- 2022-04-26 发布 |
- 37.5 KB |
- 41页
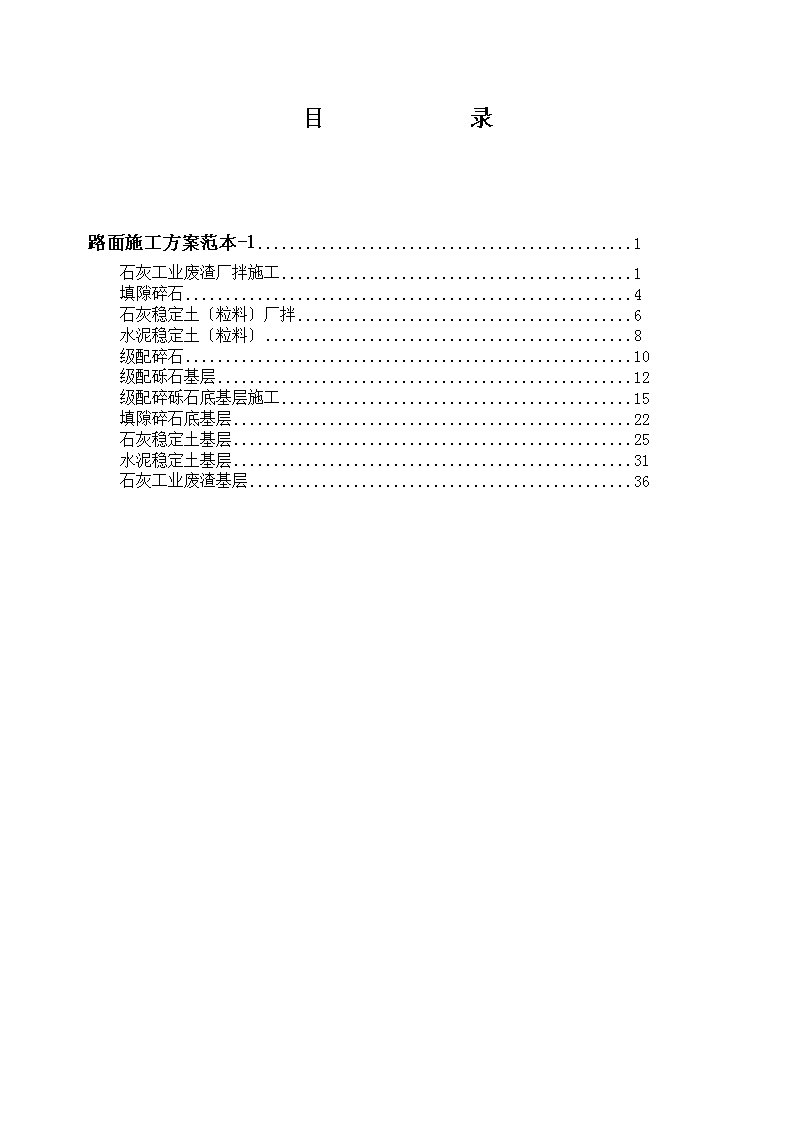
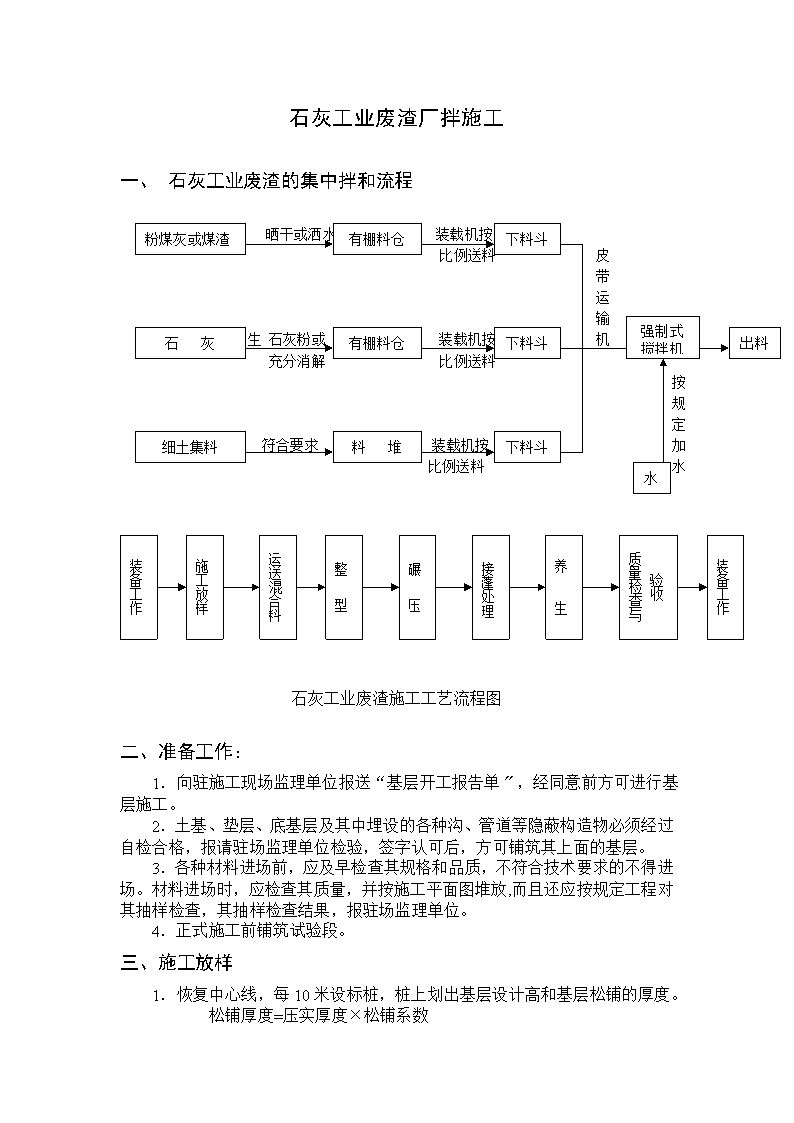
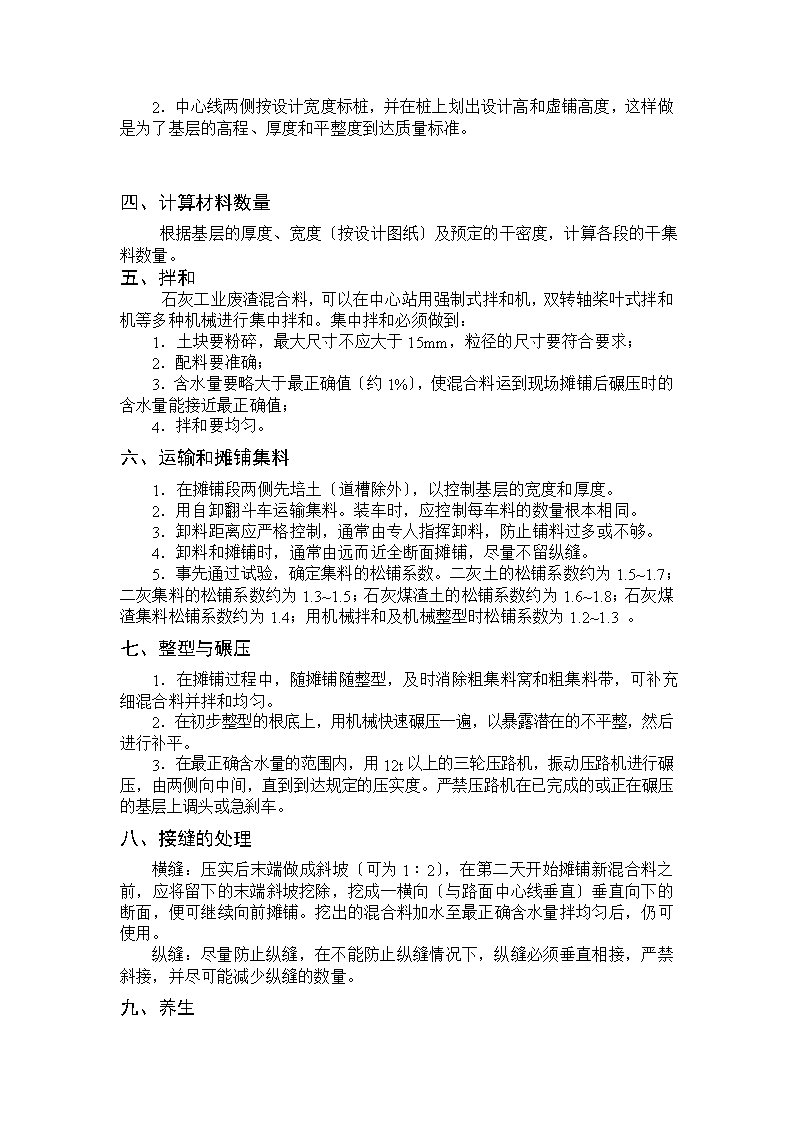
申明敬告: 本站不保证该用户上传的文档完整性,不预览、不比对内容而直接下载产生的反悔问题本站不予受理。
文档介绍
路面施工方案范本
目录路面施工方案范本-11石灰工业废渣厂拌施工1填隙碎石4石灰稳定土〔粒料〕厂拌6水泥稳定土〔粒料〕8级配碎石10级配砾石基层12级配碎砾石底基层施工15填隙碎石底基层22石灰稳定土基层25水泥稳定土基层31石灰工业废渣基层36n石灰工业废渣厂拌施工一、石灰工业废渣的集中拌和流程粉煤灰或煤渣有棚料仓下料斗石灰有棚料仓下料斗细土集料料堆下料斗强制式搅拌机出料水装备工作施工放样运送混合料整型碾压接蓬处理养生装备工作验收质量检查与施工放样晒干或洒水装载机按比例送料皮带运输生石灰粉或装载机按机充分消解比例送料按规定加水符合要求装载机按比例送料石灰工业废渣施工工艺流程图二、准备工作:1.向驻施工现场监理单位报送“基层开工报告单〞,经同意前方可进行基层施工。2.土基、垫层、底基层及其中埋设的各种沟、管道等隐蔽构造物必须经过自检合格,报请驻场监理单位检验,签字认可后,方可铺筑其上面的基层。3.各种材料进场前,应及早检查其规格和品质,不符合技术要求的不得进场。材料进场时,应检查其质量,并按施工平面图堆放,而且还应按规定工程对其抽样检查,其抽样检查结果,报驻场监理单位。4.正式施工前铺筑试验段。三、施工放样1.恢复中心线,每10米设标桩,桩上划出基层设计高和基层松铺的厚度。松铺厚度=压实厚度×松铺系数n2.中心线两侧按设计宽度标桩,并在桩上划出设计高和虚铺高度,这样做是为了基层的高程、厚度和平整度到达质量标准。四、计算材料数量根据基层的厚度、宽度〔按设计图纸〕及预定的干密度,计算各段的干集料数量。五、拌和石灰工业废渣混合料,可以在中心站用强制式拌和机,双转轴桨叶式拌和机等多种机械进行集中拌和。集中拌和必须做到:1.土块要粉碎,最大尺寸不应大于15mm,粒径的尺寸要符合要求;2.配料要准确;3.含水量要略大于最正确值〔约1%〕,使混合料运到现场摊铺后碾压时的含水量能接近最正确值;4.拌和要均匀。六、运输和摊铺集料1.在摊铺段两侧先培土〔道槽除外〕,以控制基层的宽度和厚度。2.用自卸翻斗车运输集料。装车时,应控制每车料的数量根本相同。3.卸料距离应严格控制,通常由专人指挥卸料,防止铺料过多或不够。4.卸料和摊铺时,通常由远而近全断面摊铺,尽量不留纵缝。5.事先通过试验,确定集料的松铺系数。二灰土的松铺系数约为1.5~1.7;二灰集料的松铺系数约为1.3~1.5;石灰煤渣土的松铺系数约为1.6~1.8;石灰煤渣集料松铺系数约为1.4;用机械拌和及机械整型时松铺系数为1.2~1.3。七、整型与碾压1.在摊铺过程中,随摊铺随整型,及时消除粗集料窝和粗集料带,可补充细混合料并拌和均匀。2.在初步整型的根底上,用机械快速碾压一遍,以暴露潜在的不平整,然后进行补平。3.在最正确含水量的范围内,用12t以上的三轮压路机,振动压路机进行碾压,由两侧向中间,直到到达规定的压实度。严禁压路机在已完成的或正在碾压的基层上调头或急刹车。八、接缝的处理横缝:压实后末端做成斜坡〔可为1∶2〕,在第二天开始摊铺新混合料之前,应将留下的末端斜坡挖除,挖成一横向〔与路面中心线垂直〕垂直向下的断面,便可继续向前摊铺。挖出的混合料加水至最正确含水量拌均匀后,仍可使用。纵缝:尽量防止纵缝,在不能防止纵缝情况下,纵缝必须垂直相接,严禁斜接,并尽可能减少纵缝的数量。九、养生n石灰工业废渣结构层碾压完成后的第二天或第三天开始养生,通常采用分散水流养生法。每天洒水的次数视气候条件而定,应始终保持外表潮湿,养生期一般为7d。如果采用消解的生石灰,可能石灰消解不透,在石灰工业废渣结构层中遇水膨胀,结构层外表出现鼓包。应挖除鼓包中的石灰块,再用细混合料填补,用轻型压路机碾压密实。n填隙碎石一、填隙碎石的工艺流程局屑部及补扫撒匀石施工放样振填动满压孔实隙振动压实第布二石次屑撒振动压实撒布石屑初压运铺输粗和碎摊石准备工作终压洒少量水下道工序质量检验干法干燥碾压灌浆洒水饱和湿法合格二、施工准备1.向驻施工现场监理单位报送“基层开工报告单〞,经同意前方可进行基层施工。2.土基、垫层、底基层及其中埋设的各种沟、管等隐蔽构筑物,必须经过自检合格,报请驻场监理单位检验,签字认可后,方可铺筑其上面的基层。三、施工放样1.恢复中线,每10m设标桩,桩上划出基层设计高和基层松铺的厚度。松铺厚度=压实厚度×松铺系数2.中心线两侧按路面设计图设计标桩,推测出基层设计后,在标桩上划出基层设计高和松铺高度。这样做是为了使基层的高度,厚度和平整度到达质量标准。四、备料1.根据基层、底基层的宽度、厚度及松铺系数〔1.20~1.30〕,碎石最大粒径与压实厚度之比为0.5左右时,系数取1.3,比值较大时,系数接近1.20。计算各段需要的粗碎石数量,并按施工平面图堆放。2.填隙料的用量约为粗碎石重量的30%~40%。五、铺筑试验段填隙碎石基层正式施工前应铺筑试验段,其目的与级配砾石基层相同。六、运输和摊铺粗碎石1.在摊铺段两侧先培土,以控制基层的宽度和厚度,再每隔一定距离铺筑盲沟,考虑雨后排出基层积水。n2.碎石装车时,应控制每车料的数量根本相等。3.卸料时,通常有专人指挥,严格控制卸料距离,防止铺料过多或不够。4.用平地机或其它适宜的机具,将粗碎石均匀地摊铺在预定的宽度上,可辅以人工配合。外表应力求平整,并有规定的横坡。5.检验松铺材料层的厚度是否符合预计要求,必要时应进行减料或补料工作。七、撒铺填隙料和碾压1.干法施工①初压。用8t两轮压路机碾压3~4遍,使粗碎石稳定就位,碾压时,由边向中、由低向高进行。在第一遍碾压后,应再次找平。初压结束,外表应平整,并具有要求的纵、横坡度。②撒铺填隙料。用石屑撒布机或类似的设备将枯燥的填隙料均匀地摊铺布已压稳的粗碎石层上,松厚25cm~30cm;也可用自卸汽车运送石屑至粗碎石层上,由人工摊铺,用人工进行扫匀。③用振动压路机慢速碾压,将全部填隙料振入粗碎石的孔隙中。④再次撒布填隙料。松厚2.0cm~2.5cm,人工扫匀。⑤再次碾压。用振动压路机碾压,对局部填隙料缺乏之处,人工进行找补,并将多余的填隙料用扫帚扫到缺乏之处。⑥碾压后,如外表仍有未填满的孔隙,那么还需要补撒填隙料,并用振动压路机继续碾压,直到全部孔隙被填满为止。宜在外表先洒少量水,洒水量在3kg/m2以上,再用12t以上三轮压路机碾压1~2遍。在碾压过程中,不应有任何蠕动现象。2.湿法施工①开始的工序与干法施工相同。②当粗碎石层外表孔隙全部填满后,立即用洒水车洒水,直到饱和,但不能泡软土基。③用12t以上三轮压路机跟在洒水车后面进行碾压,在碾压过程中,将湿填隙料继续扫入所出现的孔隙中,洒水和碾压应一直进行到细集料和水形成粉砂浆为止。粉砂浆应有足够的数量以填塞全部孔隙。④枯燥。碾压后的基层要留待一段时间,让水分蒸发。n石灰稳定土〔粒料〕厂拌一、石灰稳定土的工艺流程施工放样准备工作运送混合料整型碾压接缝处理养生下道工序质与量验检收查二、准备工作1.向驻施工现场监理单位报送“基屋开工报告单〞,经同意前方可进行基屋施工。2.土基、垫层、基底层及其中埋设的各种沟、管等隐敝构造物,必须经过自检合格、报请驻场监理单位检验、签字认可后,方可铺筑其上面的基层。3.各种材料进场前,应及早检查其规格和品质,不符合技术要求的不得进场。材料进场时,应检查其数量,并按施工平面图堆放,而且还应按规定工程对其抽样检查,其抽样检查结果,报驻场监理单位。4.正式施工前,铺筑试验段。三、施工放样1.恢复中心线,每10m设标桩,桩上划出基层设计高和基层松铺的厚度。松铺厚度=压实厚度×松铺系数2.中心线两侧按设计标桩,测出基层设计高,在标桩标上划出基层设计高和松铺高度,这样做是为了使基层的高度、厚度和平整度到达质量标准。四、计算材料数量根据结构层的厚度、宽度〔按设计图纸〕及预定的干密度,计算各段的干集料数量。五、拌和石灰稳定土可以在中心站用多种机械进行集中拌和,集中拌和时,必须做到:1.土块要粉碎,最大尺寸不应大于15mm,粒料的尺寸要符合要求;2.配料要准确;3.含水量要略大于最正确值〔约1%〕,使混合料运到现场摊铺后碾压时的含水量能接近最正确值;4.拌和要均匀。六、运输和摊铺集料1.在摊铺段两侧先培土,以控制结构层的宽度和厚度。2.用自卸翻斗车运输集料。装车时,应控制每车料的数量根本相同。3.卸料距离应严格控制,通常由专人指挥卸料,防止铺料过多或不够。n4.卸料和摊铺时,通常由远而近全断面摊铺尽量不留纵缝。5.应事先通过试验确定集料的松铺系数。人工摊铺石灰土,松铺系数约为1.65~1.70;人工摊铺石灰砂砾土,松铺系数约为1.52~1.56。6.检验松铺材料层的厚度,视其是否符合预计要求。必要时,应进行减料或补料工作。七、整型与碾压1.在摊铺过程中,随摊铺随整型,及时消除粗集料窝和精集料带,可补充细混合料并拌和均匀。2.在初步整型的根底上,用机械快速碾压一遍,以暴露潜在的不平整,然后进行补平。3.在最正确含水量的范围内,用12t以上的三轮压路机、振动压路机进行碾压,由两侧向中间,直到过到规定的压实度。严禁压路机在已完成的或正在碾压的基层上调头或急刹车。