- 2022-04-22 发布 |
- 37.5 KB |
- 26页
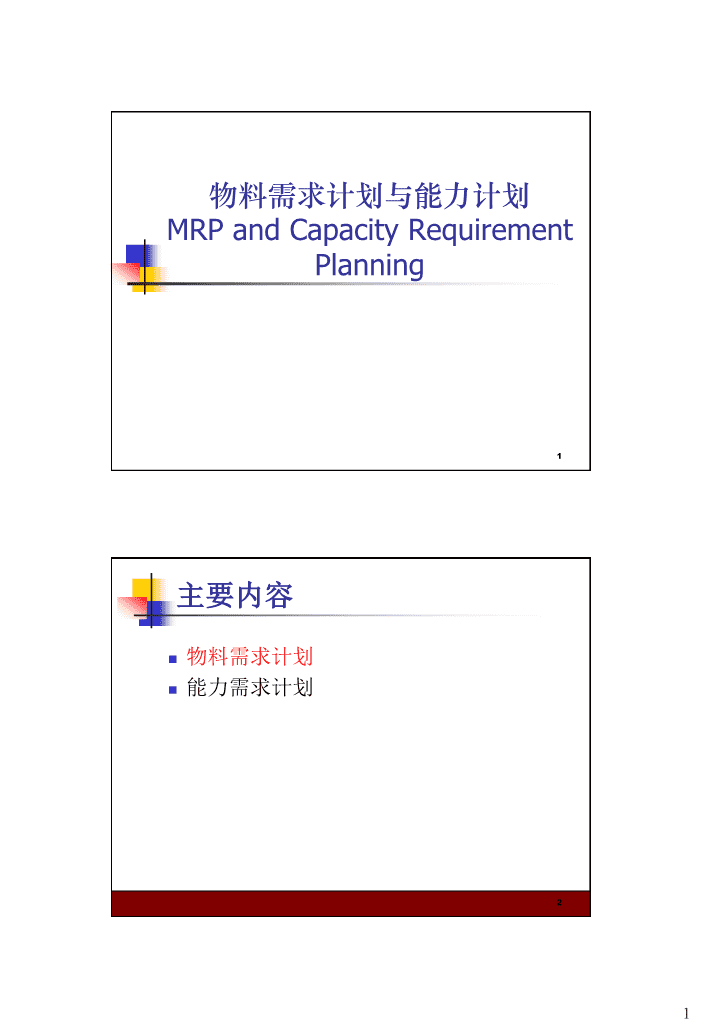
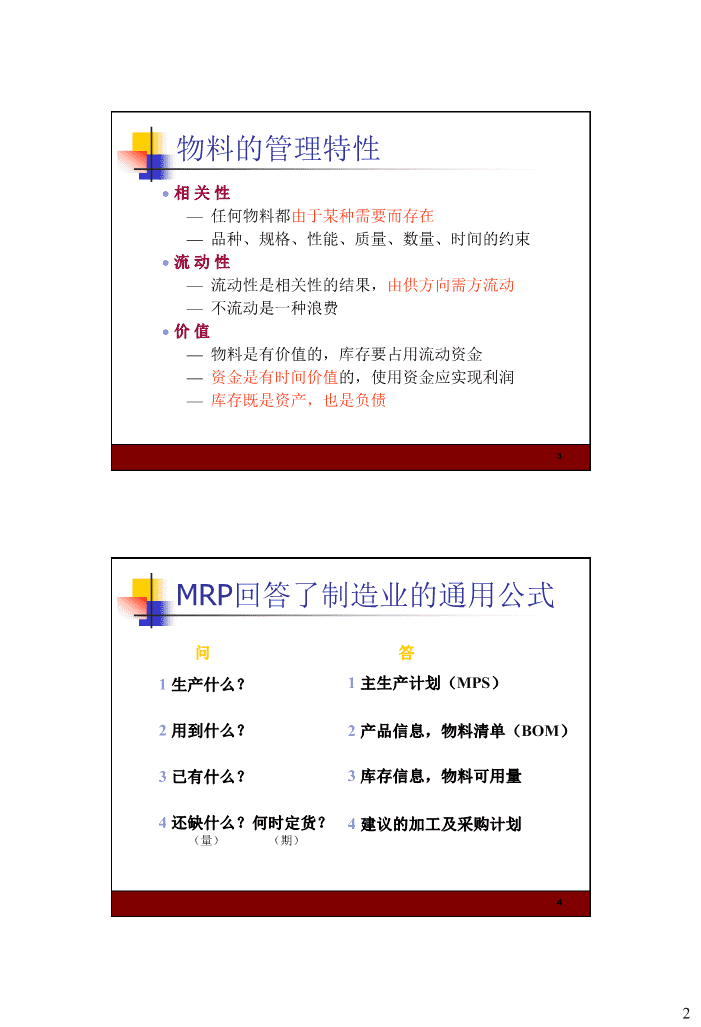
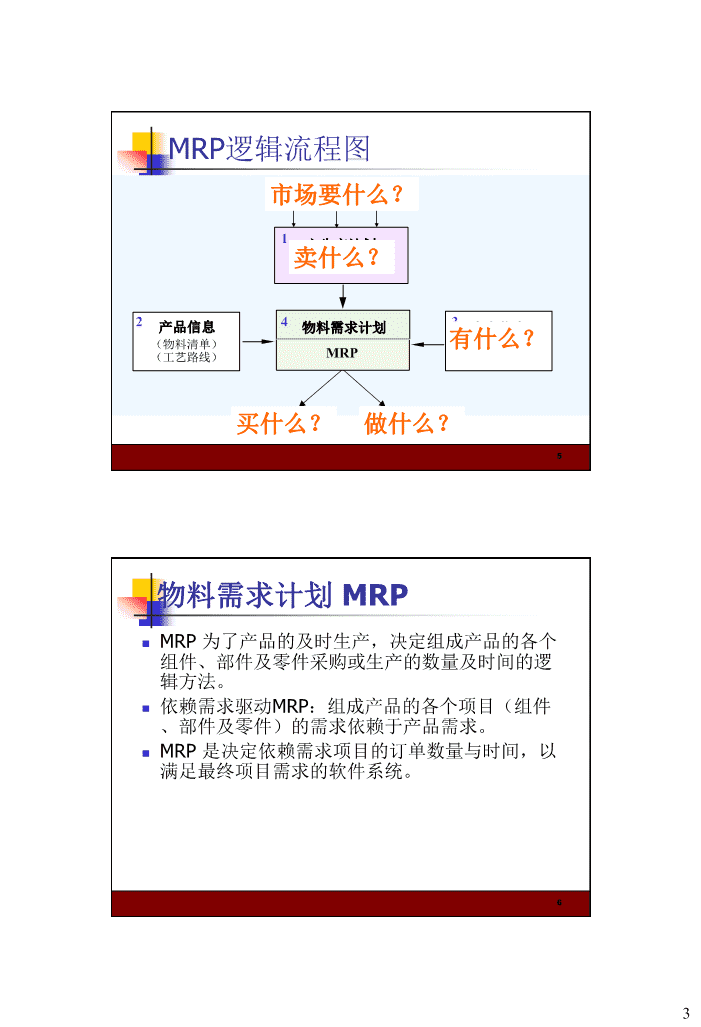
申明敬告: 本站不保证该用户上传的文档完整性,不预览、不比对内容而直接下载产生的反悔问题本站不予受理。
文档介绍
物料需求计划与能力计划
物料需求计划与能力计划MRPandCapacityRequirementPlanning1主要内容物料需求计划能力需求计划21n物料的管理特性相关性—任何物料都由于某种需要而存在—品种、规格、性能、质量、数量、时间的约束流动性—流动性是相关性的结果,由供方向需方流动—不流动是一种浪费价值—物料是有价值的,库存要占用流动资金—资金是有时间价值的,使用资金应实现利润—库存既是资产,也是负债3MRP回答了制造业的通用公式问答1生产什么?1主生产计划(MPS)2用到什么?2产品信息,物料清单(BOM)3已有什么?3库存信息,物料可用量4还缺什么?何时定货?4建议的加工及采购计划(量)(期)42nMRP逻辑流程图潜在市场要什么?预测客户合同1主生产计划卖什么?MPS243产品信息物料需求计划库存信息(物料清单)有什么?MRP(物料可用量)(工艺路线)采购计划生产计划买什么?做什么?5物料需求计划MRPMRP为了产品的及时生产,决定组成产品的各个组件、部件及零件采购或生产的数量及时间的逻辑方法。依赖需求驱动MRP:组成产品的各个项目(组件、部件及零件)的需求依赖于产品需求。MRP是决定依赖需求项目的订单数量与时间,以满足最终项目需求的软件系统。63nMRP概览MRP的输入MRP过程MRP的输出变更订货免除定单总进度订货计划预测计划时间安排MRP计算机例外报告设计变更物料清单程序计划报告业绩控制报告收货存货记录文件提取存货处理7制定MRP依据的关键信息(1)主生产计划(MPS)。物料需求计划由MPS推动。(2)物料清单(BOM)。由于最终产品结构中的各个子件加工周期不同,即对同一BOM(同一产品)中的物料需求时间不同,因此,MRP要根据产品的BOM对MPS进行需求展开(数量与提前期)。(3)库存信息。依据物料库存信息确定各个物料的需求量。84n物料清单物料清单(BillofMaterials,BOM)是指产品所需零部件明细表及其结构。它表明了产品→部件→组件→零件→原材料之间的结构关系,以及每个组装件所包含的下属部件(或零件)的数量和提前期(LT)。一个BOM文件,至少应包括3个数据项:物料标识(或物料编码)、需求量(每一个父项所需该子项的数量)、该物料的提前期。9产品结构树10000结构层次X独立需求件方桌0件1.0相关需求件销110001200013000产1桌面A桌腿BE螺钉胶油漆供件1.0件4.0套1.0111001120012100面C框DR方木22件1.0件4.0m30.21111011210板材OP方木13m21.0m30.2105n独立需求与非独立需求当细项需求来自特定产品制造计划时,涉及其间的原材料、零部件、用于生产产成品的组件等细项被认为具备非独立需求。独立需求一旦随季节变化达到定量供应,就会相对稳定下来;而非独立需求则趋于偶发性或“成块”性。