制的装┃┃┃┃(需作原料┃与组件预测)┃配产品、等等。┃┣━━━━╋━━━━╋━━━━━╋━━━━━━━╋━━━━━━━━━━┫┃┃┃┃←允许提前期→┃汽车可更换零件、消费┃┃┃┃┃(需作原料、组┃品、等等。┃┃┃┃┃件与产品预测)┃从存货发货。┃┗━━━━┻━━━━┻━━━━━┻━━━━━━━┻━━━━━━━━━━┛图4-2允许提前期与所需预测的关系料、加工它们并最终交运该产品期间客户将等待,则实际上不需作任何一种预测。当然,罕有任何行业的客户将等待他们的供应商去建造与扩展工厂或去获得要添置的机床或其它设备,所以所有公司都需做用于生产设施中资本投资的长期预测。市场营销人员喜欢说在公司拿到客户的订单之前,实际上什么也没发生。这听起来有道理,其实满不是这回事。应该说收到订单之前已经发生了许多事情。如果一家公司的竞争者们能够以比所要求的发货时间稍稍多一点的时间向客户提供产品,则该公司必须保有成品库存以便同任何其它人一样地去满足订货。这意味着公司将必须去预测原料的需求,并根据预测采购与制造零件并安排所需成品货物的生产日238第238页共238页n程。图4-2还指示某些典型行业的提前期的主要因素。毫无疑问,这幅图景现在已经有了很大变化;许多公司发现他们的竞争者以较短的提前期发运产品并不保有较高的库存投资。许多因素对一家公司的产品与服务发生影响,要识别所有这些因素并度量其影响或预测其效果是永远不可能的。然而,在预测中去识别广泛的主要影响并试图去预测它们可能引起的变化还是有帮助的。这些影响有外部的也有内部的。外部因素包括一般商业条件与国家的经济状态,它影响几乎每家公司的客户因而影响对其产品的需求。所有的长期预测──以及许多中期预测──必须包括对变化着的经济气候的影响的某些估计。竞争因素是另一个要考虑的外部力量。竞争间接地来自对客户的钱的其它需求,也直接地来自相近或相同的产品。没有哪家公司可以忽略去估计竞争者在做什么及其对本公司可能的影响。也必须考虑到市场的趋势,包括变化着的客户意向,增长着的需求,式样风尚等等是会影响一家公司的销售的。有时这些力量可以通过广告被影响到某种程度,但无论如何它们是最难于控制的。内部因素,诸如一家公司的广告计划、促销、销售努力、定价与提高质量,能对创造或扩大需求有主要的影响。若不把这些因素包括进去,没有一个预测会有效的。及时交货,较低的成本以及较短的制造周期是其它能对公司产品具有显著影响的内部作用。预测的演变早先,在大多数公司里是没有准备预测的正式手续的。有预测的话,也不是明确地委派给某人或某一部门的责任。预测难得被认为是一种真正的需要。预测的需要时常是不自觉地、直觉地由老板来满足的,他决定去买进更多物料因为他有信心,这些物料在将来可被加工然后卖出去;一名主管,他决定雇佣一名工人,因为他相信工作负荷将继续居高不下;或一名存货文书,他发出一份新的订单去补充存货室中缩小着的螺杆的供应。二次大战前若干年,许多公司开始认识到以正规方式准备预测的潜在利益。他们设置专门的小组来准备数据,提出要由组织里极其重要地有关的人来批准预测的手续并且往往把预测的分发限于给适合于接收这类机密信息的人员。在许多情况下,化了许多钱去开发使用统计技法、市场研究或其它复杂的预测方法。在这一期间,基本的假设看来是认为只要对预测投入足够的钱,努力与情报,预测问题是可以解决的。这一时期可名为预测的过分乐观时代。当完善的预测并非唾手可得时,不可避免的醒悟(幻想破灭)时期开始了。以预测为前提的计划控制系统把他们的失败归罪于未能得到一份好的预测。由于这种反应,被失败与这种方法高代价螫痛了的许多公司停止了对预测的有组织努力而返回到直觉的猜测。这一时期可称为后冲时代。大多数公司现在已从这一反应完全恢复了。对预测采取天真态度在工业界已经少见了;只有非常少数的公司仍然相信他们应当期望更加准确的预测,而且只要他们找到正确的技法就可能得到它们。大多数人认识到预测中的两个有区别的问题:做出更准确的预测与对不精确的预测做出更好的使用。原理9.预测是可作为工作出发点的一组数字,它不是工作的终点。任何预测,不管如何得出的,是为一个一体化正式系统开始其计划工作提供起始数据的。当根据更好的知识或新的见解而对于预测作出更改时,或当实际需求与238第238页共238页n预测不符时,可以更新计划以指出所需的具体的校正行动。预测的第二个问题,如何更好地使用预测,比努力去得到更准确的推测,能提供大得多的潜在利益。目前趋势是达到一种更为合理的观点,它承认预测必须做而且将被人们作出,因此,最好由最能干的人去做;它承认使用一个正式的预测作为一切其它预测的基础的价值,而不是让许多经营部门各自去猜测未来的事。预测的特征在讨论预测的技法之前,懂得预测的一般特征是重要的。最重要的特征可简述如下:1、预测将是错的2、预测附上对误差的估计是最有用的3、对于较大的物品组合,预测更准确些4、对于较短的时间,预测更准确些当前合理的方法承认预测总是有误差的,而且虽然有许多工具可以改善预测的艺术,应用这些工具需投入的金钱与努力迅速达到报酬递减点。超过了这一点,对预测误差采取灵活态度将比试图改善预测要有利得多。最好的办法是去开发一个正式的预测计划与一种发现与度量预测误差的体制,然后快速地反应去校正这些误差。本章将详述这种办法。可以使用根据以往的实际与预测数据的对比或根据有识人士的意见作出的误差估计去制订应急计划。这些办法将使为响应预测误差而采取的校正行动加速并更为有效。每一预测应包含一个对预测误差的估计──该预测可能错到什么程度的表达式。这一估计可用预测的百分数(正或负)或作为最大值与最小值之间的一个范围。如第5章所述,在建立订货点时,有必要知道在提前期间估计的平均使用量以及最大的预期使用量这二者。后者,当然,是提前期间该需求预测的准确度的一个函数。预测误差的估计提供设置确定何时要采取行动(诸如重新计算EOQ或改变某一部门的生产率)的决策规则的基础。当实际需求落在预测范围之外时,可能有非随机性的影响存在因而采取行动是必要的。虽然进入市场的新产品最难预测,但在新产品预测中使用预测误差的估计往往比其它情况更为有利。新产品可能同在大类产品中已相当稳定的东西相当地相似。这种情况下,由于销售部门有销售类似物品的一些经验,市场营销部门有过去预测类似产品的经验,预期的预测误差可能是低的。另一方面,对市场上全新的一个产品,由于公司没有经验,预测可能失误到300%之多。本书后面将详述在生产与库存控制中作出决策时预测误差的使用。一个基本的统计事实是即使总体作为整体具有非常稳定的特征,总体中每一个体的行为却是随机的。例如,要预测个别人的预期寿命是极为困难的,但保险公司能以高准确度预测大群个人的平均预期寿命。同理,虽然对个别物品的预测要受高度误差的支配,但对大系列制造产品作出相当高准确度的预测却是可能的。┏━━━━━━━━━━━━━━━━━━━━━━━━━━━━━┓┃第三季度┃┣━━━━━━━━━┳━━━━┳━━━━┳━━━━┳━━━━┫┃物品┃预测*┃实际┃差额┃差额%┃┣━━━━━━━━━╋━━━━╋━━━━╋━━━━╋━━━━┫238第238页共238页n┃#7147-灯┃47,600┃42,784┃-4816┃-10.1┃┣━━━━━━━━━╋━━━━╋━━━━╋━━━━╋━━━━┫┃#8014-钳子┃12,800┃9,125┃-3675┃-28.7┃┣━━━━━━━━━╋━━━━╋━━━━╋━━━━╋━━━━┫┃#8663-锉刀┃1,505┃1,157┃-348┃-23.1┃┣━━━━━━━━━╋━━━━╋━━━━╋━━━━╋━━━━┫┃#8726-纤维切断机┃22,500┃28,392┃+5892┃+26.1┃┣━━━━━━━━━╋━━━━╋━━━━╋━━━━╋━━━━┫┃#8933-螺刀┃10,100┃11,394┃+1834┃+18.1┃┣━━━━━━━━━╋━━━━╋━━━━╋━━━━╋━━━━┫┃#9250-剪切机┃17,450┃14,860┃-2590┃-14.8┃┣━━━━━━━━━╋━━━━╋━━━━╋━━━━╋━━━━┫┃#9261-剪刀┃28,500┃27,733┃-767┃-2.7┃┣━━━━━━━━━╋━━━━╋━━━━╋━━━━╋━━━━┫┃#9337-耙┃68,000┃68,105┃+105┃+0.2┃┣━━━━━━━━━╋━━━━╋━━━━╋━━━━╋━━━━┫┃#9604-锄┃27,200┃17,566┃-9644┃-35.4┃┣━━━━━━━━━╋━━━━╋━━━━╋━━━━╋━━━━┫┃#9638-铲┃3,320┃4,638┃+1318┃+39.8┃┣━━━━━━━━━┻━━━━┻━━━━┻━━━━┻━━━━┫┃物品的平均预测误差=19.9┃┣━━━━━━━━━┳━━━━┳━━━━┳━━━━┳━━━━┫┃全组总计┃238,975┃226,284┃-12,691┃-5.3┃┗━━━━━━━━━┻━━━━┻━━━━┻━━━━┻━━━━┛*第二季度末的预测图4-3个别物品与全组物品的预测误差图4-3所示为对一组10个物品的基本观察数据。对每一物品作出了该年度第三季度的预测。到该季度末,实际销售量与预测值作比较,可看出误差的百分数。对个别物品的预测,其平均误差为19.9%,范围为高35%到低40%。但全组产品的预测误差只有5.3%,虽然其中只有两个物品的预测误差是这样小。图4-4所示为某一物品在一长期间中预测需求与实际需求的比较。该物品原来预测每周销量900件,此预测值用了50周没有修改,累计预测需求等于该预测值乘以周数,而累计实际需求是50周内实际需求的总和。随着预测的延伸,累计预测误差呈增加趋势。例如,第二周未,偏离预测的数量是200,等于周预测┏━━━━━━━━━━━━━━━━━━━━━━━━━━┓┃#9物品┃┃预测=每周900件┃┣━━━┳━━━━┳━━━━┳━━━━┳━━━━━━━┫┃周次┃累计预测┃累计实际┃偏离预测┃偏离值表达为┃┃┃需求┃需求┃的近似值┃周预测值的倍数┃┣━━━╋━━━━╋━━━━╋━━━━╋━━━━━━━┫238第238页共238页n┃2┃1800┃2004┃200┃0.2┃┣━━━╋━━━━╋━━━━╋━━━━╋━━━━━━━┫┃5┃4500┃5230┃700┃0.8┃┣━━━╋━━━━╋━━━━╋━━━━╋━━━━━━━┫┃10┃9000┃10224┃1200┃1.3┃┣━━━╋━━━━╋━━━━╋━━━━╋━━━━━━━┫┃15┃13500┃15465┃2000┃2.2┃┣━━━╋━━━━╋━━━━╋━━━━╋━━━━━━━┫┃20┃18000┃19912┃1900┃2.1┃┣━━━╋━━━━╋━━━━╋━━━━╋━━━━━━━┫┃25┃22500┃24472┃2000┃2.2┃┣━━━╋━━━━╋━━━━╋━━━━╋━━━━━━━┫┃30┃27000┃28712┃1700┃1.9┃┣━━━╋━━━━╋━━━━╋━━━━╋━━━━━━━┫┃35┃31500┃33312┃1800┃2.0┃┣━━━╋━━━━╋━━━━╋━━━━╋━━━━━━━┫┃40┃36000┃39120┃3100┃3.5┃┣━━━╋━━━━╋━━━━╋━━━━╋━━━━━━━┫┃45┃40500┃46785┃6300┃6.9┃┣━━━╋━━━━╋━━━━╋━━━━╋━━━━━━━┫┃50┃45000┃54242┃9200┃10.2┃┗━━━┻━━━━┻━━━━┻━━━━┻━━━━━━━┛图4-4预测视界上的预测误差值的0.2倍,而到了第35周未,累计误差已达1800件──约相当于2周的供应量。到第50周未,累计误差约为10周的供应量。一般,随着预测视界长度的增加,预测误差将趋于增大。随着预测者对于预测艺术知道得越来越多,一个好的预测系统将总是处于一种流动状态。该预测者可能开发新的技法,并希望用实际的公司数据去检验它。如果预测人要确定一种新的预测技法是否有效,他无需等待销售量的实现。他可以假设这预测是1年或2年前作出的,而用实际发生的数字去检验这种预测方法。图4-5所示为一简单例子。此例中,根据去年以前5年的销售量的平均值作出了每一季度销售指数。这一计算中不包括去年的实际销售量。这些数据要留作检┏━━━━━━━━━━━━━━━━━━━━━━━━━━┓┃季度销售百分数的估计┃┣━━━━━━━━━━━━━━━┳━━━━━━━━━━┫┃估计的季度销售百分数(根据去年┃去年实际的季度销售百┃┃以前五年的实际销售量的平均值)┃分数┃┣━━━━━━━━━━━━━━━╋━━━━━━━━━━┫┃第一季度21%┃20.50%┃┣━━━━━━━━━━━━━━━╋━━━━━━━━━━┫┃第二季度29%┃30.30%┃┣━━━━━━━━━━━━━━━╋━━━━━━━━━━┫238第238页共238页n┃第三季度29%┃28.90%┃┣━━━━━━━━━━━━━━━╋━━━━━━━━━━┫┃第四季度21%┃20.30%┃┣━━━━━━━━━━━━━━━╋━━━━━━━━━━┫┃总计100%┃100.00%┃┗━━━━━━━━━━━━━━━┻━━━━━━━━━━┛图4-5预测技法的检验验预测技法之用。这一非常简单的检验指出,对于去年,这一确定季度销售百分数的预测技法可算是相当准确的。如果检验年度是用于建立预测值的五年中一年,此技法将不是有效的,因为这些指数很可能同用来产生它们的历史数据很相关。检验的重要好处是预测人可以通过仿真他的预测技法去犯廉价的错误。如果一个预测系统被检验表明是好的,则在实用时它也可能将是好的。在重点预测法(10)中,有一计算程序使用多种预选的预测模型来做这样一种仿真,并使用其中表现最好的一个模型于最近的数据去推测将来的需求。预测的实施做预测有五个主要步骤:1、定义预测的目的2、准备数据3、选择技法4、作出预测(包括估计的预测误差)5、跟踪预测公司里每一职能部门都需有其销售预测的信息。倘若没有对其产品未来需求的知识,没有一个职能部门能够有效地作业。事实上,没有一个单独的预测能够满足所有这些部门的需要。为了取得最好的结果,每家公司应产生一整套互相关联的预测,用来满足使用者们的需要。原理10.给每一使用者一个适用于其需要的预测。倘若不遵循原理10,使用者将被迫自己去解释该预测以产生他们所需的数据。有时,一家公司的制造、物料、工程设计、采购与财务部门必须用“官方的”市场营销预测去做这件事;他们各自为政,好像不是在为同一家公司做事似的。图4-1中指出了预测的一些用途;还有许多并未包括在内。各种用途在下列四个方面是有明显区别的。1、视界──短的、中等的与长的2、周期──每周、每月、每季或每年一次3、评审的频度──每天、每周、每月或更长些4、度量单位──钱、件、小时、加仑、打等等应弄清每种用途的目的及对上述四个因素的要求。负责发布官方预测的个人或小组应然后为具有相似要求的使用者小组重新组织数据。只有这样才可能有一种连贯的、一体化的计划方法。对许多公司,准备健全的数据这一基本问题往往可能是令人生畏的。为一段足够长的期间找出销售数字用来开发一种良好的预测方法并检验它不只是要求有一组历史的销售数字。没有有关的信息,单看过去的销售史将看不出什么时候罢工、提238第238页共238页n价、库存科税日期、会计日历中的更改、特别的促销等诸如此类的事可能已经在历史数据中掺进了使这些数据不能可靠地作为预测的基础的要素。在准备数据时,预测人还必须确定到底要预测什么。一家通过分支仓库来销售其大多数货物给客户的工厂必须使其生产同时面向分支仓库的需求与客户的需求,因为仓库由于对峰值客户需求的期望,将毫无疑义需有一些库存。在这种时候,这将对工厂生成超过实际客户销售量的需求。如果预测人只预测来自客户的续入业务的增量,工厂对在恰当时间内生产出足够的货物去满足分配网络将缺乏准备。预测人必须确定要使用数据去预测发货量还是去预测续入业务。发货量数据反映生产设施已经能够对续入业务作出何等的响应。例如,一种已经缺货4或5个月的畅销产品将显示一段低发货量的历史,虽然续入业务率是高的。根据以往的发货量来估计未来需求的预测人将由于未能反映对该产品的真正需求而延长了缺货期。即使具有足够的库存,也很少有公司能足够快地对需求的突然增长作响应使发货量保持同续入业务相等。图4-6是发货量对需求的关系一个典型例子,从图中可以看出四月与五月中突然增长的业务引起了发货量的增大,但发货室直到十一月以前┏━━━┳━━━━━━┳━━━━━━┳━━━━━━━┓┃月份┃发货量┃续入订货量┃欠交订货量┃┣━━━╋━━━━━━╋━━━━━━╋━━━━━━━┫┃一月┃302┃305┃31┃┣━━━╋━━━━━━╋━━━━━━╋━━━━━━━┫┃二月┃373┃372┃30┃┣━━━╋━━━━━━╋━━━━━━╋━━━━━━━┫┃三月┃465┃471┃36┃┣━━━╋━━━━━━╋━━━━━━╋━━━━━━━┫┃四月┃530┃562┃68┃┣━━━╋━━━━━━╋━━━━━━╋━━━━━━━┫┃五月┃591┃681┃158┃┣━━━╋━━━━━━╋━━━━━━╋━━━━━━━┫┃六月┃626┃615┃147┃┣━━━╋━━━━━━╋━━━━━━╋━━━━━━━┫┃七月┃603┃664┃208┃┣━━━╋━━━━━━╋━━━━━━╋━━━━━━━┫┃八月┃687┃675┃196┃┣━━━╋━━━━━━╋━━━━━━╋━━━━━━━┫┃九月┃731┃658┃123┃┣━━━╋━━━━━━╋━━━━━━╋━━━━━━━┫┃十月┃642┃570┃51┃┣━━━╋━━━━━━╋━━━━━━╋━━━━━━━┫┃十一月┃372┃340┃19┃┣━━━╋━━━━━━╋━━━━━━╋━━━━━━━┫┃十二月┃254┃269┃34┃┣━━━╋━━━━━━╋━━━━━━╋━━━━━━━┫┃总计┃6176┃6182┃┃238第238页共238页n┗━━━┻━━━━━━┻━━━━━━┻━━━━━━━┛图4-6发货量对续入订货量的关系一直不能克服所引起的欠交订货。这不是说五月份的大量订货直到十一月也未得到发货,但它表明在高峰季节,客户发货中的延迟大大地增长了。使用发货量为基础来确定季节性活动的预测人将预测出一个较晚而较高的高峰,结果该工厂将不能及时地生产出产品来满足实际的客户需求。在预测中区分不同的需求流也是重要的。上例中的工厂很可能将其货物的45%直接发给客户而把55%的货物通过仓库再发给客户。这将意味着对工厂订单有两种不同的预测类型,一种代表直接给工厂的真正的客户需求,另一种代表客户对仓库的需求再加上或减去仓库库存中的增量或减量。许多公司有一些商品是出售给不同种类的顾客的。例如,一公司可能制造一种硬件物品,正常情况下它以小量频繁订货方式出售给批发商──但有时被原设备制造商(OEM)以每年两批的方式买去制造家具。每年两次在库存上将是加在来自批发商的许多小量需求上的极大需求;这两股需求流将要求有分别的预测。平均需求量是毫无意义的。预测人在分析历史数据与做预测时使用恰当的期间也是极端重要的。图4-7┏━━━┳━━━━┳━━━━━━┳━━━━━━━━┓┃月份┃月销售量┃每月工作日数┃每一工作日销售量┃┣━━━╋━━━━╋━━━━━━╋━━━━━━━━┫┃一月┃334,000┃22┃15,200┃┣━━━╋━━━━╋━━━━━━╋━━━━━━━━┫┃二月┃310,000┃20┃15,500┃┣━━━╋━━━━╋━━━━━━╋━━━━━━━━┫┃三月┃338,000┃23┃14,700┃┗━━━┻━━━━┻━━━━━━┻━━━━━━━━┛图4-7月销售量与日销售量说明月销售量可能给出的假象。单看月销售量这一列,似乎二月份的销售比一月低不少而且三月份比一、二月都有增长。但把每月的工作日数考虑进去之后,可看出二月份每个工作日的销售量比一月份上升了,而三月份每一工作日的销售量却比一、二月份都要低。有的文献把预测技法区分为客观的方法(根据“冷的”统计的或数学的分析)与主观的方法(根据“暖的”人类判断)。这样区分对讨论是有用的,但每个好的预测都是二者的结合。一切统计技法都是以“未来将继续像过去那样”这一假设为基础的。过去数据中的模式、趋势或周期被假设将继续下去并选用预测模型来把它们外推或外插到未来的期间中去。每一企业中的管理人员都努力使未来不同于过去──希望它比过去更好。因此,任何客观预测要想成为官方的,必须首先经过人类判断的检验,判定将来与过去的这些不同点将如何影响这种预测。有两种因素必须考虑:1、内部的:在公司内部,诸如价格变化、促销、提高质量、更加及时的交货、更短的制造时间等等因素将有什么影响?2、外部的:在公司外部,竞争者、一般经济、政府法律等等将如何影响它们?238第238页共238页n统计的预测只是起点,一种以前后一贯的、有秩序的方法与在合理的计算机时间内去处理大量项目的方法。靠人对之作跟踪评审正常地是主日程计划工作的重要部份,详见第7章。时常有人问,谁应该去作预测?通常的回答是,市场营销或销售。从刚刚讨论过的对内外因素的影响的评价来看,却可见预测是一集体协作活动。物料控制、数据处理与市场分析人员将选择若干预测技法并生成“初步”预测。然后,它们将由市场营销、销售、制造、工程与其它能有助于评价这些其它因素的影响的人们来评审。判断预测这里要弄清的最重要论点是判断预测与统计预测(广义的统计)这两种预测方法是一道使用的。判断预测,有时叫做预报,它包括:根据对业务有实感的个人的专家意见而作的预言;调查销售人员以确定在即将来临的预测期间他们认为或已被告知的其帐户将接到订货的产品数量;还有市场调查,其中一位对话人走出去到市场上,也许还带着产品的样品,或直接找潜在的客户对话或找同客户有密切接触的零售商或批发商对话。对预测的判断方法中有许多缺点。虽然许多主管人员懂得市场并且具有预见未来发展的能力,但不能简单地假设由于一个人具有主管人的地位就自然会是一名好的销售预测人。销售人员按其本性是不倾向于解析思维而趋向于根据最近的趋势要末乐观,要末悲观。销售人员可能认为调查的结果将用来提高他们的定额,于是他们将给出悲观的估计。想从销售人员那里得出客观的预测是非常困难的。许多公司已丢弃了这种办法。市场调查──无论用信件、电话或个人对话──都是收集信息的昂贵手段,而且其可靠性取决于以一个小样本来代表整个市场有多大的准确性。在有些情况下,调查被证明是不可靠的,因为人们的言行并不一致。销售消费产品的公司时常采用试验市场的方法,即选择国中被认为具有代表性的一个小区,并仅仅在这一区域内销售他们的产品以确定公众的反应。这是一种相当昂贵的方法,它在许多情况下被证明是有成效的。作为预测整个市场的一种手段,其成就取决于市场营销人员选好一个具有代表性的样本地区的能力。也许判断预测法最大的问题在于人类受新近事件的影响强烈。判断预测正常地趋向于对最近的情况作出过头的反应。单凭判断而不使用其它工具的预测人可能犯下非常严重的错误。以后面的图4-9中所示的一条12年的实际销售趋势曲线为例,在第五年末作判断预测的个人,看到接连三年的弱增长之后,不大可能认识其长期趋势,因而很可能作出太低的预测。判断预测的一个严重的实际限制是一名个人只能作出较少数的预测,而大多数公司有成百种的物品必须处理。预测全新技术或类似个人计算机、空间考察与光纤等新产品的影响与结果是非常困难的任务。使用台尔菲法,在提出正确的问题方面(倘若不是说得到答案的话)已得到一些成就。一组“专家”,熟悉该技术应用领域的人们,被询问一系列的问题,每个人给出他个人的估计。然后将结果交给所有成员评审,并进行第二轮的预测。该过程持续进行若干轮,直到无一小组成员修改数字为止。于是用户应用此结果作为看起来是合适的预报。不管如何主观预测还是可贵的。它们是能够使人类的判断对预测问题有影响的唯一手段。然而很少公司单独使用判断预测,因为它们是昂贵的,倾向于对新近事238第238页共238页n件作出过度反应而且限于只能对少数物品作预测。统计预测另一种基本的预测方法──统计技法的使用──可包括使用一产品自身的需求史去确定未来销售的预测(使用内生因素,诸如平均值或历史趋势),或根据多元相关分析(使用外生因素,诸如车辆运输量、GNP、新住宅建筑动工数、汽油消耗量与其它有关活动)去预测并非同这些活动直接关联的产品的销售。趋势外推是众所周知的最简单的预测技法之一。有了这条长期趋势线可以帮助预测人稳定他的预测而不致对短期事件作出过度的反应。建立趋势线有比目视法准确得多的方法;在大多数统计学的标准教科书中叙述的最小二乘法便是预测者行业的一个重要工具。本章后面要详述的移动平均法可用来产生该序列的长期趋势并将此趋势外推到未来。季节性模式,当年复一年始终如一时,可用实际月销售量与平均月销售量之比来表示。在趋势与季节性分量被除去之后,剩下的就是随机性。没有办法可以预测随机性,但随机性的范围可表达为一个误差百分数,使得预测需求的极大值与极小值可以从预测平均值来确定。倘若此随机因素是大的,则生产计划与个别产品的重订货点,譬如说,将必须包括大的安全存货。反之,倘若过去所经历的随机性是小的,则该预测被预期为比较准确的,所以有较小的库存储备也许就足够了。总业务量的预测要使详细的产品或产品组合的预测有用,首先必须有对公司总业务量的预测。这类预测对制订生产计划也是需要的。做这类预测有许多方法,其中包括一些非常有用的技法。它是以使用一领先序列为基础的。在此例中,对过去需求的分析表明新住宅建筑动工数领先于A公司产品销售量约3个月。在有些行业中这样一种关系是存在的。重要的是要确定存在着一种始终如一的可靠关系,而不只是暂时的重合,并且要连续地跟踪这种关系以发现变化。当这类关系可用时,就能作出相当准确的预测。诸如新住宅建筑动工数等活动的信息被定期地公布在行业的杂志中。政府机构(如劳动统计局)与私营研究机构(如国家经济研究所)定期地公布许多经济序列的数据,它们可成为预测各种工业产品的基础。即使找不到一个领先序列,也往往可使用一个相关序列,其运动与某公司的销售量在时间上是重合的或甚至是滞后的,来预测该公司的销售量,因为这些序列的许多其它比较复杂的预测是由政府或私营研究机构做出的。汽车替换零件行业中的一家小公司恐怕不能化多大力量去作预测,但可以利用较大公司作出的预测或实际销售数据。不能说只因为预测是由大公司或专门的政府经济学家作出的,所以它就必定是准确的。这类预测的使用者应该有准备去发现明显的错误并迅速地发起行动以响应变化着的需求。用于预测的一种更加复杂的数学技法要求在若干外生要素与一家公司的销售之间建立起相关关系,这叫做多元相关法。这类分析的结果是一个公式,它对该预测的开发中所包括的各种因素给以不同的相对权数。图4-11所示为一简化的例,┏━━━━━┳━━━━━━━━━━━┳━━━┳━━━┓┃要素┃目前活动率┃权数*┃指数┃238第238页共238页n┣━━━━━╋━━━━━━━━━━━╋━━━╋━━━┫┃零售销售量┃¥24.3(10亿/月)┃0.023┃0.56┃┃钢锭生产┃2700(顿/周)┃0.0001┃0.27┃┃车辆运输量┃62(千辆/日)┃0.005┃0.31┃┣━━━━━┻━━━━━━━━━━━┻━━━┻━━━┫┃新指数=1.14┃┃┃┃*由多元相关法生成┃┗━━━━━━━━━━━━━━━━━━━━━━━━━┛图4-11包装材料的外生预测说明根据包括材料同零售销售量、钢锭生产、车辆运输量等外生因素的多元相关关系所作出预测。原始数据来自许多商业出版物的周刊或月刊,权数由这些数据用多元相关法算出。将每一要素的目前活动率乘上相应的权数,然后求各要素的指数之和,可得新总指数为1.14,指明此公司的产品预测现在将比预测的基期提高14%。多元相关法超出了本书的范围,可详见统计分析的高等教科书。有计算机程序可快速而准确地处理多元相关问题──在未来这类预测将毫无疑问被更加广泛地用来估计总的市场需求。各家公司仍将必须估计他们自己的市场份额并将总需求分解为大类产品的需求。销售人员的估计在作出总业务量预测中肯定是有一席之地的。如果配合上一个统计预测为基础,它可以是极其可贵的。例如,可用统计技法去建立一份预测,指明一家公司的产品其总的市场潜力明年应增长10%。然后就可以对销售人员进行民意测验以确定公司的市场份额是否将保持不变。由于熟知竞争气候,销售人员比公司中其它人有更多发言权来说,从统计预测所指明的总趋势来看,市场渗透究竟将会上升还是下降。大类产品的预测总的业务量预测做出之后,必须把它分解为更细的产品分组预测。这些产品组必须对市场营销与制造都有重要意义。例如,一家农机制造商可按金额作出其总业务量的预测,把它关联到政府对可自由支配的农场收入的估计。该总金额将进一步分解为每一类产品(诸如拖拉机、康拜因或打包机)按农产品大类(即麦、谷、大豆等等)的金额。这可以使用根据过去经验的一个百分数,再用销售部门或市场营销部门关于某一具体市场中某一特定产品大类的需求趋势的知识去修正它。有一些指示器是直接联系于某一特定产品的,诸如小麦的耕种面积或对大豆的津贴的改变。下一步是把已知的季节性指数应用于特定的产品大类,特别是在诸如农机行业中。图4-12所示为每个月的季节性指数,表示为康拜因年销售量的一个百分数。在这一假设的情况中,分析了5年的历史数据,月销售量表示为年度总量的一个百┏━━━┳━━━━┳━━━━┳━━━━┳━━━━┳━━━━┳━━━━┓┃月份┃第一年┃第二年┃第三年┃第四年┃第五年┃平均%┃┣━━━╋━━━━╋━━━━╋━━━━╋━━━━╋━━━━╋━━━━┫┃一月┃7.48%┃5.46%┃6.36%┃6.56%┃6.54%┃6.50┃┣━━━╋━━━━╋━━━━╋━━━━╋━━━━╋━━━━╋━━━━┫238第238页共238页n┃二月┃8.24┃4.70┃6.68┃7.35┃5.78┃6.55┃┣━━━╋━━━━╋━━━━╋━━━━╋━━━━╋━━━━╋━━━━┫┃三月┃8.27┃7.30┃8.84┃7.90┃8.03┃8.05┃┣━━━╋━━━━╋━━━━╋━━━━╋━━━━╋━━━━╋━━━━┫┃四月┃7.95┃9.34┃9.40┃8.79┃9.29┃8.95┃┣━━━╋━━━━╋━━━━╋━━━━╋━━━━╋━━━━╋━━━━┫┃五月┃9.66┃8.65┃10.50┃11.11┃10.44┃10.30┃┣━━━╋━━━━╋━━━━╋━━━━╋━━━━╋━━━━╋━━━━┫┃六月┃10.00┃11.30┃10.60┃8.79┃9.71┃10.10┃┣━━━╋━━━━╋━━━━╋━━━━╋━━━━╋━━━━╋━━━━┫┃七月┃9.06┃8.70┃7.66┃9.01┃9.96┃8.90┃┣━━━╋━━━━╋━━━━╋━━━━╋━━━━╋━━━━╋━━━━┫┃八月┃9.85┃11.10┃10.80┃10.12┃11.00┃10.60┃┣━━━╋━━━━╋━━━━╋━━━━╋━━━━╋━━━━╋━━━━┫┃九月┃9.71┃9.50┃8.15┃9.70┃7.90┃9.00┃┣━━━╋━━━━╋━━━━╋━━━━╋━━━━╋━━━━╋━━━━┫┃十月┃6.65┃8.72┃8.09┃8.78┃8.95┃8.25┃┣━━━╋━━━━╋━━━━╋━━━━╋━━━━╋━━━━╋━━━━┫┃十一月┃7.85┃8.08┃7.64┃7.34┃7.72┃7.70┃┣━━━╋━━━━╋━━━━╋━━━━╋━━━━╋━━━━╋━━━━┫┃十二月┃5.12┃6.15┃5.13┃4.54┃4.64┃5.10┃┣━━━╋━━━━╋━━━━╋━━━━╋━━━━╋━━━━╋━━━━┫┃总计┃99.79┃100.00┃99.85┃99.99┃99.96┃100.00┃┗━━━┻━━━━┻━━━━┻━━━━┻━━━━┻━━━━┻━━━━┛图4-12康拜因季节性指数的产生分数。使用5年的数据计算出每个月的平均百分数。一名好的预测人会再要1 ̄2年的数据,用它们来做一次仿真以检验季节性百分数的有效性。使用这一大类产品的年度销售预测,图4-12中的每月平均百分数可用来作出一份月预测。把这一预测结果表达为制造上有意义的语言(例如用工时)可能遇到的一个主要问题是因为有可能一种特定类型的农机是在一家制造厂生产而第二种类型是在另一家制造厂生产的。此外,如果大小不同型的这类农机在生产工时上的要求差异很大,则每家工厂将区分大型农机与小型农机。预测人应知道这些细节以便使产生的数据对制造人员有用。产品分组预测是用来制订能力计划的,不应用来安排型别的组合。它们是用来确定对每一种主要生产设施的工人与机器能力的需求的。产品分组预测的重要目的是去建立生产水平。这一应用利用成组预测精于个别物品预测的原理。第9章讨论生产水平的计划与控制以及使用预测误差的度量去建立何时改变生产水平的决策规则。这恐怕是预测的最重要用途与制造控制的主要功能。如果不能有效地计划与控制好生产水平,就不可能提供良好的服务并保持库存处于平衡。物品预测确定订货点、订货量与主生产日程要用到物品预测。物品预测最好使用简单的、238第238页共238页n根据该物品自身的需求历史的内生统计技法。每一类产品中各个别物品预测之和应等于为计划生产水平而准备好的分组预测。通常这需要经过调整才能使二者相等(理由见本章后面)。成功地使用统计预测的关键是选择适用于被测物品所经历过的需求模式的技法。这些模式可分为四大类,如图4-13所示。┏━━━━┳━┳━┳━┳━┳━┳━┳━┳━┳━┳━┳━━┳━━┓┃┃一┃二┃三┃四┃五┃六┃七┃八┃九┃十┃十一┃十二┃┃┃月┃月┃月┃月┃月┃月┃月┃月┃月┃月┃月┃月┃┣━━━━╋━╋━╋━╋━╋━╋━╋━╋━╋━╋━╋━━╋━━┫┃水平的┃45┃55┃35┃55┃60┃40┃65┃50┃45┃60┃40┃50┃┣━━━━╋━╋━╋━╋━╋━╋━╋━╋━╋━╋━╋━━╋━━┫┃间歇的┃6┃0┃5┃0┃0┃7┃3┃0┃1┃4┃0┃2┃┣━━━━╋━╋━╋━╋━╋━╋━╋━╋━╋━╋━╋━━╋━━┫┃趋势性的┃10┃15┃20┃15┃20┃30┃25┃25┃30┃35┃30┃40┃┣━━━━╋━╋━╋━╋━╋━╋━╋━╋━╋━╋━╋━━╋━━┫┃季节性的┃65┃60┃50┃40┃25┃30┃35┃50┃60┃70┃75┃70┃┗━━━━┻━┻━┻━┻━┻━┻━┻━┻━┻━┻━┻━━┻━━┛图4-13需求模式水平的需求代表具有稳定需求的成熟产品。间歇的需求代表处于其生命周期的很早或很晚期的低需求量物品与大多数的维修零件。趋势性需求显示较为稳定的增长或下降而季节性物品每一日历年度要经历高峰与低谷。此外,还有一些特殊的需求情况,诸如正规的周期性需求与长于一年的周期性需求,预测技法平均值:平均值提供一种很有用的技法。有两类是预测中常用的;移动平均值与加权平均值。移动平均值可在任意个数据期间之上计算出来,期间的个数越多,平均值越稳定但产生的预测越不灵敏。更新平均值的法则是D1+D2+D3+...+Dn+Dn+1-D1F=─────────────────────(4-1)n其中:D=每一期间的实际需求N=平均值中期间的个数F=预测值此式通过加上一个最近的实际需求值同时减去最早的一个从而提出一个新的预测值。该新的平均值被设想为未来的预测,这未来有多远要看预测人是否相信它是合理或必要的。图4-14所示为使用此技法于图4-13中水平的与间歇的需求模式的情况。注意由于预测值要受加进的需求与减去的需求之间的差值的影响,所以它是变动的。移动平均法计算简单,但它要求存贮大量数据(每一期间的需求)。减少期间数是238第238页共238页n容易的,但增多期间数要难得多,因为必须找到历史数字。显然此技法不适用于趋势性或季节性的模式,因为它设想一切未来期间都用同一预测值。┏━━━━━┳━━━━━┳━━━━━┳━━━━━┓┃一月┃二月┃三月┃四月┃┣━━┳━━╋━━┳━━╋━━┳━━╋━━┳━━┫┃预测┃实际┃预测┃实际┃预测┃实际┃预测┃┃┏━━━╋━━╋━━╋━━╋━━╋━━╋━━╋━━╋━━┫┃水平的┃50┃60┃51┃35┃50┃55┃51┃┃┣━━━╋━━╋━━╋━━╋━━╋━━╋━━╋━━╋━━┫┃间歇的┃2.3┃0┃1.8┃0┃1.8┃6┃1.9┃┃┗━━━┻━━┻━━┻━━┻━━┻━━┻━━┻━━┻━━┛图4-1412个月的移动平均预测图4-15说明如何用加权平均值来预测物品需求。在此特例中,早先所做的一个周预测(叫老预测)指出销售量将为每周100件;第一周的实际销售量后来达70件。若使用简单的算术平均,新预测将为85件。这其实是给老预测与最近一周的销售以同等的权数(50%=0.5),大多数人会认为这样计算是不够妥当的。┏━━━━━━━━━━━━━━━━━━━━━━━━━━━━━━━┓┃第一周┃┣━━━━━━━━━━━━━━━━━━━━━━━━━━━━━━━┫┃权数权数┃┃老预测=100(每周平均)×0.5=50×0.9=90┃┃销售量=70(最近一周)×0.5=35×0.1=7┃┃新预测=8597┃┣━━━━━━━━━━━━━━━━━━━━━━━━━━━━━━━┫┃第二周┃┣━━━━━━━━━━━━━━━━━━━━━━━━━━━━━━━┫┃老预测=97*×0.9=87┃┃销售量=105×0.1=11┃┃新预测=98┃┣━━━━━━━━━━━━━━━━━━━━━━━━━━━━━━━┫┃通用公式:┃┃新预测=α×销售量=(1-α)老预测(4-2)┃┃α是权系数的名称┃┃*它是上一周的新预测值┃┗━━━━━━━━━━━━━━━━━━━━━━━━━━━━━━━┛图4-15加权平均预测使用加权平均法,可以(如例中所示)给老预测90%的权,而给最近的实际值10%的权,这样算出的新预测值将为97。如此,则由于销售量的下降预测值238第238页共238页n只略有下降。大多数人将同意类似这样的算法要更加合理一些。注意两个权数相加必须恒等于1。图4-15还说明第二周的预测值如何用加权法计算出来,老预测值现在是97件,而第二周的实际销售量是105件,所以新预测值是98件,比上周略有上升。这一技法叫做指数平滑法,它是根据R.G.Brown的工作(1)。它提供一种常规地更新预测值的例行方法。用计算机,一个简单程序可在很短时间内在常规基础上为几千种物品做出预测。图4-15中的指数平滑方程(4-2)叫一价平滑议程;还有比它更高阶的指数平滑公式,它可以包括对趋势性与季节性变化所作的校正。为简化计算,一阶平滑方程可重新排列如下:新预测值=老预测值+α(销售量-老预测)(4-3)这种形式只做一次乘法。使用图4-15中第二周的数据(如何确定α将在以后讨论)新预测值=97+0.1(105-97)=98图4-13中两个项目的预测用此法与用移动平均法基本上是一样的。公式(4-2)与(4-3)都属于一阶指数平滑公式。当应付相当稳定的项目时它们工作得很好,而且它们将相当容易地检出趋势,虽然当有显著趋势存在时该预测将滞后于实际需求。然而,在确信存在这种趋势的场合(例如,当引进一新产品时),可使用二阶平滑法。在二阶平滑法中,预测由A与B两部份组成:A新=老预测+α(销售量-老预测)(4-4)B新=B老+α(A新-B老)(4-5)第一部份A新是简单一阶平滑。第二部份B新提供一个为一种趋势校正预测的因素,以消去一阶平滑的滞后效应。换句话说,A新比以销售订单为基础的实际需求模式要滞后。B预测把A当作实际需求使用,它将滞后于A预测一个相似量。校正方法是将一阶预测A新加上一个等于A新与B新之差的校正量:新预测=A新+(A新-B新)=2A新-B新(4-6)将些技法应用于图4-13中趋势性需求模式要求有A老与B老的数字。可使用任何合理的数据;取决于所使用的α值,在若干个期间之后,坏的猜测对计算的影响将变得不显著。目视该数据指出取A老=35与B老=32看来是合理的,而且用α=0.2是相当普通的。一月份的实际销售量是45件,则二月份的预测是:A=35+0.2(45-35)=37B=32+0.2(37-32)=33新预测=(2×37)-33=41要不要做二阶平滑的决定可通过取几个项目的实际数据并仿真其结果来确认。一般,实际工作者发现一阶平滑对大多数项目给出的结果是相当令人满意的──尤其是对短期预测。在需求很低或在某些预测期间没有需求的场合,指数平滑技法是不成功的。对图4-13中间歇性模式的数据作一阶或二阶平滑的快速检测说明这些技法用在错误的数据类型上其效果有多差。238第238页共238页n假设仿真表明指数平滑法将给出令人满意的结果,则问题就在于要确定恰当的权系数(α)。在图4-15中,取低的α值0.1的结果是老预测成为新预测的控制因素,实际销售量的影响很小,变化的趋势将因而不能被很快地检出。如果取高α值,譬如说0.3,则预测将尖锐地反应销售中的变化,而且事实上倘若在需求中有相当大的随机波动时,预测将是高度不稳定的。任何α因素值都要在太呆与太飘之间求折衷。对一组给定的数据选择恰当的α值可通过仿真,仿真将显示多大的α因素将工作,只要未来的需求模式不变的话。通常为了得到快速地移动并让实际经验去显示需要有一不同的α因素的例外情况,使用范围在0.1到0.2之间的α因素就相当可以了。在一家公司已经使用了几个星期的移动平均值并希望代之以指数平滑法以获得可存贮较少数据与对变化更具弹性的好处的场合,可使用公式(4-7)去确定α因素,使它能给出近似地相当于以前使用过的平均值的期间数的结果:2α=─────(4-7)n+1例如,倘若以前所用的预测是一个12个期间的移动平均值,则α因素将取2α=─────=0.1512+1使用此式,可以看出0.2的α因素近似地相当于一个9个期间的移动平均值,而0.1的α因素则近似地相当于一个19个期间的移动平均值。在这些期间之后,不好的起始值对使用指数平滑法的任何影响都将消失。季节性预测:老练的数学家们看来抵挡不住试图以复杂的曲线去拟合季节性数据的诱惑。这种努力不仅主要地是不必要的,它不会产生如图4-12中所示用期间基指数法所取得的那样好的效果。倘若季节性模式是重复性的,此法将同其它方法一样地好,而倘若模式是偏斜与参差不齐的,则此法将比其它方法更好些。使用图4-13中季节性模式的数据,各月的指数如图4-16所示。每一指数就是该月的实际需求与该年月平均值的比值。产生这些指数的好办法要求使用若干年份的数据,如图4-12所示。这些指数是在更新预测时用来使数据季节化与去季节化的。月份需求基指数──────────────────────────一651.2二601.1三501.0四400.8五250.5六300.6238第238页共238页n七350.7八501.0九601.1十701.3十一751.4十二701.3──────────────────────────总计630平均52.5──────────────────────────图4-16季节性指数做季节性预测要求有某种推测一个新的月平均数字的方法。可以用本章已讨论过的任何一种方法。在使用实际需求之前,不论用什么技法,首先要把实际数据除以指数使它正则化为一个平均月份。在平均月份的预测被更新之后,将新预测乘以各月份的指数使它季节化。特殊预测为促销与新产品做预测比为稳定物品做预测要困难得多。由于很少新产品是真正地原始的,这种预测往往可根据一相似产品的已往经验。例如,电视机制造商可使用24"黑白机与21"彩色机的经验去估计新品24"彩电的销售。制造不同于市场上现有的任何产品的新品时,公司恐怕得使用某种类型的市场调查。许多制造女式服装或食品的公司,由于个人的偏好与消费者的接收性极难预报,通常使用市场调查或试销以便在大规模投产该物品之前先确定产品的可接收性。重复进行促销能得出对预测它们所引起的需求有用的数据。使用S曲线要求仔细、及时地跟踪销售的实现过程,而且工厂及其供应商对预测的总需求中的变化要有快速的反应。像季节性基指数一样,S曲线法的成功取决于相继而行的促销有着十分相似的特征。管理上一个棘手的问题是要在其结果具有良好重复性(因而具有较好的计划上的潜力)的一系列相似促销与可能产生高得多的销售但也带来显著的生产问题的根本性改变之间作出选择。对于新产品与促销产品,预测误差的估计是十分重要的。应当让公司的管理层知道按预测去安排计划的后果,譬如说预测是10万件,但实际销售可能只有2万件或高达50万件之多。如果作预测时就相信销售中可能有这样大的波动范围,对高价物品的明智计划将使过量库存的风险降到最低限度,而机床设计与长提前期组件的精明处理将使生产能够快速地响应需求的增长。除非做出努力去估计预测误差,否则这样观实的计划是不可能的。为促销物品与新产品预测需求还必须考虑填满渠道的模式。当一项新计划或新产品被发布而且受到销售人员的热烈响应时,大多数销售人员将能召唤他们和客户并在电话上说服他们至少购买一个象征性的数量。以后几天,在他们的常规销售通话中,他们的热情将销售出更多的该新产品。在工厂里,将收到订单的一次原始的巨浪,随后是订单的稳定流入──所有这些只不过反映分销商、批发商或存储该产品的其它各类客户的需求。大多数产品要经过分销商才到达最终用户,所以很少数238第238页共238页n订单代表真正的消费者的需求。货架一旦存满,需求会有一个下降直到真正的消费者销售量出现──而这些销售量确定实际需求将有多大。了解这一填满渠道的模式将防止预测人对销售人员的原始热情所造成的巨浪,对存货订单被完成后的销售下降以及最后对原始的消费者反应等作出过度的反应。沉着加上有知将有助于预测人去恰当地解释新产品的销售。预测为什么失败预测为何产生出不成功的结果,原因并不神秘,有六种:1、预测不是集体的努力;而评价使将来不同于过去的内外诸因素的工作要求有各职能部门人员的参与。没有“专家”能胜任这项工作。2、发生幻想破灭;对准确度不现实的希望引起拒绝使用预测与不会使用预测;奇怪的是,人们坚持这种不切实际的希望而重复这种恶性循环。3、发生“自己动手”的变态心理;显然“他们的预测”是错误的,所以我们必须自己来做。我们昨天做得不太好,但明天的预测会更好的。4、人们有不同的需要;销售人员需要伸展开的去满足挑战性的预测,管理者的财务计划必须是保守的而制造必须具有现实主义态度。5、无人照管;每个人都希望预测将是对的,知道它将会错,而且忘记了它,因而丧失了去找出它可能如何错以及何时它显然需要修订的机会。6、不必要的项目被包含在内;企图为描述产品的物料清单中的组件或为由选件组成的产品去作需求预测是浪费时间。许多产品为其用户提供若干选件──汽车、机床、计算机、无线电、自行车以及家用电器只是少数例子。图4-21显示无线电产品中可供的选件。任何人都懂┏━━━━━━━━━┓┃音频/调频/立体声┃┃无线电┃┗━━━━┳━━━━┛┃┏━━━━━━━━┳━━━━┻━━━━┳━━━━━━┓┏━━┻━━━┓┏━┻━┓┏━┻━┓┏━┻━┓┏┫频率有关组件┃┏┫电源┃┏┫底架┃┏┫天线┃┃┗━━━━━━┛┃┗━━━┛┃┗━━━┛┃┗━━━┛┣音频┣12伏直流┣汽车用┣自带┃┃┃┃┣调频┗115伏交流┣可携式┗外部┃┃┣音频/调频┗落地式┃┗音频/调频/立体声图4-21选件的预测得企图去预报任一期间中对这些选件的每一种具体组合有多少客户订货是枉费心机的,但许多人看不出有什么替代的办法。然而,完全可以──事实上更好──去预238第238页共238页n测每一期间内无线电的需求总数以及其中每种选件所占的百分数。从这些数据,可以准备出用于制造计划的有效的主日程计划。在最终装配开始之前,不需知道哪些选件必须组成任何一架无线电;在许多情况下,未收到客户订单之前是不发生这样的问题的。这样来设计产品可使预测问题变易,便于计划与控制而且可以简化制造。这一主题将在第二册中同主日程计划与物料清单的结构问题一道详述。需求的源在本章前面粗略地提到过需求的流或源。前面讨论过的都是用来预测客户需求的技法。这一需求可分为三组:一组直接发生在工厂或邻近的主要仓库;一组发生在国内其它地方的分支仓库;一组发生在国外。出口问题超出了本书的范围。在市场要求、时机安排与产品种类方面出口需求与国内需求有许多差别,所以必须对这两种需求分别地作出预测。分支仓库的客户需求基本上与主设施相同,当然,不同的是它的数量通常较小。前面讲过,数量很小的、间歇性需求的物品很难预测。这类物品应不应在分支仓库中存储也是一个好的问题。如果必须存储,最好去预测系统总的需求,安排补货订单去处理它,然后将每批的一部份分配给每一分支仓库以便向所有仓库提供平衡的库存。分配这类物品的技法详见附录Ⅶ。厂际需求不应作预测;它应从用户厂的制造计划计算出来。主日程计划,在本书第7章与第二册的第2章将彻底讨论,必须包括供货厂与用户厂双方对足够的物料供应与均衡负荷的需要的考虑。其技法见第5与第7章。分支仓库之间的物资转移应当看作是要去避免的问题,而不是要去计划的问题。虽然它们是处理意料之外的或罕见的大量需求或供应中断等情况的有效方法,这种订单的高额搬运与发货费用使它们成为最后的一招,而不是正常作业的一部份。预测、存货与满足各类客户对各类物料的需求的主导策略应当如原理14所述。原理14.不到尽可能最后时刻,不要把存货物品委置于任一具体的地点。238第238页共238页n五.物料控制:独立需求库存的补充新物品的首次订货是库存管理的特殊情形。这类物料管理的原理与技法在第6章讨论。本章讨论常规使用中的物料被不断地补充或定期成批地补充的情形。第3章的EOQ概念回答每一次发出补充订单应订货多少的问题。回答这一问题中,订货成本要同库存持有成本相平衡以给出最小的总成本。在库存控制中,另一必须回答的基本问题是该补充订单必须在何时发出。回答这个问题中,库存投资成本必须同所希望的客户服务水平或缺货成本相平衡。显然,如果补货订单不能及时发出,物料将不会及时到货,在新批收到之前就会把剩余物料用完。反之,如果订单发出过早,库存将过高。由于重订货技法的选择最终地确定所提供的客户服务水平,这一决定通常对管理人员比批量的决定要重要得多。不良的客户服务通常比订货或库存成本更快而且更有力地引起管理人员的注意。实际上,这一事实的后果是作出的决定往往以高库存为代价大大地偏向于客户服务。原理15.正确地回答一物品何时需要的问题比确定要订多少货重要得多。任何库存控制系统,不管多么简陋,总有一些内在的决策规则。每周购买一次食品的主妇按照告诉她们何时重新订货的直觉规则来确定她的购物单。其中有些规则是相当切合实际的。主妇多半能相当准确地预报每餐要使用的肉类的数量,并多半在需要重新购买时用完上周的肉类的最后余量。另一方面,化妆纸可能服从一非常无规律的需求──也许取决于家中有无某一成员伤风感冒。主妇可能决定在衣橱里应当常备一盒擦面纸。当这一盒被打开时,她将在每周购物时购买另一盒。香草精难得一用,当用完时,该主妇可能决定暂时不买直到下次计划烘烤什么时再说。减价出售的廉价货的采购则要受有没有钱的限制,也要受水箱、冷冻室或食品柜存储容量的限制。这些是实际上很有效的简单规则,虽然它们可能甚至得不到始终如一的应用。在购买食品与杂货时,主妇通常不注意库存(食品与杂货)的投资同缺货的机会之间的平衡。倘若她偶而让一常用物品用光了,由于商店就在邻近或可从邻居暂借一下,这不方便通常是小的。对大多数日常生活中作出的库存决定这是真的。这类日常用的重订货系统可以非常松弛,因为其提前时间短库存投资小,即使缺货时所带来的不方便也较小。在企业中有许多库存──例如办公用品──可以相当成功地用类似的简单决策规则来加以控制。然而,还有许多其它物品,它们涉及巨额的库存投资,万一缺货要付出极高代价或补货提前时间很长。为了恰当地控制这些库存,可以用一些高效率的重订货方法。它们有许多形式,但通常同下列五种方法之一有关:1、两箱法:此系统中,一特定物品的存货以某一预先确定的数量被放在一边(往往放在分开的第二个箱子中)不予接触,直到该物品的主要存货被用完。当后备供应量被打开时,即有通知书被送到库存控制办公室并发出一补货订单。(详见“两种简单订238第238页共238页n货方法”)2、目视评审法:定期地用目视法核对存货水平,每次评审后在需把存货水平恢复到某一预先确定的现有库存与已定购量之和的最大值的场合就发出补货订单。(详见“两种简单订货方法”)3、订货点法(固定订货量──可变订货周期制):当提货使一物品在永续盘存记录上的库存下降到一预先确定的叫做订货点的水平时,发出补货订单(通常订货量为预先计算好的EOQ)4、定期评审法(固定周期──可变订货量制):在定期评审中,库存记录被定期地评审,也许每周一次或每月一次,并定期地订货使现有库存加上已订货量的库存总量恢复到预先确定的最高水平。(详见“定期评审技法”)。5、物料需求计划(MRP):在MRP中,物料按能满足使用物料的物品的预先制订的生产计划所需的数量与交货日程来订货。(详见第6章)。所有这些方法在概念上都是紧密联系的。显然,例如两箱法,虽然它并无库存记录,却同订货点法非常相似,因为第二只箱子里存放的就是订货点数量。同样地,众所周知的极小与极大法只是订货点法的一种变态。该极小值实际上就是订货点,而极大值就是订货点加上订货量。然而,订货点法在工业的库存控制中并未获得普遍的应用。事实上,这一技法──以及刚才列出的第1到第4种有关的方法──对成品库存与库存中持有的维修零件有极好的应用,例如,在该物品的需求倾向于连续的而且不依赖于任何其它库存物品的场合。然而,在需求倾向于间歇的而且需求量的变化取决于一更高层装配件的需求水平的场合,补充这种组件与子装配件的库存,通常以使用MRP更为有效。上述重订货技法都将进一步讨论,本章讨论前4种。订货点法被深入地讨论,因为它为用来对付重订货系统中不确定性的方法提供了最好的例子。MRP将在第6章叙述。在所有这些讨论中,需求是指在一给定期间中对一物品的总需要量。提前期是从确定必须发放一份补货订单起到该订单中的物料被收进存货并可供使用为止所经历的时间。这是一物品最易受缺货伤害的期间,因为库存正处于最低点。订货点法的基础订货点法,包括对提前期中需求的估计,加上一些储备存货用来对付无论需求还是提前期都不能被肯定地预报这一事实。假设使用率是固定的,库存将沿着斜线下降,达到订货点时发出一补货订单,订货量为EOQ,如垂直的虚线所示。在提前期中,库存继续下降,到提前期末,收到了补充订货;于是库存增加了EOQ,库存的升降循环又重新开始。另一必要的假设是补货是即时完成的。不幸的是,在大多数实际的库存情况中,无论提前期还是需求都不能准确地预报。其结果是,简单地根据提前期中的平均需求来确定的订货点将不能为防止缺货提供足够存货,因为需求的波动有一半时间要超过平均值。于是,一个主要问题就是在订货点法中需要配备多大的储备存货。头两个周期都未触及储备存货。然而,在第三个周期,使用率变大了,如图中238第238页共238页n更陡的斜线所示。由于这一较高的需求,在收进新的供应量之前,库存掉进了储备存货。倘若需求增长得更多或提前期变得更长,则库存可能降低到零──这就会产生缺货。这一技法有下列注意事项:1、订货量(诸EOQ)通常是固定的,而且仅当预期有显著的需求变化时才被重新计算。2、实际上,订货点在太多的情况下是固定的而且难得被核对。本章在后面将提出以每周或更长的间隔来更新订货点的技法,以保持它们同预期的需求或提前期的变化相协调。3、两次补货订货之间的间隔期不是常数,它随使用率而变:需求越高,订货间隔期短(因此得名为固定订货量──可变周期)。4、库存的储备存货部份通常被认为平均起来一年到头都是现有库存。5、库存的相当于满订货量的周期性存货部份只有在它刚刚被收进时才是现有库存。平均起来,只有订货量的一半将一年到头在库,因为假设使用率是均匀的。6、平均总库存的计划量等于订货量的一半加上储备存货。用目视法寻找订货点在一物品的平均需求是每周100件与预期的提前期为6周的情况下,通过察看过去的活动──如库存记录所示──可能发现由于提前期比预期的要长或需求比预期的要高而使提前期中的需求有时可高达800件。如果这样的查看表明提前期中的需求难得超过800件,则把订货点设在800件就可获得成功的服务。这在事实上已建立了200件的储备存货用来对付需求与提前期二者的变化。该订货点是两个要素之和:提前期中的预期需求与储备存货。前节所讨论的例中:订货点=600件+200件=800件虽然用查看法确定订货点是简单而吸引人的,但有一个主要的实际问题。为了通过观察来确定订货点必须有大量的数据;但在典型的商业情况中,数据越老,它们对当前情况的代表性就越差,对将来可能发生什么的代表性就更差。确定一个订货点要求对其两个构成因素提前期中的需求与储备存货量作出估计。一个期间的预期需求必须通过某种预测来确定,其技法已在第4章中讨论过。然后必须把这一需求量扩展到提前期上,提前期通常不同于预测期间。其技法在本章后面讨论。确定恰当的储备存货是一个困难问题,并无容易的解法。应用经验法则将造成许多物品的库存过多而另一些物品库存不足。更为严格的方法也最多只能稍微减少这些过多或不足。所要求的储备存货量是主要由下列要素构成的一个函数:1、准确地预测需求的能力2、提前期的长度3、准确地预测或控制提前期的能力4、订货量的大小5、所希望的服务水平某些统计技法──以不受清规戒律拘束的实用观点与方法去应用时──可以相当有效地用于实际去确定有用的储备存货。本章下面几节讨论的方法在工业中有着广泛的应用并对专业经理是有帮助的。原理16.由于不确定性不能被消除,订货点法要求有储备存货。238第238页共238页n预测误差的估计图5-2所示为2个物品,物品T与物品V的10周销售史。物品T的数据表明,虽然预测每周1000件,而且平均销售量1020非常接近预测值,但实际销售量曾高达1400,而且另有二周是1200。物品T合理的订货点将是1200件,预期当一周的补货期中的需求超过1200时将有时出现缺货。该订货点构成如下:订货点=提前期中的预期需求+储备存货(5-1)=1000+200=1200如果不允许缺货,则订货点将必须设在1400以上。当然,不能保证在未来销售量有时不会大大超过1400──因为一个10周的销售史是相当小的一个样本。┏━━━━┳━━━━━━━┳━━━━━━━┓┃第几周┃物品T┃物品V┃┣━━━━╋━━━━━━━╋━━━━━━━┫┃1┃1200┃400┃┣━━━━╋━━━━━━━╋━━━━━━━┫┃2┃1000┃600┃┣━━━━╋━━━━━━━╋━━━━━━━┫┃3┃800┃1600┃┣━━━━╋━━━━━━━╋━━━━━━━┫┃4┃900┃1200┃┣━━━━╋━━━━━━━╋━━━━━━━┫┃5┃1400┃200┃┣━━━━╋━━━━━━━╋━━━━━━━┫┃6┃1200┃1000┃┣━━━━╋━━━━━━━╋━━━━━━━┫┃7┃1100┃1500┃┣━━━━╋━━━━━━━╋━━━━━━━┫┃8┃700┃800┃┣━━━━╋━━━━━━━╋━━━━━━━┫┃9┃1000┃1400┃┣━━━━╋━━━━━━━╋━━━━━━━┫┃10┃900┃1100┃┣━━━━╋━━━━━━━╋━━━━━━━┫┃总计┃10,200┃9800┃┣━━━━┻━━━━━━━┻━━━━━━━┫┃1、两物品的每周预测均为1000件┃┃2、订货量为1000件┃┃3、提前期为一周┃┗━━━━━━━━━━━━━━━━━━━━┛图5-210周的销售史238第238页共238页n物品V表现出更为不规则的需求;事实上,如果物品V的订货点设在1200,则将发生三次缺货,因为有三周提前期中的需求超过了订货点。这种情况在工业中是常见的;对于低量物品或当订货的客户较少时,通常其需求的变动性较大。许多公司,除了直接把产品卖给消费者之外,还要以稍有不同的配置为邮购商店或其它大分销商供货。他们通常发现直接卖给许多客户的物品具有更为可预报的模式,而较少的大量需求趋向于小得多的可预报性。为了保持同样的服务水平,物品V的订货点将显然要比物品T高许多。这两种物品倘若采用相等的储备存货将使物品T持有过多库存或使物品V给出较差的服务。可用信息的小样本也带来严重的问题,因为没有保证物品V的销售量有时不会高达2200件或物品T不可能有高达1900件的销售量。因此,在订货点概念的实际应用中需有某种相当可靠而始终一贯的方法根据小样本数据来确定储备存货。对于许多物品,处理这种计算的一个非常有用的概念是正态分布。正态分布是最著名的统计关系之一──大多数人都熟悉钟形曲线。计算订货点时,对正态分布的两个特征有兴趣:1、中值或平均值它相当于钟形曲线的最高点,它是最可能发生的值。2、标准偏差,它度量值围绕平均值的变化或分散。这相当于钟形曲线的宽度,它度量这些个别值如何紧紧地围绕平均值而分布。要应用正态分布必须满足下列条件:1、需求数据是单峰的这只是说该需求趋向于分布在一个平均值的周围。如果需求可能接近每周500件或约每周1500件但不大可能取二者中间的任何值,则该需求将具有两种最频繁地出现过的状态,正态分布将不能恰当地描述为样的需求数据。2、假设该需求数据的分布是对称的换句话说,该分布中需求小于预测200件与大于预测200件的可能性是刚好一样的。这一假设在计算订货点时有一些实际问题。例如,倘若预测的需求是每周20件,它不可能少于零,然而可能多达100件或150件。换句话说,平均值离地板很近,而离天花板很远。有两种办法来处理这一问题:a、当预测值如此之低,以致正的变差将比负的变差大得多时,可忽略所有负的变差,而在标准偏差或平均绝对偏差的计算中则包括正的变差。b、对小量需求的某些类型,另一特殊的叫做泊桑分布的统计分布往往给出好的结果。详见本章后面。3、使用正态分布时,假设实际平均值将等于预测的平均值(即假设预测是准确的)。最好的保险是使用一种技法,例如使用指数平滑法,定期地去更新预测并使用一跟踪信号去指示何时此预测正在工作得不能令人满意,详见本章后面。图5-4所示为图5-2中物品T的预测误差的标准偏差的计算┏━━━━━━━━━━━━━━━━━━━━━━━━━━━━━━━━━━━┓┃物品T┃┣━━━┳━━━━━━┳━━━━━━━┳━━━━━┳━━━━━━━━━━┫┃第几周┃预测┃销售量┃偏差D┃D2┃┣━━━╋━━━━━━╋━━━━━━━╋━━━━━╋━━━━━━━━━━┫┃1┃1000┃1200┃-200┃40,000┃┣━━━╋━━━━━━╋━━━━━━━╋━━━━━╋━━━━━━━━━━┫238第238页共238页n┃2┃1000┃1000┃-----┃-----┃┣━━━╋━━━━━━╋━━━━━━━╋━━━━━╋━━━━━━━━━━┫┃3┃1000┃800┃200┃40,000┃┣━━━╋━━━━━━╋━━━━━━━╋━━━━━╋━━━━━━━━━━┫┃4┃1000┃900┃100┃10,000┃┣━━━╋━━━━━━╋━━━━━━━╋━━━━━╋━━━━━━━━━━┫┃5┃1000┃1400┃-400┃160,000┃┣━━━╋━━━━━━╋━━━━━━━╋━━━━━╋━━━━━━━━━━┫┃6┃1000┃1200┃-200┃40,000┃┣━━━╋━━━━━━╋━━━━━━━╋━━━━━╋━━━━━━━━━━┫┃7┃1000┃1100┃-100┃10,000┃┣━━━╋━━━━━━╋━━━━━━━╋━━━━━╋━━━━━━━━━━┫┃8┃1000┃700┃300┃90,000┃┣━━━╋━━━━━━╋━━━━━━━╋━━━━━╋━━━━━━━━━━┫┃9┃1000┃1000┃-----┃-----┃┣━━━╋━━━━━━╋━━━━━━━╋━━━━━╋━━━━━━━━━━┫┃10┃1000┃900┃100┃10,000┃┣━━━╋━━━━━━╋━━━━━━━╋━━━━━╋━━━━━━━━━━┫┃总计┃10,000┃10,200┃1600*┃400,000┃┣━━━┻━━━━━━┻━━━━━━━┻━━━━━┻━━━━━━━━━━┫┃D2的均值=400,000÷10=40,000*忽视正负号┃┃────┃┃σ=√40,000=200=标准偏差┃┃另一种方法:┃┃平均绝对偏差(MAD)=D的均值=1600÷10=160┃┃σ=MAD×1.25=160×1.25=200┃┗━━━━━━━━━━━━━━━━━━━━━━━━━━━━━━━━━━━图5-4标准偏差的计算计算预测误差的标准偏差要使用下列步骤:1、从预测值减去每周的实际销售量得出偏差值2、将偏差值平方3、对偏差的平方求和4、确定偏差平方的均值5、将偏差平方的均值开方,就得出标准偏差标准偏差的精确计算要求将偏差平方的和数除以(n-1),其中n是观察的次数。