八、接缝的处理横缝:压实后末端做成斜坡〔可为1:2〕,在第二天开始摊铺新混合料之前,应将留下的末端斜坡挖除,挖成一横向〔与道面中心线垂直〕垂直向下的断面,便可继续向前摊铺。挖出的混合料加水至最正确含水量拌匀后,仍可使用。纵缝:尽量防止纵缝,在不能防止纵缝情况下〔如较大站坪的石灰稳定土施工〕,纵缝必须垂直相接,严禁斜接,并尽可能减少纵缝的数量。九、养生在养生期间应保持一定的湿度,不应过湿或忽干忽湿。养生期不少于7d,可采用洒水〔分散水流〕或采用不透水薄膜。每次洒水后,宜用两轮压路机将表层压实。n水泥稳定土〔粒料〕一、水泥稳定土、粒料施工工艺流程图施工放样集中拌和摊铺整型碾压处理接缝养生竣工验收质量检验进入下道工序准备工作二、准备工作1.向驻施工现场监理单位报送“基层开工报告单〞,经同意前方可进行基层施工。2.土基、垫层、底层及其中埋设的各种沟、管等隐蔽构造物,必须经过自检合格,报请驻场监理单位检验,签字认可后,方可铺筑其上面的基层。3.各种材料进场前,及早检查其规格和品质,不符合技术要求的不得进场。材料进场时,应检查其数量,并按施工平面图堆放,而且还应按规定工程对其抽样检查,其抽样检查结果,报驻场监理单位。4.水泥稳定土基层施工前应铺筑试验段。三、施工放样1.恢复中心线,每10m设标桩,桩上划出基层设计高和基层松铺的厚度。松铺厚度=压实厚度×松铺系数2.中心线两侧按路面设计图设计标桩,在标桩上划出基层设计高和松铺厚度,这样做是为了使基层的高度、厚度和平整度到达质量标准。四、拌和中心站集中拌和〔厂拌〕法施工,集中拌合时必须掌握以下要点:1.土块、粒料的最大尺寸应符合规定。2.配料必须准确。3.混合料的含水量要略大于最正确值,使混合料运到现场摊铺后碾压时的含水量不小于最正确值〔比最正确值大1%左右〕。4.拌和必须均匀。5.根据集料和混合料含水量的大小,及时调整用水量。五、摊铺1.在铺筑段两侧先培土,以控制基层的宽度和厚度。2.应尽快将拌成的混合料,用自卸汽车运送到铺筑现场,装车时应控制每车料的数量根本相同。3.宜用摊铺机来摊铺混合料,也可用自卸汽车把混合料运到现场,由人工摊铺、整平。4.根据松铺系数〔水泥稳定砂砾松铺系数约1.30~1.35n,水泥土松铺系数约1.53~1.58,严格控制卸料距离。通常由专人指挥卸料,防止料多或不够。5.人工整平或机械整平时,要消除粗、细集料离析现象。六、整型、碾压1.宜用平土机整型,也可用人工整型。〔高速公路一般不容许人工整平〕2.用轻型机械如拖拉机、平土机在初步整平地段,快速碾压一遍,以暴露潜在的不平整,再给予整型,通常整型要1~2次。3.对局部低洼处,应用齿耙将其表层5cm耙松,并用新拌的混合料进行找补、整平、严禁用贴“薄饼〞的方法找平。4.在整型过程中,严禁任何车辆通行。5.整型后,立即用12t以上三轮压路机、重型轮胎压路机或振动压路机碾压。碾压时应控制车速,由近向中、由低向高碾压,直到到达所需的压实度。在碾压过程中,基层外表应始终保持潮湿,如表层水蒸发较快,应及时补洒少量的水。如在碾压过程中有“弹簧〞、松散、起皮等现象,应及时翻开重新拌和〔加适量的水泥〕,或用其它方法处理,使基到达质量要求。七、横缝的处理1.用人工将末端混合料整型,横缝必须垂直整齐,紧靠混合料放两根方木,方木的高度应与混合料的压实厚度相同,整平紧靠方木的混合料。2.方木另一侧用砂砾或碎石回填约3cm长,其高度略高出方木几厘米。3.将混合料碾压密实。4.第二天重新摊铺混合料之前,将砂砾〔或碎石〕和方木除去将下承层顶面清扫干净后,重新开始摊铺混合料。5.也可将在前面的一段〔约2m~3m〕不进行碾压,继续施工时,剔除未经压实的混合料,并将已碾压密实且高程和平整度符合要求的末段挖成一横向〔与中心线垂直〕的垂直向下的断面,然后再摊铺新的混合料。八、纵缝处理1.尽量防止纵向接缝。2.在不能防止纵向接缝的情况下,纵缝必须垂直相接,严禁斜接。3.在前一幅摊铺时,在靠后一幅的一侧用方木或钢模板做支撑,基高度应与混合料压实厚度相同。4.在摊铺另一幅之前,撤除支撑,继续摊铺混合料,整型、碾压。九、养生1.经压实后,检查压实度合格,立即开始养生,采用不透水薄膜保湿养生。2.养生期不宜少于7d,养生期间应封闭交通。3.养生期结束,如不立即铺筑面层,那么应延长养生期,不宜计基层长期暴晒而使基层开裂。n级配碎石一、级配碎石施工工艺流程图运输和撒布石屑洒水使碎石湿润未筛分碎石运输和摊铺拌和并补充洒水准备工作施工放样进入下道工序质量检查竣工验收碾压整型运到现场摊铺补充拌和洒水未筛分碎石和石屑在碎石场加水搅拌二、准备工作1.向驻场监理单位呈报“基层开工报告单〞,经同意前方可进行基层施工。2.土基、垫层、底基层及其中埋设的各种沟、管等隐蔽构筑物,必须经过自检合格,报请驻场监理单位检验,签字认可后,方可铺筑其上面的基层3.各种材料进场前,应及早检查其规格和品质,不符合技术要求的不得进场。材料进场时,应检查其数量,并按施工平面图堆放,而且还应按规定工程对其抽样检查,检查结果报驻场监理单位。4.级配碎石基层正式施工前,应铺筑试验段。三、施工放样1.恢复中心线,每10m设标桩,桩上划出基层设计高和基层松铺厚度。松铺厚度=压实厚度×松铺系数2.中心线两侧宜按路面设计图设置标桩,在桩上划出设计高和虚铺高度,这样做是为了使基层的高程、厚度和平整度到达质量标准。四、计算材料用量根据基层的厚度、宽度〔按设计图纸〕及预定的干密度,计算各段的干集料数量。五、运输和摊铺集料1.在摊铺段两侧先培土〔除挖方道槽外〕,以控制基层的宽度和厚度。2.可用自卸翻斗车运输集料。装车时,应控制每车料的数量相同。3.卸料距离应严格控制,通常由专人指挥卸料,防止铺料过多或不够。4.卸料和摊铺通常由远而近全断面摊铺,尽量不留纵缝。5.应事先通过试验确定集料的松铺系数,人工摊铺混合料时,其摊系数约为1.40~1.50,平地机摊铺混合料时,其松摊系数约为1.25~1.35。6.检验松铺材料层的厚度,视其是否符合预计要求,必要时,应进行减料或补料工作。n7.未筛分碎石摊铺、平整后,在其较潮湿情况下,向上运送石屑,用平地机并辅以人工将石屑均匀摊铺在碎石层上。六、拌和整型1.拌和采用稳定土拌和机拌和级配碎石,也可采用平地机或多铧犁与圆盘耙相配合进行。用稳定土拌和机拌和时一般不少于2遍,用平地机一般需6遍。用多铧犁与缺口圆盘耙相配合,用多铧犁在前面翻拌,圆盘耙在后面拌和,一般需拌2~6遍。在拌和过程中,用洒水车洒足所需水分。拌和结束时,混合料的含水量应该均匀,并较最正确含水量大1%左右,没有粗细颗粒离析现象。2.整型用平地机对拌和的混合料进行整平、整型,并用拖拉机、平地机或轮胎压路机在初步整平的基层上快速碾压一遍,以暴露潜在的不平整,便于找补。通常整型要1~2次。七、碾压1.整型后,当混合料含水量等于或略大于最正确含水量时,应立即用12t以上三轮压路机、振动压路机进行碾压,由两侧向中间碾压,直到到达规定的压实度。2.严禁压路机在已完成的或正在碾压的基层上“调头〞或急刹车。八、接缝的处理两作业段的横缝衔接处,应搭接拌和。第一段拌和后,留5m~8m不进行碾压;第二段施工时,前段留下的未压局部与第二段一起拌和整平后进行碾压。应尽量防止纵缝,在必须分两幅铺筑时,纵缝应搭接拌和。前一幅全宽碾压密实,在后一幅拌和时,应将相邻的前幅边部约30m搭接拌和,整平后一起碾压密实。n级配砾石基层一、级配砾石施工的工艺流程图检查验收下道工序碾压整型洒水拌和运输摊铺施工放样施工准备二、施工准备1、向驻施工现场监理单位报送“基层开工报告单〞,经同意前方可进行基层施工。2、土基、垫层、底基层及其中埋设的各种沟、管等隐蔽构筑物,必须经过自检合格、报请驻场监理单位检验、签字认可后,方可铺筑其上面的基层。3、各种材料进场前,应及早检查其规格和品质,不符合技术要求的不得进场。材料进场时,应检查其数量,并按施工平面图堆放,而且还应按规定工程对其抽样检查,其抽样检查结果,报驻场监理单位。4、级配砾石基层正式施工、应铺筑试验段,其目的:〔1〕确定集料的配合比例;〔2〕确定材料的松铺系数;〔3〕确定标准施工方法;①集料数量的控制②集料摊铺方法和适用机具;③适宜的拌和机械、拌和方法、拌和深度和拌和遍数;④集料含水量的控制方法;⑤整平和整型的适宜机具和方法;⑥压实机械的选择和组合、压实的顺序、速度和遍数;⑦拌和、运输、摊铺和碾压机具的协调和配合;⑧压实后的检查方法;〔4〕确定每天作业段的长度;〔5〕确定一次铺筑的适宜厚度;〔6〕培训管干优化劳动组合。三、施工放样1、恢复中心线,每10m设标桩,桩上划出基层设计高和基层松铺的厚度。松铺厚度=压实厚度×松铺系数2、中心线两侧宜按路面设计标桩,测基层设计高,在标桩上划出基层设计高和松铺高度,这样做是为了使基层的高度、厚度和平整度到达质量标准。四、计算材料用量根据基层的厚度、宽度〔按设计图纸〕n及预定的干密度、计算各段的干集料数量。五、运输和摊铺集料1、在摊铺段两侧先培土〔除挖方段路槽局部〕以控制基层的宽度和厚度。2、可用自卸翻斗车运输集料。装车时,应控制每车料的数量根本相同。3、卸料距离应严格控制,通常由专人指挥卸料,防止铺料过多或不够。4、卸料及摊铺通常由远而近,全断面摊铺尽量不留纵缝。5、应事先通过试验确定集料的松铺系数:松铺系数=松铺厚度÷压实厚度人工摊铺混合料时其松铺系数约为1.40~1.50:平地机摊铺混合料时,其松铺系数约为1.25~1.35。6、摊铺前应根据测量高程、松铺系数放样,控制好摊铺高度、平整度和宽度。