- 2022-08-08 发布 |
- 37.5 KB |
- 31页

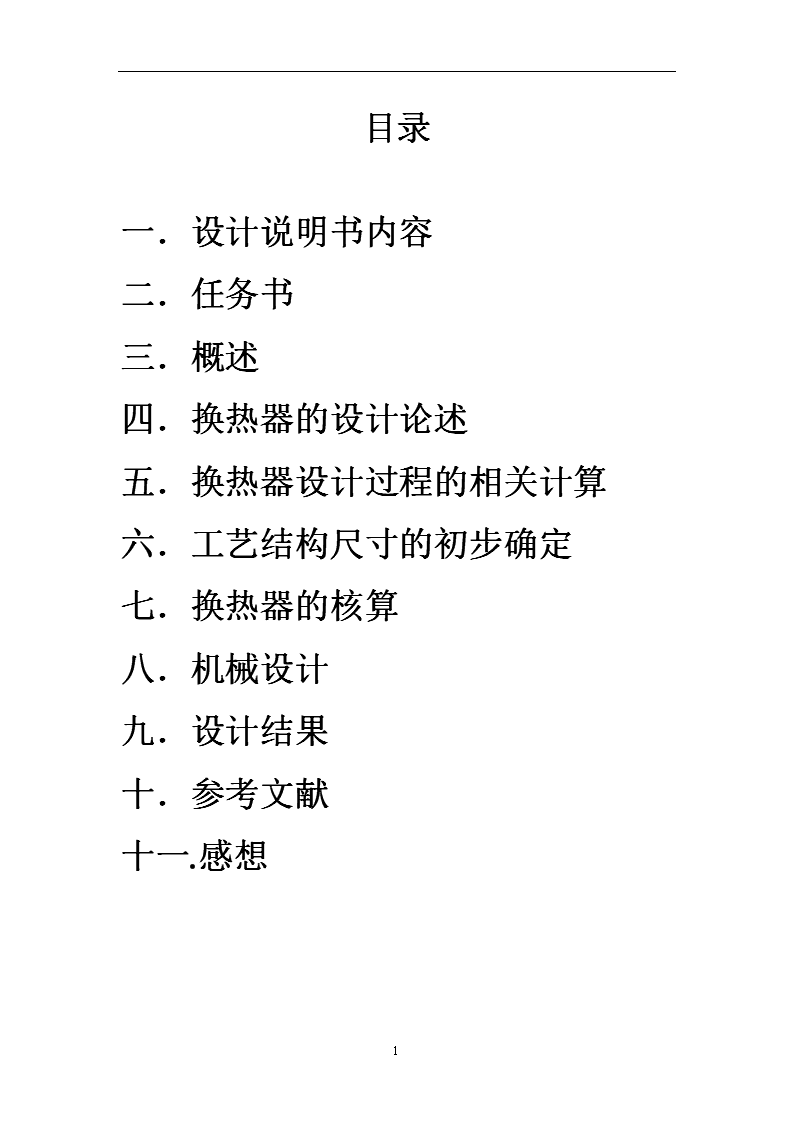
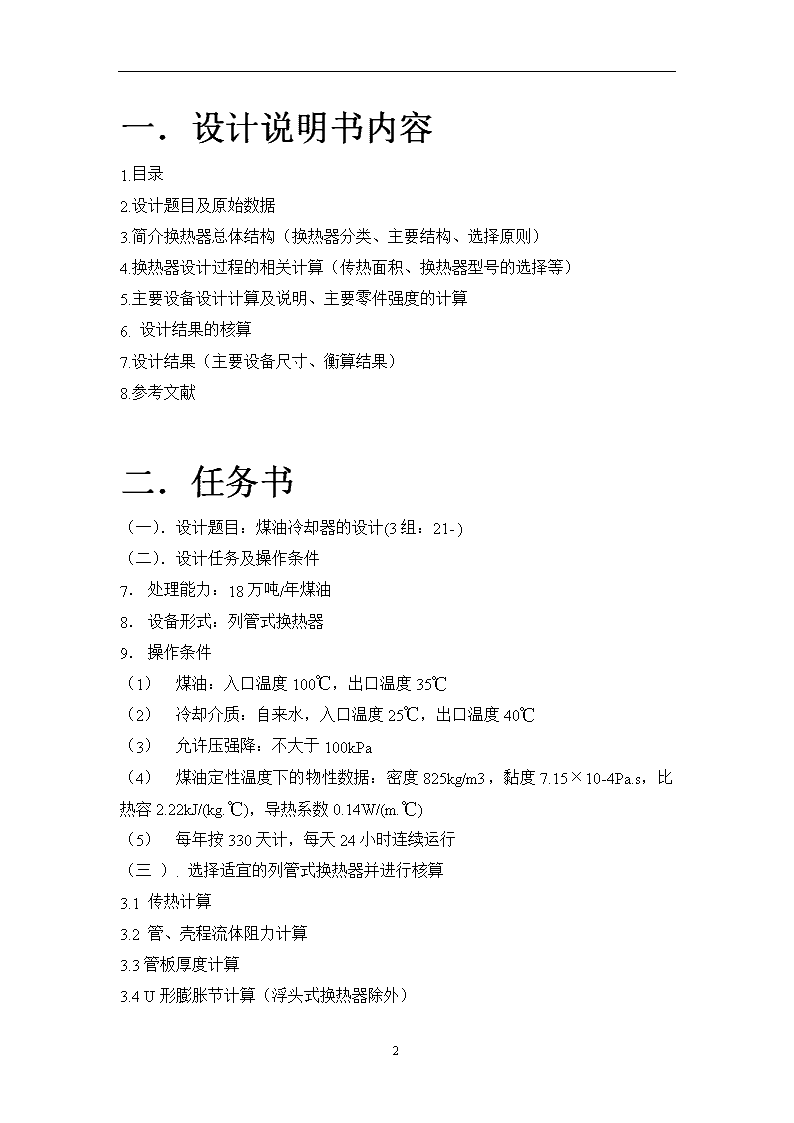
申明敬告: 本站不保证该用户上传的文档完整性,不预览、不比对内容而直接下载产生的反悔问题本站不予受理。
文档介绍
[工学]换热器设计
化工原理课程设计说明书列管式换热器的选用和设计班级--------------------姓名---------------------指导教师----------------------2011-6-200\n目录一.设计说明书内容二.任务书三.概述四.换热器的设计论述五.换热器设计过程的相关计算六.工艺结构尺寸的初步确定七.换热器的核算八.机械设计九.设计结果十.参考文献十一.感想0\n一.设计说明书内容1.目录2.设计题目及原始数据3.简介换热器总体结构(换热器分类、主要结构、选择原则)4.换热器设计过程的相关计算(传热面积、换热器型号的选择等)5.主要设备设计计算及说明、主要零件强度的计算6.设计结果的核算7.设计结果(主要设备尺寸、衡算结果)8.参考文献二.任务书(一).设计题目:煤油冷却器的设计(3组:21-)(二).设计任务及操作条件7.处理能力:18万吨/年煤油8.设备形式:列管式换热器9.操作条件(1)煤油:入口温度100℃,出口温度35℃(2)冷却介质:自来水,入口温度25℃,出口温度40℃(3)允许压强降:不大于100kPa(4)煤油定性温度下的物性数据:密度825kg/m3,黏度7.15×10-4Pa.s,比热容2.22kJ/(kg.℃),导热系数0.14W/(m.℃)(5)每年按330天计,每天24小时连续运行(三).选择适宜的列管式换热器并进行核算3.1传热计算3.2管、壳程流体阻力计算3.3管板厚度计算3.4U形膨胀节计算(浮头式换热器除外)0\n3.5管束振动3.6管壳式换热器零部件结构(四).绘制换热器装配图(A2图纸)三.概述1.换热器简介换热器,是将热流体的部分热量传递给冷流体的设备,又称热交换器。换热器是化工、石油、动力、食品及其它许多工业部门的通用设备,在生产中占有重要地位。在一般化工厂的建设中,换热器约占总投资的11%。在炼油厂的常、减压蒸馏装置中,换热器约占总投资的20%。今后换热器的发展趋势将是不断增加紧凑性、互换性、不断降低材料消耗,提高传热效率和各种比特性,提高操作和维护的便捷性。在化工生产中换热器可作为加热器、冷却器、冷凝器、蒸发器和再沸器等,应用更加广泛。换热器种类很多,但根据冷、热流体热量交换的原理和方式基本上可分三大类即:间壁式、混合式和蓄热式。在三类换热器中,间壁式换热器应用最多。列管式换热器是间壁式换热器的主要类型。2.列管式换热器的结构管壳式换热器又称列管式换热器。是以封闭在壳体中管束的壁面作为传热面的间壁式换热器。管壳式换热器主要由壳体、管束、折流板、管板和封头等部件组成。壳体多为圆筒形,内部装有管束,管束安装在壳体内,两端固定在管板上。封头用螺栓与壳体两端的法兰相连。它的主要优点是单位体积所具有的传热面积大、结构紧凑、传热效果好。结构坚固,而且可以选用的结构材料范围广,故适应性强、操作弹性较大。与其它品种换热器比较,管壳式换热器的最大缺点是传热效率低。