本章为了简化,用n代替了(n-1)。详见任何统计学教科书。当需求量小于平均值时,实际工作者在设置订货点时并不关心提前期间。只有当需求大于平均值时,才需有后备存货来满足这些期间。如果预测相当准确而且经常得到更新,长期看来约有50%的时间需求将小于平均值,而且实际工作者可以期望不用后备来给出50%的服务。如果他在预测的平均值1000之外再加一个标准偏差或200件的后备存货(使订货点为1200件),该实际工作者将在补货期间有足够库存去满足另外34%的需求(1个标准偏差=34%的事件);因此他可以期望以一个含有一个标准偏差后备存货的订货点去给出84%(50%+238第238页共238页n34%)的服务。订货点为1200件时,该实际工作者从长远看约有十分之二的机会在补货期间遇到缺货。看看图5-4中物品T的销售量,这一结果看来并非太不合理的。如果在提前期间的平均需求1000件之上再加两个标准偏差或400件,该订货点变成1400件。该第二个标准偏差将满足另外14%的事件,给出总计约为98%(84%+14%)的服务。订货点为1400件,提前期中需求超过1400件的机会将只有百分之二。从物品T的数据看,这看来也是合理的。标准偏差虽然在库存控制中是个很有用的度量,但它包含许多计算,有些麻烦。如图5-4中所示,它可用更简的方法通过MAD来确定。MAD是预测值与实际销售量之间差异(绝对偏差)的平均值。MAD与标准偏差的近似关系是σ=1.25×MAD(5-2)图5-4说明用此法计算标准偏差时要先求出MAD等于160。虽然此法不能永远得出如此接近于直接计算法的结果,通常它对于大多数实际的库存控制应用还是足够接近的。使用MAD可省去许多计算。此外,MAD有助于定期地更新,这对良好的库存控制是不可缺少的;这一技法将在本章后面叙述。MAD也指出如果没有安全库存,缺货将有多大平均数,并显示下一预测期间的预期误差。图5-5说明计算物品V的MAD的方法。物品V的需求变化比物品T的显然要大。这里MAD是380,标准偏差是475,比物品T的增1倍还多。对物品V,具有98%服务订货点可构筑如下:物品V第几周预测销售偏差───────────────────────────1100040060021000600400310001600-600410001200-20051000200800610001000---710001500-50081000800200910001400-4001010001100-100──────────总计98003800*MAD=3800÷10=380*忽视正负号σ=380×1.25=475───────────────────────────图5-5用MAD计算σ订货点=提前期中预期需求+后备存货提前期中预期需求=1000件相当于98%服务的后备存货=2σ=2×475=950件100次中约2次缺货,需求有可能超过一周1950件,根据可用数据是小238第238页共238页n样本,看来是合理的。为了计算后备存货,使用MAD是一种实用的技法,它可以按每一个别物品的特征来量体裁衣。这样算得的后备存货对具有较大的需求变动性的物品将较大,而对具有较稳定需求的物品将较小。这一技法假设实际的平均需求等于预测的需求,这不一定永远成立的。可用图5-6来说明这一问题,图中物品W的预测是每周1000件,平均绝对偏差为160件(与图5-4中物品T相同)。但物品W的销售量在大多数时间里超过了预测,指示预测应当增加到大约1100件。这将降低偏离量,从而使库存中必须持有的后备存货降低。┏━━━━━━━━━━━━━━━━━━━━━━━━━━━━━━━━┓┃物品W┃┣━━━┳━━━━┳━━━━━━━┳━━━━┳━━━━━━━━━━┫┃第几周┃预测┃销售┃偏差┃预测误差的代数和RSFE┃┣━━━╋━━━━╋━━━━━━━╋━━━━╋━━━━━━━━━━┫┃1┃1000┃1200┃-200┃-200┃┣━━━╋━━━━╋━━━━━━━╋━━━━╋━━━━━━━━━━┫┃2┃1000┃1000┃----┃-200┃┣━━━╋━━━━╋━━━━━━━╋━━━━╋━━━━━━━━━━┫┃3┃1000┃1200┃-200┃-400┃┣━━━╋━━━━╋━━━━━━━╋━━━━╋━━━━━━━━━━┫┃4┃1000┃900┃+100┃-300┃┣━━━╋━━━━╋━━━━━━━╋━━━━╋━━━━━━━━━━┫┃5┃1000┃1400┃-400┃-700┃┣━━━╋━━━━╋━━━━━━━╋━━━━╋━━━━━━━━━━┫┃6┃1000┃1200┃-200┃-900┃┣━━━╋━━━━╋━━━━━━━╋━━━━╋━━━━━━━━━━┫┃7┃1000┃1100┃-100┃-1000┃┣━━━╋━━━━╋━━━━━━━╋━━━━╋━━━━━━━━━━┫┃8┃1000┃1300┃-300┃-1300┃┣━━━╋━━━━╋━━━━━━━╋━━━━╋━━━━━━━━━━┫┃9┃1000┃1000┃----┃-1300┃┣━━━╋━━━━╋━━━━━━━╋━━━━╋━━━━━━━━━━┫┃10┃1000┃900┃+100┃-1200┃┣━━━╋━━━━╋━━━━━━━╋━━━━╋━━━━━━━━━━┫┃┃总计┃11,200┃1600┃┃┣━━━┻━━━━┻━━━━━━━┻━━━━┻━━━━━━━━━━┫┃MAD=1600÷10=160┃┃跟踪信号=RSFE÷MAD┃┃=1200÷160┃┃=7.5┃┗━━━━━━━━━━━━━━━━━━━━━━━━━━━━━━━━┛图5-6跟踪信号的确定238第238页共238页n只看物品W的预测值与MAD,会认为其需求特征与物品T是相同的,但可以计算出一个跟踪信号,它将立即揭露出事实上预测误差正在分布的一侧积累着。在这一特例中,预测在大多数周是低于实际的。对预测误差求代数和(叫RunningSumofForecastError,简写为RSFE),然后除以MAD就可得出实际值与预测值之间一贯性差值的一种度量,叫做跟踪信号。图中根据10周的数据,可以算出物品W的跟踪信号是7.5,它很高,指示销售始终超过了预测。在一实际的库存系统中,该预测将被指数平滑法更新,其结果是该跟踪信号将度量这一不断地被更新着的预测的有效度。在本例中为了避免过多的计算使用的是固定的预测1000件。倘若预测误差趋向于互相抵消(如在物品T的例子中),跟踪信号将保持低值,表明预测相当成功,不需修改。跟踪信号可接收的最大值在4与8之间,取决于该信号是如何使用的。对一高价物品,可用4为跟踪信号的最大值以及早触发预测的修改,从而避免由于等待过久而持有过多库存或危害服务。对于一低值物品,可用相当高的跟踪信号(也许用7或8),因为低值物品的预测误差可以较高而且大多数公司对较不通用的物品较少强调要保持良好的服务。第4章中也讲到过跟踪信号的使用。第4章中指数平滑法预测公式中的加权因子是对趋势反应太慢与对随机事件反应过头之间的折衷;跟踪信号也属这类工具。跟踪信号定得太低,会为了抓住少数不成功的预测而去要求评审系统为之工作得成功的许多物品。跟踪信号定得太高则可能拖延评审从而引起不良的服务或库存过多。然而,有一个跟踪信号在起作用确实提供一种例外技法用来指出某一特定预测需要评审,所以它应是每一完整系统的一部份。理想地,它将召唤人们注意人们能够在一次有效的评审中把握的物品数。订货点的计算知道了正态分布的一般统计性质并已算出了预测误差的标准偏差或平均绝对偏差MAD,订货点的计算就简单了。本章前面讨论过在提前期中预期需求之上加一个标准偏差是以给出84%的服务为目标,加2个标准偏差则将服务水平提高到98%。服务水平直接地同作为后备或安全存货的标准偏差数有关;这一数目通常称为安全因子。图5-7是正态分布下不同服务水平的安全因子表,安全因子可用标准偏差数或MAD数表示。由于MAD总是小于标准偏差,所以所用的MAD数总比所要的标准偏差数要多些。例如服务水平为84.13%时,安全存货要用1个标准偏差或1.25个MAD。┏━━━━━━━━━━━━━┳━━━━━━━━━━━━━┓┃服务水平(%)┃安全因子用:┃┃┃标准偏差平均绝对偏差┃┣━━━━━━━━━━━━━╋━━━━━━━━━━━━━┫┃50.00┃0.000.00┃┃75.00┃0.670.84┃┃80.00┃0.841.05┃┃84.13┃1.001.25┃┃85.00┃1.041.30┃238第238页共238页n┃89.44┃1.251.56┃┃90.00┃1.281.60┃┃93.32┃1.501.88┃┃94.00┃1.561.95┃┃94.52┃1.602.00┃┃95.00┃1.652.06┃┃96.00┃1.752.19┃┃97.00┃1.882.35┃┃97.72┃2.002.50┃┃98.00┃2.052.56┃┃98.61┃2.202.75┃┃99.00┃2.332.91┃┃99.18┃2.403.00┃┃99.38┃2.503.13┃┃99.50┃2.573.20┃┃99.60┃2.653.31┃┃99.70┃2.753.44┃┃99.80┃2.883.60┃┃99.86┃3.003.75┃┃99.90┃3.093.85┃┃99.93┃3.204.00┃┃99.99┃4.005.00┃┗━━━━━━━━━━━━━┻━━━━━━━━━━━━━┛图5-7正态分布下的安全因子表此表可用来计算各种服务水平的安全存货。例如假设物品X的数据如下:每周预测=500件提前期=1周MAD=200件希望的服务=98%订货量=500件由于此物品的每周需求是500件,而提前期是一周,则提前期中的需求就是500件。MAD是200件。如果希望达到98%的服务水平,图5-7指出安全因子应为2.56个MAD。故后备存货=安全因子×MAD=2.56×200=512件而订货点=提前期中的需求+后备存货=500+512=1012件这个订货点(据表)应给出98%的服务水平──但在此项计算中“服务”的意思是什么?它的意思是在补货期间的百分之多少的时间内需求不应超过订货点量。订货点是设计得用来复盖提前期中的需求,从而该物料的一份补货订单可以及时发出使得该物料在全部存货被提取完毕之前交货到存贮之中。此补货提前期的终点是一物品可能用完到缺货的关键时刻。一物品可能缺货的“曝光”次数就等于发出补238第238页共238页n货订单的次数,当然它要取决于订货量的大小。订货量较大的物品将要求较少的每年补货订单数,因而比更加频繁地订货的物品要较少地曝光于缺货。订货量与安全存货之间的这一关系可通过先确定将发生的补货期间数(曝光到缺货的次数),然后计算以不希望发生缺货的补货期间数来表示的所希望的服务水平的办法来考虑进去。可用物品X的数据来说明这种计算。此物品的周预测是500件,提前期为1周,MAD是200件,所希望的服务水平是98%。如果此服务水平用每年缺货1次来表示(由于1/52=1.9%,它粗略地相当于98%的服务水平),而且如果订货量是2600件,则:年需求量=500×52=26,000件/年每年曝光次数=26,000/2600=10个补货期间要求的服务水平是缺货1次=9/10或90%安全因子=1.60×MAD(从图5-7,服务水平90%时)订货点=500+(1.60×200)=500+320=820这一订货点比上次为物品X计算的订货量为500件时的订货点要低得多。因为500件的订货量要有52次曝光于缺货,98%的服务水平要求有2.56×MAD的安全存货,订货点将为1012件=500+2.56×200。由于订货量、曝光次数与后备存货货之间的相互作用,订货点与EOQ的简单、独立算法并不一定给出最经济的总库存水平。进一步的计算往往将揭示增加订货量将减少曝光对任一给定服务水平所要求的总库存,因为它将减少次数,从而减少了所要求的后备存货。在某些情况下,后备存货的减少量将大于所要求的批量的增量。这一关系将在附录Ⅳ中用例子说明。对价值最高的A类物品,这一统计技法的精益求精可能是非常值得的,但对大多数物品这是不得的;所得的节约比起所化的力气来将是太小了。预测间隔与提前期差别的调整在实践中计算统计的后备存货时常遇的另一问题是预测间隔不同于提前期间。通常库存中包含的许多物品具有差别很大的提前时间,为了确定这些不同物品在提前期中需求的变化并计算后备存货必须去测定它们在各各不同的提前期上的预测误差,这将是非常不方便的。必须使用某种其它方法去调整预测误差以补偿不同的提前时间。如果物品X的提前期为4周,则提前期中的需求将为4×500=2000件。期望需求大大超过平均值的机会很可能超过一周是合理的,所以有必要增加原先以一周的需求为基础的后备库存以便为现在较长的提前期提供等效的保护水平。另一方面,显然也不宜把适用于1周提前期的后备存货乘以4来确定4周提前期所需的后备存货;因为需求不大可能;连续4周保持很高。显然后备存货必须随着提前期的变长而有所增加,但增量不一定直接正比于提前期的增量。当预测间隔不同于提前时间间隔时,需有某种调整因子,实践中时常就是这样做的。┏━━━━━━━━━━━┳━━━━━━━━━━┓┃当预测间隔=1┃标准偏差或平均┃┃而提前期间隔为:┃绝对编差应乘以*:┃┣━━━━━━━━━━━╋━━━━━━━━━━┫238第238页共238页n┃2┃1.63┃┃3┃2.16┃┃4┃2.64┃┃5┃3.09┃┃6┃3.51┃┃7┃3.91┃┃8┃4.29┃┃9┃4.66┃┃10┃5.01┃┃11┃5.36┃┃12┃5.69┃┃13┃6.02┃┃14┃6.34┃┃15┃6.66┃┃16┃6.96┃┃17┃7.27┃┃18┃7.56┃┃19┃7.86┃┃20┃8.14┃┃┃┃┗━━━━━━━━━━━┻━━━━━━━━━━┛*假设β=0.7图5-9提前时间不等于预测间隔时使用的调整因子表图5-9给出一张提前期不等于预测间隔时调整MAD用的因子表。此表为较长的提前期间隔确定一等效的偏差提供一调整因子,用此调整因子乘上预测间隔的MAD,可用来计算后备存货。确定这些因子的公式是:调整后的MAD=MAD(LT/F)β(5-3)其中调整后的MAD=提前期间隔的MADMAD=预测间隔的MADLT=提前期间隔F=预测间隔β=取决于具体行业的需求模式的一个常数理论上β值应通过使用该公司实际数据的仿真来确定。实践中发现β取0.7可以给出相当好的结果。事实上,为了拟合公司的实际需求模式,需作大量仿真工作才能确定一更准确的β值。图5-9中的乘数是根据β=0.7算出的,其用法如下:1、将提前期间隔表达为预测间隔的倍数2、按此倍数查表中第一列238第238页共238页n3、将预测间隔的MAD乘上第二列中相应的调整因子,使它转换成提前期间隔的MAD使用图5-9与物品X的数据,可计算订货点如下:1、设物品X的提前时间是4周(预测间隔1周的4倍)2、倍数为4时,查表知调整因子为2.643、提前时间为1周时的MAD是200件调整后的MAD=2.64×200=528件所求后备存货=1.60×528=845件(订货量=2600件,每年允许缺货一次,安全因子为1.60)订货点=(4×500)+845=2845件对大多数物品,这种近似法已足够准确。然而,对高价物品,用此表算出的结果应再用仿真加以核对,以确定一更精确的调整因子或应在提前期间隔上直接计算出预测误差。物料经理必须找到常规地更新提前期中预测的需求与重新计算所需后备存货的手段。图5-10所示为物品X13周的实际需求。第4章讲过的指数平滑法提供这样一种常规地更新预测的方法;图5-11表示每周使用这种技法与图5-10中的数据来作一次新预测。在这里,开始的预测是每周500件,而指数平滑法计算使此预测先是有所下降然后在第6周上升到526件。图5-10表明13周的平均需求为600件,而指数平滑计算,虽然滞后了,但比原来预测的数字每周500件要好些。这表明该技法对校正一显然太低的预测从而使它更符合于实际销售是有用的。┏━━━━━━━━━━━━━━━━━━━━━━━━┓┃预测的周需求=500件┃┣━━━━━━━━━━━┳━━━━━━━━━━━━┫┃第几周┃实际需求┃┣━━━━━━━━━━━╋━━━━━━━━━━━━┫┃1┃464┃┃2┃330┃┃3┃474┃┃4┃847┃┃5┃618┃┃6┃772┃┃7┃573┃┃8┃432┃┃9┃938┃┃10┃642┃┃11┃750┃┃12┃294┃┃13┃672┃┣━━━━━━━━━━━┻━━━━━━━━━━━━┫┃7806┃┣━━━━━━━━━━━━━━━━━━━━━━━━┫┃平均周需求=600┃238第238页共238页n┗━━━━━━━━━━━━━━━━━━━━━━━━┛图5-10物品X13周的需求史┏━━━━━━━━━━━━━━━━━━━━━━━━━━━━━━━━━┓┃新预测=α×实际需求+(1-α)×老预测┃┃其中:α=0.1,(1-α)=0.9┃┣━━━┳━━━┳━━━━━━━┳━━━━┳━━━━━━┳━━━━━┫┃第几周┃老预测┃(1-α)×老预测┃实际需求┃α×实际需求┃新预测┃┣━━━╋━━━╋━━━━━━━╋━━━━╋━━━━━━╋━━━━━┫┃1┃500┃450.0┃464┃46.4┃496┃┣━━━╋━━━╋━━━━━━━╋━━━━╋━━━━━━╋━━━━━┫┃2┃496┃446.4┃330┃33.0┃479┃┣━━━╋━━━╋━━━━━━━╋━━━━╋━━━━━━╋━━━━━┫┃3┃479┃431.1┃474┃47.4┃479┃┣━━━╋━━━╋━━━━━━━╋━━━━╋━━━━━━╋━━━━━┫┃4┃479┃431.1┃874┃84.7┃516┃┣━━━╋━━━╋━━━━━━━╋━━━━╋━━━━━━╋━━━━━┫┃5┃516┃464.4┃618┃61.8┃526┃┣━━━╋━━━╋━━━━━━━╋━━━━╋━━━━━━╋━━━━━┫┃6┃526┃473.4┃772┃77.2┃551┃┣━━━╋━━━╋━━━━━━━╋━━━━╋━━━━━━╋━━━━━┫┃7┃551┃495.9┃573┃57.3┃553┃┣━━━╋━━━╋━━━━━━━╋━━━━╋━━━━━━╋━━━━━┫┃8┃553┃497.7┃432┃43.2┃541┃┣━━━╋━━━╋━━━━━━━╋━━━━╋━━━━━━╋━━━━━┫┃9┃541┃486.9┃938┃93.8┃580┃┣━━━╋━━━╋━━━━━━━╋━━━━╋━━━━━━╋━━━━━┫┃10┃580┃522.0┃642┃64.2┃586┃┣━━━╋━━━╋━━━━━━━╋━━━━╋━━━━━━╋━━━━━┫┃11┃586┃527.4┃750┃75.0┃602┃┣━━━╋━━━╋━━━━━━━╋━━━━╋━━━━━━╋━━━━━┫┃12┃602┃541.8┃294┃29.4┃571┃┣━━━╋━━━╋━━━━━━━╋━━━━╋━━━━━━╋━━━━━┫┃13┃571┃513.9┃672┃67.2┃581┃┗━━━┻━━━┻━━━━━━━┻━━━━┻━━━━━━┻━━━━━┛图5-11使用指数平滑法的预测图5-12显示同一套用于计算MAD与更新MAD的情形。更新用的是指数平滑法,用MAD替代预测,并用偏差替代需求。在图5-12中,开始时MAD是200。使用指数平滑公式,老MAD乘上0.9,新偏差乘上0.1,而新MAD是二者之和,如图5-11一列所示。实践中,图5-11与图5-12中的计算将同时进行,而订货量可以每周计算一次。即使成千种物品,现代计算机也能容易地处理这些计算。238第238页共238页n┏━━━━━━━━━━━━━━━━━━━━━━━━━━━━━━━━━━━┓┃新MAD=α×偏差+(1-α)老MAD┃┃其中=0.1,(1-α)=0.9┃┣━━━┳━━━┳━━━┳━━━┳━━━━┳━━━┳━━━━━━┳━━━┫┃第几周┃预测┃销售┃偏差┃α×偏差┃老MAD┃(1-α)×MAD┃新MAD┃┣━━━╋━━━╋━━━╋━━━╋━━━━╋━━━╋━━━━━━╋━━━┫┃1┃500┃464┃56┃3.6┃200┃180.0┃184┃┣━━━╋━━━╋━━━╋━━━╋━━━━╋━━━╋━━━━━━╋━━━┫┃2┃496┃330┃166┃16.6┃184┃165.6┃182┃┣━━━╋━━━╋━━━╋━━━╋━━━━╋━━━╋━━━━━━╋━━━┫┃3┃479┃474┃5┃0.5┃182┃163.8┃164┃┣━━━╋━━━╋━━━╋━━━╋━━━━╋━━━╋━━━━━━╋━━━┫┃4┃479┃847┃368┃36.8┃164┃147.6┃184┃┣━━━╋━━━╋━━━╋━━━╋━━━━╋━━━╋━━━━━━╋━━━┫┃5┃516┃618┃102┃10.2┃184┃165.6┃176┃┣━━━╋━━━╋━━━╋━━━╋━━━━╋━━━╋━━━━━━╋━━━┫┃6┃526┃等等┃┃┃┃┃┃┗━━━┻━━━┻━━━┻━━━┻━━━━┻━━━┻━━━━━━┻━━━┛图5-12预测的偏差与MAD使用本章所讲技法来计算订货点的全部过程如下:1、确定每年允许的缺货次数(在收到订货量之前存货可能被用完的补货期间)。这是一项管理决策,而不是计算。2、把年度需求预测量除以订货量,算出每年要发出补货订单(或曝光)的次数。3、计算出服务率,表达为一个百分数。这是不希望发生缺货的补货期间数(总曝光次数减去允许缺货次数)与补货期间总数之比。4、使用这个百分数去找出(从图5-7中)安全因子──即必须包括在后备存货中的偏差个数(标准偏差或MAD)。5、如图5-4或5-5所示地计算出标准偏差或MAD。6、使用图5-9中的表,计算出调整后的偏差(标准偏差或MAD)去对付预测间隔与提前期间隔之间的任何差异。7、将调整后的偏差乘以安全因子,计算出所需的总后备存货。8、把这一后备存货加到提前期提预测需求(DLT)之上,得出总的订货点。下面是使用物品X的数据的一例:年需求=26,000件订货量=500件提前期=4周MAD=200件则:1、每年允许缺货次数=1(由管理者决定)2、每年曝光次数=26,000÷500=523、服务率=(52-1)÷52=98%4、从图5-7,安全因子=2.56(用MAD)238第238页共238页n5、MAD=200件6、调整后的MAD=2.64×200=528件7、后备存货=2.56×528=1350件8、订货点=DLT+后备=(4×500)+1350=3350件这里讨论的技法提供可以频繁到每周一次地来生成修订后的订货点的简单方法。这些方法在工业中已有相当大的应用而且已被证明是成功的。好处不仅来自测定预测误差并实际地确定后备存货应有多大,也来自有了一种为成千种物品常规地预测其需求以及在例行的基础上同时更新预测与对预测误差的估计这二者的手段。这些统计技法必须以充分理解其基本假设与了解它们的局限性为基础谨慎地去使用。一切统计技法假设未来将像过去那样。幸运的是,在大多数情况下对最近的将来这是一个相当有效的假设,但将毕竟总归是有变化的。使用类似指数平滑法、预测跟踪信号并定期地更新预测误差的度量能够有助于迅速地找出这些变化并作出适当的校正。在前面的计算中为了简单起见,只计算了预测误差,而且曾经假设使用一个不变的提前时间──通常就是平均已计划提前时间。提前时间的变差不可直接同需求的变差相加,因为最长的提前时间不大可能与最大的需求同时发生。应注意避免改变已计划提前时间,除非是在受控条件下应用投入/出产控制法去减少在制品时。第2册第5章叙述由于对已计划提前时间修修补补而引起恶性循环的问题。即使在具有某些许可的应用场合,统计学的技法也有巨大的价值。像一切其它的所谓科学的工具一样,正态分布应当带着判断来使用。如果其答案无意义,则该项计算应请统计学方面内行的人(例如质量控制经理)予以重新审查,并在应用之前由实际工作者核对其合理性。这类概念只是试图用数学语言描述发生在商业中的实际事件。实际工作者务必理解它们的局限性与含义,这比他懂得用来推导它们的所有的数学与统计学的理论要更为重要。原理17.只有在统计学技法的假设是有效的场合并且在经过测试之后,才应用统计学技法去设定后备存货。泊桑分布的使用对某些需求类型,使用泊桑分布去计算订货点是方便的,因为它具有其标准偏差永远等于其均值的平方根这一性质。泊桑分布的主要应用是在质量控制上与涉及顾客在超级市场的收银机前或汽车在高速公路收税站前的随机到达问题的研究之中。虽然它已为实际工作者所熟知有多年了,但泊桑分布在库存控制中并未获得广泛应用(11)。它最适用于小量、不经常的需求,每一订单的物品数量相当稳定的场合,这是某些低产量产品与修理用零件的典型情况。要恰当地使用于订货点的计算,其需求史必须表达为收到的订单数以及每份订单的物品数。例如,一物品在提前期中的需求可能平均为4000件;要使用泊桑分布,必须进一步考察这4000件的需求以确定它确实是由40份每份100件的订单所构成。使用泊桑分布来计算订货点的公式如下:OP(订货点)=u(a+f√a)(5-4)其中,OP=用件数表示的订货点u=每份订单的平均需求件数a=在提前期中到达的平均订单数238第238页共238页nf=服务因子(类似但并不等于正态分布中所用的标准偏差的个数)使用上面的数据,此物品的订货点可计算如下:OP=100(40+2.1√40)=100(40+13.28)=4000+1328=5328服务因子2.1是从图5-13中选用的,图中给出了使用泊桑分布时相应服务水平的服务因子应取的值。泊桑分布取服务因子2.1将给出98%的服务率。这一计算表明要这一特定物品给出98%的服务率,需要有1328件后备存货。┏━━━━━┳━━━━━━┳━━━┓┃要满足的需┃允许的欠交┃f┃┃求的最小%┃订单的最大%┃┃┣━━━━━╋━━━━━━╋━━━┫┃75┃25┃0.7┃┣━━━━━╋━━━━━━╋━━━┫┃80┃20┃0.8┃┣━━━━━╋━━━━━━╋━━━┫┃85┃15┃1.0┃┣━━━━━╋━━━━━━╋━━━┫┃90┃10┃1.3┃┣━━━━━╋━━━━━━╋━━━┫┃95┃5┃1.7┃┣━━━━━╋━━━━━━╋━━━┫┃98┃2┃2.1┃┣━━━━━╋━━━━━━╋━━━┫┃99┃1┃2.3┃┣━━━━━╋━━━━━━╋━━━┫┃99.9┃0.10┃3.1┃┗━━━━━┻━━━━━━┻━━━┛图5-13泊桑分布的服务因子f如果另一物品在提前期中也有4000件需求,但此物品是卖给少数分销商的,他们大量订货但并不经常,答案就将大不相同。如果他们一份订单的平均订货量是1000件,而在提前期中只收到4份订单,计算将是:OP=1000(4+2.1√4)=4000+4200=8200对这一更为飘忽不定的需求,将要求有4200件后备存货才能达到98%的服务率。许多作者推荐使用泊桑分布来计算订货点。重要的是要记住:泊桑分布不能被用来描述提前期中需求的总件数。它可以用来近似地表示提前期中将收到的个别订单的份数。使用泊桑分布时所得结果的准确性直接取决于这些订单所涉及的该物品的平均订货量能被确定到多大准确度。使用泊桑分布去计算订货点时必须记住的限制性假设如下:238第238页共238页n1、订单的到达必须符合泊桑频率分布曲线。当每一提前期间的到达数相对地小时,通常就符合得更好些。2、订单的到达是随机而独立的。当客户订单要经销售办公室过滤时,他把同类物品的订单累积一段时间然后成批地发放它们,这一条就不成立了。3、对平均订货量要能作出准确的预测。预测中的误差将在订货点与后备存货中引起相应的误差。4、订货量不得与平均值有很大差异。要作一些研究以确定可以容许的变差有多大,但已知变差大时结果是不好的。5、最后,要记住一切这类统计学方法的基本假设──未来将类似于过去。正确使用时,计算订货点的泊桑公式有两个明显的优点:1、它给出前后一贯的有用的结果,远比某些常用的经验法则要优越,诸如设定后备存货为1个月的供应量或提前期中需求的10%之类。2、它不要求准备与分析大量统计数据。更为精确的订货点计算方法将给出更为准确的结果,但将要求昂贵与详细的数据分析。服务的概念前面讨论中所使用的服务的度量──每年缺货一次──是一个统计学上处理起来相当简单而且容易联系实际商业情况的度量。如果由于订货量是1周的供应量故每年要交货52次,则每年一次缺货的服务水平将要求交货率为51/52或98%。如果订货量是4周的供应量,每年曝光于缺货的次数是13次,则每年缺货一次的服务水平将要求交货率为12/13或92%。这不过是用统计学语言来表达这一明显的事实,即收货越频繁而且库存越是频繁地消耗到后备水平,则缺货的机会也越大。这一服务的度量如何使用于实践之中?每年的缺货次数并不度量缺货量也不度量缺货的持续时间,然而,这一度量满有意义而且可以成为很有用的。如果一个包括相当大数量个别物品的产品组被每周核查并计数缺货的物品数,该结果可被相当好地同每年的缺货次数这一统计概念联系起来。如果,例如,此产品组中有120种物品,而且服务的目标水平是每物品每年一次缺货,则每月平均总缺货次数不应超过10种物品。这提供去证实安全存货是足够的或要求更好的作业控制的一种简便方法。另一常用的客户服务的统计度量规定需求总件数将被货架上现有存货满足的一个百分比。例如,如果该年度总需求被期望达到26,000件,而希望欠交订货只限于1000件,则服务百分数就是25/26=96%。这一客户服务的度量通常必须设置得比使用每年缺货次数作服务──度量百分数时要高得多,以便提供足够的后备存货去生成相当的服务水平(3).以缺货次数或欠交件数为基础的服务度量并不度量缺货期的长短,它们也并未指出重要的客户正得到服务或有利可图的物品正在被发运。倘若要求这样的度量,可在计算安全存货时通过调整个别物品的服务百分数而得到。这样的度量也涉及跟踪实际绩效方面大得多的开支。在应用新的度量或改变客户服务的度量之前,应注意下列:1、仿真受控库存的实际作用以确定所建议的统计度量当前使用得如何。没有一种服务的统计度量能够完善地使它与实际完善地互相关联,为了在日常的库存情况下达到实际所要求的服务水平,永远应将统计的服务水平设置得稍高一些。这种仿真可用手工来做,但大多数实际应用将要求采用计算机。238第238页共238页n2、实际达到的服务水平通常略低于统计的服务水平。这是因为统计服务水平通常只度量一个特征,譬如欠交的总量或缺货次数;而其它特征(譬如缺货的持续时间)也对不良的客户服务起着作用。还有,理论上的基本假设在实践中往往被违反。3、使用所建议的统计服务水平,开始使用控制系统并在经验表明只需较少后备时就削减后备存货。4、一旦统计服务度量已经建立并运行起来,其实际威力可用来说明将一系列物品从一个服务水平改变到另一服务水平的经济性(详见第8章)。5、客户服务的统计度量只对付正常提前期上需求中的变差,它们并不考虑机器故障、罢工或质量问题等因素,而这些因素对补货提前期影响极大。反之,由于正常提前期通常是在服务的统计概念中被采用的,一位好的主管人往往能使他的部门表现得比统计量所指示的要好得多,因为该部门对客户需求的变化反应极快。该主管人控制提前期从而也控制了客户服务。统计量的价值虽然订货点的统计学计算在概念上是简单的,但它比直觉方法要费劲得多。这是否值得?回答是断然地值得,因为统计学技法实际地把后备库存分配到最需要的地方而不是将它平均地分配到全部库存中去。图5-14所示为根据经验法则分配后备库存的一例,例中对物品P.Y与Z的后备水平都设为1周的供应量,它们的平均周需求相等。物品P销售给许多客户,其销售史的标准偏差为261件。物品Y的预测平均需求与物品P相同,但它卖给少数客户,所以其需求更不稳定,它的标准偏差是551件。物品Z的周平均需求同物品P与Y一样,标准偏差同P一样,也是261件。它是低值物品而生产调整成本是高的,因此,其订货量大,等于6500件。所有物品都假设要有1周的补货提前期。┏━━━━━━━━━━━━━━━━━━━━━━━━━━━━━━┓┃经验法则=1周的供应量┃┣━━┳━━━━┳━━━┳━━━┳━━━┳━━━┳━━━┳━━┫┃物品┃周需求┃订货量┃标准偏┃1周储┃标准偏┃交货*┃缺货┃┃┃预测(件)┃(件)┃差(件)┃备(件)┃差个数┃服务率┃次数┃┣━━╋━━━━╋━━━╋━━━╋━━━╋━━━╋━━━╋━━┫┃P┃500┃500┃261┃500┃1.92┃97.2┃2┃┣━━╋━━━━╋━━━╋━━━╋━━━╋━━━╋━━━╋━━┫┃Y┃500┃500┃551┃500┃0.91┃81.9┃9┃┣━━╋━━━━╋━━━╋━━━╋━━━╋━━━╋━━━╋━━┫┃Z┃500┃6500┃261┃500┃1.91┃97.2┃0┃┣━━┻━━━━┻━━━┻━━━┻━━━┻━━━┻━━━┻━━┫┃总计150011┃┣━━━━━━━━━━━━━━━━━━━━━━━━━━━━━━┫┃每年缺货2次时要求统计后备┃┣━━┳━━━┳━━━━━━┳━━━━┳━━━┳━━━┳━━━┫┃物品┃每年订┃交货服务率┃标准偏*┃标准偏┃要求的┃缺货┃238第238页共238页n┃┃货次数┃┃差个数┃差(件)┃后备┃次数┃┣━━╋━━━╋━━━━━━╋━━━━╋━━━╋━━━╋━━━┫┃P┃52┃50/52=96%┃1.75┃261┃460┃2┃┣━━╋━━━╋━━━━━━╋━━━━╋━━━╋━━━╋━━━┫┃Y┃52┃50/52=96%┃1.75┃551┃965┃2┃┣━━╋━━━╋━━━━━━╋━━━━╋━━━╋━━━╋━━━┫┃Z┃4┃2/4=50%┃0┃261┃0┃2┃┣━━┻━━━┻━━━━━━┻━━━━┻━━━┻━━━┻━━━┫┃总计14256┃┗━━━━━━━━━━━━━━━━━━━━━━━━━━━━━━┛*取自图5-7安全因子表图5-14确定后备存货时统计量的价值如图5-14所示,所有物品都设1周的供应量作为后备存货水平将引起每年约11次缺货。为这些物品各自计算出统计的后备存货将使缺货次数降为每年6次,同时总后备量可降为1425件。每一物品的后备要求都与经验法则所设定的不同,这是因为:1、物品P的订货量很小,所以缺货曝光次数大(每年52次)。2、物品Y需较大的后备存货,因为其需求更不稳定。这一较大的变化导致较大的标准偏差。3、物品Z订货量为6500件;每年只有4次曝光于缺货。事实上,物品Z要保持每年缺货不超过2次无需在预期的需求之外再增加后备存货。统计法结果更佳是因为直觉技法不能考虑确定后备存货所要求考虑的全部因素。它们是:1、预测误差2、提前时间3、订货量4、所希望的服务水平此例说明虽然有困难而且开销大,采用统计方法去控制库存还是值得的。用这些技法更好地去分配后备存货,从而获得在不增加缺货次数的条件降低库存的1/3或更多、或者在不增库存的条件下减少缺货次数到原来的1/3这样的结果,并非罕见的事。对成千种物品应用统计技法进行计算所需现代计算机与软件程序都很容易弄到而且相当便宜。由于不能恰当地去应用它们而带来的过量库存与不良的客户服务,其代价要昂贵得多。原理18.用经验法则来设定后备存货不行,因为这些法则忽视了需要它们的理由。虽然统计订货技法能在公司的经营中产生相当大的进步,它们应该被谨慎地、具有常识地去应用。思想上要牢记库存的ABC分类法。高价物品应受到最紧密的注意。有时甚至把A类物品隔离为“顶A”(“TopA”)类物品,它将受到物料控制经理个人的经常注意。这些物品当然应该具有定期地使用统计技法把它计算出来的浮动的订货点;有时,采用更为精确的技法去得到这些库存控制中的最大节约也是值得的。另一方面,即便有计算机可用,可能也不使用统计技法去控制低价物品;因为有秩序地去应用较简单的技法就已经非常有效了。238第238页共238页n统计的概念不仅有助于实际工作者去降低库存,而且懂得这些概念可使他们更好地把握库存系统的日常作用。大多数物料控制人员经常面临的问题之一就是库存中必须持有的物品的品种数目日益增多。更好地了解库存的行为特征当然不会消除这一趋势,但更好地了解库存系统的作用有助于实际工作者去对付这种趋势。下面举一简单例子。在大多数企业中需求的特征之一就是较活跃的物品具有较稳定的需求,而较不活跃的物品具有变动不定的需求。存货记录通常表明,平均需求为每月10件的物品往往很少有哪个月份的需求会接近于10件──它很可能是0或30,虽年度需求量的平均值是每月10件。另一方面,如果需求为每月平均2000件,则很可能很少月份的需求会超过3000或──最多──4000件。对于大众喜爱的物品,需求很少会超过平均需求的两倍,而对于活动性低的物品,其需求可能时常达到平均需求的三至四倍。随着更多品种物品的加入库存,几乎总是需要提高总库存水平。不熟悉库存控制的人员不会立即理解这一点,因而时常提出这样的问题,如果我们去年每月出售1000件红色附件而今年我们仍将每月出售1000件,不过要分红、白、兰三种颜色,为什么你的库存必须增加呢?实际情况可能如下表中所示:─────────────────────────────库存提前期中的需求后备存货─────────────────────────────A.只存红色附件1000件300件B.红色附件160件100件白色附件420件200件兰色附件420件200件────────────────总计1000件500件─────────────────────────────在这一假设的例中,用三种产品替代一种产品要求增大后备存货才能提供同原来一样的服务水平,因为三种产品的需求量都较低,其结果是需求的变差性增大了。有一组作者(9)注意到如果一家公司增多分支仓库──库存分家的极好例子──则库存后备将随所包含的分配点数目的平方根而变。若一家公司使用300件后备存货,今若增设两个仓库(设它们平均分担需求的供应),则达到与原先同样服务水平所要求的后备是:1个分配点的后备后备(每一分配点)=───────────√分配点的数目300=─────=173√3增多产品大类中品种的数目也会加重批量大小的问题。倍增通过一个部门的品种数意味着或者要运用大于经济批量的批量或者要倍增生产调整小时数或者在这两种方案之间采取某种折衷。这就进一步强调缩短生产调整时间的必要,详见第二册(6)。这些是物料控制实际工作者每日面临的问题的典型例子。知道了库存的行为特238第238页共238页n征,这些实际工作者至少可以了解可能会发生什么问题,而他们如果在应用统计概念方面足够机灵的话,就可以向管理者提出每种情况下的有效替代方案。他们可以在知道所有的后果的情况下去作出决定,而不是在事后再去了解这些后果或者误认为库存的增加是由于物料控制不好引起的。对于任何类型的订货系统,要牢记最重要的一点是它应该管用。统计学能为实际工作者提供有用的工具,但其结果将取决于他们的良好的辨别力以及在应用这些工具中的判断力。详见第2册(6)。使用的注意事项第一次应用统计技法时,建议实际工作者在应用到整个大类产品之前先在一些样本物品上做试点以熟悉这种技法的概念及局限性。然后,实际工作者可能要在把它们应用到B类物品之前先扩展到计算全部A类物品的订货点。把它们应用到C类物品需要慎重──事实上,可能永远也不值得花这样大力气去弄低价库存物品。使用指数平滑法预测提前期中的需求并使用更新了的MAD去确定后备存货,这样定期地重新计算订货点是可行的。在工业中广泛地使用计算机为成千种物品每周地更新着订货点。计算机制造商与软件商提供有可立即被实际工作者使用的程序,让它们用这些技法去作试验并确定它们如何能应用于他们自己的公司。这些程序于是就可用来形成计算机应用程序的核心。这一办法把编计算机程序的工作,获得有用结果所需的时间以及所涉及的费用降低到最小限度。这些技法可以每周地应用,然而,并不是说它们就应该这样去使用;专业工作者最怕的是不加人工评审或控制地去应用一种机械的技法。除非一种技法的基本假设被人们理解,否则它不会被成功地应用。各种订货点技法的变体都假设:1、使用将是连续的而且希望在发生缺货之前立即补货2、以相当均匀的速率实际地使用3、提前交货是允许的但延迟交货是不允许的因而应尽可能地避免4、安全存货将对缺货提供足够的保护5、能力与物料将足以用来处理已发放的订单定期评审技法另一主要的库存控制工具是定期评审技法,它往往被称为固定周期技法。此法中,库存记录被定期地评审而且每次评审时为每种物品办理补货订单。评审周期可以是1周、2周或1个月,看情况而定。订货时,把存货提高到使现有总量或已订货总量达到一预定的目标水平。这一技法应当同传统的订货点法作对比。在传统订货点法中,每作一次登录都要评审一次库存记录,当现有量与已订货量的余额达到某一预定的订货点时就办理一个补货订单。在订货点法中,订货量是固定的,通常就是EOQ。定期评审法的适用场合是:1、需多次小量从库存提货,以致每次提货都登入记录是不实际的。食品超级市场、汽车零件供应店以及类似的零售业属于这一类型,例如电子的与机械的机器制造业中的服务零件业务。2、订货成本比较小。这发生在从一个来源收到许多不同物品的订单或写出了238第238页共238页n从一个中心仓库向一分支仓库转移许多存货物品的订单的场合。3、在一次订货许多物品以构成一生产日程是值得想望的场合,例如,可使该系列物品的设备调整组合起来或通过一组合订单能从一供应商获得折扣或通过定期发运满载车皮而降低运费。目标水平是下列需求之和:1、提前期中的预测需求(DLT)2、评审周期中的预期需求(DRP)3、后备存货(R)其中的第一项与第三项与订货点的要素是相同的。显然,倘若两周内不再评审库存记录,则这一期间中的预期使用量必须加到提前期中的需求上去,因为只有经过了这两周之后提前期才能开始。后备存货可用本章前面讨论过的方法来计算。目标库存计算的一个简单例子如下:提前期=1周提前期中的预测需求=20件评审周期=2周(平均订货量=2周的供应量)评审周期中预测需求=40件后备存货=30件目标库存水平(件)=DLT+DRP+R(5-5)=20+40+30=90使用这一库存目标,存货将每两周评审一次而且通过订货使总量达到90件。例如,在首次评审时现有库存与已订货量的总计可能为70件,于是将再订货20件。在下两周内,需求可能总量达45件,这就是第二次评审时将要订货的数量,因为要恢复总计90件的目标水平。关于定期评审应注意下列要点:1、总的提前时间实际上等于交货提前期加上评审周期2、延长评审周期就等于延长提前时间并将要求持有较大量的后备存货3、订货量等于刚刚过去的评审周期中的实际需求4、平均库存水平等于评审周期中需求的1/2加上后备存货。两种简单订货方法对于工业库存中常见的许多低年值物品,往往不值得采用前面讨论过的正规方法。有两种常用方法可用来控制这些无记录的低值物品:两箱法与目视评审法。两箱法:把相当于订货点的一部份存货存放在第二只箱子或容器中隔离起来,然后加上封条。当第一只箱子中的全部开放存货被用完时,打开第二箱或后备容器并通知物料控制人员订货。这是对低值物品保持控制的实用方法。应用中最常遇的问题是:1、缺乏足够的训练与恰当的纪律时,这种系统很快地变坏。不懂这种办法的人员将把后备存货用完也不通知任何人,或者收进补充物料而不正确地去区分开放存货与后备存货。2、一旦被确定之后,永远不再去评审第二箱中要放多少物料。随着该物品需求的改变,这一数量不再足够或变得太大了。两箱法最好应用在补货与库存维护有专人可以委托的受控存货室中。这样做时,238第238页共238页n此办法叫做银行存货法。若物料存放在车间里放开使用,此法很难行得通。目视评审法:存货被定期地核对(也许每周一次或每两周一次)并把每物品订货到一预定的存货水平。这些水平被陈述为一看就明白的数量如“1/4箱”与“6个深”作为重订货点而且通常规定的订货量是大的。当保管存货的责任不能委派到个别人时,此技法远比两箱法成功。它对邻近使用地点的车间存货很管用。在提前期短而且供应商要末发货要末就取消(欠交订单)从而除了最后一份订单之外无保留前已订货的物料的任何记录之必要的场合尤其管用。当然,这是许多零售商店──特别是大的食品超级市场──所采用的主要技法。使用这种方法时涉及三个主要问题:1、必要的定期评审存货水平的工作没有做2、由于现场管理不好,存货未被放在恰当地点,评审者未能发现实际在手头的全部库存3、没有经常核对订货目标,当需求改变时,使它变得过时了或无用了。倘若注意了下列各点,则只需最小限度记录保管工作的低值物品控制方法可以得到非常成功的使用:1、ABC库存分类法的基础是持有较高库存水平的低值物品而且化费最小限度的力气来控制它们。然而,必须记住,一条装配线或包装线可以因为缺乏一种C类物品(同缺乏一种A类物品一样地)而停工。不要忘记控制低值存货的基本规则是要有足够的数量。2、倘若对高值存货更紧的控制并不能补偿由于低值存货较松的控制而增多的库存,则此法并未带来好处。后者节省下的时间必须用来降低高值库存。3、目视控制时常用于松控制而永续记录常用于紧控制:但没有哪一个是必须如此的。工业中一个普通的事例是飞机工业中的铆钉。铆钉单价很低,但年度使用量巨大,使它们成了A类物品。使用目视技法控制此类物品可节省许多登记记录的时间,但其库存水平可以应该被控制得非常紧。4、把一切低年度金额使用量物品都应使用目视评审技法来控制作为一般规则是不好的。一种只在一个产品中每年使用一次的组件是否也要每周去目视核对它呢?对这种物品应该用物料需求计划。原理19.简单实际的技法可能提供更为经济的库存控制。分时段订货点法传统的订货点技法有几个主要问题:1、它缺乏提出被修订的订单“需要”日期的能力。2、在发放当前的一个订单之后,它不提供将被发放的未来订单的信息。3、它难于处理已知的特定时间的未来需求。4、它难于处理季节性或周期性的需求。5、它不给出提前的警告就触发订货。把订货点数据按时间分段可以克服这些困难并提供额外的利益。物品Z的数据如下:预测=20件/周订货量=100提前期=2周后备存货=55现有库存=80件已订货量=第2周到期100件订货点O.P.=(2×20)+55=95件238第238页共238页n为提供更有用的图形,该数据可分时段显示如图5-16。此显示的逻辑是采购与制造的基本逻辑:1、要求是多少?(预测)2、现有存货是多少?(现有量)3、已订货多少?(已订货量)4、必须于何时得到更多的?(已计划订货到达期)5、它们必须于何时订货?(已计划订货开始日)周次12345678等等──────────────────────────────────预测2020202020202020已发放订单100推测的可用数6014012010080*6040**100已计划订货:到期100已计划订货:开始100*已到达订货点**后备存货被打入──────────────────────────────────图5-16分时段订货点法──备货生产产品注意新订单是计划在推测的可用库存将降到订货点(95件)的那一周发放的,虽然这并不是用来确定订单发放日期的方法。没使用计算得来的订货点。该技法使用后备存货(55件)作为目标去建立订货到期日,然后扣去提前期就得到订货开始日期。它安排一批收货去应付已计划的需求以保护后备存货。如果像许多用户已经做的那样,先从现有数字扣去后备存货,再去计算订货开始时的可用总量,其结果将是一样的。由于实际需求是按每一期间对照预测而记录的,被推测的可用存货数字可以被重新计算。因此该技法能指出已发放订单现在需要比原计划提早或推迟,也可在必要时挪动已计划订单。供方(供应商或工厂)更快地响应这类信号会允许以较低的安全存货来维持客户的交货。利用这种分时段的格式克服了前述的传统订货点法的五个困难:1、可以提出不同于发放订单时所定应交货日期的订货需用日期。2、只要预测被相信是可靠的,就可以把未来的订货推测到同样远的未来。3、已知的未来需求“块”可以插入(或替代)任一期间的预测之中。4、季节性或周期性的预测可直接被使用。5、未来活动、已发放订单的状态以及已计划订单全部都表示在分时段显示中。原理20.分时段的订货点数据大大地增强了此技法的威力。这些好处的代价是数据处理的要求要大得多,而且当需求围绕预测平均数变动时可能带来“摇摆不定”。该技法作出反应去保护已计划的后备存货;它不使用后备存货去阻尼实际需求中的变化。图5-16所示为一备货生产产品的分时段订货点法。此技法也可应用于订货生产产品,如图5-17所示。在这里,预测被收到了实际订货所替代,而制造被安排得去适应实际情况。238第238页共238页n预测=20件/周提前期=2周订货量=批对批周次12345678等等───────────────────────────────────实际─预测1815211920202020已发放订单1815推测的可用数-21-19-20-20-20-20已计划的订单:到期211920202020已计划的订单:开始211920202020───────────────────────────────────图5-17分时段订货点法──订货生产产品服务件需求的处理在服务件库存的补货中,需求来自客户而且必须被预测,分时段订货点法非常有用。它能处理间歇性的需求,也能处理各期间都有需求的预测。它可应用于保管在同生产性存货相隔离的存货室中的服务件,也可应用于现行生产中已不再使用的服务件,即使它同现用物品存储在一起。服务件与现用物品完全相同而且二者存储在一起时,可通过把前者的预测需求与后者的计算需求相结合的办法得到控制。这要靠第六章所述的MRP技法来完成。分支仓库需求的处理许多公司有广泛分布的分配网络,成品库存被存储在邻近客户的分支仓库中。分支仓库由地区仓库供应。地区仓库可能是单独的设施,或可能位于一家制造工厂。地区仓库由一家或多家制造工厂供应,它们既满足客户的订货也发货给分支仓库。分时段订货点法为分支仓库的库存补充计划提供了一种良好的工具。更好的一种技法是本章前面详述过的固定周期──可变订货量(目标)法。它同定期评审分支仓库的存货水平以及正规地安排给分支仓库的交货一道工作得很好。这种技法详见附录Ⅶ。这些技法的成功应用详见第二册。独立/相关需求1965年J.A.Orlicky建议在制造业中区分两种类型的需求。他用独立需求来描述对于与一家公司的库存中其它物品的需求无关的成品或组件需求。这种独立需求的特征是客户对成品、中介体或服务件的订货。他用相关需求来描述直接由生产一母物品或其它伴随物品的日程计划所确定的物品的任何需求。相关需求的典型是原料、采购的或自制的零件或成份以及自制的子装配件、附件与附属品。Orlicky建议将这种区分作为确定选用什么订货技法的一条准则。独立需求必须被预测,传统的或分时段的订货点技法是正当的(而且是唯一的)可用技法。相关需求可以计算,物料需求计划是正确的技法。这一一般准则,或原理,是一有用的指导,但并非必须不惜一切代价去服从的牢不可变的定律。在其基本假设为有效的而且必要的纪律被维持的场合,比较简单的、不大昂贵的传统订货点法、两箱法或定期评审法均可被非常有效地使用于相关需求物品。详见第二册。原理21.Orlicky的独立/相关需求准则提供选用订货技法的良好指导。238第238页共238页n六.物料控制:相关需求物料需求计划的逻辑制造作业中使用的大量物料的需求是由要生产某种含有这些物料的物品的决定所引起的。硬货的组件、纺织品与陶瓷制品以及食品中的成份、化学品与药品不是以持续均匀的速率被利用,而且在它们所进入的物品被生产之前是不需要的。它们是如第五章所定义的相关需求。这类物料的首次采购及其不断的补充,通常最好通过应用下列逻辑分析来处理:1、我们何时要去制造多少这种具体产品?2、需要哪些组件(或成份)?3、这些物品已在手头的有多少?4、此外已经订了货的有多少,它们将在何时到达?5、何时需要更多些,而且需要多少?6、这些物品应何时订货?这就是MRP的基本逻辑。它对订货生产、客户定制的产品如船舶、建筑物或专用机器,对定期成批制造的小量或大量产品,对过程工业以及对重复性大量生产都是同样适用的。原理22.MRP逻辑适用于包含多种组件(成份)的一切类型的产品与过程。MRP逻辑应用到这些不同的加工方法要求采用显著不同的方法并使用不同的数据格式。然而,对所有这些加工方法,都要求有健全的物料计划与紧的控制:1、必须开发出一个有效的主计划,它说明要制造什么,需制多少,对每一产品何时需要各种物品。这个主计划叫做主生产日程计划(MasterProductionSchedule,简称MPS)。这些计划数字驱动MRP与其它有关的程序。如果MPS所要求的产出超过了生产设施(工厂与供应商)的能力,则所有的有关计划都是无效与不现实的。这些重要数据以及与生成这些数据有关的活动与考虑将在第七章讨论。2、准确的物料清单,它详细载明产品的组成结构,它是现代计划工作的框架,它说明当产品将被制造或被采办时产品的母物品与组件物品的关系。3、关于现有库存的准确信息,包括一个唯一的零件号、存货数量以及为制订计划所不可缺少的用来完整地描述该物品所需的数据。4、关于为了获得每一物品的增量而已发放的订单的准确信息,它包括外购的或自制的,它必须包括订货量与应交货日期。MRP不需要制造该物品各道工序的加工数据与所需的时间。5、需要有采购或制造成批物料或特定物料批的可靠的提前期。6、必须有足够的物流去满足通过总的过程中涉及的每一设施(包括供应商)的一切要求。计算机以前的MRP在1960年代初有商用计算机可用以前,MRP逻辑只有少数有用的应用。238第238页共238页n人工数据处理的局限性排除了真正净、分时段的MRP的应用,但展开表为许多公司提供了一种有用的工具。图6-1所示为一简单壁灯的物料清单,它列出了组件¿图6-1物料清单──#9W灯代号、其描述以及每次组装所需数量并指出这些零件属自制还是外购。用这种物料清单,计划人员就能够为下一批组装按所需组件数量来订货。例如,要组装2000件#9W壁灯,计划员将申请采购X18开关、Y2L插头与4107电缆各2000件,并准备9W灯罩2000件与414挂勾4000件的制造订单以便在恰当的时候发出订单。这一极端简单的例子不能说明使得许多公司中控制组件库存成为极端复杂的许多常见的复杂情况。最普通的一种复杂情况就是一种组件要用于多种组装之中。图6-2所示为另一壁灯#9P,它与#9W壁灯的唯一区别是灯罩不同。显然,把┏━━━━━━━━━━━━━━━━━━━━━━━━━━━━━┓┃日期┃┃────┃┃制造代码08/10/66┃┃────批准┃┃314────┃┃AES┃┣━━━━━━━━━━━━┳━━━━━┳━━━━┳━━━━━┫┃组件┃┃┃┃┣━━━━━┳━━━━━━┫所需数量┃来源┃备注┃┃代号┃描述┃┃┃┃┣━━━━━╋━━━━━━╋━━━━━╋━━━━╋━━━━━┫┃X18┃开关┃1┃购┃┃┣━━━━━╋━━━━━━╋━━━━━╋━━━━╋━━━━━┫┃Y2L┃插头┃1┃购┃┃┣━━━━━╋━━━━━━╋━━━━━╋━━━━╋━━━━━┫┃9P┃灯罩┃1┃制┃┃┣━━━━━╋━━━━━━╋━━━━━╋━━━━╋━━━━━┫┃414┃挂勾┃2┃制┃┃┣━━━━━╋━━━━━━╋━━━━━╋━━━━╋━━━━━┫┃4107┃电缆┃1┃购┃┃┗━━━━━┻━━━━━━┻━━━━━┻━━━━┻━━━━━┛图6-2物料清单──#9P灯通用组件的需求合并起来将更为经济、高效。因此,在办理一份订单之前,计划员应知道每一期间对每一组件的全部需求。在合并需求的许多方法之中,最简单的是图6-3所示的展开表。它实际上就是一系列物料清单被排列在一起,装配件列在左侧,其组件列在上侧。每一格中的×号表示此组件不用在相应行的装配件中。此表由该大类产品中所有物料清单组成。从展开表中将每一组件的一列需求数加总就可得到该组件的总需要量。然后可将这238第238页共238页n一总需要量同该物品在库存中的可用量相比较。┏━━━━┳━━━┳━━┳━━━┳━━┳━━┳━━┳━━┳━━┳━━┳━━┳━━┳━━━━┳━━━━┳━━┳━━┳━━━┓┃┃┃×18┃×27┃Y2L┃#7W┃#7D┃#9W┃#9D┃#9P┃#11D┃#11P┃414┃418┃381┃411┃#4107┃┃装配件┃需要量┃开关┃开关┃插头┃灯罩┃灯罩┃灯罩┃灯罩┃灯罩┃灯罩┃灯罩┃挂勾┃挂勾┃底座┃底座┃电缆┃┣━━━━╋━━━╋━━╋━━━╋━━╋━━╋━━╋━━╋━━╋━━╋━━╋━━╋━━━━╋━━━━╋━━╋━━╋━━━┫┃#7W灯┃┃┃×┃┃┃×┃×┃×┃×┃×┃×┃2/┃×┃×┃×┃┃┣━━━━╋━━━╋━━╋━━━╋━━╋━━╋━━╋━━╋━━╋━━╋━━╋━━╋━━━━╋━━━━╋━━╋━━╋━━━┫┃#7D灯┃┃┃×┃┃×┃┃×┃×┃×┃×┃×┃×┃×┃┃×┃┃┣━━━━╋━━━╋━━╋━━━╋━━╋━━╋━━╋━━╋━━╋━━╋━━╋━━╋━━━━╋━━━━╋━━╋━━╋━━━┫┃#9W灯┃2000┃2000┃×┃2000┃×┃×┃2000┃×┃×┃×┃×┃2/4000┃×┃×┃×┃2000┃┣━━━━╋━━━╋━━╋━━━╋━━╋━━╋━━╋━━╋━━╋━━╋━━╋━━╋━━━━╋━━━━╋━━╋━━╋━━━┫┃#9D灯┃┃┃×┃┃×┃×┃×┃┃×┃×┃×┃×┃×┃×┃┃┃┣━━━━╋━━━╋━━╋━━━╋━━╋━━╋━━╋━━╋━━╋━━╋━━╋━━╋━━━━╋━━━━╋━━╋━━╋━━━┫┃#9P灯┃2500┃2500┃×┃2500┃×┃×┃×┃×┃2500┃×┃×┃2/5000┃×┃×┃×┃2500┃┣━━━━╋━━━╋━━╋━━━╋━━╋━━╋━━╋━━╋━━╋━━╋━━╋━━╋━━━━╋━━━━╋━━╋━━╋━━━┫┃#11D灯┃┃×┃┃┃×┃×┃×┃×┃×┃┃×┃×┃×┃×┃┃┃┣━━━━╋━━━╋━━╋━━━╋━━╋━━╋━━╋━━╋━━╋━━╋━━╋━━╋━━━━╋━━━━╋━━╋━━╋━━━┫┃#11P灯┃2000┃×┃2000┃2000┃×┃×┃×┃×┃×┃×┃2000┃×┃2/4000┃×┃×┃2000┃┣━━━━╋━━━╋━━╋━━━╋━━╋━━╋━━╋━━╋━━╋━━╋━━╋━━╋━━━━╋━━━━╋━━╋━━╋━━━┫┃总需要量┃6500┃4500┃2000┃6500┃┃┃2000┃┃2500┃┃2000┃9000┃4000┃┃┃6500┃┣━━━━╋━━━╋━━╋━━━╋━━╋━━╋━━╋━━╋━━╋━━╋━━╋━━╋━━━━╋━━━━╋━━╋━━╋━━━┫┃总可用量┃┃7105┃15,432┃7002┃┃┃4595┃┃1244┃┃4715┃29,531┃11,648┃┃┃6400┃┣━━━━╋━━━╋━━╋━━━╋━━╋━━╋━━╋━━╋━━╋━━╋━━╋━━╋━━━━╋━━━━╋━━╋━━╋━━━┫┃不足数┃┃√┃√┃√┃┃┃√┃┃1300┃┃√┃√┃√┃┃┃100┃┗━━━━┻━━━┻━━┻━━━┻━━┻━━┻━━┻━━┻━━┻━━┻━━┻━━┻━━━━┻━━━━┻━━┻━━┻━━━┛图6-3展开表───灯图6-4所示为#9P灯罩的库存记录。这一数字也指示经典的永续库存数据关系:起始余额+收进-发出=现有+已订货-已分配=可供计划数。如展开表所示,目前有增加灯罩以满足三月下旬制造上需求的必要,所以可写1300件灯罩的订单在适当的时候留出恰当的提前期,发放到工厂。起始余额=1444──────────────────────────────────(+)(-)(=)(+)(-)(=)日期收进发出现有已订货已分配可供计划数──────────────────────────────────3/12400─-1844──60012443/14─-6001244───-12443/23─-─-1244──2500-12563/23─-─-12441300250044──────────────────────────────────238第238页共238页n图6-4库存记录──#9P灯罩在间歇的时候,每周可用此展开表来确定下周要用的组件是否正在成功地按日程表去满足装配的需要。这种情况下,展开表中“总可用量”这一行的数字要取自库存记录上的“现有”这一列而非取自“可供计划数”这一列。这种简单的、人工的需求计划技法已经使用了多年。虽然其用户发现用它来订货组件要优于用订货点系统,但除非对它作出重要的改进,否则其使用往往引起库存过多。展开表只适用于单层的物料清单;它不能处理子装配件或中间体的存货。它只能表示一个期间内总的需要量,而且这一期间必须足够地远,以包括任何组件最长的制造或采购提前期。由于提前期长,许多公司以季度为基础来制订计划,而且要向前多计划一个季度以显示本季度的不变需求与下季度的预期需求。因为倘若不在前一季度作出计划,则任何需要一两个星期以上时间来制造的组件将很可能在下一季度之初是缺货的。由于计划期间如此地长,还会发生其它问题。计划期间为13周的不变需求要求为每一最终物品的预期需求作一预测;该预测延伸到未来越远,它将越不准确。在这样一种季度计划方法中,计划员往往发现,每一季度开始时,许多组件就由于预测误差不是缺货就是供过于求。二次世界大战之后不久的时候,许多行业的产品有大量的欠交客户订单,伸展到12个月有时达18个月之久。这些需求构成了制订生产计划的坚实基础。检阅这些订单并制订一份周期性的物料计划是合乎逻辑的也是相当容易的,可从装配一种类型的机器的要求日期开始,然后向后推算去安排子装配件、组件的制造与所需物料的采购。为满足这一装配件需求的订货将把库存的中间层次与正常的提前时间考虑进去。然后由机器中心来分析对零件、子装配件与完工机器的需求以达到该中心所要求的生产水平。然后写出组件与子装配件的订单,其发放日期通过使用正常的物料计划逻辑,从已计划的装配日期倒推出来。这样一来,积压订单(由于它们远远超过了提前期)就成了已知的需求预测,所以计划可以譬如说每季度制订一次。即便用人工来做,这种季度订货系统也很有用。1950年代末与1960年代初,这些积压订单缩小到了不再能提供必要的计划信息的地步。结果是为了提供这种失去中的信息人们对预测发生了很大兴趣。由于客户要求较短的交货时间,许多行业从定货生产转向备货生产。此方法的典型是对来年每个月的各种成品需求作详细预测,而对下一季度提出一份不变生产日程计划。然后将这一预测与日程计划分解为子装配件与组件的日程计划,把它们当作过去所用的积压订单来使用。再次把开始日期分派到订单,而这些订单被放在发放文件夹中等待其发放日期。然后把这些订单上的工作按机器中心累计以确定机器的季度负荷以确保实际能力够用。不幸的是,随着期间的进展,实际销售将不同于预测,因而使安排了生产的产品将大大不同于满求最近的客户订单所要求的产品。此问题的解决办法是把所希望的产品的日程提前并试图在已安排了日程的产品之外把它们从工厂赶制出来。其结果,对生产能力的需求往往变得过大(因为经工厂赶制出来的订货实际上产生着一个额外的负荷),虽然实际能力是足以去满足平均需求的。很少有生产控制系统能够识别出哪些订单可以延迟以便给赶制的订单让路的,所以有代表性的情况是总的工作负荷超过了已计划水平。这一定期安排日程计划方法的另一特征是在每一季度的开始有大的超负荷。当库存主管评审新期间需求时,将发现许多物品已经销售得超过了上一季度开始时所238第238页共238页n做的预测,所以在安排下一季度的日程计划时要求在第一个月有高度集中的生产以满足紧迫的需求。在理论上,季度订货制企图平整生产。在实践中,当根据详细的物品预测而不是根据不变的客户订单的积压来安排生产时,它难得能够成功地达到这一目标。缩短计划工作的期间要求对迄今为止描述过的简单技法作出巨大的改进。仅仅指出(如在图6-3中)第二季度将需要2500件并未指出在该季度中的何时将需要这些组件以及需要多少。有的手工方法根据已计划的装配需求,使用物料清单,在组件记录上标出需要日期并根据标准提前期计算出开始日期。当需求改变时,这种方法不便于合并需求或重新计算组件的日程计划日期。这是为什么在实践中手工的需求计划方法往往并不比订货点技法有效多少。图6-5是一个分时段计划,它表示预测的第二季度#9P灯按周的装配日程。