7、采用两种集料掺配时,应先运铺主要集料,然后及时运送摊铺另一种集料。如粗、细两种集料最大粒径相差较大,应将粗集料摊铺并洒水后再摊铺细集料。摊铺时应使粗细颗料分布均匀,并去除超径粒料及其它杂物。六、拌和1、通常采用多铧犁或平地机等机械拌和。2、每段作业长度,多铧犁拌宜100m~150m,平地机拌宜300m~500m3、第一鹿从作业段中心开始,将混合料向内翻;第二遍从边缘开始将混合料向外翻。4、拌和过种中,用分散水流洒足所需水分,一般要拌6遍。拌和结束时,混合料的含水量应该均匀,并较最正确含水量大1%左右,没有粗细颗粒离析现象。七、整型、碾压1、根据测量放样对拌和好的混合料进行初步整型,整型作业可采取机械配合人工进行。2、当集料含水量等于或略大于最正确含水量时,容易碾压密实,故应及时碾压。但雨后或土基过分潮湿时,不得用12t以上重型压路机碾压,防止造成碾压翻浆。3、碾型应遵循“先轻后重、由低向高、由边向中、先慢后快、适当重叠〞的原那么,即在碾压时,通常先用拖拉机或轻型压路机碾压1~2遍,然后用重型压路机碾压〔一般6~8遍〕。碾压时由低处向高处、由边缘向中间进行,且应适当重叠;轻型压路机重叠15cm左右;重型压路机宜重叠1/2轮宽。碾压速度应先慢后快,用重型压路机碾压时,其速度通常为:头两遍宜用1.5km/h~1.7km/h,以后几遍宜用2km/h~2.5km/h。当重型压路机碾压4~5遍,到达根本稳定时,必须再次进行测量整型〔通常需进行1~2次〕,直到高程及平整度到达质量标准,当施工经验不多时,宜低不宜高,因为低了填混合料〔细料〕比拟方便,如果高了,刨挖比拟费时。整型后,还应及时碾压直到压,直到压实度到达质量标准。4、整型过程中,车辆和其他机械不得通行。在已完成的或正在碾压的地段,严禁压路机“调头〞或急刹车。5、横缝的处理,两作业段的横缝衔接处应搭接拌和:第一段拌和后,留5m~8m不进行碾压;第二段施工时,前段留下的末压局部,重新加水拌和,并同第二段一起碾压。n6、纵缝的处理。应防止纵向接缝。有时因某种原因可能出现纵向接缝,其处理方法是;沿作业段宽度分带作业时,其接茬处1m宽左右应予重复拌和并交错碾压,边部2m左右应增压3~4遍。八、级配砾石基层、底基层质量标准和检验方法外观要求:外表平整、密实、无细颗粒集中、无杂物和松散现象,用重型压路机碾压,无明显轮迹〔轮迹小于3mm〕。经施工单位自检合格后,报驻场监理单位,由监理单位抽检、认可签字后即基层、底基层检收合格,可进行下道工序施工。n级配碎、砾石基层〔底基层〕施工1.路拌法施工级配碎、砾石基层〔底基层〕施工工艺流程如下图。洒水使碎石湿润碾压整形拌和并补充洒水运输和撒布石屑洒水使碎石湿润施工放样准备下垫层运输和摊铺未筛分碎石a补充拌和洒水运到现场摊铺未筛分碎石和石屑在碎石场加水湿拌b洒水拌和c必要时洒水级配碎石、砾石基层〔底基层〕施工流程a-级配碎石;b-级配砾石1〕准备工作〔1〕准备下承层运输和摊铺掺配集料运输和摊铺主要集料①基层的下承层是底基层及其以下局部,底基层的下承层可能是土基也可能还包括垫层。下承层外表应平整、坚实、具有规定的路拱,没有任何松散的材料和软弱地点。②下承层的平整度和压实度应符合标准的规定。③土基不管路堤或路堑,必须用12~15t三轮压路机或等效的碾压机械进行碾压检验〔压3~4遍〕。在碾压过程中,如发现土过干、表层松散,应适应洒水;如土过湿、发生“弹簧〞现象,应采取挖开晾晒、换土、掺石灰或粒料等措施进行处理。④对于底基层,根据压实度检查〔或碾压检验〕和弯沉测定结果,凡不符合设计要求的路段,必须根据具体情况,分别采用补充碾压、加厚底基层、换填好的材料、挖开晾晒等措施,使到达标准。⑤底基层上的低洼和坑洞,应仔细填补及压实。底基层上的搓板和辙槽,应刮除;松散处应耙松、洒水并重新碾压。⑥逐一断面检查下承层标高是否符合设计要求。下承层标高的误差应符合标准要求。⑦新完成的底基层或土基,必须按标准规定进行验收。凡验收不合格的路段,必须采取措施,到达标准后,方能在上铺筑基层或底基层。⑧在槽式断面的路段,两侧路肩上每隔一定距离〔5~10m〕应交错开挖泄水沟。〔2〕测量①在下承层上恢复中线。直线段每15~20m设一桩,平曲线段每10~15m设一桩,并在两侧路面边缘外0.3~0.5m设指示桩。②进行水平测量。在两侧指示桩上用红漆标出基层或底基层边缘的设计高。〔3〕材料用量①计算材料用量,根据各路段基层或底基层的宽度、厚度及预定的干压实密度,计算各段需要的干集料数量。对于级配碎石,分别计算未筛分碎石和石屑〔细砂砾或粗砂〕n的数量,根据料场未筛分碎石和石屑的含水量以及所用运料车辆的吨位,计算每车料的堆放距离。②在料场洒水加湿未筛分碎石,使其含水量较最正确含水量大1%左右,以减少运输过程中的集料离析现象〔未筛分碎石的最正确含水量约为4%〕。③未筛分碎石和石屑可按预定比例在料场混和,同时洒水加湿,使混合料的含水量超过最正确含水量约1%,以减轻施工现场中的拌和工作量以及运输过程中的离析现象〔级配碎石的最正确含水量约为5%〕。〔4〕机具①翻斗车、汽车或其它运输车辆及平地机等摊铺、拌和机械。②洒水车,洒水或利用就近水源洒水。③压实机械,如轮胎压路机、钢筒轮式压路机、振动压路机等。④其他夯实机具,适宜小范围处理路槽翻浆等。2〕运输和摊铺集料〔1〕运输①集料装车时,应控制每车料的数量根本相等。②在同一料场供料的路段,由远到近将料按要求的间距卸置于下承层上。卸料间距应严格掌握,防止料不够或过多,并且要求料堆每隔一定距离留一缺口,以便施工。当采用两种集料时,应先将主要集料运到路上,待主要集料摊铺后,再将另一种集料运到路上。如粗细两种集料的最大粒径相差较多,应在粗集料处于潮湿状态时,再摊铺细集料。③集料在下承层上的堆置时间不宜过长。运送集料较摊铺集料工序只宜提前1~2d。〔2〕摊铺①摊铺前要事先通过试验确定集料的松铺系数〔或压实系数,它是混合料的干松密度与干压实密度的比值〕。人工摊铺混合料时,基松铺系数约为1.40~1.50;平地机摊铺混合料时,其松铺系数约为1.25~1.35。②用平地机或其他适宜的机具将集料均匀地摊铺在预定的宽度上,过宽的路〔大于22m〕适合分条进行摊铺,要求外表应平整,并具有规定的路拱。同时摊铺路肩用料。③检验松铺材料的厚度,看其是否符合预计要求。必要时应进行减料或补料工作。④级配碎石、砾石基层设计厚度一般为8~16cm,当厚度大于16cm时,应分层铺筑,下层厚度为总厚度的0.6倍,上层为总厚度的0.4倍。3〕拌和及整形应采用稳定土拌和机拌和级配碎、砾石。在无稳定土拌和机的情况下,也可采用平地机或多铧犁与缺口圆盘耙相配合进行拌和。〔1〕用稳定土拌和机拌和。用稳定土拌和机拌和2遍以上。拌和深度应直到级配碎、砾石层底。在进行最后一遍拌和之前,必要时先用多铧犁紧贴底面翻拌一遍。〔2〕用平地机拌和。用平地机将铺好的集料翻拌均匀。平地机的作业长度一般为300~500m,拌和遍数一般为5~6遍,拌和时平地机刀片的安装角度与位置如表所示。n平地机拌和级配碎、砾石基层时的刀片安装与位置项目平面角α(°)倾角β(°)切角γ(°)干拌30~50453湿拌35~40452刀片安装示意图行驶方向刀片α刀片β刀片γ〔3〕用缺口圆盘耙与多铧犁配合拌和。用多铧犁在前面翻拌,圆盘耙跟在后面拌和,即采用边翻边耙的方法,共翻耙4~6遍。圆盘耙的速度应尽量快,且应随时检查调整翻耙的深度。用多铧犁翻拌时,第一遍由路中心开始,将碎石或砾石混合料往中间翻,同时机械应慢速前进。第二遍应是相反,从两边开始,将混合料向外翻。翻拌遍数应以双数为宜。无论采用哪种拌和方法,在拌和的过程中都应用洒水车洒足所需的水分,拌和结束时,混合料的含水量应该均匀,并较最正确含水量大1%左右;应该没有粗细颗粒离析现象。如级配碎石或砾石混合料在料场已经混合,可视摊铺后混合料的具体情况〔有无粗细颗粒离析现象〕,用平地机进行补充拌和。拌和均匀后的混合料要用平地机按规定的路拱进行整平和整形〔要注意离析现象〕,然后用拖拉机,平地机或轮胎压路机在已初平的路段上快速碾压一遍,以暴露潜在的不平整。再用平地机进行最终的整平和整形。在整形过程中,必须禁止任何车辆通行。4〕碾压整形后的基层,当混合料的含水量等于或略大于最正确含水量时,立即用12t以上三轮压路机〔每层压实厚度不应超过15~18cm〕、振动压路机或重型轮胎压路机〔每层压实厚度可达20cm〕进行碾压。直线段由两侧路肩开始向路中心碾压;在有超高的路段上,由内侧路肩开始向外侧路肩进行碾压。碾压时,后轮应重叠1/2轮宽;后轮必须超过两段的接缝处。后轮压完路面全宽时,即为一遍。碾压一直进行到要求的密实度为止。一般需碾压6~8遍。压路机的碾压速度,头两遍以采用1.5~1.7km/h为宜。以后用2.0~2.5km/h为宜,级配碎石或砾石基层在碾压中还应注意以下各点:〔1〕路面的两侧,应多压2~3遍。〔2〕凡含土的级配碎石、砾石基层,都应进行滚浆碾压,直压到碎石、砾石层中无多余细土泛到外表为止。滚到外表的浆〔或事后变干的薄层土〕应予去除干净。〔3〕碾压全过程均应随碾压随洒水,使其保持最正确含水量。洒水理可参考表中数量并结合季节洒水,待外表n晾干后碾压,但薄于10cm时不宜摊铺后洒水,可在料堆上泼水,摊铺后立即碾压。碾压直到要求的密实度。碎石及砾石基层不同厚度、不同季节洒水量厚度〔cm〕季节〔温度〕说明春秋季〔kg/m2〕夏季〔kg/m2〕101520256~89~1216~2015~208~1212~1616~2020~28①天然级配砂、砾石含水量未计入,施工时应扣除天然含水量;②一般天然级配砂、砾石含水量约7%左右;③天然级配砂、砾石最正确水量为5%~9%。