- 2022-04-22 发布 |
- 37.5 KB |
- 53页
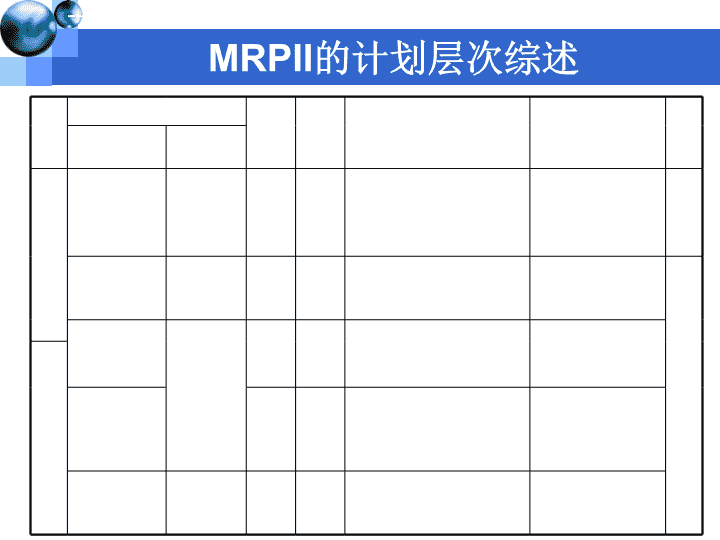
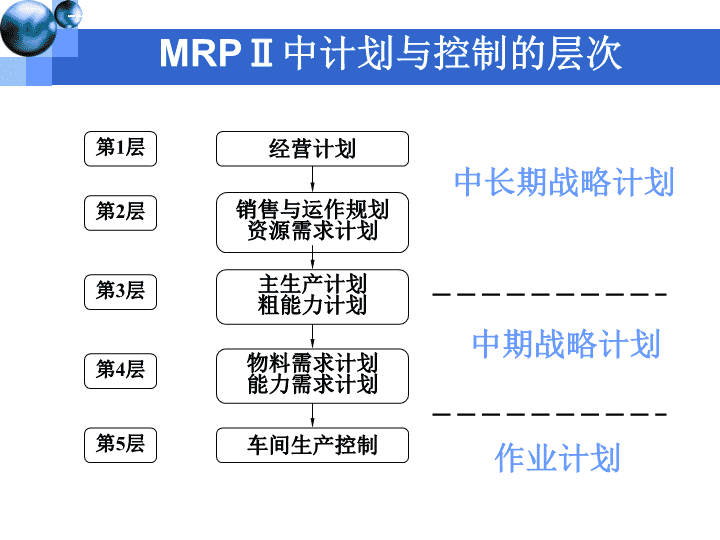
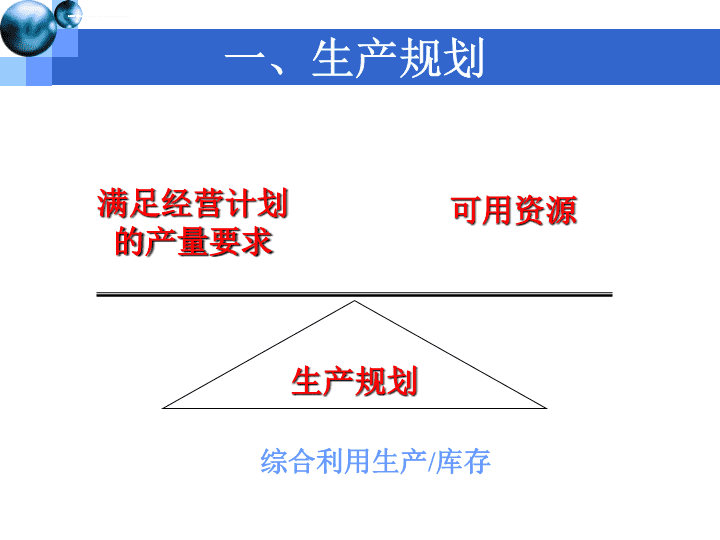
申明敬告: 本站不保证该用户上传的文档完整性,不预览、不比对内容而直接下载产生的反悔问题本站不予受理。
文档介绍
企业资源计划(ERP)---计划方法ppt课件
MRPII的计划层次综述nMRPⅡ中计划与控制的层次经营计划销售与运作规划资源需求计划主生产计划粗能力计划物料需求计划能力需求计划车间生产控制第1层第2层第3层第4层第5层中长期战略计划中期战略计划作业计划n一、生产规划满足经营计划的产量要求可用资源生产规划综合利用生产/库存n制定生产规划主要需考虑策略规划目标(生产率、控制库存量、控制拖欠量等)制定规划的组织安排计划展望期计划周期对产品类别进行合理划分计划审查频率一、生产规划n收集经营计划的相关信息编制生产规划初稿否是编制资源需求计划协调可用资源与资源需求确定生产规划可用资源与需求资源平衡否步骤1步骤2步骤3步骤4步骤5一、生产规划n计划大纲的编制步骤1-收集信息计划:销售目标、库存目标(以金额表示)市场:产品类销售预测(以数量表示)分销、运输要求工程:资源清单、专用设备要求生产:资源可用性(劳力、机时、工时)当前库存水平(MTS)当前未完成订单(MTO)财务:单位产品成本、收入、资金可用性、增加资源的财力等一、生产规划n计划大纲的编制步骤2-制订大纲初稿(MTS)把预测分布在计划展望期的每一时区上(如预测针对每一时区,则直接使用)计算期初库存(当前库存-拖期订单)计算库存水平的改变(目标库存-期初库存)计算生产总需求(预测量+库存改变)把总生产需求与库存改变分布在计划展望期的每一时区上一、生产规划n例:某工厂对自行车类编制生产规划,计划展望期为一年,按月划分时区,年末库存目标是100辆,当前实际库存是500辆,拖期订单数量(应发数量)300辆,自行车年销售预测1200辆。一、生产规划n把年预测销售量1200辆按月平均分布,计算出月销售量100辆按公式期初库存=当前库存-拖期订单计算期初库存=500-300=200按公式库存变化=目标库存-期初库存计算库存水平变化(正为增,副为减)100-200=-100预测量+库存改变=计划期内总产量1200+(-100)=1100把总产量按时区分布到整个计划展望期,表现出各时区的库存变化,要求期末库存必须与库存目标一致,则计划大纲初稿如下解:一、生产规划n预计库存的计算:第K+1时区预计库存=第K时区预计库存+第K+1时区生产大纲量-第k+1时区销售预测(K=0,1,…)第0时区预计库存=期初库存一、生产规划n计划大纲的编制步骤2(MTO)同MTS按交货期把未完成订单数量分布在计划展望期的相应时区内计算未完成订单的改变量。公式为未完成订单变化=期末未完成订单数量-当前未完成订单数量未完成订单减少,变化量为副,反之为正计算总生产量=计划展望期内预测量-未完成订单变化把总生产量分布到计划展望期的每一时区上。(分布时应满足预测和未完成订单的目标,时区产量至少满足本时区的未完成订单量。)