独立需求细项必须经常持有,而非独立需求细项只要在生产过程使用它之前存好即可。11独立需求非独立需求126n提前期前处理提前期处理提前期总装配后处理提前期子装配材料采购累计制造提前期累计总提前期13物料清单(BOM)的基本内容物料号:10000计量单位:件批量:10现有量:8物料名称:X分类码:08提前期:2累计提前期:2823物料计量累计ABC层次物料号数量类型生效日期失效日期成品率名称单位提前期码111000A件1.0M19990101999999991.0026.0A.211100C件1.0M19990101999999991.0015.0A..311110Om21.0B19990101999999990.9012.0B.211200D件4.0M19990101999999991.0022.0C....311210/1311210PP1m30.20.2B20000101999999991.0015.0CB19990101199912310.9020.0C112000B件4.0M19990101999999991.0017.0B.212100Rm30.2B19990101999999991.0010.0C1.13000E1.0B19990101999999991.005.0C套147n交货日期(2)X时时间坐标上的间ABE产品结构5(4)(5)(7)CD(2)(3)P10OR(10)(12)(15)15202515简单的MRP举例已知产品A的产品结构树(productstructuretree)、提前期(leadtime)、需求信息如下。试制订一个物料需求计划。提前期LT:A1天B2天AC1天D3天E4天B(4)C(2)F1天需求量:D(2)E(1)D(3)F(2)第10天50A第8天20B(备件)第6天15D(备件)168n简单的MRP举例求解:1、各组件的依赖需求数量;需求量:A50第10天50A第8天20B(备件)备件2050*4=20050*2=100第6天15D(备件)B(4)C(2)4020D(2)E(1)D(3)F(2)200*2=400200*1=200100*3=300100*2=200备件1517简单的MRP举例2、考虑提前期,列出产品A的需求提前期LT:数量与订货数量。A1天B2天需求量:C1天第10天50AD3天第8天20B(备件)E4天第6天15D(备件)F1天时间段(天)12345678910A需求量50订购量50LT=1天189n3、安排组成A的低一层组件的需求时间(依赖于A的订货时间)与订货时间(考虑提前期)。时间段(天)12345678910A需求量50订货量50B需求量20200订货量20200需求量:第8天20B(备件)A50备件20提前期LT:50*4=20050*2=100B2天B(4)C(2)4020D(2)E(1)D(3)F(2)200*2=400200*1=200100*3=300100*2=200194、依次向下层进行A50备件20提前期LT:200100需求量:A1天B(4)C(2)第10天50AB2天第8天20B(备件)C1天第6天15D(备件)D3天D(2)E(1)D(3)F(2)E4天4040020200300200F1天备件15时间段(天)12345678910A需求量50LT=1订购量50B需求量20200LT=2订购量20200C需求量100LT=1订购量100D需求量55400300LT=3订购量55400300E需求量20200LT=4订购量20200F需求量200LT=1订购量2002010n物料需求计划(MRP)MRP还没有做到:执行结果为企业带来什么效益?