- 2021-10-20 发布 |
- 37.5 KB |
- 4页
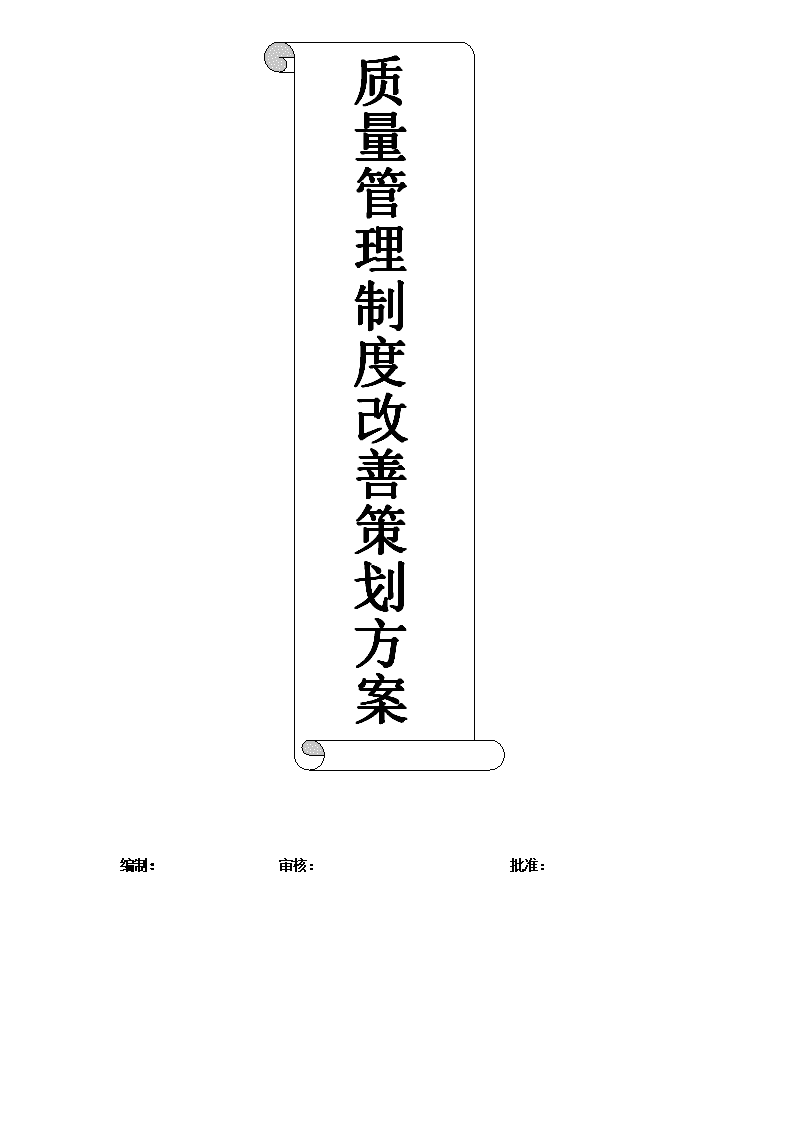
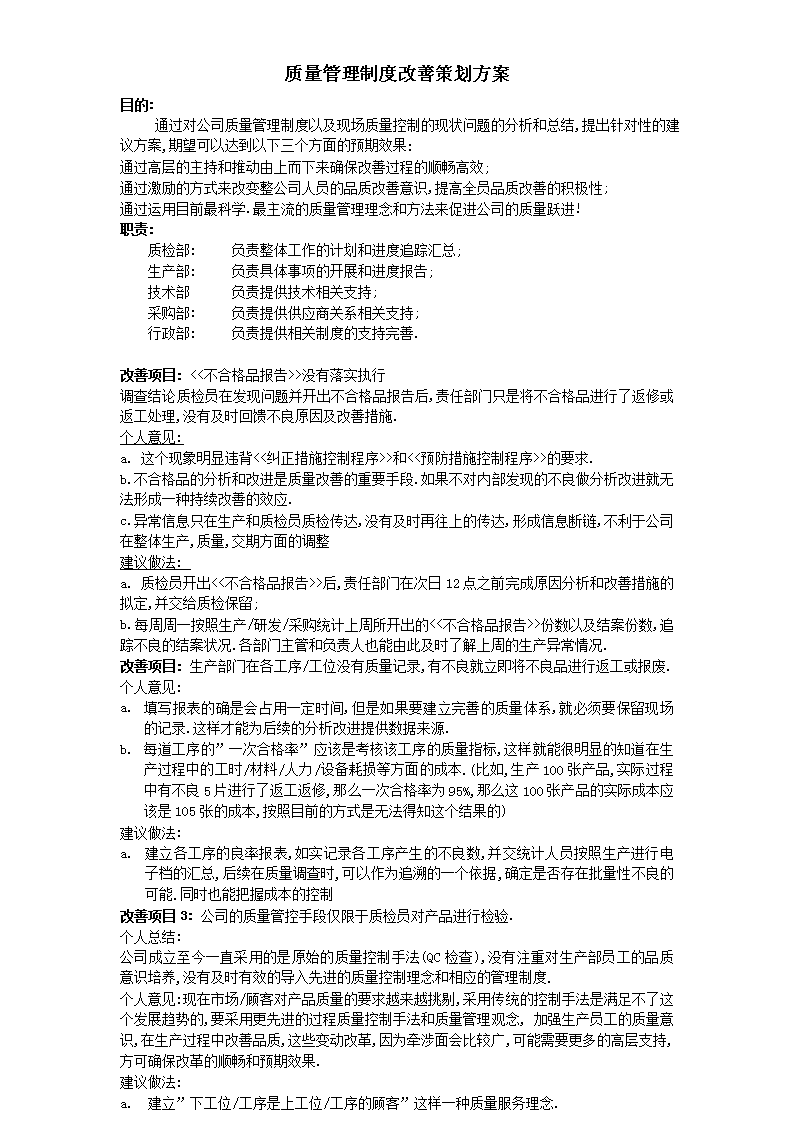
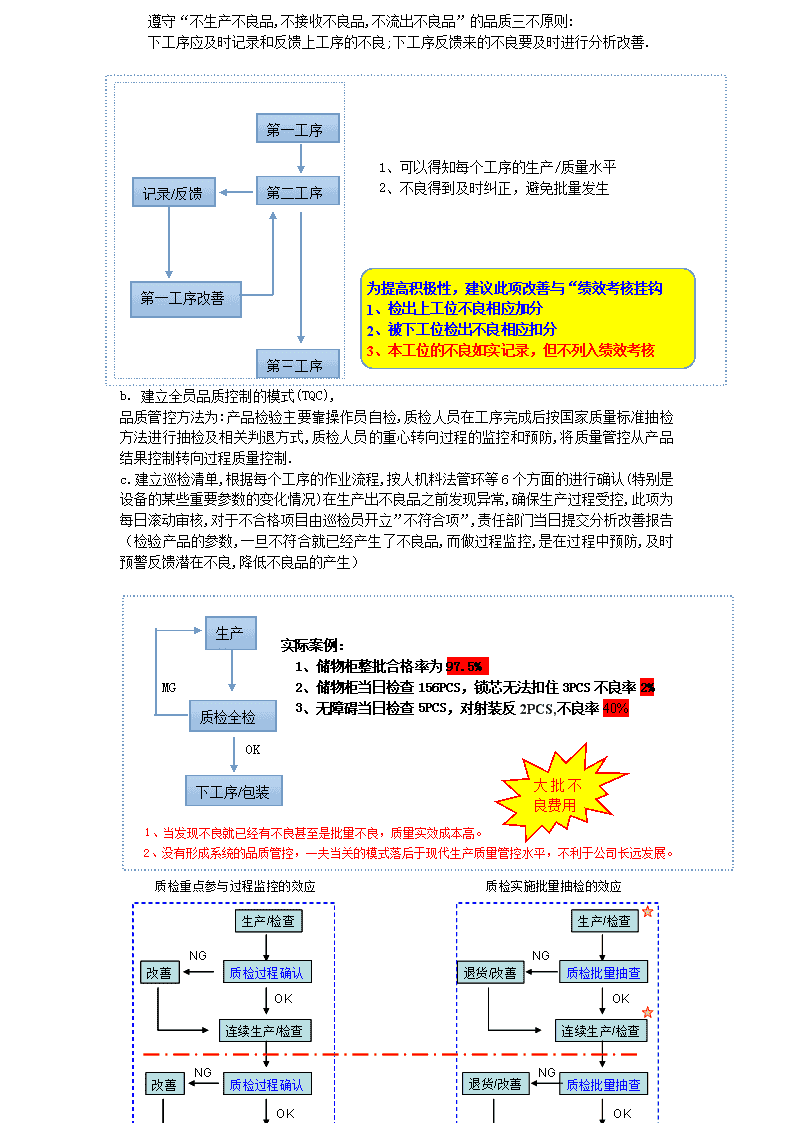
申明敬告: 本站不保证该用户上传的文档完整性,不预览、不比对内容而直接下载产生的反悔问题本站不予受理。
文档介绍
质量管理制度改善策划方案
质量管理制度改善策划方案 编制: 审核: 批准: 质量管理制度改善策划方案 目的: 通过对公司质量管理制度以及现场质量控制的现状问题的分析和总结,提出针对性的建议方案,期望可以达到以下三个方面的预期效果: 通过高层的主持和推动由上而下来确保改善过程的顺畅高效; 通过激励的方式来改变整公司人员的品质改善意识,提高全员品质改善的积极性; 通过运用目前最科学.最主流的质量管理理念和方法来促进公司的质量跃进! 职责: 质检部: 负责整体工作的计划和进度追踪汇总; 生产部: 负责具体事项的开展和进度报告; 技术部 负责提供技术相关支持; 采购部: 负责提供供应商关系相关支持; 行政部: 负责提供相关制度的支持完善. 改善项目: <<不合格品报告>>没有落实执行 调查结论 质检员在发现问题并开出不合格品报告后,责任部门只是将不合格品进行了返修或返工处理,没有及时回馈不良原因及改善措施. 个人意见: a. 这个现象明显违背<<纠正措施控制程序>>和<<预防措施控制程序>>的要求. b.不合格品的分析和改进是质量改善的重要手段.