例如,对于水一水换热,传统的管壳式换热器K值范围一般为1150~2230W/㎡•℃,而板式换热器K值为1500~4700W/㎡•℃,螺旋板式为2000~3000W/㎡•℃。0\n进行换热的冷热两种流体,一种在管内流动,称为管程流体;另一种在管外流动,称为壳程流体。为提高管外流体的传热分系数,通常在壳体内安装若干挡板。挡板可提高壳程流体速度,迫使流体按规定路程多次横向通过管束,增强流体湍流程度。图1列管式换热器的基本结构3.换热器的分类列管式换热器种类很多,目前广泛使用的按其温差补偿结构来分,主要有以下几种:(1).固定管板式换热器(代号G)此种换热器管束连接在管板上,管板分别焊在外壳两端,并在其上连接有顶盖,顶盖和壳体装有流体进出口接管。通常在管外装置一系列垂直于管束的挡板。同时管子和管板与外壳的连接都是刚性的,而管内管外是两种不同温度的流体。因此,当管壁与壳壁温差较大时,由于两者的热膨胀不同,产生了很大的温差应力,以至管子扭弯或使管子从管板上松脱,甚至毁坏换热器。固定管板式换热器有结构简单、排管多、紧凑、造价便宜,等优点。但由于结构紧凑,固定管板式换热器的壳侧不易清洗,而且当管束和壳体之间的温差太大时,管子和管板易发生脱离,故不适用与温差大的场合。为了克服温差应力必须有温差补偿装置,一般在管壁与壳壁温度相差50℃以上时,为安全起见,换热器应有温差补偿装置。但补偿装置(膨胀节)只能用在壳壁与管壁温差低于60~70℃和壳程流体压强不高的情况。一般壳程压强超过0.6Mpa时由于补偿圈过厚,难以伸缩,失去温差补偿的作用,就应考虑其他结构。0\n图2带有温度补偿的固定管板式换热器1—挡板;2—补偿圈;3—放气嘴(2).浮头式换热器(代号F)浮头式换热器针对固定管板式换热器的缺陷进行了改进,浮头式换热器的一块管板用法兰与外壳相连接,另一块管板不与外壳连接,以使管子受热或冷却时可以自由伸缩,但在这块管板上连接一个顶盖,称之为“浮头”,所以这种换热器叫做浮头式换热器。其优点是:管束可以拉出,易于清洗和检修,所以能适用于管壳壁间温差较大,或易于腐蚀和易于结垢的场合;管束的膨胀不变壳体约束,因而当两种换热器介质的温差大时,不会因管束与壳体的热膨胀量的不同而产生温差应力。但其结构复杂、笨重、造价高限制了它的使用。图3.浮头式列管换热器1—管程隔板;2—壳程隔板;3—浮头(3).填料函式换热器 填料函式换热器也只有一端与壳体固定,另一端采用填料函密封。它的管束也可自由膨胀,结构比浮头式简单,造价较低。但填料函易泄露,故壳程压力不宜过高,也不宜用于易挥发、易燃、易爆、有毒的场合。(4).U型管式换热器(代号Y)0\n U形管式换热器,每根管子都弯成U形,两端固定在同一块管板上,每根管子皆可自由伸缩,从而解决热补偿问题。管程至少为两程,管束可以抽出清洗,管子可以自由膨胀。其缺点是管子内壁清洗困难,管子更换困难,管板上排列的管子少。优点是结构简单,质量轻,适用于高温高压条件。图4U型管式列管换热器1—U形管;2—壳程隔板;3—管程隔板4.换热器的主要部件(1)换热管 换热管的尺寸和形状对传热有很大影响,管径越小,单位体积设备的传热面积就越大,这意味着设备越紧凑,体积则越小,对流传热系数较高。但制造麻烦,且小管易结垢,不易机械清洗。所以对清洁的流体小管子为宜,对粘度大或易结垢的液体管径则可取大些。目前我国列管式换热器系列标准中,所采用的无缝钢管规格多为19mm×2mm和25mm×2.5mm两种。