执行结果是否符合企业总体目标?22MRPMRPIIERPERPII(2004)的扩展关系协同商务ERP(1991)EnterpriseResourcePlanning面向供需链MRPII(1980)ManufacturingResourcePlanning是发展/包罗面向企业不是取代/否定MRP(1965)MaterialRequirementsPlanning物料信息集成物料/资金信息集成需求市场/制造企业/供应市场信息集成2311nMRP,MRPII,ERP•物料需求计划(MRP)是计划物料需求的工具•制造资源计划(MRPII)计划全厂的各项资源•企业资源规划(ERP)计划整个企业(不只一个工厂)的各项资源24MRP是ERP的引擎•MRP可用来规划所有资源的未来需求•主生产计划(MPS)记录完成品的生产计划,驱动各项资源的需求。•物料表(BOM)、人力表定义完成品与物料或人力的关系,资源表定义BOM中各零件与所需设备产能的关系。•MRP利用BOM将MPS转成未来各期的物料需求,其中的自制零件再透过人力表及资源表转换成人力及设备需求。•利用MPS中的完成品总需求及MRP中的采购/外包零件计划,可算出未来各期的资金需求。2512n制造需求计划(MRPII)经营规划领导销售与运作计划销售规划财务系统基础数据决物料系统策产品规划MRPII资源清单层资源需求计划逻辑流程图应合同预测市场宏销售收可行?帐潜在客户观实现客户信息主生产计划粗能力计划企业整体效益总成本中心计划计帐会计科目可行?划资金流与物流的层库存信息信息集成物料需求计划MRP物料清单能力需求计划微财务工作中心技术生产观工艺路线可行?车间执供应商信息采购作业车间作业行应供应控付成本会计制帐成本层业绩评价26制造需求计划(MRPII)本层人工费增加本层间接费成本成本累加X低层人工费低层间接费累计低层材料费成本低层采购间接费增加本层人工费成本本层间接费低层人工费累计低层间接费材料费成本低层材料费ABE采购间接费低层采购间接费增加本层人工费成本本层间接费材料费CDR采购间接费累计低层材料费成本低层采购间接费材料费材料费OP采购间接费采购间接费2713n能力需求计划29能力计划的层次结构3014n粗略产能计划RCCP粗略产能计划Rough-CutCapacityPlanning检查主生产计划的可行性:在每一个时间段,比较工作负荷(与MPS数量联系)与现有资源能力。检查目的:保证短缺资源、关键资源不超负荷。负荷表(LoadProfile)生产单件最终项目所需的每项资源的标准总工时列表(考虑提前期的资源列表)。资源负荷表(ResourceProfile)特定时段内,生产给定数量的最终项目所需某项资源的标准总工时数。31粗略产能计划RCCP进水率:负荷在制品库存水平WIPInventory出水率:产能Capacity3215n粗略产能计划RCCP例:以产品X(由部件A与B装配而成),假定:每一批量X组装的提前期为1周,部件A提前期为1周,B为2周。求该产品的分时段负荷表与各工作中心的资源负荷表。