- 2021-05-10 发布 |
- 37.5 KB |
- 20页
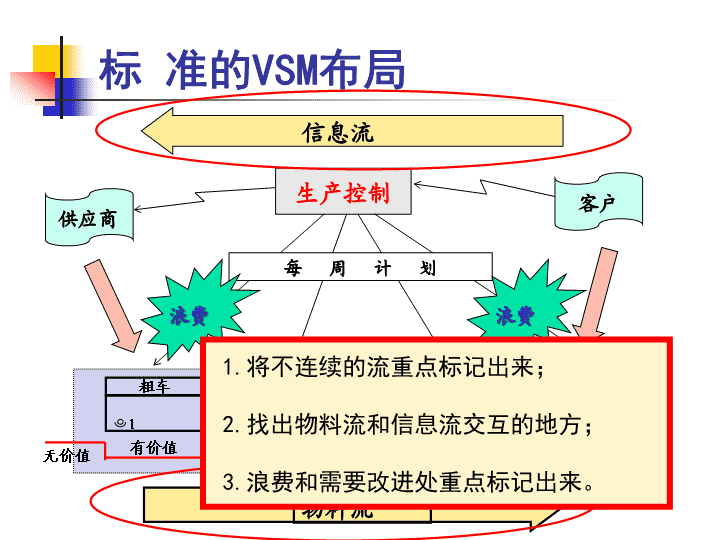
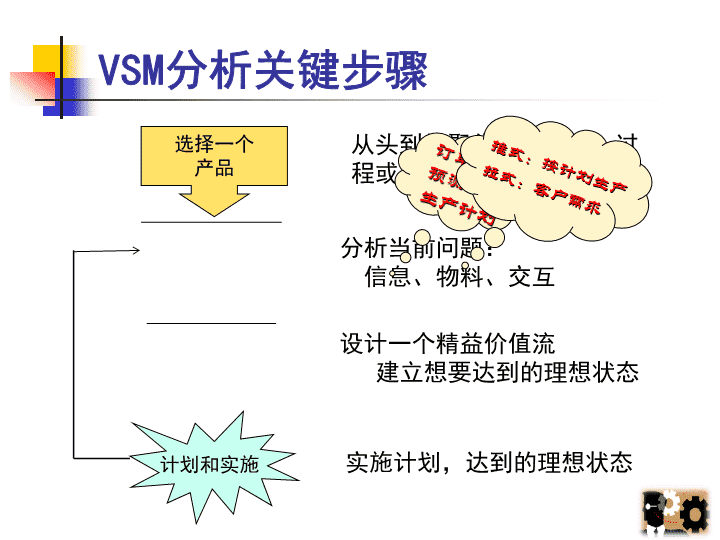
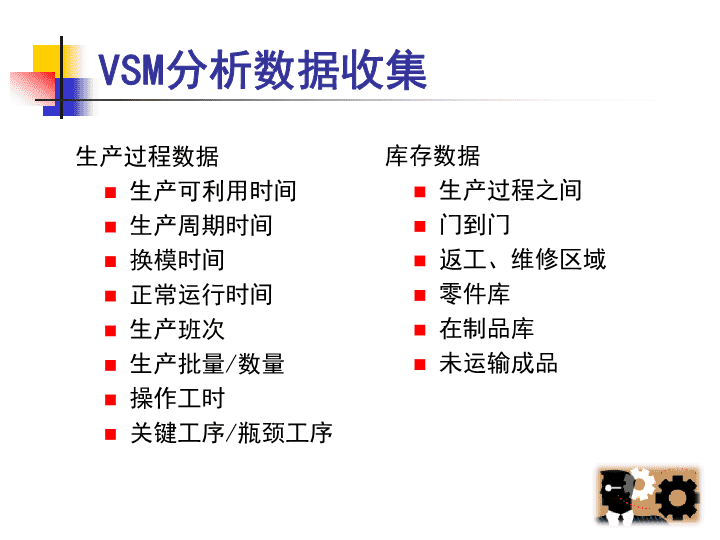
申明敬告: 本站不保证该用户上传的文档完整性,不预览、不比对内容而直接下载产生的反悔问题本站不予受理。
文档介绍
生产线平衡改善
标 准的 VSM 布局 钻孔 1 粗车 1 精车、抛光 1 供应商 生产控制 客户 每 周 计 划 物料流 信息流 浪费 浪费 有价值 无价值 1. 将不连续的流重点标记出来; 2. 找出物料流和信息流交互的地方; 3. 浪费和需要改进处重点标记出来。 VSM 分析关键步骤 选择一个 产品 计划和实施 从头到位聚焦一个产品、过程或服务,搜集 相关数据 分析当前问题: 信息、物料、交互 设计一个精益价值流 建立想要达到的理想状态 实施计划,达到的理想状态 订单 预测 生产计划 推式:按计划生产 拉式:客户需求 VSM 分析数据收集 生产过程数据 生产可利用时间 生产周期时间 换模时间 正常运行时间 生产班次 生产批量 / 数量 操作工时 关键工序 / 瓶颈工序 库存数据 生产过程之间 门到门 返工、维修区域 零件库 在制品库 未运输成品 VSM 分析案例 —1. 基本资料 4 粗车 钻孔 精车、抛光 检验 工艺流程 普通车床 普通钻床 抛光机 专用测量仪 加工设备 人员配备 1人 1人 1人 1人 时间节拍 顺序 时间 备注 1 10 s 人工 2 45 s 机动 3 5 s 人工 总 60 s 顺序 时间 备注 1 10 s 人工 2 20 s 机动 3 5 s 人工 总 35 s 顺序 时间 备注 1 10 s 人工 2 40 s 机动 3 5 s 人工 总 55 s 顺序 时间 备注 1 25 s 人工 总 25 s 布置形式 单机布置,轮番生产(生产批量为50个/料箱), 专人(1人)进行物料搬运作业 粗 加 工 车 床 待 加工 已 加工 已 加工 待 加工 工 具 切 削 废 料 钻孔 机 待 加工 已 加工 工具 废料 抛 光 机 待 加工 已 加工 工 具 废料 已 加工 检验台 完 工件 VSM 分析案例 —2.VMS 图 5 生产车间 裝配工位 700 件/日 料盘 = 25 件 2 班制 检验 加工时间=25 s 换模时间=0 使用率=100% 有效时间25200 s 两班制 1 精车、抛光 加工时间=55 s 换模时间=0 使用率=100% 有效时间25200 s 两班制 1 钻孔 加工时间=35 s 换模时间=0 使用率=100% 有效时间25200 s 两班制 1 粗车 加工时间=60 s 换模时间=0 使用率=100% 有效时间25200 s 两班制 1 手推车 2次/班 原料、半成品 仓 库 700 件/日 料盘 = 25 件 2 班制 手推车 1次/班 I 350件 I 175件 I 175件 I 175件 I 175件 车间调度部门 MRP 每周计划 每月预测 每月预测 每日计划 每 周 计 划 VSM 分析案例 —3. 