一、生产规划n例:某工厂对自行车类编制生产规划,计划展望期为一年,年销售预测1200辆。按月划分时区,期末未完成订单数量300辆,当前未完成订单420辆,分布如下:一月:90二月:90三月:70四月:60五月:50六月:30七月:30一、生产规划n把年销售预测按月平均分布,计算出月销售量100辆未完成订单分布如下:(见下页)未完成订单变化=300-420=-120总产量=1200-(-120)=1320辆把总产量分布到各月,则计划大纲初稿如下解:一、生产规划n预计未完成订单的计算:第K+1时区预计未完订订单量=第K时区预计未完成订单量+第K+1时区销售预测量-第K+1时区生产大纲量第0时区预计未完成订单量=期初未完成订单量一、生产规划n计划大纲的编制步骤3-确定资源需求分析资源清单计算资源需求-各类产品总生产量与单位需求量相乘-对于共享资源,则汇总所有产品类的需求比较可用资源与资源需求协调可用资源与资源需求一、生产规划n资源清单:计算钢需求量产品类自行车四轮车三轮车计划生产量(辆)1200x500x1000x单位需求量(吨)0.0051=0.0047=0.0029=总需求量(吨)6.122.352.90计算工时需求产品类自行车四轮车三轮车计划生产量(辆)1200x500x1000x单位需求量(时)0.63=0.24=0.39=总需求量(时)756120390总量11.4吨总量1266小时一、生产规划n计划大纲的编制步骤4比较资源需求与可用资源,进行合理平衡:加工工作中心任务替代或调整产品类别调整必要时可以通过增加可用资源以满足资源需求,同时也可以通过减少需求或者进行资源外取的方式平衡资源需求与现实可用资源之间的关系。物料短缺时:增加物料购买、减少生产总量、采用其它供应来源、采用替换原料等劳动力短缺时:加班、雇临时工、外包、减产、自动化扩大生产能力。。。设备短缺:购置、升级、优化、外包、减产等一、生产规划n二.主生产计划主生产计划(masterproductionschedule,简称MPS),是对企业生产计划大纲的细化,是指确定每一个具体产品在每一个具体时间段的生产计划。计划的对象一般是最终产品,即企业的销售产品。MPS中计划的产品由具体、特定的BOM来描述;主生产计划是对最终项目的供应描述主生产计划用来控制MRP系统中所有的其他计划n计划大纲的编制步骤5生产规划定稿经过优化平衡之后,确定生产规划,在生产规划的计划展望期内,生产规划对内部供应链的相关部门有着重要的指导意义。生产规划审批统一经营目标、协同行动并取得相关部门的支持。同时也提供了一个考核相关业务领域工作绩效的依据。一、生产规划n1.作用与意义客户需求稳定的主生产计划二.主生产计划n生产需求(生产规划)可用资源主生产计划主生产计划把企业规划与日常的生产作业计划联系起来,是日常管理的“控制把手”二.主生产计划n2.主生产计划的编制流程业务(销售)部门制定销售计划(预测);生产部门据以编制MPS:不确定是否满足销售计划需求,若满足,向业务部门确认其销售计划;否则,要求业务部门适当修改原销售计划;销售计划和MPS匹配后,产销计划定案,据此计算ATP数据;执行:业务部门依据ATP接单,生产单位要负责完成MPS约定的产量。二.