- 2022-08-08 发布 |
- 37.5 KB |
- 33页
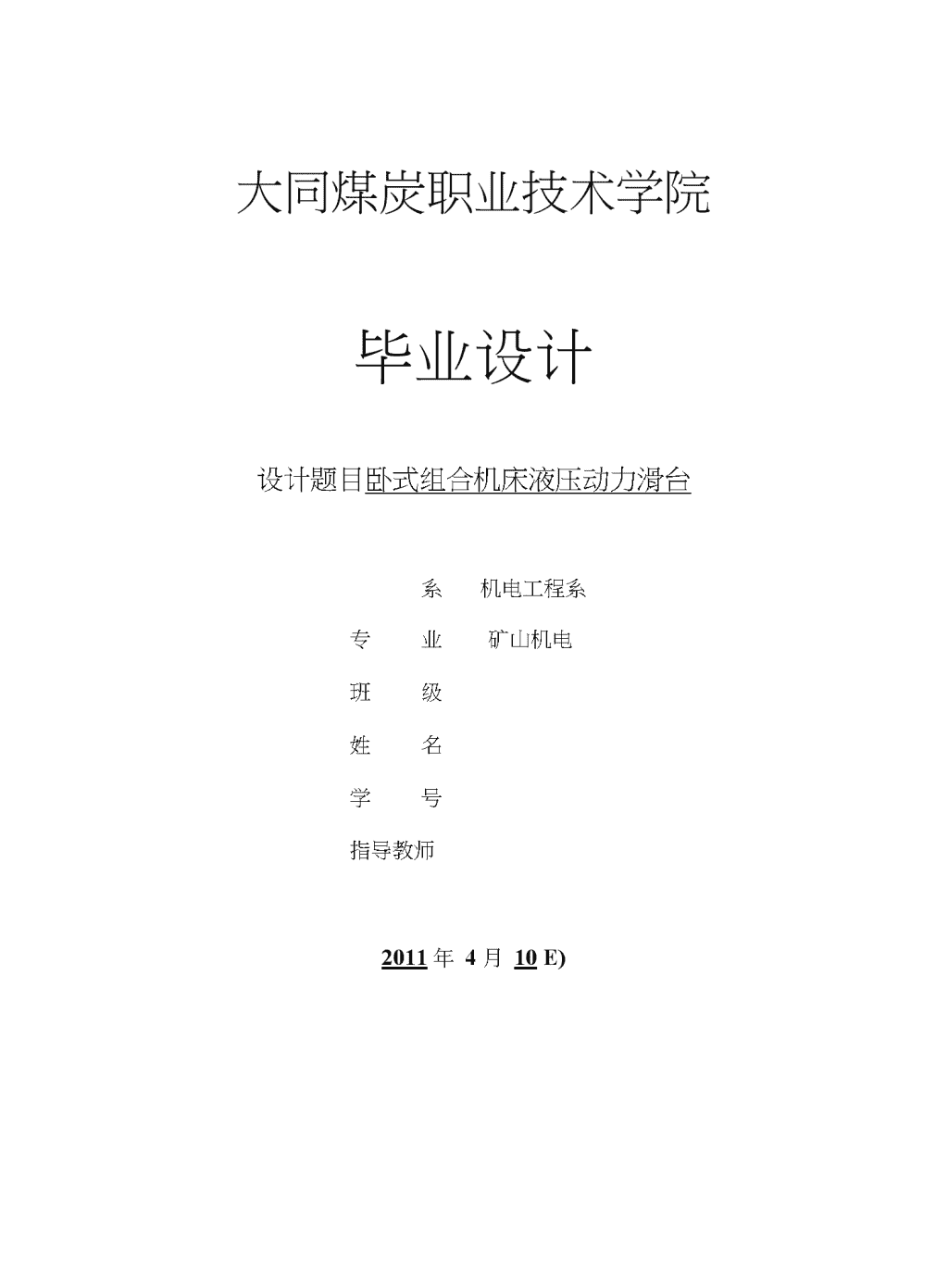
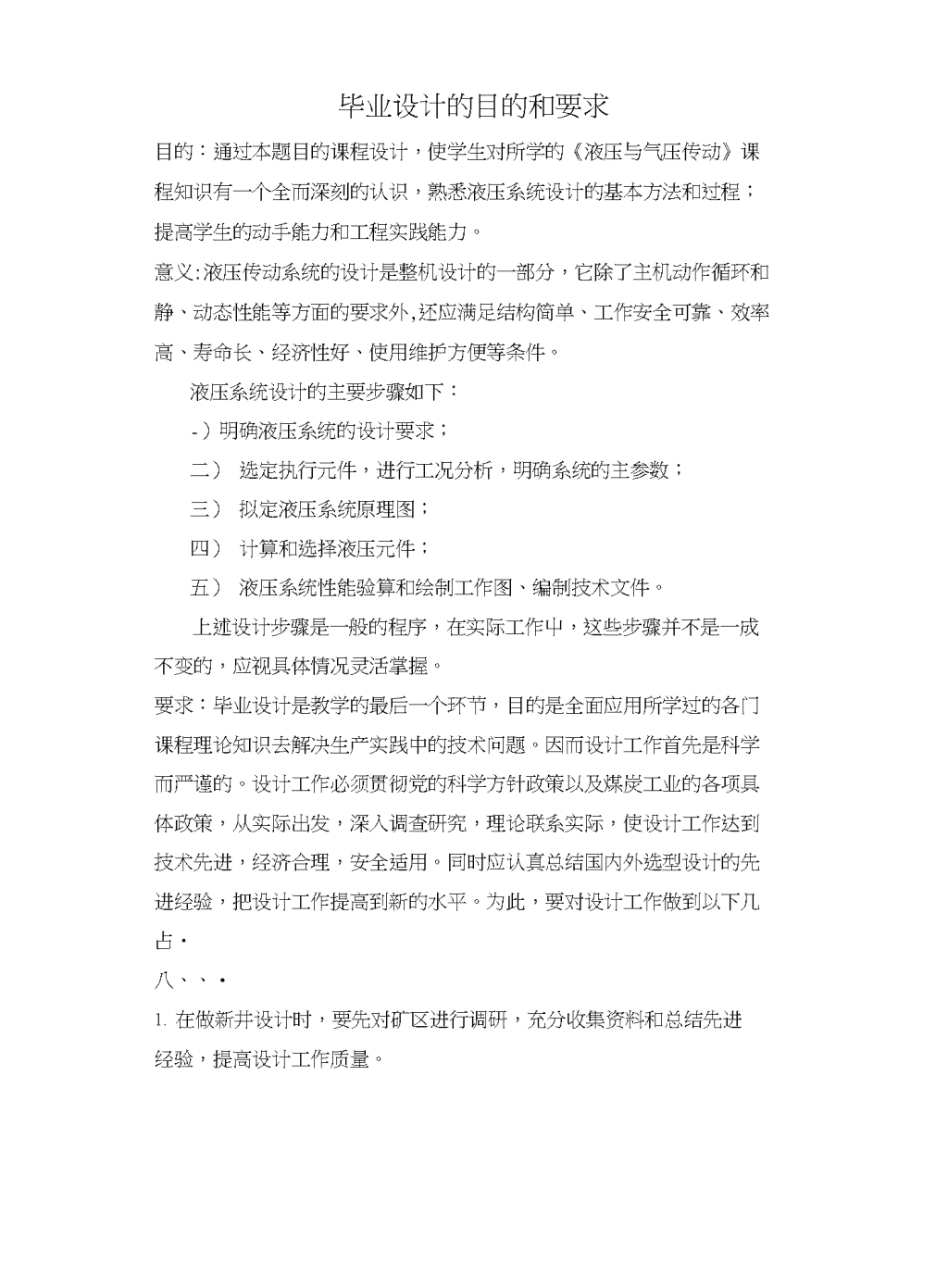
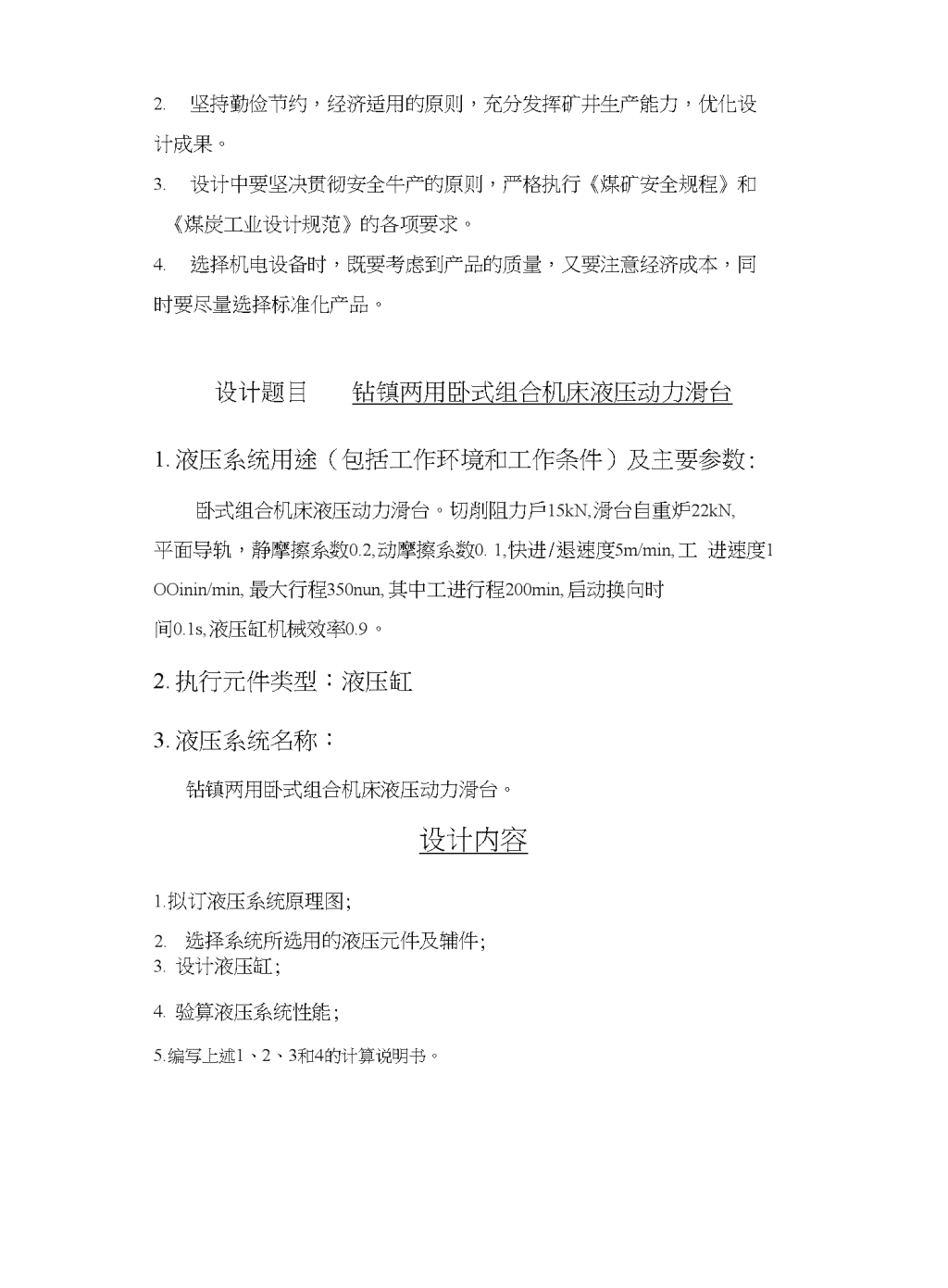
申明敬告: 本站不保证该用户上传的文档完整性,不预览、不比对内容而直接下载产生的反悔问题本站不予受理。
文档介绍
[工学]液压设计
大同煤炭职业技术学院毕业设计设计题目卧式组合机床液压动力滑台系机电工程系专业矿山机电班级姓名学号指导教师2011年4月10E)\n毕业设计的目的和要求目的:通过本题目的课程设计,使学生对所学的《液压与气压传动》课程知识有一个全而深刻的认识,熟悉液压系统设计的基本方法和过程;提高学生的动手能力和工程实践能力。意义:液压传动系统的设计是整机设计的一部分,它除了主机动作循环和静、动态性能等方面的要求外,还应满足结构简单、工作安全可靠、效率高、寿命长、经济性好、使用维护方便等条件。液压系统设计的主要步骤如下:-)明确液压系统的设计要求;二)选定执行元件,进行工况分析,明确系统的主参数;三)拟定液压系统原理图;四)计算和选择液压元件;五)液压系统性能验算和绘制工作图、编制技术文件。上述设计步骤是一般的程序,在实际工作屮,这些步骤并不是一成不变的,应视具体情况灵活掌握。要求:毕业设计是教学的最后一个环节,目的是全面应用所学过的各门课程理论知识去解决生产实践中的技术问题。因而设计工作首先是科学而严谨的。设计工作必须贯彻党的科学方针政策以及煤炭工业的各项具体政策,从实际出发,深入调查研究,理论联系实际,使设计工作达到技术先进,经济合理,安全适用。同时应认真总结国内外选型设计的先进经验,把设计工作提高到新的水平。为此,要对设计工作做到以下几占・八、、•1.在做新井设计时,要先对矿区进行调研,充分收集资料和总结先进经验,提高设计工作质量。\n1.坚持勤俭节约,经济适用的原则,充分发挥矿井生产能力,优化设计成果。2.设计中要坚决贯彻安全牛产的原则,严格执行《煤矿安全规程》和《煤炭工业设计规范》的各项要求。3.选择机电设备时,既要考虑到产品的质量,又要注意经济成本,同时要尽量选择标准化产品。设计题目钻镇两用卧式组合机床液压动力滑台1.液压系统用途(包括工作环境和工作条件)及主要参数:卧式组合机床液压动力滑台。切削阻力戶15kN,滑台自重炉22kN,平面导轨,静摩擦系数0.2,动摩擦系数0.1,快进/退速度5m/min,工进速度1OOinin/min,最大行程350nun,其中工进行程200min,启动换向时间0.1s,液压缸机械效率0.9。2.执行元件类型:液压缸3.液压系统名称:钻镇两用卧式组合机床液压动力滑台。设计内容1.拟订液压系统原理图;2.选择系统所选用的液压元件及辅件;3.设计液压缸;4.验算液压系统性能;5.编写上述1、2、3和4的计算说明书。\n目录1序言—1—2设计的技术要求和设计参数-2-3工况分析—3—3.1确定执行元件-3-3.2分析系统工况-3-3.3负载循环图和速度循环图的绘制5-3.4确定系统主要参数-6-3.4.1初选液压缸工作压力-6-3.4.2确定液压缸主要尺寸-6-3.4.3计算最大流量需求-8-3.5拟定液压系统原理图10-3.5.1速度控制回路的选择-10-3.5.2换向和速度换接回路的选择-11-3.5.3油源的选择和能耗控制-12-3.5.4压力控制回路的选择-14-3.6液压元件的选择-15-3.6.1确定液压泵和电机规格-16-3.6.2阀类元件和辅助元件的选择-18-3.6.3油管的选择-20-3.6.4油箱的设计~22-3.7液压系统性能的验算-24-3.7.1回路压力损失验算-24-3.7.2油液温升验算-24-4设计小结-26-5设计心得-27-6参考文献-28-\n1序言作为一种高效率的专用机床,组合机床在大批、大量机械加工生产中应用广泛。