换热器一般用光管,这样结构简单,制造容易,但对流传热系数较低。管子在管板上的固定,原则是必须保证管子和管板连接牢固,不能在连接处产生泄漏,否则会给操作带来严重故障。目前广泛采用胀接法和焊接法,在高温高压时有时也采用胀接加焊接的方法,近来出现了一种爆炸胀管法。胀接法是用胀管器挤压伸人管板孔中的管子端部,使管端发生塑性变形,管板孔同时产生弹性变形。当取出胀管器后,管板孔弹性收缩,管板和管子就会紧紧挤压在一起,实现密封紧固。采用胀接时,管板硬度应比管端高,这样可免除在胀接时管板孔产生塑性变形,影响胀接的紧密性。胀接法一般多用于压力低于3.923Pa,温度低于300℃0\n的场合。如果温度高,管子和管板会产生蠕变,胀接应力松弛而引起连接处泄漏。所以对高压、高温、易燃易爆的流体,换热管的紧固多采用焊接法。当温度高于300℃或压力高于3.923Pa时,一般多采用焊接法。这样可保证高温高压时连接的紧密性,同时焊接工艺较胀管工艺简便,管板孔加工要求低,且压力不太高时可使用较薄的管板,因此焊接法被广泛采用。但焊接法由于焊接接头处的热应力,可能会造成应力腐蚀和破裂,同时管板孔与管子间存在间隙。换热管在管板上可按等边三角形、正方形直列和正方形错列排列。等边三角形排列较紧凑,管外流体湍动程度高,传热分系数大;正方形排列管外清洁方便。图5换热管在管板上的排列(a)正三角形排列;(b)正方形直列;(c)正方形错列(2)管板列管式换热器的管板一般用圆平板,在上面开孔以装设换热管束,管板又与壳体连接。管板与壳体的连接方法与换热器的形式有关。对固定管板式换热器,常采用不可拆连接方式,即直接将两端管板焊接在壳体。对浮头式、U形管式换热器,由于管束要从壳体中抽出,故常用可拆连接方式,即把管板夹于壳体法兰与顶盖法兰之间,用螺栓紧固,必要时卸下顶盖就可把管板连同管束从壳体中抽出。(3)折流挡板为了加大壳程流体的速度,增强湍动程度,以提高壳程流体的对流传热系数,往往在壳程内装置折流挡板。另外折流挡板对换热管束还起着支撑作用,可防止管子的变形。不利的是挡板的存在使流体阻力增加,另外挡板和壳体间、挡板和管束间的间隙如过大,部分流体会从问隙中流过,产生旁流,严重时反而会使对流传热系数减小。折流挡板形式较多,主要有两种,一种是横向折流挡板,壳程流体横向流动;另一种是纵向折流挡板,壳程流体平行流过管束。0\n(4)主要附件①封头封头有方形和圆形两种。方形用于直径小(一般小于300mm)的壳体,圆形用于大直径的壳体。由于在清洗和检修管束时需将封头拆下,所以封头结构应便于拆装,一般通过法兰与壳体连接。②导流筒在壳程流体进、出口和管板间必存在一段流体不能流动的空间(死角),这显然对传热不利。所以常在管束外增设导流筒,使流体进、出壳程时必然经过这个空间,尽量消除死角,提高传热效果。③放气孔、排液孔在换热器的壳体上常安装放气孔和排液孔,以排出不凝气体和冷凝液体。④支撑板、缓冲挡板一般卧式换热器都有折流挡板,它既起折流作用,又对换热管起支撑作用。但当工艺上无折流挡板的要求,例如冷凝器,而管子又比较细长时,应设置一定数量的支撑板,以便于安装管子和防止管子变形。缓冲挡板是为了防止壳程流体进人换热器时对管束的冲击,在进料管口设置,但距壳壁不应太近(不小于30rnm)}缓冲挡板有圆形和方形两种。导流筒由于是将流体导至管板处才进入管束间,所以对流体流入壳程时也起着缓冲作用。有时将壳程接管在入口处加以扩大,做成喇叭形,也是为了缓冲目的。