- 2022-04-26 发布 |
- 37.5 KB |
- 9页
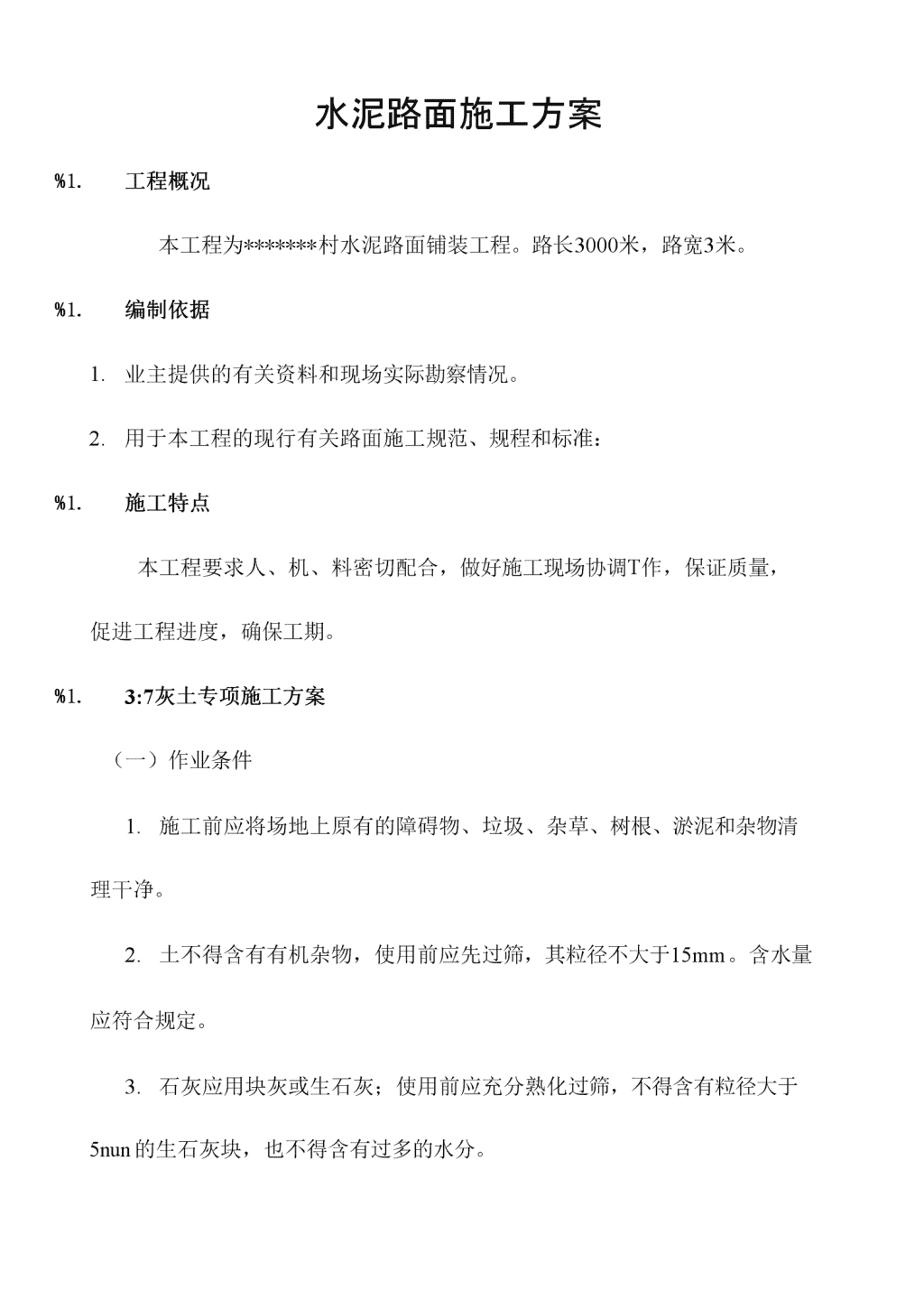
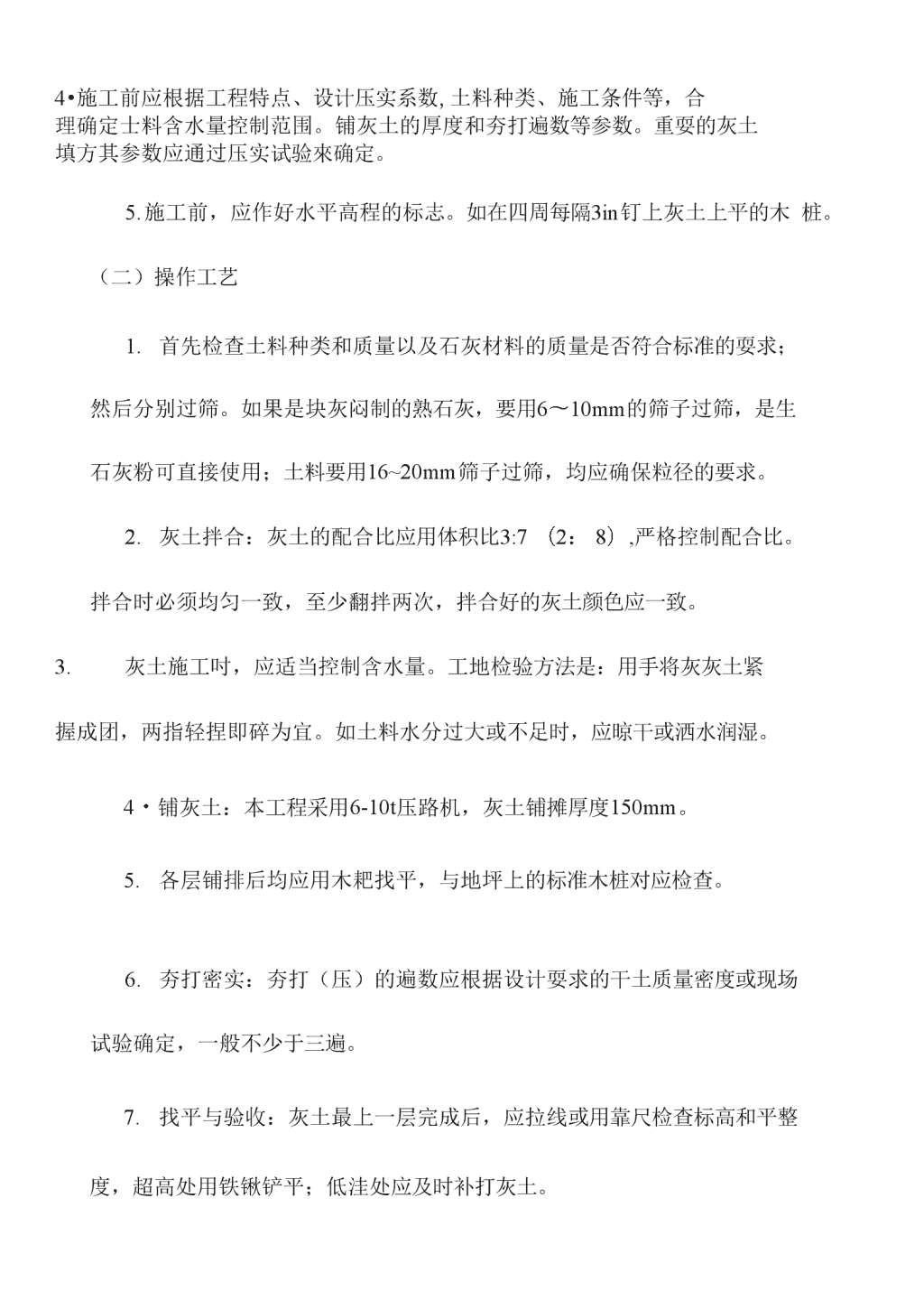
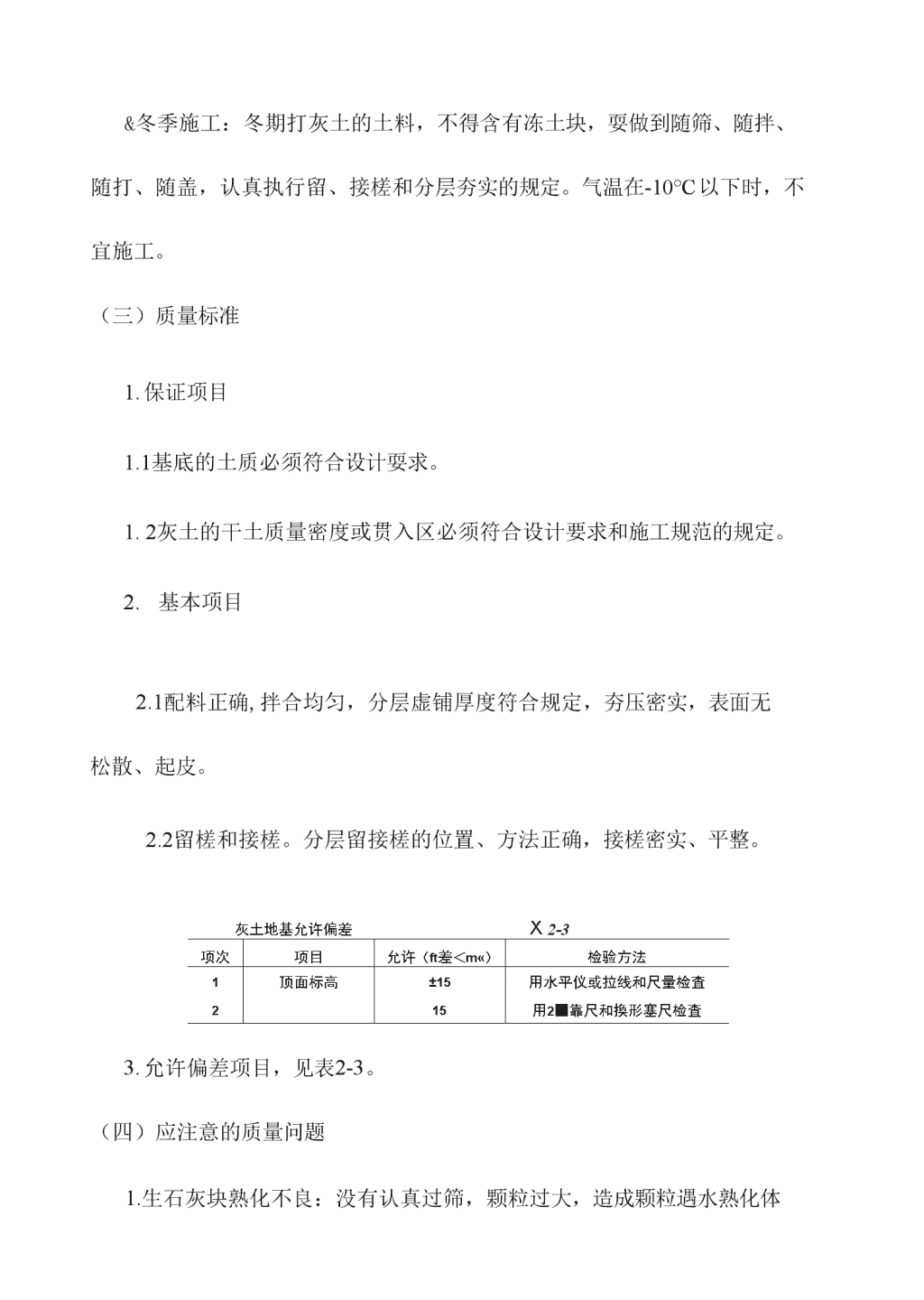
申明敬告: 本站不保证该用户上传的文档完整性,不预览、不比对内容而直接下载产生的反悔问题本站不予受理。
文档介绍
工程方案 砼路面施工方案801(定稿)
水泥路面施工方案%1.工程概况本工程为*******村水泥路面铺装工程。路长3000米,路宽3米。%1.编制依据1.业主提供的有关资料和现场实际勘察情况。2.用于本工程的现行有关路面施工规范、规程和标准:%1.施工特点本工程要求人、机、料密切配合,做好施工现场协调T作,保证质量,促进工程进度,确保工期。%1.3:7灰土专项施工方案(一)作业条件1.施工前应将场地上原有的障碍物、垃圾、杂草、树根、淤泥和杂物清理干净。2.土不得含有有机杂物,使用前应先过筛,其粒径不大于15mm。含水量应符合规定。3.石灰应用块灰或生石灰;使用前应充分熟化过筛,不得含有粒径大于5nun的生石灰块,也不得含有过多的水分。n4•施工前应根据工程特点、设计压实系数,土料种类、施工条件等,合理确定士料含水量控制范围。铺灰土的厚度和夯打遍数等参数。重耍的灰土填方其参数应通过压实试验來确定。5.施工前,应作好水平高程的标志。