- 2022-04-26 发布 |
- 37.5 KB |
- 7页
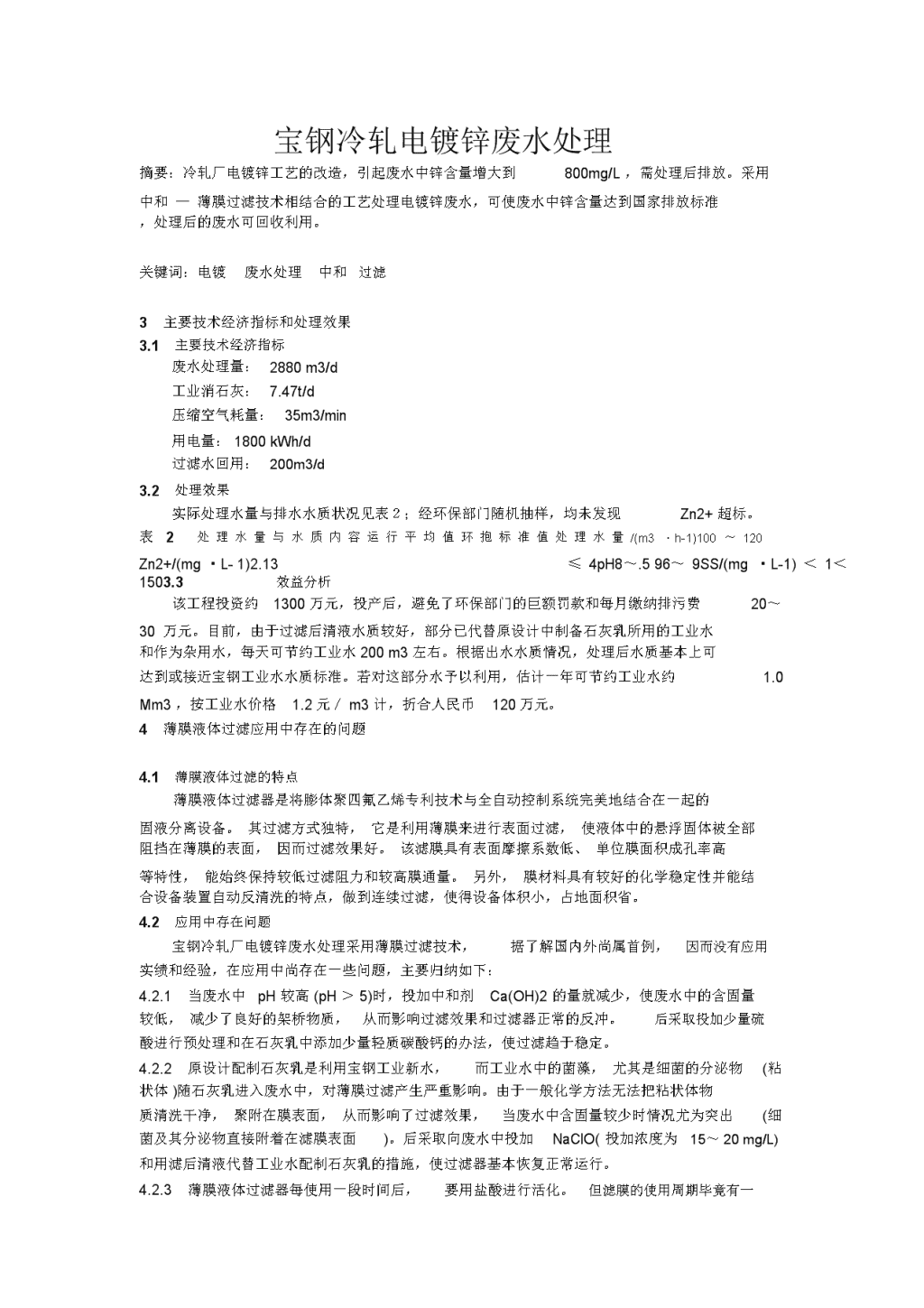
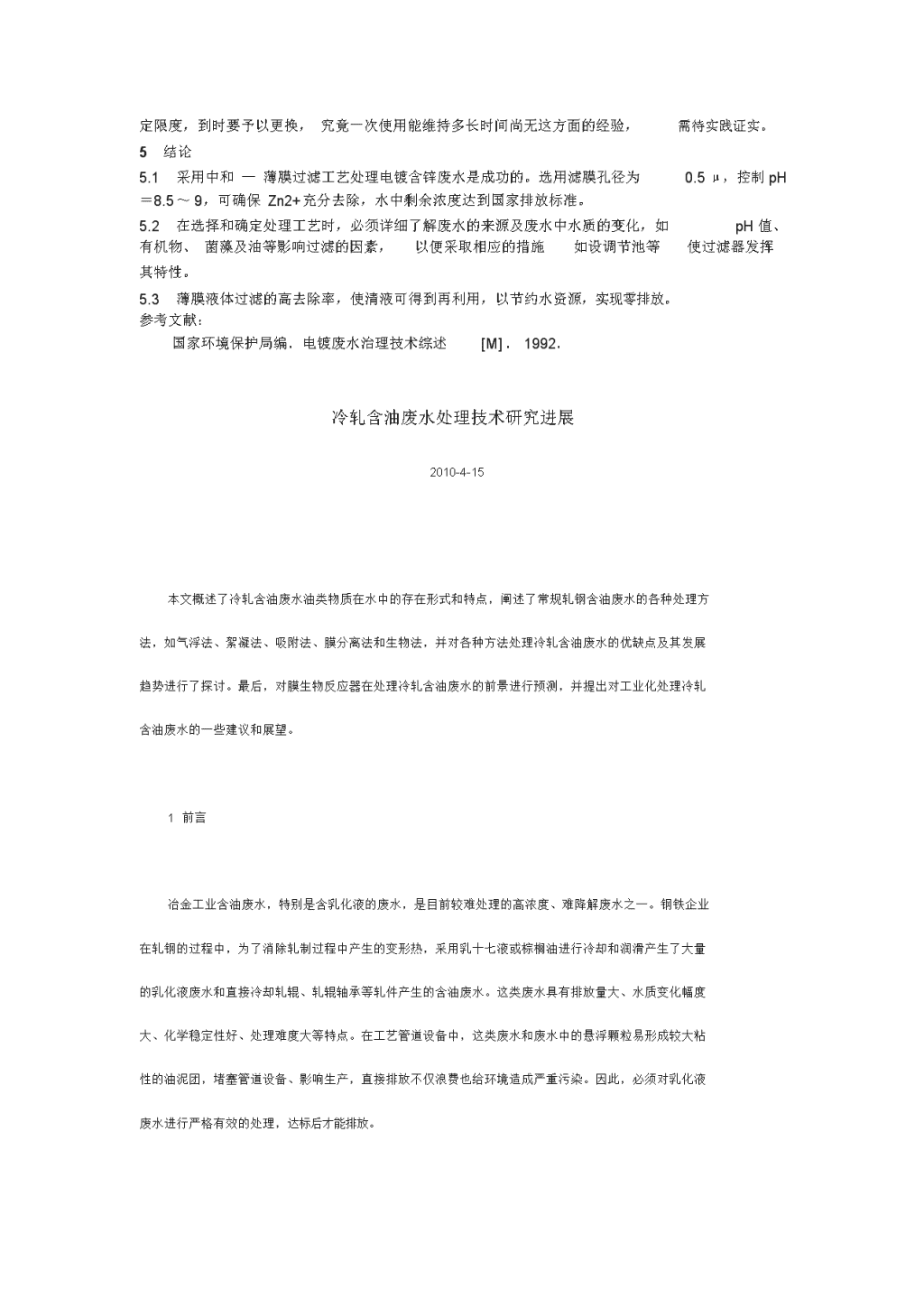
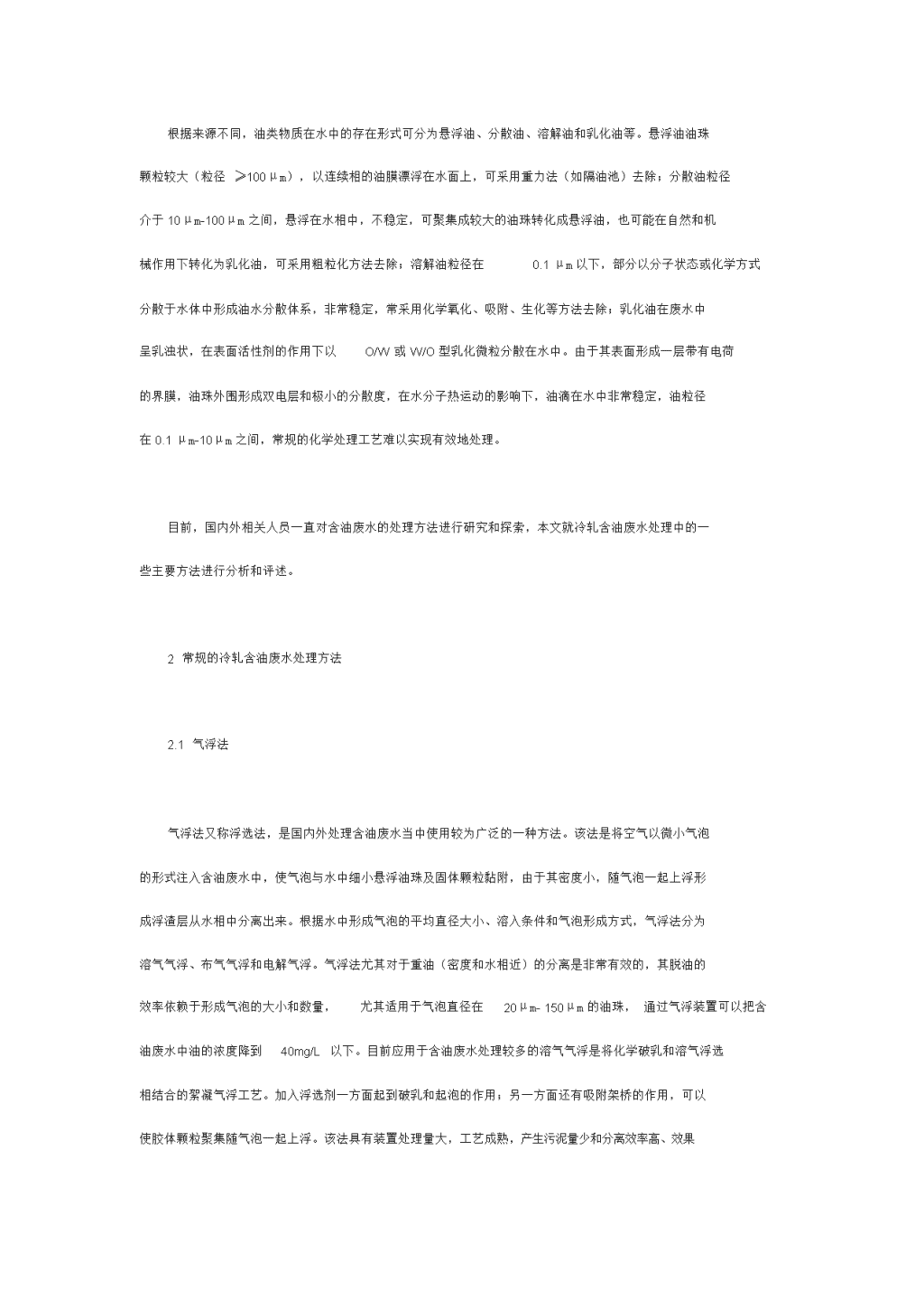
申明敬告: 本站不保证该用户上传的文档完整性,不预览、不比对内容而直接下载产生的反悔问题本站不予受理。
文档介绍
冷轧废水处理
宝钢冷轧电镀锌废水处理摘要:冷轧厂电镀锌工艺的改造,引起废水中锌含量增大到800mg/L,需处理后排放。采用中和—薄膜过滤技术相结合的工艺处理电镀锌废水,可使废水中锌含量达到国家排放标准,处理后的废水可回收利用。关键词:电镀废水处理中和过滤3主要技术经济指标和处理效果3.1主要技术经济指标废水处理量:2880m3/d工业消石灰:7.47t/d压缩空气耗量:35m3/min用电量:1800kWh/d过滤水回用:200m3/d3.2处理效果实际处理水量与排水水质状况见表2;经环保部门随机抽样,均未发现Zn2+超标。表2处理水量与水质内容运行平均值环抱标准值处理水量/(m3·h-1)100~120Zn2+/(mg·L-1)2.13≤4pH8~.596~9SS/(mg·L-1)<1<1503.3效益分析该工程投资约1300万元,投产后,避免了环保部门的巨额罚款和每月缴纳排污费20~30万元。目前,由于过滤后清液水质较好,部分已代替原设计中制备石灰乳所用的工业水和作为杂用水,每天可节约工业水200m3左右。根据出水水质情况,处理后水质基本上可达到或接近宝钢工业水水质标准。若对这部分水予以利用,估计一年可节约工业水约1.0Mm3,按工业水价格1.2元/m3计,折合人民币120万元。4薄膜液体过滤应用中存在的问题4.1薄膜液体过滤的特点薄膜液体过滤器是将膨体聚四氟乙烯专利技术与全自动控制系统完美地结合在一起的固液分离设备。