换热器的其它零部件还有壳体、接管、膨胀节、支座、法兰和法兰盖等。四.换热器的设计论述1.列管式换热器的选用原则(1)流道的选择进行换热的冷热两流体,按以下原则选择流道:①不洁净和易结垢流体宜走管程,因管内清洗较方便;②腐蚀性流体宜走管程,以免管束与壳体同时受腐蚀;③压力高的流体宜走管程,以免壳体承受压力;④饱和蒸汽宜走壳程,因蒸汽冷凝传热分系数与流速无关,且冷凝液容易排出;⑤0\n若两流体温度差较大,选用固定管板式换热器时,宜使传热分系数大的流体走壳程,以减小热应力。(2).流体的流速选择增加流体在换热器中的流速,将增大对流传热系数,减少污垢热阻,使总传热系数增大,从而减少换热器的传热面积。但流速增加使流体阻力增加,动力消耗增多。所以适宜的流速要通过经济衡算得出。(3)基本原则①满足生产工艺要求所选用的换热器,一定要能完成换热任务(或称热负荷)。换热任务是由生产工艺条件决定的,是生产卜要求流体温度变化在单位时间内吸收或放出的热量。它的具体数值,可由流体热流量平衡方程,即冷流体的吸热速率或热流体的放热速率来计算。其实,换热任务就是对换热器换热能力的要求。所以,所选用的换热器能否满足工艺要求,取决于它的换热能力。这种换热能力,是在操作条件下换热器所能实现的传热速率,是换热器本身的特性。它的具体数值,可由总传热速率方程(Q=KA)来计算。对一个能满足工艺要求的换热器,其传热速率(换热能力)应大于生产热负荷(换热任务)。在机械强度,抗蚀、耐压能力等方面,所选用的换热器都应满足工艺要求。②操作、维护、检修方便③经济上合理在换热器选型和操作上艺参数的确定中,要有技术经济的观点,尽可能地节能、省材,使操作费用和一设备费用处于一个较合理的范围内。④保证生产安全在工艺流程和操作中,若有爆炸、燃烧、中毒等危险性,则要考虑必要的安全措施。对设备材料强度的验算,除应有一定的安全系数外,还应考虑防止由于设备压力突然升高或造成真空,而需要安装安全阀等措施。2.列管式换热器的选用步骤(1).了解生产任务、工艺特点和基本数据①冷、热流体的流量,进出口温度,操作压力;②冷、热流体的已知物性参数;③冷热流体的工艺特点,包括腐蚀性、悬浮物含量、有无相变等。0\n(2)确定流体流动途径(流程),确定换热器类型(3)进行选择设备型号的有关计算①计算两流体的定性温度,在此温度下查取流体的有关物性参数,如密度、粘度、比热容、导热系数等。②根据生产换热任务计算热负荷。③计算对数平均温度差,并根据温差校正系数不应小于}.}的原则决定壳程数。④根据总传热系数K值的经验数值范围,初步选定总传热系数K值⑤根据总传热速率方程,由初选的F值,计算出传热面积,由此在换热器系列标准中初步选出合适的设备型号。⑥一计算管程、壳程压力降。根据初选的换热器型号,计算两流体的流速和压力降,检查计算结果是否合理或是否满足工艺要求。若压力降不符合要求,则要调整流速,再确定管程数或折流板间距,或另选一种规格的换热器,再重新计算压力降,直至满足要求为止。⑦核算总传热系数。分别计算管程、壳程的对流传热系数,确定污垢热阻,计算总传热系数,并与开始初选的总传热系数进行比较。如果相差较多,则应再次设定总传热系数,重复以上计算步骤,直至接近为止。⑧计算传热面积。根据核算后的K值一与总传热速率方程,求出完成换热任务所需要的换热器面积A,再与所选换热器的实际面积A‘进行比较,一般A‘/A=1.15~1.25,以留一定的裕量。