- 2021-10-21 发布 |
- 37.5 KB |
- 3页
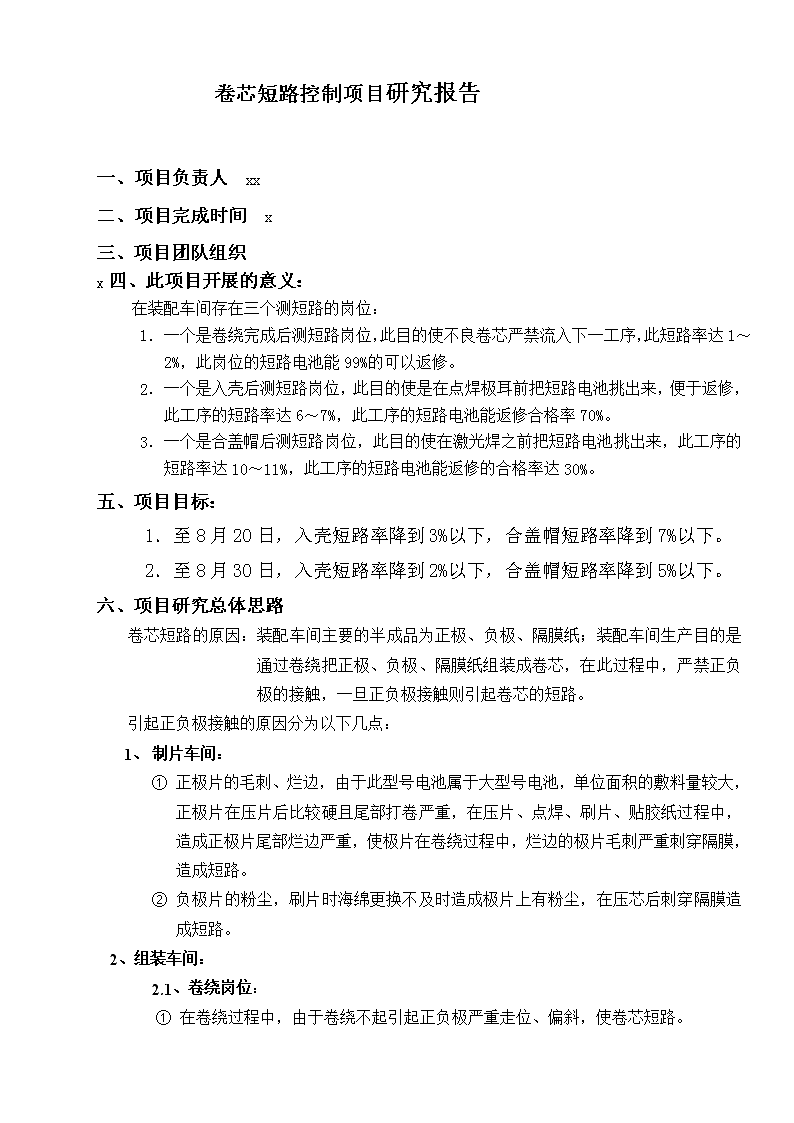
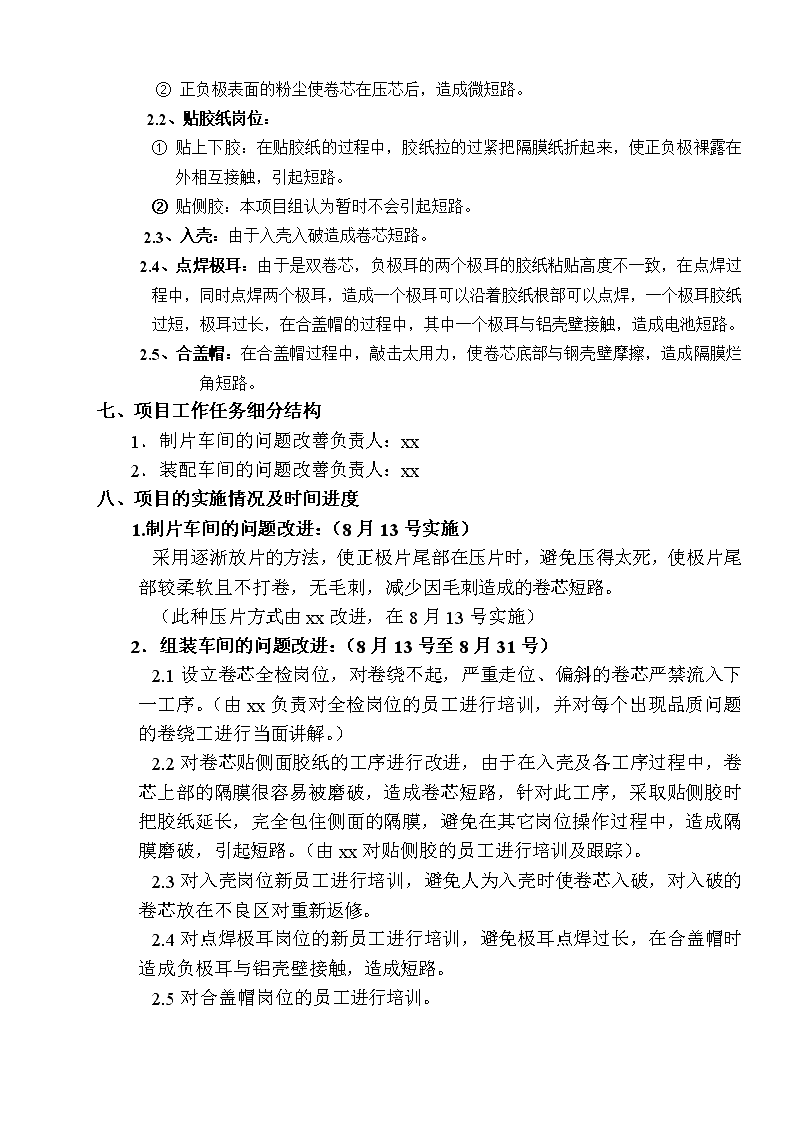
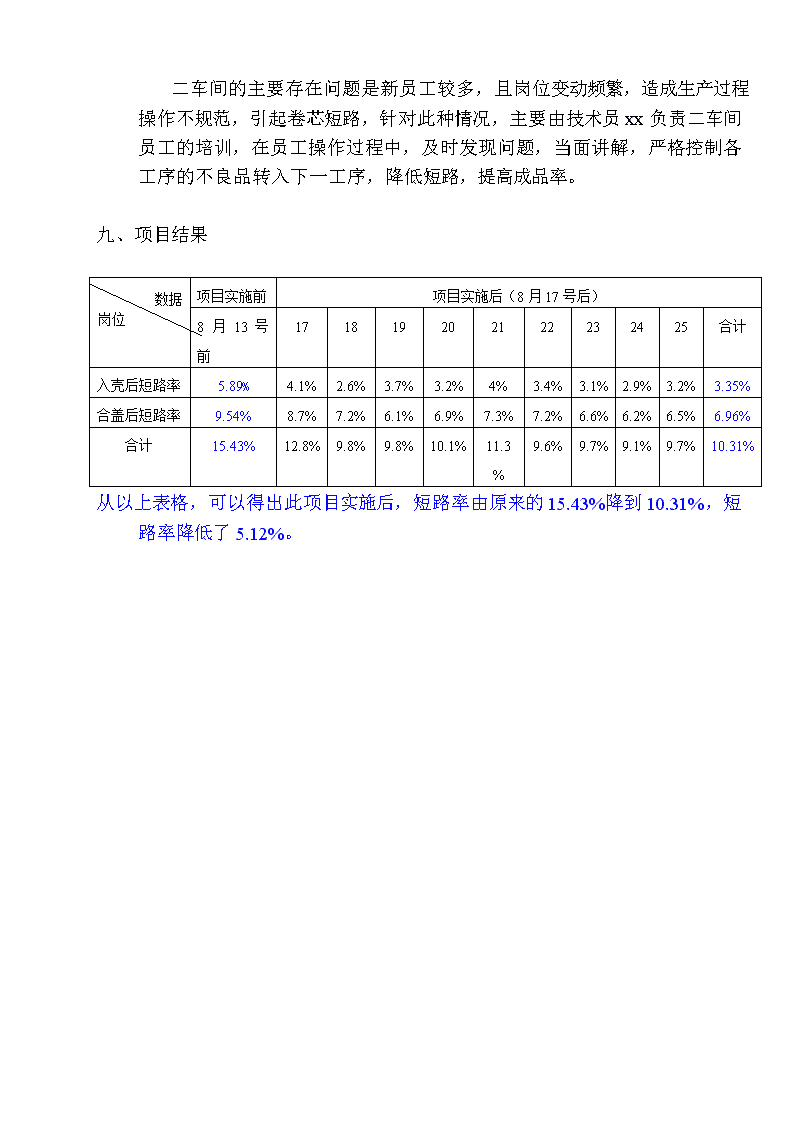
申明敬告: 本站不保证该用户上传的文档完整性,不预览、不比对内容而直接下载产生的反悔问题本站不予受理。
文档介绍
卷绕车间卷芯短路控制项目研究报告
卷芯短路控制项目研究报告 一、 项目负责人 xx 二、 项目完成时间 x 三、项目团队组织 x四、此项目开展的意义: 在装配车间存在三个测短路的岗位: 1. 一个是卷绕完成后测短路岗位,此目的使不良卷芯严禁流入下一工序,此短路率达1~2%,此岗位的短路电池能99%的可以返修。 2. 一个是入壳后测短路岗位,此目的使是在点焊极耳前把短路电池挑出来,便于返修,此工序的短路率达6~7%,此工序的短路电池能返修合格率70%。 3. 一个是合盖帽后测短路岗位,此目的使在激光焊之前把短路电池挑出来,此工序的短路率达10~11%,此工序的短路电池能返修的合格率达30%。 五、项目目标: 1.至8月20日,入壳短路率降到3%以下,合盖帽短路率降到7%以下。 2.至8月30日,入壳短路率降到2%以下,合盖帽短路率降到5%以下。 六、项目研究总体思路 卷芯短路的原因:装配车间主要的半成品为正极、负极、隔膜纸;装配车间生产目的是通过卷绕把正极、负极、隔膜纸组装成卷芯,在此过程中,严禁正负极的接触,一旦正负极接触则引起卷芯的短路。 