主生产计划n编制主生产计划-步骤1根据生产规划和计划清单确定对每个最终项目的生产预测。主生产计划计划矩阵初始库存量=175产品的提前期=1安全库存量=0需求时区计划时区预测时区时区12345678910生产预测200200200200200200200200200200n编制主生产计划-步骤2主生产计划计划矩阵初始库存量=175产品的提前期=1安全库存量=0需求时区计划时区预测时区时区12345678910生产预测200200200200200200200200200200增加的客户订单(非正常)0000130280000预测的客户订单(正常)198145234145167145150100340未消耗的预测(2)0(55)0(-34)2355335550100166200总需求量(毛需求)198145257200330228200200200200计算总需求n增加的客户订单(非正常):订单不是预测的一部分,也称非独立需求;预测的客户订单(正常):也称订单是预测的一部分;未消耗的预测=预测–本时区预测的客户订单–其他时区不能完全消耗的预测的客户订单总需求量:客户订单、未消耗预测和非独立需求之和,一般情况可取:实际需求=增加的客户订单(非正常)+预测的客户订单(正常)在需求时界前=实际需求(不能接受新订单)在需求时界后第一时区=实际需求+未消耗的预测+需求时区内的所有未消耗的预测在需求时界后其他时区=实际需求+未消耗的预测n编制主生产计划-步骤3计算主生产计划n计划接收量(SR:scheduledreceipts):是指前期已经下达的,目前正在执行中的订单量,将来要在该时段的产出数量.即以前计划的产出量。()中的数值为本次将要下达的主生产计划将在该时段的产出数量。预计可用量(预计库存量PAB:projectedavailablebalance):第一时区:PAB=初始库存量-已分配量+本时段计划接收量已分配量:指满足已下达正执行的MPS所需的数量。其他时区:PAB=上时段PAB+本时段计划接收量-本时段毛需求量n主生产计划(计划产出量):当预计可用量(预计库存量)小于安全库存量时,必须计划产出一定批量的该产品使预计可用量(预计库存量)大于安全库存量,从而给出一份主生产计划MPS的备选方案,MPS应兼顾:均衡生产的要求。批量的要求:MPS计划批量并非等于实际净需求量,而应采用直接批量,固定批量,固定周期,经济批量等方法确定或这些方法确定的整数倍。计划投入量:根据计划产出量、产品的提前期、产品的合格率等计算出的投入数量称为计划投入量。计划投入与计划产出的时间间距=产品的提前期n计算可承诺量(AvailabletoPromise)ATP编制主生产计划-步骤4n离散ATP:这个数据用于支持客户订单承诺。它告诉市场和销售部门,在不改变主生产计划的前提下还可以满足多少客户需求。第一个时区:ATP等于初始库存量加上计划接收量再减去下一次出现主生产计划之前的所有时区中未交付的实际需求量;其他时区:无计划产出量则ATP等于0;有计划产出量则ATP等于该计划产出量减去下一次出现主生产计划之前的所有时区中未交付的实际需求量。nATP:从计划展望区的最后一个时区开始计算:无计划产出量则ATP等于0,实际需求量从前面时区的计划产出量中扣除;有计划产出量则ATP等于该时区计划产出量扣除为后面时区的保留部分,然再后减去该时区实际需求量,不足部分从前面时区的计划产出量中扣除。