如果不对内部发现的不良做分析改进就无法形成一种持续改善的效应. c.异常信息只在生产和质检员质检传达,没有及时再往上的传达,形成信息断链,不利于公司在整体生产,质量,交期方面的调整 建议做法: a. 质检员开出<<不合格品报告>>后,责任部门在次日12点之前完成原因分析和改善措施的拟定,并交给质检保留; b. 每周周一按照生产/研发/采购统计上周所开出的<<不合格品报告>>份数以及结案份数,追踪不良的结案状况.各部门主管和负责人也能由此及时了解上周的生产异常情况. 改善项目: 生产部门在各工序/工位没有质量记录,有不良就立即将不良品进行返工或报废. 个人意见: a. 填写报表的确是会占用一定时间,但是如果要建立完善的质量体系,就必须要保留现场的记录.这样才能为后续的分析改进提供数据来源. b. 每道工序的”一次合格率”应该是考核该工序的质量指标,这样就能很明显的知道在生产过程中的工时/材料/人力/设备耗损等方面的成本.(比如,生产100张产品,实际过程中有不良5片进行了返工返修,那么一次合格率为95%,那么这100张产品的实际成本应该是105张的成本,按照目前的方式是无法得知这个结果的) 建议做法: a. 建立各工序的良率报表,如实记录各工序产生的不良数,并交统计人员按照生产进行电子档的汇总,后续在质量调查时,可以作为追溯的一个依据,确定是否存在批量性不良的可能.同时也能把握成本的控制 改善项目3: 公司的质量管控手段仅限于质检员对产品进行检验. 个人总结: 公司成立至今一直采用的是原始的质量控制手法(QC检查),没有注重对生产部员工的品质意识培养,没有及时有效的导入先进的质量控制理念和相应的管理制度. 