如在四周每隔3in钉上灰土上平的木桩。(二)操作工艺1.首先检查土料种类和质量以及石灰材料的质量是否符合标准的耍求;然后分别过筛。如果是块灰闷制的熟石灰,要用6〜10mm的筛子过筛,是生石灰粉可直接使用;土料要用16~20mm筛子过筛,均应确保粒径的要求。2.灰土拌合:灰土的配合比应用体积比3:7(2:8),严格控制配合比。拌合时必须均匀一致,至少翻拌两次,拌合好的灰土颜色应一致。3.灰土施工吋,应适当控制含水量。工地检验方法是:用手将灰灰土紧握成团,两指轻捏即碎为宜。如土料水分过大或不足时,应晾干或洒水润湿。4・铺灰土:本工程采用6-10t压路机,灰土铺摊厚度150mm。5.各层铺排后均应用木耙找平,与地坪上的标准木桩对应检查。6.夯打密实:夯打(压)的遍数应根据设计耍求的干土质量密度或现场试验确定,一般不少于三遍。7.找平与验收:灰土最上一层完成后,应拉线或用靠尺检查标高和平整度,超高处用铁锹铲平;低洼处应及时补打灰土。n&冬季施工:冬期打灰土的土料,不得含有冻土块,耍做到随筛、随拌、随打、随盖,认真执行留、接槎和分层夯实的规定。气温在-10°C以下时,不宜施工。(三)质量标准1.保证项目1.1基底的土质必须符合设计耍求。1.2灰土的干土质量密度或贯入区必须符合设计要求和施工规范的规定。2.基本项目2.1配料正确,拌合均匀,分层虚铺厚度符合规定,夯压密实,表面无松散、起皮。2.2留槎和接槎。分层留接槎的位置、方法正确,接槎密实、平整。