本次课程设计将以组合机床动力滑台液压系统设计为例,介绍该组合机床液压系统的设计方法和设计步骤,其中包括组合机床动力滑台液压系统的工况分析、主要参数确定、液压系统原理图的拟定、液压元件的选择以及系统性能验算等。组合机床是以通用部件为基础,配以按工件特定外形和加工工艺设计的专用部件和夹具而组成的半自动或自动专用机床。组合机床一般采用多轴、多刀、多工序、多面或多工位同时加工的方式,生产效率比通用机床高几倍至几十倍。组合机床兼有低成本和高效率的优点,在大批、大量生产中得到广泛应用,并可用以组成自动生产线。组合机床通常采用多轴、多刀、多面、多工位同时加工的方式,能完成钻、扩、饺、锂孔、攻丝、车、铳、磨削及其他精加工工序,生产效率比通用机床高几倍至几十倍。液压系统由于具有结构简单、动作灵活、操作方便、调速范围大、可无级连读调节等优点,在组合机床中得到了广泛应用。液压系统在组合机床上主要是用于实现工作台的直线运动和回转运动,如图1所示,如果动力滑台要实现二次进给,则动力滑台要完成的动作循环通常包括:原位停止T快进TI工进TII工进T死挡铁停留T快退T原位停止。\n快进工进死挡铁停留图1组合机床动力滑台工作循环2设计的技术要求和设计参数工作循环:快进T工进T快退T停止;系统设计参数如表1所示,动力滑台采用平而导轨,其静、动摩擦系数分别为&=0.2、&=0.1。表1设计参数参数数值切削阻力(N)15000滑台自重(N)22000快进、快退速度(m/min)5工进速度(mm/min)100最大行程(mm)350工进行程(mm)200启动换向吋间(s)0.1液压缸机械效率0.9\n3工况分析3.1确定执行元件金属切削机床的工作特点要求液压系统完成的主要是直线运动,因此液压系统的执行元件确定为液压缸。3.2分析系统工况在对液压系统进行工况分析时,本设计实例只考虑组合机床动力滑台所受到的工作负载、惯性负载和机械摩擦阻力负载,其他负载可忽略。(1)工作负载尺工作负载是在工作过程中由于机器特定的工作情况而产生的负载,对于金属切削机床液压系统来说,沿液压缸轴线方向的切削力即为工作负载,即戸尸15000N(2)惯性负载最大惯性负载取决于移动部件的质量和最大加速度,其中最大加速度可通过工作台最大移动速度和加速时间进行计算。已知启动换向时间为0.1s,工作台最大移动速度,即快进、快退速度为5m/min,因此惯性负载可表示为Av=m——=\tN=1871N220005x9.860x0.1(3)阻力负载阻力负载主要是工作台的机械摩擦阻力,分为静摩擦阻力和动摩擦\n阻力两部分。静摩擦阻力Ftj=f^N=Ffs=0.2x22000=4400N动摩擦阻力F^f^N=^=0.1x22000=2200N根据上述负载力计算结果,可得出液压缸在各个工况下所受到的负载力和液压缸所需推力情况,如表2所示。表2液压缸在各工作阶段的负载(单位:N)工况负载组成负载值F液压缸推力FT%起动4400N4889N加速4071N4523N快进F=Fa2200N2444N工进s+耳17200N19111N反向起动Ff4400N4889N加速F=Ffd+Fm4071N4523N快退F=52200N2444N注:此处未考虑滑台上的颠覆力矩的影响。\n3.3负载循环图和速度循环图的绘制根据表2中计算结果,绘制组合机床动力滑台液压系统的负载循环图如图2所示。1911144004071<24440.15-2444035-4071/-4400图2组合机床动力滑台液压系统负载循环图图2表明,当组合机床动力滑台处于工作进给状态时,负载力最大为19111N,其他工况下负载力相对较小。