其过滤方式独特,它是利用薄膜来进行表面过滤,使液体中的悬浮固体被全部阻挡在薄膜的表面,因而过滤效果好。该滤膜具有表面摩擦系数低、单位膜面积成孔率高等特性,能始终保持较低过滤阻力和较高膜通量。另外,膜材料具有较好的化学稳定性并能结合设备装置自动反清洗的特点,做到连续过滤,使得设备体积小,占地面积省。4.2应用中存在问题宝钢冷轧厂电镀锌废水处理采用薄膜过滤技术,据了解国内外尚属首例,因而没有应用实绩和经验,在应用中尚存在一些问题,主要归纳如下:4.2.1当废水中pH较高(pH>5)时,投加中和剂Ca(OH)2的量就减少,使废水中的含固量较低,减少了良好的架桥物质,从而影响过滤效果和过滤器正常的反冲。后采取投加少量硫酸进行预处理和在石灰乳中添加少量轻质碳酸钙的办法,使过滤趋于稳定。4.2.2原设计配制石灰乳是利用宝钢工业新水,而工业水中的菌藻,尤其是细菌的分泌物(粘状体)随石灰乳进入废水中,对薄膜过滤产生严重影响。由于一般化学方法无法把粘状体物质清洗干净,聚附在膜表面,从而影响了过滤效果,当废水中含固量较少时情况尤为突出(细菌及其分泌物直接附着在滤膜表面)。后采取向废水中投加NaClO(投加浓度为15~20mg/L)和用滤后清液代替工业水配制石灰乳的措施,使过滤器基本恢复正常运行。4.2.3薄膜液体过滤器每使用一段时间后,要用盐酸进行活化。但滤膜的使用周期毕竟有一n定限度,到时要予以更换,究竟一次使用能维持多长时间尚无这方面的经验,需待实践证实。5结论5.1采用中和—薄膜过滤工艺处理电镀含锌废水是成功的。选用滤膜孔径为0.5μ,控制pH=8.5~9,可确保Zn2+充分去除,水中剩余浓度达到国家排放标准。5.2在选择和确定处理工艺时,必须详细了解废水的来源及废水中水质的变化,如pH值、有机物、菌藻及油等影响过滤的因素,以便采取相应的措施如设调节池等使过滤器发挥其特性。5.3薄膜液体过滤的高去除率,使清液可得到再利用,以节约水资源,实现零排放。参考文献:国家环境保护局编.电镀废水治理技术综述[M].1992.