五.换热器设计过程的相关计算1.流体流动空间的选择与煤油相比,水易结垢,且对流传热系数一般较大,所以冷却水走换热器的管程;煤油走换热器的壳程,这也有利于散热降温。2.查取流体的物性参数冷却水的入口温度为25℃,出口温度为40℃,故其定性温度为0\n1.见《化工原理》上册修订版夏清、陈常贵主编331页2.见《化工原理》上册修订版夏清、陈常贵主编232页在此温度下查取冷却水和煤油的物性参数,结果见下表表1冷却水和煤油的物性参数煤油8252.220.7150.14水9964.1740.80070.61763.计算热负荷和冷却水用量若忽略换热器的热损失,水的流量可由热量衡算求得,即4.计算两流体的平均温度差先按理想逆流传热温差进行计算,对逆流传热温差进行校正。由R和P查温度校正系数图,若为单壳程,温度校正系数为<0.8,不可行,所以要选用双壳程,温度校正系数为>0.8,可行。所以校正后的温度为由于<50℃,0\n两流体间的温差较小,不需要温度补偿,故可选用双壳程的列管式换热器。3.见《化工原理》上册修订版夏清、陈常贵主编355页4.见《化工原理课程设计》柴敬诚主编11页5.计算传热面积参照列管式换热器中K的大致范围,根据两流体的具体情况,初步选定总传热系数K=350于是换热器的传热面积可初步确定,即六.工艺结构尺寸的初步确定1.管径与管内的流速目前我国列管式换热器系列标准中,所采用的无缝钢管规格多为19mm×2mm和25mm×2.5mm两种。在此选择25mm×2.5mm传热管,取管内流速u=0.8m/s。2.管程数与传热管数根据传热管内径及管内流速来确定单程传热管数:(根)按此计算换热管长度应为m可知换热管过长,易用多管程结构。工程上常用的有:1500、2000、3000、4500、6000、9000mm,现取l=4500mm,则管程数为:则所需换热管总数为:(根)3.传热管排布换热管在管板上可按正三角形、正方形直列和正方形错列0\n排列。等边三角形排列较紧凑,管外流体湍动程度高,传热分系数大;正方形排列管外清洁方便。本换热器采用正三角形排列,管间距为t=1,25d≈32mm,则横过管束中心线的管数为:5.见JB/T4715-92(根)4.壳体内经对于多管程结构,壳体内径按下式计算:其中是管板利用率,对于三角形排列四管程为0.6~0.8.5.折流挡板常用的折流挡板有弓形和圆盘—圆环形两种,本换热器采用弓形折流挡板,取弓形折流板的圆缺高度为壳体直径的25%,则切去圆缺的高度为:h=0.25D=0.25×700=175mm折流挡板的间距在允许的压力降范围内希望尽可能小,在系列标准中有如下几种:150、200、300、450、600mm,本换热器使用300mm。则折流板数为:(块)6.初选结果根据上述计算数据,通过查JB/T4715—92固定管板式换热器与基本参照的对照,初步选出适合的换热器类型,结果如下表。表2初选换热器型号及参数壳径/mm700管子尺寸25mm×2.5mm公称压力/Mpa4.00管长/m4.5计算换热面积/m111.2管子总数322管程数4管子排列方式正三角形壳程数2折流挡板形式弓形0\n七.换热器的核算1.核算总传热系数K值(1)计算管程对流传热系数该型号换热器总管数为322,由于是四管程,所以管程的流通截面积A为这样,冷却水的实际流速为故对流传热系数为:(2)计算管程对流传热系数换热器中心附近管排中流体流通截面积为式中h——折流挡板间距,取300mmt——管中心距,对于的管中心距为。