所设计组合机床动力滑台液压系统的速度循环图可根据己知的设计参数进行绘制,己知快进和快退速度m/min、快进行程£=350-200=150mm、工进行程12=200mm>快退行程L=350mm,工进速度v2=100mm/mino根据上述己知数据绘制组合机床动力滑台液压系统的速度循环图如图3所示。\n图3组合机床液压系统速度循坏图3.4确定系统主要参数3.4.1初选液压缸工作压力所设计的动力滑台在工进时负载最大,其值为19111N,其它工况时的负载都相对较低,参考第2章表3和表4按照负载大小或按照液压系统应用场合来选择工作压力的方法,初选液压缸的工作压力》=2.5MPa。3.4.2确定液压缸主要尺寸由于工作进给速度与快速运动速度差别较大,且快进、快退速度要求相等,从降低总流量需求考虑,应确定采用单杆双作用液压缸的差动连接方式。通常利用差动液压缸活塞杆较粗、可以在活塞杆中设置通油孔的有利条件,最好采用活塞杆固定,而液压缸缸体随滑台运动的常用\n典型安装形式。这种情况下,应把液压缸设计成无杆腔工作面积4是有杆腔工作面积&两倍的形式,即活塞杆直径d与缸筒直径D呈d=0.707Z)的关系。工进过程中,当孔被钻通时,由于负载突然消失,液压缸有可能会发生前冲的现象,因此液压缸的冋油腔应设置一定的背压(通过设置背压阀的方式),选取此背压值为o=0.8MPa。快进时液压缸虽然作差动连接(即有杆腔与无杆腔均与液压泵的來油连接),但连接管路中不可避免地存在着压降妙,且有杆腔的压力必须大于无杆腔,估算时取△p=0.5MPa。快退吋回油腔中也是有背压的,这时选取被压值p2=0.6MPao工进时液压缸的推力计算公式为F/叽=畑-人2P2=A\P\-(4/2)2,式屮:F负载力亦——液压缸机械效率Ax——液压缸无杆腔的有效作用面积A2——液压缸有杆腔的有效作用面积P\液压缸无杆腔压力P2——液压有无杆腔压力因此,根据已知参数,液压缸无杆腔的有效作用面积可计算为佔(£)5-少19111=0.0091m?液压缸缸筒直径为\nD=7(44)/^=7(4x0.009lxio6)/^=107.6mm由于有前述差动液压缸缸筒和活塞杆直径之间的关系,6/=0.7071),因此活塞杆直径为(1=0.707x107.6=76.1mm,根据GB/T2348—1993对液压缸缸筒内径尺寸和液压缸活塞杆外径尺寸的规定,圆整后取液压缸缸筒直径为Z)=l10mm,活塞杆直径为〃=80mm。此吋液压缸两腔的实际有效面积分别为:4=7rD2/4=9.5x10~3m2A2=7T(D2-d2)/4=4.48xIO-3m23.4.3计算最大流量需求工作台在快进过程屮,液压缸采用差动连接,此时系统所需要的流量为q快进=(昇1・力2)xvi=25.1L/min工作台在快退过程中所需要的流量为q快退2xV2=22.4/min工作台在工进过程屮所需要的流量为q工进=力1><力'=0.95L/min其中最大流量为快进流量为25.2L/mino\n根据上述液压缸直径及流量计算结果,进一步计算液压缸在各个工作阶段中的压力、流量和功率值,如表3所示。\n表3各工况下的主要参数值工况推力F'/N回油腔压力Pj/MPa进油腔压力P;/MPa输入流量q/L.min1输入功率P/Kw计算公式快进启动488901.42P,2民q=(ArA2)ViP=p】qp2=Pi+Ap加速45231.851.35恒速24441.430.9325.10.39工进191110.82.390.950.038P1=(F+p2A2)/Alq=A[V2P=piq快退起动488901.09Pl(F+p2AJ/A2q=A2v3P=Piq加速45230.62.28恒速24440.61.8222.40.679把表3中计算结果绘制成工况图,如图4所示。\n•M2JCCJ5CL03E.1.42二口5、0.930.15635■1,B2■2280.679图4液压系统工况图3.5拟定液压系统原理图根据组合机床液压系统的设计任务和工况分析,所设计机床对调速范围、低速稳定性有一定要求,因此速度控制是该机床要解决的主要问题。