个人意见:现在市场/顾客对产品质量的要求越来越挑剔,采用传统的控制手法是满足不了这个发展趋势的,要采用更先进的过程质量控制手法和质量管理观念, 加强生产员工的质量意识,在生产过程中改善品质,这些变动改革,因为牵涉面会比较广,可能需要更多的高层支持,方可确保改革的顺畅和预期效果. 建议做法: a. 建立”下工位/工序是上工位/工序的顾客”这样一种质量服务理念. 遵守“不生产不良品,不接收不良品,不流出不良品”的品质三不原则: 下工序应及时记录和反馈上工序的不良;下工序反馈来的不良要及时进行分析改善. 第一工序 第二工序 1、可以得知每个工序的生产/质量水平 记录/反馈 2、不良得到及时纠正,避免批量发生 为提高积极性,建议此项改善与“绩效考核挂钩 1、 检出上工位不良相应加分 2、 被下工位检出不良相应扣分 3、 本工位的不良如实记录,但不列入绩效考核 第一工序改善 第三工序 b. 建立全员品质控制的模式(TQC), 品质管控方法为:产品检验主要靠操作员自检,质检人员在工序完成后按国家质量标准抽检方法进行抽检及相关判退方式,质检人员的重心转向过程的监控和预防,将质量管控从产品结果控制转向过程质量控制. c. 建立巡检清单,根据每个工序的作业流程,按人机料法管环等6个方面的进行确认(特别是设备的某些重要参数的变化情况)在生产出不良品之前发现异常,确保生产过程受控, 此项为每日滚动审核,对于不合格项目由巡检员开立”不符合项”,责任部门当日提交分析改善报告(检验产品的参数,一旦不符合就已经产生了不良品,而做过程监控,是在过程中预防,及时预警反馈潜在不良,降低不良品的产生) 生产 