由于换热器为双壳程,所以煤油的流速为:由于管为三角形排列,则有当量直径为0\n6.见《化工原理课程设计》柴敬诚主编21页7.见《化工原理》上册修订版夏清、陈常贵主编354页煤油在壳程中流动的雷诺数为因为在范围内,故可采用凯恩(Kern)法求算,即由于液体被冷却取0.95,所以(3)确定污垢热阻管程与壳程热阻分别取(4)计算总传热系数(管壁热阻可忽略时,总传热系数为:)(5)核算换热面积0\n按核算后所得的总传热系数K值计算所需换热面积8.见《化工原理》上册修订版夏清、陈常贵主编54页而该型号换热器的实际传热面积A为故可用,传热面积的裕度为按实际传热面积计算传热系数为故该型号换热器在规定流体流动条件下,能提供的总传热系数为,故所选换热器是合适的,总传热系数的裕度为2.核算压力降因为壳程和管程都有压力降的要求,所以要对管程和壳程的压力降进行核算。(1)、计算管程压强降管程压力降计算的通式为其中:△P1,流体横过管束的压强降,Pa△P2,流体通过折流板缺口的压强降,PaFS压强降的结垢校正因数,式中,壳程数=2,管程数=4前已算出:取不锈钢管壁的粗糙度,则由--R关联图可知摩擦系数所以0\n对于的管子,有(2)、计算壳程压强降壳程压力降计算的通式为其中其中:F---管子排列方法对压强降的校正因数fo---壳程流体的摩擦系数,Reo>500时,取fo=5.0×Reo-0.228nc---横过管束中心线的管子数NB---折流挡板数管子为正三角形排列,则取F=0.5折流挡板间距折流板数所以0\n9.见《化工设备设计手册》朱有庭,曲文海主编702页从上面计算可知,、﹤105Pa,该换热器管程与壳程的压强降均满足题设要求,故所选换热器合适。八.机械设计1.计算壳体壁厚由于换热器为内压容器,故可以采用内压容器的设计方法来确定其壁厚,根据内压薄壁容器“弹性失效”设计准则,壳壁计算壁厚计算公式为:考虑到流体腐蚀及进行清洗时对管路的磨损腐蚀等,取腐蚀裕量C2=1.2mm,则设计壁厚为:钢板负偏差为:C1=0.25mm故设计所得壁厚可以满足要求,则名义壁厚为:对于碳钢换热器,其最小壁厚应符合下表0\n10..见JB/T4737-95由此可知计算所得壁厚基本上可以满足要求。在设计中可选择壁厚为8mm。2.封头尺寸封头有方形和圆形两种,方形用于直径小(一般小于400mm)的壳体,圆形用于大直径的壳体。壳径为700mm,故选用圆形封头。上下两封头均选用标准椭圆形封头,根据JB/T4737-95椭圆形封头标准,封头为DN=700,曲面高度h。如图所示,下封头常与裙座焊接,材料用20R钢。3.管板尺寸管板的结构如下图所示:根据下表选用合适的管板0\n表3.管板尺寸mm由表中可知,选用规格为:DNDDDDDDCd螺柱(栓)bb规格数量70083079075569774270012.523M203232424.管板与管子连接由于本换热器的工作压力为低压,且为低温操作,综合考虑各种连接工艺的优缺点及使用范围最终确定采用胀接法,在胀接法连接管板与管子时,管板的硬度应该大于管子硬度,以保证在胀接时,管子发生塑性形变时管板仅发生弹性形变。通常管子材料选用10、20优质碳钢,管板采用25、35、Q225或低合金钢16Mn、Cr5Mo等。结合本次设计,管板采用16MnR。