灰土地基允许偏差X2-3项次项目允许(ft差<m«)检验方法1顶面标高±15用水平仪或拉线和尺量检査215用2■靠尺和換形塞尺检査3.允许偏差项目,见表2-3。(四)应注意的质量问题1.生石灰块熟化不良:没有认真过筛,颗粒过大,造成颗粒遇水熟化体n积膨胀,会将上层垫层、基础拱裂。务必认真对待熟石灰的过筛要求。1.灰土配合比不准确:土料和熟石灰没有认真过标准斗,或将石灰粉花洒在土的表面,拌合也不均匀,均会造成灰土地基软硬不一致,干士质量密度也相差过大。应认真做好计量工作。2.冬期防止造成冻胀等质量返工事故。五水泥路面专项施工方案(--)安装模板安装模板是保证线形、平整度、纵缝顺直度,板厚度宽度等各项技术指标的重要环节。在操作过程屮坚持“诚、固、准”的要求。“诚”是模板采用标准木模加工而成,木模高度与混凝土板厚一致,长度4米,接头处用专用配件牢固固定,接头耍紧密,不能有离缝、前后错茬和高低不平现象。“固”将固定好的模板底部用砂浆填塞密实,保证模板稳固。“准”是保持模板顶部标高的准确,用水准仪检查顶面标高平度误差控制在毫米以内。检查无误后,在模板内侧面均匀涂刷一薄层机油。(%1)混凝土拌制本标段路面T程混凝土,采用配有350搅拌机进行拌制。施工前事先在搅拌站内备足符合要求的砂、碎石、水泥等材料。搅拌第一盘混凝土拌合物前,先用适量的混凝土拌合物或砂浆搅拌,拌后排弃,然后再按规定的配合n比进行搅拌。搅拌机装料顺序为砂、水泥、碎石或碎石、水泥、砂,进料后,边搅拌边加水。