速度的换接、稳定性和调节是该机床液压系统设计的核心。此外,与所有液压系统的设计要求一样,该组合机床液压系统应尽可能结构简单,成本低,节约能源,工作可靠。3.5.1速度控制回路的选择工况图4表明,所设计组合机床液压系统在整个工作循环过程中所需要的功率较小,系统的效率和发热问题并不突出,因此考虑采用节流调速回路即可。虽然节流调速回路效率低,但适合于小功率场合,而且结构简单、成本低。该机床的进给运动要求有较好的低速稳定性和速度・\n负载特性,因此有三种速度控制方案可以选择,即进口节流调速、出口节流调速、限压式变量泵加调速阀的容积节流调速。钻镇加工属于连续切削加工,加工过程屮切削力变化不大,因此钻削过程中负载变化不大,采用节流阀的节流调速冋路即可。但由于在钻头钻入铸件表面及孔被钻通时的瞬间,存在负载突变的可能,因此考虑在工作进给过程中采用具有压差补偿的进口调速阀的调速方式,且在回油路上设置背压阀。由于选定了节流调速方案,所以油路采用开式循环冋路,以提高散热效率,防止油液温升过高。3.5.2换向和速度换接回路的选择所设计多轴钻床液压系统对换向平稳性的要求不高,流量不大,压力不高,所以选用价格较低的电磁换向阀控制换向回路即可。为便于实现差动连接,选用三位五通电磁换向阀。为了调整方便和便于增设液压夹紧支路,应考虑选用Y型中位机能。由前述计算可知,当工作台从快进转为工进时,进入液压缸的流量由25」L/min降为0.95L/min,可选二位二通行程换向阀来进行速度换接,以减少速度换接过程中的液压冲击,如图5所示。由于工作压力较低,控制阀均用普通滑阀式结构即可。由工进转为快退时,在回路上并联了一个单向阀以实现速度换接。为了控制轴向加工尺寸,提高换向位置精度,采用死挡块加压力继电器的行程终点转换控制。\n图5换向和速度切换冋路的选择3.5.3油源的选择和能耗控制表3表明,本设计多轴钻床液压系统的供油工况主要为快进、快退时的低压大流量供油和工进吋的高压小流量供油两种工况,若采用单个定量泵供油,显然系统的功率损失大、效率低。在液压系统的流量、方向和压力等关键参数确定后,述要考虑能耗控制,用尽量少的能量来完成系统的动作要求,以达到节能和降低生产成本的目的。在图4工况图的一个工作循环内,液压缸在快进和快退行程中要求油源以低压大流量供油,工进行程中油源以高压小流量供油。其中最大流量与最小流量之比纟叭/如油=25.1/0.95=26.4,而快进和快退所需的时间g与工进所需的时间乙分别为:4=(厶/q)+(/3/q)=[(60xl50)/(5xl000)+(60x350)/(5x1000)]=6st2=(l2/v2)=(60x200)/(0.1x1000)=120s\n上述数据表明,在一个工作循环中,液压油源在大部分时间都处于高压小流量供油状态,只有小部分时间工作在低压大流量供油状态。从提高系统效率、节省能量角度来看,如果选用单个定量泵作为整个系统的油源,液压系统会长时间处于大流量溢流状态,从而造成能量的大量损失,这样的设计显然是不合理的。如果采用单个定量泵供油方式,液压泵所输出的流量假设为液压缸所需要的最大流S25.lL/min,假设忽略油路屮的所有压力和流量损失,液压系统在整个工作循环过程中所需要消耗的功率估算为快进时P=0・93x25.1=0・39Kw工进时P=px^max=2.39x25.1=1Kw快退吋P=l.82x25.l=0.76Kw如果采用一个大流量定量泵和一个小流量定量泵双泵串联的供油方式,由双联泵组成的油源在工进和快进过程中所输出的流量是不同的,此吋液压系统在整个工作循环过程中所需要消耗的功率估算为快进时P=0.93x25.1=0.39Kw工进时,大泵卸荷,大泵出口供油压力几近于零,因此P=pxqma讦2.39x0.95=0.038Kw快退时P=l.82x25.l=0.76Kw除采用双联泵作为油源外,也可选用限压式变量泵作油源。