冷轧含油废水处理技术研究进展2010-4-15本文概述了冷轧含油废水油类物质在水中的存在形式和特点,阐述了常规轧钢含油废水的各种处理方法,如气浮法、絮凝法、吸附法、膜分离法和生物法,并对各种方法处理冷轧含油废水的优缺点及其发展趋势进行了探讨。最后,对膜生物反应器在处理冷轧含油废水的前景进行预测,并提出对工业化处理冷轧含油废水的一些建议和展望。1前言冶金工业含油废水,特别是含乳化液的废水,是目前较难处理的高浓度、难降解废水之一。钢铁企业在轧钢的过程中,为了消除轧制过程中产生的变形热,采用乳十七液或棕榈油进行冷却和润滑产生了大量的乳化液废水和直接冷却轧辊、轧辊轴承等轧件产生的含油废水。这类废水具有排放量大、水质变化幅度大、化学稳定性好、处理难度大等特点。在工艺管道设备中,这类废水和废水中的悬浮颗粒易形成较大粘性的油泥团,堵塞管道设备、影响生产,直接排放不仅浪费也给环境造成严重污染。因此,必须对乳化液废水进行严格有效的处理,达标后才能排放。n根据来源不同,油类物质在水中的存在形式可分为悬浮油、分散油、溶解油和乳化油等。悬浮油油珠颗粒较大(粒径≥100μm),以连续相的油膜漂浮在水面上,可采用重力法(如隔油池)去除;分散油粒径介于10μm-100μm之间,悬浮在水相中,不稳定,可聚集成较大的油珠转化成悬浮油,也可能在自然和机械作用下转化为乳化油,可采用粗粒化方法去除;溶解油粒径在0.1μm以下,部分以分子状态或化学方式分散于水体中形成油水分散体系,非常稳定,常采用化学氧化、吸附、生化等方法去除;乳化油在废水中呈乳浊状,在表面活性剂的作用下以O/W或W/O型乳化微粒分散在水中。由于其表面形成一层带有电荷的界膜,油珠外围形成双电层和极小的分散度,在水分子热运动的影响下,油滴在水中非常稳定,油粒径在0.1μm-10μm之间,常规的化学处理工艺难以实现有效地处理。目前,国内外相关人员一直对含油废水的处理方法进行研究和探索,本文就冷轧含油废水处理中的一些主要方法进行分析和评述。