〔4〕开始时,应用相对较轻的压路机稳压,稳压两遍后,即时检测、找补,同时如发现砂窝或梅花现象应将多余的砂或砾石挖出,分别掺入适量的碎砾石或砂,彻底翻拌均匀,并补充碾压,不能采用粗砂或砾石覆盖处理。〔5〕碾压中局部有“软弹〞、“翻浆〞、现象,应立即停止碾压,等翻松晒干,或换含水量适宜的材料后再行碾压。〔6〕两作业段的衔接处,应拌和,应搭接拌和。第一段拌和后,留5~8m不进行碾压,第二段施工时,将前段留下未压局部,重新拌和,并与第二段一起碾压。〔7〕严禁压路机在已完成的或正在碾压的路段上调头和急刹车。〔8〕对于不能中断交通的路段,可采用半幅施工的方法。接缝处应对接,必须保持平整密合。2.中心站集中拌和〔厂拌〕法施工级配碎石混合料除上面介绍的路拌法外,还可以在中心站用多种机械进行集中拌和,如用强制式拌和机、卧式双转轴浆叶式拌和机、普通水泥混凝土拌和机等。1)材料宜采用不同粒级的单一尺寸碎石和石屑,按预定配合比在拌和机内拌制级配碎石混合料。2)拌制在正式拌制级配碎石混合料之前,必须先调试所用的厂拌设备,使混合料的颗粒组成和含水量都到达规定的要求。在采用未筛分碎石和石屑时,如未筛分碎石或石屑的颗粒组成发生明显变化,应重新调试设备。3)摊铺〔1〕摊铺机摊铺。可用沥青混凝土摊铺机、水泥混凝土摊铺机或稳定土摊铺机摊铺碎石混合料,摊铺时,在摊铺机后面应设专人消除粗细集料离析现象。〔2〕自动平地机摊铺。在没有摊铺机时,可采用自动平地机摊铺碎石混合料。其步骤为:n①应根据摊铺层的厚度和要求到达的压实干密度,计算每车碎石混合料的摊铺面积。②将混合料均匀地卸在路幅中央,路幅宽时,也可将混合料卸成两行;③用平地机将混合料按松铺厚度摊铺均匀;④设一个3人小组跟在平地机后面,及时消除粗细集料离析现象。对于粗集料窝和粗集料带,应添加细集料,并拌和均匀。对于细集料窝,应添加粗集料,并拌和均匀。⑤整形,与路拌法相同。4〕碾压用振动压路机、三轮压路机进行碾压,碾压方法与要求和路拌法相同。5〕接缝处理〔1〕横向接缝。用摊铺机摊铺混合料时,靠近摊铺机当天未压实的混合料,可与第二天摊铺的混合料一起碾压,但应注意此局部混合料的含水量。必要时,应人工补洒水,使其含水量到达规定要求。用平地机摊铺混合料时,每天的工作缝与路拌法相同。〔2〕纵向接缝。应防止产生纵向接缝。如摊铺机的摊铺宽度不够,必须分两幅摊铺时,宜采用两台摊铺机一前一后相隔约5~8m同步向前摊铺混合料。在仅有一台摊铺机的情况下,可先在一条摊铺带上摊铺一定长度后,再开到另一条摊铺带上摊铺,然后一起进行碾压。在不能防止纵向接缝的情况下,纵缝必须垂直相接,不应斜接,并按下述方法处理:①在前一幅摊铺时,在靠后一幅的一侧用方木或钢模板做支撑,方木或钢模板的高度与级配碎石层的压实厚度相同;②在摊铺后一幅之前,将方木或钢模木板除去;③如在摊铺前一幅未用方木或钢模板支撑,靠边缘的30cm左右难于压实,而且形成一个斜坡。在摊铺后一幅时,应先将未完全压实局部和不符合路拱要求局部挖松并补充洒水,待后一幅混合料摊铺后一起进行整平碾压。3.冬季施工冬季进行级配碎、砾石基层〔底基层〕施工,在摊铺、碾压等工序上,须注意以下各点:1〕摊铺〔1〕应缩短作业面,保证当日摊铺段当日碾压成活,不能当日摊铺次日碾压。〔2〕严格控制摊铺虚厚,每层虚厚不宜大于30cm,并保持集料均匀,无粗细料离析现象。〔3〕冻块应破碎分散,防止大冻块集中。〔4〕摊铺平整后立即洒盐水,并随洒随压。盐水浓度及用量可参考下表。n氯盐溶液表15℃时溶液相对密度(t/m3)氯化钠溶液冰点与含量氯化钙溶液冰点与含量备注氯化钠溶液冰点(℃)1kg水掺氯化钠量(g)氯化钙溶液冰点(℃)1kg水掺氯化钙量(g)1.011.021.031.041.051.061.071.081.091.101.111.121.131.141.151.161.171.175-0.9-1.8-2.6-3.5-4.4-5.4-6.4-7.5-8.6-9.8-11.0-12.2-13.6-15.1-16.6-18.3-20.0-21.2153045607590106123140157175193212231250270290301-0.6-1.2-1.8-2.4-3.0-3.7-4.4-5.2-6.1-7.1-8.1-9.1-10.1-11.4-12.7-14.2-15.7-17.413263750637690104117130144159173188202217233241①盐溶液浓度应用比重计控制;②氯盐均指纯氯盐级配碎、砾石基层〔底基层〕冬期每平方米洒盐水量参考施工气温〔℃〕设计厚度〔cm〕氯盐溶液用量〔kg/m2〕氯盐浓度〔相对密度〕备注-210152058101.03结构厚度小于10cm时,不宜洒水,应预先在料堆上洒水,摊铺后立即碾压,防止干压。-510152058101.06-1010152058101.11-1510152058101.14n2〕碾压成形〔1〕冬期碾压前必须仔细找平,防止因过多的找补延长作业时间。〔2〕碾压时,掌握先轻后重,压路机碾轮宜重轮在前,防止推移。〔3〕碾压成形后,要保持枯燥,防止冷冻使表层疏松。级配碎石、砾石基层施工完成、检测合格后,要连续进行上层施工。如不能连续铺筑上层时,要设专人进行洒水湿润养护。级配碎石、砾石基层未洒透层沥青或未铺封层时,不应开放交通,特别要禁止履带车辆通行,以保护表层不受损坏。n填隙碎石基层〔底基层〕填隙碎石基层〔底基层〕施工工艺流程如下图。终压干法洒少量水初压动实满隙振压填孔部撒屑扫局补石及匀振动压实第二次撒布石屑振动压实撒布石屑初压输摊粗料运和铺骨准备下承层施工放样干燥碾压滚浆洒水饱和湿法填隙碎石工艺流程图1.准备工作1〕准备下承层〔1〕基层的下承层是底基层及其以下局部。底基层的下承层可能还包括垫层。下承层外表应平整、坚实、具有规定的路拱,没有任何松散的材料和软弱地点。〔2〕下承层的平整度和压实度应符合标准要求。〔3〕土基不管路堤或路堑,必须用12~15t三轮压路机或等效的碾压机械进行碾压〔压3~4遍〕。在碾压过程中,如发现土过干、表层松散,应适当洒水;如土过湿、发生“弹簧〞现象,应采取挖开晾晒、换土、掺石灰或粒料等措施进行处理。〔4〕对于底基层,根据压实度检查〔或碾压检验〕和弯沉测定的结果,凡不符合设计要求的路段,必须根据具体情况,分别采用补充碾压、加厚底基层、换填好的材料、挖开晾晒等措施,使到达标准。〔5〕底基层上的低洼和坑洞,应仔细填补及压实。底基层上的搓板应刮除;松散处,应耙松洒水并重新碾压。〔6〕逐一断面检查下承层标高是否符合设计要求。下承层标高的误差应符合标准规定。〔7〕新完成的底基层或土基,必须按标准进行验收。凡验收不合格的路段,必须采取措施,使其到达标准后,方能在上铺筑基层或底基层。〔8〕在槽式断面的路段,两侧路肩上每隔一定距离〔5~10m〕n应交错开挖泄水沟。2〕测量〔1〕在下承层上恢复中线。直线段每15~20m设一桩,平曲线段每10~15m处设一桩,并在对应断面的路肩外侧设指示桩。〔2〕进行水平测量。在两侧指示桩上用红漆标出基层或底基层边缘的设计高。3〕材料用量〔1〕碎石料。根据路段基层或底基层的宽度、厚度及松铺系数〔1.20~1.30,碎石最大粒径与层厚之比为0.5左右时,系数为1.3;比值较大时,系数接近1.2〕,计算各段需要的粗碎石数量。根据运料车辆的车厢体积,计算每车料的堆放距离。〔2〕填隙料。填隙料的用量约为碎石重量的30%~40%。2.运输和摊铺粗碎石〔1〕碎石装车时,应控制每车料的数量根本相等。〔2〕在同一料场供料的路段,由远到近将粗碎石按计算的距离卸置于下承层上。卸料距离应严格掌握,防止料不够或过多,且料堆每隔一定距离应留一缺口,以便于施工作业。〔3〕用平地机或其他适宜的机具将粗碎石均匀地摊铺在预定的宽度上,外表应力求平整,且在规定的路拱。同时摊铺路肩用料。〔4〕检验松铺材料层的厚度,看其是否符合预定要求。必要时,应进行成料或补料工作。3.撒铺填隙料和碾压1〕干法施工干法施工的填隙碎石特别适宜于干旱缺水地区施工,步骤如下。〔1〕初压。用8t两轮压路机碾压3~4遍,使粗碎石稳定就位,在直线段上,碾压从两侧路肩开始,逐渐错轮向路中心进行。在有超高路段,碾压从内侧路肩开始,逐渐错轮向外侧路肩进行。错轮时,每次重叠1/3轮宽。在第一遍碾压后,应再次找平。初压终了时,外表应平整,并且有要求的路拱和纵坡。〔2〕撒铺填隙料。用石屑撒布机或类似的设备将干填隙料均匀地撒铺在已压稳的粗碎石层上,松厚约2.5~3.0cm。需要时,用人工或机械扫〔滚动式钢丝扫〕进行扫匀。〔3〕碾压。用振动压路机慢速碾压,将全部填隙料振入粗碎石间的孔隙中。如没有振动压路机,可用重型振动板。碾压方法同初压,但路面两侧应多压2~3遍。其压实厚度通常为碎石最大粒径的1.5~2.0倍,即10~12cm。碾压后基层的固体体积率应不小于85%,底基层的固体体积率应不小于83%。〔4〕再次撒铺填隙料。用石屑撒布机或类似的设备将干填隙料再次撒铺在粗碎石层上,松厚约2.0~2.5cm。用人工或机械扫匀。〔5〕再次碾压。用振动压路机进行碾压,碾压过程中,对局部填隙料缺乏之处,人工进行找补,将局部多余的填料用竹帚扫到缺乏之处或扫出路外。〔6〕振动压路机碾压后,如外表仍有未填满的孔隙,那么还需补撒填隙料,并用振动压路机继续碾压,直到全部孔隙被填满为止。同时,应将局部多余的填隙料铲除或扫除。