- 2021-05-14 发布 |
- 37.5 KB |
- 34页
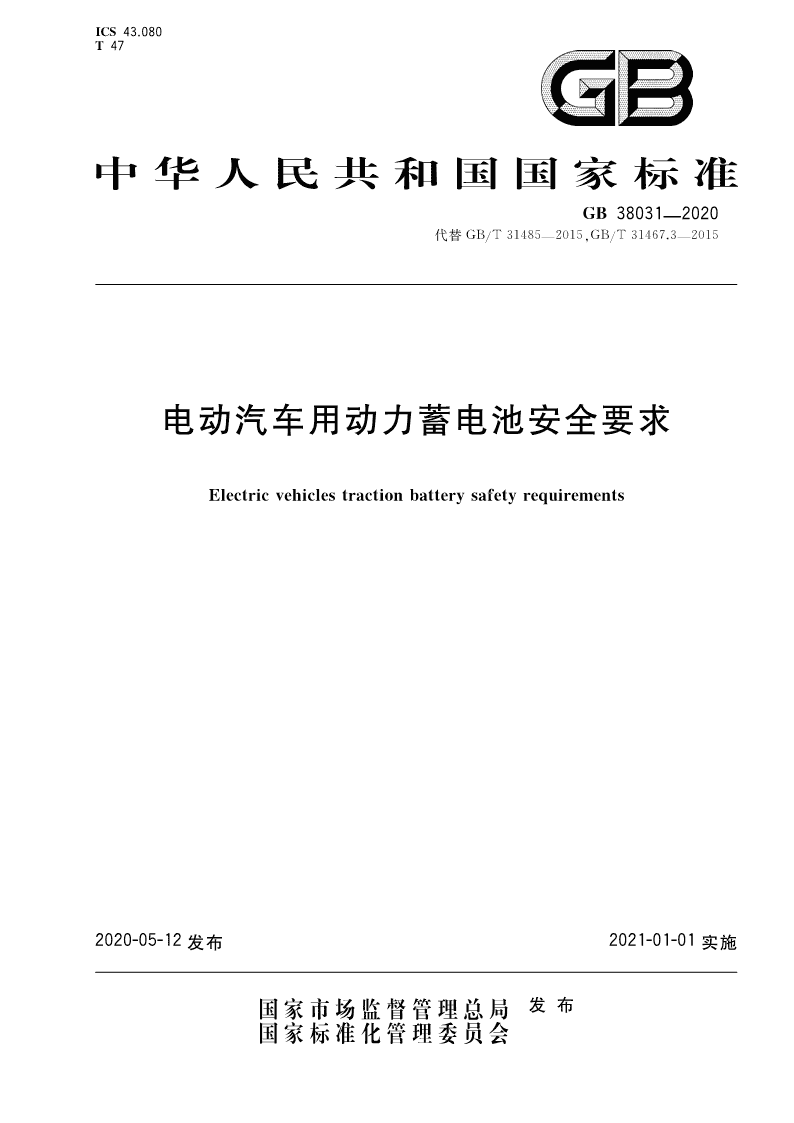
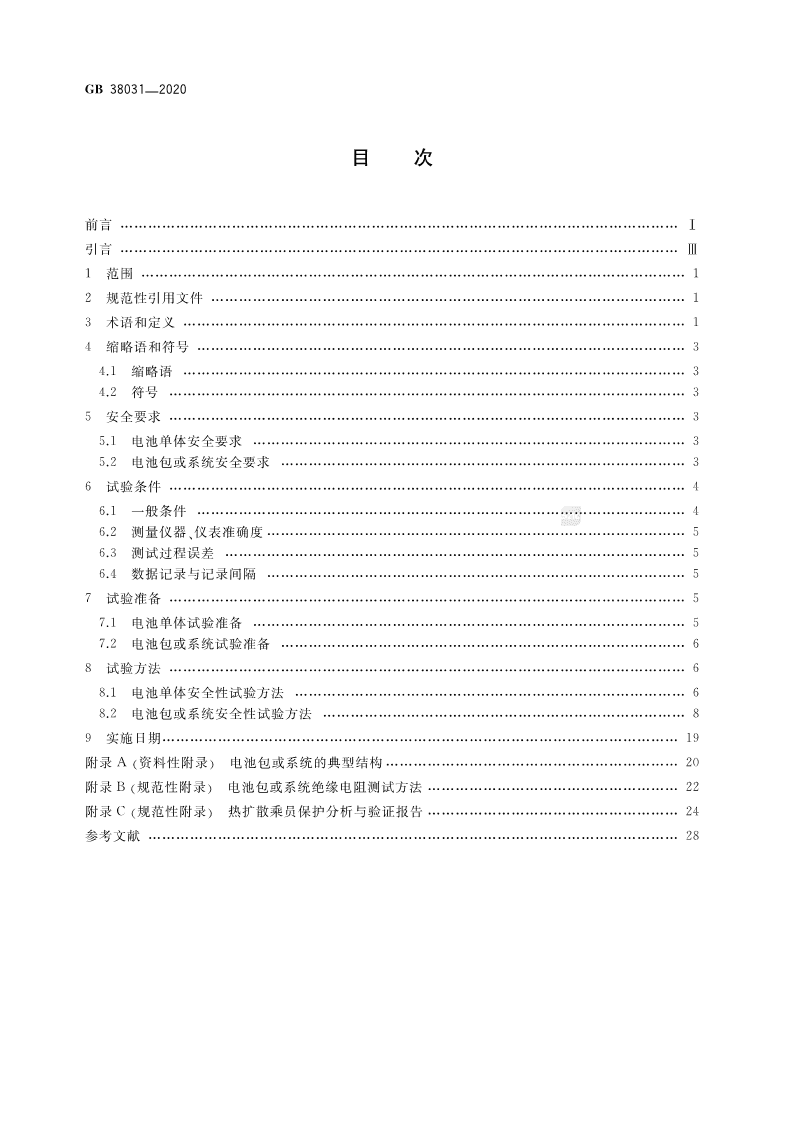
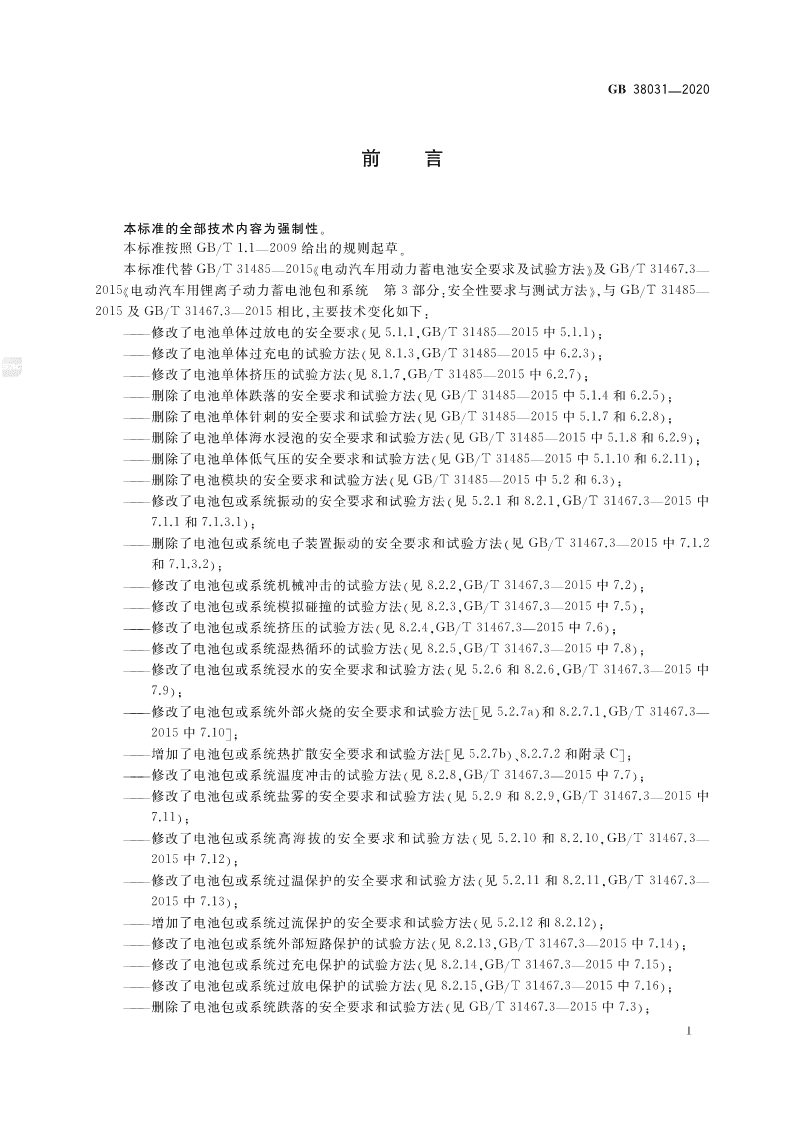
申明敬告: 本站不保证该用户上传的文档完整性,不预览、不比对内容而直接下载产生的反悔问题本站不予受理。
文档介绍
GB 38031-2020 电动汽车用动力蓄电池安全要求
书书书 犐犆犛43.080犜47 中 华 人 民 共 和 国 国 家 标 准 犌犅38031—2020代替GB/T31485—2015,GB/T31467.3—2015 电动汽车用动力蓄电池安全要求 犈犾犲犮狋狉犻犮狏犲犺犻犮犾犲狊狋狉犪犮狋犻狅狀犫犪狋狋犲狉狔狊犪犳犲狋狔狉犲狇狌犻狉犲犿犲狀狋狊 20200512发布 20210101实施 国 家 市 场 监 督 管 理 总 局 国 家 标 准 化 管 理 委 员 会 发 布 目 次 前言 Ⅰ………………………………………………………………………………………………………… 引言 Ⅲ………………………………………………………………………………………………………… 1 范围 1……………………………………………………………………………………………………… 2 规范性引用文件 1………………………………………………………………………………………… 3 术语和定义 1……………………………………………………………………………………………… 4 缩略语和符号 3…………………………………………………………………………………………… 4.1 缩略语 3……………………………………………………………………………………………… 4.2 符号 3………………………………………………………………………………………………… 5 安全要求 3………………………………………………………………………………………………… 5.1 电池单体安全要求 3………………………………………………………………………………… 5.2 电池包或系统安全要求 3…………………………………………………………………………… 6 试验条件 4………………………………………………………………………………………………… 6.1 一般条件 4…………………………………………………………………………………………… 6.2 测量仪器、仪表准确度 5……………………………………………………………………………… 6.3 测试过程误差 5……………………………………………………………………………………… 6.4 数据记录与记录间隔 5……………………………………………………………………………… 7 试验准备 5………………………………………………………………………………………………… 7.1 电池单体试验准备 5………………………………………………………………………………… 7.2 电池包或系统试验准备 6…………………………………………………………………………… 8 试验方法 6………………………………………………………………………………………………… 8.1 电池单体安全性试验方法 6………………………………………………………………………… 8.2 电池包或系统安全性试验方法 8…………………………………………………………………… 9 实施日期 19………………………………………………………………………………………………… 附录A(资料性附录) 电池包或系统的典型结构 20……………………………………………………… 附录B(规范性附录) 电池包或系统绝缘电阻测试方法 22……………………………………………… 附录C(规范性附录) 热扩散乘员保护分析与验证报告 24……………………………………………… 参考文献 28…………………………………………………………………………………………………… 犌犅38031—2020 前 言 本标准的全部技术内容为强制性。 本标准按照GB/T1.1—2009给出的规则起草。 本标准代替GB/T31485—2015《电动汽车用动力蓄电池安全要求及试验方法》及GB/T31467.3— 2015《电动汽车用锂离子动力蓄电池包和系统 第3部分:安全性要求与测试方法》,与GB/T31485— 2015及GB/T31467.3—2015相比,主要技术变化如下: ———修改了电池单体过放电的安全要求(见5.1.1,GB/T31485—2015中5.1.1); ———修改了电池单体过充电的试验方法(见8.1.3,GB/T31485—2015中6.2.3); ———修改了电池单体挤压的试验方法(见8.1.7,GB/T31485—2015中6.2.7); ———删除了电池单体跌落的安全要求和试验方法(见GB/T31485—2015中5.1.4和6.2.5); ———删除了电池单体针刺的安全要求和试验方法(见GB/T31485—2015中5.1.7和6.2.8); ———删除了电池单体海水浸泡的安全要求和试验方法(见GB/T31485—2015中5.1.8和6.2.9); ———删除了电池单体低气压的安全要求和试验方法(见GB/T31485—2015中5.1.10和6.2.11); ———删除了电池模块的安全要求和试验方法(见GB/T31485—2015中5.2和6.3); ———修改了电池包或系统振动的安全要求和试验方法(见5.2.1和8.2.1,GB/T31467.3—2015中 7.1.1和7.1.3.1); ———删除了电池包或系统电子装置振动的安全要求和试验方法(见GB/T31467.3—2015中7.1.2和7.1.3.2); ———修改了电池包或系统机械冲击的试验方法(见8.2.2,GB/T31467.3—2015中7.2); ———修改了电池包或系统模拟碰撞的试验方法(见8.2.3,GB/T31467.3—2015中7.5); ———修改了电池包或系统挤压的试验方法(见8.2.4,GB/T31467.3—2015中7.6); ———修改了电池包或系统湿热循环的试验方法(见8.2.5,GB/T31467.3—2015中7.8); ———修改了电池包或系统浸水的安全要求和试验方法(见5.2.6和8.2.6,GB/T31467.3—2015中 7.9); ———修改了电池包或系统外部火烧的安全要求和试验方法[见5.2.7a)和8.2.7.1,GB/T31467.3— 2015中7.10]; ———增加了电池包或系统热扩散安全要求和试验方法[见5.2.7b)、8.2.7.2和附录C]; ———修改了电池包或系统温度冲击的试验方法(见8.2.8,GB/T31467.3—2015中7.7); ———修改了电池包或系统盐雾的安全要求和试验方法(见5.2.9和8.2.9,GB/T31467.3—2015中 7.11); ———修改了电池包或系统高海拔的安全要求和试验方法(见5.2.10和8.2.10,GB/T31467.3— 2015中7.12); ———修改了电池包或系统过温保护的安全要求和试验方法(见5.2.11和8.2.11,GB/T31467.3— 2015中7.13); ———增加了电池包或系统过流保护的安全要求和试验方法(见5.2.12和8.2.12); ———修改了电池包或系统外部短路保护的试验方法(见8.2.13,GB/T31467.3—2015中7.14); ———修改了电池包或系统过充电保护的试验方法(见8.2.14,GB/T31467.3—2015中7.15); ———修改了电池包或系统过放电保护的试验方法(见8.2.15,GB/T31467.3—2015中7.16); ———删除了电池包或系统跌落的安全要求和试验方法(见GB/T31467.3—2015中7.3); Ⅰ 犌犅38031—2020 ———删除了电池包或系统翻转的安全要求和试验方法(见GB/T31467.3—2015中7.4)。