但限压式变量泵结构复杂、成本高,且流量突变时液压冲击较大,工作平稳性差,最后确定选用双联液压泵供油方案,有利于降低能耗和生产成本,如图6所示。\n图6双泵供油油源3.5.4压力控制回路的选择由丁采用双泵供油回路,故采用液控顺序阀实现低压大流量泵卸荷,用溢流阀调整高压小流量泵的供油压力。为了便于观察和调整压力,在液压泵的岀口处、背压阀和液压缸无杆腔进口处设测压点。将上述所选定的液压回路进行整理归并,并根据需要作必要的修改和调整,最后画出液压系统原理图如图7所示。为了解决滑台快进时回油路接通油箱,无法实现液压缸差动连接的问题,必须在回油路上串接一个液控顺序阀10,以阻止油液在快进阶段返冋油箱。同时阀9起背压阀的作用。为了避免机床停止工作时回路中的油液流回油箱,导致空气进入系统,影响滑台运动的平稳性,图中添置了一个单向阀11。考虑到这台机床用于钻孔(通孔与不通孔)加工,对位置定位精度要求较高,图中增设了一个压力继电器60当滑台碰上死扌肖块后,系统压力升高,压力继电器发岀快退信号,操纵电液换向阀换向。在进油路上设有压力表开关和压力表,钻孔行程终点定位精度不高,采用行行程开关控制即可。\n03O3「1■双叶片液压泵2■三位五通电液阀3■行程阀4■调速阀5■单向阀6■单向阀7■顺序阀8■被压阀9■溢流阀10■单向阀11■过滤器12•压力表节接点13■单向阀14■压力继电器图7液压系统原理图3.6液压元件的选择木设计所使用液压元件均为标准液压元件,因此只需确定各液压元件的主要参数和规格,然后根据现有的液压元件产品进行选择即可。\n3.6.1确定液压泵和电机规格(1)计算液压泵的最大工作压力由于本设计采用双泵供油方式,根据图4液压系统的工况图,大流量液压泵只需在快进和快退阶段向液压缸供油,因此大流量泵工作压力较低。小流量液压泵在快速运动和工进时都向液压缸供油,而液压缸在工进时工作压力最大,因此对大流量液压泵和小流量液压泵的工作压力分别进行计算。根据液压泵的最大工作压力计算方法,液压泵的最大工作压力可表示为液压缸最大工作压力与液压泵到液压缸之间压力损失之和。对于调速阀进口节流调速回路,选取进油路上的总压力损失ZAp=0.8MPa,同时考虑到压力继电器的可靠动作要求压力继电器动作压力与最大工作压力的压差为0.5MPa,则小流量泵的最高工作压力可估算为Pp\=%x+P损+P继电器=(2・39+0.8+0.5)MPa=3.69MPa大流量泵只在快进和快退吋向液压缸供油,图4表明,快退吋液压缸中的工作压力比快进时大,如取进油路上的压力损失为0.5MPa,则大流量泵的最高工作压力为:Pp2-(P\+。损)=(2.28+0.5)MPa=2J^MPa(2)计算总流量表3表明,在整个工作循环过程中,液压油源应向液压缸提供的最大流量出现在快进工作阶段,为25」L/min,若整个冋路中总的泄漏量按液压缸输入流量的10%计算,则液压油源所需提供的总流量为:工作进给时,液压缸所需流量约为0.95L/min,但由于要考虑溢流阀的最小稳定溢流量3\nL/min,故小流量泵的供油量最少应为3.95L/min。据据以上液压油源最大工作压力和总流量的计算数值,上网或查阅有关样本,例如YUKEN口本油研液压泵样本,确定PV2R型双联叶片泵能够满足上述设计要求,因此选取PV2R12-6/33型双联叶片泵,其中小泵的排量为6mL/r,大泵的排量为33mL/r,若取液压泵的容积效率7=0.9,则当泵的转速〃=940r/min时,小泵的输出流量为vp外小=6x940x0.9/1000=5.076L/min该流量能够满足液压缸工进速度的需要。大泵的输出流量为外大=33*940*0.9/1000=27.918L/min双泵供油的实际输出流量为qp=[(6+33)x940xO.9/1000]L/min=32.994L/min该流量能够满足液压缸快速动作的需要。