表1产品X的工艺路线与工时表6产品X的MPS如下:标准总工时周4567项目工作中心(Hrs/Unit)MPS300400200500X装配0.6A切0.33A绞0.86A磨0.31B切0.45B铣0.72B钻0.56B磨0.4133粗略产能计划RCCP产品的分时段负荷表:后向调度(倒退)产品X的分时段负荷表(LoadProfile)标准总工时(Hrs/Unit)项目工作中心周(n-3)周(n-2)周(n-1)周(n)X装配0.6A绞0.86A磨0.31B磨0.41A切0.33B切0.45B铣0.72B钻0.563416n粗略产能计划RCCP考虑提前期的生产数量:周1234567产品X的MPS300400200500装配3004002005000.6绞A3004002005000.86磨A3004002005000.31磨B3004002005000.41切A3004002005000.33切B3004002005000.45铣B3004002005000.72钻B3004002005000.56考虑提前期的负荷工时:周1234567产品X的MPS300400200500装配180240120300绞A258344172430磨A9312462155磨B12316482205切A9913266165切B13518090225铣B216288144360钻B16822411228035粗略产能计划RCCP汇总得到各工作中心的资源负荷表。工作中心周1234567装配汇总180240120300绞汇总258344172430磨汇总123257206267155切汇总135279222291165铣汇总216288144360钻汇总168224112280总计6421306120816108703003617n能力需求计划CRPCRP检查MPS的短期能力可行性。与RCCP类似(使用BOM、工序工艺路线、作业标准时间计算资源负荷),但更详细、精确:利用MRP程序生成的POR(POR:plannedorderreleases),通过CRP模块完成计划的检查。37能力需求计划CRP能力需求计划(CapacityRequirementPlanning,简称为CRP)是对各生产阶段、各工作中心(工序)所需的各种资源进行精确计算,得出人力负荷、设备负荷等资源负荷情况,并做好生产能力与生产负荷的平衡工作,制订出能力需求计划。CRP把MRP的物料数量转化为标准负荷小时,把物料需求转化为能力需求。3818n能力需求计划CRP能力需求计划解决如下问题:各个物料经过哪些工作中心加工?各工作中心的可用能力是多少,负荷是多少?工作中心的各个时段的可用能力与负荷是多少?39能力需求计划CRP已下达和计划下达的生产订单工艺路线工作中心能力需求计划工艺路线说明对自制件的加工顺序和标准工时定额。工作中心用来说明能够生产资源,包括机器设备和人等。4019n满足能力约束的方法增加能力重排程减少生产提前期交叉工序OverlapOperations工序全部完成之前就开始向下一工序交运。分割工序SplitOperations使用多个并行的工作站完成同一工序。分割批量Splitlots分解订单,快速执行一部分订单,然后再执行另一部分41减少提前期依次作业加工提前期平行顺序作业工作中心(机床)加工提前期4220n能力需求计划分类无限能力计划无限能力计划是在作物料需求计划时不考虑生产能力的限制,而后对各个工作中心的能力、负荷进行计算得出工作中心的负荷情况,产生能力报告。当负荷>能力时,对超负荷的工作中心进行负荷调整。