本标准由中华人民共和国工业和信息化部提出并归口。本标准起草单位:宁德时代新能源科技股份有限公司、中国汽车技术研究中心有限公司、合肥国轩高科动力能源有限公司、万向一二三股份公司、上海卡耐新能源有限公司、中国电子科技集团公司第十八研究所、工业信息化部装备工业发展中心、比亚迪汽车工业有限公司、天津力神电池股份有限公司、湖南科霸汽车动力电池有限责任公司、北京新能源汽车股份有限公司、深圳市比亚迪锂电池有限公司、上海蔚来汽车有限公司、中信国安盟固利动力科技有限公司、奇瑞新能源汽车技术有限公司、上海汽车集团股份有限公司技术中心、中国第一汽车集团有限公司、广州汽车集团股份有限公司、重庆长安新能源汽车科技有限公司、浙江吉利控股集团有限公司、上海机动车检测认证技术研究中心有限公司、国家汽车质量监督检验中心(襄阳)、长春汽车检测中心有限责任公司、知豆电动汽车有限公司、深圳市沃特玛电池有限公司、长城汽车股份有限公司、天津市捷威动力工业有限公司、惠州市亿能电子有限公司、东风汽车集团有限公司技术中心、银隆新能源股份有限公司、中通客车控股股份有限公司、微宏动力系统(湖州)有限公司、泛亚汽车技术中心有限公司。本标准主要起草人:陈小波、王芳、肖成伟、陆春、吴凯、侯飞、郑利峰、张海林、廉玉波、孟祥峰、樊彬、陈万吉、张娜、徐国昌、代康伟、王高武、邓小嘉、刘正耀、武卫忠、刘磊、曾祥兵、陆珂伟、闫国丰、刘仕强、梅骜、袁昌荣、孔治国、张红波、李宁、雒小丹、朱顺良、覃北阶、崔凤涛、王红梅、匡德志、饶睦敏、侯航、王驰伟、樊耀国、夏洋、蔡惠群、王钦普、李辉、李王玉。本标准所代替标准的历次版本发布情况为: ———GB/T31485—2015; ———GB/T31467.3—2015。 Ⅱ 犌犅38031—2020 引 言 本引言旨在介绍本标准的要求所依据的原则,理解这些原则对电动汽车用动力蓄电池单体、电池包或系统的设计和应用是很有必要的。需要注意的是本标准仅考虑电动汽车用动力蓄电池单体、电池包或系统最基本的安全要求以提供对人身的安全保护,不涉及生产、运输、维护和回收安全,也不涉及性能和功能特性。随着技术和工艺的进一步发展将会要求修订本标准。在本标准范围内电动汽车用动力蓄电池单体、电池包或系统导致的危险是指: ———泄漏,可能导致电池系统高压、绝缘失效间接造成人员电击、电池系统起火等危险; ———起火,直接烧伤人体; ———爆炸,直接危害人体,包括高温烧伤、冲击波伤害和爆炸碎片伤害等; ———电击,由于电流流过人体而引起的伤害。电动汽车用动力蓄电池单体、电池包或系统的安全性与其材料选择、设计及使用条件有关。其中使用条件包含了正常使用条件、可预见的误用条件和可预见的故障条件,还包括影响其安全的环境条件诸如温度、海拔等因素。 Ⅲ 犌犅38031—2020 电动汽车用动力蓄电池安全要求 1 范围 本标准规定了电动汽车用动力蓄电池(以下简称电池)单体、电池包或系统的安全要求和试验方法。本标准适用于电动汽车用锂离子电池和镍氢电池等可充电储能装置。 2 规范性引用文件 下列文件对于本文件的应用是必不可少的。凡是注日期的引用文件,仅注日期的版本适用于本文件。凡是不注日期的引用文件,其最新版本(包括所有的修改单)适用于本文件。 GB/T2423.4 电工电子产品环境试验 第2部分:试验方法 试验Db:交变湿热(12h+12h循环) GB/T2423.17 电工电子产品环境试验 第2部分:试验方法 试验Ka:盐雾 GB/T2423.43 电工电子产品环境试验 第2部分:试验方法 振动、冲击和类似动力学试验样品的安装 GB/T2423.56 环境试验 第2部分:试验方法 试验Fh:宽带随机振动和导则 GB/T4208—2017 外壳防护等级(IP代码) GB/T19596 电动汽车术语 GB/T28046.4—2011 道路车辆 电气及电子设备的环境条件和试验 第4部分:气候负荷 3 术语和定义 GB/T19596界定的以及下列术语和定义适用于本文件。 3.1 电池单体 狊犲犮狅狀犱犪狉狔犮犲犾犾将化学能与电能进行相互转换的基本单元装置。 注:通常包括电极、隔膜、电解质、外壳和端子,并被设计成可充电。 3.2 电池模块 犫犪狋狋犲狉狔犿狅犱狌犾犲将一个以上电池单体按照串联、并联或串并联方式组合,并作为电源使用的组合体。 3.3 电池包 犫犪狋狋犲狉狔狆犪犮犽具有从外部获得电能并可对外输出电能的单元。 注:通常包括电池单体、电池管理模块(不含BCU)、电池箱及相应附件(冷却部件、连接线缆等)。 3.4 电池系统 犫犪狋狋犲狉狔狊狔狊狋犲犿一个或一个以上的电池包及相应附件(管理系统、高压电路、低压电路及机械总成等)构成的能量存储装置。 3.5 电池电子部件 犫犪狋狋犲狉狔犲犾犲犮狋狉狅狀犻犮狊采集或者同时监测电池包电和热数据的电子装置。 1 犌犅38031—2020 注:电池电子部件可以包括单体控制器和用于电池单体均衡的电子部件。电池单体间的均衡可以由电池电子部件 控制,或者通过电池控制单元控制。 3.6 电池控制单元 犫犪狋狋犲狉狔犮狅狀狋狉狅犾狌狀犻狋控制、管理、检测或计算电池系统的电和热相关的参数,并提供电池系统和其他车辆控制器通信的电子装置。 3.7 额定容量 狉犪狋犲犱犮犪狆犪犮犻狋狔以制造商规定的条件测得的并由制造商申明的电池单体、模块、电池包或系统的容量值。 注:额定容量通常用安时(Ah)或毫安时(mAh)来表示。 3.8 实际容量 狆狉犪犮狋犻犮犪犾犮犪狆犪犮犻狋狔以制造商规定的条件,从完全充电的电池单体、模块、电池包或系统中释放的容量值。 3.9 荷电状态 狊狋犪狋犲狅犳犮犺犪狉犵犲当前电池单体、模块、电池包或系统中按照制造商规定的放电条件可以释放的容量占实际容量的百分比。 3.10爆炸 犲狓狆犾狅狊犻狅狀突然释放足量的能量产生压力波或者喷射物,可能会对周边区域造成结构或物理上的破坏。 3.11起火 犳犻狉犲电池单体、模块、电池包或系统任何部位发生持续燃烧(单次火焰持续时间大于1s)。火花及拉弧不属于燃烧。 