表4液压泵参数元件名称估计流量L/min—1规格额定流量Z/min_^额定压力MPa型号双联叶片泵—(5.1+27.9)最高工作压力为21MPaPV2R12—6/333.电机的选择由于液压缸在快退时输入功率最大,这时液压泵工作压力为2.78MPa,流量为32.994L/mino取泵的总效率〃卫=0.75,则液压泵驱动电动机所需的功率为:\nP==2.78x32.994加=2.04KWrfp60x0.75根据上述功率计算数据,此系统选取Y112M-6型电动机,其额定功率p=2.2KW,额定转速〃=940i7min。nn3.6.2阀类元件和辅助元件的选择图7液压系统原理图中包括调速阀、换向阀、单项阀等阀类元件以及滤油器、空气滤清器等辅助元件。1.阀类元件的选择根据上述流量及压力计算结果,对图7初步拟定的液压系统原理图屮各种阀类元件及辅助元件进行选择。其屮调速阀的选择应考虑使调速阀的最小稳定流量应小于液压缸工进所需流量。通过图7中5个单向阀的额定流量是各不相同的,因此最好选用不同规格的单向阀。图7中溢流阀2、背压阀9和顺序阀10的选择可根据调定压力和流经阀的额定流量来选择阀的型式和规格,其中溢流阀2的作用是调定工作进给过程屮小流量液压泵的供油压力,因此该阀应选择先导式溢流阀,连接在大流量液压泵出口处的顺序阀10用于使大流量液压泵卸荷,因此应选择外控式。背压阀9的作用是实现液压缸快进和工进的切换,同时在工进过程中做背压阀,因此采用内控式顺序阀。最后本设计所选择方案如表5所示,表中给出了齐种液压阀的型号及技术参数。\n表5阀类元件的选择序号元件名称估计流量L!min-^规格额定流量厶/min—1额定压力MPa型号1三位五通电磁阀661006.335D-1OOB2行程阀49.5636.322C-63BH3调速阀<166.3Q-6B4单向阀661006.31-100B5单向阀816.5256.3I-25B6背压阀90.475106.3B-10B7溢流阀4」3106.3Y-10B8单向阀11661006.31-100B9单向阀327.92636.3I-63B10单向阀45.1106.31-10B11顺序阀2&4636.3XY-63B2.过滤器的选择按照过滤器的流量至少是液压泵总流量的两倍的原则,取过滤器的流量为泵流量的2.5倍。由于所设计组合机床液压系统为普通的液压传动系统,对油液的过滤精度要求不高,故有9过滤器=Q泵入x2・5=(33x2.5)厶/min=82.5L/min因此系统选取通用型WU系列网式吸油过滤器,参数如表6所示。\n型号通径公称流量过滤精度尺寸mmL/minjLlmM(d)HD4WU—100X100-J32100100M42x2153082—3.空气滤清器的选择按照空气滤清器的流量至少为液压泵额定流量2倍的原则,即有9过滤器>"q卩=2x33厶/min=66/min选用EF系列液压空气滤清器,其主要参数如表7所示。表7液压空气滤清器\参数型号\过滤注油口径mm注油流量L/min空气流量L/min油过滤面积L/minAmmBmmammbmmcmm四只螺钉均布mm空气过滤精度mm油过滤精度“mE耳・32321410512010050047059064M5X80.279125注:液压油过滤精度可以根据用户的要求进行调节。3.6.3油管的选择图7中各元件间连接管道的规格可根据元件接口处尺寸来决定,液压缸进、出油管的规格可按照输入、排出油液的最大流量进行计算。由\n于液压泵具体选定Z后液压缸在各个阶段的进、出流量已与原定数值不同,所以应对液压缸进油和出油连接管路重新进行计算,如表8所示。