引起正负极接触的原因分为以下几点: 1、 制片车间: ① 正极片的毛刺、烂边,由于此型号电池属于大型号电池,单位面积的敷料量较大,正极片在压片后比较硬且尾部打卷严重,在压片、点焊、刷片、贴胶纸过程中,造成正极片尾部烂边严重,使极片在卷绕过程中,烂边的极片毛刺严重刺穿隔膜,造成短路。 ② 负极片的粉尘,刷片时海绵更换不及时造成极片上有粉尘,在压芯后刺穿隔膜造成短路。 2、组装车间: 2.1、卷绕岗位: ① 在卷绕过程中,由于卷绕不起引起正负极严重走位、偏斜,使卷芯短路。 ① 正负极表面的粉尘使卷芯在压芯后,造成微短路。 2.2、贴胶纸岗位: ① 贴上下胶:在贴胶纸的过程中,胶纸拉的过紧把隔膜纸折起来,使正负极裸露在外相互接触,引起短路。 ② 贴侧胶:本项目组认为暂时不会引起短路。 2.3、入壳:由于入壳入破造成卷芯短路。 2.4、点焊极耳:由于是双卷芯,负极耳的两个极耳的胶纸粘贴高度不一致,在点焊过程中,同时点焊两个极耳,造成一个极耳可以沿着胶纸根部可以点焊,一个极耳胶纸过短,极耳过长,在合盖帽的过程中,其中一个极耳与铝壳壁接触,造成电池短路。 2.5、合盖帽:在合盖帽过程中,敲击太用力,使卷芯底部与钢壳壁摩擦,造成隔膜烂角短路。 七、项目工作任务细分结构 1.制片车间的问题改善负责人:xx 2.装配车间的问题改善负责人:xx 八、项目的实施情况及时间进度 1.制片车间的问题改进:(8月13号实施) 采用逐淅放片的方法,使正极片尾部在压片时,避免压得太死,使极片尾部较柔软且不打卷,无毛刺,减少因毛刺造成的卷芯短路。 (此种压片方式由xx改进,在8月13号实施) 2.组装车间的问题改进:(8月13号至8月31号) 2.1设立卷芯全检岗位,对卷绕不起,严重走位、偏斜的卷芯严禁流入下一工序。