2常规的冷轧含油废水处理方法2.1气浮法气浮法又称浮选法,是国内外处理含油废水当中使用较为广泛的一种方法。该法是将空气以微小气泡的形式注入含油废水中,使气泡与水中细小悬浮油珠及固体颗粒黏附,由于其密度小,随气泡一起上浮形成浮渣层从水相中分离出来。根据水中形成气泡的平均直径大小、溶入条件和气泡形成方式,气浮法分为溶气气浮、布气气浮和电解气浮。气浮法尤其对于重油(密度和水相近)的分离是非常有效的,其脱油的效率依赖于形成气泡的大小和数量,尤其适用于气泡直径在20μm-150μm的油珠,通过气浮装置可以把含油废水中油的浓度降到40mg/L以下。目前应用于含油废水处理较多的溶气气浮是将化学破乳和溶气浮选相结合的絮凝气浮工艺。加入浮选剂一方面起到破乳和起泡的作用;另一方面还有吸附架桥的作用,可以使胶体颗粒聚集随气泡一起上浮。该法具有装置处理量大,工艺成熟,产生污泥量少和分离效率高、效果n好等优点;但也存在占地面积大、药剂用量大、浮渣造成二次污染等不足之处。目前,对气浮法的研究集中在除油的机理、气浮装置的革新、改进及与其他工艺的组合上。2.2絮凝法近年来,絮凝沉降法处理含油废水及部分难以生化降解的复杂高分子有机物在国内外有广泛的报道。该方法主要根据絮凝剂类型的不同通过三种方式进行除油:一是无机盐絮凝剂的水解聚合产物能中和油污表面电荷,使其凝聚;其二是高分子絮凝剂通过其分子链的架桥作用达到分散油污间的絮凝;其三是絮凝过程产生的矾花对油污产生吸附共沉作用。工业上,为克服无机高分子絮凝剂(如聚合氯化铝)和有机絮凝剂(如聚丙烯酰胺等)的缺点,往往将两者复合投用,大大提高含油废水的除油效果。这是因为有机絮凝剂中阳离子对废水中的乳化油滴起到了电荷中和及压缩双电层的作用,促使乳化油滴进一步破乳析出,而且有机絮凝剂有很长的分子链,能在由凝聚作用形成的胶体颗粒间进行架桥,形成大而坚韧的絮凝体,从而改善絮凝体性能。由于轧钢含油废水中存在较多的氧化铁皮微粒,可将膜技术、气浮技术、磁技术等和絮凝技术结合发展起来处理轧钢含油废水。