表8液压缸的进、出油流量和运动速度流量、速度快进工进快退输入流量L/min—1孙二⑷“)/(4-心)_(9.5x32.994)_(9.5-4.48)=62.43—0.954=9〃=32.994排出流量L/min-'弘=(如1)/&4.48x62.43~9.5=29.444.48x0.95~9.5=0.448%=(44)/力2_9.5x32.994-4.48=69.96运动速度/•-1m/minV>=%4,-4)_32.994一9.5-4.48=6.570.95~9.5=0.1_32.994-4.48=7.36根据表8中数值,当油液在压力管中流速取3m/s时,可算得与液压缸无杆腔和有杆腔相连的油管内径分别为:取标准值20mm;I69.96X10^=2224mm\ttx3x103x60=2x32.994x1()6V^x3x!03x60mm=15.28/71/71,取标准值15mm。因此与液压缸相连的两根油管可以按照标准选用公称通径为020和015的无缝钢管或高压软管。如果液压缸采用缸筒固定式,则两根连接・2:1・管采用无缝钢管连接在液压缸缸筒上即可。如果液压缸采用活塞杆固定式,则与液压缸相连的两根油管可以采用无缝钢管连接在液压缸活塞杆\n上或采用高压软管连接在缸筒上。3.6.4油箱的设计1.油箱长宽高的确定油箱的主要用途是贮存油液,同时也起到散热的作用,参考相关文献及设计资料,油箱的设计可先根据液压泵的额定流量按照经验计算方法计算油箱的体积,然后再根据散热要求对油箱的容积进行校核。油箱中能够容纳的油液容积按JB/T7938—1999标准估算,取§=7吋,求得其容积为V=gxqp="32.994L=230.96L按JB/T7938—1999规定,取标准值Q250L。V=金=型=312.5L=0.3125m3依据0.80.8如果取油箱内长h、宽⑼、高h}比例为3:2:1,可得长为:厶=1107mm,宽Wj=738mm,高为h\=369mmo对于分离式油箱采用普通钢板焊接即可,钢板的厚度分别为:油箱箱壁厚3mm,箱底厚度5mm,因为箱盖上需要安装其他液压元件,因此箱盖厚度取为lOmmo为了易于散热和便于对油箱进行搬移及维护保养,取箱底离地的距离为160mm。因此,油箱基体的总长总宽总高为:长为:I=I、+2(=(1107+2x3)mm=111\mm宽为:w=W]+2(=738+2x3"?加=744加加\n高为:h=(10+Aj+5+160)加加=(10+369+5+160)加加=544加加为了更好的清洗油箱,取油箱底而倾斜角度为0.5°。1.隔板尺寸的确定为起到消除气泡和使油液中杂质有效沉淀的作用,油箱中应采用隔板把油箱分成两部分。根据经验,隔板高度取为箱内油面高度的3/4,根据上述计算结果,隔板的高度应为:—x-=——x-mm=229mm厶]x歼41.107x0.7384隔板的厚度与箱壁厚度和同,取为3mm。2.各种油管的尺寸油箱上冋油管直径可根据前述液压缸进、出油管直径进行选取,上述油管的最大内径为20mm,外径取为28mmo泄漏油管的尺寸远小于回油管尺寸,可按照各顺序阀或液压泵等元件上泄漏油口的尺寸进行选取。油箱上吸油管的尺寸可根据液压泵流量和管中允许的最人流速进行计算。知入=业=22:221厶/min二36.66L/minw泵入叶v0.9取吸油管屮油液的流速为1必。可得:d=2仇=2x7tV32994x1f)—彳2皿=o.O265m=26.5mm^xlx60液压泵的吸油管径应尽可能选择较大的尺寸,以防止液压泵内气穴的发生。因此根据上述数据,按照标准取公称直径为^=32mm,外径为42mmo\n3.7液压系统性能的验算本例所设计系统属压力不高的中低压系统,无迅速起动、制动需求,而且设计屮已考虑了防冲击可调节环节及相关防冲击措施,因此不必进行冲击验算。这里仅验算系统的压力损失,并对系统油液的温升进行验算。3.7.1回路压力损失验算由于系统的具体管路布置尚未确定,整个冋路的压力损失无法估算,仅只阀类元件对压力损失所造成的影响可以看得出来,供调定系统中某些压力值时参考。