填隙料不应在粗碎石外表局部集中。外表必须能见粗碎石n〔如填隙碎石层上为薄沥青面层,应使粗碎石的棱角外露3~5mm〕。〔7〕设计厚度超过一层铺筑厚度,需在上再铺一层时,应将已压成的填隙碎石层外表的细料扫除一些,使外表粗碎石外露约5~10mm。然后在上摊铺第2层粗碎石,并按上述〔1〕~〔6〕的工序进行。〔8〕填隙碎石外表孔隙全部填满后,用12~15t三轮压路机再碾压1~2遍。在碾压过程中,不应有任何蠕动现象。在碾压之前,宜在外表先洒少量水〔洒水量一般在3kg/m2以上〕。2〕湿法施工〔1〕开始的工序与干法施工〔1〕~〔5〕的步骤相同。〔2〕粗碎石层外表孔隙全部填满后,立即用洒水车洒水,直到饱和〔应注意勿使多余水浸泡下承层〕。〔3〕用12~15t三轮压路机跟在洒水车后面进行碾压。其压实要求及压实厚度与干法施工相同。在碾压过程中,将湿填隙料继续扫入所出现的孔隙中。需要时,再添加新的填隙料。洒水和碾压应一直进行到细集料和水形成粉砂浆为止。粉砂浆应有足够的数量,以填塞全部孔隙,并在压路机轮前形成微波纹状。〔4〕枯燥,碾压完成的路段要留待一段时间,让水分蒸发。结构层变干后,外表多余的细料以及任何集中成一薄层的细料覆盖层,都应扫除干净。〔5〕设计厚度超过一层铺筑厚度,需在上再铺一层时,应待结构层变干后,在上摊铺第二层粗碎石,并重复上述〔1〕~〔4〕的工序。n石灰稳定土基层1.路拌法施工石灰稳定土基层施工工序流程如下图养生缝调处处接和头的理碾压整形充水拌补洒和和放摊石摆和铺灰洒水预湿碎或送铺料粉土运摊选准备下承层施工放样预定时间调料石灰稳定土基层施工流程1〕准备工作〔1〕准备下承层当石灰稳定土用作基层时,要准备底基层;当石灰稳定土用作底基层时,要准备土基。无论土基还是底基层,都必须按标准规定进行验收。凡验收不合格的路段,必须采取措施,使其到达标准后,方能在上铺筑石灰稳定土层。在槽式断面的路段,两侧路肩上每隔一定距离〔如5~10m〕应交错开挖泄水沟〔或做盲沟〕。〔2〕测量在底基层或土基上恢复中线,直线段每15~20m设一桩,平曲线段每10~15m设一桩,并在对应断面的路肩外侧设指示桩。在两侧指示桩上用红漆标出石灰稳定土层边缘的设计高。〔3〕备料①集料。采备集料前,应先将树木、草皮和杂土去除干净,并在预定采料深度范围内自上而下采集集料,不宜分层采集,不应将不合格材料采集在一起。如分层采集集料,那么应将集料先分层堆放在一场地上,然后从前到后〔上下层一起装入汽车〕,将料运到施工现场。料中的超尺寸颗粒应予筛除。对于塑性指数小于15的粘性土,机械拌和时,可视土质和机械性能确定土是否需要过筛。人工拌和时,应筛除1.5cm以上的土块。②石灰。石灰宜选在公路两侧宽敞而邻近水源且地势较高的场地集中堆放。预计堆放时间较长时,应用土或其它材料覆盖封存,石灰堆放在集中拌和场地时,宜搭设防雨棚。石灰应在使用前7~10d充分消解。每吨石灰消解需用水量一般为500~800kg。消解后的石灰应保持一定的湿度,以免过干飞扬,但也不能过湿成团。消石灰宜过孔径10mm的筛,并尽快使用。③材料用量。根据各段石灰稳定土层的宽度、厚度及预定的压实度〔换算为压实密度〕,计算各路段需要的干集料质量。根据料场集料的含水量和运料车辆的吨位,计算每车料的堆放距离。根据石灰稳定土层的厚度和预定的干容量及石灰剂量,计算每平方米石灰稳定土需用的石灰质量,并计算每车石灰的摊铺面积,如使用袋装生石灰粉,那么计算每袋石灰的摊铺面积。计算每车石灰的卸放位置,即纵向和横向间距,或计算每袋石灰的纵横间距。2〕运输及摊铺〔1〕运料n运料时,要注意:对预定堆料的下层在堆料前应先洒水,使其湿润。不应过分潮湿而造成泥泞;集料装车时,应控制每车料的数量根本相等;在同一料场供料的路段,由远到近将料按计算的距离〔间距〕卸置于下承层中间或上侧。卸料距离应严格掌握,防止料不够或过多;料堆每隔一定距离应留一缺口;集料在下承层上的堆置时间不应过长。运送集料较摊铺集料工序宜只提前1~2d;在同料场集料做石灰稳定土时,如路肩用料与稳定土层用料不同,应采取培肩措施,先将两侧路肩培好。路肩料层的压实厚度应与稳定土层的压实厚度相同。在路肩上,每隔5~10m应交错开挖临时泄水沟。〔2〕摊铺集料在摊铺集料时,应注意:事先通过试验确定集料的松铺系数。人工摊铺混合料时,其松铺系数可参考下表的值;在摊铺集料前,应先在未堆料的下承层上洒水使其湿润,不应过分潮湿而造成泥泞;对能封闭交通的道路,摊铺集料应在摊铺石灰的前一天进行。摊料长度应与施工日进度相同,以够次日加石灰、拌和、碾压成型为准。对不能封闭交通的道路以及雨季,宜在当天摊铺集料;用平地机或其它适宜的机具将集料均匀摊铺在预定的宽度上,外表应力求平整,并有规定的路拱。摊铺过程中,应注意将土块、超尺寸颗粒及其它杂物拣除。如集料中有较多土块,亦应进行粉碎;检验松铺材料层的厚度,看其是否符合预计要求〔松铺厚度=压实厚度×松铺系数〕。必要时,应进行减料或补料工作。混合料松铺系数参考值材料名称松铺系数说明石灰土1.53~1.58现场人工摊铺土和石灰,机械拌和,人工整平石灰土1.68~1.70路外集中拌和,运到现场人工摊铺石灰土、砂砾1.52~1.56路外集中拌和,运到现场人工摊铺〔3〕摊铺石灰摊铺石灰时,如粘性土过干,应事先洒水闷料,使土的含水量略小于最正确值。细粒土宜闷料一夜;中粒土和粗粒土,视细土含量的多少,可闷1~2h。在人工摊铺的集料层上,用6~8t两轮压路机碾压1~2遍,使其外表平整,并有一定密实度。然后,按计算的每车石灰的纵横间距,用石灰在集料层上做卸置石灰的标记,同时划出摊铺石灰的边线,用乱板将卸置的石灰均匀摊开。石灰摊铺完后,外表应没有空白位置。量测石灰的松铺厚度,根据石灰的含水量和松密度,较核石灰用量是否适宜。3〕拌和与洒水〔1〕集料应采用稳定土拌和机拌和,拌和深度应到达稳定层底。应设专人跟随拌和机,随时检查拌和深度并配合拌和机操作员调整拌和深度,除直接铺在土基上的一层外,严禁在拌和层底部留有“素土〞夹层。拌和应适当破坏〔约1cm左右,不应过多〕不承层的外表,以利上下层粘结。通常应拌和两遍以上〔如使用的是生石灰粉,宜先用平地机或多铧犁紧贴下承层外表翻拌一遍。直接铺在土基上的拌和层也应防止“素土〞夹层。〔2〕n在没有专用机械的情况下,如为石灰稳定细粒土和中粒土,也可用农用旋转耕作机与铧犁或平地机相配合拌和四遍,但其拌和效果较差。先用旋转耕作机拌和,后用多铧犁或平地机将底部“素土〞翻起。再用旋转耕作机拌和第二遍,多铧犁或平地机将底部料再翻起,并随时检查调整翻犁的深度,使稳定土层全部翻透。严禁在稳定土层和下承层之间残留一层“素土〞,也应防止翻犁过深,过多破坏下承层的外表。还可以用缺口圆盘耙与多铧犁或平地机相配合,拌和石灰稳定细粒土、中粒土和粗粒土〔但其拌和效果较差〕。用平地机或多铧犁在前面翻拌,用圆耙跟在后面拌和,即采用边翻边耙的方法。圆盘耙的速度应尽量快,使石灰与集料拌和均匀。共翻拌4~6遍,开始的两遍不应翻犁到底,以防石灰落到底部,后面的几遍应翻犁到底。随时检查调整翻犁的深度,使稳定土层全部翻透。〔3〕在拌和过程中,及时检查含水量。用喷管式洒水车补充洒水,使混合料的含水量等于或略大于最正确值〔视土类而定可大1%左右〕洒水车距离应长些。水车起洒处和另一端调头处都应超出拌和段2m以上。洒水车不应在正进行拌和的以及当天方案拌和的路段上调头和停留,以防局部水量过大。拌和机械应紧跟在洒水车后面进行拌和。尤其在纵坡大的路段上更应配合紧密,减少水分流失。〔4〕在洒水过程中,要人工配合拣出超尺寸颗粒,去除粗细石料“窝〞,以及局部过湿之处。拌和完成的标志是:混合料色泽一致,没有灰条、灰团和花面,没有粗细石料“窝〞,且水分适宜均匀。〔5〕拌和石灰加粘土的稳定碎石或砂砾时,应先将石灰土拌和均匀,然后均匀地摊铺在碎石或砂砾层上,再一起进行拌和。用石灰稳定塑性指数大的粘土时,由于粘土难以粉碎,宜采用两次拌和法。即每一次加70%~100%预定剂量的石灰进行拌和,闷放一夜,然后补足石灰用量,再进行第二次拌和。4〕整形与碾压〔1〕整形平地机整形。混合料拌和均匀后,先用平地机初步整平和整形。在直线段,平地机由两侧向路中心进行刮平。在平曲线段,平地机由内侧向外侧进行刮平。需要时,再返回刮一遍。用平地机或轮胎压路机快速碾压1~2遍。在用轮胎压路机碾压时,因轮胎外表没有花纹,压后外表比拟光滑。在用平地机整平前,应先用齿耙把低洼处表层5cm以上耙松,防止在较光滑的外表产生薄层找补的情况。用平地机进行整形后再碾压一遍。对于局部低洼处,应用齿耙将其表层5cm以上耙松,并用新拌的石灰混合料进行找补平整,再用平地机整形一次。每次整形都要按规定的坡度和路拱进行。特别要注意接缝处的整平,接缝必须顺适平整。〔2〕碾压整形后,当混合料处于最正确含水量±1%时〔如外表水分缺乏,应适当洒水〕,立即用12t以上三轮压路机、重型轮胎压路机或振动压路机在路基全宽内进行碾压。直线段,由两侧路肩向路中心碾压。平曲线段,由内侧路肩向外侧路肩进行碾压。碾压时后轮应重叠1/2的轮宽,后轮必须超过两段的接缝处。后轮压完路面全宽时即为一遍。碾压一直进行到要求的密实度为止。一般需6~8遍。压路机的方式同路基碾压。碾压过程中,石灰稳定土的外表应始终保持湿润。如外表水蒸发得快,应及时补洒少量的水。如有“弹簧〞、松散、起皮等现象,应及时翻开重新拌和,或用其它方法处理,使其到达n质量要求。在碾压结束之前,用平地机再终平一次,使其纵向顺适,路拱和超高符合设计要求。终平应仔细进行,必须将局部高出局部刮除并扫出路外,对于局部低洼之处,不再进行找补,留待铺筑面层时处理。