3.12外壳破裂 犺狅狌狊犻狀犵犮狉犪犮犽由于内部或外部因素引起电池单体、模块、电池包或系统外壳的机械损伤,导致内部物质暴露或溢出。 3.13泄漏 犾犲犪犽犪犵犲有可见物质从电池单体、模块、电池包或系统中漏出至试验对象外部的现象。 3.14热失控 狋犺犲狉犿犪犾狉狌狀犪狑犪狔电池单体放热连锁反应引起电池温度不可控上升的现象。 3.15热扩散 狋犺犲狉犿犪犾狆狉狅狆犪犵犪狋犻狅狀电池包或系统内由一个电池单体热失控引发的其余电池单体接连发生热失控的现象。 3.16充电终止电压 犲狀犱狅犳犮犺犪狉犵犲狏狅犾狋犪犵犲电池单体、模块、电池包或系统正常充电时允许达到的最高电压。 3.17放电终止电压 犲狀犱狅犳犱犻狊犮犺犪狉犵犲狏狅犾狋犪犵犲电池单体、模块、电池包或系统正常放电时允许达到的最低电压。 2 犌犅38031—2020 4 缩略语和符号 4.1 缩略语 下列缩略语适用于本文件。 BCU:电池控制单元(batterycontrolunit) FS:满量程(fullscale) PSD:功率谱密度(powerspectraldensity) RMS:均方根(rootmeansquare) SOC:荷电状态(stateofcharge) 4.2 符号 下列符号适用于本文件。 犐1:1h率放电电流(A),其数值等于额定容量值。 犐3:3h率放电电流(A),其数值等于额定容量值的1/3。 5 安全要求 5.1 电池单体安全要求 5.1.1 电池单体按照8.1.2进行过放电试验,应不起火、不爆炸。 5.1.2 电池单体按照8.1.3进行过充电试验,应不起火、不爆炸。 5.1.3 电池单体按照8.1.4进行外部短路试验,应不起火、不爆炸。 5.1.4 电池单体按照8.1.5进行加热试验,应不起火、不爆炸。 5.1.5 电池单体按照8.1.6进行温度循环试验,应不起火、不爆炸。 5.1.6 电池单体按照8.1.7进行挤压试验,应不起火、不爆炸。 5.2 电池包或系统安全要求 5.2.1 电池包或系统按照8.2.1进行振动试验,应无泄漏、外壳破裂、起火或爆炸现象,且不触发异常终止条件。试验后的绝缘电阻应不小于100Ω/V。 5.2.2 电池包或系统按照8.2.2进行机械冲击试验,应无泄漏、外壳破裂、起火或爆炸现象。试验后的绝缘电阻应不小于100Ω/V。 5.2.3 电池包或系统按照8.2.3进行模拟碰撞试验,应无泄漏、外壳破裂、起火或爆炸现象。试验后的绝缘电阻应不小于100Ω/V。 5.2.4 电池包或系统按照8.2.4进行挤压试验,应不起火、不爆炸。 5.2.5 电池包或系统按照8.2.5进行湿热循环试验,应无泄漏、外壳破裂、起火或爆炸现象。试验后30min之内的绝缘电阻应不小于100Ω/V。 5.2.6 电池包或系统按照8.2.6进行浸水试验,应满足如下要求之一: a) 按方式一进行,应不起火、不爆炸; b) 按方式二进行,试验后需满足IPX7要求,应无泄漏、外壳破裂、起火或爆炸现象。试验后的绝缘电阻应不小于100Ω/V。 5.2.7 电池包或系统按照8.2.7进行热稳定性试验,镍氢电池包或系统除外。包括: a) 按照8.2.7.1进行外部火烧试验,应不爆炸; b) 按照8.2.7.2进行热扩散乘员保护分析和验证。电池包或系统在由于单个电池热失控引起热扩散、进而导致乘员舱发生危险之前5min,应提供一个热事件报警信号。 3 犌犅38031—2020 5.2.8 电池包或系统按照8.2.8进行温度冲击试验,应无泄漏、外壳破裂、起火或爆炸现象。试验后的绝缘电阻应不小于100Ω/V。 5.2.9 电池包或系统按照8.2.9进行盐雾试验,应无泄漏、外壳破裂、起火或爆炸现象。试验后的绝缘电阻应不小于100Ω/V。 5.2.10 电池包或系统按照8.2.10进行高海拔试验,应无泄漏、外壳破裂、起火或爆炸现象,且不触发异常终止条件。试验后的绝缘电阻应不小于100Ω/V。 5.2.11 电池系统按照8.2.11进行过温保护试验,应无泄漏、外壳破裂、起火或爆炸现象,且不触发异常终止条件。试验后的绝缘电阻应不小于100Ω/V。 5.2.12 电池系统按照8.2.12进行过流保护试验,应无泄漏、外壳破裂、起火或爆炸现象,且不触发异常终止条件。试验后的绝缘电阻应不小于100Ω/V。 5.2.13 电池系统按照8.2.13进行外部短路保护试验,应无泄漏、外壳破裂、起火或爆炸现象。试验后的绝缘电阻应不小于100Ω/V。 5.2.14 电池系统按照8.2.14进行过充电保护试验,应无泄漏、外壳破裂、起火或爆炸现象,且不触发异常终止条件。试验后的绝缘电阻应不小于100Ω/V。 5.2.15 电池系统按照8.2.15进行过放电保护试验,应无泄漏、外壳破裂、起火或爆炸现象。试验后的绝缘电阻应不小于100Ω/V。 6 试验条件 6.1 一般条件 6.1.1 除另有规定,试验环境温度为22℃±5℃,相对湿度为10%~90%,大气压力为86kPa~106kPa。 6.1.2 8.1的试验对象为电池单体,若电池单体无法独立工作,可采用电池模块进行试验,安全要求仍按照5.1执行。 6.1.3 对于由车体包覆并构成电池包箱体的电池包或系统,可带箱体或车体测试。 6.1.4 电池包或系统试验交付需要包括必要的操作文件,以及和测试设备相连所需的接口部件,如连接器,插头,包括冷却系统接口,电池包或系统的典型结构参见附录A。制造商需要提供电池包或系统的安全工作限值。 6.1.5 电池包或系统在所有测试前和部分试验后需进行绝缘电阻测试。测试位置为:两个端子和电平台之间。要求测得的绝缘电阻值除以电池包或系统的最大工作电压不小于100Ω/V。具体测试方法见附录B。 6.1.6 如果电池包或系统由于某些原因(如尺寸或质量)不适合进行某些测试,那么制造商与检测机构协商一致后可以用电池包或系统的子系统代替作为试验对象,进行全部或部分测试,但是作为试验对象的子系统应包含和整车要求相关的所有部分(如连接部件或保护部件等)。 6.1.7 调整SOC至试验目标值狀%的方法:按制造商提供的充电方式将电池包或系统充满电,静置 1h,以1犐3 恒流放电,放电时间为犜,犜 按照式(1)计算得到,或者采用制造商提供的方法调整SOC。每次SOC调整后,在新的测试开始前试验对象应静置30min。 犜=100-狀100 ×3 …………………………(1) 式中: 犜 ———放电时间,单位为小时(h); 狀 ———试验目标值的百分数值。 6.1.8 测试过程中的充放电倍率大小、充放电方法和充放电截止条件由制造商提供。 6.1.9 电池单体、电池包或系统的额定容量应符合制造商提供的产品技术条件。 4 犌犅38031—2020 6.1.10 除有特殊规定,试验对象均以制造商规定的完全充电状态进行测试。 6.1.11 电池单体、电池包或系统放电电流符号为正,充电电流符号为负。 6.1.12 当电池冷却系统使用了冷却液时,如果试验不要求电池冷却,也可在排掉冷却液后进行试验。 6.2 测量仪器、仪表准确度 测量仪器、仪表准确度应不低于以下要求: a) 电压测量装置:±0.5%FS; b) 电流测量装置:±0.5%FS; c) 温度测量装置:±0.5℃; d) 时间测量装置:±0.1%FS; e) 尺寸测量装置:±0.1%FS; f) 质量测量装置:±0.1%FS。 