3.7.2油液温升验算液压传动系统在工作时,有压力损失、容积损失和机械损失,这些损失所消耗的能量多数转化为热能,使油温升高,导致油的粘度下降、油液变质、机器零件变形等,影响正常工作。为此,必须控制温升AT在允许的范围内,如一般机床47=25〜30°C;数控机床47^25°C;粗加工机械、工程机械和机车车辆△庐35〜40°Co液压系统的功率损失使系统发热,单位时间的发热量0(kW)可表示为(t>=P\-P2式屮P\——系统的输入功率(即泵的输入功率)(kW);系统的输岀功率(即液压缸的输岀功率)(kW)o若在一个工作循环屮有几个工作阶段,则可根据各阶段的发热量求出系统的平均发热量对于木次设计的组合机床液压系统,其工进过程在整个工作循环中所占时间比例为\n120a二—-—二'1+‘2二s=0966=96.6%120+4.22因此系统发热和油液温升可用工进时的发热情况来计算。工进时液压缸的有效功率(即系统输出功率)为p=Fv=1911\x—W=31.85"-0.032K炉°60这时大流量泵通过顺序阀10卸荷,小流量泵在高压下供油,所以两泵的总输出功率(即系统输入功率)为:P_pp\qp\+pp2qp20.3x(—)2xl06x—xl0-3+3.69x106x^xlO-3___63:6060KW0.75x103=0.418KW由此得液压系统的发热量为耳二弓―人=(0.418—0.032)KW=0.386KW即可得油液温升近似值:Z1T=0/(肋)=0.386/(9*W3*6.5*10_2*2502/3)=15.6°C温升小于普通机床允许的温升范围,因此液压系统中不需设置冷却器。4设计小结1•系统采用了“双叶片液压泵-调速阀-被压阀”式调速回路。它保证液压缸稳定的低速运动,较好的速度刚性和较大的调速范圉。回油路上加被压阀防止空气进入系统,并能使滑台承受负向负载。2.系统采用了双叶片液压泵和液压缸差动链接两项措施来实现块进,可得到较大的快进速度,•且能量利用也比较合理。滑台停止运动时,采用了单向阀,被压阀,溢流阀等来使液压泵在低压时卸荷,既减少能量损失,又控制油路保持一定的压力,以保证下一工作循环的顺利启动。3.系统采用了行程阀和顺序阀等实现快进与工进的换接,不仅简化了油路和电路,而且使动作可靠,转换的位置精度也比较高,由于速度\n比较低,采用了阀体切换和调速阀串联回路,既保证了必要的转换精度,又使油路的布局比较简单,灵活。定位准确,重复精度高。4•采用了电液阀来切换主油路,使滑台的换向更加平稳,冲击和噪声小。同时,电液换向阀的五通结构使滑台进和退时分别从两条油路回油,这样滑台快退时,系统没有被压,也减少了压力损失。总之,这个液压系统设计比较合理,它使用的元件不多,但却能完成较为复杂的半自动工作循环,且性能良好。\n5设计心得通过本次课程设计,让我深深的体会到了自身的不足之处,以及平日学习的粗略。这次课程设计,使我对液压系统有了更加全面的认识和理解,了解了液压知识在生活中的广泛应用前景。这次设计增强了自己动手能力与理论结合实际能力,同时提高了自己的独立思考能力。虽然设计过程并不是一帆风顺,但是在老师的指导与鼓励,同学的帮助下,也算是达成了本次设计的初衷,在这次课程设计中,要运用到多科课程所学知识,在查找资料的同时,复习与巩固了以前所学习的知识,同时提高了自己综合运用所学课程知识的能力。最后感谢学校,老师能够给予我们这么一次提高自身能力的机会。\n6参考文献[1]左健民•液压与气压传动第三版•机械工业出版社,2006.[2]雷天觉•新编液压工程手册•北京•机械工业出版社,199&[3]成大先•机械设计手册:第4、5卷•北京:化学工业出版社,2009.[4]丁树模.液压传动•第二版•机械工业出版社,2009[5]王春行.液压控制系统・第二版,北京•机械工业岀版社,2000.查看更多