有限能力计划是认为工作中心的能力是有限的,计划的安排按照优先级安排,先把能力分配给优先级高的物料,当工作中心负荷已满时,优先级别低的物料被推迟加工,即订单被推迟。该方法计算出的计划可以不进行负荷与能力平衡。43CRP计算CRP的编制过程:1.数据输入工艺路线工作中心工厂日历MRP计划订单2.编制工作中心负荷报告编制工序计划:倒序排产,确定各工序的开工日期按时区累计负荷,产生负荷报告或图4421nCRP—数据输入生产物料A的工艺路线:准备和加工时间物料代码:A名称:定位栓工序工作中心描述准备时间h每件加工时间h101配件生产121201组装60.546CRP—数据输入工作中心定额能力(已知/收集):天班次班工作时数利用率效率180.850.88两工作中心的天定额能力=1*8*0.85*0.88=6h/天利用率=实际投入工时数/计划工时数效率=完成定额工时数/实际投入工时数4722nCRP—数据输入工作日历日一二三四五六生活日历1234567工作时间8.08.08.08.08.08.08.0工作日3973983994004014024038910111213148.08.08.08.08.08.08.0404405406407408409410151617181920218.08.08.08.08.08.08.0411412413414415416417222324252627288.08.08.08.08.08.08.041841942042142242342448CRP—计算MRP计划生产订单号为:47物料代码为:A数量为:60需求日期为420(工作日)下达日期为397物料A订单计算如下:工序10加工时间:60件*1h/件=60h工序20加工时间:60件*0.5h/件=30h再加上准备时间得到各工作中心的负荷:工序10负荷:60+12=72h工序20负荷:30+6=36h4923nCRP—计算编制工序计划:(1)把工作中心的负荷从工时转为工作日数工序10加工时间(天):60标准工时/6标准工时=10天准备时间(天):12标准工时/6标准工时=2天工序20加工时间(天):30标准工时/6标准工时=5天准备时间(天):6标准工时/6标准工时/天=1天50CRP—计算(2)编制工序计划:加上提前期预设各工序的开工与完工日期工序工作中心到达工作排队时间准备时间加工时间传送时间完工日期中心日期/天/天/天/天1013971210141120121514114205124nCRP—负荷报告工作中心的负荷报告时区(周)总负荷(h)12345已下达负荷工时(h)2530403530160计划负荷工时042424212138总负荷工时(h)2572827742298可用能力(h)4242424242能力负荷差异(h)17-30-40-350能力利用率(%)6017119518310052CRP—负荷图1007550可用能力42250时区5325nCRP—平衡工作中心加工物品的负荷计算如下:负荷=该物品产量×占用该工作中心的标准工时(或台时)+准备时间能力-负荷≥0,则满足加工要求,能力富余(或刚好)。能力-负荷<0,则不能满足加工要求,能力不足。54CRP—调整调整能力的方法有:加班;增加人员、设备;提高工作效率;更改工艺路线;增加外协处理等。调整负荷的方法有:修改计划;调整生产批量;推迟交货期;撤消订单;交叉作业等。5526查看更多