5〕养生〔1〕石灰稳定土在养生期间应保持一定的湿度,不应过湿。养生期一般不少于7d。养生方法可视具体情况采用洒水、覆盖砂、低塑性土或沥青膜等。在养生期间石灰土表层不应忽干忽湿,每次洒水后,应用两轮压路机将表层压实。石灰稳定土层碾压结束后,过1~2d,当其表层较枯燥〔如石灰土的含水量不大于10%,石灰粒料土的含水量在5%~6%〕时,可以立即喷洒透层,做下封层或铺筑面层。但初期应禁止重型车辆通行。〔2〕在养生期间未采用覆盖措施的石灰稳定土层上,除洒水车外,应封闭交通。在采用覆盖措施的石灰稳定土层上,不能封闭交通时,应限制车速不得超过30km/h。如石灰稳定土分层施工时,下层石灰稳定土碾压完后,可以立即在上铺筑另一层石灰稳定土,不需专门的养生期。〔3〕养生期结束后,应立即喷洒透层沥青或做下封层,并在5~10d内铺筑沥青面层。在喷洒透层沥青后,应撒布3~8mm或5~10mm的小碎〔砾〕石,小碎石约撒60%的面积〔不完全覆盖,但均匀覆盖60%的面积,露黑〕。如喷洒的透层沥青能透入基层,当运料车辆和面层混合料摊铺机在上行驶不会破坏沥青膜时,可以不撒小碎石。如为水泥混凝土面层时,也不宜让基层长期暴晒开裂。6〕施工中应注意的问题〔1〕接缝和“调头〞处的处理两工作段的搭接局部,应采用对接形式。前一段拌和后,留5~8m不进行碾压。后一段施工时,将前段留下未压局部,一起再进行拌和。拌和机械及其它机械不宜在已压成的石灰稳定土层上调头。如必须在上进行调头,应采取措施〔如覆盖10cm厚的砂或砂砾〕保护调头局部,使石灰稳定土表层不受破坏。〔2〕纵缝的处理石灰稳定土层的施工应尽可能防止纵向接缝,必须分两幅施工时,纵缝必须垂直相接,不应斜接。一般情况下,纵缝可按下述方法处理。在前一幅施工时,在靠中央一侧用方木或钢模板做支撑,方木或钢模板的高度与稳定土层的压实厚度相同。混合料拌和结束后,靠近支撑木〔或板〕的一条带,应人工进行补充拌和,然后进行整形和碾压。在铺筑另一幅时,或在养生结束时,撤除支撑木〔或板〕。第二幅混合料拌和结束后,靠近第一幅的一条带,应人工进行补充拌和,然后进行整形和碾压。〔3〕路缘处理如石灰稳定土层上为薄沥青面层,基层每边应较面层展宽20cm以上。在基层全宽上喷洒透层沥青或设下封层,沥青面层边缘以三角形向路肩抛出6~10cm。如设路缘块时,必须注意防止路缘块阻滞路面外表水和结构层中的水。〔4〕用石灰稳定低塑限指数的砂、粉性土的处理用石灰稳定低塑限指数的砂性土和粉性土时,碾压过程中容易起皮松散,成形困难,施工时要大量洒水,分两阶段碾压。第一阶段,洒水后用覆带拖拉机先压2~3遍,到达初步稳定。第二阶段,待水分接近最正确含水量时,再继续用12t以上压路机压实。当缺少履带拖拉机时,洒水后,先用轻型压路机碾压两遍,然后覆盖一层素土,继续用12t以上压路机压实。养生后,将素土层n去除干净。〔5〕通车路段的施工对于不能中断交通的路段,可采用半幅施工方法。接缝处应对接,必须保持平整密合。同时,要加强管理,消除隐患,确保工程质量。2.中心站集中拌和〔厂拌〕法施工石灰稳定土可以在中心站用多种机械集中拌和,如强制式拌和机、双转轴浆叶式拌和机等。集中拌和有利于保证配料的准确性和拌和的均匀性。〔1〕备料土块要粉碎,最大尺寸不应大于15mm。集料的最大粒径和级配都应符合要求,必要时,应先筛除集料中不符合要求的颗粒。配料应准确,在潮湿多雨的地区施工时,还应采取措施保护集料,特别是细集料〔含土〕和石灰免遭雨淋。〔2〕拌制在正式拌制稳定土混合料之前,必须先调试所用的厂拌设备,使混合料的颗粒组成和含水量都到达规定的要求。集料的颗粒组成发生变化时,应重新调试设备。应根据集料和混合料的含水量及时调整向拌和室中添加的水量,拌和要均匀。〔3〕运输已拌成的混合料应尽快运送到铺筑现场。如运距远、气温高,那么车上的混合料应加以覆盖,以防水分过多蒸发。〔4〕摊铺及碾压下承层为石灰稳定土时,应先将下承层顶面拉毛,再摊铺混合料。摊铺应采用沥青混凝土摊铺机、水泥混凝土摊铺机或稳定土摊铺机摊铺混合料。在没有以上摊铺机的情况下,可以用摊铺箱或自动平地机摊铺混合料。用摊铺机或摊铺箱摊铺时,要求拌和机与摊铺机的生产能力相协调。如拌和机的生产能力较低,那么应用最低速度摊铺,以减少摊铺机停机待料的情况。在摊铺机后面应设专人消除粗细集料离析现象,特别是局部粗集料“窝〞应该铲除,并用新混合料填补。摊铺后应用振动压路机、三轮压路机和轮胎压路机及时进行碾压。用平地机摊铺混合料时,根据铺筑层的厚度和要求到达的压实干密度,计算每车混合料的铺筑面积。将混合料均匀地卸在路幅中央,路幅宽时,可将混合料卸成两行。用平地机将混合料按松铺厚度摊铺均匀,设一个3人小组跟在平地机后面,及时消除粗集料“窝〞和粗集料带〔补充细混合料并拌和均匀〕。整形、碾压及接缝处理,与路拌法相同。〔5〕横向接缝处理①用摊铺机摊铺混合料时,每天的工作缝应做成横向接缝。摊铺机应驶离混合料末端。②人工将末端混合料处理整齐,紧靠混合料放两根方木,方木的高度与混合料的压实厚度相同,整平紧靠方木的混合料。③方木的另一侧用砂砾或碎石回填3m长,其高度应高出方木几厘米。④将混合料碾压密实。⑤在重新开始摊铺混合料之前,将砂砾〔或碎石〕和方木除去,并将下承层顶面清扫干净和拉毛。⑥摊铺机返回到已压实层的末端,重新开始摊铺混合料。n⑦如压实层末端未用方木作支撑处理,在碾压后未端成一斜坡,那么在第二天开始摊铺新混合料之前,应将末端斜坡挖除,并挖成一横向〔与路中心线垂直〕垂直向下的断面。挖出的混合料加水到最正确含水量拌匀后仍可使用。〔6〕纵向接缝应防止纵向接缝。如摊铺机的摊铺宽度不够,必须分两幅摊铺时,宜采用两台摊铺机一前一后相隔约8~10m同步向前摊铺混合料,一起进行碾压。在仅有一台摊铺机的情况下,可先在一条摊铺带上摊铺一定长度后,再开到另一条摊铺带上摊铺,然后一起进行碾压。在不能防止纵向接缝的情况下,纵缝必须垂直相接,严禁斜接,并按下述方法处理。在前一幅摊铺时,在靠后一幅的一侧用方木或钢模板做支撑,方木或钢模板的高度与稳定土层的压实厚度相同。养生结束后,在摊铺另一幅之前,撤除支撑木〔或板〕。〔7〕养生及路缘处理方法同路拌法。n水泥稳定土基层水泥稳定土施工时,必须采用流水作业法,使各工序紧密衔接。特别是要尽量缩短从拌和到完成碾压之间的延迟时间。所以在施工时应做延迟时间对强度影响的试验,以确定适宜的延迟时间,并使此时水泥稳定土的强度仍能满足设计要求。水泥稳定土基层的施工方法主要有路拌法和中心站集中拌和〔厂拌〕法两种。1.路拌法施工水泥稳定土路拌法施工与石灰稳定土的施工相似,其工艺流程如下图。养生经规定时碾压整形加水并湿拌拌和〔干拌〕摆放和摊铺水泥洒水预湿摊铺选料粉碎土或运料、准备下承层施工放样接缝和调头处的处理间闷料水泥稳定土路拌法施工工艺流程1〕准备工作〔1〕准备下承层当水泥稳定土用作基层时,要准备底基层;当水泥稳定土用作底基层时,要准备土基。无论底基层还是土基,都必须按标准进行验收,凡验收不合格的路段,必须采取措施,使其到达标准后,方可铺筑水泥稳定土层。如底基层或土基已遭破坏,那么必须作如下处理:①对土基必须用12~15t三轮压路机或等效的碾压机械进行碾压检验〔压3~4遍〕。在碾压过程中,如发现土过干、表层松散,应适当洒水;如土过湿,发生“弹簧〞现象,应采取挖开晾晒、换土、掺石灰或粒料等措施进行处理。②对于底基层,根据压实度检查和弯沉测定的结果,凡不符合设计要求的路段,必须根据具体情况,分别采用补充碾压、加厚底基层、换填好的材料、挖开晾晒等措施,使其到达标准。③底基层上的低洼和坑洞,应仔细填补及压实,到达平整。底基层上的搓板和车辙,应刮除;松散处,应耙松洒水并重新碾压。④逐一断面检查土基或底基层标高是否符合设计要求,平整度、压实度、路拱是否符合规定,且应没有任何松散的材料和软弱地点。应注意在槽式断面的路段,两侧路肩上每隔一定距离〔5~10m〕应交错开挖泄水沟或做盲沟,以便排出路基积水。〔2〕测量首先是在底基层或土基上恢复中线。直线段每15~20m设一桩,平曲线段每10~15m设一桩,并在对应断面路肩外侧设指示桩。n其次是进行水平测量。在两侧指示桩上用红漆标出水泥稳定土层边缘的设计高。〔3〕确定合理的作业长度确定路拌法施工每一作业段的合理长度时,应考虑如下因素:水泥的终凝时间;延迟时间对混合料密实度和抗压强度的影响;施工机械和运输车辆的效率和数量;操作的熟练程度;尽量减少接缝;施工季节和气候条件。一般宽7~8m的稳定层,每一流水作业段以200m为宜。但每天的第一个作业段宜稍短些,可为150m。如稳定层较宽,那么作业段应该再缩短。〔4〕备料在采备集料前,应先将料场的树木、草皮和杂土和杂土去除干净。采集集料时,应在预定采料深度范围内自上而下进行,不应分层采集,不应将不合格的集料采集一起。在集料中超尺寸颗粒应予筛除。对于粘性土,可视土质和机械性能确定土是否需要过筛。〔5〕计算材料用量方法同石灰稳定土。2〕集料运输与摊铺方法与石灰稳定土施工根本相同。3〕拌和〔1〕摊铺水泥在人工摊铺的集料上,用6~8t两轮压路机碾压一遍,使其外表平整,然后按计算的每袋水泥的纵横间距,用石灰或水泥在集料层上做安放每袋水泥的标记,同时划出摊铺水泥的边线。水泥应当日用汽车直接送到摊铺路段,每袋水泥从汽车上直接卸在做标记的地点,检查有无遗漏和多余。运水泥的车应有防雨设备。翻开水泥袋,将水泥倒在集料层上,用刮板将水泥均匀摊开。应注意使每袋水泥的摊铺面积相等,水泥摊铺完后,外表应没有空白,但也不过分集中。