6.3 测试过程误差 控制值(实际值)与目标值之间的误差要求如下: a) 电压:±1%; b) 电流:±1%; c) 温度:±2℃。 6.4 数据记录与记录间隔 除在某些具体测试项目中另有说明,否则测试数据(如时间、温度、电流和电压等)的记录间隔应不大于100s。 7 试验准备 7.1 电池单体试验准备 7.1.1 标准充电 电池单体先以制造商规定且不小于1犐3 的电流放电至制造商技术条件中规定的放电终止电压,搁置1h(或制造商提供的不大于1h的搁置时间),然后按制造商提供的充电方法进行充电,充电后搁置 1h(或制造商提供的不大于1h的搁置时间)。若制造商未提供充电方法,则由检测机构和制造商协商确定合适的充电方法,或依据以下方法充电:以制造商规定且不小于1犐3 的电流恒流充电至电池单体达制造商技术条件中规定的充电终止电压时转恒压充电,至充电电流降至0.05犐1 时停止充电,充电后搁置1h(或制造商提供的不大于1h的搁置时间)。 7.1.2 预处理 7.1.2.1 正式测试开始前,电池单体需要先进行预处理循环,以确保试验对象的性能处于激活和稳定的状态。步骤如下: a) 按照7.1.1对电池单体进行标准充电; b) 以制造商规定的且不小于1犐3 的电流放电至制造商规定的放电截止条件; c) 静置30min或制造商规定时间; d) 重复步骤a)~c)不超过5次。 5 犌犅38031—2020 7.1.2.2 如果电池单体连续两次的放电容量变化不高于额定容量的3%,则认为电池单体完成了预处理,预处理循环可以中止。 7.2 电池包或系统试验准备 7.2.1 工作状态确认 正式开始测试前,电池包或系统的电子部件或BCU应处于正常工作状态。 7.2.2 预处理 7.2.2.1 正式测试开始前,电池包或系统需要先进行预处理循环,以确保测试时试验对象的性能处于激活和稳定的状态。步骤如下: a) 以不小于1犐3 的电流或按照制造商推荐的充电方法充电至制造商规定的充电截止条件; b) 静置30min或制造商规定的时间; c) 以制造商规定的且不小于1犐3 的电流放电至制造商规定的放电截止条件; d) 静置30min或制造商规定的时间; e) 重复步骤a)~d)不超过5次。 7.2.2.2 如果电池包或系统连续两次的放电容量变化不高于额定容量的3%,则认为电池包或系统完成了预处理,预处理循环可以中止。 7.2.2.3 除在某些具体测试项目中另有说明,否则若预处理循环完成并满充后和一个新的测试项目之间时间间隔大于24h,则需要重新进行一次标准充电:使用不小于1犐3 的电流充电至制造商规定的充电截止条件或按照制造商推荐的充电方法充电,静置30min或制造商规定的时间。 8 试验方法 8.1 电池单体安全性试验方法 8.1.1 一般要求 所有安全试验均在有充分安全保护的环境条件下进行。如果试验对象有附加主动保护线路或装置,应除去。 8.1.2 过放电 8.1.2.1 试验对象为电池单体。 8.1.2.2 试验对象按7.1.1方法充电。 8.1.2.3 以1犐1 电流放电90min。 8.1.2.4 完成以上试验步骤后,在试验环境温度下观察1h。 8.1.3 过充电 8.1.3.1 试验对象为电池单体。 8.1.3.2 试验对象按7.1.1方法充电。 8.1.3.3 以制造商规定且不小于1犐3 的电流恒流充电至制造商规定的充电终止电压的1.1倍或115%SOC后,停止充电。 8.1.3.4 完成以上试验步骤后,在试验环境温度下观察1h。 8.1.4 外部短路 8.1.4.1 试验对象为电池单体。 6 犌犅38031—2020 8.1.4.2 试验对象按7.1.1方法充电。 8.1.4.3 将试验对象正极端子和负极端子经外部短路10min,外部线路电阻应小于5mΩ。 8.1.4.4 完成以上试验步骤后,在试验环境温度下观察1h。 8.1.5 加热 8.1.5.1 试验对象为电池单体。 8.1.5.2 试验对象按7.1.1方法充电。 8.1.5.3 将试验对象放入温度箱,用以下的条件加热: a) 锂离子电池单体:温度箱按照5℃/min的速率由试验环境温度升至130℃±2℃,并保持此温度30min后停止加热; b) 镍氢电池单体:温度箱按照5℃/min的速率由试验环境温度升至85℃±2℃,并保持此温度 2h后停止加热。 8.1.5.4 完成以上试验步骤后,在试验环境温度下观察1h。 8.1.6 温度循环 8.1.6.1 试验对象为电池单体。 8.1.6.2 试验对象按7.1.1方法充电。 8.1.6.3 放入温度箱中,温度箱温度按照表1和图1进行调节,循环次数5次。 8.1.6.4 完成以上试验步骤后,在试验环境温度下观察1h。 表1 温度循环试验一个循环的温度和时间 温度 ℃ 时间增量 min 累计时间 min 温度变化率 ℃/min 25 0 0 0 -40 60 60 13/12 -40 90 150 0 25 60 210 13/12 85 90 300 2/3 85 110 410 0 25 70 480 6/7 图1 温度循环试验示意图 7 犌犅38031—2020 8.1.7 挤压 8.1.7.1 试验对象为电池单体。 8.1.7.2 试验对象按7.1.1方法充电。 8.1.7.3 按下列条件进行试验: a) 挤压方向:垂直于电池单体极板方向施压,或与电池单体在整车布局上最容易受到挤压的方向相同; b) 挤压板形式:半径75mm的半圆柱体,半圆柱体的长度(犔)大于被挤压电池单体的尺寸(如图6所示); c) 挤压速度:不大于2mm/s; d) 挤压程度:电压达到0V或变形量达到15%或挤压力达到100kN或1000倍试验对象重量后停止挤压; e) 保持10min。 8.1.7.4 完成以上试验步骤后,在试验环境温度下观察1h。 8.2 电池包或系统安全性试验方法 8.2.1 振动 8.2.1.1 试验对象为电池包或系统。 8.2.1.2 为保护试验操作人员和实验室安全,制造商应提供电压锐变限值作为异常终止条件。 8.2.1.3 试验开始前,将试验对象的SOC状态调至不低于制造商规定的正常SOC工作范围的50%。 8.2.1.4 按照试验对象车辆安装位置和GB/T2423.43的要求,将试验对象安装在振动台上。每个方向分别施加随机和定频振动载荷,加载顺序宜为狕轴随机、狕轴定频、狔轴随机、狔轴定频、狓轴随机、狓轴定频(汽车行驶方向为狓轴方向,另一垂直于行驶方向的水平方向为狔轴方向)。检测机构也可自行选择顺序,以缩短转换时间。测试过程按照GB/T2423.56。 8.2.1.5 对于装载在除 M1、N1 类以外的车辆上的电池包或系统,振动测试参数按照表2和图2进行,对于试验对象存在多个安装方向(狓/狔/狕)时,按照RMS大的安装方向进行试验。对于安装在车辆顶部的电池包或系统,按照制造商提供的不低于表2和图2的振动测试参数开展振动测试。 