(由xx负责对全检岗位的员工进行培训,并对每个出现品质问题的卷绕工进行当面讲解。) 2.2对卷芯贴侧面胶纸的工序进行改进,由于在入壳及各工序过程中,卷芯上部的隔膜很容易被磨破,造成卷芯短路,针对此工序,采取贴侧胶时把胶纸延长,完全包住侧面的隔膜,避免在其它岗位操作过程中,造成隔膜磨破,引起短路。(由xx对贴侧胶的员工进行培训及跟踪)。 2.3对入壳岗位新员工进行培训,避免人为入壳时使卷芯入破,对入破的卷芯放在不良区对重新返修。 2.4对点焊极耳岗位的新员工进行培训,避免极耳点焊过长,在合盖帽时造成负极耳与铝壳壁接触,造成短路。 2.5对合盖帽岗位的员工进行培训。 二车间的主要存在问题是新员工较多,且岗位变动频繁,造成生产过程操作不规范,引起卷芯短路,针对此种情况,主要由技术员xx负责二车间员工的培训,在员工操作过程中,及时发现问题,当面讲解,严格控制各工序的不良品转入下一工序,降低短路,提高成品率。 九、项目结果 数据 岗位 项目实施前 项目实施后(8月17号后) 8月13号前 17 18 19 20 21 22 23 24 25 合计 入壳后短路率 5.89% 4.1% 2.6% 3.7% 3.2% 4% 3.4% 3.1% 2.9% 3.2% 3.35% 合盖后短路率 9.54% 8.7% 7.2% 6.1% 6.9% 7.3% 7.2% 6.6% 6.2% 6.5% 6.96% 合计 15.43% 12.8% 9.8% 9.8% 10.1% 11.3% 9.6% 9.7% 9.1% 9.7% 10.31% 从以上表格,可以得出此项目实施后,短路率由原来的15.43%降到10.31%,短路率降低了5.12%。查看更多