向前看的累计ATP:从最早时区开始,把各个时区的ATP累加到所考虑的时区即是这个时区的向前看的累计ATP。n用粗能力计划评价主生产计划备选方案的可行性,模拟选优,给出主生产计划报告。编制主生产计划-步骤5主生产计划的维护需求时界:在需求时界之前,主计划员不能改变计划时界:在计划时界之前,由主计划员对主生产计划进行手工维护,在计划时界之后,由MRP系统自动维护在自动维护时:主计划员不对主生产计划进行控制n主生产计划典型报表格式n三、物料需求计划(MRP)的制定MRP的工作原理是:根据产品的生产量,自动地计算出构成这些产品的零部件与材料的需求量及时间;根据物料需求的时间和生产(订货)周期确定各零部件的生产订货时间。(1)主生产计划(3)实际库存量(2)物料清单BOM生产计划(4)物料需求计划建议的采购计划nBOM(物料清单)模块BOM是定义产品结构的技术文件,也被称为产品结构表或产品明细表。BOM描述了构成父项装配件的所有子装配件、零件和原材料之间的结构关系,是制造一个装配件所需每种零部件数量的清单。自行车的BOM结构图三、物料需求计划(MRP)的制定n相关概念物品代码:A00901计划员:LH计划日期:2004/3/27物品名称:VCD333解码板型号/规格:XS1现有量:10安全库存:5分配量:5批量规则:固定批量批量:10提前期:7天三、物料需求计划(MRP)的制定n现有库存量:是指在企业仓库中实际存放的物料的可用库存数量。计划收到量(在途量):是指根据正在执行中的采购订单或生产订单,在未来某个时段物料将要入库或将要完成的数量。已分配量:是指尚保存在仓库中但已被分配掉的物料数量。提前期:是指执行某项任务由开始到完成所消耗的时间。订购(生产)批量:在某个时段内向供应商订购或要求生产部门生产某种物料的数量。安全库存量:为了预防需求或供应方面的不可预测的波动,在仓库中经常应保持最低库存数量作为安全库存量。毛需求量:是指初步的需求数量;净需求量:即实际需要的数量,要综合毛需求量和安全库存量;净需求量=毛需求量+已分配量-计划收到量-现有库存量三、物料需求计划(MRP)的制定nMRP报表运算示例假定X与Y两种产品已经过主生产计划推算出计划投入量和产出量,其余所含物料的提前期、批量、安全库存、现有量、已分配量等均为已知。三、物料需求计划(MRP)的制定n例1:推算毛需求。在时段2,Y的计划产出量为10,由于Y的提前期为1,所以在第1时段Y的计划投入量为10,引发在时段1对C的毛需求量为30,对E的毛需求量为20。三、物料需求计划(MRP)的制定n例2:推算毛需求。推算X对A、B的投入需求。三、物料需求计划(MRP)的制定n例3:推算A的PAB初值(考虑毛需求、初始库存、计划接收量)、净需求量、计划产出量(考虑批量)、计划投入量(考虑提前期)、预计可用库存量。三、物料需求计划(MRP)的制定n例4:推算A对C的毛需求。三、物料需求计划(MRP)的制定n例5:推算X、Y对C的总毛需求。三、物料需求计划(MRP)的制定n例6:推算C的PAB初值、净需求、计划产出量、计划投入量、预计库存量。三、物料需求计划(MRP)的制定n假设产品P由2个单位A及1个单位B制成;A由1个单位C和2个单位D制成;D由3个单位E制成。