混凝土拌合物的最短时间符合的规定,其搅拌最长时间不得n超过最短时间的三倍。(三)运输、卸料、摊铺混凝土混凝土拌合物采用手扶拖拉机运送到铺筑地点进行摊铺、振捣、抹面。混凝土拌合物摊铺前,要对模板的间隔、高度、润滑、支撐稳定情况和基层的平整、润湿情况、以及钢筋的位置和传力杆装置等进彳亍全面检查。磴运送抵达铺筑现场后,采用侧向或纵向方式将栓混合料直接卸在安装好侧模的的路槽内。卸料时,尽可能均匀,如发现有个别离析现彖,立即运回搅拌站重新搅拌均匀。摊铺时,将倾卸在路槽内的混凝土按摊铺厚度均匀地充满在模板范围内,摊铺时严禁抛掷和搂耙,以防离析。在模板附近摊铺时,用铁锹插捣几下,使灰浆捣出,以免发生蜂窝。(四)碗捣固与成型首先,采用插入式振动器按顺序插振一次。插入式振捣器的移动间距不宜大于其作用半径的1.5倍,其至模板的距离也不应大于振捣器作用半径的0.5倍,插点间距要均匀,防止漏振,在振捣时耍避免与模板和钢筋碰撞。振捣时间以拌和物停止下沉、不再冒气泡并泛出水泥浆为准,不宜过振。其次,用功率不小于2.2kw的平板振动器全面振动。振动时应重叠n10-20cm,同一位置不宜少于15秒,以不再冒气泡并泛出水泥浆为准。再则,用振动梁进一步拖拉振实并初步整平。振动往返拖拉2-3遍,使表面泛浆,并赶出气泡,振动梁移动的速度要缓慢而均匀,前进速度控制在每分钟1・5m左右。对不平之处辅以人工补填找平,补填时用较细的混合料原浆,严禁用纯砂浆填补。振动梁行进时,不允许屮途停留。牵引绳不可过短,以减少振动梁底部的倾斜。