#9P灯(主计划)─────────────────────────────周次─────────────────────────────141516171819202122232425───────────────────────────────500──500──500──500─────────────────────────────现有=1244#9P灯罩单位:件(物料原计划)ABC=A提前期:4周安全存货=0订货量=批对批───────────────────────────────────过周次──────────────────────────期141516171819202122232425───────────────────────────────────推测使用量───500──500──500──500未了结订货─────────────推测可用数─12441244744744744244244244────已计划订单收货─────────256──500已计划订单发放─────256──500───────────────────────────────────────图6-5分时段订货法──灯的组件这种装配计划是主日程计划的一种形式。这样一个主日程计划很可能是根据何时该被装配的最终产品将达到其重订货点这样一种估计。图6-5中所示在第16、19、22与25周的间歇性需求实际上是最终物品的EOQ。#9P灯罩的需求是根据#9P灯的装配日程推测出来的,表示在主日程计划的下方。这一订货技法规定在哪一周将需要组件并根据组件的提前期,显示制造或238第238页共238页n采购订单必须在何时发放。可以看出,例如,当500盏该灯被装配时,#9P灯罩的库存将在第16与19周各减少500件,而在第18周必须发放另外256件灯罩的订单,使它们能在第22周到货,供已计划的装配另外的500盏灯之用。注意灯罩的订货量规则是批对批。(见第3章)图6-5只表示出#9P灯的推测的装配需求;用它来确定#9P灯罩的需求已经足够了,该灯罩只使用在这种灯上。两种或两种以上装配件通用组件的物料计划要根据分解到其恰当时间期间的各种装配件的需求之和。对于灯罩的组件,如果决定要自制而非外购,也可用相似的分时段计算法。这类订货用手工去做极为困难,除非是对比较简单产品中的少数重要物品。然而,对这些物品,它是相当有用的。关于分时段计划法有若干一般原则要牢记:1、物料计划的计划视界必须足够地长,在单层物料清单中它必须覆盖任一组件的最长提前期,而在多层物料清单中它必须覆盖各组件的提前期之和。2、为了对需求的变化作出反应,必须经常修订物料计划。3、所用的时间期间越短,物料计划将越为有效。例如,期间为一周而且每周修订一次的计划要比期间为一月而且每月修订一次的计划更为有效。然而,要记住,计划也恰恰是这样一种东西──把它弄得更精确与更频繁地修订它会很快地达到一个报酬递减点。这将在第二册充分讨论。MRP的前提条件分时段净物料需求计划(NetTime-phasedMRP)要求非常具体的数据。它们是:1、一份分时段的主生产计划,其中每一物品由一物料清单描述。2、每一物料清单中的每一组件及其父件要有唯一的识别号。3、结构恰当而准确的物料清单与工程更改的严格控制。4、关于存货物品准确的现行库存余额。5、关于未了结的采购与制造订单的准确数量与可靠的交货日期。6、关于采购物品与制造物品的可靠的提前时间。这些数据对任何MRP程序都是不可缺少的。此外,还有对实际应用该技法的要求:1、用来处理实际上每家公司中所要求的大量数据的计算机软硬件。2、物料收发、库存调整以及订单发放与了结的及时报告。3、处理计划中识别的不同批的纪律。4、有能力制订出有效的计划并然后执行它们的人员。MPS子系统最低限度的MPS子系统必须包括每一将应用MRP的产品的数量与日期数据。为了MRP逻辑能使用于所有组件,MPS的视界必须至少要伸展到等于构成从采购某些原料开始、通过生产MPS中所描述物品所要求的各道加工作业的一个最长顺序的所有提前期之和;这叫做累计提前时间、关键路径提前时间或堆积提前时间。MPS的视界还要被延伸并在较低层次使用视界填充者以提供一合理数量的(3到6个月)关于原料未来需求的数据。更完整的MPS子系统见第7章。238第238页共238页n零件代号化在现代系统中使用时,每一物品必须具有一个而且只有一个零件号。在本章的例(灯)中,所使用的零件号系统是一种非常简单的、用在小公司中的典型零件号系统,它把数字与字母无显著意义或理由地结合在一起。随着公司的成长与其产品大类的扩展,该编号系统开始变得令人难以置信地复杂化以致即使简单的系统也开始陷于困境。于是,一项开发一更加合理的零件编号系统的计划开始了──通常用多位数字,每位数字具有某种意义(描述产品的原料、它的基本制作方法、是自制还是外购等等)──并引进这一零件编号系统。对某些组件,保持每位数字具有某种意义很快变得极为不便,于是最后便采用无显著意义的零件编号。在一个不良的生产与库存控制环境里发现三种不同的零件编号系统同时并用并非少见的事。看来只有少数管理人员认识到了缺乏一个良好的零件编号系统与生产与库存控制活动缺乏成果这两件事之间的联系。理想的零件编号系统具有尽可能少的数字并且只使用数码数据。只用4位数字就可以唯一地识别出多达1万种不同物品。虽然很少公司有100,000种物品要处理,但大多数公司用6位数字,许多公司有字母字符、短划、空格参杂在零件号之中。他们受到的惩罚包括:1、处理数据的人员出错更多2、需扩充文档空间3、程序的处理时间更慢现在就是开始逐步采用一种简单、可工作的零件编号系统再好不过的时机。对一切新产品、新材料与其它被计划与控制的物品,都应采用短的、纯数码。用短数码去一下子替代现存的长而复杂的代号的庞大计划是难以论证的;时间、设计与其它变化将最终地排除它们。零件编号这一主题详见第二册。原理23.理想的零件号是短的、数码的与唯一的。物料清单的构成本章前面的例中所举的灯其物料清单非常简单,零件很少,没有子装配件。在更复杂的装配件中,有必要同计划件的与最终装配件的制造那样去计划子装配件的制造。如果灯制造商决定要自制Y2L插头,则物料清单将必须显示装配这一子装配件所需的组件以及其它进入总装的组件。图6-6出示这一较为复杂的物料清单,但它并未指出#1314开关乃是制造代码314┏━━━━━━━━━━━━━┳━━━━┳━━━━┓┃组件┃所需┃┃┣━━━━━━┳━━━━━━┫┃来源┃┃编号┃描述┃数量┃┃┣━━━━━━╋━━━━━━╋━━━━╋━━━━┫┃X18┃开关┃1┃购┃┣━━━━━━╋━━━━━━╋━━━━╋━━━━┫┃Y2L┃插头装配件┃1┃制┃238第238页共238页n┣━━━━━━╋━━━━━━╋━━━━╋━━━━┫┃1314┃开关┃1┃购┃┣━━━━━━╋━━━━━━╋━━━━╋━━━━┫┃219┃外壳┃1┃制┃┣━━━━━━╋━━━━━━╋━━━━╋━━━━┫┃326┃底座┃1┃制┃┣━━━━━━╋━━━━━━╋━━━━╋━━━━┫┃220┃外壳绝缘┃1┃购┃┣━━━━━━╋━━━━━━╋━━━━╋━━━━┫┃222┃底座绝缘┃1┃购┃┣━━━━━━╋━━━━━━╋━━━━╋━━━━┫┃405┃螺杆┃1┃制┃┣━━━━━━╋━━━━━━╋━━━━╋━━━━┫┃9P┃灯罩┃1┃制┃┣━━━━━━╋━━━━━━╋━━━━╋━━━━┫┃414┃挂勾┃2┃制┃┣━━━━━━╋━━━━━━╋━━━━╋━━━━┫┃4107┃电缆┃1┃购┃┗━━━━━━┻━━━━━━┻━━━━┻━━━━┛图6-6多层物料清单──#9P灯Y2L插头这一子装配件的零件。可在物料清单上作些标志以指明这一关系,例如使用星号去表示子装配件中所用的所有物品;但若这些子装配件还有其子装配件,这种星号标志法将显得非常不便。更为普通的方法是用缩排形式来表示物料清单,如图6-7所示。这里所有进入Y2L插头的组件,即第二层组件,向右缩排以表制造代码314━━━━━━━━━━━━━━━━━━━━━━━━━━━━━第1层第2层描述所需数量来源组件号组件号━━━━━━━━━━━━━━━━━━━━━━━━━━━━━X18开关1购Y2L插头装配件1制1314开关1购219外壳1制326底座1制220外壳绝缘1购222底座绝缘1购405螺杆1制9P灯罩1制414挂勾2制4107电缆1购━━━━━━━━━━━━━━━━━━━━━━━━━━━━━━238第238页共238页n图6-7部份缩排的物料清单──#9P灯示它们是用在紧靠前面的那个子装配件的组件。在图6-6与6-7中,#9P灯都用制造代码314来表示。由于Y2L插头要用在每种灯中,图6-7表明这种插头或其组件的任何改变都将影响到每份物料清单。一种稍有不同的物料清单形式,它有助于更好的维护与更新,可以简化这种工作。例如,如果使用图6-2中的物料清单但Y2L插头用代码表示为一个自制的子装配件,另外专用一份物料清单(如图6-8所示)来表示该子装配件。这叫做单层物料清单。这样一来该子装配件中任何变化只要不影响它在最终物品中的使用就只需更改一份物料清单──只要Y2L插头继续用于最终装配,各个较高层清单将不受影响。单层物料清单的使用也大大减少了所需的总文档空间,因为通用件的物料清单只需在产品结构文件中存储一次。计算机以高速存取与检索记录的能力使得这种分裂的文件可以实用;用人工搜索这种相关的物料清单是不切实际的。制造代码(用在#7W、#7D、#9W、#9D、418#9P、#11D、#11P灯中)━━━━━━━━━━━━━━━━━━━━━━组件编号描述所需数量来源━━━━━━━━━━━━━━━━━━━━━━1314开关1购219外壳1制326底座1制220外壳绝缘1购222底座绝缘1购405螺杆1制━━━━━━━━━━━━━━━━━━━━━━━6-8物料清单──Y2L插头装配件计算机也具有在产品结构文件中保留信息使计算机能检索与提供反查(何处使用了)物料清单。有如图6-8顶部的信息(显示使用Y2L插头的所有灯型),这种清单指出某一物品在其较高层清单中所有的应用;这些信息对设计工程师非常有用,他可以发现一个组件的设计更改将可能影响到哪些父物品。单层与多层的反查清单都是常用的。一种有用的物料清单的图示法是系列树或圣诞树,如图6-9所示。此图表示从成品到原料的各个层次并包括所有外购与自制的组件。这格式虽然对研究此产品314层次灯0┏━━━━━━━┳━━━━━━┳━━━━━━━┳━━━━━┓9PX184184107414灯罩开关插头电缆挂勾1238第238页共238页n┃┃┃┃(1.4尺2)┃┃(1.2寸)┏━━┻━━┓┏━━━┳━━━━┳━━━┳━━━━┳━━━┓┃11010522021913143262224051262铁丝纸外壳外壳开关底座底座螺杆带框架绝缘┃┃绝缘┃┃┃(0.75尺)┃(4.5寸)┃(4寸)┃(7.3尺)186126174108管子带条3铁丝图6-9系列树物料清单──#9P结构的人非常明白与有用,却只可能用在很少数公司的正式计划系统之中。在结构问题、制造作业与产品的简化与标准化问题的研究之中它有更广一些的用途;在这些研究中常常使用典型产品的手工图。在这种研究中矩阵展开表(6-3)更加有用虽然它会变得冗长。传统做法是从上到下去给层次编号;因此图6-9中314号灯的层次为0,大多数原料的层次为3。#9P灯的完全缩排物料清单如图6-10所示。此图表示设置清单的一种常用方法,将零件号缩排以显示父件──组件关系。注意这是一份四层清单(从314号灯到四种原料),它有一个子装配件(418号插头)与最终装配物料清单再加上五份用外购原料单独制成的组件的清单。还请注意126号带在不同层次上出现了两次。要真正地完全,此物料清单还应包括包装物料。在一完全缩排物料清单中(如图6-10所示),若干物品通用的组件与原料将出现多次。为了简化使用这种物料清单的许多活动,可用计算机程序去开发汇总的清单。在这种清单中,每种物品只出现一次,每件产品所需要每种物品的数量是每种物品在所有应用中所需的总计数。零件号┃描述┃所需数量┃来源━━┯━┯━┯━┯━╋━━━━━╋━━━━━━╋━━━━━X│1│8││┃开关┃1┃购Y│2│L││┃插头┃1┃制│1│3│1│4┃开关┃1┃购│2│1│9│┃外壳┃1┃制││1│8│6┃管子┃0.75尺┃购│3│2│6│┃底座┃1┃制││1│2│6┃带┃4.5寸┃购│2│2│0│┃外壳绝缘┃1┃购│2│2│2│┃底座绝缘┃1┃购│4│0│5│┃螺杆┃1┃制││1│7│4┃条┃4寸┃购9│P│││┃灯罩┃1┃制│1│0│5│┃纸┃1.4尺2┃购│1│1│0│┃框架┃1┃制238第238页共238页n││1│0│8┃铁丝┃7.3尺┃购4│1│4││┃挂勾┃2┃制│1│2│6│┃带┃1.2寸┃购4│1│0│7│┃电缆┃1┃购━━┷━┷━┷━┷━┻━━━━━┻━━━━━━┻━━━━━图6-10完全缩排物料清单──#9P灯所有用来处理物料清单的好的计算机程序都能够自动地分派低层代码;它们表明一物品在它被使用的任一物料清单中的最低层次。这些低层代码的主要用途是确定何时一MRP程序已经累计了对一组件的全部需求并可接着进展到针对这些需求去应用现有库存与已订货量以计算出净需求。例如,在图6-9中,126号带出现在第2层与第3层;在制造326号底座的需求未确定之前不会提出126号带的总需求量。低层代码确实地告诉计算机何时去为每一物品计算其净需求。若在其它应用中使用层次代码则要加上小心。当物料清单文件中加进新的物品时,计算机程序将总是确定正当的最低层代码,但它们当物品被取消时可能并不减少层次代码。在MRP的净计算中这不成问题,但对层次代码的其它用途可能有显著影响。用人工处理物料清单时,一种常用形式是增─删清单(add-and-deletebill),别名叫“除了相同之外”(same-as-except)与比较性(comparative)清单。可以通过简单地增删一份现存清单来为一种新物品开发这种清单。它的实际优点是在相似物品之间突出具体的差别,此外也使书面工作更加简单。然而,物料清单的这种形式并不有助于其在MRP程序与其它现代计划编制应用中的使用而且对于计算机清单处理程序这也是不必要的。所造产品的一般配置相似而且一次只造一件的公司(诸如造船、重型机器或建筑用设备)发现“属物料清单”(genericBOM)是有用的。这种物料清单具有任意派定的零件号与组件的一般描述,它有两个目的:1、作为核对表,以确保在设计与采购中没有忽视任何组件。2、为生产前活动提出日程计划,包括成本估计、设计、机床安装、能力计划、加工等等。为了在设计工作完成之前就可以提前发放某些细节,可以发放部份物料清单(partialBOM),使得生产前、物料采购与其它必要活动得以开始。这最好同属清单一道办理,同时显示已发放的与未发放的物品。部分清单在使用正式系统而非依赖于子系统来提出与跟踪实际成本与生产信息方面也是有用的。并非直接进入产品的其它物料也被包括在物料清单之中以改善对这些物料的计划与控制。这些物料包括医药、化工与食品加工中的清洁剂、检测用试剂、机床安装、砂轮与加工中消耗的类似物品。物料清单的其它应用详见第二册。在超量计划技法中特种结构物料清单的使用见第7章。第二册的第4章介绍许多情况下物料清单的应用。原理24.物料清单构成现代系统的框架;它们必须高度准确并恰当地构成。工程更改的控制由于物料清单的关键角色,处理物料清单的程序的一个必要属性就是一套处理工程设计更改的程序。这些程序的基本目的是去选择未来的物料计划中物料清单的正确格式。发生工程更改有种种原因──主要原因是产品改进,制造问题,降低成238第238页共238页n本,提高质量,产品寿命与政府的规章。引进更改的时机可根据下列中的任何一个:1、克服某种暂时困难的临时需要。2、由于职能、安全、健康或法律上的理由的迫切需要(也许还包括取消或翻新正在使用中的产品)。3、为了在尽可能早的时机利用更改得到新的物品。4、最小限度的成本,包括过时的库存,机床安装、制订规章的机关的批准,设备更换等等。5、具体时间或产品的序号以便同若干其它更改配合或为客户提供特定的配置。上述的第2种更改往往叫做强制性更改,而其它几种叫选择性更改。影响更改时机和数据收集与决策的处理方法的诸因素更加完整的讨论见第二册。时机方面重要的考虑有:1、现存的组件与产品库存的耗尽2、服务(备件)零件的需要3、新品的可得性──原料、机床安装、设备、等等。4、对工厂或供应商能力的影响5、竞争状况6、利润贡献7、主管机关的批准8、产品说明的手工更改有若干技法可用来恰当地引进工程更改。最普通的技法利用一生效日期,它是经过仔细地考虑了上述有关因素之后才确定的。然后把这一日期登入新组件与被替代组件的产品结构文件,如图6-11(a)所示。因此,计算机被指示#1314(a)418插头---┏━━━━┳━━━━╋━━━━┳━━━━┓---其它┃组件1314开关#927工程更改通知指导一旦有供应时即用#1369开关替代所有#1314开关生效性零件号描述工程更改通知状态日期1314开关927删除09/151369开关927增添09/16-------------------------------------------(b)1314(设订货量=批对批)开关(设提前期=0)(设安全存货=0或所需余额)1369开关238第238页共238页n图6-11物料清单更改生效日期开关要一直使用到9月15日,而从9月16日开始使用#1369开关。这一日期的确定要配合来自供应商的新开关的可得性。在某些情况下,可使用一种非常简单的(虽然是手工的)物料清单去联系现存组件与新组件,如图6-11(b)所示。它要求在物料清单的每一种应用(当然备件除外)用新品取代老品。当所有老品要被用完(或下降到某一特定量)时该更改才生效。MRP用完现存物品并在需要时调用新品。如图6-11(b)所示,在现存物品的物品主文件中有若干数据需作修改:1、确定批量大小的规则应设置为批对批(每一时间期间所需数量各异)。2、提前期应设置为零,表示新品的需要时间与老品相同。3、如果希望把现存物品用完,安全存货也应设置为零。如果要保留某些数量作服务件或其它用途,应将数量登入安全存货记录。当这种物料清单用于成本核算时,新老两物品中必须有一个的成本在其文件中要设置为零。倘要用现存物品的成本,则新品的成本要设为零,反之亦然。可以生成提料单调用新品作为现存物品的替代物。也可用这种技法去触发采购物品的信号,采购物品应该是没有物料清单的。显然,需作大量工作去调整文件,而且要有效地使用这种简单技法,使用者必须充分理解这种方法。当由于需求变化,收率问题等原因而难于确定一有效的生效日期时,这种简单方法可能是有益的。它取代了为不断监视生效日期而更换文件的工作。注意在所有情况下应定期地清除掉产品结构文件中过时的清单。序号生效性是一更为复杂的问题。用来控制更改时机的序号通常指派给最高层的产品。在计划物料时企图把序号从上层弄到底层是一种错误。这种做法要求非常大量的数据存储与长得多的运行时间;只有当涉及少数昂贵产品时才能证实这种方法。最好的办法是使用图6-11中所示的技法之一去争取把大多数现存物品用掉并在接近正确时间时得到新品。除非涉及非常昂贵的物料,否则不妨安排一些现存物品作缓冲。当执行该计划的时刻到来时,可为每一用序号编号的产品选择恰当的物料清单。当涉及昂贵物料或当要求用序号很严格地控制更改时,主计划必须包括两种产品识别号(型号与序号)并且MRP程序的净改变更新是必要的。在该截止序号以下各批产品在MPS中将用现存清单来运行而其它的在截止序号与此序号以上的产品将使用更改后的清单。当更改发生在物料清单的中层或较低层次时,需要在制造作业中有严格的纪律以确保在成品中使用恰当的组件的组合。因为这种纪律难以得到而且可能是昂贵的,所以最好在装配开始以前避免分派序号,或更好些,到生产完成之后再分派序号。工程更改把向使用该产品的客户提供正确的服务件的问题大大复杂化了。对于大型、复杂的机器诸如机床、发电设备与船舶,应为每一件产品准备一宗包括图纸、说明书与一份完整地反映该件产品实际构成情况的物料清单在内的档案材料。此档案的拷贝给予客户,而制造商要保留一份或多份以备做服务工作或需要备件时使用。对于较大量的产品诸如汽车、家用电器与电动工具,即使合理的工程更改次数也会使备件问题难以管理。最好的办法是成块更改,即许多作业更改同时实施。除了备件更好的控制以外,此法还有一些优点:1、更准确的物料清单。2、更稳定、更简单的物料计划。238第238页共238页n3、更准确的成本信息。4、较少的作业干扰。5、更明白、更准确的文档建设。工程更改的历史记录在国防、航天、医药、原子能与食品加工行业的公司中,良好的配置控制是强制性的;在其它行业中,它是健全的制造计划与控制的一种要求。除已经讨论过的零件编号、清单构成与更改控制之外,还需有一内容广泛的历史文档。这有许多用途,包括确定恰当的备件,识别问题的根源与原因,找出潜在的或实际有缺陷的产品以及在法律行动中提供数据。工程设计更改的典型历史记录包括下列:1、组件或产品的零件号。2、替代它的新零件号,生效日期与工程更改号(ECN)。3、老零件号被替代,生效日期与ECN。4、指示每一更改的主要理由的工程更改代码。5、在此同一更改中包括的其它产品或组件。维护这一历史数据的责任通常赋予设计工程。大的国防、航天与电子设备制造商设置单独的组织群体叫做制造规格或类似的名称;他们的责任包括此历史文件及其它基本文件的记录。工程更改的历史数据可用多种方法存储:1、纸文件现已过时。2、由于数据量大,计算机文档仍是昂贵的,虽然其费用正在下降。清单处理程序提供方便的连接以便追踪历史。存储整个清单是不必要的,太昂贵而且检索起来太慢。用磁带比用磁盘要好。3、缩微胶卷与缩微胶片价格低廉,使用灵活并便于检索。这种文档除了主要用来记录工程更改之外还有许多应用。它们对客户、市场营销、销售、专利、法律、质量、计划、会计与生产人员同对工程人员一样有用。如同对制造计划与控制有必要的所有文件一样,只有准确的文件才有保存的价值。原理25.物料清单中工程更改的控制对一家公司的成败犹如新设计一样重要。MRP的机制完全的、详细的、净的、分时段的MRP试图建立一非常严格的模型去表示物料将如何通过一制造厂(或许多工厂)或通过一分配系统。物料清单确定必须被计划与存储的物品以及它们被外购或自制出来的顺序与时机。时间期间(叫做时段)的长短,通常为天数(被误称为“无时段”)或周数(难得以月份计),确定计划的精度。更精确的计划不一定更准确。不准确的数据,不良的纪律与野心过大的计划使得MRP中开发的模型成为环境的一个很坏的代表。更频繁地使用MRP重新制订计划的能力与事无补。这两种常见的误解,以精确度代替准确度与以重新计划代替执行计划,将在第二册讨论。MRP显示的数据包括下列中的某些或全部:1、标题包括每一计划中物品的各种信息,包括零件号、描述、现有量、度量单位、外购还是自制(有时既购又制)、ABC分类、确定批量的数量或计算用代238第238页共238页n码、标准提前期、已计划安全存货、责任计划员代码、标准成本与已分配量。有时其它数据,譬如上次事务的日期、起始工作中心、上次循环盘点日期与类似的专用信息也包括在内。所包括的信息越多,打印它的时间就越长,显示就越显得拥挤,书面输出量就越大。难得需要的数据可在需要时通过查询计算机数据库而得到。2、时间期间的标示大多横排(如图6-5),但有时竖排(如图6-12)。其中常常包括一个过期期间(pastdueperiod),有时它被再分为若干过去的期间。有的公司在打印输出时只表示有限的几个近期的期间再加上一个“以后的总计”,以节省纸张与用户的时间。现有=1244ABC=A单位=件安全存货=0提前期=4周订货量=批对批┃┃未了结┃┃已计划┃周次┃┃订货┃推测可用┃发放┃收货┃行动━━━╋━━━━╋━━━╋━━━━╋━━━╋━━━╋━━━17┃┃┃744┃┃┃18┃┃┃744┃256┃┃订货19┃500┃┃244┃┃┃20┃┃┃244┃┃┃21┃┃┃244┃500┃┃订货22┃500┃┃-256┃┃256┃收货23┃┃┃┃┃┃24┃┃┃┃┃┃25┃500┃┃-500┃┃500┃收货.┃┃┃┃┃┃.┃┃┃┃┃┃.┃┃┃┃┃┃━━━┻━━━━┻━━━┻━━━━┻━━━┻━━━┻━━━图6-12#9P灯罩物料计划3、每一时间期间中的需求由制造父物品的计划生成或由满足分支仓库的需要生成。4、恰当时间期间中的未了结订货(最好叫它将收到数而常被称为计划内应收)表示当不变、已发放订单被满足时在该期间将被收进的已计划量。5、推测可用量(projectedavailablequantities)(最好叫将有)在每一时间期间都被显示。大多数MRP程序从现有库存扣去已计划安全存货与已分配数从而得出可供计划(available-to-plan)的数字以开始作MRP净需求的计算(netting)。少数不这样做,而是抓住已计划安全存货,安排已计划订单将在推测的可用余额下降到安全存货以下时来货。少数公司分时段进行分配,并把分配数从恰当期间中的可用余额中扣除。大多数使用者把已发放未了结订货加到可用数据但不加入已计划订货,让推测可用数据变成负数并不断增大。这指示该物品将跌到已计划安全存货水平以下的期间,如果有这样的期间的话,或指示除非及早采取行动去发放一补货订单否则就会缺货的期间。238第238页共238页n6、已计划订单到期(最好叫要补或有时叫到期)表示已计划有订单要在恰当的期间完成及其数量以满足净需求。它在打印输出中往往略去。7、已计划订单发放(最好叫开始或有时叫计划发放)表示已计划有订单要在该恰当的期间发放及其数量以配合已计划订单的完成。各种计算EOQ的技法详见第3章;它们的优缺点与应用中的问题在第二册中讨论。确定已计划安全存货水平的技法与订货点已在第5章讨论过;在MRP中没有有效、严格的技法可用。没有一种统计分布能与大多数相关需求情况中需求所经历的凹凸不平、反复无常而有限度的变化符合得足够地好,所以不能担保所需的计算。为对付客户需求中数量与品种组合的变化提供灵活性而在计划中安排额外的成套组件的一种逻辑方法将在第7章“为灵活性而超量计划MPS”这一节叙述。不作安全存货计划时MRP程序的表现要好得多;只有少数例外,将在第二册讨论。MRP机制应用于#9P灯的各层组件的情形如图6-13所示。它从灯的主生产计划往下经过#418插头装配件、#219外壳与#186管子,跟踪整个净需求与分时段的计算。当然,类似的计算要对所有的组件进行;传统的MRP显示将分别显示每一物品,通常按零件号的顺序并按计划员归类,而并非依图6-13中的父件──组件关系。┏━━━━━┳━━━━━━━━━━━━━━━━━━━━━━━━━━━┓┃┃周┃┃制造代码┣━┳━┳━━┳━┳━┳━━┳━┳━┳━━┳━┳━┳━━┫┃#134┃14┃15┃16┃17┃18┃19┃20┃21┃22┃23┃24┃25┃┃主生产计划┣━╋━╋━━╋━╋━╋━━╋━╋━╋━━╋━╋━╋━━┫┃┃┃┃500┃┃┃500┃┃┃500┃┃┃500┃┗━━━━━┻━┻━┻━━┻━┻━┻━━┻━┻━┻━━┻━┻━┻━━┛现有=700ABC=A单位=件安全存货=0提前期=1周订货量=3周┏━━━━┳━━┳━━━━━━━━━━━━━━━━━━━━━━━━━━━━━━━━━━━━━━━━┓┃自制插头┃过┃周装配件┃┃┃┣━━┳━━┳━━┳━━┳━━┳━━┳━━┳━━━┳━━━┳━━━┳━━━┳━━━┫┃#418┃期┃14┃15┃16┃17┃18┃19┃20┃21┃22┃23┃24┃25┃┣━━━━╋━━╋━━╋━━╋━━╋━━╋━━╋━━╋━━╋━━━╋━━━╋━━━╋━━━╋━━━┫┃需求┃┃400┃300┃500┃400┃300┃500┃400┃300┃500┃400┃300┃500┃┣━━━━╋━━╋━━╋━━╋━━╋━━╋━━╋━━╋━━╋━━━╋━━━╋━━━╋━━━╋━━━┫┃将收┃┃┃┃1200┃┃┃┃┃┃┃┃┃┃┣━━━━╋━━╋━━╋━━╋━━╋━━╋━━╋━━╋━━╋━━━╋━━━╋━━━╋━━━╋━━━┫┃将有┃700┃300┃--┃700┃300┃--┃-500┃-900┃-1200┃-1700┃-2100┃-2400┃2900┃┣━━━━╋━━╋━━╋━━╋━━╋━━╋━━╋━━╋━━╋━━━╋━━━╋━━━╋━━━╋━━━┫┃要补┃┃┃┃┃┃┃1200┃┃┃1200┃┃┃1200┃┣━━━━╋━━╋━━╋━━╋━━╋━━╋━━╋━━╋━━╋━━━╋━━━╋━━━╋━━━╋━━━┫┃开始┃┃┃┃┃┃1200┃┃┃1200┃┃┃1200┃┃238第238页共238页n┗━━━━┻━━┻━━┻━━┻━━┻━━┻━━┻━━┻━━┻━━━┻━━━┻━━━┻━━━┻━━━┛现有=2800ABC=B单位=件安全存货=0提前期=2周订货量=4000┏━━━━┳━━┳━━━━━━━━━━━━━━━━━━━━━━━━━━━━━━━━━━━━━━━━┓┃自制外壳┃过┃周┃┃┃┣━━┳━━┳━━┳━━┳━━┳━━┳━━┳━━━┳━━━┳━━━┳━━━┳━━━┫┃219┃期┃14┃15┃16┃17┃18┃19┃20┃21┃22┃23┃24┃25┃┣━━━━╋━━╋━━╋━━╋━━╋━━╋━━╋━━╋━━╋━━━╋━━━╋━━━╋━━━╋━━━┫┃需求┃┃┃┃┃┃1200┃┃┃1200┃┃┃1200┃┃┣━━━━╋━━╋━━╋━━╋━━╋━━╋━━╋━━╋━━╋━━━╋━━━╋━━━╋━━━╋━━━┫┃将收┃┃┃┃┃┃┃┃┃┃┃┃┃┃┣━━━━╋━━╋━━╋━━╋━━╋━━╋━━╋━━╋━━╋━━━╋━━━╋━━━╋━━━╋━━━┫┃将有┃2800┃2800┃2800┃2800┃2800┃1600┃1600┃1600┃400┃400┃400┃-800┃-800┃┣━━━━╋━━╋━━╋━━╋━━╋━━╋━━╋━━╋━━╋━━━╋━━━╋━━━╋━━━╋━━━┫┃要补┃┃┃┃┃┃┃┃┃┃┃┃4000┃┃┣━━━━╋━━╋━━╋━━╋━━╋━━╋━━╋━━╋━━╋━━━╋━━━╋━━━╋━━━╋━━━┫┃开始┃┃┃┃┃┃┃┃┃┃4000┃┃┃┃┗━━━━┻━━┻━━┻━━┻━━┻━━┻━━┻━━┻━━┻━━━┻━━━┻━━━┻━━━┻━━━┛现有=6ABC=C单位=千尺安全存货=3提前期=8周订货量=12件┏━━━━┳━━┳━━━━━━━━━━━━━━━━━━━━━━━━━━━━━━━━━━━━━━━━┓┃外购管子┃过┃周┃┃┃┣━━┳━━┳━━┳━━┳━━┳━━┳━━┳━━━┳━━━┳━━━┳━━━┳━━━┫┃#186┃期┃14┃15┃16┃17┃18┃19┃20┃21┃22┃23┃24┃25┃┣━━━━╋━━╋━━╋━━╋━━╋━━╋━━╋━━╋━━╋━━━╋━━━╋━━━╋━━━╋━━━┫┃需求┃┃┃┃┃┃┃┃┃┃3┃┃┃┃┣━━━━╋━━╋━━╋━━╋━━╋━━╋━━╋━━╋━━╋━━━╋━━━╋━━━╋━━━╋━━━┫┃将收┃┃┃┃┃┃┃┃┃┃┃┃┃┃┣━━━━╋━━╋━━╋━━╋━━╋━━╋━━╋━━╋━━╋━━━╋━━━╋━━━╋━━━╋━━━┫┃将有┃3┃3┃3┃3┃3┃3┃3┃3┃3┃--┃--┃--┃--┃┣━━━━╋━━╋━━╋━━╋━━╋━━╋━━╋━━╋━━╋━━━╋━━━╋━━━╋━━━╋━━━┫┃要补┃┃┃┃┃┃┃┃┃┃12┃┃┃┃┣━━━━╋━━╋━━╋━━╋━━╋━━╋━━╋━━╋━━╋━━━╋━━━╋━━━╋━━━╋━━━┫┃开始┃┃12┃┃┃┃┃┃┃┃┃┃┃┃┗━━━━┻━━┻━━┻━━┻━━┻━━┻━━┻━━┻━━┻━━━┻━━━┻━━━┻━━━┻━━━┛图6-13物料需求计划──#9P灯与组件#418插头装配件用在各种灯中,从每一MPS接收需求,包括从#9P灯的MPS。为了明晰,这些需求单独地显示在第16、19、22与25周。显然,238第238页共238页n其它各周中对#418插头的需求是来自制造几种别的灯的MPS。由于它是一简单子装配件,插头的提前期只有一周,但它是重要的A类物品。因此,其订货量小,是3周的供应量(期间订货量)。外壳#219只用在这一插头装配件,它是B类物品,提前期2周,因为需进行热处理作业。外壳的EOQ经计算为4000件;由于需求为每批1200件,虽然未计划安全存货仍有富余的库存。#186管子也只有一个父件即外壳,它是C类物品,必须以12,000尺为最小批量来订货。计划有安全库存以对付供应商误期或不好的质量。从所示的需要3000尺管子来制成4000件外壳可以反映出度量单位的变换与每件所需管长。图6-13中有些东西是值得注意的:1、使用了简单的措词──将收、将有等等。如果更常使用类似的简单术语,许多用户误解与迷惑的问题将可以避免。2、图中表明为了满足在第25周制造500件#9P灯的需求,#186管子现在就要订货。这总的提前期11周就是在此组件的多层结构中涉及的所有提前期之和。过渡期间的任何变化(设计,大于正常的订货,记录误差等等)将不仅影响已计划订单而且影响已发放的订单。3、物料清单、现有余额与未了结订货量中的误差,缺乏按计划去生产所需物品的能力或纪律,报废与返工等将破坏这种计算的优美与使用价值。4、#186管子计划有安全存货,这使得已计划补货订单在真正需要它的9周以前就要安排日程──而它的提前期本来只有8周!虽然MRP能处理计算与重新编制计划,若不能解决制造与采购问题其代价是非常高昂的。5、批量与需求不配合会造成昂贵的过量库存,如#219外壳的情形。6、在任一时间期间中的需求数据与订货量同该期间中任一具体日子无关。它只是意味着“该周中的某一时间”。当使用日历日期代替周号来标志期间时,必须采用某种惯例;它通常就是第一天或末一天。精确度与计划编制是不能兼容的。软的(计划用)数据不能是精确的;硬的(执行)数据必须精确、及时更新与准确。第二册充分讨论这个问题。原理26.MRP不过是把制造的基本逻辑机械化。图6-13说明展开过程是如何从MPS开始往下进行的。通用组件需求来自所有产品的MPS,它们被累计在每一恰当的时间期间上。当全部需求已被总计后,可用现有库存(减去安全存货,如果有的话)一期一期地减之以需求量。在恰当的期间加上已发放而未了结的订货(将收)。在推测可用数(将有)变为负数的期间,安排一已计划订单要被完成(要补)。如果事先并未扣除安全存货,这些订单将安排在可用量变得小于安全存货的那个期间。已计划订单的发放期间(开始)可通过从“要补”期间减去计划提前期而确定。当这些计算对总需求已被累计(如被其低层代码所指示的)的所有第1层物品均已完成后,其开始──订货数量就作为需求落到第2层物品上,于是对现已提出了总需求的物品重复地进行净需求计算与时段的划分。注意是父物品的已计划订货而非其需求确定组件的需求。这样,这些计算就一层一层、一期一期地连续进行直到MPS中物料清单中与计划视界内所有组件与所有期间都被包括在内。其结果是一充分一体化的计划,何时各种物料应被购入并运动通过一工厂以支持该MPS。原理27.物料计划只是发起获得物料的过程;执行计划才使该过程得以完成。238第238页共238页n对MRP的改进为了帮助人们使用MRP,多种改进已被增加到刚刚叙述过的基本的、优美的程序。每种改进的威力与潜在的困难将在第二册中更充分地讨论;这里只要指出只有当真正有需要并且使用者充分理解它们时才应该去使用它们。不必要的复杂化增加的是成本而非价值。随着一层一层的计算顺着物料清单自上而下地进行与一次一次地为已计划订单补偿其提前期,数据发生在其中的视界会变得越来越短。有多种视界──填充计算(horizon-fillercalculations)可用来扩展数据通过全部计划视界的各个层次。其中典型的是每期间的平均需求与重复前4(或多或少)周。由于该项计算所提出的任意数据会影响低层的已发放订单的时机与数量,选择数据时应加小心。为提供例外报告,可使用多种行动通知(actionnotices)去提醒用户注意具体情况而不要求他们去研究每一组件显示。选用它们的应注意事项与使用这类通知作为系统健康状况的诊断工具包括在第二册中。虽然在现代MRP软件包中还有别的许多行动通知,但常用的有:ReleaseOrder发放订单OrderPastDue订单过期Datamissinginthisfield此栏遗漏数据ExpediteOrder赶制订单NoRequirements无需求DelayOrder延迟订单Cancelorder取消订单Futureordercoversthisrequirement未来订单包括此需求溯源(Pegging)是识别生成着一种组件需求的父物品的技法。来自几种父物品的对一种组件的需求在一单独期间表现为其总计数。MRP程序中的屏幕当打印时并不表示父件──组件关系但分别说明每物品的数据。用户往往需知道哪一种父件引起了多大需求。特别是当没有足够的组件存货可用之时。当然一份BOM反查表将显示所有的父件但在关键期间中可能只涉及一种或两种。溯源在组件屏幕上提供信息,如图6-14所示,它直接引导用户到正确的父件。这种溯源叫完全单层溯源(fullsingle-levelpegging),它为一种组件识别时间期间、父物品与所需数量。当多种物品通用于许多父件而且这些父件被频繁地订货时,这要求大的数据存储容量与长的打印时间。注意一种父件将多次出现于每一组件的屏幕上。由于父件的屏幕也可供用户使用,采用部份单层溯源(partialsingle-levelpegging)可以节省文档空间与打印时间,部份单层溯源只给出引起需求的父件的零件号。还可以进一步限制屏幕只显示一个短视界中涉及的父件。第二册包括其它用途与溯源时的注意事项。┏━━━━━━━━┓┏━━━━━━━━┓┃周┃┃周┃MPS┣━━┳━━┳━━┫MPS┣━━┳━━┳━━┫#7W┃14┃15┃16┃#7D┃14┃15┃16┃┣━━╋━━╋━━┫┣━━╋━━╋━━┫代码#276┃50┃┃┃代码#281┃┃75┃┃━━━━━━┻━━┻━━┻━━┛━━━━━━┻━━┻━━┻━━┛┏━━━━━━━━━┓┏━━━━━━━━┓238第238页共238页n┃周┃┃周┃MPS┣━━━┳━━┳━━┫MPS┣━━┳━━┳━━┫#9W┃14┃15┃16┃#9D┃14┃15┃16┃┣━━━╋━━╋━━┫┣━━╋━━╋━━┫代码#243┃100┃┃┃代码#262┃┃60┃┃━━━━━━┻━━━┻━━┻━━┛━━━━━━┻━━┻━━┻━━┛┏━━━━━━━━━┓┏━━━━━━━━━┓┃周┃┃周┃MPS┣━━━┳━━┳━━┫MPS┣━━┳━━━┳━━┫#11D┃14┃15┃16┃#11P┃14┃15┃16┃┣━━━╋━━╋━━┫┣━━╋━━━╋━━┫代码#384┃250┃┃┃代码#385┃┃165┃┃━━━━━━┻━━━┻━━┻━━┛━━━━━━┻━━┻━━━┻━━┛自制插头┏━━┳━━┳━━┳━━┓装配件┃过┃┃┃┃#418┃期┃14┃15┃16┃┏━━━━╋━━╋━━╋━━╋━━┫┃需求┃┃400┃300┃500┃┣━━━━╋━━╋━━╋━━╋━━┫┃将收┃┃┃┃┃┣━━━━╋━━╋━━╋━━╋━━┫┃将有┃700┃300┃--┃700┃┣━━━━╋━━╋━━╋━━╋━━┫┃要补┃┃┃┃┃┣━━━━╋━━╋━━╋━━╋━━┫┃开始┃┃┃┃┃┗━━━━┻━━┻━━┻━━┻━━┛被溯源的:14周15周16周#276-50#281-75#314-500#243-100#262-60#384-250#385-165图6-14溯源需求──插头装配件#418在某些情况下,希望使MRP程序正常地处理已计划订单的方法归于无效。例如,完全成套的组件数可能少于要完成下一批某一父件的正常订货量所需的数量,或某一物品的下一批要求在短于计划提前期的时间内去完成。由于若干原因可能不希望在现行时间去发放不变订单。不变已计划订单(firmplannedorder)强迫计算机对任何这样称呼的订单要接收特殊的提前期或订货量。图6-15比较MRP程序处理已计划订单、已发放订单与不变计划订单的方法。由于这种特殊订单搞混了该系统的正常逻辑,它们应该有节制地被使用而且只应由合格的用户来使用。第二册中包括有关于各种特殊订单以及其它改进的进一步评论。238第238页共238页n┏━━━━━━━┳━━━━━━┳━━━━━┳━━━━━━━━━━━━┓┃是否展开到┃是否自动重新┃是否生成例┃用户对数量、开始与需用日┃┃较低层?┃安排日程?┃外信息?┃期有无控制?┃┏━━━━━━╋━━━━━━━╋━━━━━━╋━━━━━╋━━━━━━━━━━━━┫┃已计划订单┃是┃是┃否┃必须使用MRP程序中的规则┃┣━━━━━━╋━━━━━━━╋━━━━━━╋━━━━━╋━━━━━━━━━━━━┫┃已发放订单┃仅当首次发放时┃否┃是┃是┃┣━━━━━━╋━━━━━━━╋━━━━━━╋━━━━━╋━━━━━━━━━━━━┫┃不变计划订单┃是┃否┃否┃是┃┗━━━━━━┻━━━━━━━┻━━━━━━┻━━━━━┻━━━━━━━━━━━━┛图6-15MRP的订单处理分配当已计划订单被发放去采购或生产时,MRP数据中要作些特定的更改。对于外购物料,这些更改比较简单而且很容易说明。使用图6-13中的#186管子为例,决定发放一采购订单给供应商将带来1、把“开始”与“要补”这两行的订货量(12千尺)移到第22周中的“将收”这一行。2、对第22周以及所有以后各周(当然,到下一个需求为止)“将有”行的0更改为12(千尺)。这些更改通常由一叫做“订单发放”的计算机子程序完成。对一外购物品,不需作更多的事了。然而,对自制的组件,情况要复杂得多,因为它们本身也有组件。删除已计划订单而加上已发放订单的行动与采购物料时所采取的行动是一样的。然而,已计划订单生成“开始”周中对组件的需求而已发放订单显示该订单要完成的那一周里的数量。为保持父件记录与组件记录相平衡,(Orlicky把它叫做“维持层次间的平衡”),用来生产父件已订货量所需的各种组件要被分配(allocated)(也叫被保留reserved,被抵押mortgaged与被分派assigned)。办法有二:1、最普通而且最容易的方法是用一单独的文件带上其中的各种数量出现在MRP屏幕的标题中。任一组件的已分配量被合并在一组。倘若用户要识别同个别父件订单相伴随的具体数量,他必须做溯源。图6-16表示把第18周#418插头装配件的已计划订单改为不变已计划订单与为此而分配#219外壳的行动。现有=700单位=件提前期=1周ABC=A安全存货=0订货量=3周┏━━┳━━━━━━━━━━━━━━━━━━━━━━━━━━━━━━━━━━┓自制插头┃过┃周┃装配件┃┣━━┳━━┳━━┳━━┳━━━┳━━━┳━━━┳━━━┳━━━┳━━┫#418┃期┃17┃18┃19┃20┃21┃22┃23┃24┃25┃┃┏━━━━╋━━╋━━╋━━╋━━╋━━╋━━━╋━━━╋━━━╋━━━╋━━━╋━━┫┃需求┃┃400┃300┃500┃400┃300┃500┃400┃300┃500┃┃┣━━━━╋━━╋━━╋━━╋━━╋━━╋━━━╋━━━╋━━━╋━━━╋━━━╋━━┫┃将收┃┃┃┃1200┃┃┃┃┃┃┃┃238第238页共238页n┣━━━━╋━━╋━━╋━━╋━━╋━━╋━━━╋━━━╋━━━╋━━━╋━━━╋━━┫┃将有┃700┃300┃--┃700┃300┃--┃-500┃-900┃-1200┃-1700┃┃┣━━━━╋━━╋━━╋━━╋━━╋━━╋━━━╋━━━╋━━━╋━━━╋━━━╋━━┫┃要补┃┃┃┃1200┃┃┃┃┃┃┃┃┣━━━━╋━━╋━━╋━━╋━━╋━━╋━━━╋━━━╋━━━╋━━━╋━━━╋━━┫┃开始┃┃┃1200┃┃┃1200┃┃┃1200┃┃┃┗━━━━┻━━┻━━┻━━┻━━┻━━┻━━━┻━━━┻━━━┻━━━┻━━━┻━━┛现有=2800单位=件提前期=2周ABC=B安全存货=0订货量=4000┏━━┳━━━━━━━━━━━━━━━━━━━━━━━━━━━━━━━━━━┓自制外壳┃过┃周┃┃┣━━┳━━┳━━┳━━┳━━━┳━━━┳━━━┳━━━┳━━━┳━━┫#219┃期┃17┃18┃19┃20┃21┃22┃23┃24┃25┃┃┏━━━━╋━━╋━━╋━━╋━━╋━━╋━━━╋━━━╋━━━╋━━━╋━━━╋━━┫┃需求┃┃┃┃┃┃1200┃┃┃1200┃┃┃┣━━━━╋━━╋━━╋━━╋━━╋━━╋━━━╋━━━╋━━━╋━━━╋━━━╋━━┫┃将收┃┃┃┃┃┃┃┃┃┃┃┃┣━━━━╋━━╋━━╋━━╋━━╋━━╋━━━╋━━━╋━━━╋━━━╋━━━╋━━┫┃将有┃2800┃1600┃1600┃1600┃1600┃400┃400┃400┃-800┃┃┃┣━━━━╋━━╋━━╋━━╋━━╋━━╋━━━╋━━━╋━━━╋━━━╋━━━╋━━┫┃要补┃┃┃┃┃┃┃┃┃4000┃┃┃┣━━━━╋━━╋━━╋━━╋━━╋━━╋━━━╋━━━╋━━━╋━━━╋━━━╋━━┫┃开始┃┃┃┃┃┃┃4000┃┃┃┃┃┗━━━━┻━━┻━━┻━━┻━━┻━━┻━━━┻━━━┻━━━┻━━━┻━━━┻━━┛图6-16订单发放与分配2、一个类似MRP屏幕上需求数据的分时段文件可允许在希望时发放未来的订单而无需像单独的标题文件那样去办理对所有组件的即时需求,在订货反复无常因而经常早点发放订单是适宜的场合,这将是有用的。当父件的已计划订单被转换为已发放订单时,已分配量代替了对组件的需求。这种情况是暂时的,只存在到已分配量从存货库存被交货到在制品为止。当实际的发料被报告时,现有量与已分配量都要减去已发量。如果这就等于订货量与分配量,MRP屏幕数据保持平衡。如果实际发出数少于订货量与分配量,应生成一欠交申请以确保余额的交货除非现在的订货量被减少了;在那种情况下这一订单上剩余的分配余额必须被删除。MRP重新运行时将重新平衡该父件的已计划订单以确认父件订单上这一较小的数量。如果实际发放量超过了已分配量,必须删除超额的已分配量以免影响陈述其它已分配量。被发放的超过量被MRP看作是一种库存“损失”而且──当重新运行时──它将提出未来的已计划订单除非找到某种方法来考虑该多发量。为了避免做许多修修补补的调整,执行计划中的纪律是不可缺少的。分配例行子程序,不论是单独的还是分时段的,提供一种确定是否有全部所需组件可用来发放一订单的极好方法。如果缺少任一物品,它将被“将有”(或“推测可用数”)数据中出现负数揭露出来。这叫做在纸上中转集散(stagingonpaper),它允许使用正式的计划系统来提出深入到所希望的遥远未来的缺料单而无需实际地隔离物料。好处是明显的。分配程序既是一种计划技法也是一种执行技法。后一种238第238页共238页n应用将在第二册充分讨论。MRP的更新手工的物料计划,除了难于一体化之外,实际上几乎从来也不是及时更新的。销售预测中的变化,新设计的发放与其许多其它因素,就是不可能被很快地处理。计算机程序的开发提供了得到充分一体化与通过频繁地重新运行全部数据而保持更加及时更新的能力。一种方法叫做重新生成(regeneration),它放弃一份计划而提出一份全新的计划。由于要求长时间的计算机运行,通常每周或以更长间隔如此做一次。有经验的MRP用户通常提出能更加具体与及时地去计划数据并在一周内更均匀地分配计算机运行的希望。这可以用只运行于数据中变更部份的程序来办到。一种方法叫需求更改(requirementsalteration),它引进并且只处理MPS中的变化;它使用新近被更新的文件(物料清单、现有与已订货余额、安全存货、提前期,等等)中可以找到的最近信息。MPS未发生更改的产品在MRP的展开中将不予以处理。该技法特别适用于在计划视界远端的时间期间中当这些时间期间移动进入计划视界以内时要加进MPS数据的场合。它对集中注意力于所需行动是有用的,因为所生成的行动通知是由于引进了MPS更改加上有关组件可用性的变化而引起的。当一个新的计划期间进入视界或当MPS发生了显著更改时,往往运行需求更改。如果在各个别事务报告有报废、记录误差或原计划数据有其它显著偏离之后让系统重新计划数据,则可以引进更多的计划灵活性。定期运行时,这叫做成批净改变(batchnetchange)。在MPS更改与偏离频繁的场合,可每日运行净改变。在更为稳定、有纪律的环境中,每半周、每周甚至每二周重新计划一次就足够了。通常定期地运行重新生成程序以清洗累积误差;随着需求更改与净改变事务处理中更良好的纪律被制度化,重新生成的周期通常被延长。第二册包括这些技法的应用与重新计划对比于执行活动的更深入的讨论。图6-17对比MRP程序可被更新的三种方法。┏━━━━━━┳━━━━━┳━━━━━┓┃重新生成┃需求更改┃净改变┃┏━━━━━━╋━━━━━━╋━━━━━╋━━━━━┫┃库存未了结┃┃┃┃┃订单被更新┃是┃是┃是┃┣━━━━━━╋━━━━━━╋━━━━━╋━━━━━┫┃全部主生产┃┃┃┃┃计划被展开┃是┃否┃否┃┣━━━━━━╋━━━━━━╋━━━━━╋━━━━━┫┃MRP运行┃每周每二周┃每日┃┃┃的频度┃每月(难得)┃每半周┃每日┃┣━━━━━━╋━━━━━━╋━━━━━╋━━━━━┫┃每一事务被┃┃┃┃┃分析的效果┃否┃否┃是┃238第238页共238页n┗━━━━━━┻━━━━━━┻━━━━━┻━━━━━┛图6-17MRP的更新订货生产作业中的MRP客户定制产品的制造商曾经迟迟未采用MRP程序。这主要是由于MRP被误认为只是一种全视界、典型的净、分时段的、多层次技法,因为大多数文献是这样说的。纯订货生产产品的制造商(真正的单件或小批生产车间),包括船舶、飞机、特种机床与电子单元、导弹与重型建筑机械,它们难于开发出一传统的MPS;它们的产品产量很低(即使大于1的话)而且是间歇地生产的(即使多于1次)。其物料清单零零碎碎地被开发与发放,往往直到该产品被发货才算是最终的与完全的。设计更改频繁,许多更改发生在接收检验时的最后时刻。同时,大多数这类制造商正在计划对外购与自制品都只使用毛需求量与很宽松的提前期。他们只使用手工的或粗糙的计算机子系统,只具有很小的能力去算出已经可用的物料。因此,他们认识到MRP的逻辑可以应用但并不清楚如何去应用它。MRP的应用要求:1、对于重复生产的产品,即便它完全是客户定做的,要有属物料清单。2、由组件设计按尽可能满足计划人员所需的日程发放部份物料清单以使他们去订货物料与安排设施。3、由工程设计、计划、采购与生产人员共用一个物料清单文件。4、较宽的时段(几周与几月)5、缓冲度最小的提前期当客户允许的提前期明显地短于采购与加工物料所需的总时间时,必须在库存中备有某些外购件与自制件。既然它们的需求不能由标准MRP程序来计算,这些物料的获得与控制必须通过1、经典的或分时段的订货点技法(见第5章)2、在MRP中使用由属MPS驱动的(见第7章)模块式计划用物料清单。在发放物料清单信息,管理设计更改,处理事务,报告收货与发货,维护准确的库存与未了结订单状态以及特别是调整能力以处理会变动的负荷等活动中,严格的纪律是不可缺少的。一个具有重新制订计划能力的一体化的MRP程序对于订货生产产品不仅是可以应用的,而且是需要的。重复性制造业中的MRP难于应用MRP程序的谱中的另一端是重复生产型公司,它们往往在一个流程中生产大量很不相同的离散产品。典型产品是汽车、家用电器、电视机、无线电设备、药品、化妆用品以及精细化工产品。这里的基本困难在于传统的MRP对制造物品需要有离散的订单,而这些公司是用每班或每日的生产速率与到某一具体日期的累计总量来考虑问题的。对外购物料没有困难,它们可按通常的方法来计划。计划问题也可通过采用浅的物料清单与在原料与成品之间不存或少存作为半成品、中间体、子装配件等产品的存货而大大简化。图6-18表示通过使用作业天数、需求、收货与已计划订货(要补与开始)等的累计总量可以使MRP如何适应于重复性制造。注意“将收”与“累计将收”表示已发放订单的数据;“要补”与“开始”在这时只是已计划而238第238页共238页n已。在此期间,有两个节假日,分别落在第16周与第22周。在第18周与22┏━┳━━━━━━━━━━━━━━━━━━━━━━━━━━┓自制马达┃过┃本周*假日┃┃┣━━┳━━┳━━┳━━┳━━┳━━┳━━┳━━┳━━┫#13245┃期┃14┃15┃16┃17┃18┃19┃20┃21┃22*┃┏━━━━╋━╋━━╋━━╋━━╋━━╋━━╋━━╋━━╋━━╋━━┫┃累计天数┃┃69┃74┃78┃83┃88┃93┃98┃103┃107┃┣━━━━╋━╋━━╋━━╋━━╋━━╋━━╋━━╋━━╋━━╋━━┫┃需求┃┃12┃12┃12┃12┃17┃17┃17┃17┃22┃┣━━━━╋━╋━━╋━━╋━━╋━━╋━━╋━━╋━━╋━━╋━━┫┃累计需求┃┃140┃152┃164┃176┃193┃210┃227┃244┃266┃┣━━━━╋━╋━━╋━━╋━━╋━━╋━━╋━━╋━━╋━━╋━━┫┃将收┃┃12┃12┃10┃12┃┃┃┃┃┃┣━━━━╋━╋━━╋━━╋━━╋━━╋━━╋━━╋━━╋━━╋━━┫┃累计将收┃┃132┃144┃154┃166┃┃┃┃┃┃┣━━━━╋━╋━━╋━━╋━━╋━━╋━━╋━━╋━━╋━━╋━━┫┃将有┃7┃7┃7┃5┃5┃8┃11┃14┃17┃11┃┣━━━━╋━╋━━╋━━╋━━╋━━╋━━╋━━╋━━╋━━╋━━┫┃要补┃┃┃┃┃┃20┃20┃20┃20┃16┃┣━━━━╋━╋━━╋━━╋━━╋━━╋━━╋━━╋━━╋━━╋━━┫┃累计要补┃┃132┃144┃154┃166┃186┃206┃226┃246┃262┃┣━━━━╋━╋━━╋━━╋━━╋━━╋━━╋━━╋━━╋━━╋━━┫┃开始┃┃┃┃┃20┃20┃20┃20┃16┃20┃┣━━━━╋━╋━━╋━━╋━━╋━━╋━━╋━━╋━━╋━━╋━━┫┃累计开始┃┃144┃154┃166┃186┃206┃226┃246┃262┃282┃┗━━━━┻━┻━━┻━━┻━━┻━━┻━━┻━━┻━━┻━━┻━━┛图6-18用于重复性制造业的累计式MRP周,需求将两次增加,每次每周增加5件,但生产只在第18周增加1次,从每周12件增到20件。这将使库存从7件增长到17件直到需求再次改变,但在这一库存用完之前生产无需更改。生产与需求可以紧密配合是MRP应用的典型情况。注意提前期短,这也是重复性制造的典型情况。图中所制造的物品是家用电器中使用的一种电动机。当最低生产速率比需求大得多时,该物品将间歇地生产,开工时建立起库存而停工时库存下降。日产量、日需求与容许的高低库存水平控制着生产运行的时机与期间数。为显示各种累计总量并按给定的每期间的生产量安排生产日程,计算机程序只需作很小的修改。过程工业中的MRP有各种各样的过程工业,从石油精炼业,它连续地运行专用、设备以生产狭窄的一大类产品,到食品加工业,它间歇地运行通用设备以生产宽广的多类产品。许多生产化工品、药品与化妆品的工厂则把几种类型结合起来。间歇地成批生产这类238第238页共238页n产品时,可不加修改地应用传统的分时段MRP。使用不常中断的流水线设备来生产多类产品时(纸、香烟、软饮料),可使用前面为重复性制造讨论过的修改过的MRP程序。触媒的裂解单元,管道蒸馏室与精炼作业中的石油化工工厂与粘土、水泥与钢铁厂的连续作业只要求间歇地进行相当简单的计算以平衡销售、生产与库存,为输入原料设定流量并提出对包装物料与发货容器还有非常少量的触媒、填料、添加剂或合金元素的需要量。这种少量的计算要求很小的能力,虽然一种正式的系统方法总是比零碎的手工技法产生的结果要好些。这些作业中真正的问题在于过程的控制(从而控制住产品的质量),及时地对原料组成中的变化作出反应,对付无弹性的能力并在能力太小与太大之间求取一种平衡。MRP:技法与逻辑没有哪一种MRP的格式是最好的;只有它的逻辑才是普遍适用的。必须确定它的应用方法使它适合于运行。这里是具有独创性的、有效的适应的一例。一家著名的粗陶器制造商每周生产1000吨以上大约1800类物品加上各种成套产品的频繁促销。它们全由12种粘土物品、玻璃料与釉料,加上装饰性移画印花法所用的图案与包装材料制成。12种原料的供应计划如下:1、粘土需求量由各个加工设施中反映粘土使用率与人员配备水平关系的各种比率计算出来。这些计算结果被定期地用实际消耗量来核对并校正以反映最近的绩效。这就用粘土需求量回答了我们将制造什么、制造多少与何时制造等问题。2、可以用物料清单来表示成品由素坯制成,素坯又由用粘土捏成的原坯制成。由于破碎、多孔性与其它原因有的批其损失可达25%,估计每单位父物品需用多少组分量是个主要问题。因此,在原料订货时不使用清单。3、原料的收进与存储用货车、料斗卡车与货架上的袋子。每天由物料计划人员在他从家里到办公室的途中实地盘存。该计划员保有简单的卡片记录表明现有量、发出量、收进数以及已订货事务与余4、关于未了结采购订单上诸如物料规格号、供应商号、采购订单号、火车或卡车运货单号等事实的细节被保管在到期日期箱中一个大的台历式临时登记簿上。在途物料每天要同火车与卡车发运人核对,并在发运前3天同供应商核对。不需采购申请单,计划人员就是采购人。这回答了何时我们将收到更多物料的问题。5、根据供应商提前期与所需发货天数(火车约2周,卡车约一天),计划人员用电话联系特定的供应商按总括采购订单发放新的订单。计划人员根据检查与分析卡片数据,使用从设定的而且在每周的生产会议上修订过的人员配备水平与各种有关的比率计算出来的需求回答了何时我们需要更多物料的问题。请把这一简单办法同在经典的屏幕上的完全、净、分时段的MRP相比较。然而,一个人(另有一人受训作后备)竟然如此有效地使用这种办法使得该公司平均只用1天半的原料供应,而且只需3天的供应量作为最大存储能力。这些人员并不知道他们所做的就叫做MRP与JIT!原理28.MRP的逻辑是普遍适用的;它的应用方法要看具体的环境而定。MRP技法有三件很有价值的工作可做:1、建议(不是独断)发放订单的恰当时机。2、指明需要补货的恰当日期并保持这些日期在订单处理期间是有效的。3、提供信息去帮助能力需求计划与机器和加工中心的加载工作。238第238页共238页nMRP不是一个系统。它只是系统中的一种技法(虽然是重要的一种)。其成功使用取决于本书与第二册中详细讨论的许多因素。MRP的使用中缺乏成功的理由有:1、它是一个不完全系统的一部份(见第1章)2、它被一无效的或管理不善的MPS所驱动(见第7章)3、数据不准确4、物料清单没组织好(见本章与第7章)5、用户不合格238第238页共238页n七.主计划计划的阶梯结构制造企业中的计划过程是对或多或少紧密地一体化的多层计划的一系列修订。由于种种原因,各家公司在他们的阶梯结构中采用不同数目的层次并给这些层次以各种名称。在1970年代里,由于经理、顾问与教育家们对这一计划过程的密切关注,导致了标准名称的开发并对要求作计划的诸功能有了更明确的识别。这些成果归纳如图7-1所示。计划视界企图回答战略计划我们现在是在什么行业之中?5-10年我们要到什么行业中去?为了作好准备现在必须做成什么?下一步将要求什么?业务计划现在产品市场占位如何?2-5年哪些正在下降?降多快?哪些是成熟的、稳定的?哪些是成长中的?有多快?需要什么新产品?需要采取什么行动?生产计划现在工厂利用得如何?2-5年对它有什么要求?涉及什么新技术?将引进什么新产品?将淘汰什么产品?将需要什么新工厂、新设备?主生产计划要制造什么具体产品?多少?何时?1/4-1年需要什么其它物料?多少?何时?存在什么能力制约?存在什么物料约束?图7-1计划编制的阶梯结构战略计划(Strategicplans)从企业基本性质与管理者希望它在下一个五到十年间采取的方向的考察开始。相当具体的行动被定义,当然随着时间的流逝它们要服从于进一步的定义与修改。例如新技术与扩展地理市场可能被当作目标;后来的实际发展情况可能要求对未来的计划作很大的修改。战略计划指出总的方向,而非达到彼岸的具体道路,而且通常并不设定详细的目的。这种计划工作是有关总的业238第238页共238页n务的。每一主要组织群体──市场营销、制造、工程设计与财务──必须有它自己的战略计划。在已往,这些计划往往一体化得很差而且往往不是互相支持的。当着市场营销正沿着进攻一个需要灵活性与多种低产量产品的宽广市场的某一部份的方向移动之时,制造部门却在为了低成本而努力,它要求稳定的需求、高产量与标准化的产品。还有,在已往,最高管理者的注意力是放在兼并、获得与放弃上,他们根据企业的财务绩效是产生着大量现金流的“现金牛”还是产生着不良的投资报酬来买进或卖出它们。虽然兼并会带来实际利益(实际资源的更好利用、需求循环的平滑化、增加市场份额、获得新技术),并且虽然有的企业活得超过了它们的经济寿命(制造马车与木桶),这种对财务判据与操纵的着迷忽视了通过利用现代技法的更好的计划与控制可以改进经营。彼德.德鲁克说过战略计划涉及现在决策的未来效果,而不是论述未来的决策。它不是企图去预测在遥远未来的某些时候将要完成什么,而是企图去决定现在必须完成什么以准备一家公司更好地去把握未来可能带来什么,而更重要的是去有利地影响未来。它的重点在于整个企业,它现在是什么,它应该是什么以及为了达到那里现在必须完成什么。战略计划设定大的框架,所有其它的计划与执行将在这框架内完成。它以尽可能宽的措词来定义公司的事业:不是制造玻璃瓶子而是提供包装物,不是精炼石油而是满足能源需求。它识别强点与弱点以发挥前者而弥补后者。它关注环境、竞争、政府、资源的可得性与类似的因素甚于关注内部作业。探究对不愉快的意外的各种反应的应急计划是战略计划不可缺少的一部份。在第二卷中将对战略计划作更多评价,但彻底讨论此题目超出了这两本书的范围。企业(经营或业务)计划(Businessplans)着重于产品与市场。最高管理者的角色是去协调各个别部门的计划。市场营销部门应定义公司在市场中的角色(主要轮廓与特殊地位相对),为主要产品系列设定所希望的市场份额目标,识别值得分配更多资源的产品系列,定义所需新产品的特征,建立分配渠道并设定客户服务水平目标。制造部门应将市场营销部门的计划翻译成以概括、笼统的措词表达的在人员、设施、设备与物料方面所需的支持。细节不大可能准确到使人有足够理由化费精力去开发它们。工程设计部门应该提出技术发展的方向以及这可能对产品与加工过程具有的潜在影响。他们还应识别为了未来利益而要求现在就采取行动的在研究、开发与应用方面的机会。财务计划则把其它部门的计划转换成所需的资本规划、现金流、主要的预测与利润估算。企业计划是从概括、笼统的战略计划转变为较为详细的生产计划的过渡。过份强调(表面上)精确的财务数据与过份地依赖可见因素(诸如设备的成本)已经在若干现正下降的行业中僵化了创造性与冒险性。恐怕比考虑做什么的风险更为重要的是应当考虑不做什么会有什么风险。在做未来的预测时风险是固有的;企业计划不应强调减小风险,它应识别使冒风险的利益最大化所需的行动。生产计划(Productionplans)开发支持着企业计划的下一个详细层次。它的视界通常与企业计划相同,但着重在为支持企业计划所要求的设施与生产方面。计划的前端(1到2年)特别重要,因为它将同详细作业计划接口。典型的生产计划将被开发如下:第1年,12个月度期间,子系列产品第2年,4个季度期间,系列产品第3年,2个半年度期间,系列群238第238页共238页n第4与第5年,年度总计,系列群生产计划有三项功能:1、更详细地去定义企业计划中的制造部份2、设定制造产品系列的产量3、为作业的管理控制提供基础要回答图7-1中对生产计划所提出的诸问题,需要比通常在企业计划中提供的内容多少要详细一些。企业计划通常用财务措词陈述,但制造需要知道利用工厂的产品件数、未来的负荷与实际的资本预算,这些都是生产计划的一部份。可使用对制造有意义的表达产品关系的当量件数(一台双门冷藏/冷冻箱可能相当于两台标准冷藏箱)来确定能力与成本。使用生产计划中所陈述的系列产品的产量可开发出很适当的管理控制。图7-2表示管理评审中生产计划的一种普通应用。常被称作销售──生产──库存(S-P-I)或生产──销售──库存(P-S-I)报告,它计划与监控成品库存的投入与产出总量。这种报告通过总量成为有效的库存与生产控制的基础。这在第8第9两章详细讨论。这些报告也为提出主生产计划提供数据。主生产计划将在本章后面讨论。