需求分析 6 每天的平均产量 = 700 件 生产节拍 = 等待及运输时间1= 等待及运输时间2= VSM 分析案例 —2.VMS 图 7 生产车间 裝配工位 700 件/日 料盘 = 25 件 2 班制 检验 加工时间=25 s 换模时间=0 使用率=100% 有效时间25200 s 两班制 1 精车、抛光 加工时间=55 s 换模时间=0 使用率=100% 有效时间25200 s 两班制 1 钻孔 加工时间=35 s 换模时间=0 使用率=100% 有效时间25200 s 两班制 1 粗车 加工时间=60 s 换模时间=0 使用率=100% 有效时间25200 s 两班制 1 手推车 2次/班 原料、半成品 仓 库 700 件/日 料盘 = 25 件 2 班制 手推车 1次/班 I 350件 I 175件 I 175件 I 175件 I 175件 车间调度部门 MRP 每周计划 每月预测 每月预测 每日计划 每 周 计 划 60 s 35 s 55 s 25 s 0 .5d 0 .25d 0 .25d 0 .25d 0 .25d 一个产品的生产过程中,产品生产时间(产生价值时间)=175 s, 生产过程时间(包括物流等时间)=1.5 d, 生产时间占了2‰。 8 生产线平衡案例 3--- 物流分析法 DMAIC 镁 合金 涂装 主要 产品 Q 1. 背景介紹 S 1. 背景介紹 镁 合金 涂装生产流程 重工 重工 一底 首捡 面 2 面 1 捡包 移印 补土 二底 一底研磨 二底研磨 贴纸 入库 暂存 贴纸 一底 二底 面漆 移印 检包 镁 合金 涂装 主要 工艺 1. 背景介紹 多 处 、 大量 WIP 堆 放 物流路线迂回交叉 不必要的生产间断 镁合金涂装工段 与前工站距离 3 米! 完全 可以 合 并! 2. 现状描述 WIP, Lead Time, UPPH LT 缩 短 UPPH 提升 WIP 降低 精益 生 产 3. 改善过程 -- D- M - A-I-C 推式生產! 每日計劃 价值流图 WIP=2 , 625pcs I I I I I LT =39H UPPH=1.21pcs 以 Q 系列机种为例进行测量 3. 改善过程 --D -M- A-I-C WIP 多 LT 长 UPPH 低 人 机 推式生产 产能不匹配 良率低 管理效率低下 质量意识弱 因果 分析 环 法 料 路线迂回 重工不規范 作业分配不合理 排配不合理 洁净度不达标 工 站 不 连续 品 种 多 3. 改善过程 --D - M -A -I-C 拉 动设 置 节拍设 定 人力重排 流程 优 化 布局改善 推式生产观念 作 业 分配 不合理 重工不規范 工 站 不 连续 路线 迂回 价值流未来图 拉动生产 每日计划仅向检包发出 3. 改善过程 --D - M -A -I-C 实现价值流未来图三步走 流程 优 化 布局改善 节 拍 设 定 人力重排 拉 动设 置 3. 改善过程 --D - M - A- I -C 3. 改善过程 --D - M - A- I -C 顾客需求:約 1.4K /10H 理想出 货节 拍 为 25 秒 3. 改善过程 --D - M - A- I -C 貼紙 捡包 重工网絡排对模型 非 重工 + 重工量 = 產出 貼紙工艺: ... 3. 改善过程 --D - M - A- I -C查看更多