8.2.1.6 对于装载在 M1、N1 类车辆上的电池包或系统,振动测试参数按照表3和图3进行。 表2 除 犕1、犖1 类以外的车辆电池包或系统的振动测试条件 随机振动(每个方向测试时间为12h)频率 Hz 狕轴功率谱密度(PSD) 犵2/Hz 狔轴功率谱密度(PSD) 犵2/Hz 狓轴功率谱密度(PSD) 犵2/Hz5 0.008 0.005 0.002 10 0.042 0.025 0.018 15 0.042 0.025 0.018 40 0.0005 — — 60 — 0.0001 — 100 0.0005 0.0001 — 200 0.00001 0.00001 0.00001 RMS 狕轴 狔轴 狓轴 0.73犵 0.57犵 0.52犵正弦定频振动(每个方向测试时间为2h)频率 Hz 狕轴定频幅值 狔轴定频幅值 狓轴定频幅值 20 ±1.5犵 ±1.5犵 ±2.0犵 8 犌犅38031—2020 图2 除 犕1、犖1 类以外的车辆电池包或系统随机振动测试曲线 表3 犕1、犖1 类车辆电池包或系统的振动测试条件 随机振动(每个方向测试时间为12h) 频率 Hz 狕轴功率谱密度(PSD) 犵2/Hz 狔轴功率谱密度(PSD) 犵2/Hz 狓轴功率谱密度(PSD) 犵2/Hz 5 0.015 0.002 0.006 10 — 0.005 — 15 0.015 — — 20 — 0.005 — 30 — — 0.006 65 0.001 — — 100 0.001 — — 200 0.0001 0.00015 0.00003 RMS 狕轴 狔轴 狓轴 0.64犵 0.45犵 0.50犵 正弦定频振动(每个方向测试时间为1h) 频率 Hz 狕轴定频幅值 狔轴定频幅值 狓轴定频幅值 24 ±1.5犵 ±1.0犵 ±1.0犵 9 犌犅38031—2020 图3 犕1、犖1 类车辆电池包或系统随机振动测试曲线 8.2.1.7 试验过程中,监控试验对象内部最小监控单元的状态,如电压和温度等。 8.2.1.8 完成以上试验步骤后,在试验环境温度下观察2h。 8.2.2 机械冲击 8.2.2.1 试验对象为电池包或系统。 8.2.2.2 对试验对象施加表4规定的半正弦冲击波,±狕方向各6次,共计12次。 8.2.2.3 半正弦冲击波最大、最小容差允许范围如表5和图4所示。 8.2.2.4 相邻两次冲击的间隔时间以两次冲击在试验样品上造成的响应不发生相互影响为准,一般应不小于5倍冲击脉冲持续时间。 8.2.2.5 完成以上试验步骤后,在试验环境温度下观察2h。 表4 机械冲击测试参数 测试程序 参数要求 冲击波形 半正弦波 测试方向 ±狕 加速度值 7犵 脉冲时间/ms 6 冲击次数 正负方向各6次 表5 机械冲击脉冲容差范围 点 脉宽 ms ±狕方向加速度值 A 1.00 0.00犵 B 2.94 5.95犵 C 3.06 5.95犵 D 5.00 0.00犵 E 0.00 2.68犵 01 犌犅38031—2020 表5(续) 点 脉宽 ms ±狕方向加速度值 F 2.00 8.05犵 G 4.00 8.05犵 H 7.00 0.00犵 图4 机械冲击脉冲容差范围示意图 8.2.3 模拟碰撞 8.2.3.1 试验对象为电池包或系统。 8.2.3.2 按照试验对象车辆安装位置和GB/T2423.43的要求,将试验对象水平安装在带有支架的台车上。根据试验对象的使用环境给台车施加规定的脉冲,并落在表6和图5最大、最小容差允许范围内 (汽车行驶方向为狓轴方向,另一垂直于行驶方向的水平方向为狔轴方向)。对于试验对象存在多个安装方向(狓/狔/狕)时,按照加速度大的安装方向进行试验。 8.2.3.3 完成以上试验步骤后,在试验环境温度下观察2h。 表6 模拟碰撞脉冲容差范围 点 脉宽 ms ≤3.5t(整车整备质量) 3.5t~7.5t(整车整备质量) ≥7.5t(整车整备质量) 狓方向加速度 狔方向加速度 狓方向加速度 狔方向加速度 狓方向加速度 狔方向加速度 A 20 0犵 0犵 0犵 0犵 0犵 0犵 B 50 20犵 8犵 10犵 5犵 6.6犵 5犵 C 65 20犵 8犵 10犵 5犵 6.6犵 5犵 D 100 0犵 0犵 0犵 0犵 0犵 0犵 E 0 10犵 4.5犵 5犵 2.5犵 4犵 2.5犵 F 50 28犵 15犵 17犵 10犵 12犵 10犵 G 80 28犵 15犵 17犵 10犵 12犵 10犵 H 120 0犵 0犵 0犵 0犵 0犵 0犵 11 犌犅38031—2020 图5 模拟碰撞脉冲容差范围示意图 8.2.4 挤压 8.2.4.1 试验对象为电池包或系统。 8.2.4.2 按下列条件进行试验: a) 挤压板形式(选择以下两种挤压板中的一种): ———挤压板如图6所示,半径75mm的半圆柱体,半圆柱体的长度(犔)大于试验对象的高度,但不超过1m; ———挤压板如图7所示,尺寸为600mm×600mm(长×宽)或更小,三个半圆柱体半径为 75mm,半圆柱体间距30mm; b) 挤压方向:狓方向和狔方向(汽车行驶方向为狓 轴方向,另一垂直于行驶方向的水平方向为 狔轴方向),为保护试验操作安全,可分开在两个试验对象上执行测试; c) 挤压速度:不大于2mm/s; d) 挤压程度:挤压力达到100kN或挤压变形量达到挤压方向的整体尺寸的30%时停止挤压; e) 保持10min。 8.2.4.3 完成以上试验步骤后,在试验环境温度下观察2h。 图6 挤压板形式一示意图 21 犌犅38031—2020 图7 挤压板形式二示意图 8.2.5 湿热循环 8.2.5.1 试验对象为电池包或系统。 8.2.5.2 按照GB/T2423.4执行试验Db,变量如图8所示。其中最高温度是60℃或更高温度(如果制造商要求),循环5次。 8.2.5.3 完成以上试验步骤后,在试验环境温度下观察2h。 犪) 图8 温湿度循环 31 犌犅38031—2020 犫) 说明: 犢1———相对湿度,%; 犢2———温度,℃; 犡 ———时间,h; a ———升温结束; b ———降温开始; c ———推荐温湿度值; d ———冷凝; e ———干燥; f ———一个循环周期。 图8(续) 8.2.6 浸水 8.2.6.1 试验对象为通过8.2.1振动试验后的电池包或系统。 8.2.6.2 试验对象按照整车连接方式连接好线束、接插件等零部件,选择以下两种方式中的一种进行试验: a) 方式一:试验对象以实车装配方向置于3.5% (质量分数)氯化钠溶液中2h,水深要足以淹没试验对象; b) 方式二:试验对象按照GB/T4208—2017中14.2.7所述方法和流程进行试验。试验对象按照制造商规定的安装状态全部浸入水中。对于高度小于850mm的试验对象,其最低点应低于水面1000mm;对于高度等于或大于850mm的试验对象,其最高点应低于水面150mm。试验持续时间30min。水温与试验对象温差不大于5℃。 8.2.6.3 将电池包取出水面,在试验环境温度下静置观察2h。 