胀接长度确定:胀接长度取管板名义厚度减去3mm与50mm中的较小值,故本换热器的胀接长度为:l=min{38-3,50}=35mm5.管板与壳体的连接0\n在固定管板式换热器中,管板与壳体的连接均采用焊接。其连接结构如下图所示:局部放大图为:6.膨胀节(1)管壁温度估算由于管壁热阻一般可以忽略,故可以认为管内外壁的温度是相同的,由此可以得到以下关系:中,to、ti、tw分别为壳程、管程流体的平均温度及壁温。采用试差法最终求得tw=39.42℃(2)判断是否安装膨胀节0\n膨胀节是装在固定管板式换热器上面的挠性元件,对管子和壳体的膨胀变形差进行补偿,以消除或减少不利的温差应力。11.见《化工原理课程设计》柴敬诚主编14页12.见《化工设备设计手册》朱有庭,曲文海主编715页管、壳壁温差所产生的轴向力:压力作用于壳体上引起的轴向力:压力作用于管子上的轴向力:条件成立,故本换热器不必设置膨胀节7壳体厚度表4壳体标准尺寸壳体外径/mm325400,500,600,700800,900,10001100,1200最小壁厚/mm8101214计算知壳体外径DN=700,故壳体的厚度选用10mm。8.最大无支撑间距表5折流板的最大无支撑间距换热管外径(mm)141619253238最大无支撑间距(mm)110013001500185022002500由上表可知最大无支撑间距为1850mm0\n9折流板的厚度13.见《化工设备设计手册》朱有庭,曲文海主编715页14.见《化工设备设计手册》朱有庭,曲文海主编717页可由下表得出:(参考文献:化工设备设计手册朱有庭,曲文海主编)公称直径DN(mm)换热管无支撑跨距<300300~600600~900900~12001200~15001500折流板的最小厚度(mm)<40034581010400~700456101012700~900568101216900~15006810121616由上表知折流板的厚度取12mm。10.拉杆数量及直径由此可得本换热器需要直径为16mm的拉杆,数量为6根。11.拉杆尺寸拉杆连接尺寸由下图及下表格确定:0\n15.见《化工设备设计手册》朱有庭,曲文海主编717页12.拉杆孔拉杆与管板焊接连接的拉杆孔结构见图(a),拉杆深度等于拉杆孔直径,拉杆孔直径按下式确定:其中d为拉杆直径。拉杆与管板螺纹连接时,其结构图如(b),螺纹深度按下式确定:其中d0为拉杆公称直径。本换热器采用螺纹连接,则螺纹深度为:13定距管根据GB/T8163-2008流体输送用无缝钢管,采用Φ25×2.5的定距管。14.支座本换热器为卧式内压容器,应该选用鞍式支座,依照JB/T4712-92双鞍式支座标准,选用DN=700mmB1型鞍式支座。鞍式支座在换热器上的布置应该按照下列原则确定:如下所示0\n在本换热器设计过程中,令九.设计结果换热器主要结构尺寸和计算结果见下表:参数管程壳程进/出口温度/℃25/40100/35压力/MPa 0.1 0.1物性定性温度/℃32.567.5密度/(kg/m3)996825定压比热容/[kJ/(kg/k)]4.1742.22粘度/(Pa*s)8.007×107.15×10导热系数(W/mK)0.61760.14普朗特数5.4111.34设备结构参数形式固定管板式壳程数2壳体内径/㎜700台数1管径/㎜Φ25×2.5管心距/㎜32管长/㎜4500管子排列△管数目/根322折流板数/个14传热面积/㎡113.7折流板间距/㎜300管程数4材质碳钢0\n主要计算结果管程壳程流速/(m/s)0.5770.166表面传热系数/[]2946500.6污垢热阻/()阻力/MPa0.02019360.010856热流量/KW911.094传热温差/℃26.82传热系数/[W/(㎡?K)]335.68裕度/% 12.3% 0\n十.