┌────────┬──┬──┬──┬──┬──┬──┬──┬───┬───┐│期间│1│2│3│4│5│6│7│8│9│├────────┼──┴──┴──┴──┴──┴──┴──┴───┴───┤│生产(P)│(容限=±¥100)│├────────┼──┬──┬──┬──┬──┬──┬──┬───┬───┤│计划期间│450│450│450│450│450│450│475│500│500││累计││900│1350│1800│2250│2700│3175│3675│4175││实际期间│435│440│450│430│445│430│460│480│475││累计││875│1325│1755│2200│2630│3090│3570│4045││偏差期间│(15)│(10)│─│(20)│(5)│(20)│(15)│(20)│(25)││累计││(25)│(25)│(45)│(50)│(70)│(85)│(105)│(130)│├────────┼──┴──┴──┴──┴──┴──┴──┴───┴───┤│销售(S)│(容限=±¥100)│├────────┼──┬──┬──┬──┬──┬──┬──┬───┬───┤│计划期间│450│450│450│475│475│475│500│500│500││累计││900│1350│1825│2300│2775│3275│3775│4275││实际期间│430│470│480│415│425│460│510│490│480││累计││900│1380│1795│2220│2680│3190│3680│4160││偏差期间│(20)│20│30│(60)│(50)│(15)│10│(10)│(20)││累计││0│30│(30)│(80)│(95)│(85)│(95)│(115)│├────────┼──┴──┴──┴──┴──┴──┴──┴───┴───┤│库存(I)│(期初=¥3000)(容限=±¥200)│├────────┼──┬──┬──┬──┬──┬──┬──┬───┬───┤│计划│3000│3000│3000│2975│2950│2925│2900│2900│2900│││││││││││││实际│3005│2975│2945│2960│2980│2950│2900│2890│2885│238第238页共238页n││││││││││││偏差│5│(25)│(55)│(15)│30│25│─│(10)│(15)│└────────┴──┴──┴──┴──┴──┴──┴──┴───┴───┘图7-2P-S-I报告理想上,每一计划将包有用来同实际绩效相比较的数据而每一绩效报告将显示原计划数据。对战略计划与企业计划这是难办的,而且实际上要间隔相当长的时间才有此必要。对生产计划与主生产计划,它应该定期而且经常地进行。这些计划提供足够的明细信息使这样的比较可用作采取校正行动所需的早期警告信号。例如,在图7-2中,已设定了显著偏差的容限,可以看出虽然库存数据中偏差并未超出容限,但销售与生产二者都偏低了。独立地监视这三个因素将不会如此有效地揭露出真相。许多管理人员喜欢采用如图7-3所示的累计数的图形表示法(为了清楚起见,时间尺度作了位移)。详见第二册。根据经验,生产计划具有下列特征:1、对单件与小批生产车间、间歇生产、过程生产与重复性生产,格式基本上是一样的;但时间期间与视界可能不同。2、MRP的基本逻辑问题也适用于它们。3、超过生产能力去做计划的诱惑不可抗拒──而且对良好结果是致命的情况太多了。4、定义系列与总体时的谨慎思索对良好结果的贡献要比提供能处理更多细节的系统来得大。5、全体管理人员之间的集体协作对健全的计划工作与良好的结果是关键的。生产计划视界的不同部份被使用于不同的目的。视界前端的数据经过转换用来同正在驱动正式物料计划的MPS相比较并同粗略能力需求计划一道作在制品与提前期的投入/产出控制。在视界的较远处,生产计划为雇佣、培训、转移或解雇的劳动力总数提供信息。该同一数据被用于增加、更换或移动资本设备以及扩大或缩小工厂空间。处理新技术的技能与设备通常关系到该计划的中段。资本需求量则要在整个视界上评价。原理29.在计划视界上较远处的数据可以而且应该粗一些、总一些。主生产计划(TheMasterProductionSchedule缩写为MPS)由于主生产计划要驱动集优先级(物料)、能力与成本的计划与控制于一体的正式系统,它比生产计划要更加详细些。MPS中规定的产品必须由具体、个别的BOM来描述。MPS有三种功能:1、把企业计划同日常的作业计划联锁起来。2、为日常作业的管理提供一个“控制把手”。3、驱动正式的、一体化的计划与控制系统。如果没有一个由现代系统提供的健全地一体化的正式的计划编制能力,管理者无法确定他手下对成千种物品作着上百决定的成打的人员是否在为支持公司的战略事业与生产计划而工作着。今天的知识与现代的信息管理系统使得一个充分一体化的多层计划系统成为可能,其特征是:1、从上到下较短的视界与时间期间。238第238页共238页n2、自上而下越来越细。3、能够维持所有计划的完整性的定期重新计划。4、能提出多种计划去满足特定需要。原理30.孤立、不受约束而且多目的的计划比无用还要坏;它们是危险的。MPS着重于要被制造的产品,而且通过详细的计划系统,识别所需资源(物料、劳力、工厂设备与资金)及其需要时机。虽然现已被广泛接受与使用,它的名字起得并不好。主与生产这两个词在这里应用得很恰当;但日程计划(schedule)这个词正当地含蓄着安排时机与细节,它给中层与高层管理人员传达一幅细节的图象,订货日期与其它琐事(对他们而言)。要更换名字现在已经太晚了。然而必须消除他们的误解;MPS提供给他们的是对企业的控制把手之一。MPS的基本目的是去发起获得为实施该计划所需的资源。注意着重点是发起而非完成获得所需物料、人员、设备、资金等等的过程。计划阶段推测何时需要多少什么东西的估计量;执行阶段最后地确定──通常要晚得多──将具体地得到与生产出什么。这是一种极其重要的区别,不只是语义问题。MPS是什么根据定义,MPS是详细陈述在何时要生产出多少物品的计划。因此,任何一家公司的MPS总是计划内物品与每一计划内物品所复盖的时间期间所构成的一个矩阵。所使用的时间期间往往是一周,虽然对大而复杂的产品如发电设备与船舶有时用两周或一个月。有些理论家,被假设的重新安排计划的威力冲昏了头脑,鼓吹以每天作为时段,但这是不实际的;它们可能更精确但不会是更准确。这在第二册第2章中讨论。MPS陈述能够而且应该生产什么;它并不是管理者将喜欢去生产什么的一张希望──表。由于夸大MPS而引起的问题是非常紧迫与严重的。详见第二册。如前所述,MPS为企业管理提供一个控制把手。它是通过提供下列手段、机制与方法而做到这一点的:1、一种授权与控制支持着客户服务、获利能力与资本投资目标的劳动力水平、库存投资与现金流的手段。2、一种协调市场营销、销售、工程设计、制造与财务活动以开发一共同计划与改进集体协作的机制。3、一种调和市场营销及销售方面的需求与制造能力的方法。4、一种度量每一群体在执行共同计划中的绩效的手段。MPS不是什么销售预测不是MPS;它推测客户的需求,而MPS陈述满足这一需求的生产。当间歇地成批生产以满足持续的需求时,当生产平稳而需求是季节性的或起伏不定的时候以及当成品库存正被显著地提高或降低之时,这两者就会有大的区别。只有难得地,当这些情况不存在时,MPS才会与销售预测相同。MPS也不是一个装配或包装日程计划,后者是执行活动。对于消费产品、药品、化妆品、食品、精细化工产品及简单的硬货(BOM中层次与组件少的物品),MPS与完工日程计划在所用数字上可能相同,但在心目中必须明确保持它们的不同概念,以便恰当地为最大利益来应用它们。238第238页共238页n原理31.MPS驱动计划过程,而非执行过程。MPS的输入提出MPS时必须考虑许多因素,它们既有技术性的也有非技术性的,这包括:1、产品是备货生产的还是订货生产的还是两者结合的。2、仓储与生产设施的数目与地点。3、服务件政策。4、客户服务目标。5、组件的厂际转移。6、自制与外购的政策。7、客户订单与需求预测。8、安全存货水平。9、关于雇佣稳定性与工厂利用方面的政策。10、由物料清单定义的产品结构。显然,准备MPS不属文书人员的任务。它是一种高层次计划作业,应被高层经理透彻地理解并由他们来指导。在为MPS开发输入数据时,对备货生产与订货生产产品二者,分时段订货点法的逻辑提供一种同时考虑多个存货地点、需求预测、安全存货水平、已收客户订单与已在进行加工的生产批的有效方法。此技法的机制见第5章,它对完工产品计划的应用将在第二册作更充分的讨论。分时段订货点法的已计划订单输出数据为每种产品提供制订主生产计划的一个起点。也常用S-P-I报告去开发MPS的输入;注意其逻辑同分时段订货点法非常相似。MPS可用两种方法建立:1、表示出已完工并准备好待发货到客户、仓库或所属工厂的最终物品(同MPS一道用来开发MRP输出的物料清单的最高层物品)的数量。2、陈述准备好可用来制造最终物品的成套组件数,该最终物品的数量则陈述在所用时间期间开始的MRP中。这两种方法选用哪一种将根据产品的类型。当一产品有几种功能特色(不只是颜色或包装)可供客户选用时,或如果被客户选用时可包括有多种附属品与附件时,MPS用第2种方法陈述。这类产品包括计算机、机床、汽车、卡车、飞机与重型非公路车辆。对于具有许多通用件或成份的较简单产品,如果完工快时,也使用这种方法。典型例子是钢笔、自动铅笔、电话与电子计算器。当选用第1种方法时,来自分时段订货点法的已计划订单收货数量与时机为MPS提供输入;当MPS陈述完工开始时要用的成套组件数时,使用已计划订单的发放数据。其机制见第3章。MPS必须包括工厂设施上全部显著的需求。这些需求来自客户对产品与服务件的需求,来自分销商、代理商及公司仓储它们的分配中心,来自使用组件或产品的所属设施,并且来自建立这类物品库存的计划(注意当降低库存时,这需求是负的)。勿视其中任何一种需求将使工厂的负荷被显著地打了折扣。在具有多层供──需关系的工厂中,供方车间的MPS必须从用户车间中由MRP程序提出的已计划订单推导出来。例如在纺织厂中,纺纱生产必须有计划去满足织坯布设施的需求,而后者又必须支持完工车间中织物、衣服等等的输出。为这种一体化设施作独立的计划是浪费,特别是如果它们都属于同一公司家族。同理,即使它们属于不同企业而且即使用户工厂只取供方产出的一部份,公司同其供应商238第238页共238页n密切地合作也有实际的好处。外购物料的适时(JIT)交货要求这种类型的合作的计划与执行。不同企业中的MPS在任何企业中主生产计划是否有效的关键在于物料清单的恰当构成以及把MPS的设定选择在物料清单的正确层次上。企业按其物料清单可分为四类:1、从许多组件生产出少数重要的物品2、从许多组件制造出许多产品,它们具有显著程度的共性3、从相对少数组件的子群可以装配出非常多可能的模块组合4、从很少数组件或原料可制造出很多种成品,而且有多种不同的包装这四类物料清单及MPS的正确层次如图7-4所示。第1类企业要求把MPS设定在BOM的顶层;第2类也是如此。主要区别是在第2类中有许多产品具有运用管理评审的实践性。这种评审要求把相似产品的系列归类到一起。第1类中的产品有船舶、公共汽车、大型机床、重型机械、建筑用起重机与卷扬机,还有电梯。第2类产品包括小型家庭用具,厨房与工场工具、电动机、食品、药品与化妆品。第3类包括汽车、计算机、机床、电动机与控制器、家用加温与空调器与农业设备等产品。在这类产品中,客户可为个别特色在许多选件中作出选择,其结果是极大数目的这些选件的不同组合,倘若在第6章的例中,灯具制造商决定向客户提供如图7-5所示的新的一类Rite-Lite灯,相对少数的选择很快导致数字相当的┌─────┐│Rite-Lite││灯│└──┬──┘┌───────┬──────┼──────┬───────┐┌──┴──┐┌──┴──┐┌──┴──┐┌──┴──┐┌──┴──┐│灯泡模块││底座装配件││灯罩装配件││灯罩装配件││成套电缆│└──┬──┘└──┬──┘└─┬───┘└─┬───┘└─────┘│100瓦白炽灯│圆形│光亮的│圆柱形├─────├───├────├────│75瓦日光灯│方形│用花纹装饰的│圆锥形├─────├───├──────├────│3向白炽灯│六角形│综合的│颈状└─────├───├───├────│椭圆形│金属的│自由式└───├───└────│自由式└───图7-5灯的选件大的多种灯。假设任何组合都能制造出来,则灯的种数很容易计算出来:3种灯泡×4种底座×5种灯罩×4种柱子×1种电缆=240种灯238第238页共238页n倘若该制造商决定将灯出口到两个使用220伏电力的外国(不同于美国国内使用的110伏标准电力),而且每个国家要用不同的电缆插头,则灯的种数将是6种灯泡×4种底座×5种灯罩×4种柱子×3种电缆=1440种灯这样许多种最终产品显然不可能去准确地预测并为之制订有效的主计划。MPS不可设在BOM的顶层。对这种产品,MPS的恰当层次应该是设在最终产品的下一层──主要子装配件这一层。对美国国内该灯的总销量可作出合理的预测,譬如说每周2000台。由于每台灯都要用电缆,当然,美国用电缆的MPS就将是每周2000套。然后可根据历史销售数据,再用期望的未来趋势作些修正从而对各种选件占灯总需求的比例作出预测。例如,对灯泡模块:0.5:100瓦白炽灯=1000/周0.2:75瓦日光灯=400/周0.3:3向白炽灯=600/周主要装配件中的个别选件可用同样方法来处理。这一技法叫做模块式计划法(modularplanning),只需提出少得多的MPS,对美国用产品,MPS的总数为:3种灯泡+4种底座+5种灯罩+4种灯柱+1种电缆=17个MPS。加上出口品种时,MPS的总数将增加到22个,仍然是一个可以管理的数字。注意在灯泡模块BOM中的组件实际上将被装配在灯的不同部份之中。插座将被安装在灯柱中,开关安装在底座中同日光灯镇流器装在一起,电线把它们连接起来。但为了制订计划的目的,这些组件被归入一个模块伴随供客户选用的一个具体选件。汽车制造商也用这种方法把空调选件的组件归入一个计划用模块,虽然实际上这些零件是分散在车辆各处的。如前所述,MPS发起获得行动;这些行动在执行阶段被完成。实际上造出来的灯与汽车的具体配置将由客户行使的选择确定。最终装配物料清单将在收到客户订单(往往是代理商、分销商或代理人)之后被发放。如果计划已经生效,所需模块与主要装配件将是可得的。计划永远不会是完善的,健全的计划也不会被完善地执行,所以有某些短缺是意料之中的。把这些短缺减到最小限度并更快地反应它们的方法详见第二册第2章。超量计划(overplanning)MPS以便使短缺最小化的技法见本章下一节。图7-4中的第4类产品包括梳妆用具、化妆品、药品、精细化工产品、照相胶卷、糖果、矿物、石腊与机油等石油产品以及数不清的其它物品。对这一类,很少数原料与外购组分被转换成很多种完工的散装产品,然后往往把它们以不同的包装提供到市场。这一类也包括过程工业在内。由于原料的特征与性能不稳定,收率不确定以及昂贵的资本设备无弹性的生产能力等原因,这一类产品的计划过程不同于其它三类。计划工作不能那样精确而且往往以恰当地利用设备为重而非以库存最小化为重。任何产品系列主计划的恰当层次的选择要取决于三个判据:1、MPS中物品的数目要尽可能地少以改进管理评审与控制。238第238页共238页n2、复盖被该MPS驱动的MRP程序中尽可能多数组件。3、生成关于制造设施,特别是瓶颈供应商与机器或设备中心的负荷的尽可能多的信息。这些判据明显是有冲突的,第1项就反对第2项与第3项。对图7-4中第1类与第3类产品,层次的选择是相当容易的。对第2类产品,需在MPS份数之多与足够的能力与物料计划之间作出妥协。选择产品的系列作为一个单独的MPS项目提供一种好的妥协,因为它们既为设施建立大多数负荷又为通用组件建立需求。如果产品设计工程师与加工过程选择工程师清楚地看到对良好的计划与控制的要求,则计划过程可被大大改善。在这里,集体协作的利益是巨大的,但这一主题超出了这两本书的范围。第3类产品同样地面临着MPS中物品太多的问题。这里,用系列产品也能部份地解决问题,特别是在能力数据中。图7-4表示MPS处于BOM顶上最终产品层之下的某一层次。这是被包装物品的散装产品层次,它能够把MPS的数目减到产品总数的一个小的分数。为满足前述的第2条判据,用第二册第4章中描述的倒排BOM(aninvertedBOM)可以为有麻烦的包装材料提出需求并且也允许利用本章下一节要讨论的超量计划MPS的技法。第3条判据也可用这种技法达到,而且往往是通过使用产品的系列来满足的。原理32.最好的MPS具有最小数目的物品,而且符合足够的物料与能力计划的需要。为了灵活性而超量计划MPS在前节的Rite-Lite灯案例中,为每一种选件开发-MPS是实际的;已列出了每种灯泡选择的数据及每周2000台灯的生产总量。这种灯型选择的估计是平均数;定单的实际组合可能每周有显著变动,例如:100瓦白炽灯:0.3-0.775瓦日光灯:0.1-0.33向白炽灯:0.2-0.4满足任一周中最大需求的灵活性可用一种叫做超量MPS计划法(overplanningtheMPS)的技法。必须强调指出这并不意味着过负荷或夸大MPS;因为生产与维持附加的成套组件所需的物料与能力都必须是可得的。第一种选件的MPS,在使用此技法时,将在某一周中从每周1000这一平均值增加到1400。当需要时,这额外的400套组件将提供库存以满足对这一选件的额外的客户订单。如果1000这一平均需求是正确的,则当客户对这种灯泡的实际需求降到平均值以下时已经用掉的额外成套组件将得到补偿。这种过剩库存类似安全存货,但它是针对使用该技法的每种选件而配套地持有组件的。选择哪一周来安排该超计划量(在本例中是400套)要取决于人们希望这些组件处于什么情况。倘若此超计划量安排在第一周,该计划将使可用已完工组件为投入成品的装配作好准备。倘若,它被安排得远远地,在产品的累计制造提前期的末端,则该计划便将以备有过量的外购原料与低层组件为目标。对于定制的产品,不仅是订货装配产品,这将是此技法的恰当应用。此超计划量可以安排在中间的几周中以充分发挥以半成品或未定型式来持有通用组件或成份的好处。这同第二册第1章中要讲的制造的基本策略有关。为了最有效地使用超量计划来满足客户所需的产品组合方面的变化,可将选件238第238页共238页n模块的BOM重新构成,以区别所有选件通用的组件与每种选件的专用组件。例如,在图7-5的例中,各种灯罩都可通用的组件就有电线(如设计得当,其长度也可一律)、把灯罩弄牢在立柱上的金属箍与钢夹等。超量计划时若使用每种选件的全物料清单则将把这些通用件也多存了许多,但产品组合有变化时通用件是不需要多用的。把专用组件归入另一清单,只对这些组件做超量计划,可使过量的库存仅限于为灵活性所真正需要的物品。注意这要求为每一种选件多生成一个MPS,因为现在要展开两个物料清单(一个为通用件、一个为专用件)。这也使MPS在产品结构中要降低一个层次。在计划过程中将不使用较高层的选件装配件(灯罩、基座与立柱──它们是真正的子装配件)的物料清单与成品灯具的物料清单,在客户真正地订制特定配置之前不应开发它们也不必把它们装入产品结构记录。这些清单是执行清单,是为装配安排日程计划使用的,为存储室申请单或拣料单使用的,为实际生产的记录、核算成本与支付而使用的。为了具有在任意期间内生产总量大于2000件灯具的灵活性,对每一通用组件模块(包括成套电缆)的MPS可以有一个相同的超计划量。当然必须有足够的能力来生产与维持这些物料。倘若为了产品组合上灵活性专用的成套组件已经有了足够的超计划量,就无需再为总灯具量的增加而再提供这些专用组件的附加量。把超量计划技法同MRP程序一道使用,可以估计出为满足市场变化提供灵活性所需的附加的总的投资量。其计算方法详见第二册第3章,它也可用于根据作业计划来准备库存预算。原理33.恰当地构成物料清单是做MPS不可缺少的一部份。MPS的视界对每一产品,必须购入某些原料或组件然后经过制造过程的某种顺序把它们转换为完工物品,如图7-6所示。│BOM││层次│时间───→│├─────────────────────────────┬─┬─┐│0││││最终产品│├─────────────────────────────┴─┴─┘││||│├─────────────────────────┬─┬─┐大块产|│1││││品或子|│├─────────────────────────┴─┴─┘装配件|││||│├─────────────────┬─┬─┬─┬─┐|│2││││││中间体或装配件|│├─────────────────┴─┴─┴─┴─┘|││||│├───────────┬─┬─┬─┐|│3│││││中间体或组件|│├───────────┴─┴─┴─┘|││||238第238页共238页n│├─────────┬─┐|│4│││原料准备|│├─────────┴─┘|││||│├─┬─┬─┬─┬─┐|│5││││││原料|│└─┴─┴─┴─┴─┘|||←────────────────────────────────→最小MPS视界图7-6已计划累计提前时间完成这些工作所需最长的已计划时间跨度,等于关键路径上(有多种叫法:累计提前时间,堆积提前时间,关键路径提前时间)计划提前时间之和,决定了如果要MRP能够为所有组件计划补货订单的话MPS必须扩展的最小视界。在不同行业中这一时间为几个星期到2年或多年。如果MPS至少不扩展到那么远,则对低层组件与原料就必须使用订货点技法。关键路径有时被称为MPS的不变部份(thefirmportion),但这一术语是使人误解的;它含蓄着MPS在此期间不应被更改──但事情不是这样的。在该期间“冻结”MPS,不允许更改,是说1、不管我们是否需要,我们正在计划去制造它。2、倘若我们不作计划就不能制造它。这两种陈述不仅是谬误的,它们是危险的与不必要的。在本章前面讲过,MPS驱动计划系统以发起资源的获取。人们希望由此当执行计划时,所需的物料、劳力及其它资源将是可得的。当然,计划或执行不可能十全十美,在执行阶段总是需要有校正行动去弥补不足之处。在第二册第2章中对此有透彻的讨论。不变(firm)这一描述应解释为不可任性地在不研究其具体影响的情况下就去作更改。在这一视界内,MPS的任何更改都将对某些已发放到供应商或车间去的实际订单发生即时的影响,而不仅是影响到系统中的已计划订单。它可以恰当地称为计划视界的灵敏部份(activeportion)。更改这些订单的时间或数量要引发的代价包括伴随库存过多、催稽、废弃、失去的订单、交货延期、废品、返工与加班加点的费用。但不更改计划也可能引发所有这些费用或其中的某些费用;这就要求执行计划时对应作的更改有仔细的分析。缩短这一视界的好处是显而易见的:1、计划更有效2、受更改影响的实际订单较少3、有更大的灵活性去对付执行中的变化4、实际的竞争上的好处由于需要对低层组件、原料、劳力与设备能力的未来需要有更多信息,使得MPS的视界伸展得远比其最低限度要长。视界只有3个月的MPS是少数但某些MPS可短达6个月;大多数的视界是12个月而某些MPS的总视界要2年到3年。在视界的不同部份中,使用数据的基本目的也是不同的:近期:物料计划,车间日程安排中期:劳力水平,班制,设备的加载远期:工厂、设备、资金的需要238第238页共238页n在每家公司里,可以识别出3个、4个或更多个这样的区间。如图7-7所示,随着视界的延长对细节的需要减少,而时间期间也可以增加。因此,MPS不需用同样的措词贯穿其整个视界。区间之间的过渡,当然将提出把数据转换为更明细数字的问题。为任一公司认定其恰当的区间将简化计划工作并大大提高其有效性。│区间1│区间2│区间3│├──────┼──────┼───────┤控制性约束:│物料│长提前期物料│关键性原料供应││劳力│设备│││设备│工厂││所需细节:││││BOM│成品│典型产品│部份│加工│全部工艺流程│劳力清单│平均金额│时间期间│周│月│季或半年│││││图7-7主计划的时间区间MPS的格式如前所述,为了给每一最终产品的MPS作准备,使用了分时段订货点法、P-S-I与其它高层次计算方法去开发数据。所用的具体格式随不同的公司使用它们的情况而异。本书中所举例子是典型性的,为了说明这种技法的机制与数据之间的关系。这些例子只是表明什么是所希望的。任何MPS只是对其中每一最终产品(可以是成品,主要子装配件,计划用模块或备件)的一个数据文件,它表明在特定的时间期间之中在何时要生产多少。J.A.Orlicky博士建议把MPS看作一个连续的“卷”,它不断地(虽然可能是间歇地)移动以便在一端去掉已经过时的期间,而在另一端展现未来的期间,从而保持一恒定的视界。在任何MPS可被认为在计划工作时有用之前,必须使希望生产的东西与可能去生产的东西相符合;这要求具有对物料可得性与能力方面约束的知识,并且具有确定全部MPS最终物品对这些约束的综合影响的能力。各个个别最终物品的细节构成日程计划,但关键问题是,当想望时,能否生产出所有的物品?图7-8显示由若干最终物品构成一产品系列时MPS的一种典型格式。这里该系列包括在同一┏━━━━━━┳━━┳━━┳━━┳━━┳┳━━┳━━┳━━┳━━┓┃周┃1┃2┃3┃4┃┃23┃24┃25┃26┃┣━━━━━━╋━━╋━━╋━━╋━━╋╋━━╋━━╋━━╋━━┫┃系列#1┃┃┃┃┃┃┃┃┃┃┃最终物品A┃50┃─┃50┃─┃┃60┃─┃60┃─┃┃最终物品B┃610┃610┃610┃610┃┃610┃610┃610┃610┃┃最终物品C┃340┃360┃380┃400┃┃300┃310┃320┃330┃┃最终物品D┃180┃180┃180┃180┃┃150┃150┃150┃150┃┃最终物品E┃15┃─┃─┃─┃┃─┃─┃20┃─┃238第238页共238页n┃最终物品F┃205┃205┃205┃205┃┃225┃225┃225┃225┃┗━━━━━━╋━━┻━━┻━━┻━━╋╋━━┻━━┻━━┻━━┫系列#1┃┃┃┃总计/月┃5575┃┃5340┃图7-8MPS的格式些设施中被加工的诸种物品;它是一制造系列而非包含在同一市场中出售的一个市场营销系列。其中某些物品是要持续地生产的,某些是间歇生产的,某些是季节地生产的而某些是以较高或较低的生产率趋势来生产的。该设施必须对付这一切。把任一期间中任一物品的计划量称为订货是一种错误,虽然其中有许多是这样的;它并不是如同加工订单那样去承诺要生产某种东西,而是要为生产某种东西提供足够资源的一份计划。该系列每月总计量为把MPS细节同生产计划总计量相连接提供数据。在粗略能力需求计划(见本书第9章与第二册第5章)中要用到个别物品的每周数据或系列的月度数字。每一最终物品的每周数据要输入进MRP程序通过其物料清单去展开。在MPS的这一阶段,重要的考虑是1、尽可能地保持同所希望的产出量相接近2、平整设施上的负荷,特别是对瓶颈作业或供应商3、包括设施上的全部重要需求4、留有余地来处理意外的组合变化或额外的需求前三项考虑是不言自明的或前面已经讨论过的。第四项考虑是有很大争议而且是广泛地被人们误解的。使得MPS的负荷超过了制造设施处理负荷的能力是一种后果十分严重的错误。详见本章最后一节“MPS的问题”。客户服务将变坏,成本更高而库存过剩;这恰恰是与良好的计划与控制所希望的结果背道而驶。除了在有限数目的过程工业与重复性生产厂家之中,要去准确地确定设施能够多么好地处理MPS中已计划的物料组合、加工过程与产品是十分困难的。任何一组MPS的“正确”能力不可能被精确地计算出来;详见第9章。不可避免的结果是该MPS总计量将同生产能力不相适配;它不是超过就是不及。管理人员与计划人员的正常倾向是,对销售持乐观态度,为更高的产出施加压力,力求避免工人有闲余时间,而且力求设备有高的利用率,其结果差不多总是使得MPS的总计量过大。熟悉工厂实际上如何运作的人们经仔细的思考将得出如下的结论:1、保有一些过剩的能力以便对付“计划外的需求”(新的以及额外的产品,补偿废品,记录误差,替代作业的使用,等等)比保有安全存货要好得多。2、平滑地把订单下达给供应商与工厂设施以适配它们处理订单的能力比之只给他们发放MRP或订货点法指导的订单要更为有效得多。3、在合格的专门从事计划工作的人员手中,过剩的能力不会被浪费,调整能力过剩比调整能力太小要容易而且快得多。实际情况是MPS总计量留有余地时比之MPS总计量过大时,工厂的实际产出反而会有所增加,这是同直觉相反的,也是违反人们普遍持有的关于设施的高利用率与停工时间的代价等信念的。专业人员知道这一真理及其价值,详见第9章。MPS必须不包括过期数据(pastduedata),那是指出在以前某些时间期238第238页共238页n间中并未生产出已计划最终产品的。把过期数据包括进去是使日程计划超负荷的最坏方法。实际生产情况当然应同已计划生产相比较,但其结果应写在别的某一报告中,而非写在MPS之中。如果所有的工作或至少大部份工作已经完成,而且要求的余额是在可得能力的限度之内,则可以允许在较早的时间期间中安排大于正常的计划量。否则,必须将延误的物品与超负荷物品重新安排到未来的时间期间中去。MPS最终物品必须用可由包括恰当BOM的产品结构记录辩认的数码来识别。目录号或其它产成品识别码也可包含在内以便作为其它用户的现成参考。管理人员对这些数据要定期审查修订,这就要采用清晰易读、不用难懂的缩写的打印拷贝,通常用预先印好的表格,它可由计算机来产生。关于MPS的误解对于MPS,人们常常抱有以下几种错误看法:1、认为销售预测就是MPS。参见“MPS不是什么”这一节。2、认为最终装配进度计划就是MPS。参见同上节。3、认为当物料迟到时,必须更改MPS。已计划的提前期中包含了对排队时间的容差,它为返回到进度计划提供机会,即使当物料被延误时。只有客户决定的更改是例外,更改MPS应被看成是对失败的认可。4、认为MPS中的计划量就是“订单”。MPS中指明了计划生产的最终物品的数量,但该物品实际上可能根本不予投产。当涉及计划用(模块式)BOM时这一点是显然的(如图7-5中的例子)。发放订单去确定装配、完工与包装日程是执行阶段的事,但具体数字往往不同于MPS中的数据。使用“订单”这个术语混淆了计划与执行之间的区别,所以不推荐这样使用术语。5、MPS中的某些部份必须被冻结。参见“MPS的视界”这一节。6、要提出MPS的物品太多了。这意思是问有没有某种有效的替代的办法;没有的。这往往是由于人们不懂得如何去构成BOM并使用系列于最终物品从而把MPS物品的总数降到可管理程度的缘故。MPS的问题有五个问题破坏MPS及其所驱动的计划系统的有效性:1、夸大(Overstating)或过负荷(Overloading)a、把一个过期的时间期间包括在内b、把头几个期间过负荷(叫头重frontending)c、在整个视界上普遍地过负荷2、过分的神经质(紧张不安、摇摆不定)3、无效的数据4、不均匀的加负荷办法5、过分的自动化过负荷的具体影响是容易看得清的──瓶颈加工中心与供应商将有显著的、数量不断增加的过期订单。这些过期订单引起短缺,干扰生产与客户产品的发货,还引起赶工、使用替代物料与替代作业。非瓶颈工序将按计划出产,并将生成过量的配不上对的组件。其净影响是不良的客户服务、过量的成本与高库存。不管过负荷是由于过期订单、前端过负荷或全视界普遍超载引起的,其结果总是如上所述。当238第238页共238页n商业经济健康时,需求是高的,有一种使人非相信不可的去增大产出的需要。虽然实际能力只能慢慢地增长,却有一种不可抗拒的强烈要求去很快加大计划量,通常夸大了计划。这种做法弊大于利。在前一节“MPS的格式”里,讲过抓住现实的MPS数据与真正的利益是不容易的。频繁更改MPS所引起的摇摆不定能够很容易地由计算机来处理(事实上它们靠它来繁荣),但会激烈地干扰执行计划的努力。为数过多的去更改优先级或能力的行动通知与取消着以前行动的冲突的信号摧毁好人们把事情办成的仕气与能力。生产率只可难得作显著波动;工厂以稳定的生产率生产要经济得多。物料之间可以作一些转移──但必须付出的代价是已经开工但现在并不需要的组件所造成的过剩库存与赶工。修补MPS的唯一良药是短得多的计划提前期,如第9章中所述,以及颇策略地计划好的库存缓冲,如第二册第2章中所述。在使用分时段订货点法来为成品库存作补货计划时,使用不变计划订单(第6章),利用产品层次的安全存货,可以阻尼来自不规则的客户订货所引起的MPS更改。有效的主计划工作要求管理人员在不停地重新计划与不灵活的计划之间走出一条漂亮的路线。在MPS输入的开发中使用的无效数据包括蹩脚的预测、错误的成品库存数据、不正确的客户订单与发货量中的错误。用跟踪信号去提醒人们注意表现不好的预测,用循环盘点去发现与消除记录误差的原因以及处理MPS数据中严格的纪律都是必不可少的。可以尽全力去开发平整的MPS数据但这并不能确保在各种设施上、甚至各起始(首当)工作中心或供应商具有平整的负荷。在一给定时间期间发生两批或多批会造成不规则的工作下达,即使是设计良好的MRP程序也会如此。仔细地区分对特定加工中心产生显著负荷的MPS最终物品中的时间期间可使某些问题得到缓解。此问题的真正解决办法是压缩生产准备时间、减小批量并通过管理良好的投入──出产控制技法(见第10章)平滑地投入。不可允许计算机更新过的预测与使用分时段订货点法的分配需求计划系统直接地打入MPS数据。当涉及许多产品与众多服务件时,这样做是很吸引人的。许多软件包也是这样设计的。要制止摇摆不定,平滑负荷并确保一切MPS的现实性,人工干预是不可缺少的。尽管这种干预不容易,但必须做到。原理34.MPS必须妥善管理,它必须完整并能够被执行。MPS的用途MPS很可能是在管理者控制之下最重要的一组数据。它同它所驱动的那个一体化的正式计划与控制系统,有许多用途;其中最重要的是1、它把较高层次的生产计划与日常的日程计划连锁在一起。这就确保后者支持前者,而且在二者不可能保持同一步伐之前会生成早期警告信号。2、它驱动若干种明细计划,包括a、物料需求b、能力需求(人力与设备)这些明细计划建立物料、人员、机器、机床安装、供应、检测与用来生产MPS中最终物品所需的其它设备的恰当时机与数量。其结果是连接一家制造厂及其供应商的一套充分一体化的计划。3、它驱动财务计划,导向组件存货与制品库存、采购与承诺、直接劳务与售出货物的成本等的弹性预算。这些是可从该作业计划直接计算出来的财务分析中的238第238页共238页n主要因素。正式的利润计划所需的间接劳务、工厂管理费与销售净收益可从二次性计算得到。4、它为订货生产产品作出客户交货承诺。当客户订单被记载入册时,倘若它们被转换成MPS中的模块与最终物品并从MPS中某一适当的时间期间减去的话,这些订单就可看作是消耗了MPS。剩下的余额,常称为可供销售量,为对新的客户订单作出交货承诺提供了可靠的基础。在一种健全的计划与有效地执行的环境中,作出承诺比较容易,而且可以达到及时交货的较高水平。这些比之各种提前期公式或经验性规则要强得多,因为后者对现存负荷不能作出充分的考虑。5、它监督各项实际绩效:市场营销,通过评价市场需要与期望;销售,通过获取客户订单;工程设计,通过坚持设计与开发工作的进度;计划工作,通过开发健全的计划;以及制造,通过执行该计划。通过这一手段,失败的根源与原因得以澄清,指责可以消除而绩效得以改善。6、它协调诸多管理人员的活动。开发与维持MPS的工作迫使大家一致同意一项最好地满足他们各自的需要与期望的操作计划。这为执行该计划中的集体合作奠定了基础。在克服每一名经理试图以牺牲团体中其它人为代价来突出自己这种“全明星综合症”方面没有其它过程如此有效的了。管理层对MPS的作用这套MPS为高层管理者提供了一个真正的把手去管好业务。为了最大限度地发挥这一极好工具的作用,他们必须:1、充分理解其功能与用途。前节已经讲过了。2、为在计划与执行中作明细决定的人们建立政策与方针。具体讨论这一问题超出了这两本书的范围,但其基本目的必须是尽可能明白地去定义管理者在稳定的雇佣、客户服务、产品质量、安全与可靠性、资源的利用以及影响作业上决策的类似事情上究竟希望的是什么。3、解决具有不同见解者之间的矛盾。每一位经理对于什么是对公司最好的事情有其自己的强烈看法,通常是以个别部门与专业的观点为基础的。要在可见因素的基础上协调这些差别是不大可能的;为了确保可行的妥协,仲裁可能是有必要的。4、坚持计划要有现实性。有一种不可抗拒的冲动要去乐观地安排计划,特别是在成长期或从衰退的复苏期,去保持劳力精干而且在尽可能高的水平上去利用工厂与设备。其结果是使MPS过负荷,这是在制造设施的管理中出问题最常见的原因。最高层管理者必须懂得这种作法对作业的影响,并努力给灵活性与对变化的快速响应以足够的考虑。虽然不太容易定义并定量地度量,但灵活性与对变化的快速响应对尖锐的竞争情况可能比人头少与机器利用率高要重要得多。5、有规律地并严格地检查MPS,把它同作业中的实际绩效相比较。这一有价值的控制工具值得在最高层经理间的管理委员会或执行委员会的会议日程上占一显著地位。高层的决定可通过这一正式计划系统转换成低层的细节。协调整个组织是可行的。有了一个有效的、管理良好的MPS,虽然成功不见得就有了保证──但若没有了它,失败却是有保证的。238第238页共238页n八.总量库存管理总量控制的必要性在制造计划与控制中所用的每一种技法实际上都涉及一个项目──一一种产品、组件、原材料、工作令或采购单,工作中心或供应商。许多年以来本领域中的实际工作者都相信只要每个项目上的事情做对了(用经济批量订货,安排好正确的安全存货,保有足够的生产能力),那么总的结果也就对了。其实不然,要控制好库存并管理好生产,恰恰需要采取相反的方法──从控制好总量着手。要有效地控制好库存,必须回答四个问题:1、现在我们手头上有多少?2、我们要多少?3、我们将产出什么?4、我们必须获得什么投入?关于总库存按类别、按地址、按产品系列或按设施的信息,需要时应当随时可得。倘若记录编码得当,那么在任何时候当需要知道某项总量时,计算机应能在几分钟内把有关项目加总得出所需总量的值。很少有公司已经开发出了严格的制订库存预算的方法;大多数使用周转率(发货成本值除以总库存的成本值)、库存占销售量的百分比(周转率的倒数)或根据经验法则能指示比目前的运作有所改进的指标。虽然压缩库存的潜力是巨大的(50%-90%),通常所计划的改善是有限的(10%到20%)。现代的以MRP为基的系统所能提供的数据使我们能够计算出伴随作业计划在其实施的全过程期间的库存水平。根据作业计划来计算库存量比采用周转率或库存与销售量之比要好得多。这些老办法不能给出正确的库存水平应该是多少,也不能联系到详细的作业计划。使用其它公司所公布的周转率数据是容易把人引入岐途的,因为产品、市场、加工过程可能有显著差别;对客户服务、分配、雇佣的稳定性、产品服务支持及类似因素方面诸种政策可能大相径庭;而且他们可能对库存管理得并不好。使用下列理论上的公式计算目标库存来确定库存预算也是不好的。平均库存=1/2(订货量)+安全库存(8-1)由于下列原因之一或若干原因,这类公式总是低估了库存的正确水平:1、实际使用情况并非如理论上所假设的那样是均匀的。2、零件、组分与组件是配套使用的,并非个别地、独立地使用的。3、数量可观的在制品库存,为季节性产品建立的预期库存,在途物料,等等,未被包括在内。4、为了确保人与机器有活可干,为了获得大宗采购的折扣,为了防备涨价或供应中断,等等,而附加的缓冲库存,被忽略了。比使用周转率、库存对销售量的百分比与理论计算公式来确定库存预算好一点的办法是使用时间周期(TimeCyldes)。238第238页共238页n││计划发放率│标准│││制造阶段│¥/日│天数│标准金额¥│├────────┼─────┼──┼──────┤│原材料存货│2,550│15│38,250││加工阶段在制品│5,250│30│157,500││组件存货│9,720│10│97,200││子装配阶段在制品│12,360│2│24,720││部件存货│12,360│10│123,600││装配阶段在制品│12,700│2│25,400││完成品│12,700│10│127,000││在途物料│12,700│5│63,500││││││标准金额总计¥657,170完成品发放率=¥12,700/天库存目标=¥657,170/¥12,700=51.7天图8-1库存目标与时间周期如图8-1所示,为了支持完成品的发放率,必须建立制造过程各阶段的物料发放率。这一方法最好使用产品系列数据,但有两个严重问题,因为平均发放率与标准天数都是估计值。实际数据可能距平均值相当远。然而,时间周期法一个很强的优点是它着眼于长周期,指示出可能显著压缩库存的潜力何在。由此出发经过调整可以开发出灵活的,现实可行的库存预算。详见本书第二册第三章。投入产出总量控制库存的产出就是最终要发到客户、仓库或分厂的发货量。每家公司都对此作了仔细的预算并监视着其数值。但很少把这些数字用来控制库存。对库存的投入叫做生产量,它包含三个部份:采购的物料与服务,直接劳务与工厂管理费。当工厂管理费分摊在直接劳务上时,二者可作为一个因素来考虑。基本的库存控制方程是:现有库存+生产量-发货量=库存目标这一关系式也适用于按订单制造的公司:现有订货量+新订量-生产量=订货量目标这里订货量就是未发货订单上的订货量。在此类作业中,生产是根据订单而且生产出来后立即发货,故总生产量可以取代(8-2)式中的发货量。元月1日库存量=¥3,000,000目标12月31日=¥2,400,000│月│采购物料│生产性劳务│发货量│库存│238第238页共238页n│├──┬──┬──┼──┬──┬──┼──┬──┬──┼───┬───┬──┤│份│计划│实际│差异│计划│实际│差异│计划│实际│差异│计划│实际│差异│├──┼──┼──┼──┼──┼──┼──┼──┼──┼──┼───┼───┼──┤│一月│240│260│20│160│150│(10)│450│430│(20)│2,950│2,980│30│├──┼──┼──┼──┼──┼──┼──┼──┼──┼──┼───┼───┼──┤│二月│240│230│(10)│160│165│5│450│470│20│2,900│2,905│5│├──┼──┼──┼──┼──┼──┼──┼──┼──┼──┼───┼───┼──┤│三月│270│260│(10)│180│170│(5)│500│480│(20)│2,850│2,860│10│├──┼──┼──┼──┼──┼──┼──┼──┼──┼──┼───┼───┼──┤│四月│270│││180│││500│││2,800│││├──┼──┼──┼──┼──┼──┼──┼──┼──┼──┼───┼───┼──┤││││││││││││││表中数据的单位是¥1000图8-2库存投入/产出报告图8-2所示为当今在工业中成功地被使用的一种典型的管理控制报告。该计划是为了在一年内将一个产品系列的库存压缩20%而建立的。为完成这一压缩,采购物料与生产性劳务这两项投入必须压缩到维持库存为常数所需的水平以下。每月的压缩量取决于允许的期间:期间越短,每月的压缩量就越大。即使没有正式的详尽的计划系统,也能够轻而易举地准备出这种控制报告。实际上每一家公司都知道个别产品的采购物料与直接劳务含量,或者至少知道总生产量,通常它们被表达为已售货物的成本的百分比。某些公司的成本数据是这样安排的。这些百分比可被用来准备这两个因素的计划数据,把它们乘以计划发货量,然后再将结果下调到压缩库存所需的数字。当然一个健全的正式系统允许计划出为完成这些压缩所需的详细行动。实际数据要定期地登录并由此计算出计划与实际的差异数。对报告表中的四个变量每个都设定一个容差范围,差异一旦显著偏离计划时就可提请管理者的注意。例如,若采购物料的可接收容差为±¥10,000;而一月份实际收货超过计划数达¥20,000,就将提醒管理者应立即采取某些措施以返回到计划轨道上来。提供这种早期警告信号有利于使一个健全的计划得以顺利地执行,要观察的数据极少而且所需的校正行动远非激烈的。详细的计划必须同这些总体的总量控制相一致。库存预算必须可行而非不保险的猜测。把库存预测建立在作业计划之上是确保可行性的最好办法。修改作业计划以达到管理者在库存方面的目的是容易的;其机制详见本书第二册的第三章,本章的后面以及附录Ⅱ。发货量目标必须符合于驱动正式计划的MPS。发生显著偏离采购物料目标时必须触发迅速的行动去审查近期即将到期的收货并果断地削减之。必须找出超收的原因以防止重复发生。对直接劳务方面的偏离也必须如此处理,管理费用若不正常也包括在内。这后一个因素要求有明细的开支预算,但在工业中这些是常事情。原理35.要控制住库存的细节,必先管理好库存的总量.库存投入/产出控制报告集所有主要因素于一页供管理者审阅。它们通过诸失控因素这一例外情况向管理者提供早期警告信号从而使他们警觉。及时的、基于良好综合计划的准确数据为制造作业的管理提供了另一有力的把柄。为了帮助管理者在库存水平这一困难问题上作出决策,对下列各种主要的库存类型:批量库存,安全存货,预期库存与运输库存,都各有总量技法可用。238第238页共238页n总量批量库存在第三章与附录Ⅱ中讨论过EOQ在应用中产生的若干问题。这些问题围绕着需求预测的准确性与公式中所使用的成本值以及推导这些公式时关于这些成本值与所选择的批量大小成正比的基本假设。经济订货批量这一潜力极大的概念居然缺乏应用,其更重要的原因是因为问题在于实际工作者必须同总库存以及作业中的变更打交道。而EOQ公式适用于个别物品,它基于有关成本的某些固定的假设而为每一物品指出有一所希望的最优条件。它并未指出总库存的结果会怎么样也没有考虑作业条件(所需生产准备,要处理的订单数,等等)会怎么样,当然也没有考虑目前状况的变化。这类问题详见本书第二册的附录Ⅱ。凭感觉的订货量难得会是经济的。倘若由着制造人员他们关心的是机器的生产准备费用,因而订货批量会偏大;倘若由着较多考虑库存持有费用的人,则订货批量会偏小。在这种情况下引进EOQ不一定使实际情况真正有所改善,甚至会有使人心烦意乱的效果。如果EOQ算出来的批量小于现状,则据此批量在一定期间内订货的次数将变大,可能超过生产准备人员的能力。甚至超过了设备的能力,如果不能从生产中省出时间来用于生产准备与转换的话。倘若现状的订货批量过小,EOQ将引起批量库存相当大的增长,可能使财务资源紧张或使可用空间拥挤。为了防止发生这类令人不愉快的突然袭击,在未对总库存与采取EOQ行动将对作业条件引起的后果作好研究之前,不应贸然引进EOQ。当引进EOQ将压缩库存时,不论其节约来源于何处能否准确定位,诸如来源于投入资金的压缩,报废与报损的降低,还是税金的减少,这一库存压缩必须具有真正的价值以致由此而解放出来的资金可立即使用于其它领域。然而,当EOQ产生较少订单时,其节约可能永远不能兑现。除非真正可以少用采购人员或生产调整人员,否则较大的订货量将只会增加库存持有费用而不会实现在作业成本方面的补偿性节约。显然,为防止应用EOQ反而增加总成本,必须考察它对总库存与总的作业条件的影响。需要有一个根本上不同的确定EOQ的方法。第三章中提出的标准EOQ方程表明如果采用较低的持有成本值,则EOQ与总批量库存可以增大,反之如采用较大的持有成本值,EOQ可以减小。R.L.VanDeMark早在1960年就指出过这点。1961年,R.G.Brown建议应将持有成本作为管理上的一个“政策变量”来考虑,以便控制周期性存货或批量库存。这一解释抓住了EOQ的真正功能及其在批量库存管理中应用的关键。这一概念现在在专业人员中有许多追随者,他们考虑到库存持有费用,虽然是一项非常实际的业务支出,但像缺料的代价一样──也是一项实际的业务开支──是难于识别为一个简单而神秘的数字的,它不能被表达为一个具体的金额。这两项费用是推导有用的数学公式所需的;去寻找固定的、可供使用的真正数字可能成为一种令人灰心丧气的经历,它不应掩盖了现实生活中确定经济实惠的因素。在公式中没有持有费用精确值可用的情况下如何能实现使用EOQ概念的好处呢?在第三章里讨论过在一系列物品中重新分配订单数就可降低库存投资的简单例子。在第三章还讨论过在不改变订单数的情况下对一系列物品计算各个个别订货量以获得最小总批量库存的简单技法。它表明只要对这一技法稍作活用,总库存可保持为常数,而订单数量可以减少。虽然上述过简的技法主要是示教用的,但它给我们以启示,由于EOQ应用于现实世界时总是要遇到种种约束条件,我们应该采用何种类型的方法。当应用EOQ238第238页共238页n概念时,必须考虑下列现实生活中的一些约束:1、可用存货空间的约束2、文书人员处理订单能力的约束3、调整人员完成调整工作的能力约束4、生产设备可被生产调整占用的停机时间的约束5、可投资于库存的金额的约束APICS有一个专门项目,其中有一部份开发了一种技法用来处理EOQ总量以及有约束的EOQ计算问题。附录Ⅲ介绍了这一技法,叫做LIMIT(Lot-sizeInventory-ManagementInterpolationTechnique)。LIMIT为直接计算一个系列物品在满足某些约束诸如生产调整时间或总库存不超过某一极大值的条件下的恰当批量提供一种手段。在相同设施中加工处理的(混合、自动车床、薄板压机、包装线以及复杂测试设备是典型的)系列物品被一起处理。│持有成本=││││││20%│调││每年│年调│├─┬───┤整│EOQ│调整│整费││品│年使用│费││次数│用││目│量¥│¥│¥││¥│├─┼───┼─┼──┼──┼──┤│A│2000│10│447│5│50││B│5000│5│500│10│50││C│1500│12│424│4│48││D│4000│6│490│8│48││E│1000│15│387│3│45│总计2248241图8-3批量库存对作业成本使用EOQ计算公式很容易作出如图8-3中所示的交易曲线。持有成本要假设一系列的值(设持有成本为20%,25%,30%,35%....),对每一持有成本的假设值,要对系列物品中每一物品计算其EOQ批量值。对每一持有成本值,要算出该系列物品的平均库存投资以及年度的作业成本值。每一持有成本值相当于图8-3中的一个点,图的右边是一组典型的计算。该系列包含A、B、C、D、E五种物品,持有成本假设为库存值的20%,EOQ的值没有取整数,写订单时要取整数的。平均库存为各EOQ总计的二分之一。调整费用假定除了实际用于调整设施的劳务费以外,还要包括第一件报废、检验、写订单与其它有关费用在内。叫做订货成本更为恰当。曲线代表理想或理论上的情况;实际作业将总是在曲线上方──对给定库存量其作业成本要高些,对特定的作业成本,库存量要大些。在第三章讲过,这是由于理论上的缺陷,以及不能为了赶制一个分裂批而去运行EOQ。曲线上每一点相应于持有成本的某一特定值;在管理者已经决定要在那一点作业之后,就可用该点的持有成本值来计算EOQ。这种决策可以基于投资回收率;距离AB表示将库存从C点增长到D点时作业成本的压缩量。调整能力上的约束将在相应的作业成本最高点上竖起一道藩篱。不管有何经济效益库存不能降到此点以下,除非通过压缩调整时间或增加人员或设备而克服了这一约束条件。238第238页共238页n原理36.应当使用EOQ理论来绘制交易曲线供管理决策之用。本章所讨论的技法在批量的计算中非常有用。他们当然不能解决一切有关的生产与库存控制问题,但确实代表一种比标准的EOQ与折扣计算更加现实的方法。使用该技法必须加上判断力,因为它并未把同此类决策有关的一切可能变量都考虑进去。要牢记的一点是订货量的减少将产生更多重订货期间因而更频地曝光于缺料。因此,总库存将不会按比例地减少,既然安全存货将由此而增加。附录Ⅳ为这种现象提供一个例子。在使用任何方法计算出来的批量之前,该批量应提交制造与物料控制人员审核,他们最接近于生产区,以确保这批量是合理的。在计算机程序中,批量不应取整而应将计算结果如实打印出来。要故意如此,使得计算出的批量接收合理性审核,然后把取整作为这一审核的一部份。审核批量的人应把计算中未加考虑的损坏等或其它因素考虑进去并对批量作出调整。参见第三章图3-5将表明当批量偏离EOQ时──特别对较大的批量──总成本只略有增加。这在理论上是这样的。实际上具有意义的批量其价值是很确实的。标准的LIMIT程序在有一个主要机群(诸如自动车床或冲压部门)要考虑的场合下工作得最好。当一个物品要顺序通过一系列作业时,LIMIT提供的决策信息不如只有一个主要机群要调整时那样简单明了。例如,一个物品要顺序通过六个不同作业时,LIMIT将把这六个顺序作业当作一个作业来处理。在这种情况下该程序仍可能有用但需考虑下列建议:1、运行LIMIT程序,首先把每一主要机群当作分开的作业。这将表明倘若每一作业独立运行,所希望的批量应是多大。2、再次运行LIMIT程序,把所有作业的调整时间加总并把所有这些顺序作业当作一个机群的作业。3、比较上述计算结果然后确定最符合实际的批量。可能需要打破这个作业顺序在中间设置一个持有半成品的库存点。详细研究各种可能的处理方法已超越本书的范围。即使在以EOQ计算作为仿真程序用来研究不同批量的情况下,总量方法也比标准EOQ方法更加有助于实际工作者,因为它可以指示哪里的调整时间必须增加或何时如果采用经济批量则总库存将会增大。即便计算出来的批量不能被采用,总量计算也是有价值的,因为该程序把人们的注意力引导到库存与调整时间的总量。用这种方法使用LIMIT程序时,按某种所希望的手法确定出来的批量被作为当前批量输入LIMIT程序,然后该程序作这些计算的权衡。批量决策还有一些其他影响是时常必须考虑的。例如,执行某种特殊类型工作的机器只有一台,一年内要它加工的零件占用了大部份能力,剩下很少时间可用于调整因此这些批量都非常大。这些批量不能从调整费用与库存持有费用要平衡的经济观点来选择,而必须满足设备本身的调整时间有限这个约束。还必须考虑由于轮转问题而引起的批量对库存的影响。大的批量需要长的运转时间,每一物品等待加工的时间长所以持有的库存量也较大。几乎可以肯定当一个物品的订单被生成时,机器里将有活在干或有活等着要干。所以该物品必须等待当前的欠交订单完成之后才能得到加工。这一等待时间可能是正常加工时间的许多倍并将使库存显著增大。压缩所需调整时间的价值非常高。其它现实生活效应在EOQ理论中是不考虑的,但在总量计算中很容易被估计进去。处理所用批量所要求的总调整次数的能力就是这样一种因素。调整工作往往238第238页共238页n需要特殊技能并分派专人去从事。他们的能力限制了调整次数从而限制了可供选择的批量、理想的调整次数是保持调整人员满负荷而非过负荷。另一约束是对这类库存的可供资金。倘若批量束缚了能够更好地使用于他处的资金,那就是不经济的。类似图8-3所示的交易曲线有助于判定批量库存的投资回收是否足够。“一次一个物品”的方法也使涉及折扣的采购决策蒙受损失。接收折扣与否的决策往往是基于从较低单价与较少订货次数产生的节约能否超过持有更多库存要付出的代价。该决策依赖于要知道持有费用而且该方法对可能采取的全部折扣决策对投入资金会有什么总的影响没有一点指示。把净节省看作投资回收,把若干潜在的折扣按其附加投资的回收多少来分等,其结果将是只有满足了管理者所希望的类似于为设备投资而设的回收目标的那些折扣,才能被接收。反对这样做的理由往往被提出来,说一家公司所有物品可能得到的折扣不可能老早就知道。当然这是事实,但这不是对一切已知折扣情况不去使用这种技法的借口。应该作出实际努力去确保全部A类物品(高使用价值物品)被覆盖。这些物品显然将产生回收的大部而且最可能获得折扣。生产与库存控制决策的典型实际情况是高度复杂的。没有一种计算能够把制造情况中遇到的一切变量都计算在内。本章讨论过的公式、技法与程序可以成为良好判断的巨大帮助,但不应随心所欲地使用,应当理解单先靠它们是不能解决所有问题的。这些技法试图同总的批量库存打交道,并说明这些数学计算的现实生活含义。对于总量库存的其它部份,需有其它的技法。总量安全存货库存在大多数企业中,客户服务与库存投资之间的平衡难得是一项深思熟虑的政策的结果。管理者常常未能认识到库存水平与客户服务之间存在着一种基本的关系,它们并非独立变量。在一家已经有效地使用着制造控制系统的企业里,所希望的客户服务水平越高,成品库存也必须越高。在第五章讲过使用从一特定物品的需求数据计算出来的平均绝对偏差MAD来计算统计性后备存货的方法。下面用物品M为例来说明在服务水平的某一范围上服务与库存投资之间关系的计算。计算所需的数据是:年度预测=26,000件订货量=2000件MAD=209件单价=¥1.35可用第五章讲过的方法来计算每一服务水平所需的后备存货。例如:每年允许缺货的次数=4每年曝光次数=年度预测除以订货量=26,000/2000=13服务率=(13-4)/13=9/13=69.2%从图5-7正态分布下的安全因素表中可查出所需的MAD数约为0.75。因此所求后备存货=0.75×MAD=0.75×209=157用类似方法,可以计算出不同服务水平时所需的后备存货水平。图8-4中所238第238页共238页n示为9个不同的服务水平下对物品M所作的计算。理论上完善的服务(永不缺货)所需的后备存货量约为允许一年缺货4次时的7倍。必须记住这种计算是假定作业被良好地计划并紧紧地受控。┌────────────────────────────────┐│据:││MAD=209订货量=2000││年预测=26,000单价=¥1.35│├──────┬────┬────┬────┬─────┬────┤│缺货次数/年│曝光次数│服务分数│服务率│所需MAD数│后备存货│├──────┼────┼────┼────┼─────┼────┤│4│13/年│9/13│69.2%│0.75│157││2│13/年│11/13│84.5│1.29│268││1│13/年│12/13│92.5│1.80│376││2年1次│26│25/26│96.1│2.20│460││3年1次│39│38/39│97.4│2.40│501││4年1次│52│51/52│98.1│2.60│544││5年1次│65│64/65│98.5│2.70│565││10年1次│130│129/130│99.2│3.00│626││从不缺货│─│─│100│5.00│1044│└──────┴────┴────┴────┴─────┴────┘图8-4服务水平与后备存货对照表图8-5用曲线表示出这一关系。图中每年缺货次数表示为每10年的缺货次数,以便用统一的尺度表示各种情况。这一曲线清楚地表明随着所要求的服务水平的提高后备存货将急速地增长。使用此类曲线,可以选定一个合理的客户服务水平然后据此确定达到这一服务水平所需的后备存货。然后可用相应于该点的服务率来计算系列中每一物品的后备存货。在后备存货库存原先是凭直觉确定的大多数情况下,这种统计解法可使库存与服务水平间的关系立即有所改善。然而,此曲线的最重要的方面却是它暴露了客户服务与库存投资之间的矛盾,对物料控制与其它管理人员表明要给出相应的客户服务水平所需的成品库存。这类曲线是一种非常有用的管理工具。大多数企业中持有成千上万种库存物品,为每种物品这样去开发与分析数据与曲线是不现实的。物料控制人员必须确定每种物品的所需后备存货以便恰当地去计划其补货,但这必须在管理层已经决定了要提供的具体服务水平之后。而管理层要在服务水平问题上作决定,他所需的服务与投资数据不是对个别物品而言,而是要所有物品的库存总量数据。个别物品的库存对库存计划人员是有意义的,但在更高的管理层,要考虑的是总量库存投资。对一个物品绘制服务对投资曲线的方法可以扩展到对一组物品表示其客户服务水平同整个大类产品所需库存投资的关系。在下例中,将为具有4种物品,物品M、N、O、P的一个系列产品来计算服务对投资的关系曲线。设有数据如下:───────────────────────238第238页共238页n物品年使用量订货量单价MADM26,00020001.35209N96,00080000.701600O12,00020000.90271P6,00015000.85240───────────────────────设该物品组的最低服务水平是每年8次缺货(相当于每一物品每年缺货2次),可计算出所需后备存货、平均库存金额等,见图8-6.图中表明,要达到每年缺货8次的水平,将需有¥7518的总平均库存;要达到较高的服务水平,就需有相应┌──────────────────────────────────────┐│物品曝光服务服务后备1/2订平均库单价平均库存││次数分数率%MAD数存货货量存件数金额│├──────────────────────────────────────┤│每年缺货8次(每物品2次)时││M1311/1384.51.29268100012681.35¥1710││N1210/1283.41.201920400059200.704140││O64/666.70.54146100011460.901030││P42/450.0007507500.85638││¥7518│├──────────────────────────────────────┤│每年缺货4次(每物品1次)时││M1312/1392.41.80376100013761.35¥1860││N1211/1291.61.752800400068000.704760││O65/683.31.20325100010000.901192││P43/475.00.842027509520.85810││¥8622│├──────────────────────────────────────┤│每年缺货2次(每物品隔年1次)时││M2625/2696.12.20460100014601.35¥1970││N2423/2495.82.163460400074600.705220││O1211/1291.61.75474100014740.901325││P87/887.51.4534875010980.85923││¥9447│├──────────────────────────────────────┤│每年缺货1次(每物品每4年1次)时││M5251/5298.12.60544100015441.35¥2085││N4847/4898.02.564100400081000.706060││O2423/2495.82.16585100015850.901428││P1615/1693.71.9246175012110.851030││¥10,203│├──────────────────────────────────────┤238第238页共238页n│每2年缺货1次(每物品每8年1次)时││M104103/10499.12.95616100016161.35¥2181││N9695/9699.02.914660400086600.706060││O4847/4898.02.56694100016940.901525││P3231/3296.92.3356075013100.851113││¥10,879│├──────────────────────────────────────┤│每3年缺货1次(每物品每12年1次)时││M156155/15699.43.14656100016561.35¥2219││N144143/14499.33.104960400089600.706260││O7271/7298.62.75745100017450.901571││P4847/4898.02.5661575013650.851160││¥11,210│├──────────────────────────────────────┤│“永不缺货”(99.9%)时││M──99.94835100018351.35¥2480││N──99.946400400010,4000.707270││O──99.941083100020830.901878││P──99.9496075017100.851452││¥13,080│└──────────────────────────────────────┘图8-6服务对投资的关系(计算过程)的较高的平均库存。