〔2〕干拌①用稳定土拌和机拌和。拌和深度应达稳定层底。应设专人跟随拌和机,随时检查拌和深度并配合拌和机操作员调整拌和深度。严禁在拌和层底部留有“素土〞夹层。应略破坏〔约1cm左右〕下承层的外表,以利上下层粘结。通常应拌和两遍以上。在最后一遍拌和之前,必要时可先用多铧犁紧贴底面翻拌一遍。直接铺在土基上的拌和层也应防止“素土〞夹层。②在没有专用拌和机械的情况下,也可用农用旋转耕作机与多铧犁或平地机相配合进行拌和。先用平地机或多铧犁〔4铧犁或5铧犁〕将铺好水泥的集料翻拌两遍,使水泥分布到集料中,但不翻犁到底,以防止水泥落到底部。第一遍由路中心开始,将混合料向中间翻,同时机械应慢速前进。第二遍相反,由两边开始,将混合料向外侧翻,接着用旋转耕作机拌和两遍再用多铧犁或平地机将底部料翻起。随时检查调整翻拌深度,使稳定土层全部翻透。严禁在底部留有“素土〞夹层,也应防止过多破坏下承层的外表,通常应翻犁两遍,接着再用旋转耕作机拌和两遍,用多铧犁或平地机再翻犁两遍。③n在没有专用拌和机械的情况下,还可以用缺口圆盘耙与多铧犁或平地机相配合,拌和水泥稳定中粒土和粗粒土。用平地机或多铧犁在前面翻拌,用圆盘耙跟随在后面拌和,即采用边翻边耙的方法。圆盘耙的速度应尽量快,使水泥与集料拌和均匀。共翻拌4遍,开始的两遍不应翻犁到底,以防水泥落到底部。后面的两遍,应翻犁到底,随时检查调整翻犁的深度,使稳定土层全部翻透。〔3〕洒水的湿拌干拌过程结束时,特别是在用农业机械进行拌和的情况,如果混合料含水量缺乏,洒水车的数量应视水源远近而定,常用的洒水车仅两侧各有一个喷嘴,喷出的水量不均匀,不适宜用作路面施工。应在后面改接一根Φ50mm、长约2m的横向水平钢管,管壁钻三排,Φ4mm的孔眼。洒水车不应使洒水中断,洒水距离应长些,水车起洒处和另一端调头处都应超出拌和段2m以上。洒水车不应在正进行拌和的以及当天方案拌和的路段上调头和停留,以防局部水量过大。洒水后,应再次进行拌和,使水分在混合料中分布均匀。拌和机械应紧跟在洒水车后面进行拌和,尤其在纵坡大的路段上应配合紧密,以减少水分流出。洒水及拌和过程中,应及时检查混合料的含水量,可采用含水量快速测定仪测定混合料的含水量。混合料的最正确含水量也可以在现场人工控制。最正确含水量时的混合料,在手中能紧捏成团,落在地上能散开,并应参考室内击实试验最正确含水量的混合料的状态。水分宜略大于最正确值,稳定粗粒土和中粒土,应较最正确含水量大0.5%~1.0%,稳定细粒土,较最正确含水量大1%~2%,不应小于最正确值,以补偿施工过程中水分的蒸发,并有利于减轻延迟时间的影响。在洒水拌和过程中,还要人工配合拣出超尺寸颗粒,消除粗细颗粒“窝〞以及局部过分潮湿或过分枯燥之处。拌和完成的标志是:混合料没有灰条、灰团和花面,没有粗细颗粒“窝〞,且水分适宜和均匀。4〕整形与碾压同石灰稳定土。5〕接缝和“调头〞处的处理〔1〕当天两工作段的衔接处,应搭接拌和。第一段拌和后,留5~8m不进行碾压;第二段施工时,前段留下来压局部,要再加局部水泥重新拌和,并与第二段一起碾压。当天其余各段的接缝都可这样处理。稳定土层素土稳定土层素土方木稳定土层素土横向接缝处理示意图〔2〕应十分注意每天最后一段末端缝〔工作缝〕的处理。工作缝隙和“调头〞处的处理如以下图所示。在已碾压完成的水泥稳定土层末端沿稳定土挖一条宽约30cm的槽,直挖到下承层顶面。此槽与路的中心线垂直,靠稳定土的面应切成直线,而且应垂直向下。将两根方木〔长度为水泥稳定土层宽的一半,厚度与其压实厚度相同〕放在槽内,并紧靠着已完成的稳定土,以保护其边缘,不致遭第二天工作时的机械破坏。用原挖出的素土回填槽内其余局部。如拌和机械及其他机械必须到已压成的水泥稳定土层上“调头〞,应采取措施保护“调头〞局部。一般,可在准备用于“调头〞的约8~10cm长的稳定土层上,先覆盖一张厚塑料布〔或油毡纸〕,然后在塑料布上盖约10cm厚的一层土、砂或砂砾。第二天,摊铺水泥及湿拌后,除去顶木,用混合料回填。靠近顶木末能拌和的一小段,应人工进行补充拌和。整平时,接缝处的水泥稳定土应较已完成断面高出约5cm,以便将“调头〞处的土除去后,能刮成一个平顺的接缝。整平后,用平地机将塑料布上大局部n土除去,注意勿刮破塑料布。然后人工除去余下的土,并收起塑料布。在新混合料碾压过程中,将接缝修整平顺。〔3〕工作缝也可按下述方法处理:在水泥稳定土混合料拌和结束后,在预定长度的末端,按前述方法挖一条横贯全路宽的槽,槽内放两根与压实厚度等厚的方木,方木的另一侧用素土回填至3~5cm长,然后进行整形和碾压。第二天,邻接的作业段拌和结束后,除去方木,用混合料回填,靠近顶木未能拌和的一小段,应人工进行补充拌和。〔4〕纵缝的处理。水泥稳定土层的施工应该防止纵向接缝,在必须分两幅施工时,纵缝必须垂直相接,不应斜接,并按下述方法处理:在前一幅施工时,在靠中央一侧用方木或钢模板做支撑,方木或钢模板的高度与稳定土层的压实厚度相同。混合料拌和结束后,靠近支撑木〔或板〕的一局部,应人工进行补充拌和,然后整形和碾压。在铺筑另一幅时,或在养生结束后,撤除支撑木〔或板〕。第二幅混合料拌和结束后,靠近第一幅的局部,应人工进行补充拌和,然后进行整平和碾压。2.中心站集中拌和〔厂拌〕法施工水泥稳定土可以在中心站用强制式拌和机、双转轴桨叶式拌和机〔卧式叶片拌和机〕等厂拌设备进行集中拌和,塑性指数小,含土量少的砂砾土、级配碎石、砂、石屑等集料也可以用自落式拌和机拌和。其施工方法与石灰稳定土厂拌法施工根本相同,不作赘述。但应该注意的是:在摊铺过程中,如中断时间已超过2~3h,又末按横向接缝方法处理,那么应将摊铺机附近及其下面末经压实的混合料铲除,并将已碾压密实且高程和平整度符合要求的末端挖成一横向〔与路线垂直〕垂直向下的断面,然后再摊铺新的混合料。3.养生及路缘处理1〕养生水泥稳定土基层每一段碾压完成并经压实度检查合格后应立即开始养生,不应延误。但如水泥稳定土分层施工时,下层水泥稳定土碾压完后,过一天就可以铺筑上层水泥稳定土,不需经过7d养生期。但在铺筑土层稳定土之前,应始终保持下层外表湿润。为增加上下层之间的粘结性,在铺筑上层稳定土时,宜在下层外表撒少量水泥或水泥浆。此外,如水泥稳定土用作水泥混凝土路面板的基层,且面板是用小型机械施工的,那么基层完成后不需养生就可铺筑混凝土面层。水泥稳定土基层养生方法如下:①用不透水薄膜或湿砂进行养生。用砂覆盖时,砂层厚7~10cm,砂铺匀后,应立即洒水,并保持在整个养生期间砂的潮湿状态。也可以用潮湿的帆布、粗麻布、草帘或其他适宜的材料覆盖,但不得用湿粘土覆盖。养生结束后,必须将覆盖物去除干净。②采用沥青乳液进行养生。乳液应采作沥青含量约35%的慢裂沥青乳液,使其能透入基层几毫米深。沥青乳液的用量1.2~1.4kg/m2,宜分两次喷洒。乳液分裂后,宜撒布3~8mm或5~10mm的小碎〔砾〕石,小碎石约撒布60%的面积〔不完全覆盖,但均匀覆盖60%的面积,露黑〕。养生结束后,沥青乳液相当于透层沥青。也可以在完成基层上立即〔或第二天〕做下封层,利用下封层进行养生。n③无上述条件时,可用洒水车经常洒水进行养生,每天洒水的次数应视气候而定。整个养生期间应始终保持稳定土层外表潮湿,不应时干时湿。洒水后,应注意表层情况,必要时,用两轮压路机压实。除采用沥青养生外,养生期不宜少于7d,如养生期少于7d就已做上承层,那么应注意勿使重型车辆通行。假设养生期间末采用覆盖等措施,除洒水车外,应封闭交通,假设采用了覆盖措施,不能封闭交通时,应限制重车通行,其他车辆的车速不得超过30km/h。养生期结束后,应立即喷洒透层沥青或做下封层,并在5~10d内铺筑沥青面层。在喷洒透层沥青后,应撒布3~8mm或5~10mm的小碎〔砾〕石。如喷洒的透层沥青能透入基层,且运料车辆和面层混合料摊铺机在上行驶不会破坏沥青膜时,可以不撒小碎〔砾〕石。如面层为水泥混凝土时,也不宜让基层长期暴晒开裂。n石灰工业废渣基层〔一〕路拌法施工石灰工业废渣的路拌法施工工艺流程如下图。施工放样准备下承层输摊土运和铺输摊粉灰运和铺煤铺灰合摊二混料输摊石运和铺灰缝调处理接和头处输摊粒运和铺料养生碾压整形拌和及洒水预拌二灰石灰工业废渣工艺流程图〔路拌法施工〕1、施工准备〔1〕准备下承层当石灰工业废渣用做基层时,要准备底基层;当石灰工业废渣用做底基层时,要准备土基。对下承层总的要求是:平整、坚实、具有规定的路拱,没有任何松散的材料和软弱地点。因此,对底基层或土基,必须按标准规定进行验收。凡验收不合格的路段,必须采取措施,使其到达标准后,方能在其上铺筑石灰工业废渣层。假设底基层或土基因开放交通而受到破坏,那么应逐一进行找平、换填、碾压等处理,使其到达标准,逐一断面检查下承层标高是否符合设计要求。在槽式断面的路段,两侧路肩上每隔一定距离〔如5~10m〕应交错开挖泄水沟〔或做盲沟〕及时排出积水。保证底基层或土基的枯燥。〔2〕测量测量的主要内容是在底基或土基上恢复中线。直线段每15~20m设一桩,平曲线段10m设一桩,并在两侧边缘外0.3~0.5m设指示桩,然后进行水平测量。在两侧指示桩上用红漆标出石灰工业废渣边缘的设计高。〔3〕备料①粉煤灰被运到路上、路旁或厂内场地后,通常露天堆放。此时,必须使粉煤灰含有足够的水分〔含水量15%~20%〕,以防飞场。特别在枯燥和多风季节,必须使料堆外表保持潮湿,或者覆盖。如在堆放过程中,局部粉煤灰凝洁成块,使用时,应将灰块打碎。②土或粒料的准备。采备集料前,应先将树木、草皮和杂土去除n干净。集料中的超尺才颗粒应予筛除。