振动梁底缘应经常校正,保持设计线形。最后,再用平直的提浆棍进一步滚揉表面,使表面进一步提浆并调匀。(五)人工精修精修是保证路面平整度的把关工序。为达到要求的平整度,釆取“量”、“抹”结合的人工精修方法。“量”即用具有标准线且不易变形的铝合金直尺,紧贴模板顶而进行拉锯式搓刮,一边横向搓、一边纵向刮移,作最后一次检测殓顶面的平整度。一旦发现误差较大,立即进行修补。搓刮前,将模板顶面清理干净。搓刮后即可用直尺于两侧边部及屮间三处紧贴浆面各轻按一下,低凹处不出现压痕或印痕不明显,较高处印痕较深,据此进行找补精平。“抹”即人工用抹子将表面抹平。分两次进行,先找补精平,等磴表面收浆无泌水时,再作第二次精抹,以达到规范要求的路而平整度要求。n(六)养生混凝土浇筑完毕待磴凝固后应立即养生,拟采用覆盖旧麻袋、草袋等养n生方式。养生时间根据混凝土强度增长情况而定,一般宜为14〜21天。养护期满后方可将覆盖物清除,板面不留有痕迹。(七)切缝掌握好切缝时机是防止初期断板的重要措施。根据我们的经验,当混凝土达到强度6.0~12.0MPa时是进行切缝的最佳吋机,但气温突变时,我们将适当提早切缝时间,以防止混凝土面板产生不规则裂缝。切缝采用路面切缝机进行施工,切缝深度为1/3板厚,开始切缝前先调整刀片的进刀深度,切割时随时调整刀片切割方向,切缝时刀片用水进行冷却,水的压力不低于0.2MPao停止切缝时,先关闭旋扭开•头,将刀片提升到混凝土板面以上,停止运转。查看更多