这一组物品的服务水平对投资总的关系可概括如图8-7所示。在图8-8中,这些数据被标作两条曲线,下面一条表示后备存货,上面一条表示总的库存投资。夹在二者之间的就是周期性存货,也叫批量库存。┌────────────┬───┬───┬────┐│产品组的服务水平│││││(缺货次数)│1/2│后备存│平均库存│├─────┬──────┤订货量│货¥│总额││以1年为基│以10年为基│¥││¥│├─────┼──────┼───┼───┼────┤│8│80│¥5687│¥1831│¥7518││4│40│5687│2935│8622││2│20│5687│3760│9447││1│10│5687│4516│10,203││1/2│5│5687│5192│10,879││1/3│3.3│5687│5523│11,210││“永不”│0│5687│7393│13,080│└─────┴──────┴───┴───┴────┘图8-7服务对投资关系总计数据238第238页共238页n以实用观点看最重要的是事实上差不多在用统计性计算去替代用直觉方法确定订货点的每一个实际场合,立即可以使服务对投资的关系获得改善。以图8-8中的情形为例,现状可能是库存投资为¥11,000,而全组物品的服务水平约为每10年缺货10次。而使用统计方法去重新分配后备存货,该曲线表明库存为¥11,000时该组物品每10年的缺货次数仅为4次。前面的计算中曾假设全组物品的缺货次数由各物品平均分摊。实际情况不一定非如此不可。完全可以根据我们的希望去分配缺货次数,然后再计算出恰当的后备存货。因此,使用统计方法来确定后备存货可以用定量方法来解决那些认为库存周转率本身就是企业效率的良好指示器的人们同那些认为客户服务水平是库存控制有效性唯一度量的人们之间的基本矛盾。这是管理人员惯常要同之打交道的信息类型。这些计算当然并不直接地给予他们以最后的答案。倘若一次缺货的代价是已知的,那就可以提出一个公式来平衡缺货成本与持有必要的库存的成本,这样就很少需要依赖于管理人员的判断了。不幸的是,这两项成本都不能准确地被确定;在大多数企业的情况下,二者都随时间而有很大变化。在大多数企业中,它们被认为是实在的、但又是高度地无形的成本,它们是抓不住也不能用具体数字表达的。有经验的管理人员习惯于在不可能得到全部所希望的信息的条件下去作出决定。在这种情况下他们经常地被要求去使用他们的经验与判断。然而,物料控制人员不能只是收集信息,把它表达为对管理人员有用的形式,然后就依赖管理人员来作出决定。这些专业人员,凡能胜任认识有关库存水平或所希望的客户服务水平的决定的含义者,应当提出重要的帮助与指导意见。用这种方法,可对库存投资作出合理得多的决定。往往可在库存投资与客户服务之间的关系方面作出显著的改进。一旦物料控制人员已经提出这一决策信息并已设定了特定的库存与客户服务目标之后,使这些目标被达到便成了操作库存控制系统的人们的事了。这要通过设定同所选定的服务对投资水平相对应的后备存货水平并操作该库存系统去完成这些存货。原理37.使用交易曲线来研究各种替代方案比之为一给定的客户服务水平计算后备存货会产生好得多的决定。将总的服务对投资关系曲线应用于整个大类产品已知的首例发生于1959年。这一应用涉及80种不同物品所构成的一系列采购零件。对每一物品都计算出EOQ,后备存货则用这里描述的方法计算。实际缺货次数超过统计性计算的原因之一是缺货的计数方法。在统计上,缺货的定义是当存货不能满足当时总需求的一个事例。往往并未注意去度量一次缺货持续多久。在实际上,去计数每周缺货的物品数并把每物品发生一次缺货记为一次缺货更为实用。因此,倘若一物品缺货持续3周,缺货次数将计数为3次而不是1次。运行此系统短时期以后,人们已能将服务的统计度量联系于客户服务的实际度量并懂得为了在实际上达到某一服务水平,该服务的统计度量要设置得略高一些。有趣的是,虽然实际缺货次数仅及统计预测的一半,服务的改善如此之大以致这一缺点也无所谓了。管理者欣赏“近失弹”,认为它比原先的盲目操作要强多了。这种库存控制方法暴露的一个问题是提前期缺乏管理。这组采购物品的供应商,像其它许多制造商那样,往往在生意兴旺时要经历提前期变长,而在生意下降时经历提前期缩短,当他们以短于计划的提前期发货时,结果是较高的库存。当他们的提前期被延长时,库存水平是降低了,但由于交货迟延,其结果是客户服务受损失。必须紧密地注意交货提前期与绩效以便在没有过度短缺的情况下保持总的库存投资238第238页共238页n受控。对这一问题真正的解决办法不是去增大后备存货或推前交货日期。处理这一提前期综合症的恰当办法见第二册第5章。在操作上,这是高度成功的库存管理。它代表服务对投资的关系大有改善。管理人员高兴的是他们到底能够为这一大类产品去确定其总的库存投资而且可以如他们所希望的那样去选择库存水平与客户服务了。物料控制与直线人员在达成他们所预测的服务与投资水平时有富于挑战性的工作要做,但要达到这些水平并不像曾被预期的那样困难。总之说,有关的每个人都很满意因为他们到底能够直接地管理总的库存投资而不是通过许多个别的决定也无法预见其总的效果了。这一特定应用使用了人工的计算。由于预测与需求的变化,这些计算要求经常的修订与更新。由于这首次的服务对投资计算具有实验性,它被应用于一组低价产品。最后,在使用了约2年之后,由于要维持它涉及过多的人工努力,不得不把它放弃。从那时以来,计算机已成为可用的而且正被用来取得定期的存货状况报告,应用指数平滑法去为个别的物品预测需求并定期地计算预测误差的MAD。然后,后备存货被确定并同更新后的物品预测结合成为对每一物品的一个浮动的订货点。客户服务的这一表达式往往是比较好的用的种。必须记住这里所用服务的统计性度量并不度量缺货持续期。第5章讲过可被使用的客户服务的其它度量;在某些情况下这些度量可能更适合于某种特定应用。然而,一般说,客户服务的任何统计性度量必须同客户服务的实际相联系,并且统计性度量往往有必要设置得比实际希望的服务水平要高一些。使用统计性订货点法来确定一服务对投资关系图表的步骤如下:1、为产品组中每一物品计算一MAD并提出一经常更新它的方法。这很可能将包括使用某种统计技法去预测提前期间的需求,以及倘若预测间隔与提前期间隔不等时要作一些调整(如图5-9中)。2、作一样本计算去提出服务对投资的总量曲线,总量中包括周期存货库存(订货量的1/2)以及后备存货。在设置库存在所述的未来时间将降低到的目标时,勿忘包括任一慢移存货。调整得再好的库存控制系统也难免会有某些慢移存货将现有库存水平同一理论库存水平相比较并假定可以很快降低库存是不合理的,因为其中的某些“呆滞存货”在一段长时间内不会移动的。3、将目前客户服务所需库存水平同实际库存水平相比较并用统计性库存控制技法说明可能的改善。如果计算并不指示改善,这表明目前的后备存货的库存各物品之间分布得非常均等。倘若目前使用的是直觉方法,这种结果是很不大可能的,这将表明该计算与现有服务数据应作校验。4、使用统计性技法向管理者说明目前的服务对投资的关系及其可能的改善,然后帮他们选择出“最佳”库存水平。5、把后备存货设定在议定的水平并运行该库存控制系统。开始使用这种总量控制方法时有一些有价值的实用提示:1、第一次引进此改革时所涉及的物品其库存差不多总是很快地增加。发生这种情形是由于低于正确水平的物品立即全都被订货了。通常还有其它许多物品其库存是过高的,但必须等待它们被去掉。结果是可正常地预期库存水平会向上暴涨。用样本检验将指出要预期的增量并应警告管理者它是要发生的。更好一些是应采取平行的行动去减少某些其它类型的库存以抵消这一增长。2、这些技法应当仅仅应用于成品。统计性安全存货理论并不适用于其它制造物品的组件。3、在提出需求数据时尽可能使用每周销售史。月度销售数字往往更难于使用,238第238页共238页n因为每个月份的销售天数不同,这些数字在使用前必须加以调整。4、为了透彻地理解它,对少数物品用人工计算来试用这系统是好的。用台式计算器或便携计算器就可完成计算。5、计算机并非必须品;对少数物品这种计算很容易用人工来完成。一旦对低值库存(即使出毛病也不那么严重)已被证实,就可将一人工系统使用于最高金额值的物品(A类物品)。6、然而,有了计算机,总量方法就更加实用。所有主要的计算机制造商与许多软件供应商已经提供含有所需统计技法的软件包。虽然这些计算机程序在计算上难得同本书所述的雷同,但在基本设计上围绕的原理是相同的。如果实际工作者要有效地去使用这些程序,那么透彻地理解本章所述原理是必要的。7、服务对投资关系图只需定期绘制即可。它们最好不过是一种近似值,预测、误差、成本与其它数据中小小的变动不需触发重新计算。8、开始使用任何新技法时,要牢记确保它至少要干得同老办法一样地好,即使在开头也是如此。服务水平方面一个短暂的失误会破坏一家公司的名誉一段长的时间。实际工作者在试用新技法时以公司名誉来冒险,则不管该新法有多大潜力,并不是为公司的最佳利益在行动。因为总量库存管理的概念如此重要,所以前面已经详细地讲了两种总量库存的计算。这种计算可由懂得基本的库存概念的实际工作者施用于各种库存。总量在制品库存在制品是批量库存,少量的返工可能是例外。图8-11表明批的典型情况,其中订货量是8件,提前时间(LT)是制成该批所需的周数。此批的平均在制品量(WIP)是(q×LT)/52而一年要处理n批,n等于年使用量A除以批量q。年平均在制品WIP=nq(LT)=A×(LT/52)(8-4)52此式除了提供一种计算WIP总量的方法之外,还说明平均在制品量与批量大小无关而直接随提前时间与年使用量而变。这清楚地表明了压缩提前时间在缩减在制品投资中的好处。它也表明为补偿报废损失而加大批量与增加返工作业二者都会加大作业成本与资本投资的需求量。│在│q┌──┐制│││品││││││件││││││平均├─┤├───────││LT│WIP└─┴──┴───────0周数52238第238页共238页n图8-11平均WIP对批量一批的平均价值取决于加工过程中物料、劳务与管理费是如何增加进去的。对大多数制造作业,在订单发放时全部物料就被引入成为在制品。当大量劳务(以及管理费)被化费在加工的早期时,平均价值将接近于完工批,在前述讨论中,在制品的定义是发放到车间去被加工的物料,它不包括实际或技术上在贮藏室内为进一步加工等待发放的物料。许多公司使用壁间库存评价方法,在其中厂内全部库存都被认为是在制品,即使完工产品亦然,直到它被发运到客户或仓库。实际工作者必须懂得他们公司的会计实践以便他们的研究结果会同管理者所使用的其它数据相兼容。总量期望库存持有期望库存有两个基本理由:1、为了拉平那些具有季节性需求、促销或暂时被价格变化弄膨胀了的需求的产品的生产速率。2、为生产量低的期间或由于假期停工、工厂搬迁或机器大修与更新而生产暂时中断的期间去持有库存。持有期望库存的好处可分两类:1、工厂与设备的投资比满足高峰需求所需的要低2、降低雇佣、解雇、培训、加班与停工的费用期望库存往往是为那些决定特定制造设施上负荷的系列产品而计划。常用的技法是S-P-I报告,如图7-2与7-3中所示。所涉及的费用难得反映在公司的标准会计报表之中,所以,必须加以设计──即为每一具体情况作具体估计。总量期望库存研究中的主要问题是缺乏准确数据。季节性预测、促销与价格变动的结果、成本数据与工厂的产出率,充其量也是难于估计的。然而,使用一致的数据时,总量分析能在各种为需求或供应中大幅波动作准备的方法中指出明确的选择。将实际绩效同即使是不寻常的计划作比较能提供早期的警告信号说明有作重新研究与改变操作的必要。总量运输库存它包括所有属于公司而且正在运往公司或从公司运出的产品与其它物料。这部份投资是为保持这些物料的流通而必要的。所需的量可计算如下:运输库存(金额)=每周发运金额×在途周数(8-6)因此,这库存的价值直接正比于发运量与在途时间。该发运量取决于作业──生产率与发运(销售)率。在途时间是可变的,取决于所选用的发运方法。发运越快,其费用越高而所需库存越低。货轮最便宜;火车、卡车与空运,一个比一个更贵。使用较慢方法的总运费节约是库存中附加资本投资的回报。显然,倘若该项资金的其它用途能产生出更多的回报,就应选用更快的发运方法。要考虑的其它显著因素是:1、倘若缩短补货提前期(多半在运输中),就可以减少现场仓库中的安全存238第238页共238页n货。2、船运与火车运输的水损与震动损失要高些。3、卡车与空运中盗窃与偷窃要低些。4、较早地收回客户发票,减少应收帐,具有现实的财务价值。5、采用快速空运发货可以取消高值、小体积而量大的产品(即电子组件)的现场仓库,保持或甚至提高客户服务。这些因素中每一因素的数据必须根据个别公司的经验来提出。现场仓库库存的补货分析详见附录Ⅶ。总量屏障库存这些库存是去购买更多的诸如贵重金属、谷物、动物纤维与皮革,矿物与木料等市价有显著波动的商品的“现场”决策的结果。另一类是由于要在预期的涨价或因罢工使供应中断以前去购买额外数量的物料的决策而产生的。这两种决策都是根据现在买进所节省的钱是否是该项额外库存的附加投资的足够回报。汇总这些数量的唯一意义在于显示资金的需求总量。这可用简单的加法。物料计划人员能够做的唯一贡献是去提供这类商品与物料的未来需求与现有库存量等信息。讨论潜在风险与有关的市场情况超出了本书的范围。管理好总的库存投资大多数负有库存责任的经理人员今天都处于试图去执行从未明确形成过的库存政策这样一种令人不愉快的处境。制订合理的库存政策要求具备关于现存各种方案的知识,而这就要求从总体上来观察成本及其它数据。所要求的计算比较繁琐,但在使用计算机的任何公司中都是完全可行的。那些能够向他们的上级提出总体库存信息并帮助上级制订出合理政策决定的库存经理们将能够工作在具有明确建立的政策的条件下,这种政策对库存管理中基本的比益抉择具有清楚的认识。不能提供总量信息的经理们由于缺乏明确建立的政策将几乎不可避免地要受到经常的批评。事实上不准备总量库存信息的经理能否真正被称为是在管理库存是颇成问题的。他们当然不是称职的专业人员。当经理们变得更加专业化,并能恰当地使用库存管理的原则与技法时,制造中许多真正的比益抉择变得显然了。那些不懂得这些原则与技法的人们努力要去获得正确物品的足够库存以便最大限度地减小几个模糊地定义的“成本”并去预防由于意外的混乱所引起的短缺。这是计划着去驾驭不可能计划的事件──根本上就是一种自相矛盾而且实践上是无效的。总量计划法提示出真正的可供选择的办法:1、提高质量并杜绝废次品2、减少不及时的供应商交货与落后于进度计划的作业3、提高机器与设备的可靠性4、缩短生产调整以允许只运转现在所需的东西5、消除障碍并加快流动,缩短提前时间6、提供灵活性与快速响应去处理混乱从根本上这种方法把库存看作是一作负债,而非资产。它揭示出真正的比益抉择──要末解决问题否则就要遭受损失;持有库存,支持该项投资而无论如何仍得238第238页共238页n期望麻烦。对多少库存才足够这个长期问题的答案是,少一些,永远少一些。原理38.库存是一种负债;越少越好。238第238页共238页n九.能力需求计划提前期:种类与要素在分配中,库存被买进、存储、再卖出,库存控制可以是一种平衡着采购经济的相当独立的功能,其目的是客户服务与最小库存。在一家制造组织中,库存或作为生产的结果而存在或为了去支持生产而存在。一家制造企业可以更改订货的时机与批量,如同受优先级考虑支配时那样,但在生产率未被改变去增加或减少工厂总产出之前,总库存水平将不会因此而发生任何改变。而且,一种忽视工厂作业效率(特别是,为了质量、仕气与成本等考虑而去保持顺畅、快速流动而且速率相当稳定的生产的必要)的库存控制功能往往是以提前期长、服务差与库存高为特征的。其原因涉及提前期与库存的基本关系。有两种不同类型的提前期必须加以管理:1、工作中心提前期2、订货提前期工作中心提前期是一份定单在被加工前化费在一个工作中心的排队行列中的平均时间。图9-1表示一典型的工作中心,其中有几份定单正在等待着加工。该排队行列的长度,即工作中心提前期,是在该中心的各个别定单的调整时间与运转时间之和。平均起来,这就是下一份定单要在该中心得以开始加工之前必须等待的时间。每一具体定单究竟将等待多久,当然要取决于它的优先级。优先级较高的定单将超越低优先级定单而较快地进入中心。然而,平均时间是排队行列中订单数的直接函数。这是不受定单优先级影响的;它取决于定单到达中心与离开中心的相对速率──它的能力。┌────┐①②③...n│工作中心│└────┘队列平均长度Q=(SU+RT)1+(SU+RT)2+(SU+RT)3+...+(SU+RT)n图9-1工作中心提前期原理39.管好工作中心提前期要求管好能力。对每一重要的工作中心必须设定一计划水平。这些计划水平应考虑工作到达速率的可变性以及工作中心停工时间的重要性与代价。具有宽广投入率变化幅度、负载处于临界状态、费用昂贵的作业需设定高标准的排队水平。设定这种计划平均排队长度的具体技法见本章后面。理想上,工程师、工具设计师、车间主管、调整人员与工人将共同努力去消除障碍并加快工作的流动以减少在制品库存。本章后面以及第二册中将对此作更详细的讨论。订货提前期──去补充一项库存物品所需的时间──由下列许多基本要素构成:1、文书工作时间2、生产调整时间3、运转时间238第238页共238页n5、排队时间文书工作时间(也叫做准备或行政管理时间)是同采购或制造订货的发起有关的一切工作所需的时间。为了第一次发放这种订单,它要用相当一段时间去产生必要的例行程序、规格说明、供应商选择等等,而且必须在计划与日程安排活动中考虑它。对于重复加工的物料,文书工作时间不必也不应被包括在计划订货提前期之中。像分时段订货点法与MRP这类订货技法对于将要发放的订单都提供足够提前的预见度以便为处理文书工作与有关活动提供所需时间。第5章的图5-16以及第6章的图6-5说明了这一点。不计文书工作要素可以缩短计划提前期、延迟工作的发放、降低在制品水平,而最重要的是,缩短制造计划中的灵敏视界(activehorizon)。它在总的计划与控制过程中的重要性在本书第7章与第二册第2章中讨论。它影响所有的起始或首当工作中心,包括一切接受订单去开始加工原料、子装配或组件结合与完工总装或包装最终产品的厂内或供应商的设施。运转与生产调整时间不用解释,移动时间是实际上化费在作业之间转移的时间,包括一项工作化费在等待移动上的时间;排队时间(工作中心提前期)是一项工作在一工作中心处由于在它前面有其它工作因而不能被加工所化费的时间。在大多数按功能组织的工厂与许多过程工厂里,检查一批样本制造订单去看看运转、生产调整与移动时间占制造提前期多大百分比的结果表明它们典型地小于总制造提前期的10%。构成提前期的主要成份是排队时间──由于有其它工作在加工而化在等待上的时间。在制品库存的主要部份是典型地没有在被加工,这表明对在制品总水平的控制是差的。在对在制品的控制只有很小具体努力的公司里,其结果是长的队列与长的提前期。实际上,缺乏健全的能力计划与控制的制造计划与控制职能使得高的在制品水平成为其作业中的必要。例如,考虑一家公司,它企图去控制库存而不考虑能力是否足够。补货订单由库存控制技法随机地生成然后下达到车间。库存控制人员不承担平整负荷或理顺工厂中工作流的责任。车间作业人员认为他们过去已收到的订单数的增涨只表示了一种随机效应。他们的主要目的之一是保持一支稳定的工人队伍,他们将建立工作积压以确保工作的供应。这将加长提前期,使得订单上的要货日期越来越没有意义,而恰当地安排制造订单的顺序变得非常困难。要确保某一特定订单通过车间,唯一办法就是催稽它。因此,情况就典型地降格为库存控制与催稽。对较长的提前期,库存控制系统通常的反应是在订货点或物料计划中去增加它们。这只不过生成更多订单,它反转来又创造一更高的在制品水平,后者又生成更长的提前期。这就是著名的“恶性循环”,详见第二册第5章。看看工厂制造车间现场上的在制品就可以确认车间趋向如此作业。在那些缺乏健全的能力计划与控制的工厂里,这类库存的水平是高的,物料蹒跚地通过这种工厂而不顺畅地流动,甚至在起始工作中心也有显著的积压订单。提前期长而且高度地易变。缺乏适当的能力计划与控制时,在制品将服从帕金森定律的一个变种──它将膨胀以填充可得的空间(或车间容器或计算机磁盘文件)。要控制在制品──从而要控制订货提前期──就要求对能力需求作计划并提供足够的能力去支持MPS。否则,优先级计划与控制就不能生效,不管系统的那一部份有多么精巧与有力。原理40.管好订货提前期要求同时管好优先级与能力这二者。238第238页共238页n能力计划的一种合理方法以预测为基础来生成订单时,把个别订单足够远地提早生成以便给制造人员或供应商一种作能力计划的手段是不现实的。还有,倘若只是根据优先级计划的要求去发放订单,则提前期趋向于变得极长而且高度易变。在实践中这两种方法往往降格成为催稽系统。由于没有一家公司的预测是完美的,任何成功的系统必须能够对付不完善的预测。倘若懂得并应用第4章里讨论过的预测的基本特征,这是办得到的。所涉及的两个主要特征是:1、预测的准确度是时间的函数;预测越是深入到未来,它的准确度会越小。2、预测的准确度又是被预测物品组内物品数的函数;产品组越大,预测可能越准。原理41.能力计划应使用经过相似制造作业的尽可能广泛的产品组。利用原理41.可以用计划为这些作业建立流速,而个别的制造订单则按计划速率在尽可能晚的时机并根据最近的需求来安排进度──不管这需求是由订货点技法还是物料需求计划来生成。选择有意义的产品组去作计划要求彻底了解工厂的制造过程。这些产品组难得与市场营销部门或库存控制中所使用的相同。该产品组必须从其对制造设施的需要方面具有意义。重要之点在于对产品组作预测总是比对个别产品作预测更为准确,而即使是一项粗略的能力计划也比没有计划要好。这种计划提供1、一种计划生产速率的手段。2、一种控制生产速率以完成计划的手段。3、一种调节工作发放到车间去的速率以控制在制品水平的手段。本章的其余部份用来讨论能力计划的开发,着重于它们在向高层管理者提出替代方案时的使用以及为特定设施计划生产速率时的使用。用这种计划来控制订单发放以满足计划生产速率在第10章讨论。第11章讨论使用能力计划去控制工作产出(workoutput)时涉及的技法与原理。经验已经表明在制造控制中能够作出的所有改进之中,能力计划往往是该系统中最显著与回报最优厚的一部份。得益较高而且较快。当缺乏有效的能力计划时,具有季节性生产的公司特别容易遭受高成本与低作业效率的损害。能力计划在高峰销售季节之前提早展开建立库存的计划并规划出一条道路,以便对照计划来度量实际绩效。没有能力计划时,这类作业中典型情况是管理者为在高峰季节之前所建的库存而惊讶,但关于需要多大库存水平却并无具体信息。往往是,其反应是对计划外的库存增加感到紧张不安,恰恰在高峰季节之前把生产量降了回去,然后,当销售速率上升而库存消失时又以很大代价再去提高生产量。有了能力计划,所建立的库存可以定期地同计划水平相比较,而库存究竟是过高还是过低可以及时作出决定以便采取有效的校正行动,而没有要去作无根据的讨论与作痛苦的决定的问题。生产计划的制定生产计划是给予工厂或制造设施的主要机组的能力计划的常用名字。它也可用于外购物料的商品编组。制订生产计划必须满足两个要求:1、生产计划应包括由某些共同制造设施所加工的产品系列或产品组。这当然意味着生产计划所用的预测是为这些产品组而做的而并非为只对销售部门有意义的238第238页共238页n那些产品组所做的预测。理想上,这些产品组将各有一份个别的MPS。2、生产计划应以对工厂作业人员简明易懂的方式来表达;即生产的度量应以件数、小时数等为单位来表示。制订生产计划的步骤是:1、确定该生产计划所覆盖的期间。许多公司提前一年制订一项总的、月度生产计划用来建立总的库存/生产政策并作为核对设备能力需求的基础。然后,他们制订一详细的周生产计划去计划与稳定对工人的需求。2、建立基库存水平。这是为满足管理政策所设定的客户服务水平最低限度应该持有的库存。使用物料计划来确定总量库存水平的逻辑曾在第8章中讨论过了。3、将销售预测展开于计划期间。这应将对销售率有显著影响的促销所引起的常规周期或高峰考虑进去。4、确定计划期初该产品组的总库存。对新企业这往往就是可用净库存,但也可能包括已经制造好但尚未被包装或尚未入库的物品。5、设定期末库存的希望水平。这是第1款中提到的基库存水平加上到期末为止用来弥补工厂停工、季节性高峰或其它需求的库存。6、计算出在计划期间所希望的库存水平的变化量。7、计算出计划期间所需的总生产量。它等于销售预测总量加上或减去从期初到期末所希望的库存水平变化量。8、把总生产量按所希望的那样分配到整个期间。应考虑假日或其它损失生产的期间以及从目前生产水平提高或降低生产速率所需时间。从实有库存出发,倘若期末所希望的库存与计划期间的销售预测为已知,则周生产量可用下式计算:R=(D-S+F)(9-1)N其中:R=在计划期间均衡生产的周生产量D=所希望的期末库存总量S=实有期初库存总量F=计划期间销售预测总量N=计划期间中的周数例如,设有冲压烟灰缸大类产品的下列数据:1、实有期初库存为130,000件2、所希望的期末库存总量为110,000件3、销售预测总量为140,000件4、计划期间有5周则R=D-S+FN=110,000-130,000+140,0005=24,000┌─────────────────────┐│全部冲压烟灰缸(件数)│238第238页共238页n├────────┬───┬───┬────┤│周日期│销售│生产│库存│├────────┼───┼───┼────┤│期初│││130,000││10月3日计划│20,000│24,000│134,000││实际│││││10月10日计划│25,000│24,000│133,000││实际│││││10月17日计划│30,000│24,000│127,000││实际│││││10月24日计划│30,000│24,000│121,000││实际│││││10月31日计划│35,000│24,000│110,000││实际││││└────────┴───┴───┴────┘图9-2周生产计划图9-2所示为此例的周生产计划。期初库存比期末的希望数高出20,000件。因此,总生产量必须小于销售预测总量。注意该生产计划每周有两行,一行是计划数,一行是实际数。在10月份,销售、生产与库存的实际数将被录入,并同计划数相比较,以便跟踪与控制生产速率。生产计划应当作预算来使用,将实际绩效同计划绩效相比较,以指示何时必须采取校正行动。在形式上它同第7章讲的S-P-I报告相同。生产计划,除了计划与控制生产水平之外,也调节进入工厂的订单流。其操作技法见第10章.生产计划是一种简单──但重要的──工具,而所需信息在大多数公司里是唾手可得的。事实上,许多不这样来使用生产计划的公司具备所有这些信息并且也把绩效同计划作对比──但那是分别地对销售、生产与库存来做的。大多数市场营销与销售部门将实际销售同计划相对比。财务人员保持跟踪实际库存水平并把它同财务预算曾以之作为基础的库存数据相对比。然而,如同许多财务数据一样,这些数字往往至少是一周以前的,在库存控制中并无多大用处。物料控制经理或车间经理保有的对比实际生产与计划生产速率的记录是要每日更新过的。虽然这一信息往往未被一体化,分别地去考虑它们时是无多大意义的。只有一道来观察销售、生产与库存这三个因素,才能作出最好的制造控制决策。如果销售达不到预测而且库存高于计划数,那末去坚持要一家工厂去完成计划中的生产率增长就是错误的。另一方面,如果生产上升达到了计划速率但销售超过了预测(使得库存降到了计划水平以下),则显然制造速率还需要提高。在一份生产计划中把这三个因素联系起来观察是建立健全的制造作业控制的首要与基本的步骤。在即将假日停工或生产中其它中断之前的期间里,要求生产计划作出一个困难的选择。由于生产上的损失,库存可能降到所希望的水平以下,结果是客户服务可能将比所希望的要差。有两个可替代的方案:或者是在该年度的前期以较高生产速率运行,然后再降低生产去达到年终的库存目标,或者是设定一较高的年终库存目标而全年维持一平整的生产速率。这些方案是制造业中典型的从“最差中选其最小”的选择。无论如何,生产计划只不过是个近似数。销售完全符合预测的机会几乎是零,238第238页共238页n工厂将准确地制造出计划生产量的机会也是如此。生产计划提高精确度的问题符合报酬递减律,到达某一点以后进一步化代价去提高精度是无意义的。能力计划并不要求其数字如何精确。生产计划时常被称为“粗能力需求计划”,但不应把它解释为粗糙的或低劣的。解释为“初步的”也许更为恰当。原理42.生产计划,即使是粗略的,却为能力管理提供有效的手段。季节性生产计划制订季节性生产计划时,计划者有三种可供选用的方案:1、以持有高库存为代价,维持一平整的生产速率。2、通过改变生产速率去满足季节性销售需求从而降低库存。3、把上述两种极端作某种结合,在关键时机改变生产速率使额外库存最小同时满足季节性需求。下面举例说明这三种方案。图9-3所示为制造全钢、汽车用滤过器的年度生产计划。此些计划有两点特别值得注意。第一点是它覆盖一个销售年度而非一个日历年度。生产与销售被计划去满足一个季节性的需求模式,它从十二月份的低谷开始,┌────────────────────────────────┐│全钢、汽车用滤过器││(所有数字以1000人时的劳务为单位)│├─────────┬──────┬──────┬────┬───┤││销售│生产│库存*││├───┬──┬──┼──┬───┼──┬───┤(9月30日│备注││月份││周数│本月│累计│本月│累计│为1200)││├───┼──┼──┼──┼───┼──┼───┼────┼───┤│十月│计划│5│800│800│1120│1120│1520│产量=│││实际│││││││224/周││十一月│计划│4│600│1400│896│2016│1816││││实际│││││││││十二月│计划│4│500│1900│896│2912│2212││││实际│││││││││一月│计划│5│1000│2900│1120│4032│2332││││实际│││││││││二月│计划│4│800│3700│896│4928│2428││││实际│││││││││三月│计划│4│800│4500│896│5824│2524││││实际│││││││││四月│计划│4│900│5400│896│6720│2520││││实际│││││││││五月│计划│5│1200│6600│1120│7840│2440││││实际│││││││││六月│计划│4│1000│7600│896│8736│2336││││实际│││││││││七月│计划│2**│1000│8600│448│9189│1784││238第238页共238页n││实际│││││││││八月│计划│5│1500│10,100│1120│10,309│1404││││实际│││││││││九月│计划│4│900│11,000│896│11,200│1400││││实际││││││││└───┴──┴──┴──┴───┴──┴───┴────┴───┘*基库存水平=1400人时**假期停工=2周图9-3季节性生产计划1到八月份达到顶峰,然后再下降。计划应该在销售季节接近终了时开始,因为正当销售降到低于生产速率时库存将为最低。第二点是此计划以人工小时数来度量库存、销售与生产,因为在这一大而混合的产品组中,有些个别产品的制造时间远大于其它产品,工时是唯一有意义的度量。然而,所有这些产品要经过的基本制造设备是相同的。季节性生产计划1(图9-3)企图平整全年的生产。从一月到六月,库存相当高,但生产速率是保持稳定的。季节性生产计划2(9-4)在一年中4次改变┌────────────────────────────────┐│全钢、汽车用滤过器││(所有数字以1000人时为单位)│├─────────┬──────┬──────┬────┬───┤││销售│生产│库存*││├───┬──┬──┼──┬───┼──┬───┤(9月30日│备注││月份││周数│本月│累计│本月│累计│为1200)││├───┼──┼──┼──┼───┼──┼───┼────┼───┤│十月│计划│5│800│800│805│805│1205│产量=│││实际│││││││161/周││十一月│计划│4│600│1400│645│1450│1250││││实际│││││││││十二月│计划│4│500│1900│645│2095│1395││││实际│││││││││一月│计划│5│1000│2900│1000│3095│1395│产量=│││实际│││││││200/周││二月│计划│4│800│3700│800│3895│1395││││实际│││││││││三月│计划│4│800│4500│800│4695│1395││││实际│││││││││四月│计划│4│900│5400│950│5645│1445│产量=│││实际│││││││238/周││五月│计划│5│1200│6600│1190│6835│1445││││实际│││││││││六月│计划│4│1000│7600│950│7785│1385││││实际│││││││││七月│计划│2**│1000│8600│620│8405│1005│产量=│238第238页共238页n││实际│││││││309/周││八月│计划│5│1500│10,100│1550│9955│1055││││实际│││││││││九月│计划│4│900│11,000│1240│11,195│1395││││实际││││││││└───┴──┴──┴──┴───┴──┴───┴────┴───┘*基库存水平=1400人时**假期停工=2周图9-4季节性生产计划2生产速率,但成功地维持一低得多的库存水平。季节性生产计划3(图9-5)在一年中两次改变生产速率,其库存水平在前述两方案之间。┌────────────────────────────────┐│全钢、汽车用滤过器││(所有数字以1000人时为单位)│├─────────┬──────┬──────┬────┬───┤││销售│生产│库存*││├───┬──┬──┼──┬───┼──┬───┤(9月30日│备注││月份││周数│本月│累计│本月│累计│为1200)││├───┼──┼──┼──┼───┼──┼───┼────┼───┤│十月│计划│5│800│800│975│975│1375│产量=│││实际│││││││195/周││十一月│计划│4│600│1400│780│1755│1555││││实际│││││││││十二月│计划│4│500│1900│780│2535│1835││││实际│││││││││一月│计划│5│1000│2900│975│3510│1810││││实际│││││││││二月│计划│4│800│3700│780│4290│1790││││实际│││││││││三月│计划│4│800│4500│780│5070│1770││││实际│││││││││四月│计划│4│900│5400│780│5850│1650││││实际│││││││││五月│计划│5│1200│6600│975│6825│1425││││实际│││││││││六月│计划│4│1000│7600│1272│8097│1697│产量=│││实际│││││││318/周││七月│计划│2**│1000│8600│636│8733│1333││││实际│││││││││八月│计划│5│1500│10,100│1590│10,323│1423││││实际│││││││││九月│计划│4│900│11,000│1272│11,595│1795││238第238页共238页n││实际││││││││└───┴──┴──┴──┴───┴──┴───┴────┴───┘*基库存水平=1400人时**假期停工=2周图9-4季节性生产计划3基本问题是一个季节性生产计划试图在库存投资与改变生产水平的费用之间寻找一个平衡点。如同在经济订货量问题上那样,解决这一计划问题所需的各项成本数据并非唾手可得的。这些成本中的主要因素是加点、雇佣、培训与解雇(所有这些成本可以某种置信度加以估计)。其它费用更为模糊不清,虽然完全一样是实在的。培训新雇员与面临解雇的工人仕气低落会降低质量,带来较高的报废与返工损失。频繁的解雇会给公司在劳工市场造成一个坏名声,使得公司难以雇佣与保有高质量的工人。生产速率的改变,特别是增长,是很难按进度去完成的。新决雇员在不同长短的期间内不能以所希望的速率来生产,其中有些人永远也达不到最低速率因而必须被替换。组件生产的增长往往超前于完工速率的增长;制造主管通常在看到确有物料可待加工之前不愿增加人员。图9-6用库存价值,持有库存的成本与改变产量的成本的估计数据将前述三种方案作了比较。按这些假设的成本,方案2总成本最低。平均库存平均库存平均库存产量改改变产总成本水平(1千元)持有成本变次数量的成本(千元)(千人时)(1)(2)(3)─────────────────────────────────#1计划2060¥41,200¥82401¥150¥8390#2计划131326,260525246005852#3计划162232,440648823006788─────────────────────────────────(1)¥20/人时;(2)20%;(3)¥150千/改一次图9-6生产计划1、2与3的比较应当指出方案2与方案3比方案1要求大得多的能力去对付生产的高峰。这可能接近甚至超过了可用的机器与设备的最大能力。管理者还应注意在2号方案中,假期后库存将比基库存水平低了许多。在3号方案中,生产以高产量进入滞销的季节。除非来年的销售要高得多,否则在3号方案中可能会比2号方案更早就需作另一次产量调整。这会使方案2比方案3更强地成为成本最低的计划。生产计划工作中的实际因素制订生产计划时值得考虑的事情有:1、改变生产水平需要一定的时间。下达改变产量的决定必须给工厂留出足够的时间。2、一年中假日的天数可能是影响库存水平的一个可观因素。在生产计划中设定日生产率与每周的工作日数将可对付这个问题。238第238页共238页n3、许多工人可能有3周或甚至4周的假期,结果其生产损失将超过2周的假期停工数。七月到八月似乎是生产松弛的期间,重要的是要指出在这一期间究竟生产损失将发生在何时。4、加班加点是昂贵的,但在某些情况下比加人要好些(从纯成本观点)。许多实际工作者的一条好经验是不要作计划去使用加班加点。他们的理由是加班加点可为对付销售中意外的波涛提供灵活性或用来弥补设备故障或类似的故障所引起的生产损失。再者,有计划的加班加点上马容易而下马要难得多。5、季节性生产计划应力图以最廉价的形式去存储生产小时。与其制造并存储一种只要求很少劳务的高价组件,肯定不如加工一种劳动含量高的低价组件。6、制订生产计划时,重要的是去取得并使用可能得到的最准确的数据并将信息呈递给管理者向他们说明真正的替代方案。7、生产计划往往以月份为基础做一年的计划。在快速移动的作业中,生产计划可以周为基础做每个季度的以便给出足够的细节使人们能紧紧地遵循着计划中的生产量、销售量与库存水平。8、关于生产计划最常听到的问题是它们应该多么频繁地被更改?这个问题其实没有抓住要点──目的是只有当必要时才去更改生产计划。事先就确定在什么样的条件下将有必要去改变生产水平是极端重要的。倘若事先并未建立这些规则,那么可能每周都要讨论现在的情况要不要改变生产水平,并引起经理之间不同意见的摩擦。第11章讨论可以确立哪些决策规则用来确定何时去改变生产计划。9、一家工厂应该为它希望去控制的每一主要制造设施制订一份生产计划。事实上,倘若有机会说明以不同的生产速率去运行一个总体制造区内的两个工作区是有利的,那么就应该建立两份生产计划──每一分区一份。分别制订制造作业与完工作业的生产计划使人们有可能独立地去控制(或提高或降低)每部份的生产速率。本章下一节详细讨论此问题。如前所述,开发任何生产计划时应避免过多的讲究与精度。10、挑选正确的能力度量去使用在计划工作中是特别重要的──生产计划应使用制造主管人员易懂的最简语言。确定有意义的语言最好的方法之一是去询问制造主管人员:改变生产水平时,如果生产进度计划上的件数增加了,人员要作什么改变?如果这些术语他们感到有意义,就可以了。如果他们要求用小时数,要弄到这种数据就要难得多,但这额外的工作往往是值得化费的,因为重要的是去生成对这些负责在车间中采取行动的人有用的信息。另一种在许多公司中已证明是很有用的办法是当量单位。对制订生产计划而言,一台能够同时把两种品位不同的汽油打进两辆汽车的二元汽油泵,将相当于两台只能向一辆车供一种产品的单用泵。其它型号也可同标准单元相联系。例如,一架分配器,缺乏打油单元的马达与有关的硬件(它们是在地下的储油柜内),将算作四分之三个当量单元。11、在计划中应显示累计的销售与生产数字。这些数字可用来使实际的销售与生产同计划数相比较,也可使销售同生产互比。市场营销部门可能对前一期间销售率较低作出不改变预测的决定,因为他们不相信该赤字将被补偿。因此,未来的计划就以实际的累计销售数字为起点。如果他们期望在未来不但能卖出预测数而且还能弥补以前的赤字,那就必须加大计划中的销售率。注意一个期间的实际销售与生产的总量累计数成了下一期间的期初数。在制订新计划时生产速率的提出要以季末所希望达到的库存水平与预期的总需求为根据。制订计划时使用这些数字照顾到上一季度的生产赤字。238第238页共238页n12、在备货生产工厂里为完成品制订生产计划时,服务对投资关系表(见第8章)是一种极有价值的工具。它有助于建立生产计划所瞄准的基库存水平。但要记住,服务对投资关系表是以年平均需求为基础的。在一年中需求变化很大的场合,一特定服务水平所要求的安全存货也是变化的。应用时在一年中需求有大变化的场合,服务对投资关系表应以库存达到其低点时的需求为基础,这时手头没有预期库存去辅助正常的安全存货。服务对投资关系表也可用来估计库存下降到基库存水平以下对客户服务的影响。有些生产计划方案包括库存暂时下降到低于一理想水平的一段期间,如图9-4所示。如果对客户服务的影响有一肯定的度量,就可以更好地评价要不要这样的方案。服务对投资关系表就是这样一种度量。功能部门的粗能力计划执行基础起动、制造或完工作业的功能部门,其能力更难计划与控制。企图仅仅使用库存控制技法与订单积压度量技法(例如机器负荷计算法)去计划与控制时,这些部门中订单流的不稳定速率会造成过长与高度易变的提前期,而且当总需求由于生意的好坏而变化时其反应很慢。为这些部门建立一个计划作业水平然后安排具体订单去满足这一计划这一普适原理,能够把组件的提前期缩短许多,制造作业可显著地得到平整,而且当业务水平变化时其反应时间可以缩短。一个制造组件的功能部门,其能力需求计划可通过把所有产品的MPS转换成为工作所需的标准小时数而建立起来。把MPS中产品件数转换成各个别中心里工作的标准小时数这一简单技法涉及劳务清单的使用。图9-7所示为一典型的劳务产品#13254标准小时数工作中心总计*9210888741453283691017*调整与加工的总计图9-7典型劳务清单清单,它在结构上与物料清单相似──因而得名。该产品(MPS表中的一种产品)要求清单中开列的各工作中心以指定的标准小时总数去做一切所需的工作。它并不包括加工所涉及的所有工作中心;表中仅仅列出了要准备生产计划的那些工作中心。表中的标准小时数包括生产调整与加工二者。当然,准确的数据产生更佳的结果,但即使粗略的估计也可开发出有用的计划。这种数据有时可从成本会计记录中找到。只要有了产品系列的劳务清单,就可以为功能中心的粗能力需求计划作出很好的开端,条件是这些产品属于已经作了总生产计划的产品组或其总计量可由MPS确定者。为个别工作中心开发能力需求的机理与下面要讲的为个别产品开发能力需求的机理相同,不过所用的数量与时间期间要与生产计划中产品系列所用的相同而不是与MPS中产品所用的相同。238第238页共238页n下一步是在MPS中的每一期间中去累计要生产在该期间中已安排的所有产品产品│13254│13255│13256│13257│13258│──────┼───┼───┼───┼───┼───┤期间的MPS件数│55│─│20│40│30│总计──────┼───┼───┼───┼───┼───┼───工作中心92│550│─│200│400│300│2150工作中心88│440│─│160│320│240│1410工作中心74│770│─│280│560│420│2560工作中心53│1540│─│560│1120│840│4420工作中心36│495│─│180│300│270│1560工作中心10│935│─│340│680│510│2980图9-8期间能力需求计划所需的工作小时总数。图9-8所示为某一期间的结果。注意这些计算的假设是:1、所有这些工作小时都需在同一期间完成(无提前期补偿)。2、只生产MPS中物品的数量(无确定批量大小的问题)。3、所有物品都必须生产出来(这些物品的库存无显著变化)。最后,可开发出一份汇总的能力需求计划,如图9-9所示。表中“目前能力”指近来实际产出的标准小时数(3或4周的平均值);这叫做实有能力(demonstratedcapacity)。所需能力在同现有数据相比之前要将3或4个期间的数字平均一下。这样就排除了由于刚刚给出的第1与第2两项假设所带来的局限性。能力需求同现有能力相比暴露出能力不足的瓶颈中心(如工作中心#53)以及能力富裕的中心(工作中心#10)。超过水平的数据变化表示有必要作能力调整。(所有数据为标准小时数)││所需能力│工作│目前├───┬───┬───┬───┬───┬───┬───┤中心│能力│期间1│期间2│期间3│期间4│期间5│期间6│期间7│───┼───┼───┴───┴───┴───┼───┼───┼───┤││平均数=││││92│2120│2100││││88│1460│1470││││74│2660│2640││││53│4140│4510││││36│1510│1520││││10│3280│2910││││图9-9汇总的能力需求计划第3条假设不成问题除非要有计划地去显著地减少组件的库存。如果需要,可为这类减少作出计算。这时在存货中的组件数可折算为每一工作中心存储的能力的标准小时数。238第238页共238页n原理43.能力需求计划不可被推迟;粗略方法是很实用的。(以标准机时为单位)┌──┬──┬──────┬───────┬────┐│周││订单│生产│组件存货│││├──┬───┼──┬────┤室库存││末││每周│累计│每周│累计││├──┼──┼──┼───┼──┼────┼────┤│4/7│计划│2800│64,190│4300│55,390│12,820│││实际│2570│64,200│5100│55,390│13,670││4/14│计划│2800│66,990│4300│59,690│14,320│││实际│3400│67,600│7580│62,790│17,850││4/12│计划│2800│69,790│4300│63,990│15,820│││实际│3260│70,860│4490│67,460│19,080││.││││││││.││││││││.││││││││6/30│计划│2800│97,790│4300│106,990│30,820│││实际││││││└──┴──┴──┴───┴──┴────┴────┘图9-10某功能部门的能力计划图9-10为一典型的能力计划。库存中组件的数量被折算成机加工的标准小时数,下游作业为生产而提取组件的订单以及补充这些组件的生产量亦如此折算。如果在组件层次上不需作显著更改,计划将只说明生产数据。有时,在为减产期间作准备时,例如若工厂设备布局要重新安排或一台关键设备要停车检修时,就希望暂时提高组件的库存水平。图9-10所示为某工厂在假期停工之前逐步建立库存的情形。对每一主要设施备一生产计划有便于在有必要增加一种组件库存而减少另一种组件的库存时可对个别设施作出生产速率各异的计划。以劳务清单为依据的能力需求计划通常被认为是粗略的。然而,在实施现代一体化系统的初期,它们能够在作业中作出还算可以的显著改进。使用简单、人工的能力计划与投入/产出控制技法便可猛砍在制品与提前期。随着准确数据成为可得时,这些粗略方法应予改进。改进包括:1、较小的产品系列或甚至个别产品2、更加完整、准确的所需工时的数据3、更多工作中心4、较短的计划间隔把握改变生产水平的时机很重要。保持一家制造厂的工作中心处于平衡是一件困难任务,而当库存下降、提前期缩短时它变得更难了。当在制品低时,在组件的生产速率尚未搞上来之前,是不能提高装配与完工速率而坚持一段长时间的。生产水平要求中雇佣与培训熟练人员的任何改变都需相当的期间才能完成。除非是有意要降低在制品,否则在物料投入速率已经提高之前去提高一个部门的要求生产速率是无意义的。在一家复杂的工厂里,贯穿一系列部门的生产速率提高必须根据这一系列作业的提前期与期初库存非常仔细地加以协调。要以最小的时间损失与混乱在238第238页共238页n有序的基础上去完成这种改变,健全的能力计划是必要的。对于厂内的服务部门,诸如涂漆、电镀或混合,重要设备组合的生产速率也必须加以计划──要知道由于工作并非源出于那里而是来自许多其它工作中心,要精确地控制进入这些部门的物料并非总是可能的。进入源部门的订单的有计划投入应当平衡到尽可能接近于满足服务部门的计划生产速率并确保给它们以顺畅的物流。详见第10章。细能力需求计划当具备恰当的数据与计算机程序时,对能力需求作非常详细的计算是可能的。数据要求是:1、所有已发放与已计划订单的有效到期日期。2、及时更新的工艺路线与加工信息。3、准确的生产调整与加工时间标准。4、处理所有作业的一个安排日程计划的程序。5、把工作分派到各个时间期间的一个加载计算程序。6、各工作中心的标准排队容差。7、计划外事件引起的负荷的估计。安排日程与加载计算技法详见第10章,它也提供确定标准排队容差的方法。图9-11所示为首当(起始的,子装配,最终装配,完工与包装的)与其它类型工作中心的典型负荷报告。它包括已发放订单与已计划订单并必须向未来伸展得足够地远(远远超过图9-11中的8周)以便提供有用信息。在首当工作中心,当然负荷将是书面的已发放订单的负荷;在其它工作中心,负荷将由实际订单(物料实际上在中心)与计划订单(已安排在指定期间将在中心的订单)组成。注意已发放订单在这里可以是实际的或计划的,要看它们已否按日程计划到达了中心。图9-11是典型的,因为它表明1、有相当数量脱期工作(其意义见第10章)2、最近将来的总负荷量,大多来自已发放订单3、在不同期间负荷有波动4、已发放订单在未来的陡降。这样的一份负荷报告仅当其假设及它所根据的数据为有效时才将是工厂情况的良好表示。这是错把精确当作准确的经典例子。除非精通加负载与安排日程计划的技法,否则很容易错解这些数据。第10章讨论这些技法。去假定每一期间的负荷必须由该工作中心来处理是错误的。即使在某些工作中心这样的能力波动是可能的,它们充其量也是困难的,而往往是不可能的。去假定工作中心能力必须足以处理所示的平均负荷(图9-11中为每周400小时)则是更严重的错误。有两个理由:1、此正式计划并不包括它将必须去处理的所有负荷。2、某些负荷必须保留在工作中心以提供计划中的标准排队。除了正式计划所计算的详细负荷之外,能力需求还有其它来源:1、现行MPS中未包括的新产品。2、在危机时替代工艺路线与加工的使用。3、报废品的补货与返工作业。4、由于任何理由而需要的额外加工。238第238页共238页n5、额外物料需求所造成的记录误差。从停产的产品、方法的改变与改善、新设备与暴露出来的过剩库存等原因引起的负荷减少可部份地补偿负荷的增加。这些补偿只能靠估计以确定要比正式计划数净增或净减多少。只要持有在制品(排队)是为吸收工作中心上负荷波动所必要,确定该工作中心的能力需求时就必须把这些计划中的排队从总负荷中扣除。由于明显的理由,成功的公司总是不断地努力去减少这些波动并削减在制品。原理44.能力必须足以支持MPS并能处理额外的计划外需求。外购物料的能力计划为了有效地控制原料与组件的采购,也要求建立一生产速率并安排订货日程去满足此计划速率。当供应商的生意中大部份来自少数主要客户时尤其有必要这样做。对重要供应商的能力需求应包括在劳务清单上,如图9-7所示,它应显示出能力的度量,诸如1、千件(对于紧固件、包装物料等)2、磅或顿(对于原料)3、加仑(对液体、化工品等)4、模子(对于铸件、塑料等)粗略的估计使得有效的开始成为可能,但应尽快改进以提高对供应商的能力计划工作。使用上节讨论过的详细计算方法,客户与供应商紧密合作,就可能开发、理顺并降低在后者设施上的负荷。流到供应商去的订单其速率变化不定会在其产出要求方面产生严重的上下波动并造成对客户服务大幅变化的后果。虽然事实上这是供应商的问题,但这不会减小它对客户的库存与作业的影响。供应商对客户不稳定的订货其自然反应是去生成相当可观的订单积压以便提高自身的作业效率。倘若给每一供应商一份能力计划,让他按计划工作并正规地安排各个别物品的组合以满足此计划,可以大大缩短供应商的提前期。随着每一组合日程计划的发布,应同供应商一道检查新订单与老订单二者状态。不管一家客户占有供应商的产出中多大一部份,仔细的能力计划与投入/产出控制可以导致适时(JIT)交货的结果。详见第10章。开发详细能力需求计划的步骤是:1、在MRP程序的整个视界上更新所有已发放订单与已计划订单的到期日期。2、给已发放与已计划制造订单上的所有作业安排日程计划(使用第10章中讨论的详细技法)。3、用所有已安排了日程的订单给所有的工作中心加负荷(使用第10章讨论的无限──负荷计算法)。4、求出每月或每两个月的平均负荷。5、加上不在正式计划中的已知的额外工作的估计量。6、加上为计划外随机事件(报废、返工、替代作业等)留出的余量(通常用百分数)。7、扣除已知的改善(工具、方法、新设备等)减少工作含量的估计量。8、从能力需求计划中的第一个期间扣除标准排队。9、把每一工作中心的能力需求同现有(实有)能力相比,突出能力显著有余或不足的工作中心。238第238页共238页n10、计划并实施校正行动。这种或其它严格、高度详细的技法可被成功地应用,条件是数据要准确、完整,环境要足够地有序,使得计划接近地表示将要发生或能够使其发生的事。只是有了必需的计算机能力并不是去使用这种详细能力需求计划的理由。原理45.详细能力需求计划可能看起来高度精确而仍然是很不准确的。订货生产工厂中的能力计划工作虽然能力计划技法比较易懂,但在订货生产工厂里去应用它们是较困难的。许多在这种工厂里作业的人相信在有效的计划信息可得之前必须先有客户订单在手,因此他们只能为积压的客户订单作能力计划。这种看法忽视了我们早先讨论过的基本的预测特征──即使在个别物品难于预测的场合,对大类物品还是可以以某种准确度来预测的。根据预测来作计划而非按照积压订单来作计划可缩短提前期,而即使不一定能满足客户的交货要求,它也是一种真正的竞争优势。在订货生产工厂里能力计划的第一步是去决定自制产品组的定义。这不像备货生产工厂里那样显而易见。但若认定最终目的是要计划生产速率,就可识别出要经过相似制造设施的相似产品组。即使如此识别出来的各产品组不能代表这些设施上的全部负荷,那末即使为一部份能力准备一份生产计划也远比没有计划要好而且几乎总是证实所化费的代价是合算的。下一步是去查看这些产品组的总需求历史。图9-12所示为这类分析。此例涉及一制造各种等级的纸张的一家造纸公司。一组粗纸10周期间的续入业务统计如表中所示。这一分析并不把续入订单分解为个别物品而是汇总起来(例中汇总生产小时)使它们对生产有意义。事先预测是每周约200小时。┌───────────────────┐│预测=200小时/周│├──┬──┬────┬────┬───┤│周│订货│累计订货│累计预测│偏差│├──┼──┼────┼────┼───┤│1│210│210│200│+10││2│220│430│400│+30││3│150│580│600│-20││4│230│810│800│+10││5│300│1110│1000│+110││6│270│1380│1200│+180││7│215│1595│1400│+195││8│180│1775│1600│+175││9│140│1915│1800│+115││10│210│2125│2000│+125│└──┴──┴────┴────┴───┘图9-12粗纸的续入订货累计销售量偏离预测的范围在正1周(195小时)与负1/10周(20小时)之间。这类方法的重大价值之一在于倘若该工厂真正需要有订单积压的话则它238第238页共238页n可以确定有多少未发放积压订货是必要的。例如,不用凭空假设这一具体企业中有3到4周积压订货是正常的,图9-12指出有了1周的积压就将足以保持生产以相当平整的速率进行。这一信息可用来确立一条改变生产速率的决策规则。根据这些数据,当总的积压超过已计划生产速率1周的工作量时,就应提高生产速率。这类分析的显著优点之一是它着重在总需求而非在个别订单,使得显著的趋势与因素不致被细节的迷津所掩埋。第5章里讲过的统计方法可用来改进在订货生产工厂里的这类能力计划工作。许多工厂既有订货生产也有备货生产车间,大部份业务在备货生产产品中,但也接受许多特殊订单。这种工厂的能力计划应为特殊订单每周留出一部份总的工时,可取不可避免上下波动的特殊产品续入订货率的平均值。能力计划图解技法在前几节中,生产计划与能力计划是表格式的,使用小时数与件数。然而有的实际工作者喜欢图解技法。为使图解生产计划表示实际情况,时间标尺可用周数、天数或4周期间以消除扭曲。另一方法是标示销售与生产的累计数,显然它比列表更加费时而且要看懂它也得有些研究。但有些人喜欢图示,而且能比读表更快地理解它。图解计划可能变得非常复杂,特别是当实际数据要同计划数据一道标出来对比时;而这本是生产计划与能力计划的最重要用途之一。许多实际工作者感到图示技法在业务文献中有点强调得过分了。大多数生产计划恰恰失败在它们应当成功的地方:快速地传达图象。要采取行动去校正偏离计划的人所需的信息要以小时数、工人数、件数、顿数等等来表达。如果给他们一份图示生产计划,他们得把图翻译成数字才能确定所需的行动。优先级与能力计划的结合必须认识有4类能力:1、理论能力(Theoreticalcapacity),也叫额定(nominal)、评定(rated)与标准(standard)能力。它是现存设施应当生产的出产量(5个人每周工作40小时应生产200小时的出产。自动化机器按设计每小时要做出一定数目的件数)。理论能力必须超过其它三种能力。2、所需能力(Requiredcapacity)是支持MPS所需的能力。能力需求计划技法就是为了要计算出这个能力。它应包含为计划外的需求而留出的余量。3、实际能力(Demonstratedcapacity)是近期实际上达到了的平均出产量。它应稍微超过所需能力,而后者往往是被低估的。4、有效能力(Effectivecapacity)是实际能力中被用来去制造正确物品的那一部份。它必须非常接近于100%。理论能力是难得达到的,总是有消耗去阻挡这件事。实际能力最容易度量。能力被用来去制造错误的东西降低了有效的总量,它必须等于所需能力。原理46.能力被用来去制造不需要的东西时,它就是被浪费了。完整、一体化的能力计划与控制在各类制造厂里要求有如图9-15所示的多层次计划。这些计划的主要区别在于其计划视界的长短与详细的程度不同。如同在预测、物料订货与任何其它功能中一样,选择恰当的技法去适应计划工238第238页共238页n作的要求是有效地去控制作业的关键。图9-15指出了这些技法。没有哪一种技法是最好的,只有当一种复杂、讲究的方法所带来的显著的可见效益将会抵偿它的费用时,才应当去选择它。在能力需求计划中更精确的数据难得是更准确的。计划视界范围时间期间决策技法──────────────────────────────资源计划一年以上月度工厂建设粗略计算(长期)季度设备采购劳务清单年度人力计划作业视界一年以下每周人力转移能力需求计划计划(中期)工作计划调整(小时数、班数)替代工艺制/买转包合同执行一到四周每日订单发放作业排序(短期)每周加班加点投入/产出控制替代工艺(见第10与第订单重叠11章)图9-15能力管理库存控制技法注重优先级(所需特定物品的日期与数量),它们自身并不能控制制造出来的库存;这些技法是设计出来对付提前期的更改但不是去控制它们的。提前期的控制取决于对积压订单的控制,后者又要求具有某种计划与控制能力与生产速率的手段。生产速率的控制光凭机器加载计算法是不够的──它基本上只是机器中心那里有多少工作的一种度量。真正的控制技法要求知道吞吐率。由于要求“从货架”发货与提供更短提前期的压力日益增长,加上提供稳定的雇佣的要求也在上升,所以根据预测而不是根据积压订单去计划生产速率是有必要的。需要长的计划视界却缺乏对许多重要因素的具体、准确的数据,使得粗能力计划技法比庞大的详细计算更为实用。虽然机器加载计算技法在某些公司里可用来计划生产速率,其主要价值在于揭示何处有暂时的过负荷、欠负荷与瓶颈的存在,如第10章中所述。对大多数公司,可按对制造能力有意义的大类产品做某种形式的生产计划以便根据预测而非根据积压订单来提供能力改变。由于提前期很大程度上依赖于积压订单,有必要做生产计划去计划与控制生产速率并提供一调节器去控制订单投入以便控制住在制品的水平。于是订单便可按常规的每周甚至每日的进度表投入生产去补充客户所需的物品,目的是达到适时(JIT)响应。承担更多责任去推测能力需求然后控制投入去满足事先计划的速率这一思想并不难理解与接受;然而,要在一具体工厂里去实施却非常困难。对于习惯于发放订单然后催稽的计划人员,为顺畅的工厂作业去承担更多责任这种思想他们是陌生的。能力计划方法必须按工厂的具体情况去裁剪,并必须以主计划的推测为依据而非以现存的工作排队为根据。随着要求更低的库存、更稳定的工厂生产速率与改善客户服务的压力不断地使人们有所感受,根据预测而非根据积压订单去计划与控制生产速率的技法将有日益增多的开发与应用。238第238页共238页n十.投入控制1.投入控制在有效的制造控制中的作用2.选择恰当的投入3.从属工作中心的日程计划4.控制车间投入的行动5.安排日程计划的技法6.工作中心加负荷法7.控制对供应商的投入8.装配作业的日程计划9.项目的计划与控制10.线性规划与排队理论11.实际的考虑投入控制在有效制造控制中的作用前面我们已经开发了计划库存水平、物料订货与计划生产速率的方法。如果要控制在制品、订单积压与提前期,对投入到制造设施与供应商的订单控制必须是库存需求与可用能力二者的函数。投入控制可分解为若干因素:1、选择正确的订单去投入到工厂,或根据物料控制系统或根据客户订单而且其投入速率配合着已计划的生产速率。2、安排好订单的日程──把所希望的起始与/或完成日期分派到每份制造订单上必须被完成的作业。3、计算订单的负荷──为每一工作中心中所有已安排日程的作业开发在每一时间期间中所需小时数的总计,并将此总计同该中心的处理能力相比较。