参考文献[1]《化工原理》(上册)修订版.夏清陈常贵主编.天津:天津大学出版,2005[2]《化工设备设计手册》.潘国昌、郭庆丰主编.北京:清华大学出版社,1988[3]《化工设备设计手册》朱有庭、曲文海主编,化学工业出版社,2005[4]JB/T4715-1992标准固定管板式换热器型式与基本参数国家标准查询检索[5]JB/T4737-95椭圆形封头[6]GB151-1999管壳式换热器[7]GB/T8163-2008流体输送用无缝钢管[8]《化工设备机械基础》董大勤主编化学工业出版社2003[9]《化工工艺制图》周大军主编化学工业出版社2005[10]《化工原理课程设计》柴敬诚主编天津大学化工原理教研室0\n十一.感想课程设计是培养学生综合运用所学知识,发现,提出,分析和解决实际问题,锻炼实践能力的重要环节,是对学生实际工作能力的具体训练和考察过程。本次课程设计是理论联系实际的桥梁,是我们学习化工设计基础的初步尝试。通过课程设计,使我们能综合运用本课程和前修课程的基本知识,进行融会贯通的独立思考,在规定的时间内完成了指定的化工设计任务,从而得到了化工程序设计的初步训练。通过课程设计,使我们更加深刻的了解了工程设计的基本内容,掌握化工设计的程序和方法,培养了我们分析和解决工程实际问题的能力。同时,通过课程设计,还可以使我们树立正确的设计思想,培养实事求是,严肃认真,高度负责的工作作风。此外,通过本次课程设计,提高了我们以下方面的能力1熟悉查阅文献资料,搜索有关数据。正确选用公式。当缺乏必要数据时,尚需要自己通过实验测定或到生产现场实际查定。2在兼顾技术上先进性,可行性,经济上合理的前提下,综合分析设计任务要求,确定化工工艺流程,进行设备选型,并提出保证过得程正常,安全运行所需的检测和计量参数,同时还要考虑改善劳动条件和环境保护的有效措施。3准确而迅速地进行过程计算用主要设备的工艺设计计算。4用精炼的语言,简洁的文字,清晰的图表来表达自己的设计思想的计算结果。在这次课程设计中也使我们的同学关系更进一步了,使我认识到合作的重要性.我和同学设计不同的方案,然后集中讨论,选择最佳的设计方案。遇到难的地方,就各自查找资料,询问老师或同学,既而进行攻坚,团队的力量是无穷的,没有克不了的难关。同学之间互相帮助,有什么不懂的大家在一起商量,听听不同的看法对我们更好的理解知识,所以在这里非常感谢帮助我的同学。在此也要感谢我们的指导老师卢老师对我们悉心的指导,感谢老师们给我们的帮助。在设计过程中,我通过查阅大量有关资料,与同学交流经验和自学,并向0\n老师请教等方式,使自己学到了不少知识,也经历了不少艰辛,但收获同样巨大。在整个设计中我懂得了许多东西,也培养了我独立工作的能力,树立了对自己工作能力的信心,相信会对今后的学习工作生活有非常重要的影响。而且大大提高了动手的能力,使我充分体会到了在创造过程中探索的艰难和成功时的喜悦。虽然这个设计做的也不太好,但是在设计过程中所学到的东西是这次课程设计的最大收获和财富,使我终身受益。0\n0查看更多