8.2.7 热稳定性 8.2.7.1 外部火烧 8.2.7.1.1 试验对象为电池包或系统。对电池包或系统起到保护作用的车身结构,可以参与火烧试验。 8.2.7.1.2 试验环境温度为0℃以上,风速不大于2.5km/h。 8.2.7.1.3 测试中,盛放汽油的平盘尺寸超过试验对象水平投影尺寸20cm,不超过50cm。平盘高度不高于汽油表面8cm。试验对象应居中放置。汽油液面与试验对象底部的距离设定为50cm,或者为车辆空载状态下试验对象底面的离地高度。平盘底层注入水。外部火烧示意图如图9所示。 8.2.7.1.4 外部火烧试验分为以下4个阶段: a) 预热。在离试验对象至少3m远的地方点燃汽油,经过60s的预热后,将油盘置于试验对象下方。如果油盘尺寸太大无法移动,可以采用移动试验对象和支架的方式。 41 犌犅38031—2020 b) 直接燃烧。试验对象直接暴露在火焰下70s。 c) 间接燃烧。将耐火隔板盖在油盘上。试验对象在该状态下测试60s。或经双方协商同意,继续直接暴露在火焰中60s。耐火隔板由标准耐火砖拼成,具体筛孔尺寸如图10所示,也可以用耐火材料参考此尺寸制作。 d) 离开火源。将油盘或者试验对象移开,在试验环境温度下观察2h或试验对象外表温度降至 45℃以下。 图9 外部火烧示意图 单位为毫米 说明: 耐火性:SK30;成分:30%~33% Al2O3;密度:1900kg/m3~2000kg/m3;有效孔面积:44.18%;开孔率:20%~ 22%体积比。 图10 耐火隔板的尺寸和技术数据 8.2.7.2 热扩散 电池包或系统按照附录C进行热扩散乘员保护分析和验证。 8.2.8 温度冲击 8.2.8.1 试验对象为电池包或系统。 8.2.8.2 试验对象置于(-40℃±2℃)~(60℃±2℃)(如果制造商要求,可采用更严苛的试验温度) 51 犌犅38031—2020 的交变温度环境中,两种极端温度的转换时间在30min以内。试验对象在每个极端温度环境中保持 8h,循环5次。 8.2.8.3 完成以上试验步骤后,在试验环境温度下观察2h。 8.2.9 盐雾 8.2.9.1 试验对象为电池包或系统。 8.2.9.2 按照GB/T28046.4—2011中5.5.2的测试方法和GB/T2423.17的测试条件进行试验。 8.2.9.3 盐溶液采用氯化钠(化学纯、分析纯)和蒸馏水或去离子水配制,其浓度为5%±1%(质量分数)。35℃±2℃下测量pH值在6.5~7.2之间。 8.2.9.4 将试验对象放入盐雾箱按图11所示循环进行试验,一个循环持续24h。在35℃±2℃下对试验对象喷雾8h,然后静置16h,在一个循环的第4小时和第5小时之间进行低压上电监控。 8.2.9.5 共进行6个循环。 8.2.9.6 对于完全放置在乘员舱、行李舱或货舱的试验对象,可不进行盐雾试验。 说明: 狋———时间,h; a———低压上电监控; b———连接线束完毕,不通电; c———打开(喷盐雾); d———关闭(停喷盐雾)。 图11 盐雾试验循环 8.2.10 高海拔 8.2.10.1 试验对象为电池包或系统。 8.2.10.2 为保护试验操作人员和实验室安全,制造商应提供电流锐变限值、电压异常限值作为异常终止条件。 8.2.10.3 测试环境:气压条件为61.2kPa(模拟海拔高度为4000m的气压条件),温度为试验环境温度。 8.2.10.4 保持8.2.10.3测试环境,搁置5h。 8.2.10.5 搁置结束后,保持8.2.10.3测试环境,对试验对象按制造商规定的且不小于1犐3 的电流放电至制造商规定的放电截止条件。 8.2.10.6 完成以上试验步骤后,在试验环境温度下观察2h。 8.2.11 过温保护 8.2.11.1 试验对象为电池系统。 61 犌犅38031—2020 8.2.11.2 为保护试验操作人员和实验室安全,制造商应提供试验上限参数作为异常终止条件。 8.2.11.3 在试验开始时,影响试验对象功能并与试验结果相关的所有保护设备都应处于正常运行状态,冷却系统除外。 8.2.11.4 试验对象应由外部充放电设备进行连续充电和放电,使电流在电池系统制造商规定的正常工作范围内尽可能快地升高电池的温度,直到试验结束。 8.2.11.5 室内或温度箱的温度应从20℃±10℃或更高的温度(如果电池系统制造商要求)开始逐渐升高,直到达到根据a)或b)(如适用)确定的温度,然后保持在等于或高于此温度,直到试验结束: a) 当电池系统具有内部过热保护措施时,应提高到电池系统制造商定义为这种保护措施的工作温度阈值的温度,以确保试验对象的温度将按照8.2.11.4的规定升高。 b) 如果电池系统没有配备任何具体的内部过热防护措施,那么应将温度升高到电池系统制造商规定的最高工作温度。 8.2.11.6 当符合以下任一条件时,结束试验: a) 试验对象自动终止或限制充电或放电; b) 试验对象发出终止或限制充电或放电的信号; c) 试验对象的温度稳定,温度变化在2h内小于4℃。 8.2.11.7 完成以上试验步骤后,在试验环境温度下观察1h。 8.2.12 过流保护 8.2.12.1 试验对象为可由外部直流电源供电的电池系统。 8.2.12.2 为保护试验操作人员和实验室安全,制造商应提供试验上限参数作为异常终止条件。 8.2.12.3 试验条件如下: a) 试验应在20℃±10℃的环境温度下进行; b) 按照电池系统制造商推荐的正常操作(如使用外部充放电设备),调整试验对象的SOC到正常工作范围的中间部分,只要电池系统能够正常运行,可不需要精确的调整; c) 与电池系统制造商协商确定可以施加的过电流(假设外部直流供电设备的故障)和最大电压(在正常范围内)。 8.2.12.4 按照电池系统制造商的资料进行过电流试验: a) 连接外部直流供电设备,改变或禁用充电控制通信,以允许通过与电池系统制造商协商确定的过电流水平。 b) 启动外部直流供电设备,对电池系统进行充电,以达到电池系统制造商规定的最高正常充电电流。然后,将电流在5s内从最高正常充电电流增加到8.2.12.3中c)所述的过电流水平,并继续进行充电。 8.2.12.5 当符合以下任一条件时,结束试验: a) 试验对象自动终止充电电流; b) 试验对象发出终止充电电流的信号; c) 试验对象的温度稳定,温度变化在2h内小于4℃。 8.2.12.6 完成以上试验步骤后,在试验环境温度下观察1h。 8.2.13 外部短路保护 8.2.13.1 试验对象为电池系统。 8.2.13.2 试验条件如下: a) 试验应在20℃±10℃的环境温度或更高温度(如果电池系统制造商要求)下进行; b) 在试验开始时,影响试验对象功能并与试验结果相关的所有保护设备都应处于正常运行状态。 8.2.13.3 外部短路过程如下: 71 犌犅38031—2020 a) 在开始试验时,用于充电和放电的相关主要接触器都应闭合(如电池系统回路中包含相关继电器),来表示可行车模式以及允许外部充电的模式。如果这不能在单次试验中完成,则应进行两次或更多次试验。 