应在预定采料深度范围内自上而下采集集料,不应分层采集,不应将不合格的集料采集在一起。对于粘性土,可视土质和机械性能确定土是否需要地筛。③石灰的准备。石灰宜选在公路两侧宽敞而邻近水源且地势较高场地集中堆放。预计堆放时间较长时,应用土或其它材料覆盖封存。石灰应在使用前7~10d充分消解。1t石灰消解需用水量一般为500~800kg。消解后的石灰应保持一定的湿度,以免过干飞扬,但也不能过湿成团。消石灰宜过孔径10mm的筛,并尽快使用。〔4〕其它①如路肩用料与石灰工业废渣层用料不同,应采取培肩措施,先将两侧路肩培好。路肩料层的压实厚度应与稳定土层的压实厚度相同。路肩上每隔5~10m应交错开挖临时泄水沟。②计算材料用量,根据各路段石灰工业废渣层的宽度、厚度及预定的干压实密度,计算各路段需要的干混合料数量。根据混合料的配合比、材料的含水量、以及所用运料车辆的吨位,计算各种材料每车料的堆放距离。2、运输和摊铺集料集料运输和摊铺的方法和步骤是:〔1〕预定堆料的下承层在堆料前应先洒水,使其外表湿润。〔2〕材料装车时,应控制每车料的数量根本相等。〔3〕采用二灰混合料时,先将粉煤灰运到路上;采用二灰土时,先将土运到路上;采用二灰粒料时,先将粒料运到路上。在同一料场供料的路段内,由远到近按计算的距离卸置于下承层中间或上侧。卸料距离应严格掌握,防止料不够或过多。〔4〕料堆每隔一定距离应留一缺口,材料在下承层上的堆置时间不应过长。〔5〕应事先通过试验确定各种材料及混合料的松铺系数。〔6〕采用机械路拌时,应采用层铺法,即将先运到路上的材料摊铺均匀后,再往路上运送第二种材料,将第二种材料摊铺均匀后,再往路上运送第三种材料。在摊铺集料前,应先在末堆料的下承层上洒水,使其外表湿润。然后再用平地机或其它适宜的机具将料均匀地摊在预定的宽度上,外表应力求平整,并具有规定的路拱。粒料应较湿润,必要时先洒少量水。第一种材料摊铺均匀后,宜先用两四化建轮压路机碾压1~2遍,然后再运送并摊铺第三种材料。在二种材料层上,也应先用两轮压路机碾压1~2遍,然后再运送并摊铺第三种材料。3、拌和及洒水〔1〕机械拌和时,应采用稳定土拌和机或粉碎拌和机。在无专用拌和机械的情况下,也可采用平地机或多铧犁转耕作机或缺口圆盘耙柏配合进行拌和。采用专用拌和机时,干拌一遍;采用其它机械时,干拌2~4遍。具体拌和方法是:①用稳定土拌和机拌和两遍以上。拌和深度应直到稳定层底。应设专人跟随拌和机,随时检查拌和深度,严禁在底部留有“素土〞夹层,也应防止过多破坏〔以1mm左右为宜〕下承层的外表,以免影响结合料的剂量以及底部的压实。在进行最后一遍拌和之前,必要时先用多铧犁紧贴底面翻拌一遍,直接铺在土基上的拌和层也应防止“素土〞夹层。②在没有专用机械的情况下,如为二灰稳定中粒土和细粒土,也可用旋转耕作机与多铧犁或平地要相配合拌和4遍。先用旋转耕作机拌和,后跟铧犁或平地机将底部“素土〞n翻起。再用旋转耕作机拌和第2遍,用铧犁或平地要将底部料再翻起。随时检查、调整翻犁的深度,使稳定土层全部翻透。严禁在稳定土层和下承层之间残留一层“素土〞也应防止翻犁过深,过多破坏下承层的外表。③在没有专用拌和机械的情况下,也可以用缺口圆盘耙与多铧犁或平地机相配合,拌和二灰稳定中粒土和粗粒土〔但其拌和效果较差〕。用平地机或铧犁在前面翻拌用圆盘耙跟在后面拌和,即采用边翻边耙的方法。圆盘耙的速度应尽量快,使二灰与集料拌和均匀。共翻拌四遍,开始的两遍不应翻犁到底,以防二灰落到底部。后面的两遍,应翻犁到底,随时检查、调整翻犁的深度,使稳定土层全部翻透。〔2〕用洒水车将水均匀地喷洒在干拌后混合料上,洒水距离应长些,水车起洒处和另一端调头处都应超了拌和段2m以上。洒水车不应在正进行拌和的以及当天方案拌和的路段上调头和停留,防止局部水量过大。〔3〕拌和机械紧跟在洒水车的后面进行拌和。洒水及拌和过程中,应及时检查混合料的含水量,水分宜略大于最正确含水量度1%~2%,尤其在纵坡大的路段上应配合紧密,以减少水分流失。拌和过程中,要及时检查拌和深度,要使石灰工业废渣层全深都拌和均匀。拌和完成的标志是:混合料色泽一致,没有灰条、灰团、花面,没有粗细颗粒“窝〞,且水分适宜和均匀。对于二灰粒料,应先将石灰和粉煤灰拌和均匀,然后均匀地摊铺在粒料层上,再一起进行拌和。3、整形与碾压〔1〕整形①混合料拌和均匀后,先用平地机初步整平和整形。在直线段,平地机由两侧向路中心进行刮平。在平曲线段,平地机由内侧向外侧进行刮平。需要时,再返回刮一遍。②用拖拉机、平地机或轮胎压路机快速碾压1~2遍,以暴露潜在的不平整。③再用平地机如前述那样进行整形,并用上述机械再碾压一遍。④对于局部低洼处,应用齿耙将其表层5cm以上耙松,并用新拌和二灰混合料进行找补整平。再用平地机整形一次。⑤每次整形都要按照规定的坡度和路拱进行。特别要注意接缝处的整平,接缝必须顺适平整。在整形过程中,必须禁止任何车辆通行。初步整形后,检查混合料的松铺厚度。必要时应进行补料或减料。二灰土的松铺系数约为1.5~1.7,二灰粒料的松铺系数约为1.3~1.5。人工摊铺石灰煤渣〔土〕的松铺系数为1.6~1.8,石灰煤渣粒料为1.40。钢渣石灰为1.4~1.6,用机械拌和及机械整形时,松铺系数为1.2~1.4。〔2〕碾压整形后,当混合料处于最正确含水量士1%时,进行碾压。其压实厚度与压实度要求与水泥稳定土相同。如外表水分缺乏,应适当洒水。应用12以上三轮压路机、重型轮胎压路机或振动压路机在路基全宽内进行碾压。直线段由两侧路肩向路中心碾压。平曲线段由内侧路肩向向外侧路肩进行碾压。碾压时,后轮应重叠1/2的轮宽;后轮必须超过两段接缝。后轮压完路面全宽时,既为一遍。碾压到要求的密实度为止。一般需碾压6~8遍。压路机的碾压速度,头两遍以采用1档〔1.5~1.7km/h〕为宜,以后用2档〔n2.0~2.5km/h〕。在道路两侧,应多压2~3遍。用12~15t三轮压路机碾压时,每层的压实厚度不应超过15cm,用18~20t三轮压路机碾压时,每层的压实厚度不应超过20cm。对于二灰土,采用能量大的振动压路机碾压时,或对于二灰土,采用振动羊足碾与三轮压路机配合碾压时,每层的压实厚度可根据试验适当增加。压实厚度超过上述要求时,应分层铺筑,每层的最小压实厚度为10cm,下层宜稍厚。对于二灰土,应采用先轻型、后重型路机碾压。严禁压路机在已经完成的或正在碾压的路段上调头和急刹车,以保证稳定土层外表不受破坏。碾压过程中,二灰稳定土的外表应始终保持湿润。如外表水蒸发得快,应及时补洒少量的水。如有弹簧、松散、起皮待现象,应及时翻开重新拌和,或用其它方法处理,使其到达质量要求。在碾压结束之前,用平地机再终平一次,使其纵向顺适,路拱和超高符合设计要求。终平应仔细进行,必须将局部高出局部刮除并扫了路外,对于局部低洼之处,不再进行找补,留待铺筑面层时处理。5、其它1〕接缝和调头处理〔1〕横缝,两工作段的搭接局部,应采用对接式。前一段拌和整平后,留5~8m不进行碾压,后一段施工时,将前段留下末压局部,一起再进行拌和。如第二天接着向前施工,那么当天最后一段的末端缝可按此法处理。如第二天不接着向前施工,那么当天最后一段的工作缝应按下述方法处理:①在石灰工业废渣拌和结束后,在预定长度的末端,挖一条横贯全宽的槽,槽内放两根与压实厚度等厚的方木〔两根方木加在一起的长度等于铺筑层的宽度〕,方木的另一侧用素土回填3~5mm长,然后进行整形和碾压。②继续往前施工时,紧接的作业段拌和结束后,除去顶木,用混合料回填。靠近顶木末能拌和的一小段,应人工进行补充拌和。〔2〕纵缝。石灰工业废渣层的施工应该防止纵向接缝,在必须分两幅施工时,纵缝必须垂直相接,其处理方法与石灰稳定土相同。〔3〕拌和机械及其它机械不宜在已压成的石灰工业废渣层上调头。如必须在上进行调头;应采取措施〔如覆盖10cm厚的砂或砂砾〕,保护调头局部,使石灰工业废渣表层不受破坏。2〕路缘处理如石灰工业废渣层上为薄沥青路面,基层每边应较面层层展宽20cm以上。在基层全宽上喷洒透层沥青或设下封层。最好是满铺沥青面层,也可将沥青面层边缘以三角形向路肩抛出6~10cm。如设置路缘砖〔块〕时,必须注意防止路缘砖〔块〕阻滞路面外表水和结构层中水的排除。3〕在养及交通管理〔1〕石灰工业废渣层碾压完成后的第二天或第三天开始养生。通常采用洒水养生法。每天洒水的次数视气候条件而定,应始终保持外表潮湿或湿润。养生期一般为7d。也可借用透层沥青或下封层进行养生。〔2〕在养生期间,除洒水车外,应封闭交通。〔3〕养生期结束,应立即铺筑面层或做下封层。其要求与石灰稳定土相同。n〔4〕石灰工业废渣分层施工时,下层碾压完毕后,可以立即在铺筑另一层,不需专门的养生期。〔二〕中心站集中拌和〔厂拌〕法施工石灰工业废渣混合料可以在中心站用多种机械进行集中拌和。例如,强制式拌和机、双转轴浆叶式拌和机等。也可以用路拌机械或人工在场地上进行分批集中拌和。集中拌和时,必须掌握以下各个要点:土块、粉煤灰块要粉碎;配料要准确;含水量要略大于地佳值,使混合料运到现场、摊铺后碾压时的含水量能接近最正确值;拌和要均匀。石灰工业废渣的集中拌和流程如下图。棚仓料有料或堆煤或渣石灰粉灰煤混合料的拌和、摊铺、碾压、养生及其它问题的外理与石灰稳定土相同。棚仓料有料或堆手推车或装载机定比例进料沥干或洒水强制式拌和机或双转轴浆叶式拌和要或自落式拌和机〔用于含粘土的粒料〕下料斗出料皮带运输机充分消解手推车或装载机定比例进料下料斗细土或粒料料堆下料斗符合规定技术要求手推车或装载机定比例进料石灰工业废渣集中拌和工艺流程查看更多