该技术存在药剂消耗大、运行费用昂贵、处理后的废水含油量、COD难以达标等缺点。2.3吸附法吸附法是利用多孔、比表面积很大的吸附剂对废水中的溶解油和其他溶解性有机物进行物理性作用力吸附(如范德华力)、化学性吸附(如化学键)和静电吸附,从而达到油水分离的目的。常用的吸附剂有活性炭、泥炭、活化矾土、褐煤、高分子聚合物和吸附树脂等。目前,吸附法中应用最多的吸附剂是活性炭,但由于活性炭吸附容量有限,常与絮凝等工艺组合,用于轧钢含油废水的处理。因此,开发出具有吸附容量大、吸附速度快、回收容易、吸油效率高、保油性能好、经济的吸附材料是吸附法能否得以广泛应用的关键。n2.4膜分离法膜法是利用液—液分散体系中的两相与固体膜表面亲和力的不同,通过外界的作用力以物理截留的方式达到分离目的。目前,文献报道较多的膜分离有微滤、超滤和纳滤,三者均靠膜两侧压力差为推动力,根据分离膜截留分子量截留废水中的乳化油和溶解油。张国胜等采用0.2μm氧化锆无机膜处理钢铁厂冷轧乳化液废水,通过对操作参数和处理过程的优化,膜通量100L/(m2.h),含油质量浓度从5000mg/L降至10mg/L以下,截留率大于99%,渗透液中油的质量分数小于0.001%,成功用于工业化。随着膜处理技术的成熟,工业上将膜分离技术(如超滤、反渗透)与常规处理方法进行组合。邯钢冷轧废水处理站采用了高性能磁力滚式纸袋过滤机+无机陶瓷膜超滤系统+接触生物氧化+斜板沉淀+活性炭过滤工艺,有效地解决了油脂类分子与水分子的分离,有机物、COD的降解,悬浮物的沉淀,取得良好效果。因此,随着更耐高温、耐酸碱、耐腐蚀、机械强度高、使用寿命长、通量大的有机无机复合膜和陶瓷膜的研制成功及在膜清洗、抗污染领域的进步,膜分离技术以直接实现油水物理分离、不产生含油污泥、浓缩液可回用、处理量和水质稳定、分离效率高、能耗低的优点,将逐步取代传统电解、絮凝等先进行破乳的工艺,并在含油废水的处理过程中会应用越来越广。