各种物料的提前期均为1周。产品P的需求量如计划表中所示。假设各种物料目前没有库存;批量按照直接批量原则。要求:(1)试画出产品结构图;(2)补充完成MRP计划表。MRP报表运算示例2三、物料需求计划(MRP)的制定n三、物料需求计划(MRP)的制定n三、物料需求计划(MRP)的制定n四、能力需求计划制定方法能力需求计划(CRP)即细能力需求计划,是对具体物料需求计划所需能力进行核算的一种计划管理方法。·生产什么?何时生产?;·使用什么工作中心?需用能力是多少?·工作中心的可用能力是多少·分时段的能力需求情况如何?n物料需求计划的对象是物料,能力需求计划(CapacityRequirementsPlanning,CRP)的对象是能力。CRP把MRP的物料数量转换为标准负荷小时,把物料需求转换为能力需求。能力需求规划步骤:(1)分解产品物料需求,进行MRP规划;(2)编制工作中心能力需求①计算每个工作中心上每道工序的负荷;②计算每个工作中心的可用能力工作中心每天可用工时=每天工时×操作人数×效率×利用率③计算每个工作中心对各负荷的加工天数(小时->天)④计算每道工序的开工日期和完工日期⑤按时间周期计算每个工作中心的负荷(3)编制能力负荷图;(4)能力分析与控制。四、能力需求计划制定方法n(1)已下达订单:已释放或正在加工的订单。包括每种零部件的数量、交货期、加工工序、准备时间和加工时间、工作中心号或部门号及设备号等;(2)MRP计划订单:是MRP输出的尚未释放的订单,MRP计划订单将占有工作中心的负荷;(3)工艺路线文件:主要信息有加工工序描述、工序顺序、替换工序、工具、定额工时(准备时间+加工时间);(4)工作中心文件:包括排队时间(工件等待加工的平均时间)、运输时间(把工件从一个工序搬到另一个工序所需的时间);四、能力需求计划制定方法n编制工作中心负荷报告分为两步:编制工序计划、对工作中心按时区累计负荷例:部件A订单订货量是60,交货期是工厂日历第420天(从订单文件获得),且部件A需要在两个工作中心上加工两道工序(从工艺路线文件中获得),如表所示:已知1号工作中心的排队时间和传送时间均为1天,2号工作中心的排队时间和传送时间分别为2天和1天。(从工作中心文件中获得)四、能力需求计划制定方法n(1)求解每个加工中心上每道工序的负荷?工序10——工作中心1:加工时间+准备时间=1×60+12=72小时工序20——工作中心2:加工时间+准备时间=0.5×60+6=36小时(2)求解每道工序的交货日期和开工日期?工作中心每天可用工时=每天计划工时×工作中心利用率×效率=8×0.85×0.88=6(标准工时/天)工序10:加工时间(天)=60(标准工时)/6(标准工时/天)=10天准备时间(天)=12(标准工时)/6(标准工时/天)=2天工序20:加工时间(天)=30(标准工时)/6(标准工时/天)=5天准备时间(天)=6(标准工时)/6(标准工时/天)=1天四、能力需求计划制定方法n该例以第420天作为“工序20”的完工日期,减去传送、加工、准备和排队时间得到抵达工作中心2的日期是第411天,这时,第411天就成为“工序10”的计划交货日期。四、能力需求计划制定方法查看更多