b) 将试验对象的正极端子和负极端子相互连接。短路电阻不超过5mΩ。 8.2.13.4 保持短路状态,直至符合以下任一条件时,结束试验: a) 试验对象的保护功能起作用,并终止短路电流; b) 试验对象外壳温度稳定(温度变化在2h内小于4℃)后,继续短路至少1h。 8.2.13.5 完成以上试验步骤后,在试验环境温度下观察1h。 8.2.14 过充电保护 8.2.14.1 试验对象为电池系统。 8.2.14.2 为保护试验操作人员和实验室安全,制造商应提供试验上限参数作为异常终止条件。 8.2.14.3 试验条件如下: a) 试验应在20℃±10℃的环境温度或更高温度(如果电池系统制造商要求)下进行。 b) 按照电池系统制造商推荐的正常操作(如使用外部充放电设备),调整试验对象的SOC到正常工作范围的中间部分。只要试验对象能够正常运行,可不需要精确的调整。 c) 在试验开始时,影响试验对象功能并与试验结果相关的所有保护设备都应处于正常运行状态。用于充电的所有相关的主要接触器都应闭合(如电池系统回路中包含相关继电器)。 8.2.14.4 充电过程如下: a) 外部充电设备应连接到试验对象的主端子。外部充电设备的充电控制限制应禁用; b) 试验对象应由外部充电设备在电池系统制造商许可的用时最短的充电策略下进行充电。 8.2.14.5 充电应持续进行,直至符合以下任一条件时,结束试验: a) 试验对象自动终止充电电流。 b) 试验对象发出终止充电电流的信号。 c) 当试验对象的过充电保护控制未起作用,或者如果没有8.2.14.5中a)所述的功能。继续充电,使得试验对象温度超过电池系统制造商定义的最高工作温度再加10℃的温度值。 d) 当充电电流未终止且试验对象温度低于最高工作温度再加10℃的温度值时,充电应持续 12h。 8.2.14.6 完成以上试验步骤后,在试验环境温度下观察1h。 8.2.15 过放电保护 8.2.15.1 试验对象为电池系统。 8.2.15.2 试验条件如下: a) 试验应在20℃±10℃的环境温度或更高温度(如果电池系统制造商要求)下进行。 b) 按照电池系统制造商推荐的正常操作(如使用外部充放电设备),调整试验对象的SOC到较低水平,但应在正常的工作范围内。只要试验对象能够正常运行,可不需要精确的调整。 c) 在试验开始时,影响试验对象功能并与试验结果相关的所有保护设备都应处于正常运行状态。用于放电的所有相关的主要接触器都应闭合(如电池系统回路中包含相关继电器)。 8.2.15.3 放电过程如下: a) 外部放电设备应连接到试验对象的主端子; b) 应与电池系统制造商协商,在规定的正常工作范围内以稳定的电流进行放电。 8.2.15.4 放电应持续进行,直至符合以下任一条件时,结束试验: a) 试验对象自动终止放电电流; b) 试验对象发出终止放电电流的信号; 81 犌犅38031—2020 c) 当试验对象的自动中断功能未起作用,或者没有8.2.15.4中a)所述的功能,则应继续放电,使得试验对象放电到其额定电压的25%为止; d) 试验对象的温度稳定,温度变化在2h内小于4℃。 8.2.15.5 完成以上试验步骤后,在试验环境温度下观察1h。 9 实施日期 新申请型式批准的车型自本标准实施之日起开始执行,已获得型式批准的车型自本标准实施之日起第13个月开始执行。 91 犌犅38031—2020 附 录 犃(资料性附录) 电池包或系统的典型结构 犃.1 电池包 电池包是能量存储装置,通常包括电池单体、部件、高压电路、过流保护装置及与其他外部系统的接口(如冷却、高压、辅助低压和通信等)。图A.1是一个电池包的典型结构。 说明: In ———冷却介质进口; Out———冷却介质出口。 图犃.1 电池包典型结构 犃.2 电池系统 电池系统是能量存储装置,包括电池单体或电池包、电路和电控单元(如电池控制单元、电流接触器)。电池系统的典型结构有两种,分别是集成了电池控制单元的电池系统和带外置电池控制单元的电池系统,分别如图A.2和图A.3所示。 02 犌犅38031—2020 说明: In ———冷却介质进口; Out———冷却介质出口。 图犃.2 含集成电池控制单元的电池系统典型结构 说明: In ———冷却介质进口; Out———冷却介质出口。 图犃.3 外置集成电池控制单元的电池系统典型结构 12 犌犅38031—2020 附 录 犅(规范性附录) 电池包或系统绝缘电阻测试方法 犅.1 目的 明确电池包或系统的绝缘电阻测试方法。 犅.2 试验条件 电池包或系统均以制造商规定的完全充电状态进行,试验环境温度为22℃±5℃,湿度为 15%~90%。电压检测工具的内阻不小于10MΩ。在测量时若绝缘监测功能会对电池包或系统绝缘电阻的测试产生影响,则应将绝缘监测功能关闭或者将绝缘电阻监测单元从B级电压电路中断开,以免影响测量值,否则制造商可选择是否关闭绝缘监测功能或者将绝缘监测单元从B级电压电路中断开。 犅.3 绝缘电阻测试方法 犅.3.1 方法1 犅.3.1.1 使电池包或系统内的电力、电子开关激活以保证电池系统处于接通状态。 犅.3.1.2 用相同的两个电压检测工具同时测量电池包或系统的两个端子和电平台之间的电压,如图B.1所示。待读数稳定,较高的一个为犝1,较低的一个为犝1′。 注:电池包或系统的电平台可以是其与整车电平台连接的可导电外壳。 图犅.1 绝缘电阻测量步骤1 犅.3.1.3 添加一个已知电阻犚0,阻值推荐1MΩ。如图B.2所示并联在电池包或系统的犝1 侧端子与电 平台之间。再用B.3.1.2中的两个电压检测工具同时测量电池包或系统的两个端子和电平台之间的电压,待读数稳定,测量值为犝2 和犝2′。 22 犌犅38031—2020 图犅.2 绝缘电阻测量步骤2 犅.3.1.4 计算绝缘电阻犚i,方法如下: 犚i 可以使用犚0 和四个电压值犝1、犝1′、犝2 和犝2′以及电压检测设备内阻狉,代入式(B.1)或式(B.2)来计算。 犚i×狉犚i+狉=犚0 犝2′犝2 -犝1′犝1( ) …………………………(B.1) 犚i= 11 犚0 犝2′犝2 -犝1′犝1( )-1狉 …………………………(B.2) 犅.3.2 方法2 犅.3.2.1 使电池包或系统处于接通的状态。 犅.3.2.2 使用绝缘电阻仪分别测量电池包或系统两个端子和电平台之间的绝缘电阻。 注:电池包或系统的电平台可以是其与整车电平台连接的可导电外壳。 犅.3.2.3 测量电压:使用的测量电压应为电池包或系统标称电压的1.5倍或500V(d.c.)的电压,两者取较高值。测量时间:施加的电压应该足够长,以便获得稳定的读数,推荐值为30s。 32 犌犅38031—2020 附 录 犆(规范性附录) 热扩散乘员保护分析与验证报告 犆.1 目的 电池包或系统在由于单个电池热失控引起热扩散、进而导致乘员舱发生危险之前5min,应提供一个热事件报警信号(服务于整车热事件报警,提醒乘员疏散)。如果热扩散不会产生导致车辆乘员危险的情况,则认为该要求得到满足。 