第9章所述能力计划技法往往以相当粗糙的形式建立所需的经过诸生产设施总238第238页共238页n的流速从而为能力、总在制品水平与总提前期的控制提供一种手段。选择投入的过程选定个别制造订单的投入顺序使得库存系统的需求同工厂或供应商的能力处于最佳平衡。日程安排为跟踪工作进程经过后续的制造作业提供基础而机器加载法(machineloading)是一种短期优先级控制技法,它着重于由于企图满足物定订单的进度计划而造成的逐日的瓶颈与欠负荷。投入控制本应在为如期完成工厂计划而需的车间控制之间。在实践中,投入控制受到了太小太小的考虑。投入控制的缺乏引起过多的重新计划、调度与工作跟踪──有时包括寻找丢失的工作;它把生产控制功能降格为一群催稽者,他们工作时间极长,拼命地度图回答接二连三地来自销售人员与制造人员双方的一大堆有关工作迟延与进度被中断等问题。当某些生产控制的努力被引导进入更好的投入计划与控制时,情况就大大地改善。当完成更好的投入控制时,工作定位、催稽与调度就只需化较少时间与精力;更为重要得多的是,通过使得更多工作按日程计划完成获得的正面效益。选择恰当的投入制造公司里所用的所有库存控制技法在车间订单的发放速率方面都生成随机的峰与槽,即使MPS是平整的亦然。为了控制车间与供应商的提前期,这些订单进入车间的流动必须加以调节。按时完成订单要求有正确物品的订单以符合计划生产水平所需的速率顺畅地投入。去发放过多订单的诱惑看来是不可抗拒的;过份热情的计划人员通常工厂过负荷,看来主要是出于想通过使工作按时或提早开工来确保满足要求的日期这样一种愿望。想避免空闲或停工这一势不可挡的愿望也造成可观的缓冲订单保持在每工作中心。这种行动的弊远大于利。这些弊端包括在制品中大量的投资、要求过多的工厂空间,长而不稳定的提前期、组件的库存过多与私有制。以车间与供应商能够处理的速率来投入订单就可轻易地避免这些弊端。其机理是简单的。┌───────────┬──┬──┬─────┐│所有数字皆为件数│销售│生产│库存│├───────────┼──┼──┼─────┤│第8周(实有期初库存)│││22,000件││9周计划│5200│6000│22,800││实际│││││10周计划│6200│6000│22,600││实际│││││11周计划│6200│6000│22,400││实际│││││12周计划│7200│6000│21,200││实际│││││13周计划│7200│6000│20,000*││实际││││└───────────┴──┴──┴─────┘图10-1生产计划──各种款式的灯具238第238页共238页n图10-1所示为一家制造多种灯具的厂家所提出的一份简单的生产计划。这份生产计划只管最终装配作业;其它类似的生产计划涉及组件的制造顺序。注意此计划要求在5周期间以平整的速率生产而且期末库存要下降10%。图10-2所示为该生产计划中所包括的灯具的每周生产日程计划报告。此报告中有许多要素可在一标准的存货状态报告中找到。它出示每一物品的续入业务、净可用存货、当前工厂订货量、订货点与经济订货量等数据。但此报告的其它特色┌──┬──┬───┬──┬──┬──┬───┬──┬────┬───┐│灯│每周│年截止│净可│工厂│订货│用加权│存货│订货点表│经济│││续入│续入业│用存│││平均续│总周│达为存货│││具│业务│务│货│订货│点│入业务│数│周数│订货量│├──┼──┼───┼──┼──┼──┼───┼──┼────┼───┤│#7W│341│17,933│1739│3078│2730│485│10│5.6│2250││#7D│288│9837│1224│832│1436│274│7│5.2│1500││#9W│854│35,329│4007│1956│4242│924│6│4.5│2000││#9D│251│10,120│2189│662│1386│259│11│5.3│1500││#9P│1187│46,690│8371│----│6250│1290│6│4.8│2500││#11D│1332│47,078│2844│7050│6768│1345│7│5.0│2500││#11P│598│21,890│778│3302│3346│639│6│5.2│2000│└──┴──┴───┴──┴──┴──┴───┴──┴────┴───┘图10-2周生产日程计划报告(数字为件数与周数)是专为它能用来生成订单去满足计划生产速率而设计的。在此报告中,第4章讲过的指数平滑技法已被用来更新一每周加权平均的续入业务以作为对每一物品的需求预测,使得最近的销售趋势能被反映。订货点本身也用第5章所述的方法重新计算了平均绝对偏差以修订后备存货部份。总库存(现有破除纲与工厂订货量之和)与订货点二者都表达为存货周数,方法是用每一物品最新的续入业务预测数去除它们。安排日程者9物料计划员或调度员)在选择灯具去填写开工日程计划时使用此报告去满足计划生产速率。图10-2中生产日程计划报告上所示所有灯具的总库存都超过了其订货点。在库存由于季节性销售或假期停工的期望而逐步增加时,这是一种相当正常的情形。尽管如此,可使用这一报告去选择恰当的物品排入日程计划以满足生产计划所示的每周6000件灯具的计划生产速率。要做这件事,计划人员挑选最接近其订货点的灯具──存货数最低的──并列入日程计划使库存保持平衡。报告中有三种物品其库存水平为6周:第一种是#11P,它最接近其订货点,其次是#9P;第三是#9W。把这三种列入日程计划将发放总计6500件灯具的装配生产任务。虽然此数略为超过了计划生产速率6000件,计划者在本周发放了这些订单之后将会在下一周的开工日程计划中补偿这一小量的超额。精确地去调整订货量使它刚好等于计划生产速率既无必要也是不能被证实的。这样一份生产日程计划报告为生成一份开工日程计划去满足计划生产速率提供一种技法,它比让订货点去随机地生成订单从而对车间的生产能力提出大幅度变化的需求要来得优越。另一极有价值的特色是它还取消了当期望高销售或低生产的期间而需逐步提高库存水平时去重新计算订货点的必要。生产计划指出了要增大库存238第238页共238页n所需的总量而日程计划报告揭示为了去生产正确的产品组合应从哪个物品去着手。修补订货点是不必要的。如果在生产日程计划报告中所有物品都分等排序,使计划者一目了然哪个物品接近其订货点,它的使用就更方便了。图10-3所示为所有物品按存货周数总计的升序与订货点的存货周数的降序排列的每周生产日程计划报告。此法可由人工来应用,但物品品种数大时将需由计算机去作排序与列表的工作。这类分等排序法能加快日程计划的准备并减少此工作中的差错。┌──┬──┬───┬──┬──┬──┬───┬──┬────┬───┐│灯│每周│年截止│净可│工厂│订货│用加权│存货│订货点表│经济│││续入│续入业│用存│││平均续│总周│达为存货│││具│业务│务│货│订货│点│入业务│数│周数│订货量│├──┼──┼───┼──┼──┼──┼───┼──┼────┼───┤│#11W│598│21,896│778│3302│3346│639│6│5.2│2000││#9D│1187│46,690│8371│----│6250│1290│6│4.8│2500││#9W│894│35,329│4007│1956│4242│924│6│4.5│2000││#7D│288│9837│1224│832│1436│274│7│5.2│1500││#11D│1332│47,078│2844│7050│6768│1345│7│5.0│2500││#7W│341│17,933│1739│3078│2730│485│10│5.6│2250││#9D│251│10,120│2189│662│1386│259│11│5.3│1500│└──┴──┴───┴──┴──┴──┴───┴──┴────┴───┘图10-3分等排序的周生产日程计划报告原理47.应当在选用订单去发放之前使用订货技法简明地按优先顺序将订单分等排列。生产日程计划报告(productionschedulingreport)提供在库存控制与生产控制之间的联系环节。它提供计划人员有效地做好选用必须被包括在开工日程计划(startingschedule)上的物品的工作所需的工具,以便把工作分派到车间去达到计划生产速率。这减少车间中对大量书面订单积压的需要,当生成订单而不考虑车间的生产能力时订单大量积压是不可避免的。在计划人员与他们的上级管理仙员中间,对于去偏离被订货点法与MRP等订货技法所突出的订单的开工日期的做法有强烈的反对,许多人相信提早发放订单将以生成过量库存为结果而订单发晚了将使按时交货受到危害。这些人认为订货技法所使用的标准提前期是固定的,而其实它们只是平均值。倘若计划人员只负责及时发放订单,由负荷不稳定、高在制品水平与长而不定的提前期就是其不可避免的后果。计划人员必须也为顺畅、平衡的工作发放负责,以配合工作中心与供应商用来处理这些工作的能力。当准备日程计划时除了制造设施的总体能力之外还往往必须考虑其它因素。例如,在安排印刷业务,自动车床部门或印刷电路板组件的自动插入时,该部门完成所需调整次数的能力同它的可用它机时总数是一样重要的。在这种情况下,定期地观察部门中所制的所有零件(使用如图10-4所示的日程计划报告)将使日程安排既能照顾总的机时又能考虑极限的最大调整次数。首先,必须根据所有零件的预测使用率,加上或减去这些零件的库存水平中任何所希望的改变的效果,设定一目标小时数。这犹如第9章中讨论过的生产计划的238第238页共238页n准备一样,不过这里不用件数或金额而使用机器时间的小时数或其它能力度量。使用这两种因素,即总时数与调整时娄,计划人员能评审所有物品的库存情况,如图10-4“下次计划订单发放”栏所示。例如,此报告指出组件21、30与┌───────────────────────────────────┐│周末12-10││周号4870计划每周排定小时数││部门8410最大调整小时数││工作中心#1700110工作中心总时数│├─┬─┬─────┬─────┬──┬────┬──┬──┬──┬──┤│零│A│││年使│下次计划│订货│订货│订货│调整││件│B│描述│用途││││量成│量小│││号│C│││用量│订单发放│量│本│时│小时│├─┼─┼─────┼─────┼──┼────┼──┼──┼──┼──┤│21│A│第2轴│"A"马达│3000│#47周│200│1222│22│5││30│A│上弹簧座│"A"马达│6000│#48周│700│281│31│3││59│A│活塞│"A"马达│6000│#3周│400│298│31│2││64│B│下弹簧座│"A"马达│6000│#50周│1000│235│40│3││18│C│垫圈│齿轮箱│1000│#51周│500│41│12.5│2││27│B│衣柱│齿轮箱│2400│#51周│400│138│20│2││29│C│弹簧│连接器│200│#50周│500│25│50│3││34│C│调整螺丝│连接器│2400│#50周│2300│85│77│3││54│C│球座│紧急释放│275│#50周│150│37│30│2││55│C│弹簧插头│连接器│275│#51周│250│29│25│3││56│C│底座板│"B"马达│82│#2周│100│82│9│3││46│C│#3-第1,#5-│控制箱│850│#49周│450│131│15│5││││2镜止夹││││││││└─┴─┴─────┴─────┴──┴────┴──┴──┴──┴──┘图10-4转塔车床──周进度回顾46应在下周开工。如果计划者安排了这些组件,他将发放:──────────────────组件订货量小时调整小时──────────────────212253031346155总计6813─────────────────这将接近于计划每周排定小时数70,但将超过了最大调整小时数10。因此,车间不能运行这一日程计划。检查一下该组中接近发放日期的其它物品,计划者将发现组件27很快即将重238第238页共238页n新订货。用它取代组件46,其迟延要小于组件21或30,日程计划将是:──────────────────组件订货量小时调整小时──────────────────212253031327202总计7310─────────────────这对车间将是实际可行的。计划者然后将确保把组件46安排在再下一周,甚至可能要去催稽此零件的后续作业以削减正常提前期从而使它及时入库。虽然些例大为简化了实际情况,它阐明一很有用的去满足生产能力上两种约束的日程计划技法。前述用来选择一成功的订单组合去匹配计划生产速率的技法可直接应用于起始的(首当)工作中心,即第一个(重要的)按照从一计划系统发放出来的订单去完成作业的中心。它们的典型如车削、刨、磨、冲割与成形等机器作业。在过程工厂里,它们包括混合、配制、分类与分馏。然而,子装配与总装配作业也是起始作业,因为它们涉及按照系统所发放的订单来开始的工作。同理,外购物料的订单也应由这类技法去安排日程;供应商实际上是起始工作中心(插在一系列厂内制作的作业中间的一道转包出去的作业可能是例外)。这类工作中心可以很顺畅的投入。少数订单排队等候与短的提前期来作业,使它趋近于适时生产。从属的或下游工作中心则并非如此容易去理顺的。从属工作中心的日程计划在按功能组织的车间里,所有相似的作业与设备都集合在一起,从属工作中心通常从若干其它中心接受工作。去理顺这些从属工作中心要求识别追随相似路径经过这些设施的订单。大多数间歇型、半过程型甚至被称为任务车间(jobshop)的车间都有一可定义的由物品的系列经过该车间而形成的工作流。虽然即便是最粗糙的去控制在制品的企图也能取得某些改善,但一旦作业顺序合理的流水线能被识别,就可采用特定的安排日程计划技法,使计划人员能大大降低在制品而并无过多停工的风险。在这类流水线能够被识别的地方,由于计划人员能够超越第一个作业而看到由于能力受限制或由于作业缺乏灵活性而真正成为瓶颈或有可能成为瓶颈的后续作业,因而可以大大地改善作业。把工作投入一个后来将被积压的起始作业是自拆台脚的。有许多车间里生成一个周日程计划去满足计划生产速率,然后由计划人员逐日发放个别订单到车间是相当实际的。例如,考虑PatterPanel公司的例子,该公司制造控制板成套。作业的一般顺序是:1、剪料──冲压部2、冲割──冲压部3、成形──冲压部4、打毛刺──子装部5、插入套管──子装部238第238页共238页n6、装扣件──子装部7、电镀或涂漆──完工部门8、检查──质管部9、包装──发货部该公司追随图10-5中所示的简单生产日程计划系统,使用类似于前面所述计划者每天检查订单并发放订单到冲压部┌──┐以满足下列目的:┌───→│制造│───→到冲压部1、客户服务││订单│2、高效的车间作业│└──┘3、最低库存水平││┌───┐图汇总用来确保││已发放│发给冲压的工作├─────→│工作│要尽可能使后续│└───┘作业平衡│├──┐││┌───┐周汇总用来出示积压订单的│││待发放│组合在冲压、子装、电镀与│└──→│工作│涂漆之间是平衡的│└───┘│去冲压部的待发放订单图10-5PatterPanel公司──生产日程计划系统的技法,每周发放一均衡的负荷进入这一系列作业。其重点是快速流动。他们接受许多个别订单,其中大多要求相当短的加工期。图10-6所示为用来给所有作业安排日程计划的每周发放汇总表。┌─────────────────────┐│#14周│├────┬───────────┬────┤│负荷中心│已发放小时数│周能力│├────┼───────────┼────┤│冲压部│2048108168180│240小时││子装│4060105115│120小时││电镀│5112428│80小时││涂漆│101636│40小时│└────┴───────────┴────┘图10-6PatternPanel公司──每周发放汇总表对每一主要负荷中心,计划者有一每周要发放的累计小时数的目标。冲压部面238第238页共238页n临的订单要每天检查。随着新订单被发放,计划者试图选择能提供其负荷是在后续部门能力以内的订单。例如,根据图10-6中的信息,计划者将试图发放的订单其总计对冲压部门尽可能地接近240小时,而在子装部不超过120小时,在电镀不超过80小时或在涂漆不超过40小时。这种方法确保快速流动经过这一系列作业,只要工作中心的能力足以处理该总负荷。辅助每周发放汇总的是待发放订单的每周分析,它显示多少工作将生成给冲压、子装、电镀与涂漆等部门。因此,在事先就可以看出将被下达到车章去的小时数的组合中的任何激烈的变化,从而可以制订增加或减少能力的计划。特别是在有一部份备货生产产品同订货生产产品一道生产的场合,有时可能看到由于订货生产业务中产品的组合,电镀的负荷将发生暂时的下降。这时就可以通过生成更多备货生产订单,使得电镀设施的负荷得到补偿而有助于平衡。这种投入负荷的平衡法是控制自称为任务车间而具有半过程流水作业特征的许多车间的工厂里对一系列的三个最┌───────────────────────┐│运转时间(小时数)│├─────┬─────┬─────┬─────┤││作业2│作业8│作业10│├─────┼─────┼─────┼─────┤│工作A│---│2.22│3.99││工作B│2.76│4.96│6.00││工作C│---│---│6.75││工作D│0.63│0.50│1.30││工作E│8.75│7.80│8.75││工作F│13.52│11.84│12.64││工作G│7.64│6.56│7.24││工作H│1.46│---│3.26││工作J│2.52│2.00│5.20││工作K│4.38│4.44│8.04││工作L│7.30│8.00│14.00││工作M│16.96│13.80│13.40│├─────┴─────┴─────┴─────┤│#1日程计划=工作A,B,C,D,E,F││#2日程计划=工作A,B,C,D,E,H,J,K│├─────┬─────┬─────┬─────┤││作业2│作业8│作业10││计划能力│20小时/周│20小时/周│40小时/周│├─────┼─────┼─────┼─────┤│#1日程计划│25.66│27.32│39.43││#2日程计划│20.50│21.92│43.29│└─────┴─────┴─────┴─────┘图10-7为顺序的作业平衡其投入关键作业:第2、第8、第10作业的负荷平衡法。在实际安排订单日程之前,机器负荷已被逐周地推测地估计其所需能力。这是能力计划的功能,实际订单用物料238第238页共238页n计划分别地来生成。预期在每一作业应有足够的平均能力可用,但已知倘若只是随机地将订单下达投入投入生产则将引起工厂现场的过负荷与欠负荷。每周重新检查一次订单,把它们置于最新恰当的优先级(用字母标识,订单A为最高级)。这些制造订单放在一个“待发放”文档中并由一计划者每周加以检查,其目的是使所需订单投入加工过程同时在各设施上生成最佳平衡负荷。日程计划1,包括订单A、B、C、D、E与F,将在作业2与8造成超过10%的过负荷,超过了本公司的允许值。从它除去工作F──因为它的优先级最低而在作业2与8中它的小时数占了高百分比──则所有作业的负荷都不足了。从待发放文档中下一个较低优先级的工作中,挑选工作H、J与K,结果是一个平衡得更好的日程计划,其过负荷与欠负荷都不超过10%。工作G被跳过,因为它将生成同工作F一样的不平衡情况。显然,工作F与G在下一周的日程计划上将具有很高的优先级。这一方法实际上只是把订单积压在计划者的桌子上而不让它积压在车间现场,但其结果是避免了把工作发放到起始作业之后却不得不让它停顿在某一后续作业上。安排负荷平衡的日程计划意味着工作更加顺畅地流动使车间积压订单保持在最小值,在制品水平保持最低同时保持所有作业都有活可干。这种方法往往难以被习惯于按订货技法所说的去开始发放工作到工厂的计划人员接受。把积压放在办公室的好处是对优先级的变化、工程更改等可有更易更快的反应。若这些订单积压在车间,催稽人员得到那里试图去挑出恰当的订单而并无多少信息能帮助他。负荷平衡法是控制车间投入的一种有组织的方法,宁可同传统的安排日程计划与加负荷技法一道使用。如果工作通常并不追随同一路径,平衡负荷时就可能有必要把时间期间考虑进去。例如,一涂漆作业,在一件工作可能是第5作业而在另一工作上是第12作业。在这些条件下,把这些工作当负载来加时把到达时间考虑进去将是重要的。这一方法实际上同本章后面所述的有限能力加负荷法完全一样。为了解释其概念,前面已介绍了取简形式的负荷平衡法。但若要平衡两以上的作业,其计算可能变得很烦。这一逻辑可以编成程序让计算机来选择最佳趣始日程计划(Optimumstartingschedule)。控制车间投入的行动选择投入与负荷平衡等技法并不能阻挡客户要求与订货技法在车间引起不均匀的需求;它们只是试图以一种受控的方式而不是靠在车间现场持有在量库存去平滑掉需求中的随机起落。原理48.订单积压在办公室比它们在车间现场可以被控制得更好一些。原理48确实是车间投入控制的最重要原则之一。倘若要控制住在制品,下列行动是重要的:1、使用类似生产日程计划报告(图10-2)或每周日程计划回顾(图10-4)等技法选择恰当的投入以满足计划生产速率,如果车间不是真正按此计划速率进行生产,发放到起始作业的工作量不应超过实际的产出。对于知道该产出是需要的计划者这是一个难点。学会去使用生产计划而非用在制品的积压去控制能力可能要求对计划人员、主管人员,甚至对许多经理们推行相当大的教育计划。原理49.投入应当小于或等于──但永不大于──产出。2、把积压订单清除出车间现场,因为积压在车间现场a.较难去控制238第238页共238页nb.使得实施工程更改更加昂贵c.产出更多的赶制d.引发实际问题(较新的工作堆在较老的工作前面使它们被挤到墙角落里)。对任何计划人员最难的事情之一就是去拒绝使订单开工的诱惑。对计划人员而言,使得每样东西都已对工厂订货而且当工厂不能完成计划时去强调这一点是值得欣慰的。不幸的是,工厂里的工作越多,去控制真正的工作选择要化费的代价就越多。在工厂现场过多的积压会使得正确物品通过生产的问题严重地复杂化,而恰恰在能力紧张或车间完不成进度时,工作的选择变得最为关键。3、根据最近的需求而非订单当初生成时建立的发放日期去安排订单的顺序。当必须把某些订单的积压保留在生产控制办公室而且在发放日期的建立中包含需求预测时,该生产控制系统应该设计得使计划人员或调度人员根据在尽可能晚的时机所建立的日期去发放订单。即使当其它要求使得“待发放”订单文档有用时,计算机(它能把许多物品变化着的库存需求同生产需求相比较)的可得性与第11章中所述的诸如关键比之类技法的引进,使得定期地检查所希望的计划日期以确保订单仅仅根据尽可能晚的需求信息去发放到工厂这件事成为可能。4、只给工厂能制造的物品安排日程计划。在生成订单去满足已计划生产速率时,如果这些订单并不能在该计划期间去运行,则去发放它们就是无意义的。改善制造作业的首要步骤之一就是去强制计划人员或调度人员对缺乏原料、组件、工具或其它必备物料的一切订单不要发放。这一办法将清楚地定义要把工作弄成功其基本问题在哪里。它将使问题一目了然,究竟不能达到生产速率的原因在于物料控制未能为所要制造的物品提供外购物料、工具、车间文书工作或类似的物品,还是由于工厂没有足够的工人或设备按所希望的水平去生产。另一好处──对它不应低估──发放对工厂而言代表真正工作的不变订单提高车间作业人员对计划与控制人员能力的尊敬,而且也对后者的决定产生信心,导致更好的合作从而使车间的作业大大地改善。对于一切必要物料具备之前不应发放订单这一规则有一些例外。如果一完工产品要用3周去装配而所缺的唯一组件要在末道工序才加上去,则可将装配令下达到车间以便立即开工,条件是如果计划人员有信心到需要它时,将有该暂缺组件可供使用。在医药、电子与类似的尖端行业中,还有其它根据具体情况的例外,因为在日程计划未发放之前无法确定该产品能否真正被生产出来。在涉及定制产品这类作业中,不可能确切地肯定究竟将需要什么组成物料。5、采取短的计划周期,每周甚至每天去作安排。这不仅有助于使所安排的订单获得最近的与最准确的需要日期,而且还有助于控制这些订单流径工厂。JohnF.Magee(7)讲得非常好,他说:“日程计划做得越频繁,即计划周期越短,在制品库存就可以越低,物料就能更快地通过各部门得到加工。例如,在所描述的安例中,计划周期若从1天变到1周就将意味着总加工时间约从13天增长到约6周。在具有半过程流与许多间歇作业的典型制造作业中,为执行大多数起始作业的部门制订一每月日程计划给该部门以很大余地去选择在任一特定日期去运行哪些物品。他们正常地运行那些适合他们自己的方便与绩效度量的物品;流进后续部门的负荷可能并不配合他们的能力。结果是在这些部门为了把其生产维持在平整的速率上就必须有大量的积压工作。再者,如果不管一件工作是在月初还是月末制造出来,该部门都被认为是按计划完成任务,那么报称的提前期将必须非常地长以便告诉客户以现实的交货日期。238第238页共238页n在生产控制与制造人员中间有一种广被承认的有趣的谬论,认为计划期间必须等于提前期。往往听人提问,需要1个月去制造的一种产品,如何可能只有一每周的日程计划。虽然它听起来完全有理,但并无理由为什么计划期间必须等于总提前期。即使在具有要在6个月提前期内完成一系列的50种不同主要作业这样一家公司的极端例子中,也必须有人实际上每天要去作出决定究竟哪些物品将在每一作业中开工。这并不需要一份不变的6个月的开工日程计划。肯定更明智的办法是根据尽可能新的客户要求、库存状况与车间工作负荷信息去发布每周的开工日程计划。只有这样,一家工厂才能保持足够的灵活性以经济方式去对付变化着的需求。这些原则有助于在头道工序去控制流入车间的工作。然后由安排日程计划的技法去提供使工作不断地流入后续作业的基础。安排日程计划的技法安排日程计划是为自制产品加工过程中重要步骤规定日期的活动。它是计划与控制而非执行的一部份。它的目的是为执行情况提供与之对比的里程碑以获取有必要采取校正行动的早期警告信号。安排日程计划有三个层次:1、MPS,表示产品数量日期2、订货日程计划(Orderschedules),为成批原料、外购组件与自制产品给出开工与完工日期3、作业计划(Operationschedules),为在工厂里加工一份组件订单所需的每一重要作业提供开工与完工日期(或时间)。主生产计划与订货日程计划通过该计划产品的物料清单而连接在一起。父件与组件的订货日程计划也是如此连接的。这些计划的修订与更新都由MRP的重新计划功能来协调。作业计划应同订单交货期偶合,当这种交货期显著地变动时应通过重新安排计划使交货期保持有效。不幸的是,这一点往往被忽视,其结果是由不准确的数据来驱动车间优先级。可被任何公司用来改善其交货绩效的重要步骤之一是去按作业建立计划日期。在生产控制基本上就是催稽的那些公司里,往往也是直到订单已不能完成其交货日期时才开始去催稽。下一步骤是去检查在本周与下周应交货与已过期的工作,以确定什么问题正在造成延误。图10-8所示为这种生产日程计划检查表。倘若配合订货计划与作业计划一道使用,这种表可以成为一种非常有用的报告,以确保没有┌─┬───┬──┬──┬───┬──────┬──────┬─────────┐│客│销售││││最近的批│下一批│││││过期│本周│下周├──┬───┼──┬───┤备注││户│订单││││地点│数量│地点│数量││├─┼───┼──┼──┼───┼──┼───┼──┼───┼─────────┤│甲│17624│577│││D-32│1150│---│---│下周将发货│├─┼───┼──┼──┼───┼──┼───┼──┼───┼─────────┤│乙│11318│││40│D-40│94│---│---│在挽救(?)│├─┼───┼──┼──┼───┼──┼───┼──┼───┼─────────┤│丙│10628││1100││D-29│1000│---│N.A.│CallComplet│├─┼───┼──┼──┼───┼──┼───┼──┼───┼─────────┤238第238页共238页n│丁│10959││1780│2500│D-32│5200│---│---│平衡6040存货│├─┼───┼──┼──┼───┼──┼───┼──┼───┼─────────┤│戊│11003││7000││D-22│7500│---│---│O.K.│├─┼───┼──┼──┼───┼──┼───┼──┼───┼─────────┤│己│11004│││20,000│D-22│10,750│D-2│10,750│将发货10M平衡3126│├─┼───┼──┼──┼───┼──┼───┼──┼───┼─────────┤│甲│11008│││7000│D-40│8240│---│---│O.K.│└─┴───┴──┴──┴───┴──┴───┴──┴───┴─────────┘图10-8生产日程计划检查表──27周发生疏忽,也可以作为让销售部门及时掌握情况的手段。该生产日程计划查表可发给销售部门中有关人员使他们知道哪些工作工作将按时发货而哪些有问题,从而提供他们一种手段去提前通知客户倘若一件工作将不能原先承诺过的日期发货──这在客户服务中是一重要因素。无论如何,有必要对潜在的麻烦提出早期警告信号,而这些可由作业计划来提供。┌───────────────────┐│1、提供数据││A.作业顺序││B.设计或估计的标准││C.车间日历││2、提出安排日程计划的规则││A.块日程计划││B.细日程计划││3、选择安排日程计划的方法││A.向后安排法││B.向前安排法││4、日程计划││5、必要时的修订│└───────────────────┘图10-9制订作业计划的步骤图10-9列出了制订作业计划的步骤。第一步当然是提供作计划所需的数据,它必须包括作业顺序或工艺络线。图10-10是一展开的制造订单,它包括作业顺序并说明所需调整小时与运行时间。在此工厂订单上,本批运行小时数已计算出来,即把订单上的数量(表达为千件)乘以”运行小时/千件“这一栏的数字。这一制造订单在设计上是要伴随工作经过该厂的,以便每一作业者能直接地注意到订单上的时间与数量。工艺路线通常保管在计算机文档中。当需要生成一份订单,就打印出该制造订单,并且伴随着有一张穿孔卡,工人可用它来报告工作完成的情况。┌─────┬────┬─────────┬────┬───────┬─────────┐│零件名│图纸号│用在│日期│订单│数量││小齿轮轴│E-17352│机架装配件E-0014│21周│2950│5000│├─────┴────┴──────┬──┴────┴───────┴─────────┤238第238页共238页n│材料│备注││钢棒-0.500"│││特种#A-407│注意是左手螺纹│├──┬──┬─┬─────────┼──┬───┬───┬──┬──┬──┬──┬──┤│││作││调整│运行小│本批运│操作│完成│报废│利废│检查││部门│机组│业│作业描述│小时│时/││││││││││号││数│1000件│行小时│工号│数量│数量│数量│者号│├──┼──┼─┼─────────┼──┼───┼───┼──┼──┼──┼──┼──┤│#040│卡车│10│从存货提取钢棒│─│─│─│││││││#517│#14│20│在旋床上做小齿轮轴│41.5│3.1│15.5│││││││#319│#18│30│按B/P磨槽│1.3│9.5│47.5│││││││#771│#42│40│翻滚│─│─│2.0│││││││#624│#06│50│钻孔│0.2│4.0│20.0│││││││#771│#40│60│去油│─│─│0.5│││││││#771│#43│70│电镀─暗锌│─│─│4.7│││││││#009│#04│80│检查│─│─│AQC403│││││││#040│卡车│90│送存│─│─│─││││││└──┴──┴─┴─────────┴──┴───┴───┴──┴──┴──┴──┴──┘图10-10典型的制造订单对任何安排日程计划的系统,调整与运行的时间标准,或被设计出来或被估计出来,是不可缺少的。因为总是有新物品要在充分地设计出来的标准被开发出来之前就必须安排进生产,所以必须提供某种估计这些标准的办法。准确性不是极其重要的,重要的是这些标准在估计中的一致性。当然并无必要去安排所有工艺路线上的每作业。在同一或相似机器上的成组作业可当作一个作业来处理。次要作业(从存货提取,切断,称重,去毛刺,分类,加工中的检查等等)可并进主要作业或为所有这类作业留出一个标准时间余量。图10-11所示为一车间日历,它是许多公司用来方便日程安排自动化的类型。六月七月周日一二三四五六周日一二三四五六#┌──┬──┬──┬──┬──┬──┬──┐#┌──┬──┬──┬──┬──┬──┬──┐│五月│25│26│27│28│29│30││六月│││七月││││22│24│347│348│349│350│││││29│30│1│2│3│4│├──┼──┼──┼──┼──┼──┼──┤27│28│371│372│373│374│││││六月││││││├──┼──┼──┼──┼──┼──┼──┤│31│1│2│3│4│5│6│││││││││23││351│352│353│354│355│││5│6│7│8│9│10│11│├──┼──┼──┼──┼──┼──┼──┤28││375│376│377│378│379│││7│8│9│10│11│12│13│├──┼──┼──┼──┼──┼──┼──┤24││356│357│358│359│360││*│12│13│14│15│16│17│18│├──┼──┼──┼──┼──┼──┼──┤29│││││││││14│15│16│17│18│19│20│├──┼──┼──┼──┼──┼──┼──┤238第238页共238页n25││361│362│363│364│365││*│19│20│21│22│23│24│25│├──┼──┼──┼──┼──┼──┼──┤30│││││││││21│22│23│24│25│26│27│└──┴──┴──┴──┴──┴──┴──┘26││366│367│368│369│370││*假期周可以更改└──┴──┴──┴──┴──┴──┴──┘八月周日一二三四五六#┌──┬──┬──┬──┬──┬──┬──┐│七月│27│28│29│30│31│八月│31│26│380│381│382│383│384│1│├──┼──┼──┼──┼──┼──┼──┤│2│3│4│5│6│7│8│32││385│386│387│388│389││├──┼──┼──┼──┼──┼──┼──┤│9│10│11│12│13│14│15│33││390│391│392│393│394││├──┼──┼──┼──┼──┼──┼──┤│16│17│18│19│20│21│22│34││395│396│397│398│399││└──┴──┴──┴──┴──┴──┴──┘图10-11车间日历每一工作日被依次地编号──在一1000天日历中包括4年的期间。它使安排日程计划的程序便于直接地建立日期而无需作周末、工厂停工期或假日的校正,因为在日历中它们已经被删去了。图10-12所示为一些简单的安排日程计划的规则。它们比起大多数公司中┌──────────────────────────┐│1、将每千件的小时数乘以订货的千件数,加上调整时间。││2、把时间转换成天数;每天开2班,每天以16小时计,││四舍五入;若超过的小时数少于总量的10%则舍去;││1天是作业的最小值。││3、留出2天从存货室提货。││4、在同一部门中相继的作业之间留出1天。││5、在不同部门中相继的作业之间留出2天。││6、留出1天作检查。││7、留出1天给移动物料入存货室与作记录。│└──────────────────────────┘图10-12简单的安排日程计划的规则所需的规则来显得过于简单,但说明在开始作日程计划之前必须开发出的规则的类型。意图是提供计算与估计提前期中每一要素的手段(见第9章)。原理50.安排日程计划的规则必须为提前期的所有要素留出余地。替代图10-12中所示的明细安排日程计划规则的办法是使用一般规则,诸238第238页共238页n如图10-13中所示的块日程计划规则。它使用大块时间去粗略地估计出每一作业所需的时间,块日程计划节省计算时间但通常其结果是提前期极长。┌──────────────────────────┐│1、留出1周用来发放订单与从存货室提取物料。││2、留出4周用于自动车床作业。││3、为磨削部门中每400件留出1天;向上取整数到下一││整周。││4、对钻孔、攻螺纹、打毛刺与使用次要设备的作业留出1││天。││5、对特短的作业在同周内合并之。││6、为完工件的检查与送交存货室留出1周。│└──────────────────────────┘图10-13块日程计划规则下一步是从两种主要的日程计划安排方法中选择一种:1、向后安排法(Backwardscheduling)用来为父物品订单能开工前就需要的组件安排日程计划。它从该项订货需在存货室、在装配现场或要被发货的日期开始,向后经过工艺路线去确定该订单的恰当发放日期。这种方法假定完工日期为已知而必须计算出制造顺序中每一步骤的开工日期。2、向前安排法(Forwardschedulint)应用在安排一系列订单经过一个主要加工步骤或机器的时候。它从当天开始或从该设备第一次开工时开始并为每一后继的订单计算与安排日程以确定其完工日期。向前安排法最常用于诸如钢厂等公司,那里的任务是按客户订单制造的而且通常要求很快交货。使用此法的工厂的特征之一是该产品通常不是需要许多组件的装配件。即使采用向前安排法时,计划者也必须在安排日程之前核对客户所要求的日期。倘若所要求的日期足够远,该订单并不立即作安排。所以实际上,计划者是把向后安排法同向前安排法结合起来的。向后安排法典型地使用在供装配产品用的组件的制造中。各组件通常有长短不同的提前期,有的比其它的要短得多。在确定了主要子装配件的要求开工日期之后,计划者使用这一日期向后推算以确定每一组件制造订单的恰当发放日期。倘若计划者使用向前安排法,则所有订单将在同一时间发放,因而有许多组件将在真正需要它们之前过早地入库。比这更重要的是,紧急订单的零件将同实际并不急需的订单在工厂里为同一生产设施而竞争。图10-14所示为图10-10中制造订单的两种日程计划技法。二者都采用向后安排法(从#51周或#445天向后倒推)。块日程计划按图10-13中列出的规则安排,计划完成日期用周号表示。此法的结果是总提前期为12周。作业号│块日程计划法│作业时间日程计划法─────┼───────┬───┼───────┬────│允许时间│周│允许时间│天├───────┴───┼───────┼────│发放日期=#39││420238第238页共238页n├───────┬───┼───────┼─────10│1周│#40│2天│42220│4周│#44│2天│424│││T*=2天│30│3周│#47│3天│429│││T=2天│40│1周│#48│1天│432│││T=2天│50│1周│#49│2天│436│││T=2天│60├┐││1天│439│├1周│#50│T=1天│70├┘││1天│441│││T=2天│80├┐││1天│444│├1周│#51││90├┘││1天│445─────┼───────┼───┼───────┼─────需求日期=││#51││#445天*T=过渡时间图10-14日程计划技法的比较作业时间日程计划法从表达为天号的要求日期开始使用车间日历的天号缶后倒推去计算每一作业的要求完工日期。这一计划需要25个工作日或5周去完成。在图10-14中,调整时间已考虑在内。例如在作业20中由于自动车床要有调整时间已额外加了一个工作日。注意,在计算中所留的过渡时间比正常地去移动物料所需的时间要多。在比例中过渡时间其实是一个宽的术语,它包括下列要素:1、工作等待从该部门移出所化的时间──等待时间2、工作实际在旅程中的时间──移动时间3、工作在下一台机器中心等待加工开始所化时间──排队时间。很少有公司使用精确估计的等待与移动时间;大多依赖简单的估计。在提出严格的日程计划时真正的问题是每一工作中心标准排队时间的确定。这有三种做法:1、作出注重实效的估计2、使用负荷的近期历史3、计算未来的负荷使用工作抽样法作随机观察是实际地估计工作中心平均排队长度的简单而有效的方法。选择负荷的某种易通过目视观察来确定的度量(件数、订单数、工作的箱数等并对工作中心每次观察到的实际负荷作下记录。经过对散布在具有正常作业代表性的一个期间上足够次数(10到15次)的观察,每一工作中心的平均排队长度被确定并把它用在日程计划规则中。基本相似但更精确的办法是为一有代表性的期间作一套实际负荷的记录。所用数据为取自真正工作中心的订单上的标准小时数。将这一期间的平均值计算出来作为标准排队长度。然后作定期的重新计算去发现显著的变化。用较短的排队长度去取代原先的标准;对较长的排队长度则采取削减投入或增加产出等校正行动去缩短238第238页共238页n它们。强有力的计算引诱许多熟悉技术但缺乏在工厂里应用它们的实际经验的、本意善良的人们试图计算未来的负荷并使用这些来提出严格、精确的日程计划。这是企图准确地去仿真订单将如何被处理的情形。它是可能的但并不值得如此去做。它假定能够在计算机中建立一个工厂的模型并从模型计算出订单流。更为有效而且省事的办法是去建立估计的标准排队长度,度量实际排队长度并把它们同标准作比较,偏差显著时则采取校正行动。运行良好的工厂不断争取更低的在制品水平与更短的提前期。这一主题,其中包括由于计划排队时间不断增长而引起的恶性循环与由此生成的提前期综合症详见第二册第5章。作业时间日程计划法比块日程计划法更为复杂而且需要多得多的数据与计算。但由块日程计划法确定的提前期比作业时间日程计划法所确定的要长得多(图10-14的例子要长7周)。作业时间日程计划法的另一好处是它为机器负荷报告提供输入数据。详见本章下一节,还有当能力约束干扰以所希望的顺序来运行订单时需作什么修改的问题也在那里讨论。只对少数订单作样本日程计划计算就可看出在任一工作中心恰当的工作顺序往往不同于各订单应完工日期的顺序。因此,作业日程计划为确定在个别工作中心的工作的优先级提供更好的依据。通常公认为日期不应表示在车间订单上,因为1、当日程计划需重新安排时,日期不可能更改2、从这些日期可能得出关于真正的优先级的错误结论3、过期看起来好像存在有灾难,而其实不一定如此4、工厂人员实际上只需知道做哪份订单的恰当顺序日程计划的有效性可通过运行要求短时调整的小而均匀的批量、通过在重要工作中心加小的负荷与通过让许多订单追随一共同的加工顺序而得到大的改善。详见第二册。ABC概念适用于安排日程计划如同适用于生产与库存控制的许多其它领域一样。倘若把经过任何一个工作中心的订单按他们生成的工作小时数区分为A.B或C三类,虽然有许多订单而且总的产品组合级为多变,但80-20的关系总是显然的。经过该中心的很少数物品生成所需要的工作小时数的大部份。只要控制了这些物品的投入就可有效地平整生产速率、减少在制品从而缩短提前期。大多数纯订货生产工厂有对某些常规计划中物品提出重复订货的客户,这些物品可作为吸收一产品组续入业务中升降波动的缓冲。当总订货量降到低于期望速率时,这些常规计划物品可以略高于正常的速率来运行以补偿生产水平的损失。这一方法要求足智多谋与工作,但它减少所需的积压量而且在缩短提前期更好的客户服务方面能带来非常可观的回报。使用已计划物品作库存缓冲或使用一减量的积压时要记住的重要之点是去设定某种控制。这类方法曾在早些时候在一订货生产工厂里试验过,但用作缓冲的已计划物品的库存完全失去了控制或积压并未被恰当地控制的情况并不少见。倘若事先建立起决策规则而且在这些规则的基础上恰当地采取行动或减或增生产水平,这些技法可被使用得很成功。像所有的预测一样,在一订货生产工厂里计划未来的能力时必须明确认清,没有一种续入订货率会是长久不变的。238第238页共238页n工作中心加负荷的方法图10-15所示为工作中心加负荷的步骤。第一步是选择负荷中心。有的公司只把负荷分配到部门为止。倘若一部门中所有机器都可互换,这一简化办法可以行得通,但若该部门中不同的机器中心有不同的能力(如同一般的机加工部门中那样),把负荷分到部门实际上解决不了多少问题。独立的加工单元、装配线与包装线当然必须个别地来安排日程计划。下一个改进是把设备细分为相似的机群,例如┌───────────────────────┐│1、选择负荷中心││2、选择负荷期间││3、选择加负荷的方法││无限法││.安排工作订单的日程计划││.以任何顺序给工作中心加负荷││.更新,去掉已完成的工作,加上数的订单││有限法││.安排工作订单的日程计划││.在订单上设定优先级││.设定工作中心的能力限度││.这定义各种方案││.按优先顺序给工作中心加负荷││.选择方案││.重新安排过负荷││.更新时,重头开始│└───────────────────────┘图10-15加负荷的步骤所有的24"镗床可包括在同一群中,如果在这些机器之间可以互换的话。如果有一台自动车床在其它方面与机群中其它机床完全相同,但不同点是它具有一侧磨刀架,有的活只有它能够做,就因为它建立个别的机器代码。因此一个机群可能算示为群2400而其中包括有一台特殊的机器则标为2407。在任何一台机器上都可以做的工作将标示为机器2407的负荷。尽可能多地把机器或工作中心归入一群是重要的,因为这将减少所需的工作,生成一较小的报告并倾向去稳定该负荷。在可互换性很大的情况下个别地去给机器加负荷是不好的办法并将造成很不稳定的负荷。第二步是选择负荷期间;通常每周一次,因为以更短的间隔去加负荷是难得有用的。负荷期间不能短于安排日程计划是时所使用的期间。再下步是选择实际的加负荷方法。在上一节,曾提到一个例子,20小时的钻孔加工时间将被加到该周的机器负荷,在该周中计划要完成这些钻孔时间以满足该完工产品的日程计划。这种加负荷方法叫做无限法,意思是按无限能力加负荷;该负荷被表示在它被安排的那一周内,并不考虑在该周已经存在的现有负荷。倘若该部门加负荷以不超过其现有能力为限,就叫有限的加负荷法或按有限能力加负荷,这时日程计划不能在一次连续的计算中被完成,其加负荷的步骤如图10-15所238第238页共238页n示也是大不相同的。在采用无限的加负荷法之间,订单按作业安排日程计划,根据的假设是总会找到办法来完成计划的。这类订单可不考虑其优先级以任何方便的顺序来加负荷。如果该作业能被完成并被安排在一个负荷期间里,它就被表示在该间隔中。倘若该日程计划超过一个负荷期间,则需有某些加贡荷的规则。这可以是1、把所有负荷安排在第一个被计划的期间2、把所有负荷安排在最末一个被计划的期间3、均匀地把负荷分配在所有期间上,与被计划的天数成比例或按照某种其它基础。例如在图10-14中,作业30从第425到第429天共伸展5天,其中包括2天等待、移动与排队时间与3天的加工时间。如果第425天落在第49周的星期四而第429天落在第50周的星期三,该负荷(调整加上运行时间的标准小时数)可1、全部安排在第49周2、全部安排在第50周3、每周各安排一半或2/5在49周而3/5在50周。工作中心的负荷可以只为已发放订单开发或为已发放与已计划订单二者开发。已发放订单在工作已经(或即将)开始的意义上表示“实际负荷”。然而它仍然只是一项计划,而且负荷中只有一小部份订单交在任何时间在某一工作中心里,有些订单将不会按计划到达中心。为了优先级的最佳控制──工作中心负荷的主要用途──这种真正的负荷应同计划中的负荷有所区别。当然,用作能力需求计划基础的负荷数据不需这种区别,它必须包括已发放与已计划订单这二者。作为对第9章的补充,第二册有大量篇幅讨论工作中心加负荷法在能力需求计划时的应用以及这些技法之间的区别。还必须考虑去负荷(unloadign)技法的选择。当使用人工系统时,有必要取捷径,譬如当第一张时间卡转入时就把工作当作已经完成来考虑。这避免了许多生产批的过帐与重新计算负荷余额,但其结果是使负荷常常被少记了已从系统被卸下的每一工作上剩余的小时数。另一捷径是使用一批的最后一张时间卡去解除负荷。其结果则是一总是被夸大了的负荷,即多记了每一工作上已经完成但尚未去掉的小时数。有了计算机与数据收集设备,可以随着小时数的被完成就去扣除它们,并揭示负荷中剩下的真实小时数。只有当这些附加的工作与昂贵的设备能带来实在可见的利益时,才应当这样去做。有时被人们忽视的一点是任何一项工作要解除负荷的小时数必须等于当初曾为该项工作而加上的负荷小时数。工作中心的负荷总是使用标准小时数。例如,一项工作的标准小时数已设定为12小时,但该项工作实际上用9小时就完成了。要正确地陈述负荷中剩下的工作,必须从负荷扣除12小时。做法是把报告的已完工件数乘以标准小时数而不是从负荷扣除实际用掉的时间。如图10-15所示,有限的加负荷法比无限的加负荷法要复杂得多。由于必须考虑能力限度,订单必须以恰当的优先级顺序去加负荷使得高优先级的订单对可用能力有首先要求的权利。有了能力约束的定义,就有可能去识别可接受的方案,诸如加点(在某种预先定义的限度内)。选用经过核准的替代作业、在某各允许范围内降低订货量,等等。在有限技法中提出负荷是时,过负荷是不允许的。会引起过负荷的订单因而必须重新安排到具有可用能力的期间中去,或者238第238页共238页n1、如果物料、工具等供得上,就提早些2、晚一些,安排在能力足够的期间更新有限法负荷通常要求重新从头来一遍,因为个别订单的优先级将已改变了。与它对比起来,无限的加负荷法的维护非常简单。只要不断加进新订单并删去已完工的订单。图9-11所示为一典型的工作中心负荷。如第9章中所述,从这种数据很容易得出完全错误的结论。详见第二册第5章。这里介绍此图的一些特色:1、“脱期”的意思就是未能按计划的进度完成。实际上成不成问题取决于负荷如何落入每周的期间,日程计划中还剩下多少排队时间以及下游工作中心中的负荷条件。2、不久将来的负荷包括计划排队长度,它们是不打算去完成的。3、除非有意地去理顺它,否则由于批量化与两份或多份订单碰巧在同一期间到达,工作并不平稳地流动。4、该负荷表示有多少工作被计划要在工作中心里,不是表示它将到达与应被完成的速率。流行的参考书把像图9-11那样的图示当作一份能力需求计划,已经引起了很大的混乱。它不是的。在第9章已讲过它们之间的区别。在做过两项重要的调整之后,它可用来开发能力需求计划:1、必须扣除标准排队小时数。该计划并不打算要在任一封闭的时间期间去完成这些小时数。2、必须加上计划外对能力的需求。这些包括报废品的补充、返工与许多其它因素(见第二册第5章)。用浴盆来作比喻可清楚地说明负荷与能力的不同:负荷好比盆中的水深;能力则是水进出浴盆的速率。工作中心加负荷是一种良好的技法,它用来表明如果按现行的优先级来加工订单则何处将产生短期的过负荷或欠负荷。原理51.加负荷(Loading)是一种优先级控制技法,只有当数据符合实际时它才有用。对于长期的能力计划,加负荷并不是一种成功的手段。因为只有少数公司具有足够的不变订单可据以去计划能力而要求稳定劳力的压力已变得非常强烈,所以差不多在每一公司里都有必要根据对预期需求的仿真来制订某种形式的生产或能力计划。当应用安排日程计划与加负荷等技法时,只有充分理解控制个别订单流的问题、目的与必须注意的原则,这些技法才是有效的。往往是随机地由一库存控制系统来生成订单,日程计划被下达到车间,而且在一份机器负荷报告中度量订单的积压,但并未作出任何努力去控制这些订单流进车间的速率,也未认识到事实上在这些订单被完成之前要求的日期是可以更改的。这一在订单已被发放之后发生的需求变化应如何去响应的问题将在后面的两章里讨论。对供应商的投入控制不制造任何东西的分销商给他们的供应商生成订单的投入。大多数制造公司从外界供应商采购他们的大部份组件。在许多里物料控制与采购功能之间的关系由于从这些供应商获得正确的物品中所涉及的问题而永远是紧张的。这些问题中一些最显著的是:238第238页共238页n1、数量折扣:采购通常是以价格差异来度量的,而当采购者能利用数量折扣或大宗购买时它的绩效会显得好些。如果物料控制系统在订购外购物料时不承认数量折扣,采购者往往在交给他们的申购单上增加数量而晕样当然会增大库存。这些数量折扣在物料控制系统中可按第8章所述的办法来处理。应当考虑对成本与库存的总体效果,建立起关于什么条件构成可以接受折扣的政策。这些订货规则应该然后被建立进该物料控制系统中去。2、发出订单时采购人的迟延:一个好的采购部门集中其许多精力在采购上──价格的实际磋商与发出订单。这是一极端重要的功能因为──在大多数公司里──采购物料的成本比值直接按劳务成本要大许多。然而,对计划者而言,当一种缺件影响了一份客户订单的交货而其原因是交给采购者的申购单由于采购者要议到更好的价格而延误时,降低成本这个目的的显得有点短视。这个问题无法取消但可以处理得更好些,如果a.使用较少数供应商与较长期的合同b.何采购者提供标准组年预期的年需求量,在有计划的基础上进行议价而不是当收到申购单时再去议价。c.使用分时段订货点法与MRP技法的预见性使采购者在需将订单放给供应商的老早以前就收到申购单。3、外购组件的提前期长:时常听到采购者告诉一供应商:“只要你满足你的交货承诺,我们不在乎你的长提前期。”不幸的是,在供应商方面较长的提前期将削弱它满足交货承诺的能力同时将给客户对其需求的知识增加上更多的不确定性。一项教育采购人员去懂得计划与控制中一些基本关系的计划会产生许多可见的效益与较短的提前期。4、缺乏跟踪:外购物品交货迟延是在物料控制人员与采购人员之间引起摩擦的主要原因。改善对供应商产出的控制的技法见第11章。然而,改善对其投入的控制往往比仅仅集中于更好地控制其产出对克服供应商不良的交货──诸如老是不能按时交货──更为有效。去改善一家供应商的产出,特别是其总产量中有大部份供给一家客户时,可采取的最重要步骤是去计划其生产速率,然后每周给它一适量的工作。许多采购者对这一主意有反感,他们把它同安排供应商的工厂日程计划联系起来,那是他们不想承担的任务。与他们相似,许多物料控制人员感到如果他们生成订单而且表明何处有过负荷,那末使工作及时完成则是车间的责任。供应商实际上是在运行一种制造设施,它可以被认为是客户的工厂里的另一个工作中心,使用本书所述的某某些技法去帮助计划生产水平并控制投入以完成此计划将大大改善供应商的绩效。这远非一种利他的姿态,这种方法将导致更短、更可靠的采购件的交货。它是走向适时(JIT)交货的正当途径。原理52.为;了及时的交货,对待供应商完全像对待厂内的工作中心一个样。装配作业的日程计划安排在许多工厂里装配时间是短促的,装配工人是非常灵活的而装配日程计划是直截了当的。装配部门往往可分解为几条流水线,它们可按有限能力来加负荷。在其它具有复杂装配作业的公司里,诸如制造精巧电子设备的公司里,装配作业的详细238第238页共238页n日程计划确实能够成为很重要的事。在这种场合,安排日程计划与加负荷的工作往往变得同安排组件制造作业的日程计划同样地详细,而且装配日程计划最好能使用本章前面所讲的技法逐个作业地来安排。在重复性制造业中,例如汽车、家用器具与办公设备工厂中,那里存在明显的装配流水线,有必要去平衡流水线上工作负荷使得当产品顺流而下时每名工人有一合理的工作量去做。虽然流水线的平衡工作确定每一工作给将完成哪些工作的意义讲通常由工业工程师来做,计划人员却必须将工作源源不断地供给该平衡后的流水线。生产线平衡法的基本步骤是:1、在所有要被装配的产品的一切作业上建立时间标准,作业的要素取得尽可能地小。2、按装配线分区确定每一分区中必须完成哪些作业,而哪些作业如果希望的放可在哪里完成。3、假设所有产品都要运行,从流水线的完工产品一端开始往回倒退使工作与工作之间获得取佳平衡。通常用试错法求最佳平衡,若有计算机可用来仿真所有存在着的可能性则最为有效。4、构成在生产组合方面将具有最大灵活并能最好地利用可用人力的生产日程计划。没有一种安排日程计划的技法能够从缺少组件的装配线产生成果,而在许多工厂里(特别是要靠许多功能部门供应的装配部门里),看来总是存在着经常性的零件短缺。这是任何制造控制系统中相互作用的极好例子而且它清楚地说明需要有一个真正用来控制的有纪律的系统。太经常,系统由于缺乏良好的、基本的纪律而产生问题而企图采用“快而脏”的解决办法只会使问题复杂化。许多公司曾经历过这样的循环:1、由于库存记录不准确,在装配时发生零件短缺(系统显示说可得的零件实际上却没有)。2、这在装配线中引起严重的混乱,因而有人建议进一步提早把装配要用的成套零件拨出或筹划好。如果办事手续本来是要比装配日程计划提早一个星期去建立这些成套零件,那末该建议往往要把它提早到4或6个星期。理由是这样将会有更多的时间好通过催稽零件的制造以弥补配套的发现的缺口。3、进一步提早筹划组件于是引发这些问题:a.生成额外的4或5周的组件拨出来对付未来的装配日程计划要求组的有相当大的增长,而这通常并非立即办得到。这是相当于从库存记录上注销这样一笔库存,因为这4或5周的组件供应既不再可供新的装配需求去使用,但它又不能成为可用的已装配产品。b.增大这提前的拨出以便及早确定零件的短缺给存储室人员增添了一个有份量的高峰负荷,他们得用比组件实际被装配的速度更快的速度去牵拉所需的组件。c.更加提早的拨出要求更多空间。d.必须开发与维护一份记录拨出中缺料的文档,它指出每一次拨出中有哪些缺件。这一文档工作本身会成为极端麻烦与费时的。e.典型的是,在组件具有多种用途的场合,提早拨出技法的结果是组件被不恰当地分配。为一种装配件拨出但由于缺乏其它组件并不能投入制造的一种组件将被发现恰恰是另一份拨出中唯一缺少的组件。f.从一份拨出把组件转移到另一份拨出是不可避免的,而且增长了拨出期238第238页共238页n间。其结果,记录的准确度更难维护因而通常降低。g.退回多余组件的工作剧增。从存货拉出去制作一给定装配件的每种组件的原来数量是根据希望完成的装配件的批量。当最为短的组件最后到来时──典型地,要少于所希望的数量──它必须分配给若干份装配用拨出,其中至少有一份将不能按所希望的批量来装配。结果是,剩下的其它组件必须退回存货箱。设计更改也有同样影响。h.使用提早拨出技法时,按缺件控制在装配部门中运行各装配件的顺序的权力留给了一线人员。在零件极端短缺的期间,任何一个有组件可用的产品都会被装配部门抓去运行。由于用掉了稀缺的可互换组件,这又加重了短缺。成套组件集结待用(StahingComponents)这个“快而脏”的办法通常引发的问题比它解决的更多,而且其结果是对供应量有限的可用组件更差的利用与对库存记录准确性的进一步破坏,而记录不准又是配套待装(Kitting)的初始原因。往往,不准确的库存记录只是系统中引起装配成问题许多不足之一。组件短缺也可能是由于不好的重订货办法或优先级控制中纪律不好。短缺也可能是由于不良的能力计划所千百万的组件生产量过低的结果。为支持装配作业而对组件流有良好的控制要求:1、准确的库存记录,由定期的循环盘点而非一年一度的实物盘点来核对,依靠对进入该系统的一切人员进行教育来支持,使他们懂得处理每一笔账务的正当技法并理解遵循正当手续的重要性。详见第二册第1章与附录Ⅰ。2、以期望的装配日程计划上的组件需求──而不是已往的平均使用量──为依据的重订货系统,它通过改变表示在物料计划中的需求量来对这些装配需求中的变化作出反应。3、在装配部门的生产速率发生所希望的更改之前提早去计划组件生产速率的手段。4、配合着实际能力的平滑的工作投入。对大多数工厂,安排组件制造、组件采购与装配的日程计划是投入控制中的重要要素。本章所述的技法可由人工、图示或在计算机上实施。还有一些特殊的制造情况与为此而开发的特殊技法。下面几节叙述一种常用的图示法与必种项目日程计划方法。HenryL.Gannt1917年在弗兰克福兵工厂所开发的甘特图是生产控制者熟知的最老的计划工具之一。有许多商用工具可用,它们实际上是机械化的甘特图。其中有的使用纸条去表示已加到某一部门的负荷工作量,然后用颜色信号结合这些纸条以揭示哪里已发生了关键的过负荷。其它机械化工具有附有钉、线的穿孔板,可借以做成一幅甘特图,表示项目计划或机器负荷或工作中心积压订货。机械化甘特图有助于以礼觉方式表示信息。它们本身并非一制造控制系统。只有当用来生成所表示的信息的系统是正确合理的,项目中的要素较少,而且变化不大时才会是成功的。这些技法在记录、复制与传递它们的消息时有一些问题。纸上的甘特图易于复制并递交到需要该信息的所有人员,机械化甘特图只能用照相来复制,或人工地把信息汇总到纸上或把人们带到图前来看图。这些机械化甘特图在今日的计划与控制中用处已经不大。它们已被计算机图象所排挤,后者便于复制与传递并能处理大数目的项目要素。238第238页共238页n线性规划与排队论线性规划是给予通过一有系统的迭代程序去解联立线性方程的一系列技法的名称。不多年以前,经过广泛的宣传,线性规划恐怕已成为使用在制造业中的最广为人知的与最独特的一种运筹学技法。线性规划可应用于具有下列一般特征的问题:1、有可定义的目标(诸如利润、成本与在一定时间期内最大的生产量)2、有许多可用的替代解。例如,可以不同成本在一个生产单元上运行或在另一生产单元上运行的一项工作;或可以不同制造成本与运输成本从不同制造厂获得补充的仓库补货订货。3、资源是有限的。例如,成本最低的设施其能力不足以制造全部所需产品,因而必须使用获得较少的单元。4、重要的成本与绩效变量之间的关系可用线性(一次)代数方程表达。线性规划曾被应用于若干生产问题,主要是在过程工厂安排精炼厂、化学品、油漆与玻璃厂、最近还有柔性机器中心的日程计划。目前这种技法实际上在制造厂里用途有限。更简单与更有效的技法使得这些复杂的数学方法成为不必要的。对等待线或排队的情况也作过类似的分析,而且已经开发出了排队理论。一服务设施(工作中心、机器、存储室结帐员、银行营业员、等等)对来者(人、制造订单)执行某种工作,来者具有某各到达的模式,这种模式希望能被某种方便的统计分布(如泊桑分布、正态分布或指数分布)来描述。该技法预测对假设的到达者能被服务的速率,预测排队的长短与可变度。如同线性规划甚至MRP技法一样,排队论描述将发生什么如果环境像它所描述的那样。更多内容见本书第12章与第二册第9章。实际的考虑典型的工厂环境如图10-18所示,它指出控制投入与产出二者具有令人信服的必要。对于实际工作者,下面是控制投入时一些实用的考虑:1、当一完工产品正在被装配时,重要的是不到最后一刻要避免把组件承诺给某一特定产品。使用MRP去重新安排外购或自制组件以及处理车间中重新安排日程计划的技法见第6章与第11章。2、制作组件的设施可像装配设施一样地被有效地安排日程计划。有人正在决定──实际上是在逐日的基础上──哪些物品应该开工。在两种情况下,都就避免对长期的日程计划作不变的承诺。3、对工厂的投入进行控制是必不可少的。这种控制可以复杂到犹如为了获得对所有组件完全的控制而把组件控制在作业之间的一个中央存储室,只按照计划者的指导去发放它们。然而,功能性工作中心(诸如电镀或涂漆)往往要加工许多咱组件,详细地去控制投入到这些中心的所有物品是不可能的。相当可行的则是使用ABC分类法去确定在这些二次性中心中生成大部份工作小时的零件,大多数公司将发现它们将是流径这些中心的零件总种数中的一小部份。如果将这一小部份零件仔细地安排好,就可在这些二次性中心中维持平衡的负荷与顺畅的物流。4、同样的方法可应用到构成一特定装配件的各种组件。正常情况是只有少数组件具有长的提前期,而大多数组件可在短得多的时间内得到。