2.5生物法生物法是利用各种微生物的代谢作用,对废水中的污染物进行降解和转化为生物体内的有机成分或增殖成新的微生物或被微生物分解为稳定的无机或有机物质。在好氧条件下,污染物被分解为CO2、H2O;在厌氧条件下,污染物最终形成CH4、CO2、H2S、N2和H2O等。生物处理法主要包括活性污泥法、生物膜法(生物转盘、生物滤池)、氧化沟和厌氧消化等。常用的活性污泥法和生物膜法,同属好氧生物处理方法,是生活污水、城市污水以及有机性工业废水处理最常用的工艺。好氧活性污泥法是在曝气池内利用流动状态的絮凝体-活性污泥作为净化微生物的载体,通过吸附、浓缩在絮凝体表面上的多种好氧微生物和n兼性厌氧微生物来分解废水中的有机物;生物膜法是在生物反应器内,使微生物黏附在生物滤池滤料载体或生物转盘的盘片上,污水在流经固定载体表面过程中,废水中的有机物质便被微生物吸附和分解破坏。生物法处理含油废水工艺成熟,适应性强,投资少,无二次污染,但其基建费用高,对进水水质要求较高。目前,生物法已开始在废水的脱氮除磷、难降解物质的降解与转化、土壤和水体生物修复和生物絮凝及固定化技术等方面开展应用。伴随着高效、适应性强的菌种的开发研究,用生物法处理废水具有广阔的应用前景。3膜生物反应器膜生物反应器(MBR)是将膜技术与微生物技术相结合的一种先进的废水处理方法,既以超滤、微滤膜等取代常规活性污泥法中二沉池的污水处理新工艺。该法利用膜的高效截留作用,克服了传统活性污泥法中污泥膨胀对处理效果的影响,还可以将污水中可生化性差的乳化液、悬浮物、胶体进行截留,可灵活控制反应器水力停留时间(HRT)和污泥停留时间(SRT),增加了曝气池活性污泥的浓度,提高生物的降解速率,降低了负荷率,基本上实现无剩余污泥排放,出水悬浮物和浊度接近于零,可以直接回用,实现污水资源化。MBR有两种工艺类型,既浸没式(submerged)MBR和外置式(external)MBR。外置式MBR较适应高温、高有机浓度、高毒性和难过滤的废水。