实际案例: 1、储物柜整批合格率为97.5% MG 2、储物柜当日检查156PCS,锁芯无法扣住3PCS不良率2% 质检全检 3、无障碍当日检查5PCS,对射装反2PCS,不良率40% 大批不良费用 OK 下工序/包装 1、当发现不良就已经有不良甚至是批量不良,质量实效成本高。 2、没有形成系统的品质管控,一夫当关的模式落后于现代生产质量管控水平,不利于公司长远发展。 d.开展品质活动. 如“零缺陷活动”,具体做法:按自然月为单位,以生产部为竞争单位,从自然月的第一天开始计算”零缺陷第1天”,如果持续无不良退货,则日期累加”零缺陷第N天”.当该月出现1次不良退货时,则日期重新计算为”零缺陷第1天”.月底评出天数最高的部门为质量先进单位,给予适当奖励. 如“QCC改善圈”,具体做法:各个单位自主进行组队(无部门的限制),组成一个改善团队,拟定一个改善课题(疑难杂症或长期存在的问题现象),并通过一系列的方法对其进行改善,最终得出改善的评价和效益评估. 每月/或者每个季度对优秀的QCC圈成员进行奖励. 如“质量失败履历”,具体做法:当发生客户投诉(属生产责任)或发生重大异常时,责任部门按照固定格式将该投诉/事故的图片.原因.改善措施制作成一个履历卡,悬挂在责任点,便于后续该责任点的新员工能够准确的了解历史不良,避免再发. 如“提案改善表彰”,具体做法:鼓励所有人员在各自负责的职能范围内,提出对生产效率.产品品质.工作流程等方面的改善建议,制定对应的评价等级并予以奖励.依次提高所有人员在工作过程中对效率.质量.流程面的合理性的思考,形成一种全员积极改善的企业文化.能很好的促进公司的发展查看更多