提前期长的组件其需求是难以预料的;可能值得去保有一些库存以便用最小的投资去获取灵活性,提238第238页共238页n前期短的组件可以控制得更紧一些。5、如果物品成系列地安排日程计划,用来调整机器制造成本可大大降低。例如,对自动车床而言,在使用同样直日程计划。有人正在决定──实际上是在逐日的基础上──哪些物品应该开工。在两种情况下,都应避免对长期的日程计划作不变的承诺。3、对工厂的投入进行控制是必不可少的。这种控制可以复杂到犹如为了获得对所有组完全的控制而组件控制在作业之间的一个中央存储室,只按照计划者的指导去发放它们,然而,功能性工作中心(诸如电镀或涂漆)往往要加工许多种组件,详细地去控制投入到这些中心的所有物品是不可能的。相当可行的则是使用ABC分类法去确定在这些二次性中心中生成大部份工作小时的零件,大多数公司将发现它们将是流么这些中心的零件总种数中的一小部份。如果将这一小部份零件仔细地安排好,就可在这二次性中心中维持平衡的负荷与顺畅的物流。4、同样的方法可应用到构成一特定装配件的各种组件。正常情况是只有少数组件具有长的提前期,而大多数组件可在短得多的时间内得到。提前期长的组件其需求是难以预料的;可能值得去保有一些库存以便用最小的投资去获取灵活性。提前期短的组件可以控制得更紧一些。5、如果物品成系列地安排日程计划,用来调整机器的制造成本可大大降低。例如,对自动车床而言,在使用同样直径的原料的同一系旬的物品之间只需作简单的调整。计划者检查一个系列中的所有的产品,当其中任何一咱要订货时就把所有产品都订货,可以实现相当大的节约。使用等3章中“主要调整与次要调整”一节中讨论过的技法去为系列中每一种物品去计算其经济批量也有助于比。6、在季节性待业中确定恰当的车间投入量是仍为困难的。在库存逐步增长的期间运行什么样的物品组合是比较不重要的,因为有余量可以满足意料之外的需求。随着高峰销售季节的到来,应该使用实际需求去指示最佳产品组合应该是怎样的。典型情况是高峰季节所需调整时间与灵活性比淡季要多。许多公司对此的处理办法是让熟练的人员在淡季兼任调整工与操作工,到旺季则用较不熟练的人员担任操作工而让熟练工人只做调整工。有许多种安排日程计划与加负荷的技法。新手的标志是只学了少数几种就试图把它们到处应用。这个问题的部份原因是有的文献讨论特定技法时不及其它,也不给出应用的判据。更坏的是被广告吹嘘为万应灵丹的专卖计划,关于技法如何掌握却无足够的陈述。这种“魔法”应予避免。选择安排日程计划与加负荷技法的判据围绕可用的与所希望的提前的长短(及其后果订单积压)与工厂的安排日程计划法与无限能力加负荷法是适当的,后者为详细的能力计划提供信息。对于项目要素的宽日程计划安排,可用CPM与PERT这类技法去补充常规的详细日程计划安排与加负荷法。2、短提前期,订货生产产品:如果正常可用的积压量少于作能力更改所需的时间,则采用粗略能力需求计划,以客户订货的预测为基础,同时采用向后安排日程计划法,当MRP重新计划订货时再修订它。无限能力加负荷法只是用于揭示暂时性的过负荷与瓶颈,为了按日程计划去生产必须消除它们。装配日程计划是以实际的客户订单为依据。3、备货生产产品:使用以系产品的预测为依据的粗略能力需求计划去提供所需能力,一切详细日程计划由MPS与MRP驱动,并频繁地被更新。使用本章所述的技法去控制投入以调节在制品水平与控制提前期。238第238页共238页n选择具体的安排日程计划与加负荷的技法时应认识到控制投入从而平整经过工厂的工作流这件事做得越好,厂内的订单积压就越少。反转来,这又意味着更短、更可靠的提前期与更加有效的计划。工厂的制造配置(在上述任何一种服务分类中)可进一步分为几类:1、间歇式生产,产品大多属单件生产,例如模具生产与造船。2、半过程流水生产(Semiprocessflow),有些部门按功能设置(相似设备按部门集中而不是按其使用顺序排成生产线)但许多产品追随相同的通用作业顺序,而且有许多重复性制造。3、过程流水生产(Processflow),诸如汽车装配,化学过程单元或纺织品完工处理,包括染色与成布。对于过程流水生产类型的工厂,对投入的控制决定了对产出的控制,因为每件工作将以与开工时相同的顺序通过所有作业。能力通常可以总产出(每日几辆车,布的码数,等)来加以计划。生产线平衡技法有助于定义计划者去获取劳力的最佳使用时要受的约束。安排作业日程计划没有必要,因为每件工作流径同一作业序列,并无跟踪工作进展的实际需要。负荷报告只具有表示未发放的积压量的意义,因为,一旦进入了加工,工作并不停止多久,使得负荷报告没有意义。在大多数工厂里,有大量的半过程流水作业(即使它存在于某些大类产品之中)。在存在这类流水作业的场合,对流径相似制造顺序的大类产品作预测在计划生产速率时可能非常有用。如本章前面所述,对投入的控制可以改进到使一系列作业负荷平衡的程度。安排作业日程计划提供跟踪工作进展的基础而机器加负荷法揭示何处正在发生短期的瓶颈与过负荷。在名副其实的间歇生产类型的工厂里(大多数工厂人员认为他们的工厂是任务车间),有效的能力计划只能采用粗略方法,但它在制品控制中是不可缺少的。对投入的控制通常不能精确地做到,有时只能在起始作业中做到。在优先级与能力的控制中,机器负荷与投入/产出报告是主要的文件。以上是选择可用技法的粗线条的指导方针。原理53.投入控制得越好,产出就越少需要去控制。大多数工厂倾向于着重产出的控制而忽视了投入的控制。在并非纯过程流水作业的任何工厂里,对工厂的产出作某种控制是必要的。产出控制的原则技法是下一章的主题238第238页共238页n十一.产出控制控制的要素对任何功能的控制要求下列四个要素:1、标准或计划,对照它去度量实际数据,可知该功能何时达标。2、反馈,它报告要同计划去作比较的实际绩效。3、某种容差限度,它便得系统对于最终将被相反的变化所抵销的微小变化不作反应但它将允许系统敏捷地去认出显著变化并要求校正行动。4、具体的校正行动,当该功能失控时可采取它使功能返回到计划,或作为最后的一着,对计划的修正。在产出控制,标准就是第9章讨论过的能力计划而计划日期的开发如第10章中所述。容差限度由管理人员使用对可接受限度的判断再根据经验或管理政策加以修订而确定。反馈包括对计划所包括的同一设施实际绩效的报告而具体校正行动包括雇佣、解雇、加时、转包工作、改变优先级等等。在第1章里讨论过不良的制造控制的某些后果及其对国民经济的影响。在第9章讨论过为了控制订单积压与提前期有控制生产速率的必要与能力计划的技法。在第10章讲话过确定有效的订单开工与完成日期的日程计划安排与加负荷的技法。本章主要研究使用能力计划与日程计划去控制工厂与供应商二者的设施中的生产。原理54.产出控制必须包括能力与优先级二者。控制能力的必要如果把平常公司中生产水平的起伏同需求中的起伏相比较,很快可以看出大多数制造主管人员的倾向是在决定去改变生产水平之前等待得太久而当他们作更改时反应得过了头。这一问题的根子通常在于他们作出决定所根据的信息──或由于缺乏这种信息。制造主管人员根据负荷并根据关于未来的不确定的信息(即预测)来作出这类决定。由于这一不确定性未被度量使得管理人员连平均值也玩不上,他们倾向于在改变生产速率之前让总需求的改变累积成为大的库存过多或短缺。因为在多数公司里没有人已经建立了有多大规模的库存短缺或库存量过多就足以证实一次生产速率的改变,于是该决定就被拖延同时需求中的变化一周复一周地积累起来──逐渐增长为一场真正的灾难,然后才被迫作出决定。在备货生产公司里,库存可能跌到远低于给出良好的客户服务所需水平之下,而在订货生产公司里,报给客户的交货提前期可能被延长,直到丢去了生意,因为这些时间是没有竞争力的。另一方面,如果能力应降低时,则由于该决定被拖延,会使得库存变得越来越高。一个良好的计划与控制系统应着重在必须作出的不愉快的决定、有效的(通常是不愉快的)替代方案以及倘若不作决定将会带来的后果。原理55.有效的能力控制是优先级控制的一个前提。238第238页共238页n投入/产出控制如第10章中所述,计划与控制住到供应商与厂内工作中心去的工作的投入率至少同完成正确的产出率是同样重要的。投入与产出的速率必须保持紧密的联系以便控制外购与自制物品这二者的提前期与在制品水平。这种技法是如图11-1中所示的投入/产出报告。工作中心54是一个二次性中心,它从若干其它设施接收物料。一项理顺工厂里工作流的计划已开始取得控制而且投入的起伏比以前小了。如果这是一个接受物料计划系统所建议发放的订单的首当工作中心,一名计划人员可以比第10章中所述的那样更紧密地配合已计划的投入率。工作中心54(所有数据为标准小时数).投入:┌──┬──┬──┬──┬──┬──┬──┐周号│32│33│34│35│36│37│38│──────┼──┼──┼──┼──┼──┼──┼──┤计划│900│900│900│900│900│900│900│──────┼──┼──┼──┼──┼──┼──┼──┤实际│1033│817│836│992│847│974│811│──────┼──┼──┼──┼──┼──┼──┼──┤累计偏差│133│50│(14)│78│25│99│10│──────┴──┴──┴──┴──┴──┴──┴──┘.产出:──────┬──┬──┬──┬──┬──┬──┬──┐计划│900│900│900│900│1100│1100│1100│──────┼──┼──┼──┼──┼──┼──┼──┤实际│922│895│915│911│1076│1087│1093│──────┼──┼──┼──┼──┼──┼──┼──┤累计偏差│22│17│32│43│19│6│(1)│──────┴──┴──┴──┴──┴──┴──┴──┘.排队:──────┬──┬──┬──┬──┬──┬──┬──┐计划(900)│1800│1800│1800│1800│1600│1400│1200│──────┼──┼──┼──┼──┼──┼──┼──┤实际(1821)│1932│1854│1775│1856│1627│1514│1232│──────┴──┴──┴──┴──┴──┴──┴──┘图11-1投入/产出控制报告按计划从36周开始产出要有显著增长,但工厂达到这较高产量有点困难。注意该计划并未包括在所述期间要提高投入率;供给部门的产出将在以后增加。这将238第238页共238页n使排队长度从目前约2周的水平减少到小于1周的最终计划水平。这本身就是不断降低在制品与提前期过程中的另一步骤。投入与产出二者的计划速率都是从第9章所述的能力需求计划技法推导而得的。实际投入数据通过加总每周到达的订单上的工作含量来确定。在车间现场缺乏数据收集的场合,这可能是文书人员的一项主要差使。当订单被发放在所有运行着投入/产出控制的工作中心中时,订单上的小时数可近似地按照好象订单在被发放的当周就到达了所有中心那样去登录。实际产出事实上每家公司都有度量,当然,投入/产出控制所使用的数据是标准小时数而非实际经历的小时数。不应给报废、返工或显著的超越限度提供赊账。实际排队用工作中心中的订单来表示;虽然通过加上投入并减去产出可得出充动的总量,但定期核查实际订单是对付误差累计的良好保证。在不可能统计实际收货的场合,这一数目可以实际核查排队长度推导出来。投入/产出控制报告是任一制造公司在其计划控制系统中能有的最强有力的工具之一。对于下列它是关键:1、确保有足够的能力去支持计划2、使投入率与产出率保持平衡3、工作排队的控制与提前期的缩短4、提供需采取改变能力的校正行动的早期警告信号5、把优先级与能力计划与控制活动结合起来即使根据粗略能力需求计划、采用估计的工作标准或件数、吨位、加仑等其它能力度量,该报告也是非常有效的。少了它系统就不完整,公司就不能在紧控制下运行。这样一种报告也是要从供应商获得适时交货所不可缺少的技法。更详细地讨论其应用见第二册第5章。为了避免对生意变化作出过度的补偿这种易犯的错误,有必要通过要求生产速率仅仅采取足以在计划期间把库存拉回到计划水平的改变来实施有效的能力计划与控制。图11-2所示为一季节性产品的生产计划,7月份的实际活动已登录其中。这是一个备货生产计划,预算的库存水平(被认为足以给出所希望的客户服务水平)为1400件。┌─────────────┬───────┬───────┐│销售│生产│库存│├──┬──┬───┬───┼───┬───┼──┬────┤│月份│周数│月销量│累计│月产量│累计│本月│备注│├──┼──┼───┼───┼───┼───┼──┼────┤│七月│││││││││计划│2│1000│8600│448│9184│1784│││实际││1120│9400│470│9600│1400│在预算上│├──┼──┼───┼───┼───┼───┼──┼────┤│八月│││││││││计划│5│1500│10,100│1120│10,304│1404│││实际││││││││├──┼──┼───┼───┼───┼───┼──┼────┤│九月│││││││││计划│4│900│11,000│886│1400│1400│││实际││││││││238第238页共238页n└──┴──┴───┴───┴───┴───┴──┴────┘图11-2备货生产厂的生产计划在7月份,虽然累计生产量超过了计划,但销售量超前更多,所以当时的库存1400件是处于基水平。如果要在高峰月份8月保持这一基库存水平,生产必须是1500件而不是以前计划的1120件。这是管理者面临的典型的决策问题;他们只有两种替代方案:1、不采取措施,让库存降低到低于预算水平,同时客户服务也降到计划水平以下。2、对生产速率作相当大的改变,虽然此改变将只持续一段短的期间,因为高峰销售期已过去。包括在内的生产计划。然而重要的是要确定为了达到不持有过多库存的目的究竟必须包括多少稳定化存货。这个问题好比要去确定某一物品必须持有多少后备存货以便减少它缺货的可能性。不幸的是,这些方案所带来的成本并无明确定义也不是垂手可得的。类似的问题也发生在订货生产企业中。图11-3所示为一家出售转塔车床工作机时的小承包商的续入业务。预测的业务量是1000机时/周,但5、6、7这个三月的实际销售量偏离预测相当远。处理这一续入业务的一种办法是每周按上周进来的续入业务量不断地调整本周的生产量去满足每周续入的销售率。当生产量能便宜而容易地改变时(例如,把工人与设备转移到其它产品),这种办法当然可行而且将给出最好的客户服务。不幸的是,大多数工厂里改变产量由于加时、雇佣、训练、丧失生产、非熟练操作工较高的报废率以及许多其它因素要引发沉重的附加成本。┌─────────────┐│预测=1000小时/周│├────┬────────┤│周│续入业务(小时)│├────┼────────┤│5-1│1400││5-8│700││5-15│920││5-22│700││5-29│850││6-5│1060││6-12│425││6-19│850││6-26│1300││7-3│1060││7-24│856││7-31│502│└────┴────────┘图11-3续入业务──转塔车床工作图11-3表明原先预测的每周1000小时现在看来同实际的平均续入业务238第238页共238页n相比是显得高了。如果将第4章中讨论过的加权平均预测技法应用于这组特定数据,可得一正规地每周被更新的预测。图11-4所示为这样一份预测,它根据实际的续入业务作出的,如果生产中相当的改变是可行与可接受的,它就可作为下一周的生产量。┌─────────────────────────┐│新预测=α×续入业务+(1-α)×老预测││使用权因:α=0.2││(1-α)=0.8│├──┬────┬────┬───┬────┬───┤│││0.27││0.8×│││周│续入业务│续入业务│老预测│老预测│新预测│├──┼────┼────┼───┼────┼───┤│5-1│1400│280│1000│800│1080││5-8│700│140│1080│865│1005││5-15│920│185│1005│805│990││5-22│700│140│990│791│931││5-29│850│170│931│745│915││6-5│1060│212│915│731│943││6-12│425│85│943│755│840││6-19│950│190│840│672│862││6-26│1300│260│862│690│950││7-3│1060│212│950│760│972││7-24│856│170│972│448│948││7-31│502│---│948│---│---│└──┴────┴────┴───┴────┴───┘图11-4加权平均预测──续入业务──转塔车床工作将图11-3与图11-4对比,可知使用加权平均预测作为控制生产的手段将使周生产量的高峰从1400小时降到1080小时,而低谷将从425小时上升为840小时。把续入业务水平的起伏全数加到工厂时,周生产量将必须变动约1000小时(从1400高峰到425小时的低谷),而使用加权平均技法把这种变化减少到刚刚起过200小时。当然,这第二种办法要求有一些订单积压(图11-4中未表示出来),因为全部起伏并未都传回到生产。在一家订货生产企业中,订单积压通常用来吸收续入业务中的起伏。前面的例子假设没有订单积压,所有生产在收到订单后的下一周来处理。实际上,大多数公司发现频繁地改变生产速率是不实际的,因为这种改变代价昂贵而且要用相当多时间去完成。倘若要使用订单积压去稳定生产,那末必须回答的问题是,必须保持有多少积压?在第9章中,很粗略地讲过通过观察续入业务从预测的偏离来作出这一决定(图9-12)。更准确的一种方法是去使用第5章中解释过的统计技法去分析续入业务中的变化并确定为保持生产相当地平整所需正常的积压量。图11-5所示为对头5周的续入业务中平均绝对偏差的计算。先算出每同的偏差,然后求出其MAD为247小时。238第238页共238页n┌──┬────┬───┬───┐│周│续入业务│老预测│偏差│├──┼────┼───┼───┤│5-1│1400│1000│400││5-8│700│1080│380││5-15│920│1005│85││5-22│700│990│290││5-29│850│931│81│├──┴────┴───┴───┤│总计=1236│├───────────────┤│MAD=1236/5=247小时│└───────────────┘图11-5续入业务的平均绝对偏差──转塔车床工作在图5-7所示的正态分布的安全因子表中,只给出了变化超过平均值时的安全因子值。后备存货只针对提前期中过多的需求提供防范。由于提前期中需求大约有一半时间将小于预测值,要给出50%的客户服务就不需后备存货。因此,图5-7中给出的安全因子值是为服务水平在50%以上的情况提供的。为确定需要多大积压去稳定制造作业,需使用另一种表,因为当续入业务少于期望值时积压将下降而当续入业务高于期望值时积压将上升。换句话说,在设定后备存货水平时只需考虑正的差异,而为一生产计划确定积压的需要时时却必须考虑正的与负的两种差异。图11-6所示为兼顾正负两种差异时要使用的表。┏━━━━━━┳━━━━┳━━━━━━┓┃发生的概率%┃标准偏差┃平均绝对偏差┃┣━━━━━━╋━━━━╋━━━━━━┫┃0.00┃0.00┃0.00┃┃25.00┃0.67┃0.84┃┃30.00┃0.84┃1.05┃┃34.13┃1.00┃1.25┃┃35.00┃1.04┃1.30┃┃39.44┃1.25┃1.56┃┃40.00┃1.28┃1.60┃┃43.32┃1.50┃1.88┃┃44.00┃1.56┃1.95┃┃44.52┃1.60┃2.00┃┃45.00┃1.65┃2.06┃┃46.00┃1.75┃2.19┃┃47.00┃1.88┃2.35┃┃47.72┃2.00┃2.50┃┃48.00┃2.05┃2.56┃┃48.61┃2.20┃2.75┃238第238页共238页n┃49.00┃2.33┃2.91┃┃49.18┃2.40┃3.00┃┃49.38┃2.50┃3.13┃┃49.50┃2.57┃3.20┃┃49.60┃2.65┃3.31┃┃49.70┃2.75┃3.44┃┃49.80┃2.88┃3.60┃┃49.86┃3.00┃3.75┃┃49.90┃3.09┃3.85┃┃49.93┃3.20┃4.00┃┃49.99┃4.00┃5.00┃┗━━━━━━┻━━━━┻━━━━━━┛图11-6正态分布的安全因子表图11-7所示为以每周900小时平整生产的结果,在6-5这一周开始时积压为617小时(2.5个平均绝对偏差)。从图11-6的表中可知2.5个┌──┬────┬───┬─────┐│周│续入业务│生产│积压小时数│├──┼────┼───┼─────┤│6-5│1060│900│617*││6-12│425│900│142││6-19│950│900│192││6-26│1300│900│592││7-3│1060│900│752││7-24│856│900│708││7-31│502│900│310│├──┴────┴───┴─────┤│*2.5×247(MAD)=617│└─────────────────┘图11-7平整生产与积压小时数──转塔车床工作MAD将为95%还多的时间(47.72%给正偏差,47.72%给负偏差)防范能力变动,这意味着大约每20周只作一次变动。积压为617小时而生产量等于续入业务预测的平均数900小时时,当周续入业务低于预测时此积压将下降,而当续入业务高于预测时积压将上升。积压的低限为零(在该点将必须降低产量),高限为1234小时(在该点应增大产量)。稳定化存货越大,生产水平越少必须变动。图9-11所示为一年中生产水平改变次数与所需稳定化存量的关系。图中┌────┬────┬────┬───────┬────┐││││所需±MAD*│││每年改变│不变周│不变周│个数│稳定化││生产次数│的分数│%│(MAD=247小时)│存货│├────┼────┼────┼───────┼────┤238第238页共238页n│1│49/50│98│2.19│1440小时││2│48/50│96│2.56│1265││4│46/50│92│2.19│1080││6│44/50│88│1.95│964││8│42/50│84│1.74│860││10│40/50│80│1.60│790││12│38/50│76│1.48│730││14│36/50│72│1.36│670││16│34/50│68│1.25│617││18│32/50│64│1.15│568││20│30/50│60│1.05│519│├────┴────┴────┴───────┴────┤│*从图11-6│└───────────────────────────┘图11-9稳定化存货对生产速率改变次数的关系的计算方法是以假设差异为正态要布作根据。在上述例子中,选择改变多少次为好要取决于持有库存的积压对改变产量的成本的经济关系。像所有的统计技法一样,计算可以是严格的,但所需数据最好也不过是猜测的而且假设可能不成立。更为有效得多的办法是至少要同主要客户紧密地联系以确保更加均匀地接收订单以及更加及时地作能力调整。详见第二册。能力控制中的实际考虑下面是改善能力控制的一些实际考虑:1、季节性生产:控制产量以满足一季节性生产计划有一些有趣的问题在淡季中产量被维持在将逐步增加库存(作为稳定化存货)的水平,不需对背离生产计划的偏差作出快速反应。随着高峰销售季节末期的趋近与库存的降到其最低水平,所要求的反应变得越来越紧要。在库存逐步增加的季节中,实际库存可偏离计划水平达一个月的供应量之多而不致引起紧迫的问题只要能及时采取校正行动去满足设置在高峰销售季节之末的目标。例如,在库存逐步增加期间维持一月度生产计划然后在高峰销售季节转为每周生产计划往往是合乎实际的。2、改变生产中的惯性:在大多数工厂里生产水平有很大惯性是一种倾向。如果前所述,要让一线经理们去改变生产水平往往是困难的,因为他们对改变产量所涉及的成本与困难要比对不改变产量涉及的潜在的客户服务问题要清醒得多。这,当然恰恰是要有规则的道理──改变生产速率时的延误会使得所需的改变量大到几乎不可能去完成。例如,如果在已计划的库存最低点到来的20周之前就发现实际库存水平比目标低了1500个单位(小时、金额等),这种情况只要把产量比计划水平提高每周75个单位(1500除以20)就可校正。如果这一决定被拖延到只剩5周库存就要降到最低点的时候,产量的改变将必须达到每周300个单位(1500除以5)。这样一种改变其代价要较长期间去恢复恰当的库存水平,该期间中客户服238第238页共238页n务也将受到损失。这种惯性当产量被降低与提高时都存在。有激励制的公司往往发现他们在缩短工作小时数(例如从每周5天减到4天)之后仍能同正规时间下生产得一样多,因为在激励计划之下工人们加快他们的步伐以便挣得他们的正常工资,尽管工作小时数减少了。3、平均生产速率:一线制造人员往往倾向于把计划产量看作上限而非平均值。由于担心有空间能达到计划产量便往往忽视假日、意料之外的设备损坏与旷工等因素引起生产损失。密切注意生产计划上的累计产出总数将避免来自许多微小损失加总起来所造成的严重后果,更为重要的是,它将给出关于需要采取校正行动去克服改变能力中惯性的早期警告信号。4、改变的顺序:在装配件的制造中,传统的经验认为改变装配生产的速率必须按顺序进行,先改变原料采购计划,其次是组件制造,然后才是把子装配件弄到一起。该信念在于如果没有足够的组件去满足计划中的速率提高,那末提高装配的生产速率是毫无实际意义的。当然,如果组件的可用库存水平很低,这是对的。在大多数装配工厂里通常这种库存是过高的,减少库存并不会增加短缺的次数。不管能力如何增加,必须充分注意避免提高在制品的水平。另一方面,降低生产速率可在生产的各个阶段同时进行。如果是长期的降低,采购与生产的速率应设置得足以去减少在制品的中间库存,组件与半成品库存。不论是提高或降低能力应尽可能地避免在短期间里尖锐的增长。在这样快速的调整中工作中心之间作业的平衡实际上是不可能的。同等地困难的是去掌握好要满足总需求与库存问题二者同时增长或减少的能力改变。二者都要求过调,从而要求双重的能力调整。5、加时还是增加劳力:在制造企业中时常发生的一种争论关系到加时的相对价值。有的公司试图实施不允许加时的这样一会规则,而其它公司感到加时是极为经济的一种制造方法因而正常地把加时包括在生产计划之中。真正的问题是,该生产增长的期间是否将持续得足够长因而能证实应雇佣人员(假设有足够的设备可用)还是应该用加时来对付它?倘若有近似的成本数据可用,这问题的答案是容易作出的。所涉及的成本是加时的成本(包括任何附加的管理费,它与加时成正比地上升)与把生产提高到新的水平然后再把它降下来的成本这两方面的对比。例如,倘若要使生产水平改变一给定量预测需化费的加时奖金总计为每周¥200而若雇佣与培训人员,加上最后解雇他们以完成同样的改变所需成本估计为¥1000,就可用下列规则:当生产水平的增长预期将持续到5周以上时,就应雇佣与培训费用的点)。像其它任何给决策方案指定成本的企图一样,必须认识这里所涉及的成本也不是垂手可得的,而且管理人员怀疑这种把数字代入一个公式的决策。还可能有其它不可见的考虑──诸如公司在雇佣稳定性方面的声誉──是应予考虑的。同对竺任何决策方案一样,正当的方法是尽可能去收集可得的成本信息,揭示各方案的可能的成本并指出所涉及的不可见因素以帮助管理者去作出决策。6、把能力计划与优先级计划结合起来:显著的能力改变必须同修订MPS相结合以便使物料计划程序提供恰当的优先级。唯一的例外发生在当需要额外能力去对付计划外的混乱,诸如不平常的报废损238第238页共238页n失或生产中断的时候。产出控制中的相关要素引起实际工作者大问题的生产与库存控制的特征之一是所涉及的诸要素的相互关系。除非有一个生成现实需求的库存控制系统,否则能力计划不会有效。另一方面,只生成订单并把它们下达到工厂而不考虑能力的库存控制系统通常造成它本身过长的提前期与作为其结果的较高库存与短缺。如果对计划系统不提供控制,则生产将不可避免要变得失控而生产水平的改变将发生得太晚因而不能避免危机。生产控制系统必须包括某种决策边界,重要的是这些要被人们理解,使得任何人能认识到何时需改变生产水平。然后就可使用诸如服务对投资的关系曲线(图8-8)去揭示如果不改变生产水平,它会对客户服务产生什么潜在影响。在一家订货生产公司里,可以推测出对未来交货提前期的影响以帮助其它经理人员认识所涉及的真正替代办法。对控制而言某种决策规则或边界决不可少,这些规则在任何生产控制系统中都应实施,即使开始时它们必须根据靠判断(以后再用本章讨论的某种技法去提炼)建立起来的客限开发出来。即便开始时这些控制极限不够科学,也比没有要好。同必须不断地去辩论边界应当在哪里而把校正行动拖延到出了危机才知道该行动确实是需要的情况相比,事先只用一次就建立起边界可以提供合理得多的控制。为了确保生产出正确的物品控制生产水平是必要的。如果不存在足够的能力,诸如催稽之类的技法将只能使某些物品生产得出来。当真正的问题是能力不足时,去加大催稽的努力是愚蠢的,因为催稽不过是拆了东墙去补西墙。如果在一特暄工厂里,库存控制系统生成的需求是合乎实际的,却需要做大量的催稽,很可能这只是真正有问题的症候,这真正的问题在于对生产能力缺乏控制。总量生产速率对于采购计划(对采购者而言,最有意义的总计往往是金额)也是需要的。在第9章中讲过使用于供应商粗能力需求计划的劳务清单以及更为详细的技法。制订采购计划的另一方法是去确定在某一长视界上为满足一已计划生产速率所需组件的总数,然后将每种组件的总量乘上单价得出有意义的金额总量。在大多数方面,采购计划与生产计划是雷同的,把它作为种控制工具使用也完全是一样的。成本会计系统必须能在活动发生之后立即给出成本信息;这要求成本会计系统同生产系统相结合。组织的所有成员所需信息中的相似性使得一体化的管理信息系统成为不可少的东西。其概念就是以一种标准形式去开发与表示运行一工厂所需的基本信息,它可被所有部门及时地使用使得它作为控制信息是真正有价值的。优先级控制的目的在能力控制之外,有效的优先级控制是必要的。制造工厂必须制出足够的总产品并且要把工作做在正确的物品上;这二者都是必要的。下列功能必须恰当地处理:1、车间计划,要确信开工所需的每样东西都具备。2、工作选择与委派,对一个工作中心下一次要完成是哪一件活与由谁来做作出实际的选择。3、反馈,使得车间绩效能对照计划来予以度量,而且当需要时能产生校正行动。238第238页共238页n4、批的控制,提供工作定点的数据,对机器操作工所报告的计数进行审计的手段以及制成批的成本累计。5、重新安排日程计划,对在制工作重新安排以满足变化着的需求。车间计划是最重要的功能,它被设计来包括协调必要的文书工作与物料的到达,确保工具与设备以及开工所需任何其它物品的可得性与准备的责任。严格说来这些是计划与控制人员的责任而非第一线主管人员的责任。车间计划可通过照看需相似调整的工作一起运行而产生节约或通过批的重叠,在整批被前道工序完成之前就在下道工序开始工作从而显著缩短提前期。它也能在要求不寻常容差、特殊机器调整或独特工人技巧的工作方面向主管人员提供有用的信息。在车间现场恰当的工作选择随着一机器中心面前订单数的增加而增加其难度。车间投入控制得越好,即排队长度越短,工作选择就越不成问题。不过,在具有间歇性成批作业与功能性制造部门的工厂里,对在车间现场的工作选择必须作出一些规定。往往在第一线主管与计划人员之间关于应由谁说了算这个问题上有冲突。选择能最好地平衡车间与客户要求的工作这件事最好由主管人员与季派到制造部门的调度人员或车间计划人员之间紧密地协作来处理。这一选择往往涉及决定到底下一次应运行一种能追随机器目前调整情况的工作还是应运行一种急需去满足客户服务的工作。这种决定确定将发生的客户服务与许多费用。将工作委派给某一机器操作工通常是主管人员的责任,因为它涉及操作者的技巧与较难或较不受欢迎的工作的公平分配问题。良好的车间控制要求及时准确地跟踪订单进度的反馈。这允许产生差异报告,例如延迟报告,它指出哪项工作没有进展及其原因。这种反馈对良好的控制是必不可少的,因为它是告诉人们哪里有必要采取什么行动的警告信号的基础。批控制包括分配──识别(订单)号给一特定的制造批以积累它的有关数据。这些数据包括机器操作工报告的计件数,使得记工报告──该操作工报酬的基础──能被复核。在使用标准成本核算的公司里,对每一制造批都要积累物料与劳务成本。在大多数公司里,跟踪此批的运动是更新工作定位记录的基础使得工作进展与对计划的坚持能得到监控。下面关于优先规则的一节讨论重新安排已在车间里工作的日程计划的技法,使得选择去运行哪件工作时,可根据最新的需求。在大多数公司里,一旦工作进入加工,在下达到车间的订单上的要求日期是可以更改的。在备货生产公司里,某些物品将销售得比预测要快些,于是其库存量将在不多几周的期间内发生显著的变化。敏捷地对这些变化着的需求作出反应的能力是改善客户服务的有形资产。本章下几节进一步有选择地讨论这些功能。更深入的内容详见第二册。催稽(Expediting)催稽可能是最知名的而且是工业中使用得最悠久、最广泛的一种车间控制技法。催稽主要包括找出“紧迫的”工作并采用把它们推到竞争该同一设施的其它工作前面的办法去使它们冲过生产设施。催稽俗称加快或加急。最简单的加快办法包括找出(在制品中间)缺货物品或过期物品并取得即时的关注去移动这些物品通过生产。它是在问题已经发生之后开始起作用的。现代的催稽企图通过及早地发现潜在的短缺或困难以防止它们妨碍已计划的生产。加快已经臭名远扬,因为它往往被得过头了,产生高成本而且往往除了制造混乱与暗中破坏计划与控制活动中的信心之外对工厂极少贡献。然而,有些“救火”238第238页共238页n将总是必要的;中断与混乱不能被准确地预见,而且在计划与实际结果之间往往有点差距。有些公司声称他们没有催稽人员,但这只不过是他们用别的名词来称呼他们而已;在每家公司里总得有某人或某个小组意识到客户的要求而且负责去排队困难与解决问题使计划得以完成。常言道催稽员只是催促别人去做他们本应已十分清楚该由他们自己做的事。催稽员的资格是其成就中的重要因素。催稽员应是高度精力旺盛与足智多谋的人。他们必须在使得主管人员、检查人员、工程师与其它人员去正视他们的问题并迅速解决问题方面是有说服力的与有效的。实践中,催稽人员的活动通常组织得不好而且他们的时间浪费很多。这种情况可通过使一名主管人员同他们一道去计划催稽人员的日常活动使得他们的时间化费得有效而且有可能使用某种成就的度量去评估催稽人员的成果。加快包括在一工作中心的排队行列中挑出一件工作把它放在其它工作之前来运行。当两份订单竞相要争排队行列前头这个位置时,加快就达到了其报酬的递减点。随着加快的努力被增大,被选作加急工作的数目也增大。如果引起过度积压的真正原因未被消除,所有的工作很快都变成了加急工作,于是必须为优先级最高的工作开发出一种特殊的名称。这些成为特急工作。不用多久就会看出似乎只有特急工作才能按计划做出来。于是所有工作都变成特急。这种恶性循环继续发展。这是运行在持续的短缺情形下的所有非正式优先级系统的历史。加快只有作为例外技法才能有效。只有当很少数工作被给予超过其它工作的优先级时,这种加快办法才是有效的,不管催稽人员的人数与能力如何。原理56.加快越少,它就越有效。调度(Dispatching)调度员是通常用来称呼同一个制造部门中工人们紧密工作在一起的控制人员的职称。他们的职能是去帮助从表示已下达到每一工作中心的工作的一份订单文档中选出正确的运行这些工作的顺序。调度员也能取得由物料计划人员提出的所有制造订单的拷贝,不管它们是否已被下达,在这些订单上每一工作中心有作业要做。未下达的订单叫死负荷文档(deadloadfile);它们用于车间计划工作,以发起取得运行该工作所需的工具、夹具、量具等等的行动。当物料到达每一工作中心时,订单移进一活负荷文档(liveloadfile),同已经在等待运行中的其它工作归到一起,当一件工作被下达去运行时,某种形式的授权被给予生产现场,往往伴随以规格、兰图、时间卡与有关的文书。这通常称为订单包(orderpacket)。有商用设备可帮助调度员。最简单的手段是负荷板,表示积压中工作的机械设施。在第10章中讨论过它们。这些麻烦的手工调度技法已大多被诸如数据惧终端与其它数据传递设备等通讯硬件所取代。这种设备使得不必把调度员分散在各个别工作中心的集中式调度功能变得实际可行。集中式调度更加实际可行是因为它有且于解决调度的两个主要问题“1、比每一部门派一名调度人员,它要求的人员更少。2、它为调度员之间提供现成的交流使他们全体都知道最近的工作需求与车间状态。然而,集中式调度要求采用某种形式的通讯设备来向集中地点(诸如数据惧终端)报告工作进展,操作工要通过终端报告进度,未了结订单数据文档要即时地并连续地更新或定期成批地更新。实际工作分派通常经过主管人员或调整人员讨论后238第238页共238页n输,该员把工作分派卡恰当顺序放在车间现场的投入站处一个文件架中,在那里把工作分派卡交给被委派该工作的操作工或由操作工去看。典型的集中式调度控制中心管理几个工作中心,每一工作中心在文件架上有一份订单文档。正在进行加工的工作由放在架子正面恰当的槽中的订单包表示,而积压或排队等候的工作放在架子反面相应的槽中。工作活动的通知随着车间现场上数据的收集而来。数据收集可由人工登入与手携的文档,由话音传送到集中调度站或由复杂的电子设备。同简单的处理不变数据(订单与零件号、作业号与描述等)与可变数据(日期、时间、完成数量、工号等)的远距重现装置相比,数据收集终端在功能与成本两方面均比前者相去甚远。它们的操作或简单或复杂;有些复杂设备有教学用显示屏幕可指导人们去做报告过程的每一步骤。终端有下列优点:1、报告与记录可用较少时间。2、系统数据的更新更加及时。3、编辑错误较(例如,比较订单号与零件号的兼容性)而且人工参与较少。注意第2与第3条优点可能看不到除非结果能得到真正的节约。昂贵的数据收集设备必须有可见的效益来证实。诸如更好的决策、更快的响应与更高的生产率之类的说法并非合理的;这些效益是用较简单、较廉价的数据传送也全部做得到的。流动控制(FlowControl)1950年代中期开始,有一种用控制半过程流水作业车间生产的简单系统在基于公司中获得了非常成功的应用。当许多零件的系列追随同样的作业顺序时,即便使用的是不同的机器或设备,就存在这种作业。被称为流动控制,它所根据的原理是如果在制品保持低水平,被发动通过一半过程流的工作将以最小限度的文书工作与正式手续获得进展。流动控制有六个基本要素:1、主要活动的有计划生产水平:对每一作业或每一大类产品搞有计划生产速率是不必要的;ABC分类法犹如它适用于生产控制的其它众多领域一样也适用于这里。有少数产品需占用某一给定制造过程中的大部分可用工时。只要紧紧地控制住这些少数领域的投入率,生产速率就可保持在相当均匀的水平。2、对物料有完善定义的“进”站与“出”:每一部门中都应设有明白地樗的进站与出站,使得进入一工作中心的所有工作惚被认定为新的工作而该忠完工的所有工作立即引起物料搬运者的注意,他们将把它移动到下一个“进”站。3、在制品明白可见的日期标志与识别:流动控制强调在制品的目视控制。随着每一作业被完成,每一物料的移动批上用标签记上工作识别与完工日期使得每一有关人员都能知道每一工作已在每一作业耽了多久。4、慢移动工作的延迟报告:每经常规的间隔(通常每周2次),用表列出那些已在任一机器中心滞留而实际未被加工超过了规定时间(通常1式2天)的工作名单。5、一个优先级系统:238第238页共238页n有时需有一简单的优先级系统,但由于流动控制技法带来的短提前期与工作快速流经机器中心,通常降低了个别订单上优先级的重要性。6、良好的现场管理与车间现场纪律:由于流动控制是在车间现场控制物料的一种目视方法,它要依靠良好的车间现场管理的搬运、排列与安置车间容器中良好的纪律以便物料能安放在恰当的地点并立即可以被识别。流动控制是应用本章所讨论的在制品控制原理的一种彻底地实际的方法。它租用于工作的半过程式流动──实际工作者在企图使用流动控制之前应弄清楚他们的车间确实是如此的。这一技法把只发给工厂以实际需要的工作和使投入非常紧密地配合车间实际能力的责任加给了安排日程计划的人。它把车间计划的重担放给部门主管,而它本身并不提供批控制。因此,工作定点与计数的审计必须由另一系统来处理。重新安排日程计划与优先级规则鉴于长提前期引起的问题已被如此频繁地讨论过而且其影响在车间控制系统的设计中如此重要,考虑一个日程计划更改的典型例子是值得的。图11-10所示为已订货要在第21周到达的17种样本物品的研究结果。该订货系统指出这些物根据13周的提前期预定要在#21周交货的17种存货物品│原需要日期││││││││││││││││││││││││││││││±4周││││││││←─┬──┼──┼─→│││││││││││││││││││││││±2周│││││││││←─┼─→││││││││││││││││││││││实际需要│││││││││──────┼──┼──┼──┼──┼──┼──┼──┼──┼──日期│││││││││──────┴──┴──┴──┴──┴──┴──┴──┴──┴────12131415161718192021222324252627282930图11-10重新安排日程计划对“需要”日期的影响品根据13周的提前期将在第21周需要。后来的经验表明其中5种物品实际上在238第238页共238页n第19周以前就需要,而另5种要在第23周以后才需要1种物品实际上在第14周需要,另1种物品由于销售已放慢,第26周以前还不需要。这看来似乎是个极端例子,但工业中同长提前期打交道的人将同意这是相当典型的实际经验。一个良好的物料控制系统提供周期性地检查需要日期的手段以便根据尽可能近的信息来安排恰当的物品进入开工。它也提供检查任一已开工物品的需要日期的手段,以便如果需求有变化使得有必要或希望作修订时可以重新安排日程计划。详见第5、第6章。大多数优先级技法简单地对订单与作业使用日期,或者是需要日期或者是一工日期。第二个重要因素是剩余工作量。一种包括日期与工作会含量二者的技法叫做“临界比”临界比技法是由ArnoldO.Putnam与他的伙伴在Rath&Strong公司开发出来的。对于使用订货点法订货的物品,此技法比较该物品库存的消耗率与其制造提前期的耗费率。存货消耗率是临界比的分子而制造提前期耗费率是分母,这个比率用确定工厂中或竺发放文档中工作的优先级。它应使用实际需求的最近信息──临界比高的工作是非急需的,而低的应当被加快。计算临界比需用下列准确数据1、每一库存物品的重订货点2、任一给定时间每一物品的现有库存与可用库存。3、每一物品所要求的总制造提前期4、每一物品所需的剩余制造提前时间(在车间中的或在给定时间在竺发放文档中的制品)使用这些数据,可确定下列两个因子:存货消耗因子A=可用存货重订货点数量这一因子通常小于1.00,因为如果可用存货大于订货点就不会订另一批货。当然,客户退货或取消订单将增大可用存货从而使因子大于1。提前期因子B=剩余的标准提前期总制造提前期此因子通常也将小于1,因为如果该零件是在制品,总有一部分总提前期已被使用掉了。临界比由下列关系式确定:临界比=存货消耗因子A提前期因子B例如,设某物品的订货点是2000件。一个新批订货之后的三星期,存货室只有1000件可用存货。存消耗因子A为1000A=─────=0.52000238第238页共238页n此物品完成一批所需总时间是6周,还剩下3周。提前期因子B为3B=──=0.56因此A0.5临办比=──=───=1.00B0.5按其大小,临界比指出一订单可处于下列三种情况之一:1、良好比:A/B在0.80与1.20之间可用存货与提前期的消耗率差不多,补充批应接近按时完成。对这种工作不需采取行动。上述例子就属这种情况。2、加快比:A/B小于0.80例如,A=0.2而B=0.50(临界比0.2/0.5=0.4)指示剩余存货已降为订货点的20%──而剩下来去完成目前在制订单以补充该库存的总提前时间只有50%。在这种情况下,必须加快该工作否则将发生缺货。3、松弛比:A/B大于1.20这种比值指示可用存货的消耗率比原来建立订货点时要小与/或制造订单已经正常情况下移动经过车间的速率要快。不管什么原因,可延迟补充该物品而不致引起缺货。如果不延迟它,新批将进入库存,而现有库存仍相当多,库存持有成本将会增长。这种技法,虽然在大多数公司里它涉及大量的数据与计算要处理,却是检查与修订在制品或待发放文档中订单的计划日期或用来直接采取有效行动去控制在制品的一种极为有效的技法。在订单交货日期由物料需求计划生成的场合也可使用这类比率。考虑在同一工作中心的两项原先安排在第104天的工作,现在是第105天。表面看来似乎二者应具有同样的优先级,但工作A应在第106天发货而工作B剩下更多作业要到第110天才发货。初看起来工作A应分派更急的优先级,因为它只剩下很少时间去赶上计划了。然而,相对的工作含量是重要的,可提出一优先比如下:临界比=需要日期-今日日期需要日期-作业计划日期106-1051对工作A:────────=──=0.50106-1042110-1055对工作B:────────=──=0.83238第238页共238页n110-1046对过期的工作,临界比的计算必须作些修改,比值将是负的。一份过期1天还剩下1天工作的订单,同过期10天还剩下10天工作的订单一样,其临界比都是-1。在过期的情况下要确定优先级,这两个临界比的因子要相乘而非相除。这样工作A的临界比将为-1,而工作B的临界比将是-100,给出了更加真实的相对优先级。一个有效的优先级技法应该是:1、确定的(Definitive),能给出不同的相对优先级,“打结”(具有相同优先级的工作)的情况少。2、真实的(Factual),以准确及时的信息为依据。3、动态的(Dynamic),对客户驱动的变化(实际销售或订货量或日期的变化)与工厂驱动的变化(加工中的中断)都能作出反应。4、简单的(Simplt),为所有需要关于订单优先级信息的人们所易懂。分派优先级的各种方法的应用以及日期与工作含量之外的其它因素详见第二山第6章。有两种临界的变异曾有一些用处:1、队长比(Queueratio):剩余非工作时间除以为平衡作业而计划的原排队总长度。2、松弛比(Slackratio):剩余非工作时间除以尚未完成的作业数。二者都需要比临界比作更多数据分析而并无超过它的实际好处。此类动态系统可用来生成日调度表如图11-11所示。表中工作按优先级顺序排列比值最低的(最急件)在最前面。这可有助于把车间计划向前推进,不但表示目前已在工作中心里的工作而且也表示下几天中预期将到达的工作。这一方法提供提早的通知,以便更有效地计划工具准备、按顺序的调整与重叠的作业。┏━━━━━━━━━━━━━━━━━━━━━━━━━━━━━┓┃(按优先顺序)┃┃┃┃工作中心#4010日期3/21┃┃班1┃┃┃┃┃┣━━━┳━━━━┳━━━┳━━━━━━┳━━┳━━━━━━┫┃工作号┃零件号┃工作号┃作业描述┃比率┃备注┃┣━━━╋━━━━╋━━━╋━━━━━━╋━━╋━━━━━━┫┃70832┃7123X┃030┃Blanchard磨┃.55┃┃┣━━━╋━━━━╋━━━╋━━━━━━╋━━╋━━━━━━┫┃30765┃1937A┃070┃磨┃.68┃到B.P.23789┃┣━━━╋━━━━╋━━━╋━━━━━━╋━━╋━━━━━━┫┃63117┃6424B┃040┃粗磨┃.82┃┃┣━━━╋━━━━╋━━━╋━━━━━━╋━━╋━━━━━━┫┃92318┃7702X┃060┃粗磨┃.94┃商用容差┃238第238页共238页n┗━━━┻━━━━┻━━━┻━━━━━━┻━━┻━━━━━━┛┏━━━┳━━━━┳━━━┳━━━━━━┳━━┳━━━━━━┓┃94413┃6866M┃050┃粗磨┃1.60┃┃┗━━━┻━━━━┻━━━┻━━━━━━┻━━┻━━━━━━┛图11-11日调度表对这类报告的成功,准确、及时更新的信息的重要性不会被强调得过分。调整度表最好每天发布因为车间状态在不断变化──如果报告上表示的状态比几小时以前还要老,它们对车间的价值将非常低。前面讲调度时提到过数据收集终端在车间里的使用,重要的是要注意大多数使用动态优先级规则于重新安排车间计划的公司确实使用某种机械化系统来做车间反馈。终端解决一个同机械化系统有关的技术问题。当预告冲孔的时间卡同车间订单一道发到车间时,对每一作只需发一张卡,不管该作业要作多少次工作报告,因为该卡可以反复多次地插入终端。没有终端时,这种预告冲孔的报告卡──常称为车间包──必须有足够数量的供应以便在每班终了时(或其它报告劳务的期间)以及该作业完成时,就有一张卡可以返回到调度室。看板在日本看板的意思是卡片、标签或票。在这一特定意义上,该名词曾被应用于有关车间现场上工作控制的每一件事情,甚至包括──生产控制系统。其恰当的意思是一种用来生成产品、子装配件或外购与自制零件的补充量的执行技法。该技法为日本丰田汽车公司所开发,作为他们的丰田生产方式的一部分,而且只应用于具备某些条件的场合:1、生产日程计划是平整的。物品是定期地生产的,若不是每天生产的话,虽然某些变化是可能的。生产需平滑,所需在制品越少。为此a.3到4周的主生产日程计划必须是有效与不变的。b.生产运转期必须很小(即生产调整必须很短促)2、能力是灵活的而且能在很短时间内提高以处理小量额外负荷。3、生产流经仔细地计划并训练有素,具有清楚定义的“进”站与“出”站。4、使用标准大小的容器,每个可装一定数目的每种物品。所使用的看板卡有两种类型:移动卡与生产卡。在每一工作中心生产卡授权它去制造某一物品,数量为一个容器以替代从该工作中心的出站取走的一个容器。这些卡上的典型信息是零件号与描述,卡号,容器的容量,源工作中心号。可包括其它信息,诸如物料清单、工具等等。在只做少数物品的场合,可用色球或其它简单手段取代卡去告诉源工作中心要制什么物品。有卡非常复杂,使用条形码并用作供应商所递交物料的发票。移动卡授权从一原工作中心将一个容器的某一物品转运到用户工作中心。它们基本上载有与生产卡相同的信息。在物品移动进入并存储在用户工作中心区中时,它们被附着在容器上。这两类卡都从用户区向源区移动(通常用手)而且当移动或生产在准备之中时被放在一架中。看板技法着重在只制造所需要的东西去替代刚刚被使用掉的物品。从其容器使用任何物品触发该容器上移动卡向源工作中心的出站去递交。这一递交反转来又发起一容器向用户工作中心进站的运动,所经历的时间可能从5分钟钟最多到几个小238第238页共238页n时的范围。人其出站移走一个容器的同时要发放一生产卡到源工作中心,于是另一批被生产出来以装满一个容器。当完成时它们被递交到出站,通常在1到3天以内制造该批使用此工作中心进站中的组件,这反转来触发其上工作中心和移动卜恶性循环产。因此,使整个生产配合于只做被用掉的东西。所以,该技法被称为拉动系统(PullSystem)。看板可使用于一种生产活动或使用于一系列生产活动的全体。其大多数应用是总装与从供应商或厂内作业重置主要组件。在整个流程中一物品的总库存量取决于容器容纳每一物品的数量预期的需求差异可容忍的供应差异在运转得最好的工厂里,在整个作业中容器的数目(等于看板卡的数目)是不断减少的。当然,这要求不断地向妨碍工作顺快速流动的各种问题去进攻。提前期控制在第9章讲过,控制提前期要求控制能力与优先级二者。在尝试以缩短提前期为目的的计划之前,实际工作者应分析最近被完成的实际订单的样本以确定提前期的实际要素,诸如调整时间、运行时间、移动时间与排队时间还有处理客户订单的时间。客户在送进他们的订单时就认为提前期开始了。在某些公司里,做完订单登录过程可能拖延到10天或更多天。调整时间与运行时间的标准通常是有的,而且容易作出良好的估计。移动时间可估计得相当接近。排队时间可通过从该订单被加工时该工作运作的总时间中扣去所有其它要素而求出。通常这要占总时间的90%还要多。寻求提前期压缩时有三个主要改善领域:1、订单处理时间:这是从订单离开客户直到物料实际地从一备货生产工厂的存储室拉出或直到它被一订货生产工厂安排进入生产之前所经历的时间。从客户到供应商的订单实际传递时间难得构成这一提前期要素的重要部分。如果它是的话,使用远距打印设备、电话或现代数据传输设备可把它削减许多。大多数长的订单处理时间是以下两个原因的结果:每一订单都被当作例外来处理或者全部文书作业──订单录入、更新销售记录、库存调整、开发票等等──要在订单被发放去加工之前完成。在许多公司里信用经理必须查看进入的每份订单,而不仅是核对信用风险,因为销售部门要求有人去查看进来的每份订单以拣出反常的订单。如果这些人按顺序处理订单,即使他们敏捷地审查这一订单处理时间会需要必天;若稍有延迟它会需要几个星期。订单处理是超过本书范围的一种复杂体制,但重要的是要知道它对提前的贡献,并像工厂提前期一样地去控制它。精心地去压缩文书工作会像新处理设备或改进的生产控制系统一样改善公司的绩效。例如,复印机使人们可在开始所要求的正式文书工作(打印该订单、编辑它、并经工程、信用与销售的核查)之前很快地把客户订单交给计划人员去起动工厂的工作。在大多数工厂里,如果有什么理由因为不良的信用或工程问题而要停止该订单的话,该订单也并不会已经进展得多么远。2、安排日程计划:238第238页共238页n在大多数公司里,订单积压构成总提前期的最大部分。如第10章中所述,需有某种平整生产的方法,而如果这种方法不是用计划来提供,它将用起始作业前的积压来达成。在订货生产工厂里,续入业务的波动使得起始性积压成为不可避免的。如果没有有效的能力控制,这些积压会增加成周的不必要提前期。第10章讲的投入控制通过使生产紧密地配合总需求以及按最近的客户需求去把个别订单投入生产会有助于缩短计划提前期。按尽可能短的循环去安排日程计划也可压缩提前期。3、减少在制品:在大多数间歇作业中,对提前期的分析将指出最大的收获要通过缩短在各个别作业的等待时间来取得。在大多数公司里,提前期控制并未被人们很好地理解。许多人相信它们的实际提前时间时适当的。不幸的是,如果提前期被预期是长的,它们将如预期的那样是长的。第二册第5章中所述的业务活动增长、阶跃上升的订货、提前期变长、更多的订货与提前期进一步变长这样的恶性循环将引起外购物品与自制物品二者严重的短缺与库存不必要的增长。需要有一项主要的教育计划使所有有关人员确信通过计划工作、减少积压订单与投入产出控制,一个提前期平均长达15周尚不能满足需求的部门现在将能够以平均2周的提前期去给出正确的交货!图11-14是一位采购代理人发给她公司的物料控制经理的一份备忘录。它说明一位采购代理人Seager小姐由于供应商太忙不能给出良好的交货时为施加压力而提出一个并非不寻常的反应。在此例中,Jones先生的公司是Fairville部门轴承插的唯一供应商,而现在Moss先生该做什么是个令人感兴趣的问题。增加库存的唯Johnson-Fairville公司Fairville分部部门际通信给:物料控制部J.R.Moss先生日期:7/23主题:提前期我用电话通知了R.Jones先生关于我们马上需要轴承插。Jones先生说他们的轴承插部门目前正以6周交货期运行。他建议我们增加我们的库存以照顾未来的延迟。J.Seager采购代理人图11-14恶性循环开始一供应商,而现在Moss先生该做什么是个令人感兴趣的问题。增加库存的唯一办法是对Jones先生的公司发出更多订单,其不可避免的结果是使他报出更长的提前期。当Moss先生试图预测更远期的未来需求时,他对他需要哪些轴承插以及他何时需要它们的估计变得越来越不准确。即使供应商的服务并不随着厂内积压订单的增加而恶化(这并非似然的),由于客户将更难于预测提前期延长后的实际需求,Fair-ville分部给其客户良好服务的能力也必将恶化。供应商要求其客户早一点订货,意思是他们将因而保留足够的能力去满足客户238第238页共238页n的需要。然而,实际上由于要在较长提前期上去满足推测出来的客户需求,计划变得更差,其结果是浪费了供应商的能力。保留以机时、成顿的铸件或某种其它有意义的总件数来表示的供应商能力并将此能力在尽可能晚的时间承诺给具体的客户物品可避免这种浪费。生成较大量的订单积压将只会使能力不足问题更加恶化。提前期控制的实质在于通过有计划的生产速率与受控的投入去控制在制品。车间现场上的许多问题是由于不注意去控制在制品总量而引起的。在大多数间歇生产工厂里,有必要摆一些工作在每一工作中心前面去理顺生产流并确保由于缺乏工作而引起的空间时间为最小。然而,大多数制造人员并未认识在制品水平对提前期,产出控制从而对客户服务的巨大影响。由于缺乏这种认识,他们未能作出足够努力去把在制品保持在最低水平。在制品水平与混合产出的控制之间的基本关系在生产与库存控制的文献中已受到日益增加的强调。这并非一个新发现的主题。在此主题上最早的出版物之一是一篇最令人感兴趣的文章,其名为“管理对过量库存的案例”,它讲到一家公司对在制品库存作出非常激烈的削减,从而把平均提前期从5个月压缩到了2周他们的方法是简单的:把现场所有的工作都加上标签而把实际上不在被加工的一切物料都搬走。这就确保正确的工作将通过生产。这篇文章发表在1930年9月出版的“工厂与工业管理”上。不幸的是,看来在它问世后的几十年以来几乎并未引起人们的注意。削减在制品的好处知易行难。真正的问题在于教会下列人员懂得较低现场存货的价值:1、主管人员,他要在现场有了更多工作之后才增加劳力以满足增长的需求。2、库存控制人,他只关心生成订单以补充存货而不关心计划生产水平与恰当的日程计划安排。3、催稽员,他感到“只要再有2星期”每种工作都将按计划完成。4、日程计划安排者,他要尽快地把重要的工作弄成对工厂“已订货”,他相信额外的提前期将确保使订单按计划日期通过。这样,当他被查问某一具体工作的状态时,可以很安然地讲“它已经对工厂订货了”。5、调度员,他知道在制品太多了,但他忙于试图把正确的工作按日程计划发出去,因而没有为此做任何事情。6、调整人员,他为了等待另一件预期即将到来的工作而拖延一项工作的开始。教育工作落后是降低在制品工作的主要绊脚石,但在大多数工厂里这种努力的必要性是显然的。重要的是对所有有关人员强调过多的制品库存贯穿整个系统的影响,使他们认识到通过削减在制品可以取得什么结果。这些好处包括:1、较短的提前期──随着订单积压的减少而缩短。2、更好的计划──随着提前期缩短,计划更加可能变得准确。3、更简单的调度与沟通──订单积压减少后就得更容易。4、人员更好的利用──随着对催稽与调度的需要的减少而改善。减少在制品要求物料控制人中与制造人员双方作出主要的校正。负起保持工厂里工作顺畅流动的责任要求物料控制人员采取新的观点,他们历史上是依赖大量积压订单来做到这点的。当工厂作业人员看到制品库存在降低时,他们将为此深深担心──使每个人建立起不愁没工作可做的信心应该允许有一段相当的时间。学会去使用控制系统在订单积压失控之前就发现它们,配合上快速反应去防止它们,创造出真正的奇迹!在这过渡期间,一线人员与计划人员将必须非常紧密地一道工作去消除排队过238第238页共238页n长的问题。当在制品水平开始下降时,一位机器操作工有时可能会没有工作可做。如果客观地考察它,通常可以找到防止它的办法;例如,更好的日程计划安排本可以避免这种情况的。要使降低在制品的工作持久地有效,管理人员必须核查每一报上来的机器停车或操作工闲着的事件,确定其原因并努力去确保它不再发生。持有库存的合法理由之一是以防万一设备发生故障,而工厂人员往往以此作为持有大量在制品的主要理由。不幸的是,大多数公司里的在制品库存对故障提供非常小的保护因为它们并未被恰当的计划好。如果一台关键机器易发生故障,应备有备件,应使用预防性维护并且当它发生故障时应迅速采取修理措施使它返回作业。如果,尽管有最好的计划,它仍需有库存摆在此机器面前,则该库存应代表后续作业的平衡用负荷而且应当实体地从过程移开使它不致干扰正常作业但万一故障发生时却用得着。对大多数公司,在制品可以大量削减也不会引起不良后果。然而任何削减在制品的计划应从确定现行工厂积压条件下存在的工人与机器的停工时间开始,以便同在制品库存水平较低时的停工时间作直接对比。除非能够作出这种对比,否则停工时间过多将被人作为削减在制品的主要后果来引用。这样一种反应是可以理解的。对于已经习惯于有一大堆工作摆在每一作业面前看着这些大堆变小的工厂操作者来说,要他们学会今天工作而明天的物料尚不在手边,是一种重大的变化。尽管有这样的困难,越来越多的实际工作者正认识到减少车间里的物料是缩短提前期的最有效手段也是对产出衽真正的控制的根本。任务车间仿真(JobShopSimultion)当变量太多实际上不能直接采用数学的解法时,仿真是一种有用的工具。间歇或任务车间日程计划安排中涉及的许多问题显然符合这种情况,所以自从计算机出现以来,在任务车间仿真问题上已经化费了许多时间。在典型的任务车间仿真器中,数字数据──计算机的语言──被用来描述有多少各类机器可用,每班配多少人,以及从每一工作中心可预期有多秒个工作小时。每一件被研究的工作同制造顺序中每一工作中心、每项工作的调整时间与运行时间一道被描述。根据这一信息,计算机被编制程序去仿真实际的工厂作业并打印出结果,显示出开始日期、完工日期等信息。用几个小时计算机时间可以开发出相当于几个月的经验。有些企业与大学曾使用计算机仿真去检验在决定下一次运行哪一工作时可以使用的调度规则。应用过许多调度规则,但相当典型与常用的4种是:1、先来先服务:每一机器中心处最先来到的工作应该首先运行。2、价值优先:把优先权给予A类物品(批的金额最高的物品)使得在制品库存投资的金额保持低值。3、关键机器:后面要经过能力有限的关键机器的那些工作首先运行。该规则设计得使工作早点到达关键机器,使关键设备的利用率最高从而减少延迟的似然性。4、最短加工时间:要在机器中心运行的下一件工作是需要最少时间去完成该批的工作(把最容易做的活干掉)。238第238页共238页n已出版的结果看来似乎表明到处最好的调度规则是最短加工时间规则。此规则典型地导致:1、大多数工作被完成──这是有意义的,因为先做最容易做的工作,调度员将能帮助车间在一给定期间内完成更多件工作。2、在制品库存最低。3、平均提前时间最短。4、机器利用率最好。5、被延迟的工作最少──这一点特别令人感兴趣,因为此调度规则根本不注意工作的计划日期。然而,在一长期间上使用此规则可能意味着加工时间长的工作永远也完成不了。只有当机器中心处没有需要更少时间的工作时,他们才能被加工,而这可能永远也不发生!对任务车间中调度规则的仿真研究尚未达到找出最好的调度规则这个问题的答案,但它已表明本书一直强调的一点:任何使在制品保持低水平的技法──这是最短加工时间规则的主要效果──将从几乎每一度量上改善工厂绩效。计算机最受欢迎的应用之一是仿真流经工厂的工作以研究车间流(特别是延迟与中断)并为复杂的作业提出最优日程计划。计划者以计算机仿真为基础可以认识为二次性作业与开始性作业提供均匀负荷的作业顺序与平衡的投入。不幸的是,有几个这类程序曾被当作万应灵丹来出售,诱使管理人员去逃避把系统与工厂弄得有秩序的麻烦艰苦的工作。在这些程序所表示的工厂“模型”未超过‘实际事物的小小模仿“之前,它们的实际价值将是可以忽略的。它们不大可能找到一个超过短视界的实际应用。在控制得良好的工厂里,RaymondL.Lankford与StephanD.Smith已经成功地实施了一种他们叫做制造资源仿真(ManufacturingResourceSimulation)的技法。在一个程序中,它仿真MPS物品,组件的MRP,生产订单日程计划安排与最终装配日程计划安排。