但由于外置式MBR需消耗较高的能耗且给生物处理带来不利的因素,因而浸没式MBR得以发展起来。在浸没式MBR工艺中,膜直接浸没在生物反应池中,安置在曝气器的上方,借助曝气流引起的上升气水混合物擦洗膜表面去除滤饼层,减少运行阻力。因此,能耗主要来自于曝气装置。日前MBR研究集中在两个方面:(1)通过研究MBR组件的结构、类型和膜材料获取基本信息;(2)研究膜污染控制和MBR的应用,包括各类废水、微生物发酵、气体脱除和扩散等。我国目前有254套MBR装置,其中117套用于处理工业废水,137套用于处理市政废水。轧钢含油废水含有大量的乳化态油、脂类化合物,可生化性差,用MBR可以克服这些缺点。肖丙雁等采用A/O2-MBRn组合处理冷轧含油废水,并应用固定化微生物技术克服了常规膜处理中了一个长效、稳定的膜通量和高效的处理成果,运行成本低,出水“油封”对膜表面造成的污染,获得CODcr<70mg/L,出水水质可达《污水综合排放标准》(GB8978-1996)一级标准。随着更为严格的排放标准的实施和废水回用的迫切需要,鉴于MBR的显著优势,MBR将在废水的处理和回用过程中发挥更大的作用。4结论与展望综上所述,随着全球范围内水资源的短缺、污染的加剧,我国《钢铁工业水污染物排放标准》(征求意见稿)要求:①从2009年1月1日起,现有冷轧企业总排放口废水排放限值:COD、SS、石油类分别为:60mg/L、50mg/L和5mg/L;②从2011年1月1日起,现有冷轧企业总排放口废水排放限值:COD、SS、石油类分别为:30mg/L、20mg/L和3mg/L(新建企业从标准实施之日起)。该排放标准的实施,对开发采用新型、高效、运行费用低的处理技术无疑将起到推进作用。因此,今后轧钢含油废水处理技术的发展趋势将会集中在以下几个方面:(1)开发多种工艺组合使用,发挥各处理单元的优势;(2)加强探索含油废水降解的机理研究,为开发新型的处理工艺提供理论基础;(3)加大膜生物反应器等新型技术的研发和应用,推动钢铁行业废水回用事业的发展。查看更多