犆.2 制造商定义的热事件报警信号说明 犆.2.1 触发警告的热事件参数(例如温度、温升速率、SOC、电压下降、电流等)和相关阈值水平(通常明显区别于制造商规定的工作状态)。 犆.2.2 警告信号说明:描述传感器以及在发生热事件时电池包或系统控制说明。 犆.3 说明电池包或系统安全性文件 犆.3.1 在单个电池热失控引起热扩散的情况下,在电池单体、电池包或系统或车辆中应具有保护乘员的功能或特性。制造商应提供C.3.2~C.3.5中说明电池包或系统安全性文件。 犆.3.2 风险降低分析:使用适当的行业标准方法记录单个电池热失控导致热扩散所引起的对车辆乘员的风险以及降低风险所采用的缓解功能或特征(例如:GB/T34590、ISO26262、GB/T20438、 IEC61508中的故障分析或类似的方法)。 犆.3.3 相关物理系统和组件的系统图。相关系统和组件是指有助于保护乘员免受由单个电池热失控触发的热扩散所引起的危害影响的系统和组件。 犆.3.4 表示相关系统和组件的功能操作、确认所有风险缓解功能或特征的图表。 犆.3.5 制造商应提供电池包或系统安全性的风险缓解功能或特征的验证程序及结果文件,包括以下部分: a) 对其操作策略的描述。 b) 实现功能的物理系统或组件的标识。 c) 说明风险缓解功能技术文书:分析或模拟验证的程序和结果数据。 d) 说明风险缓解功能技术文书:验证试验的程序和结果数据。包括以下部分: 1) 试验时间、地点及产品技术参数; 2) 试验程序:包括试验方法、试验对象、触发对象、监控点布置方案、热失控触发判定条件以及对试验对象所做的改动清单等,制造商可自行提供试验程序,也可参考C.5所述程序; 3) 试验结果:包括试验关键事件(热失控触发开启、热失控触发停止、热事件报警信号、外部烟、火、爆炸等)的照片、数据和时间等。 犆.4 验证与资料提供说明 犆.4.1 检测机构依据制造商提供的技术文书、试验程序进行结果验证,并提供试验报告。 犆.4.2 热扩散乘员保护分析与验证报告应包含表C.1所列3项报告,其中第1项和第2项由制造商提 42 犌犅38031—2020 供,第3项由检测机构出具。 注:C.3.5d)与C.4所述的验证试验可为在相同检测机构进行的同一试验。 表犆.1 热扩散乘员保护分析与验证报告详细内容 编号 报告名称 对应章条 1 制造商定义的热事件报警信号说明 C.2.1、C.2.2 2 说明电池包或系统安全性技术文件 C.3.2、C.3.3、C.3.4、C.3.5 3 检测机构依据制造商提供的技术文书、试验程序进行结果验证的检测 报告 C.4 犆.5 热扩散乘员保护验证试验程序 犆.5.1 试验对象 试验对象为整车或电池包或系统。 犆.5.2 试验条件 试验应在以下条件进行: a) 本试验在温度为0℃以上,相对湿度为10%~90%,大气压力为86kPa~106kPa的环境中进行。 b) 试验开始前,对试验对象的SOC进行调整。对于设计为外部充电的电池包或系统,SOC调至不低于制造商规定的正常SOC工作范围的95%;对于设计为仅通过车辆能源进行充电的电池包或系统,SOC调至不低于制造商工作范围的90%。 c) 热扩散试验可能需要在测试开始前对电池包或系统进行一定程度的改动,导致可能无法进行充电,需在试验开始前确认试验对象的SOC满足要求。 d) 试验开始前,所有的试验装置正常运行。 e) 试验尽可能少地对测试样品进行改动,制造商需提交所做改动的清单。 f) 试验在室内环境或者风速不大于2.5km/h的环境下进行。 犆.5.3 试验方法 犆.5.3.1 推荐C.5.3.3或C.5.3.4作为热扩散试验的可选方法,制造商可以选择其中一种方法,也可自行选择其他方法来触发热失控。 犆.5.3.2 热失控触发对象:试验对象中的电池单体。选择电池包内靠近中心位置,或者被其他电池单体包围的电池单体。 犆.5.3.3 推荐的针刺触发热失控方法如下: a) 刺针材料:钢; b) 刺针直径:3mm~8mm; c) 针尖形状:圆锥形,角度为20°~60°; d) 针刺速度:0.1mm/s~10mm/s; e) 针刺位置及方向:选择能触发电池单体发生热失控的位置和方向(例如,垂直于极片的方向)。 犆.5.3.4 推荐的加热触发热失控方法:使用平面状或者棒状加热装置,并且其表面应覆盖陶瓷、金属或绝缘层。对于尺寸与电池单体相同的块状加热装置,可用该加热装置代替其中一个电池单体,与触发对象的表面直接接触;对于薄膜加热装置,则应将其始终附着在触发对象的表面;加热装置的加热面积都 52 犌犅38031—2020 应不大于电池单体的表面积;将加热装置的加热面与电池单体表面直接接触,加热装置的位置应与C.5.3.5中规定的温度传感器的位置相对应;安装完成后,应在24h内启动加热装置,以加热装置的最大功率对触发对象进行加热;加热装置的功率要求见表C.2;当发生热失控或者C.5.3.5定义的监测点温度达到 300℃时,停止触发。 表犆.2 加热装置功率选择 触发对象电能犈Wh 加热装置最大功率 W 犈<100 30~300 100≤犈<400 300~1000 400≤犈<800 300~2000 犈≥800 >600 犆.5.3.5 推荐的监控点布置方案如下: a) 监测电压或温度,应使用原始的电路或追加新增的测试用电路。监测温度定义为温度A(测试过程中触发对象的最高表面温度)。温度数据的采样间隔应小于1s,准确度要求为±2℃。 b) 针刺触发时,温度传感器的位置应尽可能接近短路点,也可使用针的温度(如图C.1所示)。 c) 加热触发时,温度传感器布置在远离热传导的一侧,即安装在加热装置的对侧(如图C.2所示)。 图犆.1 针刺触发时温度传感器的布置位置示意图 犪) 硬壳及软包电池 犫) 圆柱形电池Ⅰ 犮)圆柱形电池Ⅱ说明: 加热装置 加热装置(电阻丝) 温度监测器 图犆.2 加热触发时温度传感器的布置位置示意图 62 犌犅38031—2020 犆.5.3.6 推荐的热失控触发判定条件: a) 触发对象产生电压降,且下降值超过初始电压的25%; b) 监测点温度达到制造商规定的最高工作温度; c) 监测点的温升速率d犜/d狋≥1℃/s,且持续3s以上。当a)和c)或者b)和c)发生时,判定发生热失控。如果采用推荐的方法作为热失控触发方法,且未发生热失控,为了确保热扩散不会导致车辆乘员危险,需证明采用如上两种推荐方法均不会发生热失控。 72 犌犅38031—2020 参 考 文 献 [1] GB/T20438(所有部分) 电气/电子/可编程电子安全相关系统的功能安全 [2] GB/T34590(所有部分) 道路车辆 功能安全 [3] ISO26262(allparts) Roadvehicles—Functionalsafety[4] IEC61508(allparts) Functionalsafetyofelectrical/electronic/programmableelectronicsafetyrelatedsystems 82 犌犅38031—2020查看更多