它检测何时将有物可用去支持能力计划以及何时将有能力可用去支持物料计划。它表明被仿真的物品将与工厂中现存的订单为物料与能力而竞争。它根据仿真的工作流提出现实的完成日期。这类程序具有巨大潜力。它们能对将被瓶颈工作延误的订单在它们过期以前──在仍有时间去采取校正行动的时候──就给出早期警告信号。它们能指示在要去完成未完工作业的剩余时间里能否把订单挽回到按计划完成。它们能把许多产品的组件连接到一起以便使物料与能力的缺资源能被最好地利用去改善发货与客户服务它们能为客户订单交货承诺提供一个健康的基础。这种技法是有的。真正的问题是,环境是否适合?有效的车间现场控制对任何车间现场上工作的控制必须在该工作到达现场的老早以前就开始。下面是必须在调度、优先级技法、仿真与催稽之前进行的活动的顺序:1、缩短提前时间──对制订健全的计划与成为灵活的与反应的是必不可少的2、压缩调整时间与批量──以避免资源超出即时需要的过度承诺3、简化物料清单──以便用较少步骤与顺畅的进展来制造产品4、使用不变、有效的日程计划──以便把重新计划的神经质减到最小限度而仍确保准确的优先级238第238页共238页n5、顺畅的投入──供给设施以它们能敏捷地处理的订货速率与订单的组合。恰当地做好的话,这一系列活动将确保在车间现场的订单数最小;于是它们就可被更紧地控制,然而,对于小的排队长度,中断的影响变得更加紧迫与严重。必须作出勤奋的努力去减少或消除1、质量不好的物料2、记录错误3、不良的机床安装4、设备故障5、供应商延误6、报废与返工改善对工厂环境的控制是去控制流经工厂中的工作的基础。原理57.控制工厂现场上工作的最好方法是去防止它过早地到达现场。产出控制技法的选择对学生与对实际工作者都一样的一个最富挑战性的任务是去清理出各种产出控制技法并认清它们适用的场合。已有许多文献致力于这个或那个特别的技法但关于它们如何在一家实际制造企业中一道工作在一个系统之中却写得相对地少。本书与第二册着重于这些相互作用。考虑选择恰当的产出控制技法的指针时应有一特定的应用在胸。要确定的基本点之一是究竟产出控制(主要是能力控制与工作选择)是真正成问题还是表面上看来围绕着产出控制而实际上只是计划不周或缺乏投入控制的结果。这一问题可通过核查制造物品的一个样本所实际经历的提前时间来回答。如果平均提前期是合理的但有些物品要用很长时间去完成而制成其它物品比计划提前相当多,则工作选择就是问题所在。如果,平均提前期极长,则应认清催稽或调整度对改善这一平均是无济于事的,问题在于能力不足。如果工作选择是真正的问题,必须选择要应用的恰当技法。当许多工作在生产中追随相似的流动模式时,应考虑类如流动控制这样的技法。这里,保持各种技法正确的相互关系是重要的。流动控制的一般要素(诸如计划速率、明确识别的进站以及延迟报告)在任何系统中都有意义但并非一暄必须同一目视跟踪系统并用倘若目视方法并不适合的话。流动控制的一般概念在通过电子数据惧终端的使用而被应用。车间里使用的任何一个具有某种程度流动的系统应集中最大注意于该车间的投入控制与使工作不断地移动。如果流动真正是间歇的,正式的调度能够最好地处理工作选择而且可以仅仅在瓶颈中心引进。当调度要使用于许多部门时,采取集中调度的方法比较艰。有时,当工作选择并非特别关键而只是去处理车间计划时,值得派一名产出控制人员到制造部门。这类部门的特征是有必要计划大量的细节去协调使工作开工所需的一切因素。这些因素包括1、原料与组件的申请与交货2、文件汇编,包括图纸、规格、工艺路线、车间卡与数控带3、物料容器与搬运设施4、机床安装、量具、夹具与测试设备5、协调主管、质量保证、维修与成本会计。238第238页共238页n在工作已发放到车间之后实际需求可能有很大变化的工厂里,动态优先级技法例如临界比法在向工厂反映这些变化着的需求方面将非常有效。应用这类技法应通过帮助正确的物品通过生产去改善客户服务。当外购组件特别重要时,应考虑使用更好的跟踪技法。这一跟踪应以最近的需求为依据,而不是以发布采购订单时所确定的要求日期。坚持要求采购部门及时买到所有物料而仍要求加急的工作,必须有一件可以被推迟的工作与这相对应的。懂得这个道理将有助于更加有效地重新安排供应商的日程计划。密切注意供应交货提前期(使用图11-13的所示的汇总表)有助于在麻烦尚未发展为引人注目的厅缺或库存激增之前就去发现它。选择恰当的产出控制技法这项工作要求知道有那些可用技法以及每种技法最适用于什么场合。此外,产出控制系统的设计要求懂得一个良好的系统中诸要素必须互相联系的方法。如果由于对能力缺乏计划与控制已使得在制品水平弄得太高了则车间控制可能非常昂贵、复杂但收效甚微。当车间订单积压失控时,即使最好的动态优先级系统也会降低其有效性。另一方面,如果物料控制系统并不真实地反映需求或需求的变化,则按照不现实的日程计划想使物品通过生产的努力将大部分成为浪费。产出控制是任何生产的努力将大部分成为浪费。产出控制是任何生产控制系统中不可缺少的一部分,但必须记住它只能作为一个设计良好的总的生产控制系统的一部分来发挥作用。238第238页共238页n十二.反馈与校正行动反馈──控制的基础根据定义,控制的意思是度量实际绩效(叫做反馈),同计划相比罗,发现显著偏差并发起校正行动。如第1章图1-1所示,一个制造控制系统有两个反馈环,一个对优先级(物料),一个对能力。在第9章曾将使用生产计划去控制生产水平作为对照计划去比较执行进程有效反馈的一例讨论过。需求预测希望的库存水平的改变被用来确定生产速率。然后定期地将实际的续入业务、生产与库存状态同计划对比。当库存超出可接受范围时,需作某种校正行动。投入控制也要求销售与库存信息的反馈去准确地指示哪些物品应进入生产开工。产出控制,包括编制车间计划、催稽与调度,要求有关已经生产了什么,在制工件的位置与要求注意的问题领域等信息的经常反馈。校正行动可以是返回原计划(更可取的),修订计划(最后的手段)或二者的某种结合。原理58.返回到原计划比重新计划更加困难──但更加好。制造控制根本就是一个信息系统的作用。这并不意味它只是一种编制报告的被动功能但它确实意味控制的基础就是信息而该部门有责任生成恰当的信息以便工厂能达到既定目标。这不是一件简单的任务──建立经营该工厂的目标,对照这些目标去跟踪进展并提出恰当的校正行动是一件极其富有挑战性的工作。信息并非数据;产生信息要求作分析──筛选数据以提炼出经理人员与其它人员需知的重要事实。原理59.健全的计划工作与有效的控制必须包括信息,不是数据。物料经理们时常发现他们自己由于客户服务、库存水平或工厂经营开支失控而处于困境。由于他们对能够校正这种情况的制造作业并无直接的职权,他们有时感到自己受到埋怨是不公平的。不幸的是,在许多情况中,他们恰恰是该受埋怨的,因为问题的基本原因是他们没有及时地将足够的信息提供给管理层去及时告诉他们真正的问题与解决这些问题的有效办法。物料经理的工作就是去经常地过滤该系统所提供的数据并给工厂管理层提供经营决策的向导。制造控制之连中有三个环节。要有良好的控制,这三个环节都必须具备而且要有效地一起工作。它们是1、一个计划与控制系统──处理完整、一体化与准确信息的规定。2、该系统由合格的计划与控制人员使用去产生及时的信息。3、这一信息由胜任的工厂经营管理人员使用去有效地管理制造作业。该系统应被设计成为制造经理的有效控制小组。一切活动必须朝着解决最重要的问题以便去校正一种失控的情况。该系统应设计得用对那些负责采取行动的人们有意义与有用的方式来表达信息。例如,一个妨碍着交货的质量问题应立即报告给能生成校正行动的质量控制或直线人员。该信息应被客观而简短地报告,并附有计划与控制人员能够用来解决问题的最好建议。这一关系也存在于同组织中其它小组之间,诸如工业工程、产品设计工程、维护等小组。未被迅速而有效地解决的任何问题应然后报告到下一个更高管理层。良好的控制与快速的行动是同义语。在一个控制系统中开发及时性是最困难的问题之一。例如,在某些工厂里,使用工资名单事务去报告工厂里的工作进展往往显得经济。它使用已取机器语言形式238第238页共238页n的共用源数据来做两件重要工作。在大多数公司里,工资名单之前需作的调整延误了在工作定位报告上的工作,使得这些报告在递交到需要它们的人们手上时有时已经过了2或3天。这些人于是发现许多件工作已经移走了而且很快就把该报告看成是无用的东西。在车间现场的电子数据收集终端能够在源点为工资名单与工作状态收集信息使它更为准确及时,这对改善反馈有重大影响。表示2或3天以前存在过的存货状态的库存报告是另一常见的对及时性原则的违反。控制不可能施加于已经发生了的事情,它只能施加于将要发生的事情。过时的控制信息根本就谈不上是控制信息。原理60.对控制而言,及时性比准确性更重要,虽然二者都是需要的。一旦已建立起了一个健全的制造控制信息系统,为得到人员恰当地去使用它要求有一个有效的教育计划。未曾拥用过一个良好的信息生成系统的计划与控制人员认为他们的主要工作是催稽与解决麻烦问题,而且他们往往怨恨一个系统所强加于他们的种种规定。他们都快淹死了,没时间去学游泳。他们难于理解,譬如说,恰当地审查需要重新订货的物品并生成补货订单这样的例行公事,真正比催稽某一件已经落后于计划的个别工作要更为重要得多。许多偏向行动的解决麻烦问题能手从未真正学会向例行的文书工作、详细的计划工作与困难向前思考作出让步,而这些是在备有良好的计划控制系统的经营管理中所需要的。其结果是他们永远有许多的解决麻烦问题要占去他们的时间。管理部门的教育是需要的以避免系统被这样一种成本节约计划所圈割,它节省一至二名文书人员的支出,付出的代价是不良的客户服务、过量的库存与工厂里的混乱。系统本身必须由及时更新的例行程序与物料清单所提供的信息为基础。在维护这一基本信息上面的吝啬从长远观点看来会是代价非常昂贵的。即使有了一个设计良好的信息系统,也有了计划与控制人员对它的有效使用,然而,在直线人员采取行动之前,还是完不成什么事情。例如,当现行系统已经相当有效地指出工厂产出水平不足以支持所希望的客户服务水平时,最高层管理者往往寻找改变他们的系统的办法以治疗一个缺货问题──而车间管理部门却未采取任何实际行动去增大能力。在生产控制之链中的第三个环节不具备的场合,最有效的系统与最胜任的计划与控制人员也不可成功。生产控制的职责就是信息,该信息必须以将导致所需求的行动的方式迅速、简要而频繁地呈现。直线制造人员的职责是执行计划,以恰当的成本造出足够的优质产品。订货生产厂中的反馈与校正行动虽然在订货生产厂中计划工作比通常已做到再多做一点也是可能的,但通常它不可能像在备货生产厂里那样去重新计划各项活动。因此在订货生产厂中更迅速地报告问题与更快地作出反应去解决问题变得极其重要。它所运作的订单(即使有从客户来的订货)需要更多的工程设计、机床安装与监督管理因为它们比备货生产厂里的订单要运作得不频繁些。由于这一缘故,人们对个别工作不那么熟悉,制造问题会多一些。在订货生产厂中,重点必须放在迅速报告与作出快速反应去解决机床安装、物料、计划更改以及诸如此类的问题。许多订货生产厂的大部分生产要做新的订货,对每一工作它必须从个别的工程设计与特殊的机床安装开始。在这种情况下,它必须仔细地去安排所需的工程设计与机床安装的日程计划。如果这些要素按计划进展,就没有必要通过缩短制造提前期来弥补损失在工程设计与设计部门使用额外的外援或加班加点或在机床室加点班238第238页共238页n去完成原计划,比之在项目初期因这些要素完不成计划而去干扰其它日程计划,于是必须在后期做许多加班加点试图弥补前期损失的时间,要经济合算得多。可用第10章介绍过的项目计划技法监控项目中为每一主要要素建立的检查点。用安排作业日程计划的方法建立检查点是订货生产作业中常用的首要改进措施。大多数公司从依靠催稽员只赶制已经列入过期表上的工作(超过对客户承诺的交货期而依然在厂里的工作)进步到有一种制度,它建立一关键作业应完成的日期并采取行动让蹭作业按时完成以满足允诺的完成日期。当然,及时更新的工作定位记录是不可缺少的。下一改进步骤是迅速向客户报告不可避免的日程计划更改以免造成突然袭击。虽然这需要鼓起一点勇气,一般它会造成(在长期间)好得多的客户关系比之什么也不告诉客户除非他们询问,即使订单已经晚了。要让客户主动打电话来查问为何一件工作延误了而听到的回音是“我们将查一下再给你回音”,这给客户的印象就是他们的订单已被忘怀,这家供应厂里对生产缺乏控制。大多数订货生产公司可由于具有较短提前期与满足允诺的日期而取得相当大的竞争优势。因此,在这种公司里去开发一个脚步勤快与对变化快速反应的管理集体是重要的。这要求有一良好的反馈系统使得管理上能很快地集中注意力于延误与去它们的有效办法。例如,当起始性作业面临的积压订单增长时,管理部门可采用的办法是比较少而都是不令人愉快的:1、或者a.报出更长的提前期──并开始“恶性循环”或者b.辞去一些生意(许多公司当他们的起始性积压增长时未曾更改他们已报的提前期因完不成允诺过的交货而损失了他们的服务信誉)或者c.提高生产水平2、如果已决定要提高生产水平,这意味着a.加班加点工作b.增加人员c.转包合同d.前三者的某种结合3、决定加班加点还是增加人员主要取决于对业务增长持续期的预测,它必须来自销售或市场营销人员a.若增长是短期的,应决定加班加点或转包合同b.若增长是c.转包合同d.前三者的某种结合3、决定加班中点还是增加人员主要取决于对业务增长持续期的预测,它必须来自销售或市场营销人员。a.若增长是短期的,应决定加班加点或转包合同b.若增长是长期的,则应增加人员不幸的是,在足够快地指出这些替代办法方面有效的制造控制部门是少数。管理人员自身往往在不能面向真正有效的替代办法与不能坚持在指出这些替代办法上从控制人员取得帮助这两件事情上是自觉内疚的。其最终结果是客户对他们所受到的服务感到失望与总经理对管理集体感到彻底失望因为服务变坏而成本上升了。提供信息以便管理部门把销售与市场营销人员、工程设计、质量控制与企业的238第238页共238页n其它主要主要要素结成一个有效的经营管理集体是任何工厂中计划与控制职能面临的挑战之一。一名有效的计划与控制经理必须能够向管理部门具体地祟其真正的决策方案诸如当加急订单强制通过工厂时哪些订单将受影响。事实上,一名好的经理将能够建议管理部门去考虑到一份新近记载入册的订单会如何危及到对其它订单的服务。组织信息以便足够有效地去指出作出这类决定的合理基础是一项极富挑战性的工作,它要求比催稽多得多的技巧,而在订货生产厂里催稽却通常占去了经理如此多的时间。原理61.作业控制(Operationscontrol)必须包括从可得的替代办法中挑选出在最坏取最小的选择。备货生产厂中的反馈与校正行动在备货生产厂中,必须更加着重于生产水平的计划、投入与产出的控制与在机床安装或设备方面需相当大投资的个别零件总产量的计划。虽然不必要的去过早发放订单是错误的,但通过观察一存货零件的需求,早在生成个别订单之前就去计划机床安装、机器能力等等是可能的。在备货生产企业中,诸如预测、MRP与分时段订货点法、CRP、投入/产出控制、工作中心加负荷计算、日调度报告与工作进程反馈等标准技法被使用。库存为需求与供应的变化提供缓冲,使得备货生产不如订货生产企业敏感。控制任何备货生产作业时最难克服的困难问题产生于当全部计划系根据预测翻译成的主生产计划之时。不管怎样努力去改进MPS,总需做许多作业更改以满足变化着的需求。大多数直线作业与产出控制人员对于带着不确定性去工作有一种天然的反感──他们试图去开发相当严格的方法用老早制订的不变计划去克服这一不确定性。由于这些办法通常行不通,这些人员于是把失败归罪于缺乏可靠的预测。由于缩短提前期在备货生产企业中同它在订货生产企业中完全一样重要。如果在计划与执行活动中都引进灵活性,客户服务可得到相当大的改善,而且人们认识到当客户需求变成真正的订单时,已计划的日程表日期是有待于更改的。这就要求某种动态优先级系统以及修改这些优先级的办法;定期的MRP重新计划(见第6章)与临界比(见11章)是用来修改优先级的非常衫的技法。但应仿住,随着在制品水平的降低以及(因而)工厂提前期缩短,修改车间优先级的必要性也变小了。在大多数备货生产公司里,客户需求对引起生产控制部门注意那些销售得比预测要快的物品是相当有效的,因为它们的库存将降低或变得缺货所以需特别加以关注。MRP同样地为销售得比预测要慢的物品提供良好的信息,因此可把这些物品重新安排计划以便让更急需的零件通过。对各个别物品的存货状态要有及时反馈的信息,这件事至少同要知道他们的补货订单处于生产中的何种状态一样重要。要求计划具有灵活性在一家既有备货生产只有订货生产而且存货物品与订货生产物品竞争同一些设施的企业里可能是特别费劲的。在这种公司里给予订货生产物品高于备货生产物品的优先级这种做法非常诱人,而且事实上通常就是这样办的。这种办法持续下去直到提供给从库存购买存储物品的客户服务恶化到如此低的水平使得销售部门不得不施加相当大的压力要求改善它。通常的反应是管理部门声明备货生产订单上的计划日期与订货6生产物品的计划日期完全同样重要,并规定二者都必须被认真地加以关注。这一政策通常保持有效直到发生一个别事例其中一项按其原计划日期运行的存货物品把竞争同一制造设238第238页共238页n施的一项订货生产物品推到一边。于是有人发现该存货物品其实在该日期并不需要,因为实际销售率低于安排该制造订单时的预测数。这一事件惯例地使得订货生产物品被给予比存货物品更高的优先级,于是这种循环又重新开始。在备货生产与订货生产相结合的企业中真正需要的是某种对两类产品分摊恰当份额的物料与能力的手段。然后使用投入/产出控制法去确保各自受到其恰当的份额。当然,存货物品可作为停货生产物品的缓冲使短期的物料与能力的改道成为可能。但这些必须很快被归还。在订货生产作业中反馈主要关系到工作进展与工厂里问题的影响。由于在订货生产厂里重复作业的百分数不大可能高而且新的问题不断产生,重点必须放在良好的反馈上去找出什么是问题并把它们报告给能采取校正行动的人。另一方面,在备货生产厂里制造趋向于例行公事,反复生产同样一些物品为了取得作业效率并从库存投资取得最佳客户服务,需从车间(报告工作进度)库存两方面获得反馈以便使成品存货状态中的显著变化能反映在及时更新的制造优先级中。采购中的反馈一家公司在制造其产品时依赖于外购组件越多,它要有来自供应商的良好反馈的重要性也就越大。在订货生产企业中,跟踪上供应商以确保能尽可能地在接近要求日期时收到所有物料特别重要。这一责任通常委派给采购部门但越来越多的公司正在把它委之于物料控制(这些人员叫做计划──采购员planner-buyer),把采购解放出来更我地从事寻找更好的货源。每一供应商应按其交货绩效、质量与价格来分等。在供应商选择中这三者都必须是主要的考虑。交货绩效报告也是有价值的,它表明同任一给定周内所要求的工作总数相比按时从供应商得到交货的工作的百分数。这类绩效报告应着重在短于寻常的提前期内被要求的订单数。真正的职业采购人员懂得施加尽可能多的压力去缩短供应商的提前期的好处。他们将宁可比费时间同供应商一道去做这件事而不是仅仅频繁地报告着供应商提前期的变化。虽然,更加重要的是采购部门需要去建立反馈的安排借以使供应商能提早告诉采购方关于预期的延迟交货以便物料控制部门也能得到通知因而大家能一道工作采取可能的行动去对付这种情况。解决这类问题要求设计良好的体制与善于确定在最坏结果中取其最小的解决办法的人。详见第二册第8章。物料控制与采购之间的关系以及他们之间所需反馈信息的类型与数量也要看作业的类型而定。在订货生产作业中,交货日期一旦确定后就比较固定;在备货生产作业中,交货日期更加可能变更,必须更加着重于供应商对日程计划中更改的反应能力。同样地,在订货生产企业中,对个别物品征求出价通常开始于当一份申购该物品的单子被填写之时,而这一出价只适用于一份订单或一名特定的客户。不能及时发出订单的事是常见的;事先应该约定这一延迟可以接受的期间。另一方面,在备货生产企业中,物品被重复地采购,没有理由要等到订货技法给出要重新订货的信号。在现代系统中,已计划单的向前可见性允许在需要发出订单去补充物料之前就同现有供应商蹉商价格或寻找新的供应商。同内部作业时一样,采购物品的按时交货要求确保供应商的能力将是足够的,平滑地供应订单并在尽可能晚的时刻去决定具体的物品。反馈应该度量每一期间的产出率,也要度量个别订单符合日程计划的情况。原理62.供应商按时交货靠的是足够的能力与短提前期,不是靠客户所有权、238第238页共238页n关系密切与神通。几种反馈技法在某些公司里使用缺货单或过期单去触发一次对这些延误的原因分析。在引起延误计划的问题与它们造成的失败次数之间通常存在着一种有趣的关系。这同库存的ABC分类法所依据的关系是一样的。一般地说按原因来分析计划被打乱时,可发现大约20%的原因引起80%的问题。有了这一信息可把校正行动导向它能起最大作用的方向。当个别部门或工作中心被树立为检查点时,在那里每件工作的状态要在特定的检查点同它的计划完成日期作比较,为每一部门维持一绩效报告以表明它完成计划能有多好是有实效的。由于处在制造序列后面的部门可能接受到更多已经落后于日程计划的工作所以它们更难按计划完成工作,这一报告的主要价值是作为将目前绩效与过去的绩效相比较的一种手段。该报告是否能为这一不利条件作出调整是其次的考虑。重要之点是去度量部门在给出更好服务方面其绩效的进步,而且把这一绩效度量看待得如同主管人员完成预算的能力那样重要。许多直线经理承认难于使主管人员成为面向客户服务型的但他们继续以其它目标来衡量一名主管人员的绩效而且实际上认为客户服务主要是物料控制与销售部门的责任。常规的延误报告,类似第11章里在流动控制标题下讨论过的那一个报告,对任何工厂都是一种非常有效的反馈工具。图12-1所示的每日延误报告由部门调┌──────────────────────────────┐│部门子装配││日期10/20││││到:到:从:││部门工长调度主管部门调度员││││姓名姓名姓名│├────┬─────┬───┬──┬──┬─────────┤││││延误│延误│││零件号│零件名│订单号│数量│天数│问题及措施│├────┼─────┼───┼──┼──┼─────────┤│10-1762│X-型面板│4321│1200│4│钻模在修理中│├────┼─────┼───┼──┼──┼─────────┤││││││10/21允诺修复│├────┼─────┼───┼──┼──┼─────────┤│17-1105│开关装配件│4004│2500│2│质量控制100%检查│├────┼─────┼───┼──┼──┼─────────┤│││││││├────┼─────┼───┼──┼──┼─────────┤│││││││├────┼─────┼───┼──┼──┼─────────┤238第238页共238页n│││││││├────┼─────┼───┼──┼──┼─────────┤│││││││├────┼─────┼───┼──┼──┼─────────┤│││││││├────┼─────┼───┼──┼──┼─────────┤│││││││├────┼─────┼───┼──┼──┼─────────┤│││││││├────┼─────┼───┼──┼──┼─────────┤│││││││├────┼─────┼───┼──┼──┼─────────┤│││││││├────┼─────┼───┼──┼──┼─────────┤│││││││├────┼─────┼───┼──┼──┼─────────┤│││││││├────┼─────┼───┼──┼──┼─────────┤│││││││└────┴─────┴───┴──┴──┴─────────┘图12-1延误报告度员填写,它指出车间现场上被延误的工作,其原因及正被采取的措施。由于这一信息被及时更新是极端重要的,而且由于只有被延误的工作才列在表上,该信息往往最好由调度员作为现场上每一机器中心面前所有工作的目视检查来处理,只列入被延误超过了某种可接受时间间隔的工作。时常被人们忽视的一个反馈的基本要素是一份常规报告,它压缩车间活动与问题以引导管理部门去注意待解决的重要问题。图12-2所示为一活动与问题的每┌────────────────────────────────┐│发自:物料经理送:制造经理周号13││兼送:主任工业工程师││总工长(4)││质量控制经理││采购代理││生产计划员(2)││││活动总结:││1、当前成品库存=56,000件-比目标72,000低1周││2、上周服务水平=96%对目标值98%││3、续入业务超过第1季度预测数22%。市场预测正修订预测;星期││一可完成。│├───────────┬──────────┬─────────┤238第238页共238页n│主要问题│建议│行动│├───────────┼──────────┼─────────┤│1.电子装配部的新工人│继续加时去完成生产需│更换一名女工.││不能生产出合格产品│求,质量控制部门帮助│加强临时性监督│││工长找出有责任的具体││││操作工并重新培训,│J.P.V││2.Popco开关厂依然比计│寻找第二货源│采购员每周去Popco.││划交货期落后1个月││本周有3家潜在供应││││商正在报价.││││││││F.W.W│└───────────┴──────────┴─────────┘图12-2活动与问题的每周总结周汇总,它由物料经理汇总并发给制造人员与其它同车间作业有关的人员。它包括一周以来活动的一般总结,主要问题列表与物料经理的建议。表中为责任经理留有作行动指示的空白。例如,在图12-2中,第二个主要问题是一家供应商未能近期交货,而采购代理人在右侧的空白栏中提出了行动的建议。这种总结的作用是:1、该总结的准备迫使物料经理每周去思考工厂的问题直到得出结论,正确地观察它们,组织工厂活动与问题的知识并为制造经理压缩之知识。2、该总结可作为有关人员进行周生产会议的议程。当经理们倾向暂缓作出决定时,总结的使用将迅速指出这种无行动的后果。该报告给最高制造主管以一种跟踪决定并确保所需行动被迅速采取的手段。每周活动与问题总结的主要要求是它要简短。有的公司设置一专断的规定,每星期可被这方面要求有很大的客观性──此人应非常小心要客观(虽然是真实的)而在指出物料部门内部的失败时要表现诚实。其它经理必须在每周会议之前知道列在表上的问题。这样可避免使他们产生“被人置于困境”的怨恨,并给经理们以时间去决定采取什么正确行动。实际上,这类报告(当它被有效地提出时)使经理们注意到真正的问题因而几乎总是以使这些问题得到解决为结局。绩效的度量在第1章开头,就陈述过制造公司的三项主要目标是:1、最大限度的客户服务2、最小限度的库存投资3、高效率(低成本)的工厂作业每一项都需有绩效度量以确保在它们的改善方面有持续稳定的进展。对每项目标都有许多绩效指标可用。最重要之一是客户服务。在第5章讨论过客户服务的统计度量。在备货生产厂中其它的度量可根据存货物品的品种数,欠交订单上行物品总数占续入订单上行物品总数的百分数,或发生欠交物品的订单占订单总数的百分数。┌─────────────────────────────────┐│成品库存服务报告│238第238页共238页n│月份:1966.8│├─────────────────────────────────┤│┌──┬─────┬─────┬──┬──┬──┐│││总│从存货供应│满足总需求│当前│目标│目标││││需求│总量│的百分数│目标│上限│下限│││├──┼─────┼─────┼──┼──┼──┤│││244│231│94.6%│95%│97%│92%│││└──┴─────┴─────┴──┴──┴──┘│││││││││││││││││││││││││││││││││││││││││├─────────────────────────────────┤│评注:││本年第一季度中提前期的普遍恶化已被制止。七月末减去了额外││的一周提前期缓冲库存。已将服务拉回到可接受限度。九月份服务水││平将接近目标值。││││││×××││9/3/66│││└─────────────────────────────────┘图12-3成品库存服务报告图12-3表示一家备货生产企业中一成品库存的服务报告。这家公司所使用的度量是已满足需求占总需求的百分数目标是95%的服务。上限是97%,因为更高水平的服务所需的库存超过了能被客户关系的改善所证实的水平。下限定为9238第238页共238页n2%,因为低于该水平的服务将危及他们作为其客户的供应商的地位。物料经理所作的评注指出这一特定大类产品的库存已经减少,其结果是服务水平已从被认为是不必要或不经济的过高范围降到了95%左右。┌────────┬──┬───┬───┬───┼───┼───┼──┼──┬──┬──┬──┬──┐││已往│#1周│#2周│#3周│#4周│#5周│#6周│#7周│#8周│#9周│#10│#1│││13周││││││││││周││├────────┼──┼───┼───┼───┼───┼───┼──┼──┼──┼──┼──┼──┤│││10/16│10/23│10/30│11/6│11/3│││││││├────────┼──┼───┼───┼───┼───┼───┼──┼──┼──┼──┼──┼──┤│应发货工作││20│23│23│22│17│││││││├────────┼──┼───┼───┼───┼───┼───┼──┼──┼──┼──┼──┼──┤│已发货工作││20│22│23│22│15│││││││├────────┼──┼───┼───┼───┼───┼───┼──┼──┼──┼──┼──┼──┤│交货绩效%│91│100│96│100│100│88│││││││├────────┼──┼───┼───┼───┼───┼───┼──┼──┼──┼──┼──┼──┤│重新承诺的││││││││││││││应发货工作││0│0│1│0│0│││││││├────────┼──┼───┼───┼───┼───┼───┼──┼──┼──┼──┼──┼──┤│已发新承诺工作││0│0│1│0│0│││││││├────────┼──┼───┼───┼───┼───┼───┼──┼──┼──┼──┼──┼──┤│新承诺交货绩效%│97│0│0│100│0│0│││││││├────────┼──┼───┼───┼───┼───┼───┼──┼──┼──┼──┼──┼──┤│过期工作数││0│1│0│0│2│││││││└────────┴──┴───┴───┴───┴───┴───┴──┴──┴──┴──┴──┴──┘图12-4某公司产品交货绩效在订货生产企业,服务通常以订单是否按计划交货日期发货给客户来度量。图12-4所示为某一订货生产公司的产品交货绩效报告。在第4季度的第1周有20项工作应发货,它们全都按计划发了货,因此交货绩效是100%。注意此报告也包括重新承诺过的订单的交货绩效。提出一个合适的客户服务度量的问题在于它要涉及许多因素。在备货生产公司里缺货物品的品种数影响客户服务──但往往更加重要的是哪种物品缺货与它们缺货持续多长时间。一种非常畅销的物品会造成施放多多欠交订单而一种不大畅销的物品可能甚至引不起大多数客户注意。在保有欠交订单记录的公司里任一特定时刻的欠交订单数是绩效的一种合理度量。然而,批评家可以指出这仍然没有度量欠交订单的持续期。某些物品可能长期一叶缺货引起客户不满,那不是仅仅计数一下欠交订单数所能度量的。即使用一更加复杂的系统把这一因素包括进去,仍可以指出某种客户偏爱往往是值得想望的──因为他们是新客户、有潜在的大生意可做或因为他们是老客户、一直提供着生意中相当多份额的忠实主顾。这种理论基础会导致提出高度复杂的客户服务的度量方法,所要求的努力超过了它的价值。客户服务的度量应尽可能地简单──其主要价值在于揭示客户服务究竟是改善了还是没有改善。讨论某一具体度量是否合理是浪费精力,不如在较简单238第238页共238页n的度量下用这份精力去改善公司的绩效。不存在一个最好的方法,应该用不同的度量去适合当时管理部门的具体利益。同许多其它绩效度量一样,用库存周转次数去比较一家公司的活动与另一家公司的活动是没有多大意义的。如果有条件地使用的话,可用它来比较一家公司同该行业的平均绩效。在同一行业中的两家公司可能具有极不相同的周转次数这要取决于最终产品中所含制造物料与外购物料的对比程度,该企业是备货生产还是订货生产还是两都者兼有,寄销存货政策,供应商的距离,拥有仓库的数目以及许多其它考虑,上述这些因素都会很具体地影响公司周转其库存的能力。比达到某一周转水平远为重要的是去建立给出所希望的客户服务的合理库存水平然后以达到这些库存水平为公司短期绩效的度量而以改善一给定库存数量所达到的服务为公司长期绩效的度量。库存周转次数作为库存控制绩效中改善的度量对其意义最大。确定库存周转次数的常用公式是期间的销售成本周转次数=────────────平均现有库存的成本周转次数的数字往往是从损益表与资产负债表中公布的数据取得;最常见的给出数据是年末库存(成本价)与年销售量(净销售价)。从库存值与年度销售活动的销售数字计算出来的周转次数给出的数据用来做比较是很不合适的。虽然行业范围的比较还得继续使用可得的数据,每家公司应时库存与销售二者都使用成本数据来度量自身绩效的改善,因为这样算出来的结果最有意义而且它是不受价格政策、利润政策、行政管理费用与其它无关因素掩蔽的。像所有绩效度量一样,库存周转次数必须慎重地使用。应用它的人应该彻底地懂得它,在公司内部各分公司之间甚至部门之间作比较时应极其小心并充分了解影响他们的表现能力的全部要素。大多数物料控制部门在认识他们有保持工厂高效地运行的责任方面曾经是迟缓的,其结果是很少有公司度量这种绩效。这要求度量加班加点时间、机器停工时间、雇员闲暇时间以及一年中雇佣与解雇的人数与所提出的计划的有效性之间的关系。由于物料控制关系到平衡的客户服务、最小限度的库存投资高效的工厂作业,任何一组有效的绩效度量必须包括对照这些目标的工厂作业度量,这恰如任何一位线主管人员的活动的度量应该包括他完成计划交货日期与总产出以及开支目标的绩效一样。最后,在任何办公部门的运行中有一个不言而喻的目标就是以最少数人员去取得良好绩效。设计一种手段来度量计划与控制人员做出的工作量与所需人数的关系恐怕是一件吃力不讨好的事。现代的以计算机为基的系统已经减少了大多数低水平文书劳务。剩下的决策与解决问题的活动是难于度量的。一种简单而有效的技法是去比较计划人员、日程计划安排人员与调度人员处理的物品、产品或工作中心的数目,假定他们的难度完全相同。应定期地将计划与控制人员的人数与部门的预算同工厂活动的度量相比较。注意同一产品更高的产出率并不一定要求增加计划人员。另一方面,产量较低而产品、物料屯加工过程花样较多则多半将需要更多人员去恰当地计划与控制。在这几年中,大多数计划与控制部门已增加了他们的职能因而需要越来越多的238第238页共238页n人员。不管这样做是否真有道理,现有人员的使用效率不高倒多半是真的。每一名增多的人员要求有更大一部分集体时间用于人员之间的沟通──这在计划与控制部门比其它任何地方都更为明显。在一家小型工厂里,要让少数人去知道其它人员在做些什么是比较容易的,但在一家大型工厂里,在计划与控制人员之间与计划控制人员同采购人员或制造人员之间的沟通却变成一项令人望而生畏的任务。在任何公司里,绩效度量都是极其重要的。在开始任何改善计划之前,应该建立起绩效度量从表明未来的绩效将如何同目前情况相比。人们总是容易看到了今天的问题而忘记了昨天的问题曾经有多在。如果不在改善计划开始之前就开始绩效的度量,很少有人将会记住“老早的好时光里”实际情形有多糟。绩效度量本身就是改善绩效的最好方法之一,因此它应成为任何一个生产控制系统的基本要素之一。公认的事实是在任一活动领域中的绩效度量有助于引发一种健康的竞争精神而人们钭努力工作去达到或超过一个他们已经接受了的现实的目标。原理63.精心地选择绩效度量;人们钭为按这些度量看起来不错而行动。初出茅庐的物料经理(物别是如果他们在公司里受到批评的压力时)往往急于要得到其它公司的绩效信息。这些经理询问其它公司的物料控制经理他们在其部门中有多少人员,他们的客户服务怎样,他们持有多少库存,等等,希望其中有些数字可被用来说服老板本公司的绩效实际上毕竟不坏。较有经验的物料经理们知道在公司之间比较绩效是并无多大意义的。这些经理集中他们的注意力去改善他们自己的绩效而不是试图以有人更差些来为一种不好的表现辩护。作业控制(OperatingControls)设计良好的制造业计划与控制系统能够生成包含若干重要作业度量的绩效与计划相对照的信息报告。这些包括1、主生产计划(MPS)由于MPS是基本的制造计划,对照它来度量实际绩效对于良好的控制是不可缺少的。图12-5所示为一种报告格式。其中有若干特色值得注意:││周││滚转│------│------│------│------│------│------│------│││23│24│25│26│六月份│27│28│────────┼───┼───┼───┼───┼───┼───┼───┼───┤12A341MPS││50│-│50│-│100│52│-│实际│─│48│-│52│-│100│││────────┼───┼───┼───┼───┼───┼───┼───┼───┤12B423MPS││610│610│610│610│2440│610│610│实际│(10)│603│610│610│625│2439│││────────┼───┼───┼───┼───┼───┼───┼───┼───┤12C246MPS││340│360│380│400│1480│420│440│实际│(12)│342│355│373│400│1470│││────────┼───┼───┼───┼───┼───┼───┼───┼───┤12D318MPS││180│180│180│180│720│170│170│238第238页共238页n实际│5│185│176│172│180│719│││────────┼───┼───┼───┼───┼───┼───┼───┼───┤12E416MPS││15│-│-│-│15│15│-│实际│-│-│15│-│-│15│││────────┼───┼───┼───┼───┼───┼───┼───┼───┤12F195MPS││205│205│205│205│820│210│210││实际│8│206│202│203│207│818│││────────┼───┼───┼───┼───┼───┼───┼───┼───┤12系列计划││1400│1335│1425│1395│5575│1477│1430│实际│(9)│1384│1349│1416│1412│5561│││生产计划││││││5600│││图12-5MPS对照实际生产a.报告显示每周的与月度的总计量。后者还要同生产计划相比较以确保明细计划同更高层、更长期总量计划中的产品系列总产量保持一致的步伐。b.在使用模块式物料清单的、具有许多选择的产品的MPS的场合,这种以实际产量与计划产量直接比较的做法是不易的(有时是不可能的)。本书第6章与第二册第4章有关于这种物料清单及其用途的详细讨论。c.产品系列的周生产量总计可能比个别产品的产出更重要。对实际需求最后一分钏的反应可能显著地改变产品的组合但总量必须足够。d.“滚转”显示过去未完成的数量,在大多公司里这是非常实际的经验。重要的是这一数字不要持续地增加或减少。二者都是实际生产有问题的信号。2、问题库存投入/产出详见第8章图8-2。它允许在一份报告上监控外购物料、直接劳务(投入)与发货量(产出)的实际对照计划的数据,其余额就确定总量库存。3、工作中心产出实际上每家公司都有生产产出的详细报告,但难得显示实际对照计划的数据。常见的报告显示劳动效率、按标准完成的工作的百分数与机器利用率,这些都是容易记录的,但并无多大重要性。报告应按时间期间显示产出问题;第9章的图9-10是一例。在每一时间期间工作中心中所处理的个别订单是否符合日程计划也应被度量。应对照最近的应交货日期来比较,而不是用订单发放时确定的交货日期。像第11章中图11-11中的日调度表为统计延误的,按时的与超前于日程计划的工作提供一种方便的基础去作为绩效度量来使用。4、供应商跟踪外购物炅的技法在第11章里讲过。这些技法能生成对供应商总的产出速率(当然,供本公司所需的)与及时交货二者很充分的报告。质量与价格通常由质量控制、采购与成本会计来跟踪。5、提前期在第一册、第二册的许多章里都强调过提前期管理的重要性。应对外购物品与自制物品二者都作定期的抽样以提出实际的平均提前期去同计划中的提前期相比较。这是最重要的绩效度量之一。同等重要的是产品的累计提前期(见第7章图7-6);应该定期地用实际的供应商与车间绩效的样本来检验。虽然不易取得,提前期的度量是值得化费力气去做的。6、记录的准确性238第238页共238页n评估系统记录准确性水平变化的报告见本书的附录Ⅵ,其它见第二册附录Ⅰ。关键的度量是无显著错误的项目数。这要通过抽样一切重要记录来提出,重要的记录有:a.客户订单b.物料清单c.现有库存d.未了结采购订单e.未了结制造订单f.加工数据(方法、工艺、标准、安装等等)g.成本系统健康状况诊断设计良好的系统能够产生报告指出系统自身中实际的或潜在的问题。譬如体温、血压、肿胀与发抖,这些度量能指出需引起注意的“疾病”:1、行动通知的份量知类型或例外信息2、数据遗漏与误差3、计划外事务这些问题在第二册第7章中同系统设计与安装问题一道讨论。校正行动的生成本章前面讨论过的生产控制之链中的三个环节是:1、一个生成信息的系统2、使用该系统去产生恰当的信息3、工厂作业人员方面响应所产生的信息而采取的行动。图12-2所示的活动问题的每周汇总是计划与控制人员必须提供给制造经理的引类信息的一个适例。这一信息必须及时地生成──控制只能施加于尚未发生的事件。表示这一努力是成功的一个良好指数是制造经理对一个问题必须查问的次数而不是他已经首先被通知有了问题的次数。一名有效的物料经理提前告诉工厂经理即将来临的问题并推荐行动防止它们变成对良好客户服务或高效工厂作业的严重干扰。原理64.辩解与控制信息之间的区别仅仅在于时机。计划与控制的真正职能是去生成为了使工厂避免陷入困境而管理工厂所需的信息而不只是处理为摆脱困境而要进行的日常活动。制造控制系统是一门处理信息的学科;它要求特定的活动要在特定的时间进行。物料经理像其它职能经理一样发现他们最好制订一张日程表把每天要求他们注意的事情列入表中并遵循这张表首先去做最重要的工作。没有一名经理能够去关照所有存在的问题,所以把问题排序并首先处理更重要的问题是极其重要的。如图12-6所示的检查表有助于确保那些为了保持该系统有效地运转而要求经常注意的例行活动被包括在此表中。这一特别的检查表表明必须每周编制日程计划,生产计划必须对照已计划活动每周公布实际活动,日程计划必须每月复审与修订(若有必要时)。238第238页共238页n┌──────────┬───┬───┬───┬───┬───┬───┬───┬───┬───┐││11/23│11/30│12/7│12/14│12/21│12/28│1/4│1/11│1/18│├──────────┼───┼───┼───┼───┼───┼───┼───┼───┼───┤│日程计划准备好││││││││││├──────────┼───┼───┼───┼───┼───┼───┼───┼───┼───┤│公布生产计划││││││││││├──────────┼───┼───┼───┼───┼───┼───┼───┼───┼───┤│修订生产计划│×││×│×│×│×││×│×│├──────────┼───┼───┼───┼───┼───┼───┼───┼───┼───┤│复审MRP输出││││││││││├──────────┼───┼───┼───┼───┼───┼───┼───┼───┼───┤│缺货百分数图更新││││││││││├──────────┼───┼───┼───┼───┼───┼───┼───┼───┼───┤│发出原料库存报告││││││││││├──────────┼───┼───┼───┼───┼───┼───┼───┼───┼───┤│完成"C"类存货复审│×││×│×│×│×││×│×│├──────────┼───┼───┼───┼───┼───┼───┼───┼───┼───┤│审计成品卡库存││││││││││├──────────┼───┼───┼───┼───┼───┼───┼───┼───┼───┤│活动与问题汇总准备好││││││││││├──────────┼───┼───┼───┼───┼───┼───┼───┼───┼───┤│编好制造区延误报告││││││││││├──────────┼───┼───┼───┼───┼───┼───┼───┼───┼───┤│编好外购组件延误报告││││││││││├──────────┼───┼───┼───┼───┼───┼───┼───┼───┼───┤│复审提前期│×│×││×│×│×│×││×│└──────────┴───┴───┴───┴───┴───┴───┴───┴───┴───┘图12-6计划与控制检查表有些物料经理使用一种制造控制日历,把一年中必须进行的主要活动列入其中,它包括诸如复审ABC等级与订货政策代码,实物盘的准备审查工作人员的绩效,编制报废物料表以备处理以及平时不常做但为了做好该项工作时必须迅速办好的许多其它活动。计划与控制职能的管理本书忆多次指出计划与控制小组的主要职能是管理好一个信息系统。必须强调这一管理不能被动地去做。物料经理在向管理层提出替代方案与这些方案的成本与结果的估计时应采取主动。在一家具有季节性销售的公司里物料经理应提出多种替代的生产计划以揭示如果完全用平整生产将额外地持有多少库存,如果生产直接紧跟销售则将增加多大能力,一牛人员水平将必须改变多少次,等等。物料经理应估计这些不同计划的成本,认识到其中大多数钭不在成本会计帐目表上,推荐一份计划给管理层并协助作出基本的决策。一旦作出决策之后,物料经理为工作就是去产238第238页共238页n出控制信息使工厂保持在轨道上。由于在长过程中将有许多从计划的偏离,这就需要有不断的校正行动。具有讽刺意味的是,在直线人员未曾采取过恰当的校正行动时,一个制造控制系统难得被认为是成功的。一个系统是必要的但不是充分的。仅仅产生了正确信息──即使作出了很大努力去告诉直线经理们需要去做什么──并不保证正确的行动将被采取。胆小的物料经理当他们允许其绩效要按其他人的行动来判断时是最易受责难的。即使该系统指出需要增加能力而且这一增大能力的估计已经及早地通知了工厂作业人员,但他们拖延不去增加能力,当结果使客户服务变嗟时,受埋怨的往往是计划与控制小组。几乎每个人都知道客户服务不好,但少有人能识别其真正原因。在管理信息的同时,物料经理们应能去引起行动。如果他们内行地做他们的处理信息的工作,他们将使所有有关人员知道需要采取什么行动并且谁要负责去采取这些行动。制造控制系统所生成的信息往往把巨大的压力施加在一名直线经理肩上,甚至加在往往是物料经理上司的制造经理肩上。如果物料经理对系统没有信心,如果他们不采取主动并且强有力地与勇敢地提出问题,他们会成为代人受过的“好小伙”,因某一别人不能采取恰当行动而受埋怨。制造控制系统必须能经得起来自直线经理们的相当大背后压力与挑烈,他们试图通过对该系统产生的信息表示怀疑并要求作彻底的复审或进一步分析来推迟采取行动。能被证实的或能被容忍的怀疑态度的重要性有一个限度。在这一点上,能干的物料经理值得其上司给他以坚强的支持以克服消极的阻力并采取有效的行动而不再进一步要求该系统证明它自己是可靠的。保持主动要求勇敢的经量配上良好的系统与胜任的操作人员。它也要求经理们记住他们的工作在他人看来是容易的。每天,物料经理们及其办事人员必须作出关于未来的成百甚至上千个决定。事后看来不可避免有些决定是错的,5批评者将能指出在计划过程中所犯的错误。此外,物料经理必须与之一道工作的许多其他经理可能搞次优化──其工作目标朝着有别于整个企业的目标。当物糍理不成这些目标时他们可能感到物料经理并不了解其实情况。在把唯一责任组织理论推行到极端的公司里,就是说在那里销售经理独自地对销售负责,总工程师单独地对生产职能负责,以此类推,这种情况就更加恶化了。有效的制造控制要求一客观的方法,它承认救火是必要的但防火才是更可取的。制造控制中最严重的引诱之一就是去当一名救火员──每天早上一来就准备好接到电话呼叫马上冲出去并且由俱来处理大多数催稽。这无疑问地满足着志向行动的人;它造成超乎寻常的能动性与把手指按在工厂脉膊上并随时知道什么事情正在进行中的一名经理的印象。不幸的是,这种救火活动明白地表明平凡的──但却不可缺少的──防火任务正被忽视。找出主要机床的期望寿命,弄清它们是否及时更新以达到所需容量或分析建议中新大类产品的设施年年何处可能发生瓶颈,如何避免它们:这些工作看来确实平凡而单调无味。忽视防火活动的物料经理可以肯定明天将带来更大更好的救火机会。物料经理必须对麻烦有思想准备。墨菲定律“可能出错的钭在最不适宜的时间出错“就是在一家工厂里发明的。物料经理应该是快乐的悲观者,他承认问题是一咱生活方式而明天的问题今天毫无疑问正在酝酿着。工厂里的危机非常罕见是一夜之间造成的──它们通常在一个长期间成长而且时常是久久未采取行动的结果。物料经理有责任及早指出麻烦可能出现何处,指示有哪些办法并做一切可能做的事去确保作业按计划持续进行或被校正以防止出现危机。有效的控制信息的最生要特之一就是它的及时性。在原理64中讲过,这是事238第238页共238页n后给出辩解还是及早地提出信息使得有人能采取措施去防止问题之间的区别。如果物料经理的上司询问为什么一种特定产品缺货了,而经过一些调查,他被告知它是上周在电镀部门一个瓶颈引起的,该物料经理只是给出了一种辩解。如果,另一方面,该物料经理老早就曾指出该瓶颈并提出正面建议去克服它而且预言,如果这个瓶颈不解决,产品将会缺货那么他就是发出;控制信息。这简单的差别就在于及时性──向工厂作业人员及时提供信息使他们在麻烦发生之前去采取必要的校正行动。为保持有效,物料经理必须用一客观的建设性的方式去使用他们的信息与知识的力量。他们应该是现实主义的并避免乐观主义者的痴心妄想,去指望麻烦可能不会发生或如果你不理它它就会自己跑掉。因为他们经常在提醒人们注意现存的与潜在的麻烦,可是,他们必须用下面的方式来做这件事,避免责备与隐含别人不能胜任并且不要忍不住去证明自己永远是正确的。由于物料经理的成就将主要地依赖于信息系统的准确性与敏捷性,使用简单技法去确保及时办成事情会对确保达到系统对注意力和活动的要求作出许多贡献。时常,某些最重要但是例行的活动(复审物料计划或提前期)是因为紧急中断的压力而被拖延的。有时要把后来表明的不良结果同其真正原因相联系是困难的。用如图12-6所示的检查表示确保重要的例行公事正被常规地及时地遵循会对正确地组织生产控制部门的活动有很大的帮助。对物料经理不可缺少的一项智力练习应该是定期地(至少每月一次)坐下来对下六个月里已知的与预期的问题作ABC分析,排出最大的问题并确保设计出活动来处理与防止这些问题。一个良好的习惯是每天准备一张今日按优先次序“要做”的活动表。每个工作日开始前先化半小时把此表准备好将使一天的活动有好得多的方向与高得多的生产率。物料经理每天应抽出一些时间去访问工厂里主要的或关键的生产区域。往往,快速地在工厂里兜一趟将发现潜在的问题比最最及时更新的信息系统还快得多。物料经理还必须抽出一点时间──这多半需要在工厂正规上班时间以外──去思考与计划对本部门未来绩效至关重要的事。这是他想像出防火项目与开发出改善本部门绩效的长期计划的时候。一名优秀的物料经理应努力使解决今天问题的行动与防止明天问题的计划之间达到平衡。虽然其办公室的力量在解决许多日常危机中是需要的,但他们必须避免过多地直接介入于催稽之中。必须有一个为未来作准备的有纪律的计划去平衡这种工作。为未来作准备最重要步骤之一就是教育。详细讨论这一课题超出了本书的范围;但在第二册第8章中提供有更多的内容。必须包括新技法、新系统、更现代化的设备的开发与使用的教育,以及通过参与专业社团去扩大眼界与听特殊课程以获得制造控制领域以外企业管理领域的知识。这个教育还应包括厂内计划。开始时,大多数人参加计划与控制工作时并未在此领域中学习过。他们不仅对生产控制知识知之不多,而且往往并不理解有许多东西要学。这种人往往变成催稽员与救火人而并无多大能力去有效地控制生产。牌价媾起,该领域已成为具有独特知识主体、语言、技法与应用的一门真正的专业。可通过APICS参加考试,由此一个人可被证明作为技术上合格的专业人员。这要求教育而且由于其对象包括成年人,这一教育必须尽可能切合实际。成年人必须看到教材的实际应用,否则教育计划就不会有效。对订货生产厂里的人员学习经济订货批量是浪费时间,因为厂里大多数批量取决于订货量。如果人们能具体地看到每种技法如何应用到他们的公司以及不能正确地使用这些技法曾经如何在过去引起过238第238页共238页n问题,他们钭热烈地作出响应。差不多每个人都有点场所想变得对工作更加精通。然而,需要接受有关制造控制活动的教育的人远远超过计划与控制人员。在许多公司里其它部门主管曾经能够把计划小组当作代人受罪者使用,对所产生的任何信息表示怀疑从而减少他们根据这一信息采取行动的需要。让这些主管去懂得实际上一个制造控制系统是什么,他们必须如何同它合作并使用它,他们提供的信息与他们所采取的行动会如何对系统的绩效产生影响,这是任何公司的成功所不可缺少的。最高层管理人员往往对制造控制的真正作用知之不多。他们不知道在库存与生产管理方面有效的替代方案是有限的而且并不总是意识到有必要去平衡日常作业中互相冲突的目标。制造控制必须接受指出这此冲突的责任。一项广泛的教育计划可以证实其非常高的引用如果其结果是开发出制造控制职能及其对企业各方面贡献的充分意识。一个非常有效的自我开发计划可由任一制造控制部门在部门高级成员指导下承担一既训练低级成员也为市场营销人员、直线主管、采购人员与其它必须同生产控制有效地一道工作的人员提供定白计划。用这种方法后一部分人认识到从计划与控制活动可以期望什么与不可以期望什么。虽然归根到底,向管理层与公司中其它人宣传制造控制的工作其成就要看结果如何。一名乐于冒险去设定有雄心的目标,努力工作去改善其部门的作业并在开发与管理库存控制、客户服务与有利可图的工厂作业等领域改善工厂整体绩效的计划方面获得成就的经理将不难说服管理层相信他的工作的重要性与价值。压缩库存大多数物品库存过多伴以许多缺货已成为常规而非例外而且将持续一段长时间。最高管理层已把库存作为必要的弊病(甚至作为一项资产)来接受,中层经理与工人把它看作必需品而教师、顾问与其它思想家则使用库存去提出以高等数学为基础的一套理论。这种理论的基础是假设制造与分配的环境具有某些不能被改变的特征。这些特征包括:1、不准确的预测与不可靠的供应,要求成品超过预期的需求。2、不可靠的供应商与长而不确定的采购时间,使得过量的原料与外购组件成为必要。3、长的调整,不稳定的流,不良的质量,报废与返工,不完善的机床安装与设备还有墨匪菲定律,使得高水平的在制品成为必要。4、种种变化引起报废的库存。现代的方法拒绝接受这些作为不可避免的条件。原理65.干扰有计划作业的一切问题可以而且必须解决。管理层不断施加压力去减少库存是健康的。在任何公司里,“正确的”库存量比现存于许多企业中的要少而比现存于大多数企业中的要少得多。正当的步骤如下:1、设定一个要在一规定期间(例如6个月内)减少(譬如25%)的挑战性目标。2、提出投入(外购物料与生产性劳务)与产出(发货)速率指标并每月监控它们。迅速而敢作敢为地去校正偏差。3、进攻环境中问题,包括a.预测误差──缩短提前期,产品归类b.记录误差──循环盘点238第238页共238页nc.质量不好,报废与返工──消除原因d.缩短调整──工程─生产协作组e.理顺物流──控制投入,设置单元f.减少排队──主设入挨饿,加快产出4、使压缩库存成为人公司范围的计划。一切部门都有角色要担当。种类库存包括报废品都要被进攻。太经常了这种库存被认为是进步的代价;这种看法中有一点真理──扔掉某些物料可能比拖延引进一项改革更加符合实际更加经济。然而,大多数报废是可以避免的。关键是在物料变成报废品之前去识别它们,通过注意具有库存却无已计划需求的物品,自从某一特定日期后一直没有交易的物品平均使用率已下降一个特定百分数的物品中去识别出潜在的报废物料。下列手段是可用的:1、以部分或全部信贷方式把物品返回给供应商2、把物品应用在新设计中作为暂用品或永久性用品3、重新加工物品到可使用状态4、报废该物品原理66.只有通过找出并解决过剩的原因才能显著地削减库存。缩短提前期没有比开发越来越短的提前期更重要的工作要去做的。这捉看法同制造作业中许多人所持的看法相反;他们俱有更多时间将确保更好的绩效。他们的经验通常支持这种信念:缺货需更长时间去克服,过多的负荷要用更多时间去处理,而延误是时间不够的证明。削减提前期已被证明是可能的、比较容易的而且最为有效的,将首先要求克服这些谬论。一项有效的计划是:1、准备人员:a.谁?直线制造、制造计划与控制、设计与制造工程师、经理b.怎么办?用厂外与厂内课程进行教育2、选择工作中心a.具有长而不稳定的提前期并供应着大量产品的供应商b.具有大量书面订单积压而且处理着显著数量工作的首当开始作业c.具有不稳定负荷与高水平在制品的二次性作业3、设计更短的调整:a.模块式机床安装b.具有相似调整的产品成系列地运行c.重新设计工作站,设备d.训练调整人员4、实施投入/产出控制a.有计划的排队长度b.开发粗略CRP,改进到设定投入/产出速率c.紧紧地管理能力5、使物料保持运动6、顶住非难但忠于信仰238第238页共238页n制造控制的未来制造控制原先是一种文书工作职能:维护库存与订单记录,发放车间订单与处理其它必要的记录保管职能。从那里它发展到包括存货催促与一些部门的机器负荷计划──但大多数技法是粗糙的而功能高度分散,直到许多公司把库存控制从生产控制分离出来。分散化是大多数公司试图用来解决规模扩大与复杂性与上升问题的办法。虽然它带来某些改进,它也引进自己的问题(诸如工作重复与相当的次优化),因为每个小组倾向去考虑它自身的有限目标而不是公司的总体目标。髭公司甚至走到工厂里每一主要制造区都有单独的生产控制职能。这一朝着分散化的倾向使控制问题复杂化,因为它使得要让财务、制造与销售经理们朝着共同目标一道工作的任务更加困难了。有三个主要的发展:运筹学,也叫管理科学;计算机,提供经济地处理所涉及的大量数据的手段;与APICS,为实际工作者提供开发与交换知识的手段,其结果是随着切实可行的技法与实施它们的手段的广为人知在不到三十年的时间内已发生了一场革命。在1960年代里,实际工作者寻找安全存货的正确数量以便在一个极其敌对的环境里针对需求中的变化与供应中的不确定性去缓冲作业。他们为有统计技法去更新预测与重新评价所需的缓冲库存量而感到高兴。在1970年代,人们弄清了即使需求有变化有效的日程计划也是可能的而且可以使用及时更新的优先级去改变补货提前期使急需的物品按时。强有力的MRP技法使这成为可能并在实际工作者的思想与行动中超过了所有其它技法。在1970年代这十年里,所有需要的技法都开发出来并经过了试验。未来将只是改进。在1980年代初,人们弄清了在最复杂的系统中所有的技法在大多数制造工厂的混乱环境里实际上是无能为力的。人们认识到了对短提前期有迫切的需要并在成功的公司里开始认真地去减少记录误差,提高质量、缩小批量并理顺工厂里的物流。实际成就虽然多有斑点,都是引人注目的。在1970年代里人们识别出了一个完整系统的要素,但少有公司为他们自己开发出了完整的系统。对少数技法的偏见──MRP与每日调度──造成了支离破碎的系统,大多数缺乏能力计划与控制。这类系统的有效使用由于与财务、工程技术、采购与质量控制系统缺乏一体化而进一步受到困扰。这可以由一体化程序的网络中使用的小型或微型计算机来克服而且正在逐步克服。计算机硬件和软件的技术与经济在未来将支持这一体化工作。然而,随着环境被扫除与提前期被缩短,趋势将是朝着更简单、较不复杂的系统。现代制造控制已创造出一个有组织的知识主体,它可以从那些曾经证实过现代技法的实际应用的实际工作者经过教师、顾问与APICS传授给需要它们的人。许多早期的进展是在技法的开发方面,只是到了后来它们才成功地互相关联起来或同具体的应用关联起来。一个能被立即传授而实用的知识主体的开发对科学技法的进一步使用开发提供了最好的鼓励。这些统计学的与数学的技法(排队论,线性规划、数学的日程计划安排法)最多也只好比是细调谐装置,它们只有在控制的真正基础在位并有效地动作之后者有用的。对改进的制造控制的要求也已创造出对合格人员,即对懂得该知识主体、熟悉这些技法的长处与短处并知道如何在他的公司中去应用它们的专业人员日益增长的需求。优良的教育计划已在学术界、顾问的课程、公司内部计划与APICS研讨238第238页共238页n会中扩散。APICS证书将继续成长作为雇佣与在此领域中持有管理级别的一种条件。使得取得与保有胜任人员的问题复合起来的是由于管理层承认这一领域开发一名经理的眼力与对企业各主要部门的理解,而且许多成功的实际工作者将被提升到管理的更高层次。新的组织形式将继续出现。一种强有力的趋势将继续去结合会计库存控制功能的努力,因为它们基本上处理同样的信息而且都是管理控制最关心的办公职能。这样一种探索的问题与带来的好处在建立标准成本系统的公司里表现出来。典型情况是设计与建立标准成本系统是由财务部门发起的而且遭受续生的问题。几乎每一年,由于系统中数据有误差必须作出重大的库存调整。如果物料经理在计划与控制生产时也使用该标准成本数据,该系统问题会更加成功;当不起作用的数据每天被使用时缺点会很快地暴露出来。在源头发现错误避免了根据不正确的数据去作决定并防止了在错误发生之后很久再浪费时间去追查错误的原因。将继续加大努力去产生决策所需的成本数据,而不只是为了记帐与记录历史。毫无疑问,过去曾经使管理层重视制造控制的同样一些影响将使制造控制在将来变得日益重要。产品的复杂性与品种将继续剧增同时要求平整生产的压力将空前地加强。大多数公司必须继续削减库存以便解放稀少、昂贵的资金用于其它有利可图的机会。首要的是,来自车内外企业为更好的客户服务的竞争压力将加强。本领域提供增加利润的最丰腴土壤与增强针对竞争的市场渗透力的基础。改善必须是持久的而不是孤立而断续的刺激。毫无疑问,制造控制领域上最大的影响将来自日益增长的职业化,更好的教育与现代一体化系统的更广泛应用。传统的组织形式将继续激烈地改变。委派给每一小组的主要角色将根据需要作修改以产生一个好的工作班了而不是过去常见的全明星集全合。物料部门将消失,让位给一个承认其功能将同等地关心金钱、机器与人员的部门。该职能部门的名称是将要的──不管它叫什么,去管理一个面临强烈竞争的制造作业所需的基本信息对每家公司将变得越来越不可缺少。这一计划与控制功能不仅在公司的动作中将变得更加重要,而且将成为高层管理人员不可缺少的培训领域。最高层经理必须学会如何去经营制造公司以及如何在金融市场中去操纵它们。对这些事实日益增长的意识,加上强烈的外车的竞争与不断的尖锐衰退,使人们更加重视计划工作析更加一体化与计划的执行要更加有效。这两个主题概括了这两本羽的大部分内容。表现出由于善于做这些作业控制而获得报酬的成功的公司已给兴趣之火加了油。制造业(同农业与采掘工业一道)作为真正财富创造者的重要性在经理们身上加了一付责任的重担,要求他们用这个知识为他们公司与国家而且并非附带一为他们自己谋取最大的利益。238第238页共238页查看更多